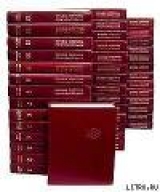
Текст книги "Большая Советская Энциклопедия (ПР)"
Автор книги: Большая Советская Энциклопедия
Жанр:
Энциклопедии
сообщить о нарушении
Текущая страница: 76 (всего у книги 122 страниц)
Прокатное производство
Прока'тное произво'дство, получение путём прокатки из стали и других металлов различных изделий и полуфабрикатов, а также дополнительная обработка их с целью повышения качества (термическая обработка, травление, нанесение покрытий). В промышленных странах прокатке подвергается больше 4 /5 выплавляемой стали. П. п. обычно организуется на металлургических заводах (реже на машиностроительных); как правило, особенно в чёрной металлургии, является завершающим звеном цикла производства (см. Металлургия ; о П. п. как отрасли металлургической промышленности см. в статьях Чёрная металлургия ,Цветная металлургия ).
К основным видам проката относятся: полупродукт, или заготовка, листовой и сортовой прокат, катаные трубы, заготовки деталей машин (особые виды проката) – колёса, кольца, оси, свёрла, шары, профили переменного сечения и др. Перечень прокатываемых изделий с указанием размеров называемым сортаментом проката , большая часть которого в СССР стандартизована. Основное количество проката изготовляется из низкоуглеродистой стали, некоторая часть – из легированной стали и стали с повышенным (больше 0,4%) содержанием углерода. Прокат цветных металлов производится главным образом в виде листов, ленты и проволоки; трубы и сортовые профили из цветных металлов изготовляются преимущественно прессованием (см. Прессование металлов ).
Прокатка стали. производство стального проката на современном металлургическом заводе осуществляется двумя способами. При первом исходным материалом служат слитки (отлитые в изложницы), которые перерабатываются в готовый прокат обычно в 2 стадии. Сначала слитки нагревают и прокатывают на обжимных станах в заготовку. После осмотра заготовки и удаления поверхностных дефектов (закатов, трещин и т.п.) производят повторный нагрев и прокатку готовой продукции на специализированных станах. Размеры и форма сечения заготовки зависят от её назначения: для прокатки листового и полосового металла применяют заготовки прямоугольного сечения шириной 400—2500 мм и толщиной 75—600 мм, называемые слябами ; для сортового металла – заготовки квадратного сечения размером примерно от 60´60 см до 400´400 мм , а для цельнокатаных труб – круглого сечения диаметром 80—350 мм .
При втором способе, применяемом с середины 20 в., прокатка исходной заготовки заменяется непрерывным литьём (разливкой) на специальных машинах. После осмотра и удаления дефектов заготовка, как и при первом способе, поступает на станы для прокатки готовой продукции. Благодаря применению непрерывно-литой заготовки упраздняются слябинги и блюминги, повышается качество проката, устраняются потери на обрезку головной части слитка, доходящие у слитков спокойной стали до 15—20%.
Преимущества применения непрерывно-литой заготовки в производстве проката становятся ещё более значительными при совмещении процессов непрерывного литья и прокатки в одном неразрывном потоке. Для этой цели созданы литейно-прокатные агрегаты, в которых слиток на выходе из кристаллизатора не подвергается разрезке, проходит печь, где выравнивается температура по сечению, и затем поступает в валки прокатного стана. Т. о. осуществляется процесс кристаллизации и прокатки бесконечного слитка, т. е. пепрерывное производство проката из жидкого металла. Процесс получил широкое распространение при прокатке цветных металлов; он применяется также для производства стальной заготовки небольших сечений (примерно менее чем 150´150 мм ) повышенного качества. Основная трудность в развитии этого процесса состоит в относительно низкой скорости выхода слитка из кристаллизатора (1—6 м/мин ), что не позволяет в полной мере использовать производственные возможности непрерывного прокатного стана.
