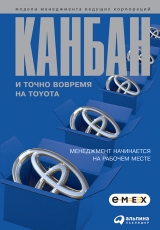
Текст книги "Канбан и «точно вовремя» на Toyota. Менеджмент начинается на рабочем месте"
Автор книги: авторов Коллектив
Жанры:
Деловая литература
,сообщить о нарушении
Текущая страница: 7 (всего у книги 15 страниц)
«Точно вовремя»
«Когда я только пришел в компанию, кто-то сказал при мне, что детали должны собираться „точно вовремя“. Я отметил про себя это интересное выражение, но не заметил, чтобы кто-нибудь следовал этому правилу. Я стал придумывать способ реализовать этот принцип „точно вовремя“ на практике. Возможно, я не такой, как все: у меня есть привычка мысленно менять направление какого-нибудь процесса. Применив этот прием, я пришел к выводу, что все, что нам нужно сделать, – это разрешить рабочим, занятым на следующем этапе производства, самим получать то, что им требовалось, когда требовалось и сколько требовалось. Таким образом, я просто изменил направление процесса транспортировки.
Раньше во всех компаниях (наша тоже не была исключением) по завершении одного процесса его продукт отправлялся на следующий процесс. В некоторых случаях следующие процессы выполняли роль промежуточных складов. Там хранилось все, что угодно, но за доставку деталей следующему процессу отвечал процесс, который их произвел. Я решил, что за транспортировку должен отвечать следующий процесс. А что касается предыдущего процесса, то он должен просто складывать то, что произвел, на пол. Когда следующему процессу понадобится эта продукция, он сам за ней придет, но только тогда, когда она ему действительно понадобится.
Когда следующий процесс приходил на предыдущий, чтобы забрать материалы, предыдущему приходилось возмещать то, что было изъято. При такой системе промежуточные склады не нужны. Предыдущий процесс производил только то, что требовалось, и сам это хранил. Когда складывать продукцию было уже некуда, производство просто останавливалось.
У этой системы есть целый ряд преимуществ. Поскольку рабочих много, а у станков и оборудования есть избыточная мощность, некоторые менеджеры считают, что позволять им простаивать было бы расточительством. Поэтому они продолжают производить. Также они знают, что у них недостаточно места для хранения. Вот почему я говорю им, что они должны хранить все, что произвели, именно там, где это произведено. И они должны возмещать то, что у них забрали. Тогда все рабочие будут знать, что им делать, просто взглянув на запасы. Рабочие смогут определять, как они работают: слишком быстро или слишком медленно. Предположим теперь, что материалов много, но места для хранения готовой продукции нет, и поэтому рабочие вынуждены простаивать. В этом случае и бригадиры, и рабочие поймут, что, возможно, столько людей на данном процессе вовсе не требуется. Благодаря этому задача расстановки людей упрощается. С изменением порядка транспортировки система "точно вовремя"» из идеи превратилась в реально применимый на практике метод».
Транспортировку осуществляет следующий процесс
Автомобили собирают из десятков тысяч деталей. Процессы производства автомобиля состоят из множества операций. Встроить все эти процессы и операции в систему «точно вовремя» – задача крайне сложная. На практике, чтобы ее решить, приходится довольно часто менять производственные планы.
Перемены в производственных планах обусловлены множеством причин: это изменение рыночной конъюнктуры и условий, в которых приходится трудиться предприятию. Когда эти факторы налицо и если в предыдущем процессе появилась проблема, то в следующем процессе может возникнуть дефицит деталей или других вещей. И тогда следующим процессам придется волей-неволей остановить свои линии или изменить свои планы.
Если менеджмент проигнорирует эти реальные условия и спустит на каждый участок жесткий производственный план, это может привести к ряду нежелательных последствий, и в том числе к: 1) производству деталей без учета потребностей следующего процесса и 2) созданию серьезного дефицита и одновременно избытка ненужных деталей. План все равно придется менять, что будет совсем непросто. Менеджерам потребуется немало времени на то, чтобы дать новые указания и внести коррективы. Даже если менеджеры и справятся со своей задачей, все равно останутся такие прозаические проблемы, как уборка, защита от ржавчины и подсчет. Все это может потребовать больших трудозатрат. Ясно, что так вы только создадите условия для роста потерь на производстве.
