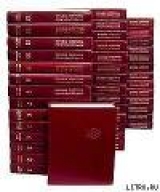
Текст книги "Большая Советская Энциклопедия (МЕ)"
Автор книги: Большая Советская Энциклопедия
Жанр:
Энциклопедии
сообщить о нарушении
Текущая страница: 100 (всего у книги 105 страниц)
Механическая запись
Механи'ческая за'пись звука, система записи звука посредством изменения формы носителя при механическом воздействии на него. М. з. является первой практической системой звукозаписи. Ещё в начале 19 в. при исследовании звуковых сигналов физики стали записывать колебания некоторых источников звука. Эти записи предназначались только для визуального изучения и не могли быть воспроизведены. В 1877 французский учёный Ш. Кро впервые научно обосновал принципы записи звука на барабан (или диск) и её последующего воспроизведения. Первым аппаратом механической записи и воспроизведения звука был фонограф (заявка на изобретение 1877) американского изобретателя Т. Эдисона . Его фонограф с восковым валиком не получил широкого распространения ввиду сложности копирования записи, быстрого изнашивания валиков и плохого качества воспроизведения. В 1888 немецкий инженер Э. Берлинер предложил использовать для записи носитель в форме диска. После записи с диска гальваническим способом получали матрицы, которые использовались для прессования граммофонных пластинок . До 50-х гг. 20 в. М. з. была монофонической (см. Монофоническая звукозапись ). В дальнейшем получила распространение также стереофоническая М. з., обеспечивающая лучшее качество звучания (см. Стереофоническая звукозапись ). В начале 70-х гг. 20 в. предложена квадрофоническая М. з., в которой звуковые сигналы, передаваемые по 4 независимым каналам, записываются в одной канавке диска. Такая запись воспроизводится 4 громкоговорителями, располагаемыми по углам комнаты.
Процесс М. з. делится на 3 этапа: перезапись с магнитной ленты на лаковый диск, изготовление матриц и прессование грампластинок. Установка для перезаписи на лаковый диск состоит из магнитофона, электронного устройства для усиления и коррекции электрических сигналов и станка записи (рис. ), имеющего движущий механизм, рекордер и устройство управления. Преобразование электрических сигналов в механические колебания осуществляется рекордером, резец которого вырезает на лаковом диске канавку, модулированную звуковым сигналом. Стереофонический рекордер имеет две (по числу каналов) независимые динамические системы, связанные с одним резцом. Сигналы каждого канала раздельно записываются на левую и правую стенки канавки. Для получения металлических оригиналов и матриц, с которых затем будут изготавливаться грампластинки, запись с лакового диска переносится гальванопластическим способом на металлические диски. Для этого лаковый диск сначала покрывают тонким слоем серебра, а затем – никелевой плёнкой, на которую наращивают слой меди. После отделения лакового диска получают первый оригинал. Аналогичным образом получают вторые оригиналы, с которых изготавливают никелевые матрицы . Эти матрицы прикрепляются к подогреваемым пресс-формам . Прессование грампластинок из синтетических материалов производится гидравлическими прессами.
Для воспроизведения М. з. служат электропроигрыватели . Преимущества М. з. – массовое тиражирование грампластинок, их относительная дешевизна и простота обращения, а также возможность надёжного хранения записи длительное время в металлических оригиналах (матрицах), основные недостатки – сравнительно быстрый износ грампластинки из-за непосредственного механического контакта граммофонной иглы с ней, невозможность монтажа и стирания записи.
Лит.: Калашников Л. А., Очерк развития техники механической записи звука, «Тр. института истории естествознания и техники», 1959, т. 26; Аполлонова Л. П., Шумова Н. Д., Механическая звукозапись, М. – Л., 1964; Волков-Ланнит Л. Ф., Искусство запечатленного звука, М., 1964.
Ю. А. Вознесенский.

