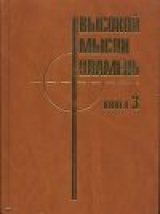
Текст книги "Высокой мысли пламень (Часть третья)"
Автор книги: авторов Коллектив
сообщить о нарушении
Текущая страница: 25 (всего у книги 37 страниц)
А. Балыкин.
23-йавтомобиль был у нас первым, аэродинамическую доводку которого мы вели по полной программе. Причём сами, уже никуда не обращаясь.
По 23-ймашине основной проблемой было подкапотное пространство. Сначала решили попробовать один механический вентилятор, а при необходимости к нему – электровентилятор.
Но механический получался слишком громоздким, и пришли в итоге к двум электровентиляторам, которые включаются по определённому алгоритму. Кстати, если на какой-то модели есть только один вентилятор, то там тоже есть свой алгоритм – сначала он включается через сопротивление на малую скорость, а затем при необходимости – и на полную.
Много пришлось заниматься потоками воздуха. Нужно ведь не просто засосать воздух в моторный отсек, но правильно им распорядиться, а потом его оптимально выбросить наружу. Иначе образуются застойные зоны и, как следствие, перегрев.
Не всё удалось оптимизировать должным образом, кое-что осталось. Но в основном проблема была решена.
Л. Комин.
По 23-му автомобилю было найдено соломоноворешение – поставили сиденья с десятки. Механизм продольной регулировки был сконструирован на бугурусланском заводе. Новый, современный механизм, который более-менее соответствует современным требованиям.
Задние сиденья разработаны ВАЗом. Подушка откидывается вперёд, да ещё раскладывается спинка. Она разделена на две части – треть справа, две трети слева.
А. Орлов.
По 2123мы провели подготовку производства. В самом конце поменяли наклон стойки, поменяли дизайн задка, всё это – в лучшую сторону.
GMплохие проекты не берёт. Они дали нам культуру. И не только нам, у нас же много поставщиков. Их надо было воспитать. Один АВТОВАЗих бы не победил никогда.
И когда ставили на производство 1118, с поставщиками было работать уже гораздо легче. Да и внутри завода тоже.
Н. Зуб.
По 23-йпервоначально были проекты выпуска до 290 000 автомобилей в год (как в 62-м корпусе, так и на главном конвейере).
Но реально начали заниматься проектом, когда стало ясно, что автомобиль может быть сделан только на существующей механике.
Считаю этот проект очень успешным, поскольку из имеющегося оборудования удалось выжать всё, что можно.
Спереди получено отрицательное плечо обката, что позволило применить диагональную схему тормозов со всеми преимуществами. Надо упомянуть и 9'' вакуумный усилитель (он пошёл именно с этой машины).
Задние амортизаторы установлены вертикально. Вкупе с передней подвеской это улучшило управляемость и устойчивость, а также плавность хода.
По КП сначала не давали делать никаких изменений. Но разорванный пакетпришлось-таки внедрять уже в ходе производства.
Сцепление 200 мм не годилось, применено покупное 215 мм.
Стальные диски колёс делаются на заводе, легкосплавные – в других местах (Красноярске, к примеру).
Это был первый автомобиль с ЭУР ( десяткаи прочие – это уже после). Сначала как комплектация, потом 100%. Но к моменту передачи в СПон ещё не был освоен. Наложилось и то, что в червячном рулевом механизме неизбежно имеется зазор в нулевом положении.
Это ведёт к отсутствию усиления в пределах этого зазора.
Наши испытатели это существенным не посчитали, но GMэто не устроило. А поскольку ГУР был уже проработан, то он и пошёл в производство в сентябре 2002 года.
АБС тоже была разработана и адаптирована.
Н. Овчинников, испытатель.
Если говорить о 23-ймашине, то там изначально была проблема с усилиями на руле. Из-за большего веса и более широких шин применение чисто механического РМ (без какого-либо усиления) исключалось напрочь.
Омологацию-то мы, может быть, и прошли бы, там требования послабее, а сертификацию по российским нормам – однозначно нет.
Сначала было решено применить ЭУР. Занимались этим долго и упорно, но результат был отрицательным.
Дело в том, что применение ЭУР на механизме типа червяк-роликнагружает сам РМ раза в полтора, что чревато снижением прочности и ходимости. Он начинает разрушаться при пробеге до 10 000 км!
Да и то, что нам предлагал махачкалинский завод Авиаагрегат, не годилось. Если величину компенсирующего момента они довели, то по шумам и надёжности сделать ничего так и не сумели.
Когда к этому плотно подключился GM, то после сравнения всех заи против, был выбран ГУР. С рулевым механизмом типа винт – шариковая гайка, созданным в своё время на ZFи модернизированным на ВАЗенашими специалистами Таршиным и Захаровым.
Его как раз и изготавливает предприятие Рулевые системы.
Механизм оказался на редкость удачным, и управляемость авт. Шеви Ниваоценивается на высоком уровне, не хуже зарубежных аналогов. При его приёмке участвовали специалисты фирмы Opel(европейского филиала GM), мы с ними работали совместно.
Усилие на руле просто прекрасное, повороты руля малые, довороты малые, чувствительность в центре превосходная.
П. Прусов.
К 23-му автомобилю мы шли дольше всех. Дважды делали фальстарт – не находилось средств. Первый – с макетом Белякова. Второй – когда работали Кряжев и Сёмушкин. Были сделаны макеты, прорисовки. Дальше дело не пошло.
Потом машина начала рождаться. Первые ходовые макеты были с независимой подвеской, реечным рулевым управлением.
Образцы показали себя неплохо. Но когда посчитали, во что это выливается по деньгам… И я предложил перейти от машины развитияк машине выживания. Сократить затраты втрое.
То есть, делать лишь то, что крайне необходимо. На задней подвеске только поставили амортизаторы вертикально.
Переднюю подвеску лишь причесалипо кинематике, да поменяли схему монтажа на конвейере.
Не стали трогать рулевой механизм. На первых машинах был электроусилитель, потом СПот него отказалось, они перешли на ГУР.
Довели двигатель по токсичности и шуму, перенесли наверх генератор. Передний мост отсоединили от двигателя.
