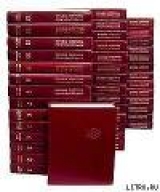
Текст книги "Большая Советская Энциклопедия (МЕ)"
Автор книги: Большая Советская Энциклопедия
Жанр:
Энциклопедии
сообщить о нарушении
Текущая страница: 78 (всего у книги 105 страниц)
«Металлург»
«Металлу'рг», ежемесячный производственно-массовый журнал министерства чёрной металлургии СССР и ЦК профсоюза рабочих металлургической промышленности. Выходит в Москве с 1956. Переиздаётся на английском языке в США. Освещает вопросы внедрения новой техники и передовой технологии, механизации и автоматизации производства, модернизации оборудования и повышения производительности труда. Публикует материалы о передовиках производства чёрной металлургии, по экономике и технике безопасности отрасли, о работе творческих объединений и др. Тираж (1974) 23 тыс. экземпляров.
Металлургии институт
Металлу'рги'и институ'т им. А. А. Байкова Академии наук СССР, научно-исследовательское учреждение, ведущее работы по металлургии, металловедению и обработке чёрных, цветных и редких металлов и сплавов. Создан в Москве в 1938. Изучает физико-химические основы процессов получения металлов и сплавов, в том числе новых металлических материалов со специальными свойствами; разрабатывает эффективные процессы производства и обработки металлов. Результаты работ публикуются в сборниках института, монографиях, «Докладах АН СССР», «Известиях Академии наук СССР. Металлы», в журнале «Физика и химия обработки материалов» и др. В М. и. имеется аспирантура (институту дано право приёма к защите докторских и кандидатских диссертаций), своё СКБ, разрабатывающее приборы и установки для исследований в области металлургии. Организатором и первым директором института был академик АН СССР И. П. Бардин; в институте работали академики АН СССР А. А. Байков, Э. В. Брицке, Н. Т. Гудцов, М. М. Карнаухов, М. А. Павлов, А. М. Самарин, член-корреспондент АН СССР И. А. Одинг и др.
Металлургическая печь
Металлурги'ческая печь, тепловой агрегат для выплавки металлов и сплавов, нагрева слитков и заготовок перед прокаткой, термической обработки прокатной продукции и др. целей. См. Печь .
Металлургическое машиностроение
Металлурги'ческое машинострое'ние, см. в ст. Тяжёлое машиностроение .
Металлургическое образование
Металлурги'ческое образова'ние, отрасль технического образования , имеющая целью подготовку инженеров и техников различного профиля по выплавке чёрных и цветных металлов и сплавов, по обработке их давлением, металловедению, металлофизике, термической обработке металлов, литейному производству, экономике и организации металлургического производства и др.
История и развитие М. о. тесно связаны с горным образованием . В России в 18—19 вв. квалифицированные рабочие и мастера-металлурги готовились в горнозаводских школах и горных училищах. Наиболее высокий уровень подготовки (соответствующий квалификации техника) был достигнут в Уральском горном, Пермском реальном (на горнопромышленном отделении), Нижнетагильском горнозаводском, Домбровском горном училищах и в горном училище Полякова в Горловке.
Высшее М. о. возникло в России во 2-й половине 18 в., когда в 1773 в Петербурге открылось Горное училище, переименованное впоследствии в Горный институт. В течение столетия Горный институт являлся единственным горно-металлургическим вузом России. Из него вышли выдающиеся учёные, внёсшие большой вклад в развитие отечественной металлургии: П. П. Аносов, Н. А. Курнаков, М. А. Павлов и др. В 1834 преподавателями института была организована в Петербурге Горная школа для подготовки техников-металлургов (один из выпускников этой школы Д. К. Чернов стал впоследствии основоположником металловедения).
