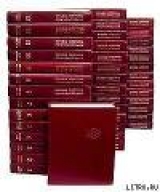
Текст книги "Большая Советская Энциклопедия (ТЕ)"
Автор книги: Большая Советская Энциклопедия
Жанр:
Энциклопедии
сообщить о нарушении
Текущая страница: 60 (всего у книги 79 страниц)
Термометрия
Термометри'я (от термо ... и... метрия ), раздел прикладной физики, посвященный разработке методов и средств измерения температуры. Т. является также разделом метрологии , в её задачи входит обеспечение единства и точности температурных измерений: установление температурных шкал , создание эталонов , разработка методик градуировки и поверки приборов для измерения температуры.
Температура не может быть измерена непосредственно. Об её изменении судят по изменению других физических свойств тел (объёма, давления, электрического сопротивления, эдс, интенсивности излучения и др.), связанных с температурой определёнными закономерностями. Поэтому методы измерения температуры являются по существу методами измерения указанных выше термометрических свойств, которые должны однозначно зависеть от температуры и измеряться достаточно просто и точно. При разработке конкретного метода или прибора необходимо выбрать термометрическое вещество, у которого соответствующее свойство хорошо воспроизводится и достаточно сильно изменяется с температурой.
Для измерения температуры (при любом методе) необходимо определить температурную шкалу.
Методы измерения температуры разнообразны; они зависят от принципов действия используемых приборов, диапазонов измеряемых температур, условий измерений и требуемой точности. Их можно разделить на две основные группы: контактные методы – собственно термометрия, и бесконтактные методы – Т. излучения, или пирометрия .
Общим и существенным для всех контактных методов измерения температуры является то, что всякий прибор, измеряющий температуру среды, должен находиться с ней в тепловом равновесии (см. Температура ), то есть иметь одинаковую со средой температуру.
Основными узлами всех приборов для измерения температуры являются: чувствительный элемент, где реализуется термометрическое свойство, и связанный с ним измерительный прибор, который измеряет численные значения этого свойства.
В газовой Т. термометрическим свойством является температурная зависимость давления газа (при постоянном объёме) или объёма газа (при постоянном давлении), соответственно различают – газовый термометр постоянного объёма и газовый термометр постоянного давления. Термометрическое вещество в этих термометрах – газ, приближающийся по своим свойствам к идеальному. Уравнение состояния идеального газа pV = RT устанавливает связь абсолютной температуры Т с давлением р (при постоянном объёме V) или Т с объёмом V (при постоянном давлении). Газовым термометром измеряют термодинамическую температуру. Точность прибора зависит от степени приближения используемого газа (азот, гелий) к идеальному.
В конденсационных термометрах термометрическим свойством является температурная зависимость давления насыщенных паров жидкости. Чувствительный элемент – резервуар с жидкостью и находящимися с ней в равновесии насыщенными парами – соединён капилляром с манометром. Термометрические вещества – обычно низкокипящие газы: кислород, аргон, неон, водород, гелий. Для вычисления температуры по измеренному давлению пользуются эмпирическими соотношениями. Диапазон применения конденсационного термометра ограничен. Высокоточные термометры (до 0,001 град ) служат для реализации реперных точек (см. Международная практическая температурная шкала ).
В термометрах жидкостных термометрическим свойством является тепловое расширение жидкостей, термометрическим веществом – главным образом ртуть. При определении температуры не производят измерений объёма жидкости; для этого при изготовлении калибруют капилляр термометра в °С, то есть по его длине наносят отметки с интервалами, соответствующими изменению объёма при заданном изменении температуры. Точность термометра зависит от точности калибровки.
В термометрах манометрических , которые являются приборами технического применения, используются те же термометрические свойства, что и в жидкостных или газовых термометрах.
В термометрах сопротивления термометрическим свойством является температурная зависимость электрического сопротивления чистых металлов, сплавов, полупроводников; термометрического вещества выбираются в зависимости от области температурных измерений и требуемой точности. Для определения температуры по измеренному электрическому сопротивлению пользуются эмпирическими формулами или таблицами. Термометры для точных измерений (платина, легированный германий) градуируются индивидуально.
В термометрах термоэлектрических с термопарой в качестве чувствительного элемента термометрическим свойством является термо-эдс термопары; термометрические вещества разнообразны и выбираются в зависимости от области применения и требуемой точности. Для определения температуры по измеренной эдс также пользуются эмпирическими формулами или таблицами. В связи со спецификой термоэлектрического термометра (дифференциального прибора) его точность зависит от точности поддержания и измерения температуры одного из спаев термопары («реперного» спая).