Делали машину для себя, не думая о продаже какой-то компании. А когда начались переговоры с GMи маркетинговые исследования, из всех машин они выбрали нашу новую Ниву. И она была продана в СП.
В соответствии с первым контрактом мы после 2005 года вообще не имели права выпускать Ниву. И не разрабатывать ничего в этом диапазоне. Но потом появилось обращение общественных организаций ( ВАЗничего тут не мог поделать, поскольку подписал контракт).
Это были: Ассоциация автомобильных инженеров России, товаропроизводители, журнал « 4x4» (по факту – журнал любителей Нивы).
Был разбор в антимонопольном комитете, который признал эти пункты несущественными. В результате чего бренд мы потеряли.
В 23-мсемействе были ещё пикапи фургон. На одной из модификаций был установлен барнаульский дизель 1,8 л, разработанный на ВАЗе(развитие 1,5-л версии).
Сейчас пикапи фургонне выпускаются.
Любая разработка стоит денег. Но работать на уровне пластилина нам никто не мешает. Как и на уровне компоновочных предложений.
Но мы сейчас все стали такими законопослушными! Если нет строчки в плане, никто и пальцем не пошевелит.
А я вот считал и считаю так. Все мы родом из Советского Союза. Надо сделать опытный образец, показать его руководству. Если оно кивнёт, тогда и строчка появится. А бумаге кто поверит?

С. Васильев, конструктор.
В конце 1988 года была завершена выдача конструкторской документации на модернизированный автомобиль 21213.
Ещё шла подготовка производства, предстоял запуск на конвейер, а в Дизайн-центре уже шли работы по новому проекту – автомобилю 2123.
На тот момент основным вариантом был дизайн-проект А. Белякова. Его-то мы и использовали для предварительной эскизной компоновки каркаса кузова – в частности, передка. В это время продолжались работы по проектам 2110, 1121, намечался также совместный с ФИАТомпроект А-93(для Елабуги).
В перерывах между этапами этих работ мы (я и Н. Вершинников), чтобы не терять времени (приказа на проектирование ещё не было), начали прикидывать, что из себя может представлять конструкция передка кузова.
Всегда ведь хочется, чтобы новый кузов был лишён недостатков кузова предыдущей модели. Это желание формирует критерии или, скажем, задачи, поставленные самим себе, которые необходимо решить. К таким недостаткам кузова 2121мы отнесли:
1) горизонтальный нижний фланец лонжерона и брызговика переднего крыла, что потребовало усиления лонжерона (точки сварки на отрыв работают хуже, чем на срез), а это – дополнительные детали и точки сварки;
2) окнов брызговике для прохода верхнего рычага передней подвески – это требовало частичной разборки на конвейере передней подвески, чтобы пропихнутьрычаг при сборке автомобиля, а это дополнительная трудоёмкость;
3) слабенькоесечение передних лонжеронов, что делало проблематичным соответствие требованиям пассивной безопасности и требовало наличия раскосов передка (т.е. дополнительных деталей и точек сварки);
4) предполагаемое усиление щитка передка (по опыту 2110, когда работа реечного рулевого механизма приводила к разрушениям в этой зоне, что потребовало в своё время дополнительного усиления). А на 2123как раз предполагался рулевой механизм с рейкой.
Решая первую проблему, Вершинников набрасывал всевозможные варианты сопряжения лонжерон-брызговикс тем, чтобы иметь гладкую нижнюю часть лонжерона и вертикальные фланцы.
Я же прикидывал, куда направить лонжерон после щитка передка – прямо или в порог пола (это определяло конструкцию и самого щитка, и брызговика, да и панели пола).
Но на этом факультативномэтапе ничего конкретного не получилось. Все варианты сопряжения имели свои плюсы и минусы, некоторые элементы получались сложными для реализации. Следовательно, была неопределённой и дальнейшая разузловка.
Единственное, что стало ясным, это то, что из-за большой глубины брызговика направление лонжерона в порог пола было маловероятным.
Вторая и третья задачи решались сами собой. Поскольку предполагалось применение подвески Мак-Ферсон, то и верхнего рычага подвески не было, и, как следствие, не нужно было организовывать окно в брызговике и не было ограничений по высоте, что позволяло сделать сечение лонжерона достаточным для соответствия требованиям по пассивной безопасности.
Четвёртая задача решалась тем, что на щитке передка рейка должна располагаться в своеобразном тоннеле, что привело бы к уменьшению крутящего момента от сил при работе рулевого механизма относительно щитка передка.
Все эти прикидочные работы были приостановлены после невозвращения А. Белякова из международной парусной регаты в 1989 году, из-за чего дизайн-проект на некоторое время завис.
Правда, спустя некоторое время работы над дизайн-проектом возобновились, и уже после переезда в шоколадку(в 1992 году) были представлены несколько вариантов, в том числе и В. Кряжева.
Но к моменту выхода Приказа на разработку и постановку на производство автомобиля 2123за основу был принят проект В. Сёмушкина – автора дизайн-проекта 2121.
Когда всё утряслось – и дизайн-проект, и компоновка – то стало ясно, что проблем здесь хватает с избытком.К примеру, штатной должна была стать фара 2110, а сверху, как и на 2121, располагался указатель поворота.
Но у фары 2110уже есть точки крепления, которые определяют конструкцию верхней поперечины рамки радиатора, а указатель поворота, как самостоятельная деталь, должен крепиться на какие-то дополнительные кронштейны.
Возникло опасение, что погрешности при сварке кузова не позволят собрать автомобиль с равномерными зазорами (забегая вперёд, скажу, что так и вышло).
Смотрим дальше. Реечный рулевой механизм почему-то располагается в зоне моторного отсека не полностью, а левой своей стороной выходит в зону арки колеса. С учётом хода рулевых тяг получалось, что в этой зоне сопряжения брызговика и щитка передка вообще не может быть никакогометалла!
С такой ситуацией пришлось столкнуться впервые. Тем не менее, чем сложнее задачи, тем интереснее их решать. И мы принялись за работу (хотя к этому моменту Вершинников работал над проектами Консули 2120, так что решать эти проблемы мне пришлось самому).
