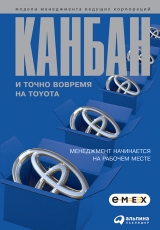
Текст книги "Канбан и «точно вовремя» на Toyota. Менеджмент начинается на рабочем месте"
Автор книги: авторов Коллектив
Жанры:
Деловая литература
,сообщить о нарушении
Текущая страница: 13 (всего у книги 15 страниц)
Не стоит заранее выписывать свидетельство о смерти
Поговорим теперь о проверке, проводимой специальными инспекторами.
Считается, что инспекторы отделяют хорошую продукцию от плохой, подсчитывают результаты и посылают отчет в предыдущий процесс. Обычно на этом проверка и заканчивается – но это неправильно. Инспекторы должны быть участниками процесса, чтобы проанализировать причины появления дефектов, попытаться их исправить и положить этой практике конец. Они не экзаменаторы, которые определяют, кто сдал экзамен, а кто нет. Они должны уметь объяснить рабочим, почему были допущены ошибки, и научить не повторять их впредь. Они должны выполнять роль, аналогичную роли частного наставника.
Когда детали собраны неправильно, нередко причиной называют невнимательность рабочего. Но, возможно, все не так просто. Может быть, детали не положили заранее в том порядке, в каком их обычно собирают, или же кнопка включения или вызова находится слишком далеко. Или же рабочие инструкции трудночитаемы. Причины могут быть самыми разными. Но, только выяснив эти причины и приняв соответствующие меры, можно сделать шаг вперед к сокращению количества дефектной продукции.
Функция инспектора должна состоять не в том, чтобы отбраковывать некачественную продукцию, а в том, чтобы прекратить ее производство. И это должно быть основным критерием оценки его деятельности.
«Защита от дурака» (пока-ёкэ)
Что должны делать рабочие, чтобы качество было встроено в процесс производства? Что именно они обязаны проверять и какие детали измерять? Когда надо менять режущий инструмент?
Определенную роль в решении этих проблем могут сыграть оснастка и инструменты. Можно сделать так, чтобы они автоматически проверяли поступающие с предыдущего процесса детали. Вы можете сделать ваш процесс дуракоустойчивым и способным обнаруживать дефекты.
Процесс обеспечения «защиты от дурака» (пока-ёкэ) надо стандартизовать, чтобы гарантировать стабильное качество при минимальных трудозатратах, даже если эту работу будет выполнять другая смена.
Любой человек, даже соблюдая максимальную осторожность, может совершенно ненамеренно допустить ошибку при измерениях или при проверке партии деталей. Поэтому нужно найти способ предотвращения таких явлений, как выпуск дефектной продукции, ошибки при выполнении операций и производственные травмы. Предлагаемая нами система «защиты от дурака» предусматривает создание устройств для обнаружения аномалий, которые освобождают рабочих от постоянного слежения за мельчайшими деталями. В частности, мы рекомендуем установить устройства, которые:
• не позволят поместить деталь в зажимное приспособление, если произошла ошибка;
• не дадут станку приступить к обработке, если возник непорядок;
• не позволят станку приступить к обработке, если произошла ошибка;
• автоматически осуществят регулировку в случае неправильного выполнения какой-либо операции и только потом разрешат продолжить обработку;
• остановят выпуск несоответствующей продукции;
• не позволят приступить к следующему процессу, если какой-либо из предыдущих не выполнен.
Для «защиты от дурака» могут использоваться следующие методы:
1. Визуальный метод. Обеспечьте полноценное освещение, чтобы рабочему было легче различать инструменты по цвету и другим признакам и самому обнаруживать неполадки.
2. Метод оснастки. Можно сделать так, чтобы непригодную деталь нельзя было вставить в зажимное приспособление, что исключает работу станка, если деталь установлена неправильно. Этот метод предполагает использование такой оснастки, которая позволяет обнаружить непорядок.
3. Автоматический метод. Станок сам останавливается, если в процессе обработки происходит сбой. Некоторые не считают, что этот метод входит в нашу систему методов «защиты от дурака».
Создавая систему «защиты от дурака» для вашей компании, выберите те проблемы, которые легче всего решить, и те участки, потери на которых могут быть минимальными.
