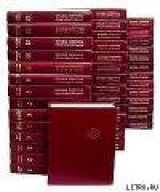
Текст книги "Большая Советская Энциклопедия (СС)"
Автор книги: Большая Советская Энциклопедия
Жанр:
Энциклопедии
сообщить о нарушении
Текущая страница: 121 (всего у книги 151 страниц)
В 70-х гг. получили промышленное применение процессы плавки в усовершенствованных вагранках и электрических печах. Для улучшения свойств отливок осуществляется легирование и модифицирование сплавов. Высокая точность отливок достигается применением литья в кокиль, литья по выплавляемым моделям, использованием разовых литейных форм, изготовленных на автоматах под высоким давлением или с применением специальных, твердеющих в технологической оснастке формовочных и стержневых смесей. Используются вакуумная плавка, различные виды рафинирования расплавов и др., а также полуавтоматическое и автоматическое оборудование, облегчающее труд рабочих и обеспечивающее охрану окружающей среды от воздействия производств. отходов. Автоматизируется управление технологическими процессами и производством в целом.
Ведущие институты по разработке литейных технологии и машиностроения: Всесоюзный НИИ литейного машиностроения, литейной технологии и автоматизации литейного производства и институт проблем литья АН УССР.
Советские учёные являются членами Международной ассоциации литейщиков, участвуют в международных конгрессах (40-й конгресс проходил в Москве в 1973). См. также Литейное производство.
Обработка металлов давлением (ковка, штамповка, прессование) [Развитие техники и технологии прокатного производства рассмотрено в разделе Металлургическая наука, техника и технология]. До 1917 кузнечные и прессовые цехи выпускали ограниченную номенклатуру деталей. Уже в годы 1-й пятилетки (1929—32) кузнечно-штамповочное и прессовое производство получило заметное развитие, особенно в новых отраслях машиностроения (энергетическом, тракторном, автомобильном, транспортном). Кузнечные цехи начали производить поковки и штамповки из стали многих марок, алюминиевых и магниевых сплавов и др. Были созданы первые специализированные прессовые цехи лёгких сплавов. Технология ковки и штамповки усовершенствовалась в 30—40-е гг.: расширилась номенклатура поковок, повысилась точность штамповки, форма поковок приблизилась к готовым деталям. Начала применяться горячая штамповка в многоручьевых штампах. Увеличилась толщина листового металла для ковки и горячей штамповки крупных пустотелых деталей – барабанов, котлов и др. Рост выпуска тонкого холоднокатаного листа повлиял на совершенствование холодной листовой штамповки крупных автомобильных, судовых, вагонных и др. деталей. Увеличение размеров кованых деталей привело к повышению верхнего предела массы кузнечных слитков до 200—250 т. В 50-е гг. положит. результаты дало применение электрошлаковой сварки при изготовлении ковано-сварных крупногабаритных изделий.
Развитие атомной, авиационной и ракетной техники, приборостроения, повышение рабочих параметров машин (усилий, напряжений, скоростей, давлений, температур) потребовало разработки новых технологических процессов для высокопрочных и жаропрочных сплавов, новых термомеханических режимов обработки тугоплавких металлов (Mo, Nb, W, Cr и др.). Значит. развитие получил процесс прессования (выдавливания) металлов. Было освоено прессование профилей и труб переменного сечения, пустотелых профилей и панелей из алюминиевых сплавов, труб и профилей (в т. ч. переменного сечения и пустотелых) из титановых сплавов, прутков, профилей и труб из высокопрочных сталей, а также из жаропрочных сплавов на никелевой основе и тугоплавких сплавов. Помимо внедрения гидропрессовой техники, в том числе мощных штамповочных прессов с усилием 30—75 тыс. тс и горизонтальных гидравлических прессов для прессования металлов с усилием 12—20 тыс. тс, в 60—70-е гг. распространились принципиально новые технологические процессы: импульсное и взрывное прессование, беспрессовое изготовление деталей в холодном состоянии из жаропрочных сталей, титана, алюминиевых сплавов и др. Созданы установки со взрывом в воде, в вакууме, электроразрядные установки в воде, взрывные со смесью газов, импульсные установки с сильными магнитными полями. Разработано гидростатическое прессование металлов, а также высокотемпературное гидростатическое формование порошков труднодеформируемых металлов и сплавов (газостаты). Создано уникальное прессовое оборудование для получения синтетических алмазов. Осуществляется комплексная механизация и автоматизация технологических процессов ковки и штамповки (автоматические установки по выдавливанию сплошных и трубчатых деталей, автоматические линии по высадке болтов, заклёпок, по штамповке колец шарикоподшипников, вагонных колёс, звеньев гусениц и т. д.).