По пограничнымзонам работали В.Черненко (впоследствии В. Хохленков) – пол, Ю. Пушкин – проём ветрового окна, крыша, проём двери задка, И. Новиков – боковина.
Итак, наступил момент истины– либо всё с нуля, либо максимально использовать предварительные наработки. Я решил, что проделанная работа не должна быть бесполезной и к конкретной компоновке узлов и агрегатов начал примерять то, что уже вырисовывалось до этого.
Сечение лонжерона, как и в наработках, решил оставить с гладкой донной частью, в виде перевёрнутой буквы П. Верхний, замыкающий сечение элемент – тоже перевёрнутая П с фланцем, привариваемым к брызговику.
Это позволяло иметь брызговик несложной формы и максимально опустить лонжерон и направить его под щиток передка и пол по прямой (это было очень хорошо с точки зрения фронтального удара, что впоследствии и подтвердилось).
Образовавшаяся в верхней части лонжерона (перевёрнутая П) ванночка была отмечена Мирзоевым после сборки прототипа как водосборник, хотя из-за наклона лонжерона и организованной зоны слива воды в районе щитка передка это было не так.
Более того, мне виделось, что в сочетании с пластмассовой крышкой это было идеальным местом для прокладки трубопроводов и жгутов проводов. Самое интересное, что Мирзоев больше никогда об этом не упоминал (поскольку доверял разработчикам и верил, что всё имеет свой смысл). А вот многочисленные доброхоты, однажды услышав мнение самого, постоянно мне об этом напоминали, и приходилось раз за разом объяснять, что так и задумано.
Проблему брызговика, где располагался рулевой механизм и тяги, решил так – чтобы не произошла потеря жёсткости кузова, развил верхнюю часть опоры подвески и замкнул её на щиток передка.
После сварки первого прототипа В. Доманский (ведущий конструктор проекта) усомнился, выдержит ли такое решение испытания на булыжникеи предложил приварить дополнительный раскос, замыкаемый на щиток передка.
Я был уверен, что выдержит, но с его предложением согласился, поскольку на серии 200функции раскоса можно было передать на элемент стойки, слегка изменив её конструкцию.
И вот прототипы пошли на испытания. Испытания на фронтальный удар – результат положительный. Ждём результатов по булыжнику и ресурсу.
А вот здесь всё пошло неудовлетворительно. Стали разрушаться кронштейны крепления рулевой рейки, хотя щиток передка не разрушался. Ну ладно, кронштейны можно будет усилить.
Начались разрушения передних амортизаторов, испытатели замучились их менять. Стало ясно, что необходимо увеличить размерность амортизаторов (тоже решаемо). Это, правда, не кузов.
Ещё одна проблема появилась неожиданно – невозможно вытащить силовой агрегат (с коробкой) через капот, а это условие оговорено техническим заданием. Верхняя поперечина не позволяла вынуть двигатель вверх и вперёд где-то на 40 – 50 мм.
Ю. Овчинников, инженер отдела компоновки, предложил сделать поперечину съёмной и даже выдал в экспериментальное производство эскизы такой поперечины, что и было реализовано.
Далее прототип каталсяв этом плане без проблем. Нужно сказать, что такие решения мне тоже очень нравятся, поскольку дают очень большие возможности при техническом обслуживании.
Но неожиданно воспротивились технологи-сварщики. Им нужна цельная поперечина для фиксации геометрии передка при сварке, в противном случае брызговики, не связанные между собой, впоследствии могут просто развалиться в стороны.
Тогда мы с И. Моряковым, технологом-сварщиком, который хотел всё же реализовать задуманное, решили выполнить поперечину из двух боковых и одной средней части, которые скрепляются болтами и поступают на сварку кузова как цельная деталь, но центральная часть может быть при необходимости снята. В таком виде и была выдана документация.
Итак, завершился первый цикл испытаний, и мы готовились к выдаче документации на серию 200с учётом полученных результатов. Мы и предположить не могли, какие коррективы заставит вводить в конструкцию политическая и экономическая ситуация в стране в 1994 – 95 гг.
В это время предприятие буквально боролось за выживание. Начались задержки выплаты заработной платы из-за несовершенства системы сбыта и, как следствие, несвоевременного возврата средств.
Для запуска семейства 2110требовались средства, и завод вынужден был прекратить отчисления в бюджет и внебюджетные фонды. Считалась каждая копейка. Стало ясно, что запуск авт. 2123в задуманном виде потребует значительных расходов.
В это время к руководству НТЦ пришли из МСП Н. Головко и А. Мелешихин, которые предложили применить для 2123имеющуюся агрегатную базу 21213, что должно было удешевить проект.
Конечно, такой поворот событий был вынужденным, в надежде довести всё-таки машину до конвейера.
Таким образом, при разработке конструкции кузова серии 200применялась уже старая двухрычажная подвеска.
Гидроусилитель рулевого управления был заменён на электроусилитель (впоследствии опять заменённый на СПна ГУР), съёмная верхняя поперечина по настоянию технологов заменена на цельную сварную.
Изменились фары и облицовка радиатора, что хорошо сказалось на облике автомобиля. Агрегатированная установка шасси (тоже хорошее решение) потребовала поднять лонжероны, что привело к сильному воздействию на щиток передка при фронтальном ударе, и с кузовом пришлось ещё долго повозиться.
Нужно сказать, что ввиду неопределённости судьбы проекта работы велись в рваном ритме – то затишье, то аврал. Например, контракт с фирмой Kukaна поставку линии сварки кузова заключался на свой страх и риск, без полной уверенности в благополучной перспективе.
В конце концов с компанией General Motorsбыло подписано генеральное соглашение о создании совместного производства авт. 2123под торговой маркой ШевролеНива. Американцы построили сборочный корпус и линию окраски (их доля в СП), и в сентябре 2002 года автомобиль пошёл по конвейеру.
Оглядываясь назад и понимая всю сложность судьбы этого автомобиля, мне всё-таки до сих пор кажется, что автомобиль серии 100стал автомобилем утерянных возможностей, мне он нравился больше.

Г. Троицкий, конструктор.
