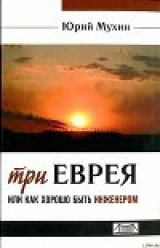
Текст книги "Три еврея"
Автор книги: Юрий Мухин
Жанр:
Современная проза
сообщить о нарушении
Текущая страница: 17 (всего у книги 51 страниц)
Глава 4 ЗАВОДСКИЕ ИНЖЕНЕРЫ
В этой книге главным действующим лицом являюсь я – так уж получается. Но мое амплуа – «рассказчик». А рассказывать мне приходится о том, о чем мало кто знает, тем не менее, мне хочется, чтобы все, о чем я пишу, было понятно. Поэтому мне приходится и много объяснять, и давать много примеров в объяснение того или иного. Я мог бы давать и примеры из чужой практики, но зачем, когда у меня есть собственные? А отсюда вытекает то, что я не могу в отношении себя следовать хронологии – я вынужден давать случаи, объясняющие ту или иную мою мысль, а характерные случаи были из разных периодов моей жизни. Понимаю, что это неудобно читать, но вы обращайте внимание не на мое жизнеописание, а на то, что я хочу сказать.
Инженер Друинский
Поскольку я не могу дать полностью воспоминания М.И. Друинского, то дам с сокращением, а частью перескажу биографическую справку о нем, которая была написана Заведующим кафедрой электрометаллургии стали и ферросплавов Днепропетровского металлургического института, академиком АН Украины, профессором, доктором технических наук, лауреатом Государственной премии Украины и премии Совета Министров СССР М.И.Гасиком. Тем самым Гасиком, про которого я писал, что когда учился в институте, то хотел быть таким ученым, как он.
«…М.И. Друинский родился 27 февраля 1925 года на Украине, в гор. Артемовске, Донецкой области. В 1928 г. семья переезжает в гор. Горловку, Донецкой обл., где в 1941 году он оканчивает 8 классов. Через несколько месяцев после начала войны эвакуируется в Сталинградскую обл., а затем в гор. Актюбинск, Казахстан.
Здесь в 1942 году он начал работать на строящемся Актюбинском заводе ферросплавов Наркомата черной металлургии СССР. С пуском завода в январе 1943 г. Друинский – плавильщик, затем – горновой электроплавильной печи плавильного цеха, участник первой плавки, которая состоялась 20 января 1943 года.

М.И. Друинский, 1946 год. Для меня было удивительным, что на его груди орденская планка ордена «Красной Звезды», который он мог получить только за доблестный труд в годы войны. Удивительным потому, что он никогда не говорил о своих наградах, никогда их не носил и ничего не написал в воспоминаниях
Затем в течение 20 лет он прошел все рабочие и инженерно-технические должности в цехе: старший горновой, помощник старшего плавильщика, старший плавильщик (бригадир электроплавильной печи), сменный мастер-технолог, начальник смены, обер-мастер, заместитель начальника цеха, начальник плавильного цеха № 1. Работая на заводе, без отрыва от производства, окончил вечернюю школу и Всесоюзный заочный политехнический институт (гор. Москва).
В период работы обер-мастером Друинским была проведена важная работа по освоению технологии производства передельного феррохрома с содержанием кремния 3–4 % Это дало возможность улучшить технико-экономические показатели и качество продукции на следующем переделе: при выплавке ферросиликохрома. Были проведены работы по исследованию причин повышения содержания серы в углеродистом феррохроме и осуществлены меры по ее снижению в сплаве.
Благодаря целеустремленности и настойчивости Друинского было осуществлено внедрение стальных ковшей (без футеровки) для разливки углеродистого феррохрома через нижнее очко ковша. Внедрена завалка шихты на печах, выплавляющих силикохром, с помощью завалочных машин. Вместе с группой инженеров им была предложена конструкция и внедрена в производство электропушка для механизированного закрытия леток феррохромовых печей. Он один из участников освоения и внедрения впервые в стране новой технологии получения среднеуглеродистого феррохрома путем продувки углеродистого феррохрома чистым кислородом в конвертерах.
В марте 1962 г. ЦК КП Казахстана и Казахский Совнархоз направляют его главным инженером на Ермаковский завод ферросплавов (Павлодарская область), строительство которого только начиналось.
Район строительства завода относился к неосвоенным: не имел автомобильных и рельсовых дорог, энергетических сетей и установок, коммуникаций, предприятий строительной индустрии, жилья для строителей.