Измерительные приборы, которыми определяют численные значения термометрических свойств (манометры , потенциометры , логометры , мосты измерительные , милливольтметры и т. д.), называются вторичными приборами. Точность измерения температуры зависит от точности вторичных приборов. Термометры технического применения обычно индивидуально не градуируются и комплектуются соответствующими вторичными приборами, шкала которых нанесена непосредственно в °С.
В диапазоне криогенных (ниже 90 К) и сверхнизких (ниже 1 К) температур, кроме обычных методов измерения температур, применяются специфические (см. Низкие температуры ). Это – магнитная термометрия (диапазон 0,006—30 К; точность до 0,001 град ); методы, основанные на температурной зависимости Мёссбауэра эффекта и анизотропии g-излучения (ниже 1 К), термошумовой термометр с преобразователем на Джозефсона эффекте (ниже 1 К). Особой сложностью Т. в диапазоне сверхнизких температур является осуществление теплового контакта между термометром и средой.
Для обеспечения единства и точности температурных измерений служит Государственный эталон единицы температуры – кельвин , что позволяет в диапазоне 1,5—2800 К воспроизводить Международную практическую температурную шкалу (МПТШ) с наивысшей достижимой в настоящее время точностью. Путём сравнения с эталоном значения температур передаются образцовым приборам, по которым градуируются и проверяются рабочие приборы для измерения температуры. Образцовыми приборами являются германиевые (1,5– 13,8 К) и платиновые [13,8—903,9 К (630,7 °С)] термометры сопротивления, платинородий (90% Pt, 10% Rd) – платиновая термопара (630,7—1064,4 °С) и оптический пирометр (выше 1064,4 °С).
Лит.: Попов М. М., Термометрия и калориметрия, 2 изд., М., 1954; Методы измерения температуры. Сб., ч. 1—2, М., 1954; Температура и её измерение. Сб., пер. с англ., М., 1960; Сосновский А. Г., Столярова Н. И., Измерение температур, М., 1970.
Д. Н. Астров, Д. И. Шаревская.
Термометры метеорологические
Термо'метры метеорологи'ческие, группа термометров жидкостных специальной конструкции, предназначенных для метеорологических измерений главным образом на метеорологических станциях. Различные Т. м. в зависимости от назначения отличаются размерами, устройством, пределами измерений и ценой деления шкалы.
Для определения температуры и влажности воздуха пользуются ртутными психрометрическими Т. м. в стационарном и аспирационном психрометре . Цена их деления 0,2 °С; нижний предел измерения -35 °С, верхний 40 °С (или соответственно -25 °С и 50 °С). При температурах ниже -35 °С (вблизи точки замерзания ртути) показания ртутного Т. м. становятся ненадёжными; поэтому для измерения более низких температур пользуются низкоградусным спиртовым Т. м., устройство которого аналогично психрометрическому, цена деления его шкалы 0,5 °С, а пределы измерений варьируют: нижний -75, -65, -60 °С, а верхний 20, 25 °С.
Для измерения максимальной температуры за некоторый промежуток времени применяется ртутный максимальный Т. м. Цена деления его шкалы 0,5 °С; пределы измерения от -35 до 50 °С (или от -20 до 70 °С), рабочее положение почти горизонтальное (резервуар слегка опущен). Показания максимальных значений температуры сохраняются благодаря наличию в резервуаре 1 (рис. 1 ) штифта 2 и вакуума в капилляре 3 над ртутью. При повышении температуры избыток ртути из резервуара вытесняется в капилляр через узкое кольцеобразное отверстие между штифтом и стенками капилляра и остается там и при понижении температуры (так как в капилляре вакуум). Таким образом, положение конца столбика ртути относительно шкалы соответствует значению максимальной температуры. Приведение показаний термометра в соответствие с температурой в данный момент производят его встряхиванием. Для измерения минимальной температуры за некоторый промежуток времени используются спиртовые минимальные Т. м. Цена деления шкалы 0,5 °С; нижний предел измерений варьирует от -75 до -41 °С, верхний от 21 до 41 °С. Рабочее положение Т. – горизонтальное. Сохранение минимальных значений обеспечивается находящимся в капилляре 1 (рис. 2 ) внутри спирта штифтом – указателем 2. Утолщения штифта меньше внутреннего диаметра капилляра; поэтому при повышении температуры спирт, поступающий из резервуара в капилляр, обтекает штифт, не смещая его. При понижении температуры штифт после соприкосновения с мениском столбика спирта перемещается вместе с ним к резервуару (так как силы поверхностного натяжения плёнки спирта больше сил трения) и остаётся в ближайшем к резервуару положении. Положение конца штифта, ближайшего к мениску спирта, указывает минимальную температуру, а мениск – температуру в настоящий момент. До установки в рабочее положение минимальный Т. м. приподнимают резервуаром кверху и держат, пока штифт не опустится до мениска спирта.