Металлургические знания впервые начали сообщаться в Петербургском горном институте в курсе «Наставление учителю химического класса». В этом курсе металлургия была составной частью химии; в 1804 курс металлургии стал самостоятельной дисциплиной. Позднее в Горном институте выделились как самостоятельные горное и заводское отделения (на заводском отделении, которое давало высшее М. о., читались курсы физической химии и металлургии). С развитием горнозаводской промышленности на юге России открылись новые специальные учебные заведения. В 1899 в Екатеринославе (ныне Днепропетровск) основано Высшее горное училище, в котором преподавалась металлургия (в 1921 преобразовано в Горный институт им. Артема, из которого в 1930 выделился Днепропетровский металлургический институт ); в 1898 в Киеве открылся политехнический институт, где готовились и инженеры-технологи по металлургии. В начале 20 в. созданы Томский технологический (1900), Петербургский политехнический (1902) и Новочеркасский политехнический (1907) институты. где также осуществлялась подготовка инженеров-металлургов. Известная научная металлургическая школа сложилась в Петербургском политехническом институте, в котором преподавали виднейшие учёные-металлурги А. А. Байков, М. А. Павлов, В. Е. Грум-Гржимайло и др.
Бурное развитие металлургии и М. о. началось после Октябрьской революции 1917. В 1918 в Москве открылась Горная академия, в составе которой был и металлургический факультет; в 1930 на базе факультетов академии созданы Московский институт стали (ныне Московский институт стали и сплавов ) и Московский институт цветных металлов и золота (см. в ст. Красноярский институт цветных металлов ). В период индустриализации страны для подготовки специалистов-металлургов организованы металлургический и горно-металлургический институты: Сибирский (в Новокузнецке, 1930), Мариупольский (ныне Ждановский, 1930), Московский вечерний (1931), Северокавказский (в Орджоникидзе, 1931), Магнитогорский (1932) и др., а также несколько металлургических техникумов.
Строительство крупных металлургических заводов, оснащенных современной техникой, потребовало не только увеличения числа инженеров, но и улучшения их подготовки. В 1937 были пересмотрены учебные планы металлургических институтов и установлены 3 основные специальности: металлургия чёрных металлов (доменное, сталеплавильное и литейное производство); пластическая и термическая обработка металлов (прокатное производство, ковка, штамповка и термическая обработка); механическое оборудование металлургических цехов. В учебном планы включены новые дисциплины: теория металлургических процессов, металлургические печи, огнеупорные материалы, металлургия чугуна и стали, обработка металлов давлением, рентгенография и испытание металлов, экономика металлургии, техника безопасности и др.
Система современного М. о. в СССР основана на органическом соединении теоретического обучения с практической подготовкой будущих специалистов. Теоретический фундамент М. о. составляют физико-математические и химические науки, механика (теоретическая и прикладная), металловедение, теория металлургических процессов, электроника, экономика и др. Все студенты изучают марксистско-ленинскую теорию. В учебные планы старших курсов включены специальные дисциплины, определяющие специализацию в области металлургии.
В соответствии с требованиями научно-технической революции и новыми задачами коммунистического строительства в вузах расширено изучение фундаментальных наук, новых курсов: научной организации труда, автоматизированных систем управления, электронно-вычислительных машин и их практическое применения в металлургии, инженерной психологии и др. Широкое привлечение студентов к участию в научных исследованиях, а также введение учебной научно-исследовательской практики стали одними из основных методов воспитания творческого специалиста.
Современное М. о. имеет стройную систему специальностей и отражает состояние металлургической промышленности и науки. В связи с потребностями народного хозяйства, науки и техники введены новые специальности: физика металлов, физико-химические исследования металлургических процессов, автоматизация и комплексная механизация металлургической промышленности, производство чистых металлов и полупроводниковых материалов, кибернетика металлургического производства, физические методы пыле– и газоулавливания на металлургических предприятиях. Срок обучения в металлургических вузах (факультетах) – 5—5,5 лет.
В 1973 подготовка инженеров-металлургов в СССР осуществлялась в металлургическом и горно-металлургическом институтах Москвы, Днепропетровска, Жданова, Красноярска, Магнитогорска, Орджоникидзе, Новокузнецка, в Коммунарском горно-металлургическом институте (основан в 1958 в Коммунарске Ворошиловградской области), а также в Ленинградском горном институте, на металлургических факультетах Ленинградского, Уральского (Свердловск), Челябинского, Иркутского, Киевского, Донецкого, Казахского (Алма-Ата), Карагандинского, Грузинского (Тбилиси), Липецкого политехнического институтов, Днепродзержинского индустриального института (в большинстве этих вузов имеются дневные, вечерние и заочные отделения), Норильского и Краматорского вечерних индустриальных институтов, Всесоюзного (Москва), Северо-Западного (Ленинград) и Украинского (Харьков) заочных политехнических институтов, на заводе-втузе при Карагандинском металлургическом комбинате (Темиртау), в Московском вечернем металлургическом институте.