В разработке теоретических и технологическим проблем ковки, штамповки, прессования участвовали С. И. Губкин, И. М. Павлов, Е. П. Унксов, А. И. Целиков, И. А. Перлин, Б. В. Розанов, А. И. Зимин, П. С. Истомин и др. Исследования этих процессов ведутся в Центральном НИИ технологии машиностроения, Всесоюзном научно-исследовательском и проектно-конструкторском институте металлургического машиностроения, Всесоюзном институте лёгких сплавов и др.
Сварка. До конца 19 в. в России использовали только два способа сварки металлов – литейный и кузнечный. Основой принципиально новых методов соединения металлов явилось открытие в 1802 В. В. Петровым дугового разряда. В 1882 Н. Н. Бенардос и в 1890 Н. Г. Славянов предложили первые практически пригодные способы сварки с использованием электрической дуги. К 1911 распространилась также газовая сварка.
Научные исследования в области сварки развернулись после Октябрьской социалистической революции. В 1924 выпущены первые сварочные машины, спроектированные В. П. Никитиным. В 1929 для концентрации научно-исследовательских и конструкторских работ по сварке и резке металлов был создан Автогенный комитет при ВСНХ, а в 1931 – Всесоюзный автогенный трест. В годы 1-й пятилетки (1929—32) электросварку применяли не только для ремонта оборудования, но и для производства новых конструкций в строит. промышленности, транспортном и энергетическом машиностроении, судостроении и др. отраслях. Многие заводы использовали её в качестве основного технологического процесса при производстве котлов, вагонных конструкций, железнодорожных цистерн, цельносварных судов, трубопроводов и т. п. Научно-исследовательские работы велись в Центральном институте железнодорожного транспорта, Центральном НИИ технологии и машиностроения (ЦНИИТМАШ), НИИсудпроме, заводских лабораториях. Начались исследования по изучению распространения тепла при сварке (Н. Н. Рыкалин), прочности сварных конструкций и механизма образования напряжений от сварки (В. П. Вологдин, Г. А. Николаев). В 30-е гг. в НИИ и на заводах (особенно в Киеве под рук. Е. О. Патона) начались работы, в результате которых был создан способ автоматической сварки открытой дугой, а затем (начало 40-х гг.) способ автоматической сварки под флюсом с использованием оригинальной отечеств. аппаратуры. Эти методы позволили ликвидировать тяжёлый ручной труд, перевести сварку на индустриальную основу.
В период Великой Отечеств. войны 1941—45 сварочная техника использовалась в производстве танков, снарядов к ракетным установкам БМ-13 («Катюша») и др. вооружения. При изготовлении сварных бронекорпусов применялось оборудование для автоматической сварки под флюсом с постоянной скоростью подачи электродной проволоки (по принципу саморегулирования длины дуги, открытому В. И. Дятловым). В 1942 по дну Ладожского озера был проложен сварной трубопровод для доставки топлива в осажденный Ленинград. Разработаны методы подводной сварки и резки (К. К. Хренов и др.), используемые при ремонте поврежденных кораблей. Не прекращалась и научно-исследовательская работа: В. П. Никитин предложил сварку жидким присадочным металлом, Б. Е. Патон и И. К. Олейник – шланговую сварку под флюсом. Проводились исследования по точечной сварке металла больших толщин (А. С. Гельман), по металлургическим и металловедческим процессам при сварке (К. В. Любавский, А. М. Макара) и др.