Станок для механической звукозаписи: 1 – микроскоп для контроля качества записи; 2 – трубка отсоса воздуха из-под лакового диска; 3 – вращающаяся планшайба со стробоскопическими метками, по которым контролируется скорость вращения; 4 – каретка, обеспечивающая передвижение рекордера 5 при записи.
Механическая лопата
Механи'ческая лопа'та, 1) вид одноковшового экскаватора, характеризуемый жёсткой связью между стрелой и ковшом. М. л. выполняется в виде прямой либо обратной лопаты. Прямая лопата (рис. , а) применяется для земляных работ в строительстве, для вскрышных и добычных работ в карьерах, для выемки руды в камерах подземных рудников (крепкие горные породы предварительно рыхлятся взрывом). Строительная М. л. выпускаются обычно с ковшом ёмкостью до 3 м3 , карьерные – с ковшом 2—22 м3 , вскрышные – с ковшом до 150 м3 , подземные – с ковшом до 3 м3 . Прямая лопата выпускается в СССР с ковшами ёмкостью 0,25—35 м3 ; готовятся к выпуску М. л. с ковшом 100 м3 . В зависимости от условий работ годовая выработка М. л. составляет на 1 м3 ёмкости ковша 120—250 тыс. м3 , а расход энергии 0,4—0,8 квт ×ч/м3 . Обратная М. л. (рис. , б) отличается от прямой направлением рабочего движения ковша и применяется для проходки канав, траншей и др. вспомогательных работ, когда забой расположен ниже уровня установки экскаватора. Обратная лопата выпускается в СССР с ковшами ёмкостью 0,15—2 м3 . Производительность её примерно на 20 % меньше, чем прямой при той же ёмкости ковша. 2) Канатно-скреперная установка для выгрузки из крытых вагонов сыпучих грузов (зерна, цемента и т. п.).
В. Г. Афонин.

Механическая лопата: а – прямая; б – обратная; 1 – ковш; 2 – рукоять; 3 – стрела; 4 – кузов.
Механические музыкальные инструменты
Механи'ческие музыка'льные инструме'нты, инструменты, снабженные техническими приспособлениями для исполнения зафиксированных на дисках произведений или наигрышей без непосредственного участия музыкантов. М. м. и. бывают самых различных конструкций и форм – от маленьких примитивных табакерок, музыкальных шкатулок , часов-будильников до сложных по устройству стационарных напольных часов, полифонов, оркестрионов , башенных курантов , «озвученных» карет. Первые сведения о М. м. и. относятся к 16 в. Особенно много систем М. м. и. появилось, в том числе и в России, в конце 19 – начале 20 вв. Применялись они в трактирах, ресторанах, мещанско-купеческом быту. Широкое распространение в это время получила шарманка . С появлением граммофона, а затем радиомагнитофонной аппаратуры М. м. и. вышли из употребления. См. также Механическое фортепьяно .
Механические свойства материалов
Механи'ческие сво'йства материа'лов, совокупность показателей, характеризующих сопротивление материала воз действующей на него нагрузке, его способность деформироваться при этом, а также особенности его поведения в процессе разрушения. В соответствии с этим М. с. м. измеряют напряжениями (обычно в кгс/мм2 или Мн/м2 ), деформациями (в %), удельной работой деформации и разрушения (обычно в кгс ×м/см2 или Мдж/м2 ), скоростью развития процесса разрушения при статической или повторной нагрузке (чаще всего в мм за 1 сек или за 1000 циклов повторений нагрузки, мм/кцикл ). М. с. м. определяются при механических испытаниях образцов различной формы.
В общем случае материалы в конструкциях могут подвергаться самым различным по характеру нагрузкам (рис. 1 ): работать на растяжение , сжатие, изгиб , кручение , срез и т. д. или подвергаться совместному действию нескольких видов нагрузки, например растяжению и изгибу. Также разнообразны условия эксплуатации материалов и по температуре, окружающей среде, скорости приложения нагрузки и закону её изменения во времени. В соответствии с этим имеется много показателей М. с. м. и много методов механических испытаний. Для металлов и конструкционных пластмасс наиболее распространены испытания на растяжение, твёрдость , ударный изгиб; хрупкие конструкционные материалы (например, керамику, металлокерамику) часто испытывают на сжатие и статический изгиб; механические свойства композиционных материалов важно оценивать, кроме того, при испытаниях на сдвиг.