Подготовка техников-металлургов осуществляется в СССР по широкой номенклатуре специальностей в горно-металлургическом и металлургическом техникумах Свердловска, Первоуральска, Серова, Москвы, Челябинска, Златоуста, Днепродзержинска, Никополя, Днепропетровска, Кривого Рога, Енакиева, Макеевки, Запорожья и др., а также в индустриальных техникумах Новокузнецка, Златоуста, Днепропетровска и др. Срок обучения – 4 года (см. Среднее специальное образование ). В 1972/73 учебном году на специальностях М. о. обучалось: в вузах 54,5 тыс. человек, в техникумах – 48,5 тыс. человек; приём соответственно составил: в вузах – 11,6 тыс. человек, в техникумах – 14,9 тыс. человек; выпуск – 8 тыс. человек и 11,2 тыс. человек. Педагогические и научные кадры в области металлургии готовятся в аспирантуре, организованной в более чем 30 металлургических, горно-металлургических, политехнических, индустриальных втузах и научно-исследовательских учреждениях. Московского институту стали и сплавов, Днепропетровскому и Магнитогорскому им. Г. И. Носова металлургическим институтам предоставлено право принимать к защите докторские и кандидатские диссертации, Московскому вечернему, Северокавказскому и Сибирскому им. Серго Орджоникидзе институтам – кандидатские. Квалифицированных рабочих для металлургической промышленности (горновые доменных печей, подручные сталеваров, вальцовщики, плавильщики и др.) выпускают профессионально-технические учебные заведения (см. также Профессионально-техническое образование ).
Существенный вклад в развитие металлургии и М. о. внесли известные советские учёные И. П. Бардин, Б. В. Старк, М. М. Карнаухов. А. Н. Вельский, А. М. Самарин, В. П. Елютин, А. А. Бочвар и др.
В др. социалистических странах подготовка металлургов осуществляется: в ГДР – во Фрейбергской горной академии, в Дрезденской высшей технической школе; в Польше – в Краковской горно-металлургической академии, Варшавском и Познанском политехническом институтах; в Чехословакии – в Горно-металлургической школе (Острава), в Высшей технической школе (Кошице); в Венгрии – в Будапештском политехническом институте; в Болгарии – в Софийском химико-технологическом институте.
В капиталистических странах М. о., как правило, осуществляется в инженерных колледжах или на металлургических факультетах, входящих в состав университетов. Важнейшими центрами М. о. являются: в США – Массачусетсский технологический институт (Кембридж), Технологический институт Карнеги (Питсбург), металлургические факультеты и колледжи Гарвардского, Нью-Йоркского, Колумбийского, Чикагского и др. университетов; в Великобритании – металлургические факультеты и колледжи университетов Кембриджа, Бирмингема, Манчестера, Лидса и Шеффилда; в ФРГ – Горная академия в Клаустале, высшие технические школы в Ахене, Кельне, Гамбурге и др.; во Франции – Центральные научно-исследовательские институты металлургии в Париже и Сент-Этьенне, Высшая национальная школа электрохимии и электрометаллургии в Гренобле и др. В развивающихся странах М. о. осуществляют: в Индии – Бомбейский, Кхарагпурский и Канпурский технологический институты, Бенгальский инженерный колледж, инженерные колледжи в Пуне и Варанаси; Бирме – Рангунский технологический институт; АРЕ – Каирский университет, Эт-Таббинский металлургический институт; Алжире – Аннабский горно-металлургический институт и др.
Лит.: Высшие учебные заведения горной и металлургической промышленности СССР, М., 1948; Полухин П. И., О подготовке специалистов-металлургов в США, «Вестник высшей школы», 1958, № 3; его же, Новый этап в развитии советской высшей школы, М., 1960; его же, Высшее металлургическое образование в СССР за 50 лет, «Известия вузов. Чёрная металлургия», 1967, № 10; Веселова А. Н., Среднее профессионально-техническое образование в дореволюционной России, М., 1959. См. также лит. при ст. Горное образование .
