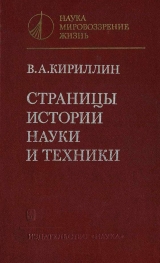
Текст книги "Страницы истории науки и техники"
Автор книги: Владимир Кириллин
сообщить о нарушении
Текущая страница: 19 (всего у книги 34 страниц)
Сталь, сплав железа, углерода (до 2 %) и некоторых других элементов, – наиболее широко применяемый металл, используемый во всех отраслях производства. Сталь обладает прочностью, ковкостью (является деформируемой), в то время как чугун, как правило, хрупок, а чистое железо слишком легко деформируется (является слишком мягким). Эти ценные свойства стали достигаются тем, что по содержанию углерода она стоит между чугуном и железом. В зависимости от химического состава сталь подразделяют на два вида: углеродистую и легированную. Углеродистые стали (машиностроительная, иначе говоря, конструкционная, и строительная) содержат не менее 0,6 % углерода и 0,4–1,1 % марганца. Легированные стали обычно разделяют на низколегированные, среднелегированные и высоколегированные, отличающиеся друг от друга количеством легирующих добавок (элементов); первые содержат не более 2,5 % легирующих элементов, вторые – 2,5–5,5 %, третьи – свыше 5,5 %. В зависимости от того, какой из легирующих элементов преобладает, сталь именуется никелевой, хромистой, хромоникелевой и т. д. Различные сорта стали могут обладать существенно отличными друг от друга свойствами. Весьма различна и стоимость разных сортов стали. Существуют нержавеющая, жаропрочная, износоустойчивая и другие сорта стали.
Сталь в настоящее время получают главным образом из смеси передельного чугуна со стальным ломом (поэтому годовая выплавка стали существенно больше выплавки чугуна) в кислородных конвертерах, мартеновских печах и электропечах. В этой книге представляется возможным лишь весьма кратко остановиться на существе названных методов производства стали. При этом мы откажемся от применявшегося в основном до сих пор хронологического способа изложения и рассмотрим весь период развития производства стали, вплоть до настоящего времени.

Рис. 24. Кислородный конвертер.
1 – корпус; 2 – днище; 3 – опорные подшипники; 4 – шлем.
Современный кислородно-конвертерный способ производства стали состоит в том, что в стальной сосуд – конвертер (от лат. converto – изменяю, превращаю) загружается стальной лом (скрап) и заливается расплавленный чугун (рис. 24, 25). Изнутри поверхность конвертера обложена огнеупором толщиной до 1 м. Из рисунков видно, что массивный конвертер может поворачиваться на специальных опорных подшипниках. Когда происходит загрузка скрапа (см. рис. 25, а) и заливка жидкого чугуна (см. рис. 25, б), а также выпуск готовой стали и затем жидкого шлака, конвертер находится в наклонном (при выпуске стали, близком к горизонтальному) положении.