Берусь утверждать, что конструкция кузова и его систем автомобиля 2123(известного сейчас как ШевролеНива) была полностью, на 100% разработана конструкторами-кузовщиками управления проектирования автомобилей НТЦ ВАЗа. Свидетельство тому – большое количество полученных патентов на конструкцию.
Мне было доверено разработать конструкцию двери задка 2123. Тут надо рассмотреть несколько подробнее – что же здесь является новым по отношению к предыдущим автомобилям ВАЗ?
Это, пожалуй, два главных конструктивных решения, принятых техсоветом завода. Первое: открывание двери задка в сторону, а не вверх. Второе: закрепление на этой двери снаружи запасного колеса.
Итак, задача определена и поставлена: вперёд, в атаку! Кто же бойцыи какое у них оружие?
Бойцы– конструкторы: уважаемые нами Ю. Полев и В. Епишин от КБ механизмов; от КБ каркаса кузова способный В. Лихачёв и автор этих строк. Взаимопонимание в группе было полное.
Оружие– плазы и плёнка с сеткой, карандаши, циркули, линейки, калькуляторы и чертёжные кульманы. Часть проектных работ выполнялась с применением графических станций IBMи системы Catia.
Начались поиски и увязка конструктивных решений. Петли – справа, наружные видовые, дверь задка должна была открываться в правую (по направлению движения автомобиля) сторону. На этом настаивал как ведущий дизайнер В. Сёмушкин, так и некоторые коллеги.
Мне же представлялось рациональнее открывать дверь задка в левую сторону (т.е. петли слева) из условий погрузки багажа при нашем правостороннем движении в стране. Этого же мнения придерживались и многие другие коллеги – конструкторы, испытатели, эргономисты.
Впоследствии наша точка зрения возобладала на второйсерии проекта. Первая же серия опытных образцов была спроектирована с дверью задка, открывающейся в правую сторону. Дебаты были по этому вопросу большие, в том числе и в отделе общей компоновки.
Но если решение утверждено, то что же зря кулаками махать, надо работать!
Сложности при первоначальном проекте были большие, особенно с креплением петель и усилением под запасное колесо.
Надо отметить, что опыт проектирования подобной двери был накоплен при работе над проектом автомобиля для Ульяновского автозавода – ныне известного, как УАЗ Патриот.
По проекту его двери задка у нас основную работу вёл конструктор В. Михалёв, работали и другие конструкторы.
Дверь также была с боковой навеской и запасным колесом. На эту конструкцию был выдан патент на изобретение и до сих пор (включая 2007 год) мы получали из Ульяновска кое-какие ежегодные вознаграждения. Работали тогда мы с С. Гайсиным, ныне он работает у нас.
Но вернёмся к проекту двери задка для первых опытных образцов. Чтобы не нанести ущерба внешней форме, т.е. наружной поверхности двери задка и обеспечить штампуемость наружной панели без дефектов, поверхности прилегания петель пришлось выбрать плоскими (для упрощения регулировки петель в целях обеспечения требуемых зазоров).
Это вызвало необходимость применения метода построения плоскостей общего положения, что при ручном проектировании достаточно трудоёмко, и построения плавных переходов для штампуемости.
В свою очередь потребовалось сконструировать сложные для изготовления литые петли (Ю. Полев) и места прилегания неподвижных частей петель к каркасу кузова (В. Лихачёв). Но задача была решена.
Были сложности и с установкой кронштейна крепления запасного колеса (его положение было задано отделом общей компоновки).
Конструктор отдела шасси В. Григоров предложил простой в изготовлении (из листовой стали), но очень массивный и длинный кронштейн запасного колеса в целях сохранения гнёзд конусных гаек, которыми колесо крепится на ступицах.
Между внутренней и наружной панелями двери мною был спроектирован достаточно мощный усилитель, который передавал нагрузки от запасного колеса на петли.
Как только были изготовлены и переданы чертежи в экспериментальный цех и его технологические службы для изготовления опытных образцов, мы – проектировщики-конструкторы – стали проводить глубокий анализ наших решений и искать пути совершенствования конструкции.
В первую очередь было принято решение сделать анализ прочности с привлечением КБ расчётов, тогда только что организованного. Начался и подбор материалов, особенно по листовой стали, чтобы снизить вес автомобиля. Здесь неоценимую помощь нам оказывал исследовательский центр НТЦ.
При изготовлении опытных образцов 2123в экспериментальном цехе (начальник производства В. Бакулин) надо отметить добросовестную работу его технологических служб, особенно технологов Ю. Сухойвана и Д. Хусаинова. В ОПП прекрасно работал с нами технолог Бригинец, знающий и творческий специалист.
Хочу отметить и других специалистов, как руководителей, так и технологов и рабочих (модельщиков, сварщиков, сборщиков и т.д.) экспериментального цеха и ОПП.
Но вот и собран первый опытный образец. Что же получилось (коснёмся лишь двери задка)? Внешний вид – нелепо и дико торчит запасное колесо, неказистые петли двери также торчат и мозолят глаза (а на дизайнерском пластилиновом макете были вылеплены миниатюрные петли без учёта соосности, ось вращения должна быть одна!).
Открываем дверь – натыкаемся на травмоопасные углы внизу и вверху, на другие мелкие недочёты.
Начались ходовые и стендовые испытания опытных образцов. Выявились и неожиданные неприятности. Например: давно отработанный и освоенный упор, разгружающий замок от вертикальных нагрузок, разрушился чуть ли не на первых километрах пробега. К тому же деформировались задние стойки кузова, пришлось продолжить испытания данного образца с наглухо закрытой дверью задка.
Испытатели нашли и предложили простое решение проблемы упора – перевернуть его на 180°.
Проявилось и предсказанное ранее неудобство пользования открывающейся вправо дверью задка. Причём как в плане погрузки-разгрузки багажного отделения, так и по недостаточной обзорности через заднее стекло при движении задним ходом.
Внутреннее пространство двери съеденоприменённым освоенным действующим ограничителем открывания двери (в целях удешевления производства). Что ж, от промахов никто не застрахован, автомобиль создаётся людьми со всеми присущими им особенностями и характерами.
