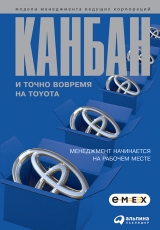
Текст книги "Канбан и «точно вовремя» на Toyota. Менеджмент начинается на рабочем месте"
Автор книги: авторов Коллектив
Жанры:
Деловая литература
,сообщить о нарушении
Текущая страница: 11 (всего у книги 15 страниц)
Это простейший вид расстановки. Каждый станок обслуживал один рабочий. Этот рабочий устанавливал на станок деталь, которую нужно было обработать, и включал его. Пока станок выполнял резку, он либо просто наблюдал за этим, либо смахивал щеткой стружку или смазывал станок.
Это приводило к потерям, связанным с ожиданиями. Пока станок резал, работал станок, а не рабочий.
То время, которое рабочий просто проводил у станка, считалось частью стандартного времени и в качестве таковой включалось в общие затраты времени на обработку данной детали.

Рис. 29. Один человек, один станок
2. Размещение по типам станков – один рабочий, два станкаОбсуждавшееся выше отдельное размещение было сопряжено с большими потерями, связанными в том числе с ожиданиями. Чтобы устранить некоторые из этих потерь, мы решили, что пока первый станок выполняет резку, тот же рабочий может устанавливать и снимать детали с другого станка. Мы сделали так, чтобы два станка либо стояли параллельно друг другу, либо образовывали букву Г, и поручили одному рабочему обслуживать два станка (это произошло примерно в 1946–1947 гг.).
Это стало значительным шагом вперед по сравнению с системой, при которой один рабочий обслуживал один станок. Однако когда рабочий стал отвечать за два станка, ему приходилось все время думать, сколько уже успел сделать другой станок, и он не мог сконцентрироваться на том, чем занимался. При такой системе он не мог спокойно перейти к последующему этапу работы.
Эту проблему решило следующее нововведение.
Мы установили автоматическое устройство, которое не позволяло поместить деталь на следующий станок, если резка на первом станке уже достигла определенного этапа. Мы также сделали так, чтобы станки останавливались автоматически. Стружка удалялась дерриком, а смазку режущего инструмента мы автоматизировали, так что рабочему больше не нужно было этим заниматься. Были проведены исследования, позволившие стандартизировать режущий инструмент (форму сверл и резцов и то, как они режут). Благодаря этому рабочие смогли уверенно переходить к следующему этапу работы.
Со временем, когда выяснилось, что у обслуживающего два станка рабочего все равно остается свободное время, он стал обслуживать три станка, образующие букву П или треугольник (рис. 31). В дальнейшем один рабочий стал обслуживать четыре станка, образующие квадрат или ромб (это произошло примерно в 1949–1950 гг.).

Рис. 30. Один рабочий, два станка

Рис. 31. Один рабочий, три или четыре станка
Добившись того, что один рабочий стал обслуживать одновременно несколько однотипных станков, мы сумели повысить производительность одного рабочего. Но побочным эффектом этого достижения стали излишние запасы заготовок. В цехе скапливались горы незаконченных деталей, уже прошедших обработку на токарном или сверлильном станке. К тому же, поскольку эти заготовки нельзя было отправить на следующий участок, в готовые детали они превращались очень не скоро. Чтобы решить эту проблему, станки разместили в порядке, соответствующем последовательности операций.
3. Размещение в соответствии с последовательностью процессаСтолкнувшись с перепроизводством заготовок и ростом объема их транспортировки, мы решили, что размещение рядом станков одного типа – не самый лучший вариант.
Мы поставили себе цель положить конец перепроизводству заготовок, минимизировать объем их транспортировки и сразу же доводить их до полной готовности.
Для этого мы поставили рядом станки, на которых детали обрабатывались по очереди, например токарный, сверлильный и фрезерный. Иными словами, мы постепенно перешли от размещения по типам станков к размещению в соответствии с последовательностью процесса (рис. 32).