Село Ермак было в прошлом пристанью на берегу реки Иртыш, к которой была подведена железнодорожная линия для вывоза углей Экибастузского месторождения. Впоследствии ж.д. линия была разобрана. Общая численность населения села в период проектирования завода составляла около 4 тысяч человек, занятых в сельском хозяйстве, учреждениях районного значения и мелких мастерских местной промышленности.
Жилой фонд состоял из 800 домов усадебного типа общей площадью 25 тыс. м2. В 1961 г. Указом Президиума Верховного Совета Казахстана село Ермак было отнесено к категории городов, но этот акт был чисто символическим.
«Ермак тех лет производил гнетущее, удручающее впечатление, как будто человек попадал в далекое прошлое. Не было ничего: ни нормального жилья, ни теплоснабжения, ни воды, ни канализации, ни надежного электроснабжения, ни бани, ни столовой, ни дорог и тротуаров, ни зелени. Одним словом, сплошные «ни». Ночью из-за отсутствия электроэнергии город был погружен в сплошную тьму. Нарушал тишину лишь лай собак. Был один примитивный детский садик и старая одноэтажная деревянная школа. Вокруг – одни землянки и ни одного кустика, ни одного деревца… Не на чем глазу остановиться…» – так описывает Друинский свое знакомство с Ермаком.
И здесь предстояло построить завод, крупнейшую ГРЭС, мощные заводы стройиндустрии, а также канал «Иртыш – Караганда», который брал начало в Ермаке. Здесь предстояло построить и город!
С чего начинать? Вместе с директором завода В.В. Боровиченко и руководителями строительного управления был пересмотрен титульный список на сооружение объектов завода и города, с целью ввода в 1962 г. жизненно-важных объектов для быстрого улучшения условий жизни населения. Далее, с учетом опыта, приобретенного Друинским в командировках на Запорожский и строящийся Алмазнянский заводы ферросплавов (Украина), было предложено внести существенные изменения в проект электроплавильного цеха № 2 Ермаковского завода, проектирование которого велось институтом «Гипросталь», и который должен был первым построен на заводе.
Основное содержание их сводилось к изменению некоторых конструктивных параметров печей (увеличение диаметра и глубины ванны и диаметра распада электродов). Однако это правильное (с технологической точки зрения) решение влекло за собой то, что 1300 тонн строительных металлоконструкций оказались бросовыми. Тем не менее, руководство завода пошло на это непопулярное среди строителей решение, однако до этого директору и главному инженеру пришлось вынести натиск строителей, обвинения в задержке строительных и монтажных работ, угрозы Республиканского Комитета народного контроля о передаче дела в следственные органы.
М.И.Друинский и В.В. Боровиченко устояли перед этим мощным натиском, а потом был настолько удачный пуск завода и досрочное освоение проектных мощностей, что директор ЦНИИЧМ им. И.П.Бардина, академик Н.П. Лякишев признал: «Ермаковский завод ферросплавов является единственным из заводов, где столь успешно был проведен пуск и освоение закрытых ферросплавных печей».
М.И.Друинский многое сделал по созданию коллектива эксплуатационников, обучению рабочих и инженерно-технических работников профессиям электрометаллургического производства, что позволило успешно осваивать технологию производства, а его глубокие инженерные знания, замечательные организаторские способности, большой производственный и жизненный опыт особо проявлялись в трудных и критических ситуациях.
Так, летом 1967 года на строительной площадке завода уже было собрано 2000 строителей, монтажников и металлургов-эксплуатационников с тем, чтобы обеспечить ввод в действие первой очереди завода в установленный Правительством СССР срок, но проведенный анализ показал, что технически эту задачу в срок решить нельзя. Можно было обеспечить ввод всех объектов, кроме оборотного цикла технической воды, а без этого цикла пуск плавильного цеха в январе 1968 года был невозможен.
Тогда М.И. Друинскии взял на себя ответственность осуществить пуск первых двух печей без этого цикла, путем подачи технической воды для охлаждения печей непосредственно с насосной станции первого подъема, расположенной в 7 км от завода на реке Иртыш. Проектным отделом завода по заданию Друинского были выполнены рабочие чертежи, которые были выданы в производство строителям и монтажникам, но когда техническая документация была готова, представители генерального проектировщика – института «Гипросталь» отказались ее утверждать, ссылаясь на то, что в этом случае они не могут гарантировать работу завода без аварий.