Прокатка листового металла производится из катаных или непрерывно-литых слябов и только листов толщиной свыше 50—100 мм — непосредственно из слитков или кованых слябов. В технологический процесс входят следующие основные операции: подача слябов со склада к нагревательным печам; нагрев; подача по рольгангу к рабочей клети стана и прокатка в несколько проходов (пропусков между валками), причём в первые проходы для получения листов требуемой ширины сляб иногда подаётся в валки поперёк или под углом; правка на роликовых правильных машинах; охлаждение на холодильниках; контроль и разметка; обрезка продольных кромок; обрезка концов, разрезка на листы определённой длины; иногда термическая обработка и покраска; отправка на склад готовой продукции.
Листы толщиной от 4 до 50 мм и плиты толщиной до 350 мм прокатываются на толстолистовых или броневых станах, состоящих из одной или двух рабочих клетей, а листы толщиной от 1,2 до 20 мм — на значительно более производительных непрерывных станах, на которых листы получаются в виде длинных (более 500 м ) полос; при выходе из последней клети стана полосы сматываются в рулон. Листы толщиной менее 1,5—3 мм выгоднее прокатывать в холодном состоянии, поэтому дальнейшее уменьшение толщины листа осуществляется обычно на станах холодной прокатки. Для этого рулоны после их получения на непрерывных станах горячей прокатки транспортируются в цех холодной прокатки, где с поверхности металла удаляется окалина (в линии непрерывного травления), затем обрезаются концы и производится стыковка (электрическая контактная сварка) для полной непрерывности дальнейшего процесса. Травленые рулоны разматываются и в несколько проходов обжимаются до требуемой толщины (общее обжатие для низкоуглеродистой стали доходит до 75—90%). Прокатка осуществляется на непрерывных станах, состоящих из 4 или 6 четырёхвалковых клетей, или на одноклетевых реверсивных станах. После холодной прокатки полосу отжигают для устранения наклёпа, затем подвергают дрессировке , правке, резке на листы и упаковке (рис. 1 ).
Прокатка сортового металла включает следубющие основные операции: нагрев до 1100—1250 °С; подачу нагретой заготовки к рабочим клетям и прокатку в несколько проходов в калибрах, постепенно приближающих сечение исходной заготовки к сечению готового профиля; резку проката на пилах или ножницах на части требуемой длины или сматывание в бунты; охлаждение на холодильниках; правку на роликовых правильных машинах; контроль и отправку на склад готовой продукции.
Число проходов выбирается в зависимости от размеров и формы сечения исходной заготовки и готового профиля и составляет: для рельсов обычно 9, балок 9—13, угловых и других сортовых профилей, например зетообразного (рис. 2 ), 5—12, проволоки 15—21. Выполнение указанных технологических операций производится на специализированных сортовых прокатных станах, представляющих собой поточную автоматическую систему различных машин.
Прокатка (горячая) труб состоит из 3 основных и нескольких вспомогательных операций. Первая операция (прошивка ) – образование отверстия в заготовке или слитке; в результате получается толстостенная труба, называемая гильзой. Вторая операция (раскатка ) — удлинение прошитой заготовки и уменьшение толщины её стенки примерно до требуемых в готовой трубе размеров. Обе операции осуществляются с одного нагрева, но на различных прокатных станах, установленных рядом и входящих в общую систему машин трубопрокатного агрегата . Первая операция выполняется на прошивных станах винтовой прокатки между бочкообразными или дисковыми валками на короткой оправке, вторая – на различных прокатных станах: непрерывных, пилигримовых, автоматических и трёх-валковых станах винтовой прокатки. Третья операция – калибровка (или редуцирование ) труб после раскатки. Калибровка осуществляется на калибровочных станах, затем трубы охлаждаются, правятся, контролируются и разрезаются на куски определённой длины. Трубы диаметром менее 65—70 мм подвергаются дополнительной горячей прокатке на редукционных станах. С целью уменьшения толщины стенки и диаметра, получения более высоких механических свойств, гладкой поверхности и точных размеров трубы после горячей прокатки подвергаются холодной прокатке на специальных станах, а также волочению.