П. И. Полухин.
«Металлургия»
«Металлу'рги'я», центральное издательство Государстввенного комитета Совета Министров СССР по делам издательств, полиграфии и книжной торговли, выпускающее литературу по чёрной и цветной металлургии. Основано в 1939 в Москве как Металлургиздат, с 1963 – «М.». Издаёт научно-техническую, производственно-техническую, справочную, учебную и др. литературу, а также каталоги, плакаты; 7 журналов, в том числе «Сталь» , «Цветные металлы» и др. В 1973 книжная продукция издательства составила 207 названий тиражом 1,7 млн. экземпляров, объёмом 21 400 тыс. печатных листов-оттисков.
В. П. Адрианова.
Металлургия
Металлурги'я (от греч. metallurgéo – добываю руду, обрабатываю металлы, от métallon – рудник, металл и érgon – работа), в первоначальном, узком значении – искусство извлечения металлов из руд; в современном значении – область науки и техники и отрасль промышленности, охватывающие процессы получения металлов из руд или др. материалов, а также процессы, связанные с изменением химического состава, структуры, а следовательно, и свойств металлических сплавов. К М. относятся: предварительная обработка добытых из недр земли руд, получение и рафинирование металлов и сплавов; придание им определённой формы и свойств.
В современной технике исторически сложилось разделение М. на чёрную и цветную. Чёрная металлургия охватывает производство сплавов на основе железа: чугуна , стали , ферросплавов (на долю чёрных металлов приходится около 95% всей производимой в мире металлопродукции). Цветная металлургия включает производство большинства остальных металлов (см. Металлы в технике). В связи с использованием атомной энергии развивается производство радиоактивных металлов. Металлургические процессы применяются также для производства полупроводников и неметаллов (кремний, германий, селен, теллур, мышьяк, фосфор, сера и др.); некоторые из них получают попутно с извлечением металлов. В целом современная М. охватывает процессы получения почти всех элементов периодической системы, за исключением галоидов и газов.
Возникновение М., как показывают археологические находки, относится к глубокой древности (см. рис. 1 ). Обнаруженные в 50—60-х гг. 20 в. в юго-западной части Малой Азии следы выплавки меди датируются 7—6-м тыс. до н. э. Примерно в это же время человек познакомился с самородными металлами: золотом, серебром, медью, а затем и с метеоритным железом. Сначала металлические изделия изготовляли путём обработки металлов в холодном состоянии. Медь и железо с трудом подвергались такой обработке и поэтому не могли найти широкого применения. После изобретения горячей кузнечной обработки (ковки) медные изделия получили более широкое распространение (эпоха энеолита ). Овладение искусством выплавки меди из окисленных медных руд и придания ей нужной формы литьём (5—4 тыс. до н. э.) привело к быстрому росту производства меди и к значительному расширению её применения. Однако ограниченное количество месторождений окисленных медных руд обусловило необходимость освоения гораздо более сложного процесса переработки сульфидных руд с применением предварительного обжига руды и рафинирования меди путём повторного плавления. Возникновение этого процесса относится примерно к середине 2-го тыс. до н. э. (Ближний Восток, Центральная Европа).
Во 2-м тыс. до н. э. начали широко применяться изделия из бронзы (сплава меди с оловом), которые по качеству значительно превосходили медные. Бронзовые орудия труда, оружие и др. предметы отличались большей устойчивостью против коррозии, упругостью, твёрдостью, остротой лезвия. Кроме того, бронза имела более низкую температуру плавления, чем медь, и лучше заполняла литейную форму. Из неё легче было отливать всевозможные изделия. Вытеснение меди бронзой означало переход к бронзовому веку . В конце 3-го и во 2-м тыс. до н. э. крупным центром М. меди и бронзы на территории СССР был Кавказ.