Для определения температуры поверхности почвы пользуются ртутным Т. м. Деления его шкалы 0,5 °С; пределы измерения варьируются: нижний от -35 до -10 °С, верхний от 60 до 85 °С. Измерения температуры почвы на глубинах 5, 10, 15 и 20 см производят ртутным коленчатым Т. м. (Савинова). Цена деления его шкалы 0,5 °С; пределы измерения от -10 до 50 °С. Вблизи резервуара термометр изогнут под углом 135°, а капилляр от резервуара до начала шкалы теплоизолирован, что уменьшает влияние на показания Т. слоя почвы, лежащего над его резервуаром. Измерения температуры почвы на глубинах до нескольких м осуществляются ртутными почвенно-глубинными Т. м., помещенными в специальных установках. Цена деления его шкалы 0,2 °С; пределы измерения варьируют: нижний -20, -10°С, а верхний 30, 40 °С. Менее распространены ртутно-талиевые психрометрические Т. м. с пределами от -50 до 35 °С и некоторые др.
Кроме Т. м., в метеорологии применяются термометры сопротивления , термоэлектрические, транзисторные, биметаллические, радиационные и др. Термометры сопротивления широко используются в дистанционных и автоматических метеорологических станциях (металлические резисторы – медные или платиновые) и в радиозондах (полупроводниковые резисторы); термоэлектрические применяются для измерения градиентов температуры; транзисторные термометры (термотранзисторы) – в агрометеорологии, для измерения температуры пахотного слоя почвы; биметаллические термометры (термопреобразователи) применяются в термографах для регистрации температуры, радиационные термометры – в наземных, самолётных и спутниковых установках для измерения температуры различных участков поверхности Земли и облачных образований.
Лит.: Стернзат М. С., Метеорологические приборы и наблюдения, Л., 1968.
М. С. Стернзат.

Рис. 1. Устройство максимального термометра.

Рис. 2. Устройство минимального термометра.
Термомеханическая обработка
Термомехани'ческая обрабо'тка металлов (ТМО), совокупность операций деформации, нагрева и охлаждения (в различной последовательности), в результате которой формирование окончательной структуры металла, а следовательно, и его свойств происходит в условиях повышенной плотности и оптимального распределения несовершенств строения, созданных пластической деформацией. Т. о., особенностью этого способа изменения свойств металлических сплавов является сочетание операций обработки металлов давлением и термической обработки .
Возможность применения ТМО определяется тем, что на процессы структурных превращений существ влияние оказывают присутствующие в реальных сплавах несовершенства строения (дислокации , дефекты упаковки, вакансии ). С другой стороны, в результате некоторых структурных изменений образуются новые несовершенства, а также происходит перераспределение имеющихся несовершенств. Отсюда механизм и кинетика структурных изменений при ТМО зависят от характера и плотности несовершенств строения и, в свою очередь, влияют на их количество и распределение.
Для классификации технологических схем ТМО целесообразно выбрать в качестве классификационного признака последовательность проведения пластического деформирования и термической обработки (рис. ).
Совмещение пластической деформации с фазовыми превращениями получило впервые практическую реализацию в начале 20 в. при осуществлении патентирования в процессе производства стальной проволоки. Использование по своеобразной технологической схеме комбинированного воздействия пластической деформации и термической обработки привело к получению таких высоких механических свойств, которые были недостижимы при всех др. способах упрочняющей обработки. В 30-е гг. 20 в. применялась другая схема ТМО при упрочнении бериллиевой бронзы: закалка, холодная деформация, старение; такая обработка также обеспечила существенное повышение механических свойств сплава.
Развитие ТМО и создание её основных положений оказались возможными лишь на базе теории дислокаций, в частности тех её разделов, в которых устанавливается связь между несовершенствами строения и процессами структурообразования при превращениях. Исторически первой опробованной схемой термомеханического упрочнения машиностроительной стали (1954, США) была низкотемпературная термомеханическая обработка (НТМО). Смысл переохлаждения аустенита в схеме НТМО заключается в том, чтобы вести деформацию ниже температуры его рекристаллизации . Этим НТМО отличается от разработанной несколько позднее в СССР высокотемпературной термомеханической обработки (ВТМО), которая в дальнейшем получила большее распространение в связи с необходимостью повышения механических свойств массовых сортов стали, применяемых в современном машиностроении.