В послевоенные годы развитие сварочной техники велось по трём направлениям: расширение механизации и автоматизации; изыскание новых способов нагрева металла; изучение и совершенствование металлургических процессов. В конце 50-х гг. в промышленности используют автоматическую сварку под слоем флюса, электрошлаковую сварку, газоэлектрические способы сварки, механизированную наплавку металлов. С помощью автоматической сварки перешли к поточному крупносекционному методу постройки судов, создали на её базе производство газо– и нефтепроводных труб большого диаметра, решили проблему цельносварного мостостроения. Электрошлаковая сварка, разработанная в институте электросварки им. Е. О. Патона, позволила преобразовать технологию и организацию производства массивных крупногабаритных изделий – прокатного оборудования, мощных прессов, валов гидротурбин, доменных комплексов и т. п. Сварку использовали при строительстве таких уникальных сооружений, как крупнейший в Европе цельносварной мост через Днепр в Киеве (1953), каркасы московских высотных зданий (начало 50-х гг.), атомные ледоколы «Ленин» (1959) и «Арктика» (1974). В 60 – начале 70-х гг. с помощью сварки построены мощные гидрогенераторы и гидропрессы, магистральные газо– и нефтепроводы, АЭС, цельносварные танкеры большого водоизмещения. Сварку используют в тяжёлом, энергетическом и транспортном машиностроении, электронной, полупроводниковой технике и в др. отраслях. Для повышения уровня сварочной техники созданы показательные заводы, цехи и участки сварных конструкций.
В 70-х гг. научно-исследовательская работа в области сварки сосредоточена на решении следующих проблем: работоспособность сварных соединений, расчёт сварочных напряжений и деформаций (Николаев и др.); развитие теории источников тепла при сварке (Б. Е. Патон, Рыкалин, Хренов и др.); разработка физико-химических и металлургических основ сварки (Б. И. Медовар, В. В. Фролов, Любавский, М. Х. Шоршоров и др.); технология сварки, совершенствование сварочных материалов (А. И. Акулов, Г. Д. Никифоров и др.). Разработаны принципиально новые эффективные методы – диффузионная сварка в вакууме, в защитных и инертных газах, сварка трением, электроннолучевая и лазерная сварка, сварка дуговой плазмой и др. Сварку осуществляют в любых пространственных положениях, на суше, под водой. На космическом корабле «Союз-6» впервые в мире проводились опыты по сварке в космосе (1969, В. Н. Кубасов, Г. С. Шонин). институтом электросварки им. Е. О. Патона (СССР) и Центральным институтом сварки (ГДР). Созданы установки для электроннолучевой сварки изделий автомобильной промышленности (1974). Н. -и. работы по сварке ведутся в ЦНИИТМАШе, институте электросварки им. Е. О. Патона, МВТУ им. Баумана, Всесоюзном НИИ электросварочного оборудования, институте металлургии им. Байкова, ВНИИавтогенмаше, Московском авиационно-технологическом институте (МАТИ), Ленинградский политехническом институте, Московском энергетическом институте, в других НИИ и на кафедрах вузов. См. также Сварка, Сварное соединение, Сварочное оборудование, Сварочные материалы.