Рис. 32. Размещение по типам станков или в соответствии с последовательностью процесса
Несложно было обнаружить, что размещение станков в соответствии с последовательностью операций процесса сводит к минимуму расстояние, преодолеваемое рабочим, и позволяет одному человеку обслуживать несколько станков. Однако когда мы оценили этот способ с точки зрения производительности всей производственной линии, то выяснилось, что он приводит к возникновению нескольких «дальних островов». Поддерживать общий баланс было сложно. В результате на каждом участке стали накапливаться груды деталей. Мы не могли разместить рабочих так, как того требовали происходящие перемены в спросе на выпускаемые нами машины.
В те годы мы постоянно изучали, какие движения приходится делать рабочим, и станки были размещены так, чтобы люди могли оставаться на месте. Тогда считалось, что чем меньше движений требуется, тем лучше, и перемещение от станка к станку было признано нежелательным. При этом подходе под производительностью понималась только продуктивность труда отдельного рабочего. Производительность всей производственной линии не учитывалась.
4. Становление производственной системы сглаженного потокаЧтобы обеспечить гладкий поток, повысить производительность и приучить рабочих к тому, что переходы от станка к станку также часть их работы, примерно в 1960 г. мы стали ставить станки в ряд, что позволило выпустить рабочих из их «клеток» (рис. 33). Преимуществом этой новой системы стало то, что рабочие во время работы могли обслуживать сразу несколько машин.

Рис. 33. Размещение станков в ряд
Однако у нас снова возникли проблемы. Сначала мы разместили станки в ряд и превратили каждую группу станков в независимую производственную линию. Когда мы расставляли рабочих исходя из числа машин, которые нужно было произвести, нередко оказывалось, что каждую линию должно обслуживать дробное число рабочих. Поскольку мы не могли приставить к станку полчеловека, нам пришлось эту цифру округлить в сторону увеличения. Поэтому как бы ни старалась группа рабочих, обслуживающих данную производственную линию, из-за переизбытка рабочей силы постоянно возникало перепроизводство, хотя и незначительное,
Выходом из этой ситуации стало объединение нескольких «независимых» производственных линий, с тем чтобы к ним можно было приставить целое число рабочих. Мы сумели найти такую расстановку персонала, которая позволила учитывать число машин, которые надо произвести. Мы до сих пор используем эту рабочую компоновку и теперь можем производить только то, что требуется.
Глава 7
Улучшения для сокращения трудозатрат
Хорошее знание рабочего места
Способы снижения трудозатрат намного легче найти тем, кто досконально знает существующие на производстве условия. Осознав, что их работа сопряжена с потерями, эти специалисты внедряют систему визуального контроля потерь, связанных либо с ожиданием, либо с излишними запасами, и прибегают к канбан для предотвращения перепроизводства. Их деятельность по снижению трудозатрат может включать мероприятия по:
• устранению потерь;
• перераспределению работы;
• сокращению числа занятых.
Поэтому любая работа по снижению трудозатрат должна начинаться с анализа существующих на производстве организационных условий. Однако некоторые могут считать, что существующая система не требует изменений. Они думают, что если коэффициент использования производственной линии удовлетворителен, а процент брака достаточно низок, то вся линия работает хорошо. Поэтому эти люди самоуспокаиваются и не имеют ни малейшего желания заниматься улучшениями.
Все рабочие трудятся примерно одинаково. Если мы понаблюдаем за ними, то увидим, что все выполняемые ими действия можно разделить на несколько категорий (см. рис. 34). Примеры этих действий приводятся ниже.

Рис. 34. Работа по снижению трудозатрат
Потери (муда): операции, которые не обязательны для выполнения данной работы и которые можно устранить немедленно.
Примеры: простои, ненужная транспортировка (складирование заготовок, транспортировка к месту, отличному от места назначения, и смена людей).
Операции, не добавляющие ценности. Эти операции не увеличивают добавленную ценность, но при существующей организации производства их приходится выполнять (иногда их можно рассматривать как потери). Чтобы их устранить, надо частично изменить организацию производства.