Но возможно и другое, еще более нежелательное последствие. Занятые на всех этих линиях рабочие перестанут понимать, что нормально, а что нет, и в результате не смогут правильно реагировать на аномалии. Рабочих слишком много, и линия выпускает чрезмерное количество продукции. Если ситуация именно такова, но о ней известно, то можно принять соответствующие меры. Но когда люди оказываются заложниками плана, они ничего не предпринимают. При взаимодействии этих факторов потери возникают одна за другой, что может привести к ухудшению финансового положения компании.
Однако если один процесс может доставлять другим процессам нужные им вещи в нужное время и в нужных количествах, то упоминавшиеся выше напрасные потери на производстве можно устранить, тогда работа по улучшению продвинется на шаг вперед. Для этого менеджмент должен отказаться от установления производственных планов для всех процессов или от той системы, при которой предыдущий процесс доставляет свою продукцию последующему. Эта система не позволяет понять, сколько деталей действительно нужно последующему процессу, и на предыдущем может возникнуть перепроизводство. Когда какой-нибудь процесс производит лишние детали или доставляет следующему ненужные сырье и материалы, производительность падает.
Родилась новая идея – перевернуть процесс, так чтобы последующий процесс сам забирал с предыдущего то, что ему нужно. Вместо того чтобы предыдущему процессу отправлять на следующий то, что он произвел, направление этого потока меняется таким образом, что последующий процесс сам забирает с предыдущего то, что нужно, и тогда, когда нужно. Предыдущий процесс выпускает именно то количество, которое изъято. Так можно решить все упомянутые выше разнообразные проблемы.
Последний производственный процесс – финишная сборочная линия. Отправным пунктом должна стать именно она, и производственный план нужно спускать только этой последней линии. Он показывает, какие виды машин и в каком количестве надо сделать и когда. Сборочная линия идет на предыдущий процесс, чтобы забрать нужные ей детали. Так инициируется движение вспять по всем этапам производственного процесса, и даже распределение сырья и материалов оказывается сразу же связанным одной цепью с остальными производственными процессами. Появляется возможность реализовать концепцию «точно вовремя» на практике и существенно сократить затраты управленческого труда.
Канбан используется при этом, чтобы забирать детали или давать указания об их производстве. Благодаря системе канбан производство «точно вовремя» может осуществляться бесперебойно, и можно устранить многие напрасные потери на производстве. Эффективность управления производством повышается. Кроме того, сборочные линии становятся более гибкими, что также уменьшает возможность потерь.
Автоматизация «с человеческим лицом»
Другой столп системы Toyota – автоматизация «с человеческим лицом».
Многие из наших станков приводятся в действие одним нажатием кнопки. Также у нас много высокоскоростных и высокопроизводительных станков. Если происходит что-то необычное, например, если в станок попадает посторонний предмет, то оборудование и инструмент могут сломаться. Нормальной работе станка может помешать накопившаяся металлическая стружка. Если сломается метчик и появятся дефекты, то вокруг станка может моментально образоваться целая гора из десятков и сотен единиц бракованной продукции. В таких случаях можно считать, что станки вообще не работали. Как мы можем все это предотвратить? Приставить к каждому станку рабочего, который наблюдал бы за его работой? Если бы автоматизация означала именно это, то вряд ли она позволила бы повысить производительность труда. Мы в Toyota поставили подобную автоматизацию под запрет.
Давайте теперь снова послушаем г-на Óно, чтобы узнать, что он думает об автоматизации.