Примерно в середине 2-го тыс. до н. э. человек начинает овладевать и искусством получения железа из руд. Сначала для этой цели использовали костры, а затем специальные плавильные ямы – сыродутные горны (см. Сыродутный процесс ). В горн, выложенный из камня, загружали легковосстановимую руду и древесный уголь. Дутьё, необходимое для горения угля, подавалось в горн снизу (первое время естественной тягой, а впоследствии при помощи мехов). Образующиеся газы (окись углерода) восстанавливали окислы железа. Относительно низкая температура процесса и большое количество железистого шлака препятствовали науглероживанию металла и позволяли получать железо только с низким содержанием углерода. Процесс был малопроизводительным и обеспечивал извлечение из руды лишь около половины содержащегося в ней железа. М. железа развивалась очень медленно, несмотря на то, что железные руды гораздо более распространены, чем медные, а температура их восстановления ниже. Причина первоочередного развития М. меди заключается в том, что сыродутное железо по качеству значительно уступало меди. Это объясняется прежде всего тем, что при достижимых в то время температурах процесса медь получалась в расплавленном состоянии, а железо – в виде тестообразной массы с многочисленными включениями шлака и несгоревшего древесного угля. В связи с низким содержанием углерода сыродутное железо было мягким – изготовленные из него оружие и орудия труда быстро затуплялись, гнулись, не подвергались закалке; они уступали по качеству бронзовым. Для перехода к более широкому производству и применению железа необходимо было усовершенствовать примитивный сыродутный процесс, а главное – овладеть процессами науглероживания железа и его последующей закалки, т. с. получения стали. Эти усовершенствования обеспечили железу в 1-м тыс. до н. э. главенствующее положение среди материалов, используемых человеком (см. Железный век ). К началу н. э. М. железа была почти повсеместно распространена в Европе и Азии.
На протяжении почти 3 тысячелетий М. железа не претерпела принципиальных изменений. Постепенно процесс совершенствовался: увеличивались размеры сыродутных горнов, улучшалась их форма, повышалась мощность дутья; в результате горны превратились в небольшие печи для производства сыродутного железа – домницы (рис. 2 ). Дальнейшее увеличение размеров домниц привело в середине 14 в. к появлению небольших доменных печей (см. Доменное производство ). Увеличение высоты этих печей и более интенсивная подача дутья способствовали повышению температуры и значительно более сильному развитию процессов восстановления и науглероживания металла. Вместо тестообразной массы сыродутного железа в доменных печах получали уже высокоуглеродистый железный расплав с примесями кремния и марганца – чугун. Росту производства чугуна способствовало изобретение в 14 в. способа передела его в ковкое железо – т. н. кричного передела . Переплавляя чугун в кричном горне, его рафинировали от примесей путём окисления их кислородом дутья и специально загружаемого в горн железистого шлака. Кричный процесс постепенно вытеснил прежние малопроизводительные способы получения стали на основе сыродутного железа, несмотря на достигнутое с их помощью чрезвычайно высокое качество металла (см. Булат , Дамасская сталь ). Т. о., возник двухстадийный способ получения железа, сохранивший своё значение и являющийся основой современных схем производства стали. Следующим этапом развития М. стали в Европе было появление в Англии в 1740 тигельной плавки (задолго до того известной на Востоке) и в последней четверти 18 в. – пудлингования . Тигельный процесс был первым способом производства литой стали . Её выплавляли в тиглях из огнеупорной глины, которые устанавливались в специальной печи. В пудлинговом процессе, как и в кричном, получали т. н. сварочное железо. Для этого чугун рафинировали от углерода и др. примесей на поду отражательной печи.
Несмотря на большое значение для развития техники своего времени, тигельный и пудлинговый процессы не могли удовлетворить потребности в стали. М. чугуна развивалась опережающими темпами. Этому способствовало внедрение водяных воздуходувных труб (рис. 3 ), мехов с приводом от водяного колеса (с 15 в.), паровых воздуходувных машин (1782). В конце 18 в. в доменном производстве начали широко использовать каменноугольный кокс (1735); к 19 в. относится начало применения нагретого дутья и тщательной подготовки руды к доменной плавке. Отставание сталеплавильного производства проявлялось в том, что количество выплавляемого чугуна долгое время (до начала 20 в.) превышало количество производимой стали. Главная роль в наступившем переломе сыграло изобретение трёх новых процессов производства литой стали: в 1856 – бессемеровского процесса , в 1864 – мартеновского (см. Мартеновское производство ) и в 1878 – томасовского процесса . Распространение этих процессов (в первую очередь мартеновского, которому свойственно использование большого количества металлического лома) привело к тому, что к середине 20 в. выпуск чугуна составлял уже только 70% от выплавки стали.