Примеры: хождение за деталями, распаковка купленных у поставщиков деталей, перекладывание деталей из большой палеты и нажатие кнопки.
Чистые операции, добавляющие ценность. Операции, которые добавляют ценность, можно встретить при обработке (изменение формы, качества или характера изделия, сборка и т. д.). Чтобы превратить предметы обработки, например сырье и полуфабрикаты, в детали и готовую продукцию, нужно потратить определенные усилия. Эти операции увеличивают добавленную ценность; чем выше их доля, тем операции эффективнее.
Примеры: сборка деталей, литье, штамповка листовой стали, сварка, термическая обработка шестерен, окраска корпуса и т. д.
Кроме того, в процессе работы рабочий делает движения, не связанные с выполнением стандартных операций, например налаживает оборудование или регулирует оснастку, а также перерабатывает дефектную продукцию.
И если проанализировать его работу, то можно обнаружить, что доля чистых операций, способных увеличить добавленную ценность, на удивление мала. А между тем все операции, кроме чистых, увеличивают затраты.
Цель нашей работы по снижению трудозатрат – максимизировать долю чистых операций, приблизить ее по возможности к 100 %.
Перераспределение работ
Обнаружив операции, которые не увеличивают добавленную ценность, следует срочно принять меры по их устранению, если только эти действия не потребуют больших затрат и не будут иметь неблагоприятных последствий для предыдущего процесса.
Например, если рабочие вынуждены далеко ходить за заготовками, то связанные с этим потери времени можно устранить, просто поставив стеллаж для заготовок рядом с рабочим местом. Сделав это, бригадир сможет перераспределить работу между всеми рабочими. И в результате им придется выполнять как чистые, так и прочие операции, которые нельзя устранить немедленно.
Как происходит это перераспределение, показано на рис. 35.

Рис. 35. Перераспределение работ
Рассмотрим внимательнее пример с неудачным распределением. Распределять избыточную производительность четвертого рабочего (которая приводит к потерям) поровну между всеми рабочими, как это показано на рисунке, не следует.
В этом случае предпринимается попытка сделать потери очевидными. Все понимают, что существует проблема, и ощущают потребность в улучшении. Но если мы перераспределим работу так, чтобы все рабочие работали одинаковое время, то потери станут скрытыми. В этом примере у каждого рабочего остается свободное время – 15 % времени такта (т. е. возникают потери, связанные с ожиданием). Если каждый проработает в таких условиях хотя бы десять дней, то привыкнет работать медленнее. И когда будут приняты меры по улучшению организации производства, эти рабочие, возможно, будут недовольны, поскольку эти меры приведут к увеличению их нагрузки.
Посмотрим теперь, какой прогресс обеспечивает показанное на рисунке удачное перераспределение работ. Если устранить потери и полностью загрузить работой трех рабочих, то работу, которую ранее выполняли пятеро, смогут делать 3–4 человека. Конечно, на самом деле потребуется четыре человека. В этом примере один человек может быть высвобожден немедленно, а другой будет загружен только на 40 %.
Следующее, что нужно сделать, высвободив благодаря перераспределению работ пятого рабочего, – решить проблемы неполной загрузки четвертого рабочего. Таким образом, следующая цель – устранить работу, для выполнения которой требуется только 0,4 человека.
Как можно без труда высвободить эти 0,4 человека? Решая проблему, мы должны тщательно продумать несколько вариантов. Можно автоматизировать производство – что потребует больших затрат. Или же установить на участке желоб, чтобы рабочим не нужно было больше ходить за деталями. Также можно использовать палеты меньшего размера.
На этом этапе не следует ставить перед собой слишком высокие цели. Вашей задачей остается высвобождение 0,4 рабочего. Примите такой план, который позволит вам решить эту задачу легко и с небольшими затратами.