Температура проведения деформации при ВТМО лежит обычно выше верхней критической точки полиморфного превращения, поэтому неизбежны попытки проведения аналогии между ВТМО и термической обработкой с прокатного (или ковочного) нагрева. Принципиальное различие между этими видами обработки состоит в том, что при ВТМО создаются такие условия высокотемпературной пластической деформации и последующей закалки, при которых подавляется развитие рекристаллизационных процессов и создаётся особое структурное состояние, характеризующееся повышенной плотностью несовершенств и особым их распределением с образованием субструктуры полигонизации (см. Возврат металлов). Отсюда и экспериментально наблюдаемая развитая мозаичность строения стали после ВТМО, повышенная тонкая субмикроскопическая неоднородность строения и состава мартенсита , которая обеспечивает после ВТМО уникальное сочетание свойств, когда наряду с повышением прочности одновременно увеличиваются пластичность, вязкость и сопротивление хрупкому разрушению.
В таблице сопоставлены свойства типичной среднеуглеродистой машиностроительной легированной стали после ВТМО и НТМО. ТМО приводит к повышению усталостных характеристик; особенно велик прирост времени до разрушения в зоне ограниченной выносливости после ВТМО. В результате этой обработки повышается ударная выносливость стали, снижается порог хладноломкости и практически ликвидируется опасная склонность к хрупкости при отпуске (чего не наблюдается после НТМО). Развитие технологии ВТМО привело к созданию новой схемы – ВТМизО, в которой высокотемпературная деформация сочетается с изотермическим превращением. Изделия (в частности, рессоры), обработанные по этой схеме, характеризуются повышенными служебными характеристиками. В большем или меньшем объёме применяются все схемы термомеханического упрочнения, приведённые на рисунке. Выбор схемы проводится с учётом природы и назначения металлического сплава и конкретного изделия.
Механические свойства стали после ВТМО и НТМО
Обработка | Образцы для испытаний | Предел прочности sв , кгс/мм2 | Предел текучести sт , кгс/мм2 | Относи-тельное удлинение d , % | Относи-тельное сжатие y, % | Ударная вязкость, ak , кгс×м/см2 |
ВТМО + низкий отпуск | Плоские (нешлифованные) | 220—260 | 190—210 | 7—10 | 20—40 | 4—5 |
НТМО + низкий отпуск | Круглые (шлифованные) | 240—280 | 200—230 | 5—7 | 15—30 | 3—4 |
Примечание: 1 кгс/мм2 = 10 Мн/м2.
Эффективность конкретного способа термомеханического упрочнения оценивается по комплексу механических свойств. В инженерном смысле под повышением прочности понимают повышение сопротивления деформации и сопротивления разрушению в различных напряжённых состояниях, в том числе и таком, которое может вызвать образование хрупкой трещины и преждевременное разрушение. Поэтому наряду с традиционными испытаниями на растяжение, удар, усталость современные высокопрочные, в том числе термомеханически упрочнённые, стали должны оцениваться по критериям механики разрушения, с определением энергоёмкости процесса развития трещины и других аналогичных параметров.
Понимание физической сущности упрочнения в результате ТМО оказалось возможным лишь после того, как стали проясняться основные закономерности структурных изменений при горячей деформации. Старое представление о том, что горячая деформация всегда сопровождается рекристаллизацией, оказалось неверным.
