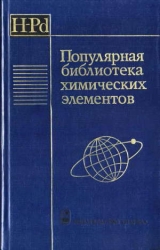
Текст книги "Популярная библиотека химических элементов. Книга первая. Водород — палладий"
Автор книги: авторов Коллектив
Жанры:
Химия
,сообщить о нарушении
Текущая страница: 28 (всего у книги 47 страниц)
Без домен?
Выше уже говорилось, что черная металлургия с точки зрения химика – занятие, мягко говоря, нелогичное. Сначала железо насыщают углеродом и другими элементами, а потом тратят много труда и энергии для выжигания этих элементов. Не проще ли сразу восстановить железо из руды. Ведь именно так и поступали древние металлурги, которые получали размягченное горячее губчатое железо в сыродутных горнах.
В последние годы эта точка зрения уже вышла из стадии риторических вопросов и опирается на совершенно реальные и даже осуществленные проекты. Получением железа непосредственно из руды, минуя доменный процесс, занимались еще в прошлом веке. Тогда этот процесс и получил название прямого восстановления. Однако до последнего времени он не нашел большого распространения. Во-первых, все предложенные способы прямого восстановления были малопроизводительными, а во-вторых, полученный продукт – губчатое железо – был низкокачественным и загрязненным примесями. И все же энтузиасты продолжали работать в этом направлении.
Положение коренным образом изменилось с тех пор, когда в промышленности начали широко использовать природный газ. Он оказался идеальным средством восстановления железной руды. Основной компонент природного газа – метан CH4 разлагают окислением в присутствии катализатора в специальных аппаратах – реформерах по реакции
2СН4 + O2 → 2СО + 2Н2.
Получается смесь восстановительных газов – окиси углерода и водорода. Эта смесь поступает в реактор, в который подается и железная руда. Оговоримся сразу – формы и конструкции реакторов очень разнообразны. Иногда реактором служит вращающаяся трубчатая печь типа цементной, иногда – шахтная печь, иногда – закрытая реторта. Этим и объясняется разнообразие названий способов прямого восстановления: Мидрекс, Пурофер, Охалата-и-Ламина, СЛ-РН и т. д. Число способов уже перевалило за два десятка. Но суть их обычно одна и та же. Богатое железорудное сырье восстанавливается смесью окиси углерода и водорода.
Но что же делать с полученной продукцией? Из губчатого железа не только хорошего топора – хорошего гвоздя отковать нельзя. Как бы ни была богата исходная руда, чистого железа из нее все равно не получится. По законам химической термодинамики даже восстановить все содержащееся в руде железо не удастся; часть его все равно останется в продукте в виде окислов. И здесь на помощь нам приходит испытанный друг – электропечь. Губчатое железо оказывается почти идеальным сырьем для электрометаллургии. Оно содержит мало вредных примесей и хорошо плавится.
Итак, опять двухступенчатый процесс! Но это уже другой способ. Выгода схемы прямое восстановление – электропечь состоит в ее дешевизне. Установки прямого восстановления значительно дешевле и потребляют меньше энергии, чем доменные печи.
Такая бездоменная технология сталеплавильного производства была заложена в проект Оскольского электрометаллургического комбината.
В нашей стране вблизи Старого Оскола сооружается большой металлургический комбинат, который будет работать именно по такой схеме. Его первая очередь уже введена в эксплуатацию.
Заметим, что прямой переплав – не единственный способ применения губчатого железа в черной металлургии. Его можно также использовать вместо металлолома в мартеновских печах, конвертерах и электросталеплавильных печах.
Способ переплава губчатого железа в электропечах бурно распространяется и за рубежом, особенно в странах, располагающих большими запасами нефти и природного газа, т. е. в странах Латинской Америки и Ближнего Востока. Однако, уже исходя из этих соображений (наличия природного газа), пока нет еще оснований считать, что новый способ когда-нибудь полностью вытеснит традиционный двухступенчатый способ доменная печь – сталеплавильный агрегат.
Будущее железа
Железный век продолжается. Примерно 90% всех используемых человечеством металлов и сплавов – это сплавы на основе железа. Железа выплавляется в мире примерно в 50 раз больше, чем алюминия, не говоря уже о прочих металлах. Пластмассы? Но они в наше время чаще всего выполняют в различных конструкциях самостоятельную роль, а если уж их в соответствии с традицией пытаются ввести в ранг «незаменимых заменителей», то чаще они заменяют цветные металлы, а не черные. На замену стали идут лишь несколько процентов потребляемых нами пластиков.