Тогда М.И. Друинскии единолично утвердил документацию сам, и сам провел пуск завода настолько успешно, что результат превзошел самые оптимистические прогнозы и ожидания.
Завод начал работать. Первая плавка состоялась 18 января 1968 г., и вновь Друинский – участник первой плавки, как и ровно 25 лет назад на Актюбинском заводе. Только тогда он был рядовым участником, а теперь – руководителем, тогда – горновым, теперь – главным инженером. Изменения, внесенные по предложению Друинского в проект цеха и завода, начали давать плоды: через 5–6 месяцев (вместо норматива – 2 года) после пуска печи стали выходить на проектную мощность.
К июню 1970 года был полностью введен в действие плавильный цех № 2, в составе 8 печей мощностью по 16500 KB А каждая, и несколько вспомогательных цехов завода. Завод давал важную для народного хозяйства страны продукцию. Началась отгрузка ферросплавов и на экспорт.
Параллельно с основным производством под руководством Друинского начали проводить научно-исследовательские работы, в которых участвовали инженеры экспериментального цеха, центральной заводской лаборатории (ЦЗЛ) и плавильного цеха.
Во всех работах Друинскии принимал участие не только как руководитель, но и как непосредственный исполнитель. Он выполнял расчеты шихт для плавки различных сплавов, разработал оптимальные электрические режимы для плавки. Большой личный вклад внес он в разработку теоретических положений совместного восстановления оксидов при получении комплексных сплавов, разработку технологии их производства с использованием высокозольных каменных углей Экибастузского месторождения в качестве восстановителя при плавке. М.И. Друинский обобщил свои научные исследования в диссертационной работе на соискание ученой степени кандидата технических наук и в 1979 г. успешно защитил диссертацию.
Строительство завода интенсивно продолжалось. В июне 1974 года был введен в эксплуатацию плавильный цех № 4 такой же мощностью, как и цех № 2.
Друинский ставит перед инженерами завода новые задачи и возглавляет работу, в ходе которой электрики завода, в сотрудничестве с Московским предприятием «Энергопромремонт», в течение нескольких лет заменили обмотки трансформаторов всех печей плавильных цехов №№ 2 и 4 и таким образом довели мощность трансформаторов каждой печи с 16500 до 21000 KB А. Это стало еще одной важной предпосылкой для досрочного освоения проектных мощностей. Более того, на отдельных печах освоение проектных мощностей достигало 110–115 %.
Благодаря этому в 1974 году завод из планово-убыточного стал рентабельным предприятием. И это при столь низких оптовых ценах на ферросплавы в то время!
Наряду со своим непосредственным делом – техникой и технологией, Друинский много внимания уделял строительству жилья и объектов соцкультбыта. Благодаря ему началось проектирование и строительство Дворца металлургов со зрительным залом на 800 мест, закрытого плавательного бассейна с дорожкой 25 м, больничного комплекса с поликлиникой, которые были построены в сжатые сроки.
Друинский вынужден был заниматься и организацией проектирования и строительства и объектов теплоснабжения, водоснабжения и канализации города Ермака и всего промышленного района. Что представляли из себя сооружения, так лаконично названные словом «объекты»?
Теплоснабжение – это районная отопительная котельная в составе 8 водогрейных котлов общей мощностью 480 ГИГА калорий в час с комплексом теплосетей. Водоснабжение – это сложное гидротехническое сооружение с водозабором из канала «Иртыш-Караганда» и водозаборными сетями. Канализация – это несколько станций перекачки хозфекальных стоков с напорным коллектором протяженностью 28 км, внутригородскими сетями, системой механической и полной биологической очистки. Сооружения рассчитаны на город с населением 50 тыс. жителей с перспективой роста до 100 тыс. человек.
…Завод продолжал расширяться. В феврале 1979 года был введен в эксплуатацию плавильный цех № 1 в составе 6 закрытых печей мощностью по 33000 KB А каждая, а в начале 1980 года – печь № 61 плавильного цеха № 6 мощностью 63000 КВА. Затем ежегодно вводилась одна печь и в 1983 году цех № 6 был введен в эксплуатацию полностью (4 печи по 63000 КВА каждая). Печи такой мощности и конструкции для производства ферросплавов были ведены в стране впервые и, естественно, на первых порах возникли трудности в их освоении.