Прокатка заготовок деталей машин (штучных изделий) находит широкое применение главным образом в производстве различных тел вращения и профилей переменного сечения: вагонных колёс, осей, бандажей, колец для подшипников качения, шаров, зубчатых колёс, винтов, свёрл и т.д. При этом иногда прокатка используется для выполнения лишь одной операции в комбинации с ковкой или штамповкой.
Прокатка цветных металлов. Наибольшее применение получила прокатка листов, ленты, фольги и проволоки из алюминия, меди, магния, цинка и их сплавов.
В технологический процесс прокатки листов из алюминиевых сплавов входят следующие основные операции: предварительнаяалепрокатка плоских непрерывно-литых слитков массой 0,5—5 т с обжатием около 10% для выравнивания их поверхности; правка на роликовых правильных машинах; фрезерование для получения чистой и гладкой поверхности; накладывание с обеих сторон слитка алюминиевых листов; нагрев; горячая прокатка с плакированием до толщины 4—12 мм с последующим свёртыванием в рулоны; отжиг и холодная прокатка. После холодной прокатки рулоны разматываются и режутся на листы, которые затем закаливают, травят, прокатывают вторично в холодном состоянии для прогладки или получения наклёпа, травят, разрезают и упаковывают.
В начале 60-х гг. 20 в. был разработан новый процесс прокатки листов из алюминия и его сплавов. Особенность этого процесса состоит в совмещении непрерывного литья с прокаткой. Исходным материалом служит жидкий алюминий, который поступает через распределительную проводку в межвалковое пространство, образованное между двумя горизонтальными валками (рис. 3 ). Алюминий, соприкасаясь с валками, кристаллизуется, а образующаяся полоса непрерывно выходит из валков стана. Валки могут быть расположены как в вертикальной плоскости, так и в горизонтальной. В первом случае алюминий подводится сбоку, а во втором – снизу. Этим методом успешно изготовляются полосы толщиной 8—12 мм , шириной 1000—1600 мм , которые затем сматывают в рулоны. Применение такой технологии вместо прокатки полосы из крупных слитков даёт большой экономический эффект.
Исходной заготовкой при прокатке листов и лепты из меди и латуни служат плоские слитки массой около 0,5—1 т , толщиной 100—150 мм , которые прокатываются в горячем состоянии до толщины 10—15 мм. Прокатанные листы фрезеруют для удаления поверхностных дефектов и затем подвергают холодной прокатке с промежуточными отжигами при 450—800 °С.
Для производства катанки из алюминиевых и медных сплавов наиболее эффективен способ непрерывного литья, совмещенный с прокаткой на непрерывном стане.
Технический прогресс в области П. п. характеризуется в первую очередь повышением качества прокатываемых изделий, которое обеспечивало бы наиболее эффективное использование металла потребителем. С этой целью прокатываемому изделию придаётся возможно более рациональная форма, способствующая снижению его массы, расширяется производство экономичных профилей проката, повышается точность его размеров, улучшаются прочностные и др. свойства металла, на его поверхность наносятся эффективные защитные покрытия. Одновременно снижается стоимость производственных затрат путём внедрения непрерывных процессов (от жидкого металла до готового проката), повышения скорости прокатки и автоматизации всех технологических процессов.
Лит.: Прокатное производство. Справочник, под ред. Е. С. Рокотяна, т, 1—2, М., 1962; Прокатное производство, 2 изд., М., 1968; Higgins R. A., Engineering metallurgy, 2 ed., pt 2, L., 1970; Holub J., Pžicné klinové válcováni, Praha, 1972.
А. И. Целиков.

