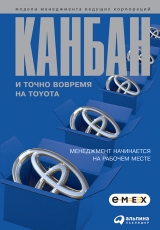
Текст книги "Канбан и «точно вовремя» на Toyota. Менеджмент начинается на рабочем месте"
Автор книги: авторов Коллектив
Жанры:
Деловая литература
,сообщить о нарушении
Текущая страница: 14 (всего у книги 15 страниц)
Мастер всемогущ
Нередко нам задают вопрос: «Хорошо ли, когда мастер сам приходит в цех?» Ответ, следующий из принципов системы Toyota: «Плохо, если он постоянно находится в цехе, но неправильно, если он там вообще не показывается».
Если мастер все время находится в цехе, то он ничем не отличается от простого рабочего. Он не сумеет выполнять такие важные функции, как управление, проведение преобразований и обеспечение обучения и подготовки рабочих. Тем не менее он также не сможет полностью освободиться от визитов в цех, какой бы переизбыток персонала там ни был. Если он будет постоянно заниматься устранением потерь, то, естественно, ему временами придется бывать в цехе.
Мастер никогда не должен думать, что вынужден посещать цех. Снижение трудозатрат – одна из его основных задач. Он должен отстраниться от какой-то работы в цехе, чтобы увидеть общую картину. Он делает это потому, что обязан заниматься улучшениями. Чтобы добиться прогресса, он должен знать, легко или сложно выполнять данную операцию, а для этого он должен досконально изучить каждую процедуру. Всегда имеются потери, неравномерность и нецелесообразность (муда, мура и мури), которые с одного взгляда обнаружить невозможно.
Чтобы учить подчиненных, изменить последовательность работ так, как он считает нужным, и обнаруживать даже самые незначительные потери, мастер должен время от времени бывать в цехе. Когда какой-то рабочий отсутствует, мастер может поработать вместо него на линии, чтобы самому понаблюдать за ее работой.