За время работы главным инженером Ермаковского завода ферросплавов Друинским М.И. была решена масштабная задача: создание крупнейшего завода по производству ферросплавов и досрочное освоение его проектных мощностей. Большой вклад он внес и в решение другой, не менее важной задачи: создание современного города Ермака с развитой инфраструктурой.
В октябре 1980 года в Павлодарском индустриальном институте организовывается новая кафедра «Машины и технология литейного производства» и Друинский избирается ее заведующим.
Начался новый период его трудовой деятельности. И вновь как в Ермаке: начинать надо было с нуля. Он провел большую работу по созданию кафедры. В короткий срок создал работоспособный педагогический коллектив и подобрал опытный учебно-вспомогательный персонал в основном из сотрудников литейного производства Павлодарского тракторного завода. Были созданы и оснащены учебные и научно-исследовательские лаборатории, лекционные аудитории были оснащены современными техническими средствами обучения. Разработаны методические руководства к лабораторным работам, курсовому и дипломному проектированию, программы производственных практик. Друинский целенаправленно вел работу по улучшению качества подготовки специалистов, внедрял новые методы обучения, им был Создан филиал кафедры на Павлодарском тракторном заводе, где ведется целевая подготовка будущих инженеров по заказам предприятий.
В литейной лаборатории кафедры, оснащенной необходимым полупромышленным оборудованием, позволяющим изготавливать отливки массой до 200 кг, выполнялись заказы предприятий по изготовлению наукоемкой продукции.
М.И. Друинский создал кафедру, представляющую собой высококвалифицированный работоспособный коллектив, обеспечивающий подготовку инженерных кадров на высоком уровне.
В 1992 году Комитет по высшей школе Министерства науки, высшей школы и технической политики Российской Федерации присвоил Друинскому М.И. ученое звание профессора.
Его производственная, научная и педагогическая деятельность (проработал он 52 года) свидетельствуют о большом вкладе, который он внес в развитие производства, науки и высшей школы Советского Союза и Казахстана».
Немного больше о сути и терминологии
Мне хочется, чтобы читатели, многие из которых не представляют, как выглядит завод и чем занимаются металлурги, образно представили, что именно Друинский делал, хочется более зримо показать тяжесть стоявших перед ним проблем. Простите, если у меня это не получится и этот текст окажется для вас лишним, но я буду стараться.
Суть металлургии ферросплавов. В природе металлов в чистом виде практически нет, все они находятся в виде химических соединений с кислородом, серой или другими элементами. И для того, чтобы получить металл в том виде, в котором мы его используем, его нужно «оторвать», скажем, от кислорода или серы.
Черная металлургия сначала отрывает от кислорода железо, а затем долго с железом возится в жидком виде. Чистит его от нежелательных примесей, добавляет в него улучшающие свойства железа химические элементы (легирует его), из затвердевшего железа (которое уже называется сталью) катает балки, листы, проволоку, трубы и в ряде случае еще и наносит на их поверхность различные покрытия. Черная металлургия СССР производила стали больше, чем какая-либо иная страна мира, и работало в отрасли 3 млн. человек.
Те химические элементы, которые добавляются к стали, также находятся в природе в виде соединений и прямо из природы для добавления к стали не годятся, их тоже нужно выделить из окислов. Этим в составе черной металлургии занимаются ферросплавщики. Они отрывают нужный элемент от кислорода, вернее наоборот – кислород от нужного элемента, и сплавляют этот элемент с железом, получая железный сплав (ферросплав). Сплавляют нужные элементы с железом чаще всего потому, что для черной металлургии в чистом виде химические элементы получать не только очень дорого, но и очень невыгодно – они очень сильно угорают при введении их в сталь.
Из всех химических элементов, которые используются для легирования, три отличаются своей универсальностью и огромным объемом производства – кремний, марганец и хром. Первые два присутствуют практически в любой стали, а хром – в любой качественной стали.