Часто при оценке предлагаемого решения у одних людей голос громче, у других погоны старше, а голос единицыедва слышен.
Многолетний конструкторский опыт дебатов при выборе конструктивного решения узлов и деталей проектируемого автомобиля привёл меня к своеобразному приёму (кстати, это нравилось Л. Вихко).
Рисую несколько (10 – 15) эскизных вариантов конструкции, вплоть до самых немыслимых и экзотических. У каждого отмечаю преимущества и недостатки, обсуждаю с заинтересованными специалистами, учитываю их мнения, вношу уточнения, составляю сводную табличку.
Указываю, что нами при обсуждении и анализе выбраны 1 – 2, как наиболее предпочтительные, и представляю начальникам, у которых при рассмотрении отпадают лишние вопросы.
В результате утверждается какое-то одно решение, как правило – наиболее рациональное.
Все материалы складывались мной в свой архив. Этот приём позволял быстро вести основное проектирование без дискуссий и дебатов, даже при освоении производства автомобиля и его узлов ВАЗоми заводами-поставщиками комплектующих изделий.
Продолжим наше повествование. Началось проектирование следующей серии образцов. Здесь полностью на 100% использовались графические станции и система Catia.
В составе конструкторов по двери задка произошли изменения: остались Г. Троицкий (сама дверь и стекло), В. Лихачёв (от КБ каркаса кузова), а вот от КБ механизмов вместо Полева и Епишина вошли Груненков (замок и ручка), Лукьянов (петли и упор в зоне замка), В. Гневшев (ограничитель открывания двери) под общим руководством и консультацией В. Носенко.
Следует упомянуть и других специалистов: Кислицын (КБ интерьера, обивка двери), В. Колесов (отдел электрооборудования, стеклоочиститель), Ж. Петрова (стеклоомыватель), В. Григоров (отдел шасси, запасное колесо). Со всеми работа шла плодотворно, творчески.
Сначала пришлось выполнить поиск оси вращения двери, так как техсоветом было принято решение – петли двери задка сделать невидовыми, внутренними. Петли расположить в зоне: наружная – внутренняя панели и стойка каркаса кузова, чтобы их не было видно снаружи.
Наружная поверхность двери весьма сложной формы. Расстояние между петлями должно быть как можно больше, но при этом оно ограничено глубиной штамповки петельной стойки каркаса кузова.
Поиск вариантов привёл к предложению конструкции петель: приварные к двери и крепление на болтах к стойке каркаса. На другом варианте настаивал технолог по сварке В. Тищенко – петли крепить на болтах и к двери, и к каркасу, чтобы облегчить регулировку по зазорам и по поверхности дверь – кузов.
По поверхности мы заранее заложили некоторое западание (2 – 3 мм), а вот на приварке петель к двери всё же настояли.
Тищенко не без оснований опасался за возможные дефекты сварных электродуговых швов. Поэтому, чтобы исключить возможность отрыва петель от двери в эксплуатации, ввели по одному страховочному болту крепления петли к двери – только для этой цели.
Наконец, положение оси петель было найдено, но при этом пришлось настоять на изменении формы зазора дверь – кузовв зоне фонаря, что, по моему мнению, только улучшило дизайн автомобиля.
Дело в том, что между торцом внутренней панели двери задка и стойкой каркаса кузова (петельной) в зоне заднего фонаря образовалось довольно большое пустое пространство.
И мне пришло в голову использовать его для компактного ограничителя, без захода его деталей внутрь двери.
Подумали мы вместе с В. Гневшевым, высказали свои соображения и получили поддержку В. Носенко. Он же поддержал нас и по конструкции петель.
Гневшевым был разработан оригинальный ограничитель открывания с применением торсионной пружины, дверь могла фиксироваться в трёх положениях. А в освободившемся месте внутри двери удалось разместить бачок с насосом для стеклоомывателя.
КБ электрооборудования применило новую разработку редуктора и электромотора стеклоочистителя – плоскую конструкцию, имеющую малые габариты и массу, что позволило увеличить в некоторой степени багажное отделение (внутрь ничего не торчало).
Внутри двери между наружной и внутренней панелями должен был разместиться какой-то усилитель, принимающий на себя силовые нагрузки от запасного колеса и агрегатов.
При поддержке А. Орлова нами было принято решение – единый усилитель, штампованный из листовой стали и передающий нагрузки на петли и упор в зоне замка. При этом замок разгружался от нагрузок.
Исследовательский центр предложил для этого усилителя сталь повышенной прочности (новую разработку металлургов).
Её особенностью являлось то, что она при изготовлении деталей ведёт себя, как обычная кузовная сталь (в части штампуемости и свариваемости), а затем после определённой тепловой обработки и выдержки увеличивает свои прочностные показатели.
За счёт явления старенияполучался наклёп. Температура и выдержка были подобраны к условиям прохождения кузова через сушильные камеры при окраске. Эта сталь стала для нас настоящей находкой, позволила снизить массу двери задка при необходимой прочности.
Специалисты КБ прочностных расчётов во главе со Шмелёвым сделали прочностные расчёты эскизных компоновок и дали свои рекомендации по сечениям и толщинам деталей, а также рекомендовали укоротить кронштейн запасного колеса, на чём мы ранее настаивали.
В отделе шасси разработали новый компактный кронштейн и крепление колеса с переворотом, а также изобрели новые детали крепления без деформации основных гнёзд.
Все вышеуказанные изменения позволили значительно снизить массу двери задка при обеспечении необходимой прочности.
При конструировании двери задка и деталей проёма неоценимую помощь оказал нам опытный технолог по штамповке Ш. Муфтеев, консультировавший нас постоянно в течение всего периода проектирования (он и донёс до нас народноеназвание внутреннего усилителя двери – жираф).
А технологи по сборке предложили крепить ограничитель открывания двери с расположением головок болтов внутри двери, между панелями – обеспечивался хороший доступ инструмента.
Стекло окна двери задка приклеивается полиуретановым клеем, окантовка стекла оригинальной формы была освоена Балаковским заводом РТИ с применением формованного участка в зоне стеклоочистителя.
Уплотнение проёма двери – замкнутый в кольцо неразъёмный профиль. Замок двери дополнительно защищён специальным резиновым уплотнителем, приклеенным на кузове в зоне замка.