Безопасность превыше всего
Есть поговорка: «Что с возу упало, то пропало». В нашей жизни есть нечто такое, что уже никогда не вернуть в первоначальное состояние. Потратив достаточно денег, можно починить станки и другие средства производства. Но если человек получит травму, то его здоровье уже никогда не восстановится полностью. Несчастный случай может привести и к смерти рабочего, и тогда никакие деньги не помогут вернуть его к жизни. Поэтому безопасность всегда была нашей главной заботой, и никакая работа по снижению трудозатрат не может проводиться без максимального учета фактора безопасности.
Конечно, нужно использовать все возможности для снижения производственных затрат, в том числе сокращение трудозатрат, но мы никогда не должны забывать, что безопасность для нас – это основа всего. Некоторые рационализаторы забывают об этом. Поэтому всегда нужно вернуться к исходному пункту и еще раз уточнить цель действий. Нельзя бездействовать. Чтобы добиться прогресса, усомнитесь в своей цели и определите ее заново.
На первый взгляд безопасность и снижение трудозатрат взаимоисключающие понятия. На самом же деле методы их достижения идентичны, поскольку снижение трудозатрат способствует также устранению потерь (мýда), неравномерности (мýра) и нецелесообразности (мýри).
На любом заводе большинство несчастных случаев происходит из-за движений, вызванных потерями, нецелесообразностью и неравномерностью. Говоря коротко, рабочих заставляют делать что-то ненужное или очень трудное. Поэтому они совершают бесполезные движения и в результате получают травмы.
По-японски «травма» – это кега. Это слово состоит из двух китайских иероглифов ке и га. Если прочитать их слитно, то получится: «даже для меня (га) это кажется странным (ке)». Причина травм – движения, которые кажутся странными, т. е. движения, связанные с потерями, неравномерностью и нецелесообразностью. Устранение этих трех факторов имеет самое прямое отношение к обеспечению безопасности.
Как правило, рабочие получают травмы на таких участках, где отсутствует надлежащий контроль порядка. На любом заводе должны следить за тем, чтобы рабочие удаляли со своего рабочего места все ненужное, заранее готовили необходимое, поддерживали чистоту, занимались уборкой и были обеспечены инструкциями по выполнению требуемых операций. Несчастные случаи чаще всего происходят там, где этим факторам не придают особого значения. И наоборот: там, где активно занимаются снижением трудозатрат и улучшениями, несчастные случаи происходят редко.
Выполняемые на производстве операции надо упрощать. Чем они проще, тем легче ими управлять и выявлять ненормальности.
Надо упрощать и выполняемые при работе движения.
Если эти движения просты, то они не становятся причиной потерь, неравномерности и нецелесообразности. Их легко выполнять и просто контролировать. Чем операции проще, тем они безопаснее. Важно создать систему визуального контроля, позволяющую быстро обнаруживать небезопасные движения.
Ранее мы говорили, что упрощение помогает снизить трудозатраты. Как можно видеть из этого анализа, упрощение способствует и повышению безопасности.
Удаление ненужных предметов, предварительная подготовка того, что потребуется, поддержание чистоты и проведение уборки – эти четыре вида деятельности выполняются силами нашего персонала и оборудования. Поэтому если людей или вещей слишком много или станки расставлены неудачно, эффективность этих видов деятельности будет невысока. Если процесс усложнен, то людям трудно пробираться среди вещей на рабочем месте. Нельзя забывать, что на производстве существует определенное соотношение между людьми, вещами и оборудованием, все они зависят друг от друга. Например, если людей слишком много, то может возникнуть перепроизводство (затоваривание). И тогда потребуется дополнительный персонал, который будет что-то относить, приносить, ремонтировать и перерабатывать. И возникает порочный круг.
На производстве нельзя увеличить что-то одно, не вызывая увеличения другого. А сложность возрастает прямо пропорционально росту количества. Снижение трудозатрат – важный шаг по предотвращению повышения сложности. Также это важное условие повышения безопасности.
Афоризмы Óно
Японское слово «сейри» означает удаление с рабочего места тех вещей, которые не нужны. «Сейтон» означает упорядочение вещей, с тем чтобы их можно было использовать в любую минуту. Просто аккуратное расположение вещей в ряд называется «сейрецу». От рабочего требуется и сейри, и сейтон.