Рис. 25. Схема кислородно-конвертерного процесса.
а – загрузка металлолома; б – заливка чугуна; в – продувка.
Кислород подается снизу. Правда, за последнее время начала практиковаться подводка кислорода сверху (см. рис. 25, в), в чем имеются свои преимущества. Какого-либо топлива для конвертера не требуется: необходимое количество тепла выделяется в результате соединения кислорода с находящимися в чугуне примесями – кремнием, углеродом и др. Поэтому металл в конвертере всегда находится в жидком состоянии. Количество углерода в готовой стали регулируется длительностью процесса: чем дольше длится процесс, тем больше углерода выгорает и меньше его остается в стали. Обычно продувка конвертера кислородом длится 15–25 мин. Тепло газов, образующихся во время продувки конвертера кислородом, используется – за конвертером, как правило, устанавливается котел-утилизатор, задачей которого является использование тепла отходящих газов и который собственной топки пе имеет.
Кислородный конвертер способен переплавлять в сталь чугуны с добавкой большого количества скрапа (25 % и более) и руды (до 5 %). Кислородно-конвертерный процесс является очень экономичным. По сравнению с мартеновским процессом экономия на капитальных вложениях составляет 20–25 %, увеличение производительности труда – 25–30, снижение себестоимости стали – 2–4 %.
Продувка чугуна чистым кислородом впервые была применена в 1936 г. советским инженером Н. И. Мозговым. Первый промышленный кислородный конвертер был построен в Австрии в 1952 г.
Значительно раньше в черной металлургии для выплавки стали из чугуна начали применяться конвертеры с продувкой чугуна воздухом снизу. Широкое применение получили бессемеровский и томасовский процессы производства стали.
Английский инженер и изобретатель Г. Бессемер (1813–1898) в 1856 г. предложил новый способ выплавки стали, названный его именем и получивший широкое применение. Однако бессемеровский метод производства стали при всей его внешней схожести с кислородно-конвертерным имел очень существенный недостаток. Дело заключалось в том, что при продувке чугуна воздухом плохо выгорали фосфор и сера, и поэтому, если в чугуне (в железных рудах) содержалось относительно много фосфора и серы, сталь получалась низкого качества. Единственный выход состоял в том, чтобы использовать железные руды, содержащие немного фосфора и серы. Но таких руд оказалось мало.
С. Томас (1850–1885), английский инженер-металлург, предложил в 1878 г. существенную модификацию бессемеровского конвертерного метода выплавки стали, заключавшуюся в том, что он заменил кислую динасовую футеровку бессемеровских конвертеров на основную и для лучшего связывания фосфора вводил известь. Таким путем была достигнута возможность использования более низкосортных железных руд, содержащих много фосфора и серы. Однако качество стали, получаемой томасовским процессом, было низким.
Поэтому, когда в 1864 г. французский металлург П. Мартен (1824–1915) разработал метод выплавки стали, впоследствии названный его именем, а несколько позднее была сооружена первая мартеновская речь, все большее развитие начал получать мартеновский метод производства стали. Хотя мартеновский процесс был медленнее и менее экономичен по сравнению с конвертерными процессами Бессемера и Томаса, он имел неоспоримые преимущества перед ними: меньшую требовательность к составу железорудного сырья, возможность использовать большое количество скрапа и получать сталь более высокого качества. По этой причине в середине XX в. около 80 % всей производимой в мире стали получали в мартеновских печах.
Как следует из сказанного выше, в середине XX в. у мартеновского метода выплавки стали появился сильный конкурент – кислородно-конвертерный метод, соревнование между которыми все более склонялось в пользу последнего. В 70-х годах XX в. строительство мартеновских печей практически было прекращено.
На существе мартеновского способа производства стали с учетом всего сказанного мы остановимся совсем кратко. Плавка стали из чугуна и стального лома происходит в верхней части мартеновской печи – камере из огнеупорных материалов, в которую поступает нагретый горючий газ (например, природный), служащий топливом (иногда в мартеновских печах используется жидкое топливо, например, мазут), и нагретый воздух. Продукты сгорания топлива, образующиеся в камере, поступают в так называемые регенеративные нагреватели, через каждый из которых поочередно пропускаются горячие продукты сгорания, повышающие температуру набивки регенеративных нагревателей (обычно набивка представляет собой кладку из огнеупорного кирпича), воздух и горючий газ; последние нагреваются за счет охлаждения набивки нагревателей, т. е. в конечном итоге за счет тепла продуктов сгорания. Готовая сталь выпускается черев выпускное отверстие в ковш. Все, о чем было сказано, не более чем описание простейшей схемы мартеновской печи и мартеновского процесса.