Верхний зазор между крышей и дверью задка я предложил уплотнить понадёжнее. Удалось спроектировать оригинальный приклеенный ленточным клеем резиновый уплотнитель, и в верхней части двери задка получилось надёжнейшее тройное уплотнение.
В результате проведённых работ была создана неплохая и надёжная конструкция двери задка и проёма двери. С незначительными доработками она прошла все стадии изготовления и испытаний опытных образцов, где подтвердились наши конструкторские предложения.
Прошла также все стадии подготовки и освоения производства автомобиля Шевроле Нива. Конструкция защищена несколькими патентами – свидетельствами на изобретения.
После окончания проектных работ меня попросили разработать ТУ на поставку кузова 2123. Этой работой я занимался до ухода на пенсию в 2004 году. Работу над ТУ продолжил и закончил конструктор В. Коковин.
Эта работа заняла очень много времени – совещания, уточнения, согласование и тому подобное, но в конце концов и она была завершена.
Надо ещё добавить, что изготовление опытно-промышленных образцов 2123в ОПП на всех стадиях курировал В.Михалёв.

А.Байбаков, испытатель.
Думаю, что теперь уже можно, не опасаясь антирекламы, говорить о проблемах, возникавших на опытных кузовах 2123.
Не секрет, что этот автомобиль спроектирован на базе узлов и агрегатов автомобиля Нива 21213.
Но это не касается кузова, в котором нет ни одной заимствованной детали. Это внесло, разумеется, дополнительные ограничения на конструктивные решения при проектировании.
В службе главного конструктора АВТОВАЗисторически сложилась и продолжает развиваться технология проектирования и доводки кузова с упором на экспериментальную оценку конструкции.
Первый кузов, изготовленный в управлении экспериментального производства (УЭП), поступает в отдел доводки кузова (ОДК) на статические и динамические стендовые испытания для оценки на соответствие требованиям по жёсткости, прочности и долговечности.
Для примера приведу отдельные наименования методик испытаний из более 30-ти, применяемых для оценки каркаса и навесных узлов кузова:
– испытания кузова на статическую жёсткость при кручении и изгибе;
– испытания зон крепления рулевой колонки;
– испытания крыши, капота и крышки багажника на имитацию снеговой нагрузки;
– испытания боковых дверей на провисание и т.д.
Один из первых экспериментальных образцов в обязательном порядке направляется на ускоренные ресурсные испытания кузова на булыжной дорогетрека ВАЗа, где за три месяца накатывает 15 тыс. км, что эквивалентно пробегу в 150 тыс. км по дорогам общего пользования.
По результатам стендовых и трековых испытаний кузова выявляются проблемные зоны конструкции, проводятся доводочные работы и принимаются новые конструкторские решения. По такой схеме проводятся работы до получения положительных результатов испытаний.
Кузов автомобиля 2123также прошёл все этапы проектирования, испытаний, доводочных работ. Не обошлось тут без сложных и, в то же время, интересных доводочных работ.
К примеру, так сложилось, что испытания ПТ-577на булыжнике были начаты в ноябре 2001 года. Но, как это типично для России, в декабре совершенно неожиданнонаступила зима с морозами и метелями.
Занесённый снегом булыжник становится практически ровной дорогой, нагрузки на кузов резко снижаются, продолжать испытания бессмысленно. А очистить булыжник от снега практически невозможно – пробовали неоднократно и в конце концов отступились.
При пробеге 6 230 км натурные испытания были прекращены. Было принято решение продолжить испытания этого же образца в ОДК на стенде-имитаторе дороги фирмы Schenck.
Автомобиль ставится всеми колёсами на четыре гидроцилиндра, которые начинают пульсировать по заданной программе, имитируя движение по разбитой дороге.
И испытания были успешно завершены, получены разрушения и дефекты по кузову более 30 наименований, определены их причины.
Для обеспечения требуемой долговечности и жёсткости выданы замечания по качеству изготовления, а также рекомендации по доработке конструкции:
– задних кронштейнов крепления передней подвески к кузову;
– средних лонжеронов пола;
– щитка передка;
– нижнего усилителя щитка передка;
– стоек рамки радиатора;
– задних точек крепления раздаточной коробки.
Итоговое заключение: кузов не удовлетворяет требованиям по падению жёсткости на 24% (допустимо не более 10%) и по наличию усталостных разрушений на силовых элементах кузова.
При этом был также сделан вывод, что испытания на имитаторе не могут обеспечить полного нагружения кузова, поскольку нет продольных и поперечных нагрузок от разгона, торможения и поворотов автомобиля.
Для окончательной оценки усталостной прочности кузова необходимо всё-таки проведение испытаний в полном объёме на тяжёлом булыжникетрека ВАЗа.
Однако опять случилось так, что следующий образец ПТ-655с доработанным кузовом был собран только в ноябре 2002 года.
Поэтому его испытания на булыжнике даже начинать не стали, сразу установили на имитатор. Где он и был за три месяца испытан в объёме, эквивалентном 14 000 км пробега по тяжёлому булыжникутрека ВАЗа.
Результаты испытаний оказались значительно лучше предыдущих – падение жёсткости кузова составило всего 11%.
Прочность кузова в целом получила одобрение с небольшими рекомендациями на доработку. После проведения доработки кузов был передан в СПи запущен в производство.
С начала 2003 года выпуск автомобилей Шеви Нивастал постепенно увеличиваться. Но в связи с необходимостью установки силового агрегата FAMи гидроусилителя рулевого управления работа по конструкции кузова продолжилась.
В августе 2003 года начаты испытания на булыжном треке сразу двух автомобилей ШевиНива: серийного ПТ-119и опытного ПТ-211с двигателем FAMи с гидроусилителем рулевого управления.
Уже на первой трети пробега были отмечены разрушения кузова в зонах крепления продольных штанг заднего моста, а также в зоне крепления гидроусилителя.
Это вызвало серьёзные опасения за возможные рекламации в гарантийный период эксплуатации у потребителей и претензии от СП. В ОДК срочно были начаты доводочные работы.