«Мы в Toyota настаиваем на автоматизации «с человеческим лицом» (нинбен но цуита дзидока). Без элементов человеческого интеллекта автоматизация теряет свой смысл. Любой станок можно сделать автоматическим, и такую автоматизацию могут осуществить и другие производители, располагающие этими станками. Но мы добавляем человеческий интеллект, и как пользователи этих станков мы отдаем им частицу себя.
Говоря коротко, эта автоматизация «с человеческим лицом» предполагает наличие устройства автоматической остановки на случай, если что-то пойдет не так. Если такого устройства нет и обработка окончена или изготовлено дефектное изделие, то ситуация может стать опасной. Если бы дефекты начали проявляться часто, то их стало бы трудно контролировать. Мы были просто вынуждены установить специальное устройство для предотвращения массового производства дефектной продукции».
Поделитесь своими знаниями с автоматом
Выражение автоматизация «с человеческим лицом» придумал, вероятно, тоже г-н Тоёда. Многоуважаемый покойный Сакити Тоёда, основатель компании Toyota, создал ткацкий станок-автомат с элементами человеческого интеллекта.
В ткачестве существуют строгие правила. Для каждого вида переплетения нитей на одном квадратном дюйме ткани должно находиться точное количество нитей основы и утка. Если не хватает хотя бы одной нити основы или утка, то продукция признается дефектной.
Ткацкий станок-автомат Toyota останавливался немедленно, как только нить основы или утка обрывалась или просто заканчивалась в челноке. Иными словами, станок не мог производить дефекты, поскольку был оборудован устройством автоматической остановки. Мы говорили, что это станок с элементами человеческого интеллекта.
Посетив принадлежащую г-ну Тоёда фабрику по производству ткацких станков-автоматов, я пошутил: «Скажите, обычно говорят, что ваш завод выпускает автоматы с элементами человеческого интеллекта. Я вижу, вы убрали из своего названия упоминание о человеческом интеллекте. Вы что, так обеднели?» Автоматы с элементами человеческого интеллекта – это такие станки, которые сами следят за тем, чтобы не выпускать дефекты. Они останавливаются, как только возникает такая угроза. Благодаря этому изобретению один рабочий смог обслуживать 20 или около того высокоскоростных ткацких станков. По сравнению со временами, когда к каждому ткацкому станку был приставлен один человек, производительность выросла на порядки.
Мы применили тот же подход к производству автомобильных деталей. Теперь, когда мы добавили требуемые элементы человеческого интеллекта, мы не видим ничего невозможного в том, чтобы увеличить свою производительность в десять или даже в сто раз.
Мы говорим своим сотрудникам: «Вы только что получили эти станки, но пока что это не автоматы с элементами человеческого интеллекта. Такими они должны стать благодаря вам. Под этим мы понимаем, что вы должны передать свои знания станкам, на которых работаете. Если вы просто работаете на станках, которые только что купили, то не проявляете никакой изобретательности. Чтобы сделать свою повседневную работу достойной вас, вы должны поделиться со станком своими знаниями».
Станки должны останавливаться автоматически
Сегодня никто не станет спорить с тем, что Toyota – автомобильная компания мирового класса, но в 1937 г., в год ее основания, все было иначе. Ей пришлось столкнуться с острой конкуренцией со стороны далеко ушедших вперед американских и европейских автомобилестроителей. Чтобы догнать и обогнать конкурентов, она должна была автоматизировать производство. В 1955–1965 гг. компания сделала гигантский рывок в области автоматизации.
Однако, несмотря на автоматизацию, ее потребность в рабочей силе, похоже, не уменьшилась. В некоторых цехах станки-автоматы стояли рядами, но к каждому приходилось приставлять человека. По сути, эти станки ничем не отличалась от обычных.
Это не означает, что лучше было бы использовать не автоматы, а обычные станки. Просто на том этапе мы еще не понимали, какой должна быть автоматизация. Приступая к автоматизации, нужно было сначала придумать не то, как станки будут делать детали автоматически, а то, как они смогут сами обнаруживать аномалии и останавливаться.