Диаграмма деформации. Приложенная к образцу нагрузка вызывает его деформацию . Соотношения между нагрузкой и деформацией описываются т. н. диаграммой деформации (рис. 2 ). Вначале деформация образца (при растяжении – приращение длины Dl ) пропорциональна возрастающей нагрузке Р , затем в точке n эта пропорциональность нарушается, однако для увеличения деформации необходимо дальнейшее повышение нагрузки Р ; при Dl > Dlв деформация развивается без приложения усилия извне, при постепенно падающей нагрузке. Вид диаграммы деформации не меняется, если по оси ординат откладывать напряжение
а по оси абсцисс – относительное удлинение
(F и l – соответственно начальная площадь поперечного сечения и расчётная длина образца).
Сопротивление материалов измеряется напряжениями, характеризующими нагрузку, приходящуюся на единицу площади поперечного сечения образца
в кгс/мм2 . Напряжение
при котором нарушается пропорциональный нагрузке рост деформации, называется пределом пропорциональности. При нагрузке Р < Рn разгрузка образца приводит к исчезновению деформации, возникшей в нём под действием приложенного усилия; такая деформация называется упругой. Небольшое превышение нагрузки относительно Рn может не изменить характера деформации – она по-прежнему сохранит упругий характер. Наибольшая нагрузка, которую выдерживает образец без появления остаточной пластической деформации при разгрузке, определяет предел упругости материала:
У конструкционных неметаллический материалов (пластмассы, резины) приложенная нагрузка может вызвать упругую, высокоэластическую и остаточную деформации. В отличие от упругой, высокоэластическая деформация исчезает не сразу после разгрузки, а с течением времени. Высокопрочные армированные полимеры (стеклопластики, углепластики и др.) разрушаются при удлинении 1—3%. На последних стадиях нагружения у некоторых армированных полимеров появляется высокоэластическая деформация. Высокоэластический модуль ниже модуля упругости, поэтому диаграмма деформации в этом случае имеет тенденцию отклоняться к оси абсцисс.
Упругие свойства. В упругой области напряжение и деформация связаны коэффициентом пропорциональности. При растяжении s = Еd, где Е – т. н. модуль нормальной упругости, численно равный тангенсу угла наклона прямолинейного участка кривой s = s(d) к оси деформации (рис. 2 ). При испытании на растяжение цилиндрического или плоского образца одноосному (s1 >0; (s2 = s3 = 0) напряжённому состоянию соответствует трёхосное деформированное состояние (приращение длины в направлении действия приложенных сил и уменьшение линейных размеров в двух других взаимно перпендикулярных направлениях): d1 >0; d2 = d3 < 0. Соотношение между поперечной и продольной деформацией (коэффициент Пуассона)
в пределах упругости для основных конструкционных материалов колеблется в довольно узких пределах (0,27—0,3 для сталей, 0,3—0,33 для алюминиевых сплавов). Коэффициент Пуассона является одной из основных расчётных характеристик. Зная m и Е , можно расчётным путём определить и модуль сдвига
и модуль объёмной упругости
Для определения Е, G , и m пользуются тензометрами .