Сплавы на основе железа универсальны, технологичны, доступны и в массе – дешевы. Сырьевая база этого металла тоже не вызывает опасений: уже разведанных запасов железных руд хватило бы по меньшей мере на два века вперед. Железу еще долго быть фундаментом цивилизации.
КАК ПИСАЛ ПЛИНИЙ СТАРШИЙ. «Железные рудокопы доставляют человеку превосходнейшее и зловреднейшее орудие. Ибо сим орудием прорезываем, мы землю, обрабатываем плодовитые сады и, обрезая дикие лозы с виноградом, понуждаем их каждый год юнеть. Сим орудием выстраиваем домы, разбиваем камни и употребляем железо на все подобные надобности. Но тем же железом производим брани, битвы и грабежи и употребляем оное не только вблизи, но мещем окрыленное вдаль то из бойниц, то из мощных рук, то в виде оперенных стрел. Самое порочнейшее, по мнению моему, ухищрение ума человеческого. Ибо, чтобы смерть скорее постигла человека, соделали ее крылатою и железу придали перья. Того ради да будет вина приписана человеку, а не природе».
ДРАГОЦЕННЫЙ МЕТАЛЛ. В «Географии» древнегреческого писателя Страбона упоминается о том, что африканские народы за один фунт железа отдавали десять фунтов золота.
Извлеченное из древнескандинавских гробниц оружие также свидетельствует о драгоценности железа в прошлом – из него сделаны только острия мечей, а все остальные части – из бронзы.
ОРУЖИЕ ИЗ МЕТЕОРИТОВ. С давних времен люди пытались использовать метеоритное железо, хотя сделать это было не просто.
Бухарский эмир приказал своим лучшим оружейникам отковать ему меч из куска «небесного железа». Но сколько они ни старались, ничего не получалось. Оружейников казнили. Они погибли из-за того, что нагретый металл не поддавался ковке. Это характерно для никелистого метеоритного железа: оно куется только холодным, а при нагревании становится хрупким.
Несмотря на это, у властителя индийского княжества Джехангира в XVII в. были две сабли, кинжал и наконечник пики из метеоритного железа. Есть сведения, что из этого же материала были изготовлены шпаги Александра I и Боливара – героя Южной Америки.
САМОРОДНЫЙ ЧУГУН. Металлическое железо встречается не только в метеоритах. Еще в 1789 г. в «Словаре коммерческом» Василия Левшина о самородном железе писалось: «Так называется железо, совсем приготовленное природой в недрах земных и совсем очищенное от веществ посторонних настолько, что можно из него ковать без переплавки всякие вещи».
Крупное скопление самородного железа было найдено на южном берегу острова Диско у берегов Гренландии. Оно залегало здесь в извергнутом через пласты каменного угля базальте в виде блесток, зерен и иногда мощных глыб.
В отличие от метеоритного железа, всегда содержащего сравнительно много никеля, самородное железо содержит не более 2% никеля, иногда до 0,3% кобальта, около 0,4% меди и до 0,1% платины. Обычно оно исключительно бедно углеродом. Однако возможно образование и самородного чугуна, например в результате контакта раскаленного углерода с железной рудой. В 1905 г. геолог А. А. Иностранцев обнаружил в районе острова Русского на Дальнем Востоке небольшие пластообразные скопления самородного чугуна, находящегося на глубине 30–40 м под скальными породами морского берега. В извлеченных образцах металла содержалось около 3,2% углерода.
УБИТ ИЗ-ЗА ЖЕЛЕЗА. В 1735 г. вогул Степан Чумпин нашел у горы Благодать большой кусок магнитного железняка и показал его горному технику И. Ярцеву. После осмотра месторождения Ярцев помчался с докладом в Екатеринбург. Эта поездка была самым настоящим бегством – по следу Ярцева скакали вооруженные стражники некоронованного короля Урала Демидова, который не допускал и мысли, что новые богатства минуют его.
Ярцеву удалось уйти от погони. Первооткрыватели рудника получили вознаграждение от Горной канцелярии, но вскоре Степан Чумпин был убит. Убийца остался непойманным.
КРИСТАЛЛ ЧЕРНОВА. Знаменитый русский металлург Д. К. Чернов (1839–1921) собрал коллекцию кристаллов железа. Некоторые кристаллы, найденные им в стальных слитках, достигали длины 5 мм, большинство же не более 3 мм.