Дальнейшее развитие сталеплавильного производства во 2-й половине 20 в. связано с существенным увеличением ёмкости и производительности агрегатов, широким применением кислорода для повышения эффективности металлургических процессов, появлением нового, быстро развивающегося способа получения стали в кислородных конвертерах (см. Кислородно-конвертерный процесс ), с развитием внепечного рафинирования жидкой стали в вакууме, обработки стали синтетическими шлаками и инертным газом, с внедрением непрерывной разливки стали , широкой механизацией и автоматизацией производственных процессов. Большое значение в современной М. железа имеет выплавка высококачественной и в том числе легированной стали , которая с начала 20 в. производится в основном в электропечах (см. Электросталеплавильное производство ). Со 2-й половины 20 в. для получения некоторых цветных металлов, а также стали особо ответственные назначения начали применять дополнительный переплав металла в дуговых вакуумных печах , электрошлаковых, электроннолучевых и плазменных установках (см. Электрошлаковый переплав , Электроннолучевая плавка , Плазменная металлургия ). В области извлечения железа из руд наряду с доменным производством, которое продолжает расширяться, развиваются разнообразные способы прямого получения железа . Этим процессам, позволяющим получать железо, пригодное для выплавки стали в электропечах, принадлежит большое будущее.
Кроме железа, в древнем мире добывали и применяли золото, серебро, медь, олово, свинец, ртуть. Многие др. металлы (в т. ч. неизвестные древним) использовались в сплавах, минералах или соединениях.
Золото в виде песка и самородков добывали в доисторические времена из россыпей путём промывки. Для получения изделий золотой песок подвергали горячей ковке (кузнечной сварке) или переплавляли в тиглях. При этом обычно получали сплавы золота с серебром и др. элементами, что обусловливало разнообразные вариации цвета, а также литейных и механических свойств металла. Рафинирование золота и отделение его от серебра началось во 2-й половине 2-го тыс. до н. э., но до 6 в. до н. э. распространялось довольно медленно. Удаление примесей (вместе со свинцом, добавляемым для улучшения процесса) производили путём окисления их воздухом. Отделение серебра осуществляли путём хлорирования сплава при нагреве в присутствии поваренной соли, с последующей отгонкой летучих хлоридов или их растворением. Др. способ отделения серебра заключался в переводе его в сульфиды при нагревании сплава с сернистыми материалами и древесным углём. Применение азотной кислоты для отделения серебра от золота относится уже к 13—14 вв. Процесс амальгамации также был известен в древнем мире, но уверенности в том, что он применялся для извлечения золота из руд и песков, нет. После открытия русским учёным П. Р. Багратионом в 1843 основ цианирования золотых руд и особенно после работ английских металлургов Дж. С. Мак-Артура и бр. Р. и У. Форрестов (1887—88) этот процесс занял ведущее место в М. золота; иногда он используется в соединении с амальгамацией. Успешно применяется для извлечения золота флотационное (см. флотация ) и гравитационное обогащение .
Серебро в древности получали главным образом попутно со свинцом из галенита. Начало их совместной выплавки можно отнести к 3-му тыс. до н. э. (Малая Азия); широкое распространение процесс получил только через 1500—2000 лет. Можно полагать, что технологическая схема включала в себя обжиг руды, горновую плавку, разделительную плавку (ликвационное рафинирование, зейгерование ) и купеляцию . Во 2-й половине 20 в. свинец получают преимущественно из полиметаллических руд в результате флотационного обогащения, агломерирующего обжига, восстановительной плавки в шахтных печах и рафинирования продукта этой плавки – чернового свинца (веркблея ). При рафинировании извлекается также серебро (и золото, если оно есть).