Рис. 41. Мастер всемогущ
Крайне важно, как мастер относится к подобной смене деятельности. Считает ли он, что встает к станку в силу обстоятельств? Хочет ли он обнаружить скрытые проблемы? В конечном счете эта разница в подходе приобретает большое значение. Мастер, который положительно относится к собственной работе на линии, может добиться улучшений. Также он в состоянии подменить любого рабочего в случае его отсутствия.
Поэтому нет ничего из ряда вон выходящего в том, чтобы предложить мастеру при случае поработать в цехе. Для того чтобы постоянно учиться и совершенствоваться, он должен работать на линии. Ведь менеджмент начинается на рабочем месте.
Приложение А
Производственное планирование, позволяющее Toyota Motor координировать работу своих дилеров и поставщиков автодеталей[9]9
Эта глава написана по материалам статьи Ясухиро Мондена «Построение новой системы управления производством, объединяющей торговые компании, производителей и поставщиков деталей», опубликованной в январском номере журнала Японской ассоциации менеджмента Production Management за 1986 г.
[Закрыть]
Координация работы автомобилестроителей и дилеров
Процесс разработки автомобилестроителями производственных планов на основе предоставляемой дилерами информации обычно состоит из двух этапов:
• составления основного плана производства готовых машин и таблицы поставки деталей;
• разработки графика выполнения заказов на готовые машины и схемы последовательности сборки отдельных моделей.
Составление основного производственного плана и таблицы поставки деталей
Этот этап начинается с анализа планов продаж, подготовленных отделом продаж на внутреннем рынке и отделом продаж на внешнем рынке. Раз в месяц дилеры посылают в отдел продаж на внутреннем рынке трехмесячный прогноз спроса на каждую линейку машин, которой они торгуют. Этот отдел анализирует полученную информацию и разрабатывает планы продаж по конкретным моделям или линейкам, а также по более широким группам машин с общими спецификациями. Одновременно отдел продаж на внешнем рынке получает месячные проектировки от зарубежных дилеров по заказам на следующие три месяца и также составляет планы продаж конкретных моделей и больших партий машин с общими спецификациями.
Далее отдел управления производством анализирует планы продаж как на внутреннем, так и на внешнем рынке, оценивает свои производственные мощности и составляет трехмесячный план производства. Затем на основе плана производства на первый месяц определяется дневной объем производства всех линий, занимающихся сборкой отдельных моделей. При этом с целью выравнивания производства его месячный объем просто равномерно распределяется по дням месяца. Полученный производственный план называется основным графиком производства.
В отдельные большие группы объединяют машины с такими общими характеристиками, как тип корпуса, тип двигателя (т. е. объем, используемое топливо и т. п.), тип трансмиссии (автоматика или механика) и класс машины (эконом, люкс и т. д.).
Далее отдел управления производством составляет на основе перечня материалов и этого основного графика производства список требуемых материалов, который называют «планом потребности в материалах» (MRP).
Затем автомобилестроитель информирует свои заводы и поставщиков об этом графике, используя данные MRP. Это уведомление называют «таблицей поставки деталей». Однако, как еще будет сказано ниже, вовсе не ожидается, что производители деталей выпустят именно то их количество, которое указано в этой таблице. На самом деле они будут руководствоваться теми указаниями о точном количестве деталей и материалов, которые станут ежедневно считывать с карточек канбан. В этом случае данные MRP не более чем ориентир, используемый для целей планирования.
График поставки и схема последовательности сборки
На этом этапе процесса планирования подготавливаются дневные заказы-наряды на производство.
Первый шаг – дилеры размещают заказы на десять дней. Для этого каждый дилер готовит окончательный заказ, разделенный по категориям со сходными спецификациями, который охватывает десятидневный период и вписывается в основной график производства. Дилер посылает этот заказ телексом в отдел продаж автомобилестроителя за семь-восемь дней до начала этого десятидневного периода. В этом заказе машины сгруппированы по указанным выше общим характеристикам, а также по дополнительному (по желанию) оборудованию и цвету салона и корпуса.
Затем производственный отдел определяет на основе этих десятидневных заказов дневной объем производства каждого завода и сборочной линии. Результатом этого является пересмотренный основной производственный график. Затем автомобилестроитель составляет графики поставки своим дилерам (см. рис. 42). С момента получения десятидневных заказов до разработки этих графиков проходит порядка двух дней.