По завершении работы по снижению затрат с тем, что ранее делали пять рабочих, будут успешно справляться трое и общее число занятых сократится на два. Посмотрим теперь на нашу производственную линию еще раз. Наверняка существуют потери, которых мы раньше не заметили. Еще мы можем обнаружить, что операции, с которыми мы раньше вынужденно мирились, не увеличивают добавленной ценности. Соберем всю нужную информацию и затем поставим перед собой новую вызванную переменами задачу – высвободить еще одного человека.
На этот раз сделать это будет уже не так легко. Какой бы вариант мы ни выбрали, воплощение этого замысла потребует гораздо более существенных расходов. И реализация наших планов может отразиться на работе следующего и предыдущего процессов. Возможно, сейчас с нововведениями следует повременить. Но не отчаивайтесь. Если вы знаете, в чем заключается проблема, и наблюдаете за производством каждый день, то однажды вам обязательно придет в голову замечательная идея.
Объемы ваших продаж могут побудить вас изменить время такта для каждого из этих процессов. Или смена модели потребует модернизации оборудования. Когда у вас возникнут эти новые потребности, вам могут понадобиться те планы, которые ранее вам пришлось отложить.
Даже если что-то нельзя сделать немедленно, не сдавайтесь. Решая проблемы, сохраняйте терпение.
От улучшения работы к улучшению оборудования
До сих пор мы обсуждали меры по снижению трудозатрат в следующей последовательности: перераспределение работ в целях устранения потерь, обеспечение полной занятости в течение времени такта и повторный анализ всей проблемы. Возвращаясь к исходным категориям, задачи нашей работы можно переформулировать следующим образом:
1. Немедленное устранение потерь.
2. Для операций, не увеличивающих добавленной ценности, начать улучшения с тех, которые легче всего исправить.
3. Сохранение чистых операций.
Когда мы занимаемся снижением трудозатрат, на решение некоторых задач, которые определяет второе направление нашей работы, могут потребоваться денежные средства. Третье направление связано с чистыми операциями, что, впрочем, не исключает сокращения ручного труда и автоматизации данного процесса. Если автоматизация действительно нужна, то провести ее следует как можно быстрее. Иными словами, все три направления этой работы предполагают улучшения, и в некоторых случаях эти улучшения надо делать одновременно.
Все меры по улучшению можно условно разделить на две категории. Улучшением работы называется изменение правил работы, перераспределение работ, определение места для зоны хранения и т. п. Совершенствование оборудования предполагает установку новых устройств, автоматического оборудования и т. п. И никогда не забывайте о том, что начинать нужно с улучшения работы и что в этом деле нет мелочей. Только по завершении этого этапа вы можете приступить к совершенствованию материальной базы.
Такая последовательность обусловлена следующими причинами:
1. Совершенствование оборудования требует денежных затрат. Цель наших улучшений – сокращение числа рабочих. Этого можно добиться и путем повышения качества работы. Когда кто-то тратит на совершенствование оборудования большие деньги, он поступает неправильно.
2. Совершенствованием оборудования нельзя заниматься постоянно. Если на этапе планирования данный подход и считался наилучшим, в дальнейшем он может оказаться неудачным. Любая затея сопряжена с определенным риском. Если потерпит неудачу план улучшения работы, то исправить ситуацию будет несложно. Но если неудачным окажется план совершенствования оборудования, то потраченные деньги уже не вернуть.
3. Улучшение работы – условие успешного совершенствования оборудования. Станки негибки. Если они устанавливаются там, где операции не стандартизированы или их последовательность до конца не продумана, вряд ли это даст положительный эффект. Например, штамповочный станок-автомат устанавливается на участке, где низкий контроль расходования материалов. Обработанные детали смешиваются с заготовками, и пресс-форма или автоматическое устройство выходит из строя. Чтобы не допустить повторения подобной ситуации, рабочим поручают наблюдать за станками-автоматами. Конечно, никакого снижения трудозатрат при этом не происходит.
Вот почему мы в Toyota всегда сначала совершенствуем работу и только потом – оборудование.