Механическая обработка. Первые теоретические исследования процесса резания металлов были проведены в России в 1868—69 И. А. Тиме. Основы науки о резании металлов были заложены русскими учёными К. А. Зворыкиным, А. А. Бриксом, А. В. Гадолиным и др. Широкие научные исследования в области резания металлов развернулись после Октябрьской революции 1917 благодаря быстрому развитию социалистической индустрии, в частности станкостроения, инструментальной промышленности, металлообработки. Начало исследованиям в области процесса резания положили работы А. Н. Челюсткина, обосновавшего формулу для силы резания (1922—26). Базой для научно-исследовательских работ в области резания металлов, разработки новых станков и инструментов, подготовки научных кадров стал созданный в 20-х гг. трест Оргаметалл. В начале 30-х гг. в Экспериментальном НИИ металлорежущих станков (ЭНИМС), Московском станкоинструментальном институте (СТАНКИН) и конструкторских бюро многих заводов развернулись научные и проектные работы по основным проблемам станкостроения: созданию отдельных типов станков и их типажа в целом, увеличению быстроходности и мощности станков, изысканию совершенных конструкций деталей и механизмов, применению автоматического управления, повышению износостойкости и долговечности станков. К этой работе были привлечены учёные и специалисты (А. С. Бриткин, Г. М. Головин, В. И. Дикущин, Д. Н. Решетов, Г. А. Шаумян и др.). В 1934 в ЭНИМСе был создан первый в Европе агрегатный многошпиндельный станок.
В 30-е гг. проводились интенсивные исследовательские работы в области создания новых инструментов и материалов для них. После выпуска первого отечественного прессованного твёрдого сплава «победит» (1929) в лабораториях вузов и заводов, в созданных в начале 30-х гг. Всесоюзном научно-исследовательском инструментальном институте (ВНИИ), Всесоюзном НИИ абразивов и шлифования (ВНИИАШ), СТАНКИНе велись исследования с целью широкого внедрения в производство твердосплавного инструмента, создания новых твёрдых сплавов и др. инструментальных материалов (минералокерамики), позволяющих повысить режимы резания. В разработке основ конструирования и расчёта режущего инструмента участвовали Г. И. Грановский, В. М. Матюшкин, И. И. Семенченко и др.
К началу 30-х гг. относятся первые после Октябрьской революции научные работы в области технологии машиностроения (А. П. Соколовский), продолженные затем Б. С. Балакшиным (точность регулирования размеров в процессе обработки), Н. А. Бородачёвым (теория точности), К. В. Вотиновым (проблемы жёсткости станков), О. М. Кованом (теория припусков), А. Б. Яхиным (теория баз) и др. Эти работы сыграли большую роль в решении многих технических проблем, связанных с механической обработкой материалов.
Важное значение для развития науки о резании металлов и создания советской школы резания имел период 1935—41, когда стахановское движение передовиков производства опрокинуло нормативы, тормозившие дальнейшее развитие техники, в том числе и в области резания металлов. Декабрьский (1935) пленум ЦК ВКП(б) предложил пересмотреть технические руководящие материалы, на которых базировались нормативы. С этой целью была создана Комиссия по резанию металлов для объединения всех научных исследований в стране в этой области. В работе Комиссии участвовали не только учёные (И. М. Беспрозванный, В. А. Кривоухов, Е. П. Надеинская, А. В. Панкин и др.), но и заводские коллективы, инженеры, мастера и рабочие. Было проведено по единой методике свыше 120 000 экспериментов по исследованию процесса резания, установлены силовые и стойкостные зависимости для всех видов металлорежущего инструмента и по всем основным металлам, применяемым в машиностроении, созданы инженерные методы расчёта геометрии режущей части инструмента и оптимальных режимов обработки различных материалов. В разработке физических основ процесса резания важную роль сыграли работы учёных в области смежных наук (В. Д. Кузнецов, П. А. Ребиндер и др.).