Рис. 42. График поставки
Дилеры могут ежедневно информировать отдел продаж об изменении своих десятидневных заказов (в пределах 10 %) с учетом реального потребительского спроса. Например, если согласно представленному на рис. 42 графику поставки 1 июня должна быть поставлена белая машина, то дилер может попросить заменить ее на красную. Эти изменения называются просто «дилерскими изменениями», и сведения о них должны быть получены автомобилестроителем за четыре-пять дней до намеченной даты сборки данной машины.
Отдел управления производством направляет заводам обновленный основной производственный план, учитывающий эти дилерские изменения. Это делается за три дня до намеченной даты сборки автомобиля.
Далее отдел управления производством дает заводам указание составить свои схемы последовательности сборки. Это делается за полтора дня до даты сборки автомобиля. Из-за большого количества деталей и размера этих схем Toyota требует, чтобы ее самые крупные поставщики деталей представляли свои схемы на магнитной ленте, в то время как более мелкие могут подавать их и в бумажном виде. Затем Toyota печатает бирки, аналогичные показанной на рис. 16 и содержащие информацию, полученную из этих схем последовательности сборки. Эти бирки приклеивают на машины в начале каждой сборочной линии, чтобы рабочие руководствовались ими при сборке.
Шестой и последний этап связан с использованием карточек канбан для отбора и заказа деталей, но это касается только деталей, не охваченных схемой последовательности сборки. Более подробно об этом говорится в пятой главе.
Система информирования дистрибьюторов в реальном времени (онлайн)
Как уже упоминалось выше, дилеры по телексу отправляют автомобилестроителям сначала свои десятидневные заказы, а потом и поправки к ним. Благодаря этой системе срок выполнения заказа в Toyota (период между получением десятидневных заказов и фактической поставкой заказанной машины) составляет в зависимости от географического расстояния от трех недель до двух месяцев. А если исключить время на транспортировку, то интервал между получением десятидневных заказов и датой сборки машины составляет от 11 до 21 дня, а между получением сведений о дилерских изменениях и датой сборки – около 5 дней.
Чтобы еще больше уменьшить этот интервал и благодаря этому быстрее удовлетворять запросы потребителей, Toyota создает систему онлайнового информирования, обеспечивающую ежедневный обмен информацией между нею и дилерами. Когда эта новая сетевая система заработает, сроки выполнения заказов сократятся на несколько дней и вероятность скопления у дилеров лишних запасов уменьшится. Фактически это будет равнозначно внедрению на этапе продаж системы «точно вовремя».
Эта сетевая система использует новую ветку оптоволоконного канала, проложенную Nippon Telephone and Telegraph (NTT), ведущей японской телефонной компанией, по всей Японии. Система Toyota планирует использовать два универсальных компьютера (один в головном офисе Toyota в Тоёде, а другой – в филиале в Нагое), которые будут соединены с компьютерами и сетевыми терминалами всех дилеров, что облегчит ежедневное уточнение заказов и обмен другой информацией. Ожидается, что это поможет создать производственную систему, быстрее реагирующую на поступление заказов, а также еще больше сократить сроки их выполнения.
Свой вклад в создание этой системы уже внесли четыре крупных японских сбытовых подразделения Toyota (Tokyo Toyopet, Osaka Toyopet, Aichi Toyota Motor и Kanagawa Toyota Motor), добившиеся больших успехов в создании собственных внутренних сетей. Благодаря этим компаниям все заказы на роскошную салонную модель Crown с января 1986 г. обрабатываются в онлайновом режиме, и постепенно эта система охватывает всех дилеров Toyota в Японии и все марки ее легковых автомобилей.
Таблица поставки деталей
Каждый месяц автомобилестроители направляют своим поставщикам деталей трехмесячные графики производства. В этих таблицах поставки деталей (см. рис. 43) приводятся данные о дневной поставке деталей (дневник поставок) за последний месяц. Также в них заложены данные о заказах на детали на два предстоящих месяца, но эти цифры подлежат уточнению.
Кроме того, несколько раз в месяц рассчитывается разница между текущим объемом производства и объемом поставок за предыдущие месяцы согласно дневнику поставок, что важно для уточнения сроков выполнения заказов при использовании канбан.
Хотя применяемая компанией Toyota система канбан описывалась уже неоднократно, о ее таблицах поставки деталей написано немного. Автомобилестроители используют эти таблицы для передачи поставщикам деталей следующей количественной информации по каждому виду (номеру) деталей (см. рис. 43 и 44):

Рис. 43. Таблица поставки деталей
1. По детали В, например, эта таблица содержит следующие итоговые цифры:
а) всего заказано на май: 1600 деталей;
б) незавершенное производство всего в июне: 1600 деталей;
в) незавершенное производство всего в июле: 1700 деталей
(данные за июнь и июль в таблице не приведены ввиду ограниченности места).
2. Далее указывается число деталей в ящике (в каждом ящике 10 деталей).
3. Также указывается среднее число ящиков, которое должно поставляться ежедневно в период с 1 по 31 мая. В случае с деталью В в выходные и праздники (3, 4, 5, 11, 12, 18, 19, 25, 26 мая) поставки будут нулевыми. Если учесть, что в месяце 22 рабочих дня, получим, что в среднем ежедневно будет поставляться по 7 ящиков (1600 деталей по 10 деталей в ящике, произведенных за 22 дня), т. е. производство недополучит 60 деталей. Если поставщики будут производить ежедневно по 8 ящиков, а не по 7, то образуется избыток в 160 деталей. Поэтому чтобы покрыть разницу, они должны каждый третий или четвертый день производить по 8 ящиков, а в остальные дни – по 7 ящиков.
4. Кроме того, для функционирования канбан нужна информация:
а) о том, сколько раз в день должны предоставляться карточки канбан: в случае детали В эти карточки передаются 10 раз в день, а готовые детали обычно поставляются поставщиком после получения этих карточек в два приема (см. столбец «позднее» таблицы на рис. 43). Этот цикл поставок можно выразить формулой 1–10–2 (см. примечание к рис. 43);
б) о числе карточек канбан: указывается общее число карточек канбан, которые автомобилестроитель должен использовать для этих деталей. В случае детали В требуется три карточки;
в) о разнице (положительной или отрицательной) в числе карточек канбан, использованных при текущих и предыдущих поставках деталей. В случае детали, требующей использования двух карточек и поставляемой каждую вторую партию, разница, равная единице, означает, что в момент поставки t доставляются детали, соответствующие двум карточкам канбан, но в момент времени t + 2 поставляются детали, соответствующие только одной карточке (см. рис. 44).