Рис. 26. Схема дуговой электропечи прямого действия.
Для получения стали, особенно высококачественной, используются также электрические печи различных конструкций. На рис. 26 показана одна из наиболее распространенных в электрометаллургии печей – электродуговая печь прямого действия. Свое название печь получив потому, что электрические дуги зажигаются непосредственно между электродами (на рисунке их показано три) и нагреваемым телом, в данном случае жидким металлом.
Преимуществами электропечей перед другими агрегатами, предназначенными для выплавки стали, обеспечившими им приоритет в производстве высококачественной легированной стали, являются: возможность нагрева металла до высокой температуры за счет электрической дуги практически без внесения в металл каких-либо примесей; восстановительная атмосфера печи, делающая излишним процесс раскисления стали, т. е. удаления из нее растворенного в ней кислорода[233]233
Раскисление металла осуществляется добавлением к нему химических элементов (Al, Si и др.), образующих с кислородом устойчивые соединения.
[Закрыть]; меньший угар легирующих элементов и некоторые другие. В последнее время электрометаллургия все шире используется и в производстве обычной углеродистой стали.
Лет двадцать тому назад казалось, что кислородно-конвертерный метод выплавки стали, в силу его больших, названных выше преимуществ на многие годы останется наиболее распространенным. Рано, конечно, говорить, что, скажем, к концу XX в. ему придется уступить лидерство еще более прогрессивному способу производства стали. Но нельзя обойти молчанием вопрос так называемого прямого получения железа, т. е. процесс получения железа и стали непосредственно из рудных материалов, минуя стадию выплавки чугуна в доменных печах, не используя кокс. Однако ограничимся здесь только тем, что заметим: прямое получение железа является перспективным направлением в развитии металлургии; в ряде стран мира, в том числе в Советском Союзе, создаются соответствующие промышленные установки.

Рис. 27. Схема прокатки (поперечной)
1 – прокатываемый материал; 2, 3 – валки.

Рис. 28. Схема прокатки цельнокатаных труб.
В черной металлургии обычно различают три основные стадии получения и переработки металла, три передела: 1) выплавка чугуна – доменное производство, 2) выплавка стали – сталелитейное производство, 3) прокатка – способ обработки металла давлением, осуществляемый путем обжатия металла вращающимися валками.
Схема такого процесса показана на рис. 27. Прокатка производится чаще всего на металлургических предприятиях. Крупные заводы черной металлургии обычно имеют все три передела.
Прокатка производится на прокатных станах. Продукт прокатки металла – прокат может быть в форме листов (как толстых, так и тонких), ленты, полос, рельсов, труб, проволоки, а также в виде сложных фасонных профилей. Прокатные станы для производства стального проката делятся на две основные группы, а процесс прокатки – соответственно на две стадии. Первая стадия – это производство заготовок из слитков, получаемых в сталеплавильных печах. Заготовки, более удобные чем слитки для производства готового проката, обычно делаются одного из двух типов: либо квадратного или прямоугольного сечения, размером чаще всего от 50x50 до 400x400 мм2, либо плоского сечения. Первые, именуемые блюмами, предназначаются для производства сортового металла (не листа), а прокатные станы, на которых они делаются – блюмингами. Второй тип заготовок, получивших название слябов, предназначается для выделки листа, а прокатные станы на которых делаются слябы, называются слябингами. Для производства цельнокатаных труб (без сварного шва) на блюмингах делаются специальные заготовки круглого сечения. Схема изготовления цельнокатаных труб представлена на рис. 28 и пояснений не требует. На входе в блюминг или слябинг слитки должны быть, конечно, хорошо нагреты (сохранять тепло после сталелитейного процесса).
Готовый прокат производится из соответствующих нагретых заготовок. Стальной прокат соответствующего профиля – необходимая и высокоэкономичная продукция для потребителей. Поэтому большая часть стали (как и многих других металлов, например алюминия, меди, латуни, цинка, свинца и их сплавов) выпускается в виде проката.