Перед Великой Отечеств. войной 1941—1945 станкостроение выпускало станки многих типов (в т. ч. агрегатные и специальные) с высокой степенью автоматизации, чему способствовали научно-исследовательские работы, выполненные в АН СССР, отраслевых институтах и специализированных лабораториях. Первые проекты автоматических линий из агрегатных станков были разработаны в ЭНИМСе ещё в 1936. В годы войны станки-автоматы, автоматические и полуавтоматические линии сыграли важную роль в массовом производстве вооружения при нехватке рабочей силы (только одна полуавтоматическая линия для расточки и сверления отверстий в корпусных деталях танка Т-34 заменила 19 тяжёлых расточных и радиально-сверлильных станков и высвободила 36 квалифицированных рабочих). В это же время значительно увеличился типаж станков (лишь одно конструкторское бюро под руководством Г. И. Неклюдова разработало около 190 типов оригинальных станков для производства миномётного вооружения).
В первые послевоенные годы научно-исследовательские и проектные институты работали над проблемами скоростного резания. Одно из основных условий перехода на повышенные скорости обработки – автоматизация управления станками путём электрификации и гидрофикации привода. В 1946 в ЭНИМСе был разработан бесступенчатый ионный электропривод станков с электронным управлением, сконструированы (Н. А. Волчек, Ю. Б. Эрпшер) для автотракторной промышленности автоматические линии из 14, 45 и 25 агрегатных станков, основанные на принципе сквозного (поточного) прохода деталей, транспортируемых с помощью гидропривода. В создании станков-автоматов и автоматических линий участвовали также ВНИИ, ВНИИАШ и др. научно-исследовательские институты. Основы теории проектирования станков-автоматов разработаны Г. А. Шаумяном (1948). Впервые в мировой практике был спроектирован и построен в 1949 (начал работать в 1950) комплексно-автоматизированный завод поршней.
В 50—70-х гг., выполняя задачи по улучшению отраслевой структуры промышленности и техническому перевооружению народного хозяйства, отраслевые НИИ и конструкторские бюро уделяли особое внимание проектированию и отработке конструкций прецизионных станков, тяжёлых и уникальных станков, станков для электрофизической и электрохимической обработки (ультразвуковой, электроэрозионной, лазерной, плазменной и др.), многооперационных станков с автоматической сменой инструментов, станков с числовым программным управлением (ЧПУ). Для заводов, выпускающих универсальные станки, к 1965 была разработана единая унифицированная серия моделей и их модификаций. Разработкой методов расчёта и конструирования станков занимались Н. С. Ачеркан, В. С. Васильев, В. И. Дикушин, В. Ф. Кудинов, вопросами технологии – А. С. Проников, проблемами износостойкости станков – Д. Н. Решетов.
Освоение выпуска новых машин и оборудования, связанное с применением жаропрочных, нержавеющих, эрозионностойких, тугоплавких и др. труднообрабатываемых материалов, потребовало разработки новых инструментальных материалов, изменения конструкций режущего инструмента, иного подхода к выбору рациональных условий обработки резанием. В конце 50 – начале 70-х гг. на основе работ института физики высоких давлений АН СССР (А. Ф. Верещагин) и института сверхтвёрдых материалов АН УССР (В. Н. Бакуль) созданы сверхтвёрдые инструментальные материалы – синтетические алмазы, эльбор, гексанит и др. СССР занимает ведущее место в мире по производству сверхтвёрдых материалов. Так, предназначенный для обработки высокотвёрдых сложнолегированных сплавов эльбор (его производство впервые освоено ленинградским абразивным заводом «Ильич») экспортируется во многие страны. В создании новых инструментов и материалов большое значение имели работы Г. Н. Сахарова, В. Н. Слесарева, Н. Е. Филоненко-Бородича, Д. Ф. Шпотаковского и др. Теорию обработки металлов резанием обогатили труды Н. Н. Зорева, М. В. Касьяна, Т. Н. Лоладзе и др. Важную роль в развитии прогрессивных методов механической обработки металлов сыграли рабочие-новаторы: Г. С. Борткевич, С. И. Бушуев, П. Б. Быков, В. А. Карасёв, В. А. Колосов, В. К. Семинский и мн. др.