Создание безопасных условий для работы требует принятия мер в масштабах всей компании. Первый шаг к достижению этой цели – исключить потери, неравномерность и нецелесообразность. Для этого надо создать такие условия, в которых эти потери, неравномерность и нецелесообразность было бы легко обнаружить.
Ниже приводятся вопросы, которые надо включить в рабочие инструкции.
• При каких условиях выполняются данные операции?
• В каком порядке?
• Сколько времени они занимают?
Вывод прост: снижение трудозатрат может повысить безопасность. Поэтому чтобы создать безопасные условия для работы, надо активно снижать трудозатраты.
Простая автоматизация ведет к травматизму
Когда автоматизация лишена элементов человеческого интеллекта (если оборудование устанавливается только ради сбережения труда, а не сбережения людей), обычно требуется, чтобы за работой станков-автоматов наблюдал специальный рабочий. Без этого рабочего станок-автомат нормально работать не будет. Автоматизация по образцу Toyota – это автоматизация «с человеческим лицом». В крайних случаях у нас срабатывает устройство автоматической остановки, и это очень важно с точки зрения безопасности и снижения трудозатрат.
Проблемы многих автоматизированных предприятий иллюстрирует следующий взятый из реальной жизни пример.
При выполнении операции, схематично представленной на рис. 38, одному рабочему отрезало палец. Его работа состояла в упаковке деталей, производимых станком-автоматом. Всего на заводе десять таких станков, и обычно их обслуживал один человек. Но в данном случае эту работу выполняло то три, то четыре человека, потому что детали поступали неравномерно. Переключатели, которые регулировали работу станков, были установлены неправильно, и механизм не останавливался, когда это требовалось. Несчастный случай произошел, потому что палец рабочего попал в станок, который вовремя не остановился.
В данном случае надо было заранее выяснить, в состоянии ли один человек справиться с этой работой. Нужно было также отрегулировать переключатели. Можно было принять такие меры по снижению трудозатрат, которые повысили бы безопасность, и этот несчастный случай был бы предотвращен.

Рис. 38. Простая автоматизация ведет к травматизму
Опасно ли запускать станок одной кнопкой?
Теперь у наших штамповочных и других станков только одна пусковая кнопка. В большинстве цехов такие станки используются уже давно. Те, кто там работает, всегда считали, что один человек может обслуживать целый ряд станков. Они все тщательно продумали и уверены, что эта работа совершенно безопасна.
Но все преимущества обслуживания одним человеком нескольких станков теряются, если для того, чтобы запустить эти станки, нужно использовать обе руки. Это лишняя трата времени. Сюда прибавляется время на переход от одного станка к другому. Зачем нужно включать станок двумя руками? Чтобы выполнить требования японского Закона об охране труда и здоровья. Закон требует, чтобы «на таких станках, как штамповочные, ни одна часть тела рабочего не могла попасть в опасную зону, пока пресс и режущий инструмент находятся в движении. Это положение неприменимо, если у штамповочных станков есть устройства, которые быстро останавливают пресс и режущий инструмент, как только какая-то часть тела рабочего попадает в опасную зону». Кнопки, которые нужно нажимать двумя руками, позволяют соблюсти это требование, но только формально. Эта система никуда не годится. Она не обеспечивает безопасности третьего лица, если оператор станка не знает о его присутствии.
Метод запуска станка одной кнопкой ничем не хуже. Однако прежде у таких станков не было устройства автоматической остановки в случае попадания какой-либо части тела рабочего в опасную зону.
А теперь наши станки оборудованы устройствами немедленной остановки, если какая-то часть тела человека попадет в опасную зону или если кто-то просто подойдет слишком близко, и они совершенно безопасны. Эти устройства работают и тогда, когда сам станок сломан. Хотя совать руки в работающий станок все равно никому не рекомендуется.
Мы постепенно перешли на этот принцип на линиях штамповки и автоматической сварки. В одном случае под заслонкой 250-тонного штамповочного пресса протянут провод; если кто-то до него дотронется, сработает переключатель и станок остановится. А около сварочного станка-автомата устроен небольшой помост; пока человек на нем стоит, станок не работает. И в том и в другом случае система пуска с двумя кнопками заменена системой пуска с одной кнопкой.