Рис. 29.Схема непрерывной разливки стали.
За последние десятилетия все большее распространение получает непрерывная разливка стали. Существо этого процесса, схема которого представлена на рис. 29, состоит в том, что жидкая сталь, полученная в сталеплавильных печах (особенно удобно сочетание непрерывной разливки стали с кислородными конвертерами, так как цикл плавки стали в кислородном конвертере близок по времени к циклу работы установки непрерывной разливки стали), поступает в интенсивно охлаждаемый водой кристаллизатор 3, где жидкая сталь начинает затвердевать вначале преимущественно около стенок кристаллизатора. Образующаяся оболочка будущей заготовки движется вниз. При этом вследствие непрерывного дальнейшего охлаждения (обрызгивания) водой из форсунок, не показанного на рисунке, будущая заготовка затвердевает полностью, а не только у поверхности.
Таким образом, жидкий металл непрерывно подается сверху через промежуточное разливочное устройство 1, 2 в кристаллизатор; затвердевающий сначала с внешней поверхности металл движется под действием роликов и валков (4, 5) вниз; после того как металл затвердевает полностью, его режут (6) на отдельные куски – заготовки.
Конечно, процесс непрерывной разливки стали далеко не так прост, как может показаться из приведенного описания. В этом описании по причине оправданного (с нашей точки зрения) стремления к краткости изложения совершенно не были затронуты такие, например, вопросы, как подача смазки на внутренние поверхности кристаллизатора для лучшего скольжения металла, необходимость предохранения от окисления поверхности жидкого металла инертным газом или синтетическим шлаком и др.
Однако непрерывная разливка стали имеет столь большие преимущества, что ею оснащаются в нашей стране практически все вновь строящиеся крупные кислородные конвертеры. Главные преимущества непрерывной разливки стали заключаются в следующем: сокращаются капитальные вложения, так как становятся излишними такие дорогостоящие агрегаты, как блюминги, слябинги, чугунные изложницы и кое-что другое; улучшается качество металла, его однородность вследствие того, что затвердевание происходит быстрее; уменьшение обрези головной и донной частей заготовок приводит к экономии 10–15 % металла.

Рис. 30. Схемы установок непрерывной разливки стали.
а – вертикального, б – радиального, в – криволинейного типа.
Установки непрерывной разливки стали, как это можно видеть из рис. 30, могут быть вертикального, радиального и криволинейного типов. Преимущество радиального и особенно криволинейного типов установок перед вертикальным – в их меньшей высоте.
Все остальные металлы, кроме железа и его сплавов, получили в промышленности название цветных металлов.
Число их велико, значение для промышленности – огромное. Скажем только несколько слов об алюминии, занимающем третье место по распространенности в природе среди всех других элементов и первое – среди металлов. Алюминий и его сплавы обладают очень важными свойствами: прочностью, легкостью, пластичностью и высокой электропроводностью. Алюминий и его сплавы имеют очень широкое применение, включая изделия для быта. Но особое значение они получили для авиации (для всех тех изделий, где легкость должна сочетаться с прочностью и пластичностью) и электротехники. Токопроводящая часть линий дальней электропередачи, в частности, делается в настоящее время исключительно из алюминия.
Получают алюминий чаще всего путем электролиза глинозема (Al3O2), содержащегося в некоторых алюминиевых рудах. По величине производства алюминий занимает среди металлов второе место (вслед за железом).
Наличие универсального двигателя и успехи металлургии уже в XVIII в. создали предпосылки для появления рабочих машин, прежде всего в области машиностроения. Однако вплоть до последней четверти XVIII в. даже в наиболее крупных мануфактурах, занимавшихся обработкой металла, основные процессы производились за счет мускульной силы человека. При этом использовались многочисленные инструменты и орудия (клещи, молотки, ножницы, сверла и др.). Но это не изменяло дела.

Рис. 31. Лучковый токарный станок.
Даже предшественник современных токарных и фрезерных станков – представленный на рис. 31 лучковый токарный станок приводился в действие мускулами человека.
Принцип действия этого станка очень прост. Большое значение для его работы имела простая крепкая веревка, верхние концы которой привязывались к твердо закрепленной гибкой жерди. Опускаясь вниз, веревка обвивала вал станка и затем закреплялась своим нижним концом на доске-педали. Если человек периодически нажимал на педаль, то, как это видно из рисунка, вал станка (в данном случае валом является само изделие) приходил во вращение. Заметим, между прочим, что это устройство для привода в движение вала (изделия) станка очень напоминает способ добычи огня первобытными людьми.
Инструментом, с помощью которого производилась обработка изделия, рабочий действовал вручную.