В области технологии машиностроения в 50—70-х гг. проведены многочисленные научные исследования и решены проблемы адаптивного управления станками (Б. С. Балакшин), групповой обработки (С. П. Митрофанов), контактной жёсткости (Э. В. Рыжов), определения влияния различных факторов на точность обработки и качество поверхности (П. Е. Дьяченко). В разработке проблем технологии машиностроения участвовали также М. Е. Егоров, В. С. Корсаков и др. Советским учёным (И. В. Кудрявцеву, Е. Г. Коновалову, С. В. Серенсену и др.) принадлежит приоритет в разработке основ упрочняющей технологии, при которой в процессе механической обработки улучшаются свойства материалов в направлении, обеспечивающем повышенную эксплуатационную надёжность и долговечность изделий.
В 10-й пятилетке (1976—80) отраслевые научно-исследовательские, проектные и технологические институты, конструкторские бюро заводов работают над созданием автоматического оборудования с малогабаритными электронными системами числового программного управления (ЧПУ) и контроля, улучшением структуры выпускаемого металлообрабатывающего оборудования (станки с ЧПУ, тяжёлые, уникальные и высокоточные станки, специальные станки и автоматические линии, в том числе переналаживаемые комплексные линии, комплекты высокопроизводит. оборудования с управлением от ЭВМ), созданием нового металлообрабатывающего инструмента из природных и синтетических алмазов, минералокерамических и др. сверхтвёрдых материалов, абразивных материалов высокой стойкости. В этих работах участвуют ЭНИМС и его филиалы (в Армянской ССР и Литовской ССР), ВНИИ, ВНИИалмаз, Украинский НИИ станков и инструментов, технологический институт Оргстанкинпром, другие институты и широкая сеть конструкторских бюро во многих союзных республиках.
Между странами – членами СЭВ заключены соглашения о совместной разработке основных научно-технических проблем в области металлообработки: создании и усовершенствовании станков с ЧПУ, создании единого программного языка, методов испытаний станков, норм точности, унификации систем и элементов управления и т. д. При этом достигается более высокий уровень концентрации научно-исследовательского потенциала в социалистических странах.
См. также Станкостроение, Инструментальная промышленность, Обработка металлов резанием, Металлорежущий станок, Металлорежущий инструмент, Инструмент алмазный.
А. А. Пархоменко, О. А. Владимиров, Л. И. Леей, Д. Л. Юдин.
Периодические издания: «Машиноведение» (с 1965), «Вестник машиностроения» (с 1921), «Известия АН СССР. Механика твёрдого тела» (с 1966), «Стандарты и качество» (с 1927), «Машиностроитель» (с 1931),«Приборостроение»(с 1956), «Измерительная техника» (с 1939), «Металловедение и термическая обработка металлов» (с 1955), «Сталь» (с 1941), «Литейное производство» (с 1930), «Сварочное производство» (с 1930), «Автоматическая сварка» (с 1948), «Кузнечно-штамповочное производство» (с 1959), «Станки и инструмент» (с 1930) и другие отраслевые журналы.