Для сравнительных испытаний на усталостную прочность необходимо было определиться с фрагментами кузовов, с их креплением на стенде, направлением приложения нагрузок, режимом нагружения, изготовить оснастку и варианты усиления конструкции.
Специалисты бюро доводки каркаса и навесных узлов кузова в составе: начальника бюро С. Еверзова, инженеров О. Бакулина, В. Хлызова, А. Андреева, жестянщика К. Кукушкина, слесаря Л. Вахутова и сварщика А. Жаринова успешно решили все проблемы в сжатые сроки.
К концу января 2004 года было испытано девять вариантов внутреннего усилителя рулевого управления. Разница в долговечности лучшего и худшего варианта конструкции получилась более чем в 50 раз!
Таким образом, решение было найдено и реализовано в конструкции кузова автомобиля Шеви Нива. Испытания вариантов конструкции кузовов в зонах крепления продольных штанг заднего моста продлились до конца июля 2004 года.
В общей сложности было испытано 14 образцов трёх вариантов конструкции в зоне соединения порога и лонжерона. Вариант с минимальными изменениями конструкции соединителя порога обеспечил прочность крепления задней подвески и также был реализован в конструкции кузова автомобиля Шеви Нива.
По прошествии пяти лет эксплуатации автомобилей Шеви Нивапо дорогам и бездорожью России можно уверенно заявить об успешном проведении проектирования, испытаний и доводки кузова.

К. Кукушкин, испытатель.
Что такое доводка? В словаре Ожегова значится: доработка до состояния окончательной готовности.
Этим и занимается наш отдел – отдел доводки кузовов (ОДК), где я и проработал более 30 лет.
Но с чего, например, начинается доводка? В какой степени готовности должен поступать объект на эту самую доводку? Не начинать же её с нуля!
А ведь зачастую приходится! Значит, не был использован в полной мере предыдущий опыт.
И как довести неработоспособную конструкцию? Заменить её другой? Тогда будет ли это доводкой? Конечно, нет.
Долгожданная новая Нива2123, которой А. Мелешихин дал прозвище Иван( Нивас перестановкой букв) поставлена, наконец, на испытания на булыжнике – очень серьёзная проверка для любого автомобиля.
Первые сотни километров – первые неприятности для конструкторов и изготовителей. Где тонко, там и рвётся.
Где конструктор намудрил, стараясь внедрить что-то новое, необкатанное, непродуманное, там и появляются ляпсусы, прорехи. Уж более 20 лет (на тот момент) прошло, как вышла Нива. Полученный за это время опыт должен был помочь Ивануделать первые шаги поувереннее, но этого почему-то не произошло.
Почти каждый день Иванзаезжал на сварочный участок нашего отдела доводки кузовов для ремонта. Но как-то раз он задержался здесь уж слишком надолго.
Явилась целая делегация во главе с главным конструктором. Полностью разобранный Иванстоял на подъёмнике сварочного участка ОДК. Изъяны, полученные на булыжнике, были отмечены белыми стикерами с указанием даты и пробега.
Взглянув на автомобиль, Мирзоев быстро оценил ситуацию:
– И какой же это умник так наконструировал?
Все притихли, раздался чей-то негромкий голос:
– Черненко! Но он уволился.
Всё, виновник найден (хотя он и работал не в безвоздушном же пространстве!). А мне, подобно реаниматору, пришлось возвращать к жизни Иванадля продолжения булыжных испытаний.
Насмотревшись, вероятно, на иностранные внедорожники, наши дизайнеры и конструкторы решили навесить запасное колесо на заднюю дверь (в моторном отсеке для него места не нашлось).
Первые образцы поразили. Такая консольность крепления – и никаких усилений в двери! И зачем учат сопромат в учебных заведениях?
Доводка двери досталась мне. Переделал внутреннюю панель двери (без дополнительного металла) и кронштейн подвески колеса. И всё, дефект был ликвидирован, переделанная мною дверь задка 2123испытания выдержала.
Но получилось так, что как раз в эти дни у меня был юбилей, и ТВВАЗапочему-то решило сделать обо мне репортаж.
И я с этой дверью в руках и высказал в сердцах всё, что думал.
Конструктор – автор двери – передачу посмотрел и очень на меня обиделся, и зря. На авторство я не претендовал, а выполнял свою работу. За 30 лет работы на ВАЗев каждой модели есть хоть одна железка, переделанная или доведённая мной до приемлемого состояния. Но ни на одном чертеже нет моей фамилии! И я не обижаюсь, дело-то общее.
А вообще-то все конструкторы – люди разные, и к доработке (а то и переделке) своих творений относятся по-разному.
Одни категорически не приемлют никакихпредложений по изменениям, особенно с низов– какой-то слесарь (!) подрывает их авторитет!
Другие же, поняв суть и смысл изменения, просят изготовить для них лишнюю деталь. И по ней уже сделать чертёж, исключив ошибки, чтобы не изобретать велосипед. Мне же порой кажется, что деталь тут нужна просто для снятия с себя ответственности: доводчики предлагают.
Но мы немного отвлеклись. В общем, на булыжнике новая Ниватрещала по швам. Каждый день приходилось что-то подваривать, переделывать. Чтобы прийти к какому-то единому мнению, времени тратилось не очень много, а вот воплощать мнение приходилось, конечно, мне.
А тут ещё эта интеграция. Один за свой узел отвечает и тянет одеяло на себя, другой к себе тянет, забывая, что автомобиль – общее дитя и всё надо делать в комплексе.
У нас же зачастую получается, как у Крылова: один рвётся в облака, другой пятится назад, а третий… уже занял очередь в кассе.
Ещё вспоминается, как в декабре 1996 года дали мне задание: изготовить макет кузова будущей Нивы. Мне надо было выполнить в металле передние лонжероны, щиток передка, место для электро– или гидроусилителя руля и другие мелочи (хотя в автомобиле мелочей не бывает). Всё это делалось в спешном порядке. Месяц работы – месяц волнений. Условия-то воистину гаражные. Из оборудования – только пазовая плита, на которой всё и выставлял.
В 1997 году были произведены ударные испытания. Результаты – положительные. Успех? Конечно. Это можно было заметить по поощрительным премиям, где оказалось на удивление много непричастных. Но мы же общее дело делали.