Издалека процесс получения ферросплавов кажется проще пареной репы. Возьмем производство ферросилиция – сплава железа с кремнием (кремния в этом сплаве в зависимости от марки от 12 до 80 %). Есть в природе такой минерал – кварцит, в нем где-то в среднем 97 % двуокиси кремния – химического соединения, в котором один атом кремния удерживает два атома кислорода. При нормальной температуре кремний этот кислород не отдаст. Но если рядом с молекулой двуокиси кремния положить два атома углерода и начать нагревать, то с ростом температуры сила, с которой кремний удерживает кислород, ослабевает, а сила, с которой углерод может удержать кислород, растет. И при достижении нужной температуры атомы углерода отрывают от атома кремния по одному атому кислорода, образуют с кислородом газообразное соединение моноокись углерода (угарный газ), который улетает из зоны реакции, а свободный атом кремния уходит в жидкий сплав. Что может быть проще? (Точно так же можно описать производство всех ферросплавов). Но, к сожалению, эту реакцию всем металлургам хочется провести, да редко получается провести ее хорошо.
Проблемы технологии. Давайте поговорим немного о месте, в котором ведут химические реакции получения ферросплавов.
Я уже плохо помню необходимые числа, поэтому пусть меня извинят металлурги за неточности в описании параметров. Ферросплавный цех можно представить себе в виде 9-14 этажного здания, примерно метров 50 шириной и метров 200 длинной. Внутри в длину оно разделено на две части, на два пролета – печной и разливочный, названия пролетов говорят сами за себя. В разливочном пролете, вдоль которого расположены колонны, несущие высоко вверху рельсы крановых эстакад, мостовые краны переносят пустые ковши и ковши с металлом, разливают металл в Чугунные плоские емкости – изложницы, либо ставят ковши на опрокидыватели разливочных машин. Тут же таким же способом Перемещаются короба с металлом и с различными нешихтовыми материалами, поступающими в цех. Краны называются мостовыми, поскольку как мост переброшены с одной эстакады на другую, сами они перекатываются по рельсам вдоль пролета, а по мосту крана катаются поперек пролета две крановые тележки с лебедками для подъема грузов.
Цеха, в которых процесс получения сплавов сопровождается большим количество шлака (при производстве ферросилиция шлака очень мало, около 2–3 % от веса металла), имеют и шлаковый пролет (у нас в Ермаке в цехе углеродистого феррохрома шлаковый пролет был под открытым небом). В шлаковом пролете такие же мостовые краны обрабатывают шлаковни (короба, отлитые из толстого чугуна) с жидким и затвердевшим шлаком, вываливая шлак из последних в думпкары (самоопрокидывающиеся железнодорожные платформы).
В печном пролете находятся печи, обычно не более 8. Чтобы представить себе печь, возьмите реально или мысленно кастрюлю – это кожух печи, но выполняется он сварным методом из листов 10-20-мм стали. Диаметром кожух до 12 м и в высоту до 6 м. Теперь возьмите сахар и его кусочками плотно и ровненько заложите дно кастрюли примерно на треть ее высоты – это подина или под печи. В реальной печи подина выкладывается огнеупорами – угольными блоками или магнезитовым кирпичом. Теперь обложите сахаром внутренние стенки кастрюли на всю оставшуюся высоту примерно на четверть диаметра – это стены печи. Весь сахар (подина и стены) будет моделировать то, что на печи называется футеровкой, т. е. тепловой защитой, а металлурги, глядя на вас, скажут, что вы отфутеровали кастрюлю.
На уровне подины к наружной поверхности печи в футеровке делается сквозной канал. По нему из печи будут вытекать образующиеся на подине печи в ходе плавки металл и шлак. Этот канал называется леткой, место, в котором летка выходит из наружной стенки печи, называется горном печи, а металлурги, обслуживающие горн (вытекающие металл и шлак из печи), называются горновыми. Работают они на втором этаже печного пролета, который обычно расположен в 2,5–4 м от пола цеха и называется либо площадкой горновых, либо «отметкой» с указанием числа метров от уровня земли (все этажи в цехе принято называть так – «отметка»). Выше (если считать пол первым этажом, то на третьем этаже) на уровне верхнего среза нашей кастрюли (кожуха печи) находится площадка плавильщиков, которую можно называть и колошниковой (об этом ниже). На этой площадке находится пульт управления печью и работают металлурги, которых называют плавильщиками, поскольку их задача выплавить из сырья металл.