Металлургическая наука, техника и технология
Русские учёные внесли большой вклад в науку о металлах, в развитие техники и технологии их производства. В 1763 М. В. Ломоносов опубликовал «Первые основания металлургии или рудных дел», в которых рассмотрел ряд проблем, связанных с добычей руд и получением металлов. В 60-х гг. И. И. Ползунов построил первую доменную воздуходувку, приводимую в движение силой пара. В. В. Петров, открывший в 1802 явление электрической дуги, указал на возможность её применения для электроплавки и восстановления металлов из окислов. Труды
П. Г. Соболевского по получению ковкой платины и изготовлению из неё изделий (1826) положили начало порошковой металлургии. П. П. Аносов разработал новые способы выплавки стали высокого качества, положил начало металлургии легированных сталей, впервые применил микроскоп для исследования структуры металла (1831). Классические работы Д. К. Чернова в области кристаллизации стального слитка, фазовых превращений в стали, строения металлов и сплавов послужили фундаментом для создания современного металловедения и термической обработки металлов. Наследие Чернова творчески развивали А. А. Байков, А. А. Ржешотарский, Н. С. Курнаков и др. Крупный вклад в теорию и практику доменного процесса внесли М. А. Павлов и М. К. Курако. Одну из первых в Европе мартеновских печей построил в 1870 А. А. Износков; Д. К. Чернов (1872) и К. П. Поленов (1875—76) предложили т. н. русское бессемерование – разновидность бессемеровского процесса, обеспечивающую переработку малокремнистых чугунов. Братья А. М. и Ю. М. Горяиновы разработали и внедрили технологию мартеновской плавки на жидком чугуне (1894). На основе научных трудов, открытий и изобретений русских учёных, инженеров и практиков-металлургов развивалась металлургическая промышленность, улучшались конструкции агрегатов, совершенствовались технологические процессы. Однако создать мощную металлургию в условиях дореволюционной России не представлялось возможным.
Октябрьская революция 1917 дала мощный толчок развитию производительных сил, в том числе металлургии. Восстановление и развитие чёрной и цветной металлургии на базе электрификации явилось одной из основных задач плана ГОЭЛРО. В годы 1-й пятилетки (1929—32) было развёрнуто строительство крупных металлургических предприятий, а также заводов тяжёлого машиностроения, выпускающих оборудование и машины для металлургической промышленности.
До 1917в стране не существовало металлургических научно-исследовательских институтов. На ряде заводов (Путиловском, Обуховском и др.) и на кафедрах горно-металлургических вузов имелись небольшие научно-исследовательские лаборатории. За годы Советской власти созданы научные центры – Институт металлургии им. А. А. Байкова АН СССР, Центральный НИИ чёрной металлургии им. И. П. Бардина (ЦНИИчермет), Украинский НИИ металлов (Харьков), Украинский НИИ специальных сталей, сплавов и ферросплавов (Запорожье), Институт чёрной металлургии (Днепропетровск), Донецкий НИИ чёрной металлургии, Научно-исследовательский и проектный институт металлургии и обогащения АН Казахской ССР, Государственный научно-исследовательский и проектный институт редкометаллической промышленности (Гиредмет), Государственный научно-исследовательский институт цветных металлов (Гинцветмет), Институт металлургии и Институт физики металлов Уральского научного центра АН СССР и мн. др. Научными кадрами высокой квалификации располагают и металлургические вузы страны. Работы советских учёных в значительной мере определили и определяют научно-технический прогресс в области металлургии. Исследованы физико-химические основы металлургических процессов и на этой базе разработаны способы интенсификации металлургического производства, усовершенствованы технологические процессы и созданы новые.
Существенно расширилась металлургическая база страны. Наряду с Югом, Уралом и Центром страны металлургические заводы создавались в Западной и Восточной Сибири, в Казахстане, Узбекистане, Грузии, Азербайджане и на Дальнем Востоке. В крупную базу по производству металла превратились районы Севера и Северо-Запада. Большую роль в реконструкции и строительстве предприятий металлургии сыграл Государственный институт по проектированию металлургических заводов (Гипромез), основанный в Ленинграде в 1926. В 1930 институт создал проект типовой доменной печи объёмом 930—1000 м3. С 1936 по проекту Гипромеза строились уникальные по тому времени доменные печи объёмом 1300 м3, а затем 2000 м3. В начале 70-х гг. объёмы советских доменных печей возросли до 2700—3200 м3, а в 1974 на Криворожском металлургическом заводе им. В. И. Ленина вступила в строй самая мощная в мире доменная печь объёмом 5000 м3. СССР располагает крупнейшими в мире мартеновскими печами ёмкостью до 600 т и двухванными печами той же мощности, кислородными конвертерами ёмкостью 300—350 т, электропечами ёмкостью 100 и 200 т. На ряде заводов действуют станы горячей прокатки производительностью до 4 и более млн. т проката в год.