Рис. 1. Технологическая схема цеха холодной прокатки для производства листов: 1 – конвейер горячекатаных рулонов; 2 – агрегат нормализации; 3 – непрерывно-травильный агрегат; 4 – агрегат комбинированной резки; 5 – непрерывный стан холодной прокатки; 6 – термическое отделение; 7 – агрегат нанесения защитного покрытия; 8 – дрессировочный стан; 9 – непрерывно-цинковальный агрегат; 10 – отделение упаковки готовых продуктов.

Рис. 2. Схема изменения сечения (калибровка) при прокате зетового профиля.

Рис. 3. Схемы способов бесслитковой прокатки полос: а – подача металла сбоку; б – подача металла снизу; 1 – распределительная ванна; 2 – межвалковое пространство (кристаллизатор); 3 – валки; 4 – полоса.
Прокатный профиль
Прока'тный про'филь, металлическое изделие (различной формы поперечного сечения), полученное прокаткой . Различают П. п. с постоянным поперечным сечением по длине, переменные профили и специальные. К 1-му виду относятся П. п. сортовой стали (рис. ), имеющие простую геометрическую форму (например, круг, прямоугольник, квадрат, овал, шестиугольник, сегмент), и т. н. фасонные профили, представляющие собой сочетания простых профилей (например, угловые П. п., двутавровые балки, полосы для ободьев колёс автомобиля, колосниковых решёток, тракторных шпор и т.п.), листы, трубы (в т. ч. и профильные: квадратные, прямоугольные, ромбические, овальные и специальные), гнутые профили. Ко 2-му виду относятся, например, т. н. периодические профили, к 3-му – бандажи, колёса, шестерни, шары, ребристые трубы и др. изделия. См. также Сортамент проката .

Некоторые профили сортового проката: 1 – квдратный; 2 – круглый; 3 – прямоугольный (полосовой); 4 – угловой; 5 – двутавровый; 6 – швеллерный; 7 – железнодорожный рельс; 8 – трамвайный рельс; 9 – тавровый; 10 – шпунтовый; 11 – полоса для гусениц тракторов; 12 – полоса для ободьев колес грузовых автомобилей; 13 – полоса для турбинных лопаток.
Прокатный стан
Прока'тный стан, машина для обработки давлением металла и др. материалов между вращающимися валками, т. е. для осуществления процесса прокатки , в более широком значении – автоматическая система или линия машин (агрегат), выполняющая не только прокатку, но и вспомогательные операции: транспортирование исходной заготовки со склада к нагревательным печам и к валкам стана, передачу прокатываемого материала от одного калибра к другому, кантовку, транспортирование металла после прокатки, резку на части, маркировку или клеймение, правку, упаковку, передачу на склад готовой продукции и др.
Историческая справка. Время и место появления первого П. с. неизвестны. Бесспорно, что раньше прокатки железа применяли прокатку цветных металлов – свинца, олова, меди, монетных сплавов и др. Наиболее ранний документ (рисунок с описанием), характеризующий устройство для прокатки олова, оставлен Леонардо да Винчи (1495). Примерно до конца 17 в. привод П. с. был ручным, в 18 в. – водяным. Промышленная прокатка железа началась примерно с 18 в. В России она особенно широко развивалась на Урале. П. с. применялись для производства кровельного железа, плющения кричной заготовки в полосу или лист, разделения откованной полосы по длине на более мелкие профили квадратного или прямоугольного сечения (т. н. «резные» станы).
