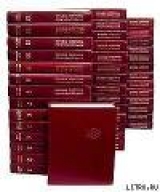
Текст книги "Большая Советская Энциклопедия (ЛИ)"
Автор книги: Большая Советская Энциклопедия
Жанр:
Энциклопедии
сообщить о нарушении
Текущая страница: 61 (всего у книги 67 страниц)
Литра
Ли'тра (греч. lítra), 1) древнейшая весовая и денежная единица Сицилии, равнявшаяся 219,7 г. С 6 в. до н. э. чеканилась серебряная Л. в 0,87 г. 2) Основная единица византийского монетного веса (327,456 г) – византийский фунт. В Древней Руси термин «Л.» известен с начала 10 в.
Литраж двигателя
Литра'ж дви'гателя, суммарный рабочий объём цилиндров двигателя внутреннего сгорания. Рабочий объём одного цилиндра равен произведению площади поперечного сечения цилиндра на ход поршня. Л. д. – показатель, характеризующий мощность двигателя. Обычно Л. д. измеряется в дм3 (литрах); у двигателей с небольшим рабочим объёмом цилиндров (например, у мотоциклетных) Л. д. часто измеряется в см3.
Литров Йозеф Иоганн
Ли'тров (Littrow) Йозеф Иоганн (13.3.1781, Бишофтайниц, – 30.11.1840, Вена), австрийский астроном, член-корреспондент Петербургской АН (1813). Окончил Пражский университет (1803). Профессор астрономии в Краковском (1807), Казанском (1810—16) университетах. Под руководством Л. в Казанской обсерватории были начаты (1814) систематические астрономические наблюдения. С 1819 директор Венской обсерватории. Основные труды посвящены вопросам практической и теоретической астрономии, известен как популяризатор астрономии.
Соч.: Theoretische und practische Astronomic, Tl 1—3, W., 1821—27; в рус. пер. – Тайны неба, СПБ, 1902—04.
Литровая мощность
Литро'вая мо'щность, наибольшая эффективная мощность, снимаемая с 1 дм3 (1л) рабочего объёма цилиндров двигателя внутреннего сгорания. Л. м. – один из основных показателей совершенства конструкции двигателя. Наибольшую Л. м., составляющую около 74 квт/л (100 л. с./л), имеют форсированные автомобильные и мотоциклетные двигатели (см. Форсированная мощность). У двигателей серийных легковых автомобилей Л. м. 29—44 квт/л, у дизельных двигателей грузовых автомобилей 12—18 квт/л.
Литт Теодор
Литт (Litt) Теодор (27.12.1880, Дюссельдорф, – 16.7.1962, Бонн), немецкий философ-идеалист и педагог. Профессор в Бонне (с 1919, затем с 1947) и Лейпциге (1920—37 и 1945—47). Работы Л. посвящены преимущественно вопросам культуры, социологии, педагогики. Взгляды Л. формировались под влиянием В. Дильтея, а также Г. Зиммеля и Э. Гуссерля. Определяющие для Л. идеи неогегельянства переплетаются в его мировоззрении с мотивами философии жизни. В области педагогики Л. исследовал исторические формы образования и его особенности в условиях современной технической цивилизации.
Соч.: Individuum und Gemeinschaft, 3 Aufl., Lpz., 1926; Geschichte und Leben, 3 Aufl., Lpz. – B., 1930; Möglichkeiten und Grenzen der Pädagogik, 2 Aufl., Lpz. – B., 1931; Hegel, Hdlb., 1953; Mensch und Welt, 2 Aufl., Hdlb., 1961; Technisches Denken und menschliche Bildung, 3 Aufl., Hdlb., 1964; Führen oder Wachsenlassen?, 13 Aufl., Stuttg., 1967; Ethik der Neuzeit, Bd 1—2, 2 Aufl., Münch., 1968; Naturwissenschaft und Menschenbildung, 5 Aufl., Hdlb., 1968.
Лит.: Erkenntnis und Verantwortung, Festschrift, Düsseldorf, 1960 (библ.); Lassahn R., Das Selbstverständnis der Pädagogik Th. Litts, Düsseldorf, 1968.
А. П. Огурцов.