Рис. 32. Токарный станок с суппортом.
Коренные усовершенствования в ручной токарный станок были внесены приводом его в действие от универсального двигателя (вначале от паровой машины) и изобретением суппорта. Суппортом (от лат. supporto – поддерживаю) называется главный узел металлорежущего станка, на котором закрепляется и вместе с которым перемещается режущий инструмент (резец).
Идея суппорта нашла отражение в сконструированном русским механиком и изобретателем А. К. Нартовым (1693–1756) токарном станке. Первый же токарный станок с механическим суппортом, представленный на рис. 32, был создан в 1795 г. английским механиком Г. Модели (1771–1831). В 1797 г. Модели построил вполне работоспособный токарный станок с самоходным суппортом и чугунной станиной.
Первая половина XIX в. была ознаменована большими успехами в станкостроении. Усовершенствованный суппорт нашел широкое применение не только на токарных, но и на других станках. В машиностроении появились и все в большей мере использовались строгальные, шлифовальные, фрезерные и другие металлообрабатывающие станки. Точность металлообработки повышалась.

Рис. 33. Кривошипный (эксцентриковый) (а) и винтовой (б) прессы.
Начала находить применение, а в последующем получила широкое развитие обработка металла давлением. Речь здесь идет не о прокатных станах, используемых, как уже говорилось, чаще всего на металлургических заводах, а о разного рода прессах, которые по способу приведения их в действие разделяются на гидравлические и механические. На рис. 33 показаны кривошипный, или эксцентриковый, пресс и винтовой пресс, схема работы которых ясна из рисунка. В этом случае различие между ними определяется основным механизмом (в данном случае кривошипным механизмом и винтом). С точки зрения этого признака (характера основного механизма) можно было бы назвать немало типов прессов. Металл на них куется или штампуется чаще всего в горячем состоянии (исключение – листоштампоночные и вырубные прессы).


Рис. 34. Способы прессования.
Большое применение, особенно за последние десятилетия, находит метод прессования изделий и полуфабрикатов из цветных металлов, сплавов и пластических масс, осуществляемый как при горячем, так и при холодном состоянии материала. При такого рода прессовании особое значение имеют два элемента машины: матрица – инструмент, имеющий сквозное отверстие (иногда углубление), с помощью которого производятся штамповка, прессование или волочение, и пуансон – инструмент, оказывающий непосредственное давление на материал или передающий его через пресс-шайбу. Во всем этом гораздо проще разобраться, посмотрев на рис. 34, па котором представлены оба названных варианта прессования (с пресс-шайбой и без нее).
Следует заметить, что метод обработки металла (и других материалов, в частности пластических масс) давлением оказался весьма прогрессивным. Во-первых, снижаются потери металла (отсутствие стружки, всегда имеющейся при обработке резанием), и, во-вторых, во многих случаях увеличивается скорость обработки, а вместе с тем и производительность труда.
ЧАСТЬ ВТОРАЯ
Наука и техника в XIX–XX вв
Глава пятая
Диалектический материализм
XIX век – век рождения марксизма – науки о заколах развития природы и общества, революционного коммунистического мировоззрения. Учение Маркса, объединяющее в себе диалектический и исторический материализм, политическую экономию и теорию научного коммунизма, знаменовало переход на новый, более высокий этан развития общественной мысли, превратило социализм из утопии в науку.
Ленин – величайший ученый и революционер, верный последователь Маркса и Энгельса – дал дальнейшее развитие марксизму, поднял его на новую ступень. Ленинизм – это марксизм эпохи империализма и социалистических, пролетарских революций. Имена Маркса и Ленина стали неразделимы.
Великая Октябрьская социалистическая революция, совершившаяся в 1917 г. в России под руководством партии большевиков во главе с Лениным, открыла новую страницу в истории: научный социализм стал реальным, живым делом миллионов трудящихся.
Естественные науки получили в XIX и особенно XX в. необычайно быстрое развитие. Научно-техническая революция, начало которой относится к середине XX в., явилась следствием высокого уровня развития науки и производства (наука может дать много новых идей и разработок, а производство может их реализовать; кроме того, и это очень важно, производство дает науке сложные и совершенные приборы и другие устройства, стимулирующие развитие науки) и, самое главное, еще более ускорила научно-технический прогресс. Говоря в этой книге о развитии естественных наук и техники в XIX и XX вв., мы вынуждены будем коснуться только некоторых областей, но постараемся сделать это так, чтобы в их числе оказались наиболее важные.