Но мы продолжаем работать над этой системой, и когда мы ее улучшим, все наши станки будут включаться одной кнопкой.
Следуя этой логике, мы обнаруживаем, что существует множество более безопасных и рациональных способов работы. Как часто мы забываем об этом и готовы пожертвовать безопасностью ради рационализации!
Хороший пример позитивного подхода приведен на рис. 39.

Рис. 39. Когда один рабочий обслуживает три штамповочных пресса
Роль мастеров на рабочем месте
Говорят, что 10-процентное снижение затрат эквивалентно 100-процентному росту продаж. Работа по снижению затрат имеет для любой компании огромное значение. Пренебрегать этой работой – значит расшатывать основание, на котором стоит вся система.
Те мастера, кто понимает значение этой работы, приносят своей компании большую пользу. Осознавая это, мы в Toyota разработали аналитический инструмент, представленный на рис. 40.

Рис. 40. Цикл управления мастера
Как может мастер следовать этому циклу управления и в то же время принимать такие меры по снижению трудозатрат, которые отвечали бы целям компании? Чем он должен руководствоваться и как действовать?
Он должен выполнять две основные функции: обеспечивать требуемые объем производства и качество продукции и заниматься улучшениями для снижения трудозатрат.
Может показаться, что эти две функции противоречат друг другу, поскольку мастер должен, с одной стороны, гарантировать и качество, и количество, а с другой – делать это с минимальным числом рабочих и оборудования. И то и другое совсем непросто. Некоторые мастера, слишком заботясь о количестве, не разрешают останавливать линию. Число рабочих, оборудования и объем запасов на участках таких мастеров может увеличиться. Это означает, что затраты также увеличатся, и в конце концов компания не сможет достичь своей цели. Поэтому мастер должен научиться так руководить работой своей линии, чтобы выполнять оба предъявляемых к нему требования.
Управление несоответствиями
Как может мастер производить продукцию требуемого качества и себестоимости в установленном количестве? Какими конкретными способами он может улучшить работу своей линии?
Мастеру приходится следить за множеством вещей. В частности, он должен наблюдать за тем, как происходит распределение работ, обучение рабочих операциям, соблюдается качество, выполняются производственные планы, а также обращать внимание на состояние оборудования, технику безопасности, на правила хранения и подготовки материалов и переналадки оборудования. Есть множество методов управления, и все же, если мастер попытается следить за всем, ему придется работать круглосуточно.
В системе Toyota все стандартизировано, и система обращает внимание только на те участки работы, где происходят отклонения от установленных норм. Иными словами, мы учим мастеров заниматься управлением несоответствиями.
На производстве стандартизировать означает определить содержание стандартных операций и убедить всех в важности их соблюдения. Применительно к материалам и запасам стандартизировать означает разработать четкие указания относительно их количества и места хранения. Если говорить об инструкциях по запуску станка, то это означает использовать канбан, о безопасности – разработать соответствующие правила. Как только эти правила будут установлены, рабочие должны убедиться в их нужности.
Организовав работу подобным образом, мастер сможет обращать больше внимания на то, что выходит за рамки этих правил. Это можно рассматривать как проблемы, которые надо решить. Последовательно придерживаясь этого подхода, он со временем станет лучше понимать, что должен делать. В конечном счете мастер будет четко представлять себе собственные обязанности.
В первую очередь мастеру надо тщательно организовать работу своей линии. Это значит, что он должен установить нормы, определить место для хранения материалов и деталей и их количество, внедрить канбан, а также установить кнопки вызова, кнопки остановки оборудования и световые табло (андон).
Ознакомив рабочих со своими требованиями, мастер должен следить за тем, как они выполняются и какие это дает результаты. Если неожиданно происходит что-то нежелательное, он может пересмотреть свои стандарты.
В подобной ситуации крайне важно суметь отличить то, что соответствует норме, от несоответствия. Как бы тщательно ни была проведена стандартизация, если аномалии обнаружить невозможно или если, обнаружив их, мастер ведет себя так, словно их нет, он не выполняет своих обязанностей.
Проследите за тем, чтобы все поняли, что ненормально, и имели возможность об этом подумать. Ведь обнаружить аномалии означает сделать первый шаг к улучшению.
Вот некоторые проблемы, которые могут возникнуть, и их возможные решения.