Мы нуждались не в станке-автомате, а в станке, который, подобно человеку, мог бы сам следить за своей работой. Мы в Toyota прилагаем максимум усилий и изобретательности, чтобы наши машины, как старые, так и новые, приобрели эту человеческую способность. Об этом свидетельствуют наши устройства, гарантирующие остановку станка в строго определенный момент, система полной работы, система «защиты от дурака» и другие средства для обеспечения безопасности.
Цель этой автоматизации не сводится к замене людей на конвейере машинами. Люди и машины должны немедленно останавливаться при обнаружении аномалии. Вся эта система и есть то, что мы называем автоматизацией «с человеческим лицом».
Афоризмы Óно
Автоматизация «с человеческим лицом» означает, что станок может сам принять решение о своей остановке.
Автоматизация «без человеческого лица» – это просто способность к движению.
Станки-автоматы (без обязательного «человеческого лица») могут ломать станки и пресс-формы при возникновении ненормальности. Они могут произвести множество дефектов и требуют присутствия рабочих.
По-японски автоматизация – дзи-до-ка, слово, записываемое тремя китайскими иероглифами. Первый иероглиф дзи означает «рабочий». Если рабочему покажется, что что-то идет не так или что он производит дефектное изделие, он должен немедленно остановить конвейер. По сути, мы предлагаем, чтобы у каждого рабочего была кнопка остановки конвейера. Как только он поймет, что произошел сбой, он должен немедленно остановить конвейер.
Зачем останавливать конвейер
Остановить конвейер в процессе работы не так-то просто. Если он замрет даже на мгновение, объем производства упадет, что, конечно, не понравится ни одному начальнику. В Toyota конвейер останавливается, но вовсе не потому, что нам это нравится.
В Toyota конвейеры время от времени останавливаются, хотя и не надолго, всего на несколько секунд. Это делается для того, чтобы вся линия могла работать гладко. Мы останавливаем линии, потому что наша конечная цель – никогда их больше не останавливать.
Вот какая история реально произошла у нас в компании.
В Toyota был бригадир – назовем его г-н А, – который упорно отказывался останавливать свой конвейер, и был бригадир г-н Б, который останавливал свой конвейер всякий раз, когда это требовалось.
Господин Б всегда останавливал конвейер без колебаний, поэтому сначала он делал это слишком часто. Число машин, собираемых на этом конвейере, резко упало, и производственный план не выполнялся. Однако конвейер останавливался из-за многочисленных проблем, о которых рабочие хорошо знали, но не сообщали г-ну Б.
Когда конвейер останавливался, эти проблемы выявлялись и решались одна за другой. Через три недели ситуация в корне изменилась. Конвейер г-на Б стал работать лучше конвейера г-на А. Последний продолжал думать, что остановить конвейер означает снизить производительность и ввести компанию в убытки.
Как это ни парадоксально, но для нас остановить конвейер означает сделать так, чтобы он стал работать лучше, и гарантировать, что его не придется останавливать вновь по той же причине. Наша цель – создать идеальный конвейер, и компания готова нести связанные с остановкой конвейера убытки. Поэтому когда конвейер останавливается, бригадиры прилагают все силы к тому, чтобы решить обнаруженные проблемы.
Бригадиры, которые никогда не говорят: «Остановите конвейер», – плохие бригадиры, равно как и те, кто дважды или трижды останавливает одну линию по одной и той же причине.
Афоризмы Óно
Линия, которую не останавливают, либо очень хороша, либо никуда не годится.
Большинство линий нельзя остановить, потому что их окружает столько людей, что не видны проблемы.
Надо сделать так, чтобы линию можно было остановить. А затем продолжать совершенствовать ее таким образом, чтобы она превратилась в линию, которую уже не придется останавливать, даже если это кому-то и захочется.
Особого внимания заслуживает следующая фраза: «Линия, которую не останавливают, либо очень хороша, либо никуда не годится».