Главной ценностью коллекции был уникальный «кристалл Д. К. Чернова», описанный во многих учебниках по металловедению. Его нашел в груде стального лома шихтового двора подполковник морской артиллерии А. Г. Берсенев, служивший приемщиком на металлургическом заводе. Как удалось выяснить, кристалл вырос в 100-тонном слитке стали. Берсенев подарил его своему учителю Чернову.
Чернов тщательно исследовал кристалл. Вес его оказался 3 кг 450 г, длина 39 см, химический состав: 0,78% углерода, 0,255% кремния, 1,055% марганца, 97,863% железа.
СТАЛЬНОЕ ВИНО. В старинных журналах можно найти рецепты различных «железных» лекарств. Так, в «Экономическом журнале» за 1783 г. сообщалось: «В некоторых случаях и болезнях и самое железо составляет весьма хорошее лекарство, и принимаются с пользой наимельчайшие оного опилки либо просто, либо обсахаренные». Там же перечисляются другие лекарства того времени: обсахаренное железо, железный снег, железная вода, стальное вино («виноградное кислое вино, как, например, рейнвейн, настоять с железными опилками и получится железное или стальное вино и вкупе весьма хорошее лекарство»).
МАГНИТНЫЕ ЛЕКАРСТВА. В 1835 г. «Журнал мануфактур и торговли», сообщая о товарах, присланных из Вены в Петербург, упоминает металлические намагниченные бруски как средство от зубной и головной боли. Бруски рекомендовалось носить на шее. «Этот способ лечения ныне в моде, – сообщалось в журнале, – и по отзывам врачей, заслуживающим вероятия, помогает весьма многим».
В древности и в средние века магнит употребляли не только как наружное, но и как внутреннее. Гален считал магнит слабительным, Авиценна лечил им ипохондриков, Парацельс приготовлял «магнитную манну», Агрикола – магнитную соль, магнитное масло и даже магнитную эссенцию.
ХИМИЯ ЖЕЛЕЗА. Вероятно, вы обратили внимание, что и статья, и заметки об элементе № 26 посвящены главным образом железу-металлу. Это и не удивительно: именно этим прежде всего железо интересно для пас. Но, отдавая должное главному металлу современной техники, нельзя забывать, что:
элемент № 26 обладает значительной химической активностью, он образует множество соединений, проявляя обычно валентности 2+ и 3+;
существуют соли железной кислоты H2FeO4, но в свободном состоянии эта кислота не получена, так же как и ее ангидрид – FeO3;
природное железо состоит из четырех стабильных изотопов с массовыми числами 54, 56, 57 и 58;
железо – жизненно важный элемент; в крови человека 14,5% ее веса приходится на долю гемоглобина – красного пигмента эритроцитов, в центре молекулы которого находится атом железа.
АЛЬФА, БЕТА, ГАММА, ДЕЛЬТА. Железо – полиморфный металл, оно кристаллизуется по-разному в зависимости от температуры. При обычных условиях железо существует в виде кристаллов с объемноцентрированной решеткой. Это привычное нам альфа-железо. При медленном его нагревании наблюдаются странные, на первый взгляд, температурные остановки: тепло продолжает поступать в металл, а температура его не повышается. Первая такая остановка для чистого железа будет при 769, вторая – при 910, третья – при 1401°С. Закон сохранения энергии при этом, конечно, не нарушается. «Исчезнувшее» тепло тратится на перестройки кристаллической решетки. Они сказываются на многих свойствах металла. При 769°С, когда альфа-железо превращается в бета-железо, оно утрачивает свои магнитные свойства. При 910°С происходит обычная перекристаллизация: объемноцентрированная решетка перестраивается в гранецентрированную (это гамма-железо). При 1401°С – последняя перестройка: решетка вновь становится объемноцентрированной, но уже с большими, чем у альфа-железа, размерами элементарных кристаллов. Эта разновидность называется дельта-железом. При охлаждении расплавленного железа те же перестройки происходят в обратном порядке.
Кобальт

Несколько сот лет назад немецкая провинция Саксония была крупным по тогдашним временам центром добычи серебра, меди и других цветных металлов. В тамошних рудниках случалось находить руду, которая по всем внешним признакам казалась серебряной, но при плавке получить из нее драгоценный металл не удавалось. Хуже того, при обжиге такой руды выделялся ядовитый газ, отравлявший рабочих. Саксонцы объясняли эти неприятности вмешательством нечистой силы, коварного подземного гнома кобольда. От него же исходили и другие опасности, подкарауливающие рудокопов в подземельях. В те времена в Германии даже читали в церквах молитвы о спасении горняков от злого духа кобольда… И со временем, когда саксонцы научились отличать «нечистую» руду от серебряной, они ее назвали «кобольд».