У рабочего А каждый день остается много свободного времени. Возможно, он уже произвел слишком много деталей или начал делать работу, не требуемую стандартными операциями. И то и другое – аномалия. Рабочий А недостаточно загружен.
Рабочий Б, напротив, не выполняет свою работу вовремя. Он останавливает линию. Он пропускает какие-то операции и выпускает дефектную продукцию. Это также аномалии. Рабочий Б перегружен. Если рабочий А может выполнять работу рабочего Б за отведенное время, это означает, что мастер плохо обучил рабочего Б.
Рабочий В помогает руками работе автоматических устройств, что не предусмотрено стандартными операциями. Это тоже аномалия. При анализе этой проблемы обнаружено, что зажимы плохо фиксированы и, если рабочий уберет руки, то будет производиться дефектная продукция. Чтобы исправить это положение, мастер должен немедленно вызвать инженера или наладчиков.
Где-то обнаружена деталь без карточки канбан. Это также ненормально. Объяснением этому может быть следующее: время такта установлено неверно и детали сходят с конвейера слишком быстро, у всех рабочих остается слишком много свободного времени или следующий процесс перестал забирать то, что ему нужно, из-за неполадки. В любом случае это происшествие, которое нельзя игнорировать.
Для мастера, который определяет стандартные операции, все это – серьезные аномалии. Однако их причины установить нетрудно, например, стандартные операции слишком сложны, используются дефектные детали и материалы или что-то не в порядке с оборудованием.
Когда линия останавливается или производится дефектная продукция, обнаружить аномалии легко, поскольку все они проявляются в несоответствии продукции по количеству или качеству. Но есть и другие виды аномалий, обусловленные небольшими потерями в разных местах или ничтожной долей стандартных операций. Эти аномалии легко проглядеть и недооценить, тем не менее они способствуют росту затрат компании. Все эти отклонения должны учитываться при определении направлений дальнейшей работы по улучшениям и снижению затрат. Не игнорируйте аномалии, даже если они незначительны.
Задача мастера состоит в том, чтобы придерживаться цикла, состоящего из стандартизации, обнаружения аномалий, выяснения причин, улучшения и снова стандартизации. Реализуя этот цикл снова и снова, он может совмещать две внешне несовместимые функции: обеспечение качества и количества, с одной стороны, и снижения затрат – с другой.
Когда вы – мастер
Есть несколько условий, которые должен выполнять хороший мастер.
Во-первых, он всегда наблюдает за тем, что происходит на участке. Если он не наведывается на линию и не проявляет интереса к тому, что там происходит, уже одно это обрекает его на неудачу; тем самым он показывает, что не следит за выполнением норм, которые сам установил. Конечно, он не сумеет отличить норму от аномалии. Как тогда он будет заниматься улучшениями?
Во-вторых, он хорошо управляет своими подчиненными и направляет их. Это значит сказать им, что делать, и научить их этому. Это не означает заботу об их хорошем настроении или даже уступок им. Так хорошие человеческие взаимоотношения не установишь. Со временем один из подчиненных мастера сменит его на этом посту. Поэтому мастер должен научить их и в итоге подготовить к выполнению этих функций. Только таким образом он может стать по-настоящему «отцом» для всех.
У нас в Toyota мы нередко спрашиваем: «Разрешил ли кто-то создавать эти запасы или они возникли сами собой?» У нас есть материалы, оборудование и рабочие. Но временами ничего производить не нужно. Мастер должен быть в состоянии сказать своим подчиненным, когда остановиться, а когда возобновить работу. Управление и контроль – существенные составляющие его работы.
Третье важное условие – иметь широкий кругозор и принимать решения, выгодные для всей компании. Каким бы критичным ни был данный критерий для улучшения работы данного процесса, если это отрицательно скажется на работе предыдущего или следующего процесса или потребует передачи сложной работы на сторону, то подобную самостоятельность нельзя расценивать положительно.
Каждый мастер должен считать себя менеджером линии, иметь широкий кругозор и желание заботиться о благе всей компании.
Если после проведения стандартизации и улучшения мастер может сказать: «Пожалуйста, избавьте меня от этой работы», то это – самый лучший мастер. Он «обучил» свою линию, и теперь она может работать без него!