В конце 18 в. для привода П. с. начали применять паровые машины; прокатка становится одним из трёх основных звеньев производственного цикла металлургических заводов, постепенно вытесняя менее производительный способ ковки . К этому периоду относится промышленное применение П. с. с калиброванными валками, сконструированного в 1783 Г. Кортом (Великооритания); П. с. постепенно дифференцируются на обжимные, листовые и сортовые. В 30—40-х гг. 19 в. в связи с бурным развитием железных дорог в разных странах начинают прокатывать рельсы. В 1856—57 в Сааре (Германия) был установлен первый П. с., предназначенный для прокатки крупных балок. Развитие конструкций и специализация этих станов привели к появлению в США в конце 19 в. блюмингов и слябингов . В 1867 Г. Бедсон (Великобритания) построил непрерывный проволочный стан. В 1885 братья М. и Р. Маннесман (Германия) изобрели способ винтовой прокатки бесшовных труб в П. с. с косо расположенными валками. В 1886 В. Эденборн и Ч. Морган (США) применили быстроходную проволочную моталку с осевой подачей. Первые летучие ножницы (конструкции В. Эдвардса) установлены в 1892 в США. В 1897 для привода П. с. с успехом применен электродвигатель (Германия). В 1906 в г. Тршинец (ныне Чехословакия) пущен П. с. с реверсивным электродвигателем. Принцип непрерывной горячей прокатки листов нашёл практическое применение в 1892 в г. Теплице (ныне Чехословакия), где был установлен полунепрерывный стан. Первый непрерывный широкополосовой (листовой) стан построен в 1923 в США. Начало холодной прокатки листов относится к 80-м гг. 19 в.; холодная прокатка труб освоена в 1930 в США.
В СССР первым достижением станостроения явилось сооружение Ижорским заводом двух блюмингов, которые в 1933 введены в эксплуатацию на Макеевском и Днепродзержинском металлургических заводах. В 1940—60-х гг. Всесоюзным научно-исследовательским и проектно-конструкторским институтом металлургического машиностроения (ВНИИМЕТМАШ) создан ряд П. с. для новых технологических процессов, обеспечивающих производство прокаткой многих изделий, которые ранее изготовлялись другими, менее эффективными способами (тонкостенные безрисочные трубы, листы переменной толщины по длине, профили круглого периодического сечения, шары, втулки, винты с крупным шагом, ребристые трубы и др.). В 1959—62 ВНИИМЕТМАШем и Электростальским заводом тяжёлого машиностроения созданы принципиально новые трубные станы с бесконечным редуцированием труб (как при печной сварке, так и при радиочастотной), а также станы для непрерывной прокатки бесшовных труб (стан 30—102) производительностью на порядок выше по сравнению с действующими (около 550 тыс. т /год). В эти же годы пущены разработанные ВНИИМЕТМАШем, Научно-исследовательским институтом автомобильной промышленности и Горьковским автомобильным заводом первые станы для прокатки цилиндрических и конических колёс.
В 60-е гг. в СССР, США, ФРГ и Италии начато создание литейно-прокатных агрегатов, в которых совмещены процессы непрерывного литья и прокатки в едином неразрывном потоке. Такие агрегаты уже получили широкое применение для производства катанки из алюминиевых и медных сплавов, листов из алюминиевых сплавов и заготовок из стали.
Классификация и устройство прокатных станов. Главный признак, определяющий устройство П. с., – его назначение в зависимости от сортамента продукции или выполняемого технологического процесса. По сортаменту продукции П. с. разделяют на заготовочные, в том числе станы для прокатки слябов и блюмов , листовые и полосовые, сортовые, в том числе балочные и проволочные, трубопрокатные и деталепрокатные (бандажи, колёса, оси и т.д.). По технологическому процессу П. с. делят на следующие группы: литейно-прокатные (агрегаты), обжимные (для обжатия слитков), в том числе слябинги и блюминги, реверсивные одноклетевые, тандемы, многоклетевые, непрерывные, холодной прокатки. Размер П. с., предназначенного для прокатки листов или полос, характеризуется длиной бочки валков, для заготовки или сортового металла – диаметром валков, а трубопрокатного стана – наружным диаметром прокатываемых труб.