Сопротивление пластической деформации. При нагрузках Р > Рв наряду со всё возрастающей упругой деформацией появляется заметная необратимая, не исчезающая при разгрузке пластическая деформация. Напряжение, при котором остаточная относительная деформация (при растяжении – удлинение) достигает заданной величины (по ГОСТ – 0,2 %), называется условным пределом текучести и обозначается
Практически точность современных методов испытания такова, что sп и sе определяют с заданными допусками соответственно на отклонение от закона пропорциональности [увеличение ctg(90 – a) на 25—50 %] и на величину остаточной деформации (0,003—0,05 %) и говорят об условных пределах пропорциональности и упругости. Кривая растяжения конструкционных металлов может иметь максимум (точка в на рис. 2 ) или обрываться при достижении наибольшей нагрузки Рв’ . Отношение
характеризует временное сопротивление (предел прочности) материала. При наличии максимума на кривой растяжения в области нагрузок, лежащих на кривой левее в , образец деформируется равномерно по всей расчётной длине l , постепенно уменьшаясь в диаметре, но сохраняя начальную цилиндрическую или призматическую форму. При пластической деформации металлы упрочняются, поэтому, несмотря на уменьшение сечения образца, для дальнейшей деформации требуется прикладывать всё возрастающую нагрузку. sв , как и условные s0,2 , sn и sе , характеризует сопротивление металлов пластической деформации. На участке диаграммы деформации правее в форма растягиваемого образца изменяется: наступает период сосредоточенной деформации, выражающейся в появлении «шейки». Уменьшение сечения в шейке «обгоняет» упрочнение металлов, что и обусловливает падение внешней нагрузки на участке Рв – Pk .
У многих конструкционных материалов сопротивление пластической деформации в упруго-пластической области при растяжении и сжатии практически одинаково. Для некоторых металлов и сплавов (например, магниевые сплавы, высокопрочные стали) характерны заметные различия по этой характеристике при растяжении и сжатии. Сопротивление пластической деформации особенно часто (при контроле качества продукции, стандартности режимов термической обработки и в др. случаях) оценивается по результатам испытаний на твёрдость путём вдавливания твёрдого наконечника в форме шарика (твёрдость по Бринеллю или Роквеллу), конуса (твёрдость по Роквеллу) или пирамиды (твёрдость по Виккерсу). Испытания на твёрдость не требуют нарушения целостности детали и потому являются самым массовым средством контроля механических свойств. Твёрдость по Бринеллю (HB) при вдавливании шарика диаметром D под нагрузкой Р характеризует среднее сжимающее напряжение, условно вычисляемое на единицу поверхности шарового отпечатка диаметром d :
Характеристики пластичности. Пластичность при растяжении конструкционных материалов оценивается удлинением
или сужением
при сжатии – укорочением
(где h и hk – начальная и конечная высота образца), при кручении – предельным углом закручивания рабочей части образца Q, рад или относительным сдвигом g = Qr (где r – радиус образца). Конечная ордината диаграммы деформации (точка k на рис. 2 ) характеризует сопротивление разрушению металла Sk , которое определяется
(Fk – фактическая площадь в месте разрыва).
Характеристики разрушения. Разрушение происходит не мгновенно (в точке k ), а развивается во времени, причём начало в разрушения может соответствовать какой-то промежуточной точке на участке вк , а весь процесс заканчиваться при постепенно падающей до нуля нагрузке. Положение точки к на диаграмме деформации в значительной степени определяется жёсткостью испытательной машины и иннерционностью измерительной системы. Это делает величину Sk в большой мере условной.
Многие конструкционные металлы (стали, в том числе высокопрочные, жаропрочные хромоникелевые сплавы, мягкие алюминиевые сплавы и др.) разрушаются при растяжении после значительной пластической деформации с образованием шейки. Часто (например, у высокопрочных алюминиевых сплавов) поверхность разрушения располагается под углом примерно 45° к направлению растягивающего усилия. При определенных условиях (например, при испытании хладноломких сталей в жидком азоте или водороде, при воздействии растягивающих напряжений и коррозионной среды для металлов, склонных к коррозии под напряжением) разрушение происходит по сечениям, перпендикулярным растягивающей силе (прямой излом), без макропластической деформации.