Город Актюбинск, 1956 год. Обер-мастера М. Друинский (слева)
и И. Галаган у печи на колошниковой площадке, На заднем плане
виден колошник печи весь в пламени догорающих газов. Под
зонтом виднеется электрододержатель первого электрода, справа,
на рельсах, – завалочная машина Плюйко
Внутренний объем вашей кастрюльки, образованный сахарным подом и стенами, а в настоящей печи – огнеупорной футеровкой, называется ванной печи. Поставьте в ванну три бутылки (если влезут), а лучше три бумажных цилиндра так, чтобы между ними и футеровкой было примерно одинаковое расстояние. Этими цилиндрами вы смоделируете расположение электродов. На самом деле электроды подвешены над ванной и каждый из них может перемещаться вверх или вниз. По электродам в ванну вводится электрическая мощность. Очень большая. (Забегая вперед, и для сравнения скажу, что тот завод в Ермаке, который построил М.И. Друинский, потреблял мощность, которую должны были бы выработать три такие электростанции, как знаменитая Днепрогэс, и этой мощности хватило бы, чтобы очень ярко осветить все квартиры города с 3–4 млн, жителей.)
Электроды состоят из кожуха, выполненного из стали толщиной 3–5 мм, внутрь кожуха засыпается электродная масса. По мере нагрева эта масса сначала размягчается, заполняя кожух, а затем коксуется, превращаясь в твердый угольный цилиндрический блок, диаметром (в зависимости от мощности печи) от 0,9 до 2 м. И по этому блоку внутрь печи вводится электрический ток силою от 40 до 100 кА (килоампер). В быту лампочка в 100 ватт считается достаточно яркой, а по ее спирали идет ток менее 0,5 А, т. е. через каждый электрод проходит ток, способный зажечь до 200 000 лампочек, но между электродом и находящимся на поде печи металлом этот ток зажигает электрическую дугу, температура которой около 10 000°. Вот этими дугами и нагревается то, что подается в печь. Теперь об этом.
Продолжим моделирование. Возьмем рис и будем считать, что это руда для получения кремния – кварцит, возьмем гречку, которая смоделирует кокс, возьмем пшено, которому поручим обозначать железную стружку, смешаем все крупы и засыплем доверху в ванну, в пространство между футеровкой и электродами.
Отдельный компонент – это сырье, а вот их тщательно отдозированная смесь для получения металла называется шихтой. Для подачи в печь шихта тщательно дозируется мелкими порциями и делается это так: в специальные весы сначала засыпается (к примеру) 300 кг кварцита, затем 90 кг кокса, затем 50 кг стружки (все компоненты шихты) – и так порция за порцией. Каждая порция называется колошей. Поэтому поверхность шихты в печи – место, куда подаются (вручную или механизированно) колоши, – называется колошником.
Думаю, что для начала терминологии хватит, новую буду пояснять по ходу повествования.
Темная металлургия
В биографии Друинского для меня невероятна та скорость, с которой он повышался в цеховых должностях. В январе 1943 на Актюбинском ферросплавном была пущена первая печь, и 17-летний помощник горнового Миша Друинский впервые увидел, как она работает, а всего через год, в мае 1944-го он становится бригадиром печи! Мало этого, он вспоминал: «В августе 1943 года была введена в эксплуатацию электроплавильная печь № 3, бригадиром в нашей смене был назначен 18-летний Александр Макшаев…». А в июле 1945 года Друинский уже мастер блока печей!
Для меня невероятна та скорость, с которой он стал бригадиром ферросплавной печи – «бугром», как у нас называют бригадиров. У нас на Ермаковском заводе ферросплавов тоже был

Город Актюбинск, Казахстан, завод ферросплавов. 1944 год.
Бригадир печи (старший плавильщик) Миша Друинский.
Фото с Доски почета
ужасный период, когда из даже явно недостаточной штатной численности в 5 тысяч человек на заводе не хватало около тысячи. Было уже пущено не 3 как тогда в Актюбинске, а 26 печей, а работать на них было некому. Идешь по цеху, а везде ребята, которые по возрасту еще в армии не служили или только вернулись, редко увидишь более-менее солидного мужчину. И у нас тогда были очень молодые бригадиры, но все же это были мужчины, пожалуй, не менее 25 лет, со стажем работы у печи хотя бы 4–5 лет. Все имели среднее образование, всех обучали около года в заводском ПТУ (производственно-техническое училище). Представить себе «бугра» в 18 лет, как А.Макшаев или как сам Друинский в 19 лет, я не могу даже со скидкой на войну.