Оборудование П. с., служащее для деформации металла между вращающимися валками, называют основным, а для выполнения прочих операций – вспомогательным. Основное оборудование состоит из одной или нескольких главных линий, в каждой из которых располагается 3 вида устройств (рис. 1 ): рабочие клети (одна или несколько) – к ним относятся прокатные валки с подшипниками, станины, установочные механизмы, плитовины, проводки; электродвигатели для вращения валков; передаточные устройства от электродвигателей к прокатным валкам, состоящие большей частью из шестерённой клети, шпинделей и муфт. Между шестерённой клетью и электродвигателем часто устанавливают ещё редуктор. Если каждый валок имеет свой электродвигатель, передаточные устройства состоят лишь из шпинделей. Наибольшее распространение получили станы с горизонтальными валками: двухвалковые (дуо), трёхвалковые (трио), четырёхвалковые (кварто) и многовалковые (рис. 2 ). Для обжатия металла по боковым поверхностям используют клети с вертикальными валками, называемые эджерами . Станы, у которых вблизи горизонтальных валков расположены вертикальные, называются универсальными. Они служат для прокатки широких полос и двутавровых балок с широкими полками. В станах винтовой прокатки валки располагаются в рабочей клети косо – под углом подачи. Такие станы применяют для прокатки труб, осей, шаров и т.д.
Число и расположение рабочих клетей П. с. определяются его назначением, требуемым числом проходов металла между валками для получения данного профиля и заданной производительностью. По этому признаку П. с. подразделяются на 8 типов (рис. 3 ). К одноклетевым станам относится большинство блюмингов, слябинги, шаропрокатные станы, станы для холодной прокатки листов, ленты и труб. В случае, когда в одной рабочей клети не удаётся расположить необходимое число калибров (см. Калибровка прокатных валков) или когда требуется высокая производительность, применяют станы с несколькими рабочими клетями. Наиболее совершенный многоклетевой стан – непрерывный, в котором металл одновременно прокатывается в нескольких клетях (рис. 4 ). Непрерывные станы служат для горячей прокатки заготовки, полос, сортового металла, проволоки, труб, а также для холодной прокатки листов, жести, ленты и др. профилей.
Скорости прокатки весьма различны и зависят главным образом от требуемой производительности П. с., сортамента прокатываемой продукции и технологического процесса. У обжимных, заготовочных, толстолистовых, крупносортных станов скорость прокатки около 2—8 м /сек. Наибольшие скорости характерны для непрерывных станов: при прокатке сортового металла 10—20 м/сек ; полосового 25—35 м /сек ; проволоки 50—70 м /сек ; при холодной прокатке жести 40 м/сек. Данные о производительности, мощности приводов и массе оборудования некоторых П. с., получивших наибольшее распространение в СССР для производства горячекатаной стали, приведены в таблице.
Краткая характеристика основных станов для горячей прокатки стали
Тип стана | Сортамент проката | Производительность, тыс. т/год | Общая мощность главных приводов, квт | Масса оборудования, т |
Блюминг одноклетевой дуо 1000—1300 | Блюмы от 200´200 мм до 370´370 мм | До 6 000 | До 13 600 | До 5 500 |
Листовой широкополосовой непрерывный 2000 | Полосы толщиной 1,2—16 мм, шириной до 1850 мм | 6 000 | 120 000 | 40 000 |
Толстолистовой сдвоенный 3600 | Листы и плиты толщннэй 5—200 мм, шириной до 3200 мм | 1 750 | 21000 | 60 000 |
Заготовочный непрерывный 900/700/500 | Заготовки сечением от 80´80 мм до 200´200 мм | 5 550 | 30 400 | 10 500 |