Литтре Эмиль
Литтре' (Littré) Эмиль (1.2.1801, Париж, – 2.6.1881, там же), французский философ и филолог, представитель позитивизма, член Французской академии (1871), сенатор (с 1875). Ученик и последователь О. Конта, дополнил его учение о трёх стадиях развития человечества понятием четвёртой стадии – техники. Л. не разделял позднейшей эволюции Конта в направлении религиозного мистицизма. Вместе с Г. Н. Вырубовым основал и издавал журнал «La philosophie positive» (т. 1—26, 1867—81); перевёл на французский язык сочинения Гиппократа и Плиния. Автор «Истории французского языка» (т. 1—2, 1863) и «Словаря французского языка» (т. 1—4, 1863—72; т. 1—7, 1958), который сохранил своё значение.
Соч.: De la philosophie positive, P., 1845; Paroles de philosophie positive, 2 éd., P., 1863; Auguste Comte et la philosophie positive, 3 éd., P., 1873; в рус. пер. – Конт и Милль, в кн.: Тэн И., Об уме и познании, т. 2, СПБ, 1872; Несколько слов по поводу положительной философии, Берлин, 1865.
Лит.: Каро Э. М., Э. Литтре и позитивизм, пер. с франц., [М.], 1884; Aquarone S. R. A., The life and works of E. Littré, Leyden, 1958.
Литургическая драма
Литурги'ческая дра'ма, вид средневекового, преимущественно западноевропейского, религиозного представления (9—13 вв.). Входила в состав пасхальной или рождественской церковной службы (литургии); представляла собой инсценировку отдельных эпизодов Евангелия. Постепенно в Л. д. проникали реалистические, бытовые элементы, усиливалась зрелищная сторона представления, расширялся круг сюжетов – включались сцены из Ветхого завета, сказаний о святых и мучениках. С 1210 Л. д. разыгрывалась на паперти перед храмом; помимо духовенства, в ней участвовали миряне, а также ваганты и жонглёры, которым поручались роли торговцев, палачей, чертей и др. Наиболее значительное произведение – «Действо об Адаме» (середина 12 в.).
Лит.: История западноевропейского театра, т. 1, М., 1956.
Литургия (др.-греч. госуд. повинность)
Литурги'я (от греч. leiturgía – общественная обязанность), государственная повинность в древнегреческих полисах, которую несли состоятельные граждане и метеки (чужеземцы и отпущенные на волю рабы, располагавшие имуществом, оцениваемым в три таланта и выше). Они должны были оплачивать некоторые значительные государственные расходы. Л. могли быть обычными и чрезвычайными. К первым принадлежали: хорегия (оплата хоров, выступавших на драматических и музыкальных состязаниях), архифеория (содержание посольств, отправляемых на религиозные празднества), гимнасиархия (набор и содержание участников гимнастических соревнований) и некоторые др. Чрезвычайной Л. была, например, триерархия (снаряжение военного корабля-триеры). Особенно широкое распространение Л. получила в Афинах в 5—4 вв. до н. э. Введение Л. преследовало две цели: смягчить противоречия между богатыми и бедными и укрепить военную и политическую мощь полиса.
Помимо древнегреческих полисов, Л. была распространена в эллинистическом и римском Египте, в Римской империи и в Византии.
Лит.: Oertel F., Die Liturgie. Studien zur ptolemäischen und kaiserlichen Verwaltung Ägyptens, Lpz., 1917.
Литургия (христ. богослужение)
Литурги'я, христианское богослужение, во время которого совершается причащение (см. в ст. Таинства). Русское народное название Л. – обедня (по времени её проведения – до обеда); название Л. у католиков – месса. Первоначально форма и содержание Л. определялись устной традицией, разной в различных местностях. В Восточной Римской империи в 4—5 вв. сложились 2 основных типа Л. (приписываемых Василию Великому и Иоанну Златоусту); они перерабатывались и пополнялись вплоть до 14 в. В такой форме они сохранились в современной православной церкви. Л. включает чтение отрывков из Библии, песнопения, молитвы и ряд символических действий и процессий, аллегорически изображающих жизнь и смерть Христа. С конца 17 в. композиторами создавались законченные циклы песнопений Л. Классические образцы таких Л. принадлежат П. И. Чайковскому, А. Т. Гречанинову, С. В. Рахманинову.
Лит.: Schuiz Н.-J., Die byzantinische Liturgie, Freiburg im Breisgau, 1964.
Литы
Ли'ты, слой полусвободного населения у германских племён франков и саксов (у лангобардов им соответствовали альдии, у англо-саксов – лэты). Занимали промежуточное положение между свободными общинниками и рабами. В процессе формирования феодальных отношений вливались в возникавший класс феодально-зависимого крестьянства.