Рис. 44. Цикл поставок и число карточек канбан на партию
Разработка производственного плана компанией – поставщиком деталей
Компании – поставщики автодеталей разрабатывают свои производственные планы в два этапа. На первом на основе подготовленных автомобилестроителями таблиц поставки деталей определяется предварительный производственный график на предстоящий месяц.
На втором этапе на основе ежедневно присылаемых автомобилестроителями карточек канбан и схем последовательности сборки, а также MRP или списков подтвержденных заказов (дневников поставок) составляется производственный график, основанный на заказах и выполняющий роль дневного плана производства. На рис. 45 проиллюстрированы эти два описываемых ниже этапа процесса производственного планирования.

Рис. 45. Предварительный производственный график компании – поставщика деталей и ее производственный график, основанный на заказах
Предварительный производственный график компании – поставщика деталей
Для производственного отдела компании – поставщика деталей полученные от автомобильной компании таблицы поставки деталей выполняют (по крайней мере, по этим деталям) роль основного производственного графика.
На основе содержащихся в этих таблицах данных по незавершенному производству, а также разработанных на основе MRP списков деталей компания – производитель деталей составляет план закупок у своих поставщиков и дневной производственный график основных участков собственных заводов (точно так же, как автомобильная компания разрабатывает свой основной производственный график на основе MRP).
Возьмем для примера сравнительно простую систему и посмотрим, как средняя по размеру компания – поставщик деталей (сальников для автомашин и мотоциклов) составляет свой план закупок и производственный график.
На основе MRP и полученных от автомобильной компании таблиц поставки деталей компания А разрабатывает таблицы заказа деталей у своих поставщиков. Эти таблицы составляются на месяц с 10-го по 10-е число следующего месяца. Поставщикам они предоставляются как дневные планы.
Каждый понедельник компания А составляет ведомость заказов на детали на следующую неделю. Размещение заказов за неделю означает, что время выполнения заказа поставщиком также составляет одну неделю (см. рис. 46).

Рис. 46. Использование списка заказов при разработке графика выполнения заказов на детали
Далее компания А разрабатывает на основе MRP и присланных автомобилестроителем таблиц заказа деталей производственный график для собственных заводов. Поскольку компания А специализируется на литье, главное внимание при разработке этого графика уделяется именно этой операции. Так же, как автомобилестроитель информирует компанию А с помощью таблиц поставки деталей, компания А ежедневно ставит в известность своих поставщиков о материалах, необходимых ей для процесса литья.
Если предположить, что план закупок и описанный выше график литья составлены на месяц n, то эти документы будут охватывать период от месяца n – 1 и учитывать данные таблицы поставки, которая поступила от автомобилестроителя после 20-го числа месяца n – 2. Содержащиеся в полученной от автомобилестроителя таблице цифры могут измениться в любую сторону в зависимости от того, какие подтвержденные заказы будут получены в течение самого месяца n; однако с уверенностью можно сказать, что их погрешность составляет не более 20 % (см. рис. 47). У каждого автомобилестроителя свой запас безопасности. В некоторых случаях он составляет 50 %.