В 1735 г. шведский химик Георг Брандт выделил из этой «нечистой» руды серый со слабым розоватым оттенком неизвестный металл. Имя «кобольд», или «кобальт», сохранилось и за ним.
От венецианского стекла до светофоров
В диссертации Брандта, посвященной новому металлу, говорилось, в частности, о том, что из металла можно изготавливать сафру – краску, придающую стеклу глубокий и очень красивый синий цвет. Но еще в Древнем Египте было известно синее стекло, сделанное по тщательно скрываемым рецептам.
В средние века ни одно из государств Европы не могло соперничать в производстве стекла с Венецианской республикой. Чтобы оградить секреты варки цветных стекол от чужого любопытства, правительство Венеции в XIII в. специальным указом перевело все стекольные фабрики на уединенный остров Мурано. О том, какими способами охранялись там секреты производства, можно составить себе некоторое представление по такой истории. Однажды с острова бежал подмастерье по имени Джиорджио Белеринo, а вскоре в одном из немецких городков сгорела стекольная мастерская. Ее владелец – его звали Белерино – был заколот кинжалом…
И все-таки, несмотря на столь жестокие меры, секреты варки цветного стекла стали известны в других государствах. В 1520 г. Вейденхаммер в Германии нашел способ приготовления краски для синего стекла и по дорогой цепе стал продавать ее… венецианскому правительству! Еще через 20 лет богемский стекольный мастер Шюрер тоже стал делать синюю краску из какой-то руды, известной ему одному. С его помощью такую краску стали изготовлять и в Голландии. Современники писали, что стекло окрашивается «цаффером», но что собой представлял этот продукт – никто не знал. Только через столетие (в 1679 г.) известный химик Иоганн Кункель подробно описал процесс получения краски, но оставалось неизвестным, из какой именно руды ее делают, где эту руду искать и какая ее составная часть обладает красящим свойством.
Только после исследования Брандта было выяснено, что сафр, или цаффер, – продукт прокаливания руды, богатой кобальтом, содержит окислы кобальта и множество окислов других металлов. Сплавленный затем с песком и поташом цаффер образовывал смальту, которая и представляла собой краску для стекла. Кобальта в смальте содержалось немного – всего 2–7%. Но красящая способность окиси кобальта оказалась большой: уже 0,0001% ее в шихте придает стеклу голубоватый оттенок.

Таким представляли кобольда. Рисунок XVII в.
Стеклоделы средних веков пользовались свойствами кобальта бессознательно, отыскав их чисто опытным путем. Разумеется, это не может даже в самой малой степени умалить в наших глазах замечательное искусство этих тружеников.
Помимо смальты, существуют и другие кобальтовые красители: синяя алюминиево-кобальтовая краска – тенарова синь; зеленая – комбинация окислов кобальта, хрома, алюминия, магния и других элементов. Краски эти красивы и достаточно стойки при высокой температуре, но не всегда имеют хорошую кроющую способность. Значение их гораздо меньше, чем смальты. Заслуживает внимания другое: изменчивость окраски соединений кобальта.
Чудеса превращения красок известны еще с XVI столетия. Профессор Базельского университета химик и врач Парацельс показывал написанную им самим картину. Она изображала зимний пейзаж – деревья и пригорки, покрытые снегом. Дав зрителям насмотреться, профессор слегка подогревал картину, и прямо на глазах у всех зимний ландшафт сменялся летним: деревья одевались листвой, на пригорках зеленела трава. Это производило впечатление чуда.
Для современного химика история с картиной Парацельса выглядит довольно просто. Такой эффект могли дать, в частности, кобальтовые краски. Хлористый кобальт, к которому добавлено соответствующее количество хлористого никеля, почти бесцветен. Но при нагревании эти соли теряют кристаллизационную воду, и цвет их меняется.
В 1737 г. один французский химик открыл свойство кобальтовых солей окрашиваться под действием тепла и использовал их в качестве симпатических чернил. Написанное ими на бумаге становится видимым только после того, как бумагу нагреют. Сейчас эта особенность солей кобальта имеет практическое значение в лабораторной технике: раствором кобальтовых солей метят фарфоровые тигли. После прогрева такая метка четко выступает на белой поверхности фарфора.