Научно-технический прогресс характерен для всех стадий металлургического производства – от подготовки исходных материалов до выпуска готовой продукции. В важнейших горнорудных бассейнах построены обогатит. фабрики. Технический прогресс в обогащении руд характеризуется улучшением применяемых технологических схем и методов, совершенствованием оборудования, увеличением глубины обогащения, обусловленным повышенными требованиями современной металлургии к сырым материалам, а также вовлечением в эксплуатацию всё более бедных труднообогатимых руд. Разработаны и внедрены в промышленность технологические схемы, обеспечивающие комплексное использование сырья, в том числе полиметаллических руд. Ещё в годы довоенных пятилеток и особенно после войны получило развитие агломерационное производство. Построены крупнейшие в мире агломерационные фабрики. В 60-х гг. освоено производство офлюсованных окатышей из тонкоизмельчённого железорудного концентрата.
За годы Советской власти возникла и развилась коксохимическая промышленность, освоена прогрессивная технология коксования. Коксохимическое производство развивается в направлении строительства всё более мощных коксовых батарей с печами большой ёмкости, внедрения бездымной загрузки шихты и сухого тушения кокса, механизации и автоматизации обслуживания коксовых печей, совершенствования процессов улавливания и переработки химических продуктов коксования, ассортимент которых включает (70-е гг.) свыше 200 наименований. Наряду с коксовыми печами объёмом 30 м3 и высотой 5—6 м сооружаются печи объёмом более 40 м3 и высотой 7 м. Годовая производительность коксовой батареи из 65 таких печей превышает 1 млн. т кокса.
Индустриализация страны, быстрое развитие чёрной металлургии и др. отраслей народного хозяйства обусловили форсированное наращивание мощностей по производству огнеупоров. В дореволюционной России производство огнеупоров носило полукустарный характер. Многие виды огнеупорных изделий (например, для доменных и коксовых печей) импортировались. К концу 30-х гг. нужды страны почти полностью обеспечивались отечеств. огнеупорами. В годы Великой Отечественной войны 1941—45 около половины предприятий огнеупорной промышленности были разрушены. Их восстановление сопровождалось техническим перевооружением, особенно усилившимся в 60—70-х гг. Благодаря научным исследованиям, проводимым учёными совместно с работниками огнеупорной промышленности, повысилось качество изделий, увеличился их ассортимент, освоено производство ряда новых огнеупоров (смолосвязанных для кислородных конвертеров, плотных каолиновых для шахт доменных печей, высокоглинозёмистых, высокоплотных динасовых, периклазо-шпинелидных, изделий для установок вакуумирования, непрерывной разливки стали и др.), расширилась сырьевая база.
Решающим звеном в интенсификации доменного производства явилось применение кислорода и природного газа. Опытные плавки с использованием дутья, обогащенного кислородом, были начаты в СССР на Чернореченском химическом заводе в 30-е гг. В 1940—41 опыты были продолжены на доменной печи Днепропетровского завода металлургического оборудования. В более широких масштабах доменный процесс на кислородном дутье исследовался на опытной печи Новотульского завода в 1948—53. В 1957 на заводе им. Петровского (Днепропетровск) впервые в мире был применен природный газ, что позволило значительно снизить расход кокса. Год спустя по этой технологии работало уже 12 доменных печей. В сочетании с дутьём, обогащенным кислородом, применение природного газа обеспечивает стабильность работы доменной печи и улучшение технико-экономических показателей плавки. Уже в начале 70-х гг. свыше 80% чугуна выплавлялось в СССР с применением природного газа и около 60% – с. использованием кислорода. Большой эффект для роста производительности доменных печей даёт повышение давления газов на колошнике и температуры дутья до 1200 °С.