Рабочее место, которое легко наблюдать
Чтобы линию можно было остановить, каждый рабочий должен иметь возможность нажать на кнопку остановки. Если на его участке произойдет сбой, то он нажмет на эту кнопку и остановит линию.
Заминка в работе может возникнуть из-за того, что детали собраны неправильно или они дефектны и их нельзя подогнать друг к другу. Эти причины тщательно изучаются, и ошибки сразу же исправляются, что исключает возможность их повторения. Если говорить о долгосрочных результатах, то останавливать конвейер оказывается даже выгодным.
В Toyota Motors кнопки остановки есть у всех линий. Когда в цех приходит новый рабочий, первое, чему его учат, – это как остановить конвейер.
Если по какой-либо причине конвейер остановился, то висящее над каждой линией световое табло немедленно показывает, во время выполнения какой операции возникла проблема. Это табло называется андон (сигнальная лампа).

Рис. 14. Конвейер, за которым легко наблюдать
Например, конвейер состоит из двенадцати процессов. По какой-то причине он остановился при выполнении процесса 4. На табло немедленно загорится цифра 4, показывающая, что проблема возникла именно здесь. Находившийся ближе всего мастер сразу же подойдет, чтобы выяснить, в чем проблема, и предложить техническое решение.
Если конвейер оборудован и кнопкой остановки, и световым табло, то понять, что на нем происходит, можно с одного взгляда, т. е. кнопка остановки и световое табло делают возможным визуальный контроль.
Визуальный контроль
Мы уже не раз говорили, что важнейшая цель системы Toyota – исключение потерь. Однако понять, из чего они на самом деле складываются, довольно трудно. А вот найти методы или пути устранения потерь, напротив, не слишком сложно.
Поэтому если мы сможем сделать потери очевидными для всех, это станет первым шагом к их устранению.
Президент одной дочерней компании Toyota как-то пришел в ее штаб-квартиру и сказал: «У нас мало заказов. Пожалуйста, сделайте что-нибудь». Руководство Toyota встревожилось и попросило вице-президента Óно посетить этот завод со своими сотрудниками.
Óно отправился туда в тревоге. «Если заказов нет, то на заводе может быть ужасно тихо, а я ненавижу, когда на заводе тишина». Но вот странность: и рабочие, и станки на этом заводе работали в полную мощь. Никаких признаков того, что людям нечего делать, не было.
Визитеры были озадачены. Они приехали сюда, так как считали, что Toyota обязана обеспечивать свои дочерние компании работой, но увидели совсем не то, что ожидали.
Óно и его спутники готовились к тому, что все служащие, включая самого президента, будут смотреть на них с мольбой и жалобно вопрошать: «И что же вы намерены теперь предпринять?» Но ничего подобного не произошло.
Проведенный ими осмотр показал, что эта дочерняя фирма на самом деле могла бы выполнять больше заказов, чем имела сейчас. Но визуально это никак не проявлялось. Если бы заказов действительно катастрофически не хватало, то часть рабочих обязательно бы простаивала.
«Пусть у вас будет свободное время»
Это может показаться крайностью, но мы в Toyota говорим своим рабочим: «Пусть у вас будет свободное время». Мы не хотим, чтобы они делали что-то ненужное, когда у них нет работы. Лучше, чтобы они оставались там, где находятся, и ничего не делали.
У рабочих появляется свободное время, потому что им дали такое задание. Все дело в этом задании, и рабочие здесь ни при чем. Когда у них появляется свободное время, бригадиры и мастера немедленно узнают об этом, что дает возможность последним оценить собственные задания и инициировать действия по улучшению.
Это еще один пример конвейера, за работой которого легко наблюдать и где возможен визуальный контроль.
Нередко можно видеть, как по заводу ходит его директор или президент отделения или всей компании. Если такие обходы проводятся только раз в год, то рабочие могут счесть это недостаточным. Но если работа в цехе будет организована таким образом, что любой посетитель сможет понять, что здесь происходит, с одного взгляда, то такой обход станет намного более полезным.