Рельсо-балочный ступенчатый трио 800 | Рельсы, балки от № 24 до № 60, швеллеры от № 20 до №40 и др. | 1 700 | 9 800 | 22 000 |
Крупносортный ступенчатый трио 650 | Круглая сталь диаметром 70—220 мм, б. ллки от № 16 до № 30 и др. | 750 | 8 700 | 6 500 |
Крупносортный полунепрерывный 600 | Круглля сталь диаметром 50—120 мм, балки от № 10 до № 20 и др. | 1 600 | 34 400 | 18 000 |
Среднесортный полунепрерывный 350 | Круглая сталь диаметром 20—75 мм, балки и швеллеры до № 10 и др. | 1000 | 16 000 | 7200 |
Мелкосортный непрерывный 250 | Круглая сталь диаметром 8—30 мм, угловой профиль от 20´20 мм до 40´40 мм и др. | 800 | 16 000 | 6 600 |
Узкополосовой непрерывный 300 | Полоса толщиной 2—8 мм, шириной 120—460 мм | Более 1000 | 15 200 | 2 700 |
Проволочный непрерывный 150 | Катанка диаметром 5,5—12,5 мм | 900 | – | – |
Трубопрокатный автоматический | Бесшовные трубы дилметром 140—426 мм | 50—70 т/ч | 12 000 | 8000—12 000 |
Трубопрокатный непревывный 110 | Бесшовные трубы диаметром 50—110 мм | 50—80 т/ч | 12 000 | 3 500—5 000 |
Заготовочные станы строятся двух типов в зависимости от исходного материала – слитков, отлитых в изложницах, или непрерывно-литых заготовок. В первом случае заготовочный стан одновременно является также обжимным станом. Типичные представители таких станов – слябинг, когда требуется плоская заготовка крупных сечений (слябы), и блюминг с установленным за ним собственно заготовочным непрерывным станом, если требуется прокатывать заготовку для сортовых или трубопрокатных станов. За последней клетью этих станов находятся летучие ножницы для разрезки заготовки на куски требуемой длины или пилы и стеллажи для разрезки, охлаждения и осмотра заготовки. При использовании непрерывно-литой заготовки заготовочный стан устанавливается рядом с машиной для непрерывного литья в целях использования тепла неостывшего металла. Некоторые заготовочные станы выполнены так, чтобы литая заготовка поступала из кристаллизатора в валки непрерывного стана без разрезки, т. е. в этом случае осуществляется прокатка заготовки бесконечной длины и деление её на куски требуемой длины летучими ножницами или пилами при выходе из валков стана.
Листовые и полосовые станы горячей прокатки предназначены для получения плит толщиной 50—350 мм, листов толщиной 3—50 мм и полос (сматываемых в рулоны) толщиной 1,2—20 мм. Толстолистовые станы обычно состоят из 1—2 клетей дуо и кварто с длиной бочки валков 3500—5500 мм (см. рис. 1 ), иногда с установленными перед ними дополнительными клетями, имеющими вертикальные валки для обжатия боковых кромок. Для прокатки полос наибольшее применение получили широкополосовые непрерывные или полунепрерывные станы, состоящие из 10—15 клетей кварто с длиной бочки валков 1500—2500 мм и нескольких клетей с вертикальными валками. Весь прокатываемый материал сматывается в рулоны по 15—50 т. Эти станы значительно более производительны, чем толстолистовые, поэтому они используются также и для прокатки толстых листов (4—20 мм ), которые изготовляются путём разматывания рулонов и их последующей разрезки. Со стороны выхода прокатанного металла из валков устанавливаются выходные рольганги и большое количество др. вспомогательного оборудования для последующей обработки проката и его транспортирования: у толстолистовых станов – правильные машины , ножницы, печи для термической обработки и т.д., а у широкополосовых станов – моталки для сматывания полос в рулоны, конвейер для транспортирования рулонов и оборудование для разматывания рулонов, их правки и разрезки на карточки (листы).