Окраска стекол соединениями кобальта имеет немаловажное значение и в наше время, хотя существуют более дешевые красители.
Для технических целей часто нужны стекла, поглощающие и пропускающие лучи определенного цвета. Такие стекла необходимы в фотографии, сигнализации, колориметрическом анализе и других случаях. Смальтой в наше время не пользуются, а употребляют непосредственно окись кобальта, которую вводят в состав шихты, загружаемой в стекловаренную печь.
Стекла, применяемые для сигнальных огней, должны давать резкий, отчетливый свет. Нужно исключить возможность ошибочного восприятия сигнала даже в условиях плохой видимости, даже при больших скоростях транспорта и несовершенстве человеческого зрения. А для этого необходимо, чтобы стекла световых сигнальных устройств пропускали только свет волны точно определенной длины.
У стекол, окрашенных окисью кобальта, нет соперников по прозрачности, а добавка в такое стекло ничтожных количеств окиси меди придает ему способность задерживать некоторые лучи красной и фиолетовой части спектра. Для фотохимических исследований бывают нужны стекла, совершенно не пропускающие желтых и оранжевых лучей. Этому условию отвечают кобальто-рубиновые стекла: на окрашенное кобальтом синее стекло накладывается нагретое стекло, окрашенное в красный цвет соединениями меди, – так называемый медный рубин. Хорошо известно применение окиси кобальта для придания красивого, очень устойчивого темно-синего цвета фарфоровым и эмалированным изделиям.
Кобальт – легирующий металл
В 1912 г. о кобальте писали: «До настоящего времени металлический кобальт с точки зрения потребления не представляет интереса. Были попытки ввести кобальт в железо и приготовить специальные стали, но последние не нашли еще никакого применения». Действительно, в начале нашего века первые попытки использовать кобальт в металлургии были неудачными. Было известно, что хром, вольфрам, ванадий придают стали высокую твердость и износоустойчивость при повышенных температурах. Сначала создалось впечатление, что кобальт для этой цели не годится – сталь плохо закаливалась, точнее, закалка проникала в изделие на очень небольшую глубину. Вольфрам, хром и ванадий, соединяясь с растворенным в стали углеродом, образуют твердые карбиды, кобальт же, как оказалось, способствует выделению углерода в виде графита. Сталь при этом обогащается несвязанным углеродом и становится хрупкой. В дальнейшем это осложнение было устранено: добавка в кобальтовую сталь небольшого количества хрома предотвращает графитизацию; такая сталь хорошо закаляется.
Теперь кобальт, как и вольфрам, незаменим в металлообработке – он служит важнейшей составной частью инструментальных быстрорежущих сталей. Вот, например, результат сравнительных испытаний трех резцов. В стали, из которой они были изготовлены, углерод, хром, ванадий, вольфрам и молибден содержались в одинаковых количествах, различие было лишь в содержании кобальта. В первой, ванадиевой, стали кобальта совсем не было, во второй, кобальтовой, его было 6%, а в третьей, суперкобальтовой, – 18%. Во всех трех опытах резцом точили стальной цилиндр. Толщина снимаемой стружки была одинаковой – 20 мм, скорость резания тоже – 14 м/мин.
Что же показал эксперимент? Ванадиевый резец затупился, пройдя 7 м, кобальтовый – 10 м, а резец из суперкобальтовой стали прошел 1000 м и остался в хорошем состоянии! Таким образом, для резкого повышения износоустойчивости и режущих свойств стали кобальт должен входить в ее состав в значительных количествах.
В 1907 г. в промышленности появились твердые сплавы, не содержащие железа, – стеллиты (от латинского слова Stella – звезда). Один из лучших стеллитов содержал больше 50% кобальта. И в твердых сплавах, которые в наше время стали важнейшим материалом для металлорежущих инструментов, кобальт играет не последнюю роль. Карбид вольфрама или титана – основной компонент твердого сплава – спекается в смеси с порошком металлического кобальта. Кобальт соединяет зерна карбидов и придает всему сплаву большую вязкость, уменьшает его чувствительность к толчкам и ударам.
Твердые сплавы могут служить не только для изготовления режущих инструментов. Иногда приходится наваривать твердый сплав на поверхность деталей, подвергающихся сильному износу при работе машины. Такой сплав на кобальтовой основе может повысить срок службы стальной детали в 4–8 раз.