Литьё
Литьё, технологический процесс изготовления отливок, заключающийся в заполнении форм расплавленным материалом (литейным сплавом, пластмассой, некоторыми горными породами) и дальнейшей обработке полученных изделий (см. Литейное производство, Каменное литьё). Л. неправильно называют также продукцию литейного производства.
Литьё в кокиль
Литьё в ко'киль, кокильное литьё, способ получения фасонных отливок в металлических формах – кокилях. В отличие от других способов литья в металлические формы (литьё под давлением, центробежное литьё и др.), при Л. в к. заполнение формы жидким сплавом и его затвердевание происходят без какого-либо внешнего воздействия на жидкий металл, а лишь под действием силы тяжести. Основные операции и процессы: очистка кокиля от старой облицовки, прогрев его до 200—300°С, покрытие рабочей полости новым слоем облицовки, простановка стержней, закрывание частей кокиля, заливка металла, охлаждение и удаление полученной отливки. Процесс кристаллизации сплава при Л. в к. ускоряется, что способствует получению отливок с плотным и мелкозернистым строением, а следовательно, с хорошей герметичностью и высокими физико-механическими свойствами. Однако отливки из чугуна из-за образующихся на поверхности карбидов требуют последующего отжига. При многократном использовании кокиль коробится и размеры отливок в направлениях, перпендикулярных плоскости разъёма, увеличиваются.
В кокилях получают отливки из чугуна, стали, алюминиевых, магниевых и др. сплавов. Особенно эффективно применение кокильного литья при изготовлении отливок из алюминиевых и магниевых сплавов. Эти сплавы имеют относительно невысокую температуру плавления, поэтому один кокиль можно использовать до 10000 раз (с простановкой металлических стержней). До 45% всех отливок из этих сплавов получают в кокилях. При Л. в к. расширяется диапазон скоростей охлаждения сплавов и образования различных структур. Сталь имеет относительно высокую температуру плавления, стойкость кокилей при получении стальных отливок резко снижается, большинство поверхностей образуют стержни, поэтому метод кокильного литья для стали находит меньшее применение, чем для цветных сплавов.
Лит.: Кокильное литье, М., 1967; Петриченко А. М., Теория и технология кокильного литья, [К., 1967].
Н. П. Дубинин.
Литьё в оболочковые формы
Литьё в оболо'чковые фо'рмы, способ получения фасонных отливок из металлических сплавов в формах, состоящих из смеси песчаных зёрен (обычно кварцевых) и синтетического порошка (обычно фенолоформальдегидной смолы и пульвер-бакелита). Предпочтительно применение плакированных песчаных зёрен (покрытых слоем синтетической смолы).
Оболочковую форму получают одним из двух методов. Смесь насыпают на металлическую модель, нагретую до 300°С, выдерживают в течение нескольких десятков сек до образования тонкого упрочнённого слоя, избыток смеси удаляют. При использовании плакированной смеси её вдувают в зазор между нагретой моделью и наружной контурной плитой. В обоих случаях необходимо доупрочнение оболочки в печи (при температуре до 400°С) на модели. Полученные оболочковые полуформы скрепляют, и в них заливают жидкий сплав. Во избежание деформации форм под действием заливаемого сплава перед заливкой их помещают в металлический кожух, а пространство между его стенками и формой заполняют металлической дробью, наличие которой воздействует также на температурный режим охлаждающейся отливки.
Этим способом изготавливают различные отливки массой до 25 кг. Преимуществами способа являются значительные повышение производительности по сравнению с изготовлением отливок литьём в песчаные формы, управление тепловым режимом охлаждения отливки и возможность механизировать процесс.
П. П. Берг.
Литьё в песчаные формы
Литьё в песча'ные фо'рмы, способ получения отливок в разовых литейных формах, изготовленных из песчано-глинистых формовочных смесей (см. Литейное производство).
Литьё в самотвердеющие формы
Литьё в самотверде'ющие фо'рмы, процесс получения отливок, при котором используют литейные формы и стержни, изготовленные из смесей, затвердевающих на воздухе и не требующих сушки или дополнительной обработки внешними реагентами.