Рис. 47. Предварительный производственный график на месяц n и дата его разработки
Производственный график поставщика деталей, основанный на заказах
На основе описанного выше предварительного графика производства компания А составила дневной график литья на энный месяц данного года. Как показано в строке «Ожидаемое производство» рис. 48, в графике предусмотрено, что каждый второй день будет выпускаться партия в 3325 деталей. Данные о подтвержденных заказах на энный месяц поступают от заказчиков после 20-го числа предыдущего месяца (месяца n – 1). Эти данные представлены в виде таблицы поставки деталей, аналогичной приведенной на рис. 43. Если автомобилестроитель готовил эти указания по производству только на основе MRP, то в принципе они будут окончательными. Цифра из MRP показана в строке «Расчетная дата поставки» рис. 48.

Рис. 48. Основанный на подтвержденных заказах план восполнения дефицита, возникшего из-за недостаточного объема производства
В результате на шестой день месяца возникнет дефицит в размере 425 деталей. Поэтому в этот день было намечено произвести 3500 деталей.
В этом случае производственный график для участков литья или сборки спускается по деталям и узлам, которые потребуются на следующей неделе, каждый вторник, а работа должна быть завершена на неделю позднее (см. рис. 49). В компании А планы закупок и графики литья составляются с использованием MRP каждую вторую неделю, а установленное для выполнения время – три дня.

Рис. 49. График литья, составляемый каждый второй вторник
В описанном выше примере мы предположили, что данные о подтвержденных заказах поступают после 20-го числа месяца, предшествующего месяцу n, т. е. месяца (n – 1), но заказчики нередко используют канбан, чтобы размещать окончательно подтвержденные заказы ежедневно. В этих условиях фактическое производство не может превысить число карточек канбан, поскольку оно инициируется исключительно содержащимися на этих карточках указаниями.
Эти карточки поступают сначала на процесс финишной сборки, а затем уже последовательно на все предыдущие процессы. Движение карточек канбан по каждой группе деталей или узлов от участка сборки до процессов литья контролируется мастером. Он регистрирует любые расхождения между объемом производства, который рассчитан на основе MRP, и числом карточек канбан и следит за тем, чтобы процессы литья и сборки не превысили количество, предусмотренное всеми карточками канбан (см. рис. 45).
Компании А было бы удобнее использовать при работе со своими поставщиками карточки канбан, соответствующие заказам клиентов, но ее поставщики не имеют возможности обработать эти карточки, а значит, и сократить время выполнения заказа. Вместо этого компания А посылает своим поставщикам составленные на основе MRP таблицы поставки деталей и описанные выше ведомости заказов. В результате, хотя компания А и может постоянно контролировать запас для своих процессов сборки и литья, на ее складе деталей, полученных от поставщиков, могут образоваться излишки. В связи с этим кому-то может показаться, что система канбан всегда перемещает излишние запасы в конец цепочки поставок, что на самом деле не соответствует действительности.
Предположим, масштабы использования канбан в компании А ограничены. Если бы она попыталась решить эту проблему, навязав эту систему своему поставщику Б, то у последнего неизбежно возникли бы излишние запасы, но компания А не стала действовать подобным образом. Почему? Да потому, что, решив внедрить у себя канбан, она приняла целый ряд мер по сокращению собственного времени цикла выполнения заказа. В результате компания А уменьшила свои запасы во всех процессах, начиная от сборки и заканчивая литьем. Что касается проблемы возможного увеличения запасов на складах поставщиков, то компания А еще до перехода на канбан поняла, что и теоретически, и практически этот переход не заставит поставщиков увеличить свои запасы. Наоборот, компания А использовала MRP, чтобы минимизировать запасы у поставщиков. Поэтому одно только то, что компания А использует канбан, до тех пор пока эта система никому не навязывается и не превышает возможности производственной системы А, вовсе не приводит к перекладыванию бремени содержания крупных запасов на плечи поставщика.