Когда-то я со злости шутил, что черную металлургию следовало бы называть «темной металлургией», поскольку, пожалуй, ни одна отрасль человеческой деятельности не отличается такой слабой доступностью к замерам параметров, как восстановительные процессы в металлургии – как доменное и ферросплавное производство. Даже медицина, даже человек, и тот более доступен изучению, чем эта чертова ферросплавная печь.
Процесс я вам выше описал и на бумаге он очень прост: оторви в руде от атомов металла атомы кислорода – и готово. Но в жизни в печь даются не чистые окислы, а руды, которые в залежах никогда не имеют одного и того же содержания металла по всему объему месторождения. И ты полагаешь, что двуокиси кремния у тебя в кварците 97,5 %, и в среднем по заводскому складу кварцита это так и есть, но в той порции, которая именно сейчас поступила в печь, ее может быть и 95 %, и 98 %. В печь даются не атомы углерода, а коксик, а в нем, кроме углерода, содержатся и зола, и летучие, и влага, и очень много влаги, если полувагоны с коксиком по пути вымочил дождь. Ты взвешиваешь 100 кг коксика, полагая, что даешь в печь 80 кг чистого углерода, а на самом деле можешь дать всего 70 кг, если эта порция коксика оказалась и очень влажной, и очень зольной, и 90 кг, если грейфер захватил порцию с дальнего угла склада, где коксик давно лежал и хорошо подсох.
А если ты не можешь ввести в печь точное количество углерода, то его недостаток или его избыток начинают менять ход химических реакций, и это приводит к тому, что ты не можешь получить из печи заданное количество металла. Себестоимость металла начинает переваливать за тот предел, что тебе определен, твоя работа на печи становится неимоверно тяжелой и все это приводит к тому, что ни ты, ни твои товарищи не получат тех денег, которые могли бы получить.
Химия тут вкратце такова. Если ты ввел в реакцию углерода меньше, чем нужно, то часть окислов кремния будет недовосстанавливаться, превращаясь в газ и уходя из печи в атмосферу и унося с собой ту электроэнергию, которую печь затратила на этот процесс. Часть окислов образует вязкий шлак, который с одной стороны, будет перекрывать изнутри ванны летку, не давая выходить металлу, поднимая его уровень в печи и давление его на стены, а с другой стороны, окислы этого шлака будут реагировать с угольными блоками футеровки печи и в конце концов размоют ее. Металл начнет литься через стены и будет тяжелейшая авария. Это только одна из десятков, а то и сотен неприятностей, которые последуют одна за другой и все вместе, если у тебя в печи недостаток углерода.
А если его избыток, то список неприятностей не намного короче, и тяжесть последствий от них не намного меньше.
Так в чем же дело? – скажете вы. Замеряйте по ходу процесса, сколько в печи углерода и окислов, и соответственно корректируйте процесс. Хотелось бы, очень хотелось бы, да нечем замерить. Я 14 лет читал всю литературу по этому вопросу, сам думал, но, по-моему, и до сих пор ситуация та же. В печи в районе электрических дуг температура 10 000°, как на поверхности Солнца, металл очень агрессивен, растворяет любую сталь так быстро, что и глазом не успеешь моргнуть, даже огнеупорная футеровка (стены и подина) выдерживают эти температуру и агрессивность жидкого металла только потому, что изнутри печи футеровку защищает полурасплавившаяся шихта, ее называют гарнисажем. Возьмите толстую свечу и зажгите. Вскоре под пламенем свечи, которое смоделирует нам электрические дуги в печи, образуется лужица жидкого парафина и она не будет вытекать из центра, поскольку ее удерживает от этого еще не расплавившийся парафин наружной части свечи. Так и в печи, но только ни дуги, ни металла, ни идущих процессов не видно, поскольку и сверху все закрыто толстым слоем шихты. Для того, чтобы понять, что происходит в печи, процесс нужно как-то замерить, а замерить его, повторю, нечем.
И остается смотреть на печь снаружи и гадать, что же этой заразе сейчас нужно: то ли кокса дать, то ли кварцита, то ли электроды перепустить (удлинить их), то ли напряжение поднять. Если угадаешь, то печь улучшит свою работу и ты с премией, если не угадаешь, то положение на печи станет еще хуже, и тогда прощай производственная премия, а это треть твоего заработка. И не только твоего, а и твоих товарищей, возможно, и всего цеха, не исключено, что и всего завода.