Та же логика применима и при проведении автоматизации «с человеческим лицом». Автоматизация, будучи одним из направлений совершенствования оборудования, имеет конечной целью снижение всех затрат. Плохо, когда автоматизация становится самоцелью, проводится без учета достигнутого на конкретном участке улучшения работы.
Недостаточные усилия по рационализации труда могут привести к тому, что дорогостоящий станок-автомат будет производить дефекты, часто ломаться, или использоваться недостаточно эффективно, или же к нему придется приставить специального рабочего. Учтите это, прежде чем приступить к проведению автоматизации.
Афоризмы Óно
Улучшить работу – значит найти наилучший способ делать вещи на существующем оборудовании. Это не значит установить новое оборудование. Это значит переосмыслить свои методы работы.
Мышление, ориентированное на людей
Когда работа организована так, что рабочие заняты все 100 % времени такта (рассчитанного на основе требуемого объема производства), то один рабочий может обслуживать несколько станков. В этом случае было бы неправильным считать потерями то, что станки время от времени простаивают. Если существует избыточная мощность, то следует снизить коэффициент использования станков.
Производить сверх требуемого количества означает создавать потери. Поэтому, продумывая компоновку работы и определяя набор стандартных операций, лучше сосредоточиться на человеке, а не на машине. Так вы скорее добьетесь снижения затрат.
Когда говорят о трудозатратах, то нередко подразумевают число занятых. И хотя при расчетах требуемых трудозатрат мы можем получить 0,1 и 0,5 человека, фактически работа потребует выделения одного человека. Поэтому уменьшение загруженности одного человека на 90 % не приведет к снижению затрат. Оно произойдет только в случае реального снижения числа занятых.
Целью снижения трудозатрат всегда должно быть уменьшение числа рабочих. С установкой какого-либо автоматического устройства трудоемкость может сократиться на 90 %. Но если к автомату все равно придется приставить рабочего (обычно для наблюдения за работой станка), то сокращения числа занятых может и не произойти, несмотря на потраченные деньги. Кто-то все равно назовет это сбережением труда. Но мы в Toyota говорим не о сбережении труда, а о «сбережении людей» (содзинка), и только тогда, когда действительно происходит снижение затрат.
От сбережения людей к меньшему числу людей
Когда разразился нефтяной кризис 1973 г., автомобилестроители поняли, что возможности роста их отрасли ограничены. С падением производства автомашин задача сокращения персонала путем автоматизации утратила свою актуальность. Многие считали, что автоматизация означает сохранение фиксированного числа рабочих.
Автоматизация в некоторых случаях означает передачу или транспортировку товаров без участия человека. По этой причине станки-автоматы становились все мощнее и мощнее.
Рабочие превратились в исполнителей вспомогательных операций, не подлежащих автоматизации. Так люди стали сдавать свои позиции автоматам.
Число выпускаемых машин никак не зависело от количества занятых в их производстве. Например, сколько бы машин ни производилось, определенный станок всегда обслуживался тремя рабочими. Вот почему говорили, что автоматизация означает сохранение фиксированного числа рабочих.
Но эта ситуация породила проблемы. Если объем производства автомашин упал, то и число рабочих на заводе должно было сократиться. Вот почему мы стали заботиться и об уменьшении числа рабочих, выполняющих данную работу.
Первый шаг к сокращению потребности в рабочей силе требует от нас переоценки автоматизации как таковой. В ходе этого процесса мы должны покончить с мифом о том, что автоматизация означает фиксированное число рабочих.
Подход «эту операцию можно автоматизировать, поэтому мы ее автоматизируем» никуда не годится. Задайте себе сначала следующий вопрос: «А нет ли у нас иного выхода, кроме автоматизации?» Например, вы сделали все, что могли, для улучшения работы. Для выполнения данной операции требуется 0,2 рабочего, а вы хотите довести эту цифру до нуля. В таком случае автоматизация может быть выходом.