Прочность материалов, реализуемая в элементах конструкций, зависит не только от механических свойств самого металла, но и от формы и размеров детали (т. н. эффекты формы и масштаба), упругой энергии, накопленной в нагруженной конструкции, характера действующей нагрузки (статическая, динамическая, периодически изменяющаяся по величине), схемы приложения внешних сил (растяжение одноосное, двухосное, с наложением изгиба и др.), рабочей температуры, окружающей среды. Зависимость прочности и пластичности металлов от формы характеризуется т. н. чувствительностью к надрезу, оцениваемой обычно по отношению пределов прочности надрезанного и гладкого образцов
(у цилиндрических образцов надрез обычно выполняют в виде круговой выточки, у полос – в виде центрального отверстия или боковых вырезов). Для многих конструкционных материалов это отношение при статической нагрузке больше единицы, что связано со значительной местной пластической деформацией в вершине надреза. Чем острее надрез, тем меньше локальная пластическая деформация и тем больше доля прямого излома в разрушенном сечении. Хорошо развитый прямой излом можно получить при комнатной температуре у большинства конструкционных материалов в лабораторных условиях, если растяжению или изгибу подвергать образцы массивного сечения (тем толще, чем пластичнее материал), снабдив эти образцы специальной узкой прорезью с искусственно созданной трещиной (рис. 3 ). При растяжении широкого, плоского образца пластическая деформация затруднена и ограничивается небольшой областью размером 2ry (на рис. 3 , б заштрихована), непосредственно примыкающей к кончику трещины. Прямой излом обычно характерен для эксплуатационных разрушений элементов конструкций.
Широкое распространение получили предложенные американским учёным Дж. Р. Ирвином в качестве констант для условий хрупкого разрушения такие показатели, как критический коэффициент интенсивности напряжений при плоской деформации K1C и вязкость разрушения
При этом процесс разрушения рассматривается во времени и показатели K1C (G1C ) относятся к тому критическому моменту, когда нарушается устойчивое развитие трещины; трещина становится неустойчивой и распространяется самопроизвольно, когда энергия, необходимая для увеличения её длины, меньше энергии упругой деформации, поступающей к вершине трещины из соседних упруго напряжённых зон металла.
При назначении толщины образца t и размеров трещины 2lтр исходят из следующего требования
Коэффициент интенсивности напряжений К учитывает не только значение нагрузки, но и длину движущейся трещины:
(l учитывает геометрию трещины и образца), выражается в кгс/мм3/2 или Мн/м3/2 . По K1C или G1C можно судить о склонности конструкционных материалов к хрупкому разрушению в условиях эксплуатации.
Для оценки качества металла весьма распространены испытания на ударный о изгиб призматических образцов, имеющих на одной стороне надрез. При этом оценивают ударную вязкость (в кгс ×м/см2 или Мдж/м2 ) – работу деформации и разрушения образца, условно отнесённую к поперечному сечению в месте надреза. Широкое распространение получили испытания на ударный изгиб образцов с искусственно полученной в основании надреза трещиной усталости. Работа разрушения таких образцов ату находится в целом в удовлетворительном соответствии с такой характеристикой разрушения, как K1C , и ещё лучше с отношением
Временна'я зависимость прочности. С увеличением времени действия нагрузки сопротивление пластической деформации и сопротивление разрушению понижаются. При комнатной температуре у металлов это становится особенно заметным при воздействии коррозионной (коррозия под напряжением) или др. активной (эффект Ребиндера) среды. При высоких температурах наблюдается явление ползучести , т. е. прироста пластической деформации с течением времени при постоянном напряжении (рис. 4 , а). Сопротивление металлов ползучести оценивают условным пределом ползучести – чаще всего напряжением, при котором пластическая деформация за 100 ч достигает 0,2 %, и обозначают его s0,2/100 . Чем выше температура t , тем сильнее выражено явление ползучести и тем больше снижается во времени сопротивление разрушению металла (рис. 4 , б). Последнее свойство характеризуют т. н. пределом длительной прочности, т. е. напряжением, которое при данной температуре вызывает разрушение материала за заданное время (например, st100 , st1000 и т. д.). У полимерных материалов температурно-временная зависимость прочности и деформации выражена сильнее, чем у металлов. При нагреве пластмасс наблюдается высокоэластическая обратимая деформация; начиная с некоторой более высокой температуры развивается необратимая деформация, связанная с переходом материала в вязкотекучее состояние. С ползучестью связано и др. важное механическое свойство материалов – склонность к релаксации напряжений, т. е. к постепенному падению напряжения в условиях, когда общая (упругая и пластическая) деформация сохраняет постоянную заданную величину (например, в затянутых болтах). Релаксация напряжений обусловлена увеличением доли пластической составляющей общей деформации и уменьшением её упругой части.