При ТМО проводится немедленное и резкое охлаждение после завершения горячей деформации, и конечная структура упрочнённой стали наследует тонкое строение горячедеформированного аустенита. В зависимости от условий деформирования, определяемых величиной напряжения, температурой и скоростью деформации, структура аустенита по окончании горячей деформации сильно различается. Она может отвечать: а) состоянию горячего наклёпа с неупорядоченным распределением дислокаций, когда при последующей закалке прочность повышается и одновременно снижается сопротивление хрупкому разрушению; б) формированию субструктуры в результате динамического возврата и особенно чёткого и устойчивого субзёренного строения в результате динамической полигонизации – закалка в этом случае приведёт к оптимальному сочетанию высоких значений прочности и сопротивления хрупкому разрушению; в) состоянию динамической рекристаллизации, когда в одних объёмах еще сохранена повышенная плотность дислокаций, а в других она резко понижена – закалка в этом случае может привести к получению комплекса повышенных механических свойств, однако значения их в связи с неоднородностью и нестабильностью тонкого строения будут неустойчивы. Следовательно, режимы горячей деформации металлических сплавов при осуществлении ТМО необходимо выбирать с таким расчётом, чтобы получить развитую и устойчивую субструктуру в результате динамической полигонизации. При последующей закалке благодаря сдвиговому характеру мартенситного превращения субструктура деформированного аустенита, сформированная на стадии динамической полигонизации, наследуется образующимся мартенситом. Если, например, осуществляется др. схема ТМО, а именно ВТМизО (рис. ), то благодаря сдвиговому характеру превращения при образовании бейнита последний также наследует субструктуру горячедеформированного аустенита. Во всех случаях присутствие в конечных фазах (мартенсите и др.) этой устойчивой субструктуры определяет высокую дисперсность и мозаичность этих фаз, а также тонкое распределение примесей в них – это и приводит к повышению всех механических свойств, характеризуемому одновременным возрастанием сопротивления пластической деформации и сопротивления разрушению. Это наблюдается не только при «прямой» ТМО, но и при последующей после ТМО термической обработке. Открытое в СССР и широко используемое в отечественной и зарубежной практике явление «наследования» термомеханическое упрочнения базируется на том, что созданная при горячей деформации совершенная и устойчивая субструктура оказывается устойчивой при последующей перекристаллизации. В условиях повторной термической обработки после ТМО перекристаллизация протекает по сдвиговому механизму, что определяет сохранение субструктуры и, следовательно, комплекса высоких механических свойств, созданного при «прямой» ТМО. Развитие идей «наследования» термомеханического упрочнения позволило создать новую схему – предварительную термомеханическую обработку (ПТМО), нашедшую применение в СССР и США, а также объяснить высокий уровень свойств в результате патентирования, являющегося, по существу, разновидностью ТМО.
Применительно к дисперсионно-твердеющим сплавам ТМО в промышленности осуществляют по следующим технологическим схемам: а) нагрев до температуры закалки, деформация, немедленная закалка, старение (ВТМО); б) закалка, деформация, старение (НТМО). Первая схема сравнительно легко осуществима, но имеет недостаток – опасность сильного развития рекристаллизации в связи с высокой температурой деформации, проводимой при температуре закалки. Она широко используется в производстве прессованных изделий из многих алюминиевых сплавов, в которых небольшие добавки Mn, Сr и др. затрудняют рекристаллизацию. При осуществлении второй схемы могут возникать трудности, связанные с высоким сопротивлением деформации твёрдого раствора при комнатной температуре. Эта схема имеет ряд преимуществ: происходит старение с образованием весьма дисперсных фаз уже при холодной (или тёплой) деформации, создаётся более равномерное распределение выделений упрочняющих фаз, образующихся на дислокациях по всему объёму зёрен. Вторая схема ТМО успешно используется для повышения прочности стареющих медных и алюминиевых сплавов.
Лит.: Бернштейн М. Л., Термомеханическая обработка металлов и сплавов, т. 1—2, М., 1968.
М. Л. Бернштейн.

Классификация видов термомеханической обработки: ПТМО – предварительная термомеханическая обработка; ВТМО – высокотемпературная термомеханическая обработка; ВТМПО – высокотемпературная термомеханическая поверхностная обработка; ВТМизО – высокотемпературная термомеханическая изотермическая обработка; НТМО – низкотемпературная термомеханическая обработка; НТМизО – низкотемпературная термомеханическая изотермическая обработка; ВНТМО – высоко-низкотемпературная термомеханическая обработка; НВТМО – низко-высокотемпературная термомеханическая обработка; ДМО-1 – деформация мартенсита с последующим отпуском; ДМО-2 – деформация мартенсита после ВТМО с последующим отпуском; МТО – деформация немартенситных структур на площадке текучести, в том числе многократная ММТО; МТО-1 – механико-термическая обработка деформацией при комнатной температуре со старением; МТО-2 – механико-термическая обработка деформацией при повышенных температурах со старением; НВТМУ – наследственное высокотемпературное термомеханическое упрочнение; A1 и А3 – нижняя и верхняя критические точки; Мн – температура начала мартенситного превращения. Термомеханическая обработка I и IV классов основана на явлении наследования упрочнения, сохраняющегося после соответствующей термической обработки.