Массовое производство меди началось после изобретения В. А. Семенниковым в 1866 конвертирования штейна. Большую роль в развитии конвертерной переработки штейна сыграла предложенная в 1880 продувка расплава сбоку (а не снизу, как в бессемеровском способе получения стали из чугуна). При боковой продувке воздух поступает непосредственно в рафинируемый расплав, минуя легко затвердевающую медь, которая собирается на дне конвертера. Огромное значение для массового производства меди имело изобретённое на рубеже 20 в. флотационное обогащение, позволившее успешно перерабатывать руды с содержанием меди менее 1%. Нефлотирующиеся бедные окисленные руды (менее 0,7% Cu) обрабатывают гидрометаллургическим способом (путём выщелачивания ). Сульфидные руды можно выщелачивать в самом месторождении (без добычи руды), используя способ интенсификации выщелачивания с применением бактерий (см. Бактериальное выщелачивание ).
Олово в древности выплавляли в простейших шахтных печах, а затем очищали от посторонних примесей посредством ликвационных и окислительных процессов. Коренные оловянные руды перед плавкой подвергали дроблению и простейшему обогащению; из россыпей руду добывали промывкой. В современной М. в связи с необходимостью использования бедных оловянных руд со значительным содержанием примесей (сера, мышьяк, сурьма, висмут, серебро и др.) олово получают по сложным схемам комплексной переработки руд, которые включают в себя обогащение, обжиг, выщелачивание примесей из рудных концентратов, магнитную сепарацию их, восстановительную плавку в отражательных, шахтных или электрических (лучший способ) печах с получением чернового олова и рафинирование его главным образом пирометаллургическим (иногда электролитическим) методом.
Первые способы производства ртути сводились, по-видимому, к обжигу руды в кучах; ртуть конденсировалась при этом на холодных предметах. Позднее появилась керамического реторта. Методы получения ртути, описанные немецким учёным Г. Агриколой (16 в.), сводятся к обжигу руды в керамических сосудах с различными конденсаторами. Железные реторты появились в 17 в. (1641). Затем по мере роста спроса на ртуть получили применение более производительных шахтные печи (периодического, а позднее и непрерывного действия), отражательные печи (с 1842), трубчатые вращающиеся печи (с начала 20 в.), которые служат основным агрегатом для переработки ртутных руд. Перспективный способ получения ртути – переработка руд в кипящего слоя печах , успешно освоенная в СССР.
Технологические схемы процессов получения остальных металлов, производство которых достигло значительного уровня только в течение последних столетий (а иногда и лет), освещаются в соответствующих статьях (см. Алюминий , Цинк , Марганец , Хром , Никель , Магний и др.).
Современная М. как совокупность основных технологических операций производства металлов и сплавов включает в себя: 1) подготовку руд к извлечению металлов (в т. ч. обогащение); 2) процессы извлечения и рафинирования металлов: пирометаллургические, гидрометаллургические, электролитические; 3) процессы получения изделий из металлических порошков путём спекания; 4) кристаллофизические методы рафинирования металлов и сплавов; 5) процессы разливки металлов и сплавов (с получением слитков или отливок); 6) обработку металлов давлением; 7) термическую, термомеханическую, химико-термическую и др. виды обработки металлов для придания им соответствующих свойств; 8) процессы нанесения защитных покрытий.
С М. тесно связаны коксохимическая промышленность , производство огнеупоров и ряд др. отраслей промышленности.
Подготовка руд к извлечению металлов начинается с дробления , измельчения , грохочения и классификации (см. Классификатор ). Следующая стадия обработки – обогащение (см. Обогащение полезных ископаемых ). В процессе обогащения или после него материалы подвергают обычно обжигу или сушке. Весьма перспективен обжиг в кипящем слое. Наибольшее применение в обогатительной технике имеют флотационные, гравитационные, магнитные и электрические методы. Флотационными процессами перерабатывают более 90% всех обогащаемых руд цветных и редких металлов. Из гравитационных процессов распространены обогащение в тяжёлых средах, отсадка, концентрация на столах и др. методы.
Большое значение обогатительных процессов в современной М. обусловлено стремлением к повышению эффективности металлургического производства, а также тем, что по мере роста выплавки металлов приходится использовать всё более бедные руды. Непосредственная металлургическая переработка таких руд (без обогащения), как правило, неэкономична, а в некоторых случаях даже невозможна.