Сортовые станы весьма разнообразны по своей характеристике и расположению оборудования. Основные типы: универсальные станы для прокатки широкополочных балок, состоящие обычно из 3 или 5 клетей, расположенных последовательно одна за другой, из которых 2 или 3 клети универсальные, с горизонтальными валками диаметром около 1350 мм , а 1 или 2 – дуо, с валками диаметром около 800 мм ; рельсо-балочные станы ступенчатого типа из двух или нескольких линий с рабочими клетями трио и дуо и валками диаметром около 800 мм ; крупносортные станы ступенчатого и полунепрерывного типа из двух или нескольких линий с рабочими клетями трио и дуо и валками диаметром около 650 мм ; среднесортные станы ступенчатого типа в 2 или 3 линии, полунепрерывные и непрерывные; мелкосортные станы, большей частью непрерывные или полунепрерывные; узкополосовые станы непрерывные; проволочные станы непрерывные.
Для производства проволоки из алюминиевых и медных сплавов наиболее эффективны литейно-прокатные станы, в которых осуществляется непрерывный процесс получения проволоки из жидкого металла. Вначале происходит кристаллизация бесконечного слитка между ободом вращающегося колеса и обтягивающей его стальной лентой, а затем прокатка его на непрерывном стане. Производительность стана 5—8 т/ч (рис. 5 ).
Сортовые станы, как и листовые, имеют разнообразное вспомогательное оборудование, установленное по движению потока прокатываемого металла и выполняющее в общем ритме, без участия ручного труда, все вспомогательные технологические и транспортные операции, начиная с выдачи со склада исходной заготовки и кончая передачей проката на склад готовой продукции.
Трубопрокатные агрегаты состоят обычно из 3 станов. Первый стан производит прошивку отверстия в заготовке или слитке методом винтовой прокатки, второй служит для вытяжки прошитой заготовки в трубу и третий – для калибровки (редуцирования), т. е. уменьшения диаметра прокатанной трубы. Конструкция трубопрокатных агрегатов определяется главным образом выбранным технологическим процессом второго стана, т. е. вытяжного. Наиболее производительным является непрерывный стан; находят применение также станы дуо, работающие на короткой оправке, пилигримовые и трёхвалковые винтовой прокатки.
Станы холодной прокатки стали и цветных металлов изготовляются следующих типов: листовые – для штучной прокатки; листовые широкополосовые – для рулонной прокатки; ленто-прокатные – для прокатки ленты толщиной от 1 мкм до 4 мм и шириной от 20 до 600 мм , сматываемой после прокатки в бунты или рулоны; фольгопрокатные – для прокатки полосы толщиной менее 0,1 мм ; плющильные – для обжатия проволоки в узкую ленту; станы для холодной прокатки труб. При рулонной прокатке полос с обеих сторон рабочей клети устанавливаются намоточно-натяжные барабаны – моталки, которые служат для разматывания рулонов перед подачей металла в валки и сматывания при выходе из валков. Наиболее производительные листовые станы – непрерывные; они также выгоднее в отношении использования моталок и др. вспомогательного оборудования. Моталки у непрерывных станов располагаются только сзади, а спереди находятся механизмы для подачи рулонов, разматывания их и направления металла в валки первой рабочей клети.
Деталепрокатные станы работают в основном на принципе поперечной и винтовой прокатки и служат для производства точных заготовок деталей машиностроения – круглых периодических валов, шаров, винтов, ребристых труб, зубчатых колёс, а также инструмента – червячных фрез, свёрл и др. Эти станы разнообразны по конструкции и характеризуются высокой степенью механизации и автоматизации.
Оборудование прокатных станов. Конструкция основных деталей и механизмов П. с., несмотря на их различное назначение и многообразие, во многих случаях одинакова. Главные элементы рабочей клети – валки прокатные , подшипниковые узлы, механизмы для установки валков, станина, шпиндели, муфты и проводки.
Подшипники прокатных валков работают при очень больших нагрузках, доходящих на некоторых станах до 30—60 Мн (3000—6000 тс ) на валок. Возможные габариты их ограничиваются диаметром валков. Подшипники (качения или жидкостного трения) устанавливаются в массивных корпусах, называются подушками, которые располагаются в проёмах станины.