Е. Венгранович, конструктор.
В 1996 году я был начальником бюро панели приборов отдела интерьера и систем кузова УПА. Впереди был проект панели приборов автомобиля 2123.
Честно говоря, накопилась уже некоторая усталость от того алгоритма работы, который мы обычно использовали в прежних проектах.
Это компоновка на плазе по рисункам и сечениям дизайнеров, выдача чертежей, постоянное пребывание у деревомодельщиков и мучения по поводу того, как обеспечить сопряжение деталей, полученных с деревомодельных форм и сделанных людьми разной квалификации.
Мы, конечно уже использовали в некоторых работах элементы САПР – пробовали пакеты Anvil, Euclid, Proengineer.
Но какого-то системного подхода в этом направлении не было. Были энтузиасты своего дела и со стороны конструкторов, и со стороны работников УСАПР (с которыми в то время у меня сложились особенно тесные отношения).
При одной из встреч с начальником отдела УСАПР Ю. Колодяжным узнал от него, что предполагается заключение контракта на оснащение подразделений УПА графическими станциями IBMс лицензионным пакетом Catia.
Это делается для того, чтобы обеспечить кардинальное решение вопросов по качеству и скорости проектирования, исключить технические ошибки, вызванные ошибочными построениями, а также ошибками при изготовлении оснастки.
Нужна только тема, которая могла бы стать носителем и движителем этого процесса. Вот тут мы и предложили панель приборов 2123.
Вопрос о том, заниматься этим или нет, не стоял, была и тема, была и команда. Это были молодые ребята, в которых я был уверен на 100%: Ю. Карпов, В. Жуков, потом к ним присоединились А. Мавлоназаров, В. Кийко, В. Филиппов, И. Гончаров.
И, конечно, наш бывший начальник бюро В. Лылов, с его колоссальным опытом и золотыми человеческими качествами, который сам за графической станцией не работал, но резюме в решениях выдавал безошибочные, да и просто обеспечивал нам надёжный тыл, освобождая от рутинной, отвлекающей от проекта работы.
Это было замечательное чувство единой команды, понятной цели, уверенности в своих силах и ощущение всесторонней поддержки и доброжелательности.
Большую помощь оказывали нам П. Прусов и А. Москалюк.
Никто не знал, каким именно будет результат и успеем ли мы вообще в срок. С пакетом Catiaмы только начинали работать, никто из нас никогда не строил в этой системе сложных поверхностей, а строить было что!
Я-то был уверен, что результат будет, но и риск был велик. Это ведь не экспериментальный проект, это плановый полный проект с конкретными жёсткими сроками.
Разработка дизайн-проекта интерьера 2123была поручена молодому дизайнеру А. Плюхину. У меня до этого был опыт работы с ним, и эта работа всегда приносила удовольствие.
Алексей – один из немногих дизайнеров, который внимательно слушает оппонента (в данном случае – конструктора). И без вреда стилевому решению может дать вариант, устраивающий конструктора по технологии производства и сборке узла, исключающей возможные дефекты. Гибкий и творческий человек, с хорошим чувством юмора, что несомненно очень помогает в работе.
Итак, Алексей уже имел дизайн-проект интерьера, а мы уже сделали предварительную плановую проработку конструкции панели приборов.
Но тут такие возможности по использованию САПР!
Я познакомился с отличными ребятами из Москвы, которые работали на фирме IBMи как раз в это время продвигали свой продукт Catia.
Они изъявили готовность поработать с нами на этом пилотномпроекте, обучить, выявить и решить проблемные вопросы. И они действительно очень нам помогли.
Р. Сюняев, Н. Костерина, Ю. Колодяжный, начальник УСАПР В. Карпов, да и все, к кому приходилось обращаться в УСАПР, с полной отдачей помогали в работе. Я не помню случая в то время, когда возникающая техническая или иная проблема не решалась бы ими в самое кратчайшее время.
Если мне не изменяет память, на разработку поверхности по данным А. Плюхина мы затратили чуть более месяца. Потом месяц её дорабатывали, а разработку конструкции закончили уже через 3 месяца.
Для того времени это было быстро, но, если учитывать, что начали с нуля– это была первая победа! Мы впервые имели полностью разработанную на компьютере панель приборов с её очень сложной поверхностью и полным объёмом математических моделей.
Следует заметить, что впервые в нашей практике это была модульная конструкция панели приборов с оригинальной системой отопления, которую проектировали А. Свиридов, С. Ласточкин, А. Чухарев, А. Лукин и начальник КБ А. Альтгаузен.
А тут ещё мы впервые получили возможность изготовления прототипных деталей с применением новейших в то время средств быстрого прототипирования.
Я уже говорил, какими методами и с какими трудностями проходило изготовление оснастки для прототипов, а затем и самих прототипов.
Слух о том, что мы полностью имеем матмодель для этой панели приборов, достиг в то время директора ОПП С. Перевезенцева. Кто знает этого человека, тому не нужно много о нём рассказывать.
Человек неуёмной энергии и зачастую невероятно фантастических идей, он, тем не менее, находил способ их воплощать в жизнь (бывало, через потери и ошибки). Но то, что без Перевезенцева ничего бы не произошло того, о чём пойдёт речь далее, – это факт.
Итак, приглашает он меня как-то к себе в кабинет на совещание, не предупреждая о теме.
Слушаю и ничего не понимаю. Он предлагает изготовить прототип панели приборов со всеми входящими деталями, главной из которых должен был быть каркас. До этого подобные каркасы изготавливались с помощью вакуумного формования, но качество и свойства не выдерживали никакой критики. А его предложение – практически литая деталь.
Он понял моё недоумение и, оставив после совещания, познакомил с молодыми ребятами из вновь образованной лаборатории ИЦ, которую возглавлял А. Басаев. Я раньше его не знал и в лаборатории не был.
То что мне показали ребята: А. Басаев, К. Чучадеев, И. Макушин, меня откровенно потрясло.


По первому варианту панели приборов 2123было много замечаний, особенно по конфигурации поручня пассажира (отмечен стрелкой).