Самотвердеющие смеси (СС) состоят из наполнителей, связующих материалов, отвердителей, иногда в их состав входит вода. В некоторых смесях один и тот же материал (например, цемент) выполняет роль связующего и обеспечивает самозатвердевание. Применяются неорганические и органические связующие материалы. Используют смеси 3 типов: пластичные – ПСС, жидкие – ЖСС и сыпучие – ССС (термины условные). Стержни и формы из ПСС при изготовлении необходимо уплотнять, ЖСС наливают в стержневые ящики и на модели, ССС почти не требуют уплотнения.
В 30-х гг. 20 в. получили распространение ПСС с цементом и кварцевым песком (применяют в литейном производстве, преимущественно в странах Западной Европы). Формы и стержни из них затвердевают на воздухе в течение 24—72 ч. В начале 60-х гг. в СССР были разработаны принципиально новые смеси – ЖСС, состоящие из наполнителей, неорганических или органических связующих материалов, отвердителей и поверхностно-активных веществ (ПАВ). Смеси без ПАВ или с очень малым содержанием ПАВ используются в качестве ПСС и ССС. Большое распространение в СССР и ряде зарубежных стран получили ЖСС и ПСС, включающие в себя жидкое стекло. В них в качестве отвердитсля применяют различные продукты, в частности материалы, в которые входит двухкальциевый силикат (например, шлак феррохромового производства). Длительность затвердевания стержней и форм из этих смесей на воздухе 20—60 мин. Для улучшения выбиваемости СС, содержащих неорганический связующий материал (например, жидкое стекло), иногда вводят небольшое количество специальных (преимущественно органических) добавок.
Во всех промышленно развитых странах находят применение смеси с органическими связующими добавками, например, смеси, в состав которых входят искусственные смолы – карбамидно-фурановые, фенолофурановые и фенольные. В составы смесей при их изготовлении вводят отвердители: ортофосфорную кислоту, паратолуолсульфокислоту, бензолсульфокислоту и др. Из этих смесей изготовляют главным образом стержни, которые легко выбиваются из отливок. Время затвердевания стержней на воздухе от 10 до 30 мин. Все типы СС применяют для изготовления форм и стержней преимущественно в индивидуальном, мелкосерийном и крупносерийном производстве для получения отливок практически любой формы и размеров из стали, чугуна и нежелезных сплавов. Разрабатываются смеси с очень коротким циклом затвердевания, соответствующим требованиям массового производства.
А. М. Лясс.
Литьё по выплавляемым моделям
Литьё по выплавля'емым моде'лям, способ получения фасонных отливок из металлических сплавов в неразъёмной, горячей и негазотворной оболочковой форме, рабочая полость которой образована удалением литейной модели выжиганием, выплавлением или растворением.
При этом способе литья в пресс-формы (обычно металлические) запрессовывают модельный состав, который после затвердевания образует модели деталей и литниковой системы. Модельный состав удаляют, чаще всего выплавляя его в горячей воде (отсюда и название способа – литьё по выплавляемым моделям). Полученные оболочки прокаливают при температуре 800—1000°С и заливают металлом.
Способ обеспечивает получение сложных по форме отливок массой от нескольких г до десятков кг, со стенками толщиной от 0,5 мм и более, с поверхностью, соответствующей 4—6-му классам чистоты, и с высокой точностью размеров по сравнению с др. способами литья. Указанные особенности послужили причиной прежних названий способа – точное, или прецизионное литьё. Размеры отливок, полученных Л. по в. м., максимально приближены к размерам готовой детали, вследствие чего за счёт сокращения механической обработки снижается стоимость готового изделия.
Методом Л. по в. м. изготовляют художественные отливки, ювелирные изделия, зубные протезы и др. изделия. Этот способ литья, являясь одним из древних, получил широкое промышленное применение в результате совершенствования технологии литейного производства и изучения свойств кремнийорганических соединений.
В СССР Л. по в. м. сосредоточено в больших высокомеханизированных цехах, которые производят до 2,5 тыс. т готовых отливок в год. Достижением советской промышленности является создание комплексно-автоматизированного производства Л. по в. м.
В. Н. Иванов.
Литьё под давлением металлов
Литьё под давле'нием металлов, способ получения отливок из сплавов цветных металлов и сталей некоторых марок в пресс-формах, которые сплав заполняет с большой скоростью под высоким давлением, приобретая очертания отливки. Этим способом получают детали сантехнического оборудования, карбюраторов двигателей, алюминиевые блоки двигателей и др. Литьё производят на литейных машинах с холодной и горячей камерами прессования (рис.). Литейные формы, называются обычно пресс-формами, изготовляют из стали. Оформляющая полость формы соответствует наружной поверхности отливки с учётом факторов, влияющих на размерную точность. Кроме того, в пресс-форму входят подвижные металлические стержни, образующие внутренние полости отливок, и выталкиватели.