Если на металл действует нагрузка, периодически меняющаяся по какому-либо закону (например, синусоидальному), то с увеличением числа циклов N нагрузки его прочность уменьшается (рис. 4 , в) – металл «устаёт». Для конструкционной стали такое падение прочности наблюдается до N = (2—5) ×106 циклов. В соответствии с этим говорят о пределе усталости конструкционной стали, понимая под ним обычно амплитуду напряжения
ниже которой сталь при повторно-переменной нагрузке не разрушается. При |smin | = |smax | предел усталости обозначают символом s-1 . Кривые усталости алюминиевых, титановых и магниевых сплавов обычно не имеют горизонтального участка, поэтому сопротивление усталости этих сплавов характеризуют т. н. ограниченными (соответствующими заданному N ) пределами усталости. Сопротивление усталости зависит также от частоты приложения нагрузки. Сопротивление материалов в условиях низкой частоты и высоких значений повторной нагрузки (медленная, или малоцикловая, усталость) не связано однозначно с пределами усталости. В отличие от статической нагрузки, при повторно-переменных нагрузках всегда проявляется чувствительность к надрезу, т. е. предел усталости при наличии надреза ниже предела усталости гладкого образца. Для удобства чувствительность к надрезу при усталости выражают отношением
характеризует асимметрию цикла). В процессе уставания можно выделить период, предшествующий образованию очага усталостного разрушения, и следующий за ним, иногда довольно длительный, период развития трещины усталости. Чем медленнее развивается трещина, тем надёжнее работает материал в конструкции. Скорость развития трещины усталости dl/dN связывают с коэффициентом интенсивности напряжений степенной функцией:
Различают сопротивление термической усталости, когда появляющиеся в материале напряжения обусловлены тем, что в силу тех или иных причин, например из-за формы детали или условий её закрепления, возникающие при циклическом изменении температуры тепловые перемещения не могут быть реализованы. Сопротивление термической усталости зависит и от многих других свойств материала – коэффициентов линейного расширения и температуропроводности, модуля упругости, предела упругости и др.
Лит.: Давиденков Н. Н., Динамические испытания металлов, 2 изд., Л. – М., 1936; Ратнер С. И., Разрушение при повторных нагрузках, М., 1959; Серенсен С. В., Когаев В. П., Шнейдерович Р. М., Несущая способность и расчеты деталей машин на прочность, 2 изд., М., 1963; Прикладные вопросы вязкости разрушения, пер. с англ., М., 1968; Фридман Я. Б., Механические свойства металлов, 3 изд., М., 1974; Методы испытания, контроля и исследования машиностроительных материалов, под ред. А. Т. Туманова, т. 2, М., 1974.
С. И. Кишкина.

Рис. 4. Изменение механических свойств конструкционных материалов в функции времени (или числа циклов).

Рис. 3. Образец со специально созданной в вершине надреза трещиной усталости для определения K1C . Испытания на внецентренное (а) и осевое (б) растяжение.

Рис. 1. Схемы деформации при разных способах нагружения: а – растяжение, б – сжатие, в – изгиб, г – кручение (пунктиром показана начальная форма образцов).

Рис. 2. Типичная диаграмма деформации при растяжении конструкционных металлов.