При получении отливок на литейных машинах с холодной камерой прессования (рис., а, б) необходимое количество сплава заливается в камеру прессования вручную или заливочным дозирующим устройством. Сплав из камеры прессования под давлением прессующего поршня через литниковые каналы поступает в оформляющую полость плотно закрытой формы, излишек сплава остаётся в камере прессования в виде пресс-остатка и удаляется. После затвердевания сплава форму открывают, снимают подвижные стержни и отливка выталкивателями удаляется из формы. При получении отливок на машинах с горячей камерой прессования (рис., в) сплав из тигля нагревательной печи самотёком поступает в камеру прессования. После заполнения камеры прессования срабатывает автоматическое устройство (реле времени, настроенное на определённый интервал), а поршень начинает давить на жидкий сплав, который через обогреваемый мундштук и литниковую втулку под давлением поступает по литниковым каналам в оформляющую полость формы и кристаллизуется. Через определённое время, необходимое для образования отливки, срабатывает автоматическое устройство на раскрытие формы, и отливка удаляется выталкивателями. У полученных отливок обрубают (обрезают) заливы (облой), элементы литниковых систем, затем их очищают вручную или на машинах; если необходимо, производят термообработку.
Для этого метода литья характерны высокая скорость прессования и большое удельное давление [30—150 Мн/м2 (300—1500 кгс/см2)] на жидкий сплав в форме. Качество отливок зависит от ряда технологических и конструктивных факторов, например выбора сплава, конструкции отливки, литниковой и вентиляционной систем, формы, стабильности температуры сплава и формы, вакуумирования формы для предупреждения образования пористости и т. д. Метод обеспечивает высокую производительность, точность размеров (3—7-й классы точности), чёткость рельефа и качество поверхности (для отливок массой до 45 кг из алюминиевых сплавов – 5—8-й классы чистоты). Производительность машин от 1 до 50 заливок в мин. Применяют многогнёздные формы, в которых за 1 заливку изготовляют более 20 деталей.
Лит.: Пляцкий В. М., Технология литья под давлением, 3 изд., М., 1957; Беккер М. Б., Литье под давлением,2 изд., М., 1973.
М. Б. Беккер.

Схемы литья под давлением на машинах с камерами прессования: а – холодной горизонтальной; б – холодной вертикальной; в – горячей; 1 – плита крепления подвижной части формы; 2 – выталкиватели; 3 – подвижная матрица формы; 4 – полость формы (отливка); 5 – неподвижная матрица формы; 6 – камера прессования; 7 – прессующий поршень; 8 – пресс-остаток; 9 – тигель нагревательной передачи; 10 – обогреваемый мундштук.
Литьё под давлением полимерных материалов
Литьё под давле'нием полимерных материалов, метод изготовления изделий различной формы из пластических масс (термопластови реактопластов) и резиновых смесей, при котором материал нагревается и размягчается (пластицируется) в обогреваемом цилиндре литьевой машины (рис.), откуда под давлением червяка или поршня нагнетается в литьевую форму. После остывания материала (для термопластов), отверждения (для реактопластов) или вулканизации (для резиновых смесей) он сохраняет конфигурацию и размеры изделия. Метод пригоден для переработки термопластов в изделия объёмом от 0,1 до 30 000 см3, а также специально разработанных реактопластов и резиновых смесей в изделия объёмом до 3000 см3. Преимущества метода по сравнению с другими методами формования изделий из полимерных материалов – высокие производительность и качество изготовляемых изделий.
Лит.: Завгородний В. К., Калинчев Э. Л., Махаринский Е. Г., Оборудование предприятий по переработке пластмасс, Л., 1972.
В. К. Завгородний.

Червячная литьевая машина для полимерных материалов: 1 и 2 – приводы поступательного и вращательного движений червяка; 3 – червяк (при пластикации материала совершает вращательное и медленное поступательное движение вправо; при нагнетании материала в форму – быстрое поступательное движение влево); 4 – бункер; 5 – нагреваемый материал; 6 – расплавленный (пластицированный) материал; 7 – обогреваемый цилиндр; 8 – обогреватели; 9 – литьевая форма; 10 – изделие.