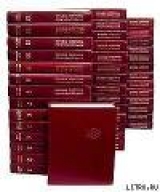
Текст книги "Большая Советская Энциклопедия (ЛИ)"
Автор книги: Большая Советская Энциклопедия
Жанр:
Энциклопедии
сообщить о нарушении
Текущая страница: 42 (всего у книги 67 страниц)
Литвиненко-Вольгемут Мария Ивановна
Литвине'нко-Вольгему'т (по мужу – Вольгемут) Мария Ивановна [по уточнённым данным, 1(13).2.1892, Киев, – 3.4.1966, там же], украинская советская певица (лирико-драматическое сопрано), педагог, народная артистка СССР (1936). Член КПСС с 1944. В 1912 окончила Киевское музыкальное училище по классу пения; дебютировала в украинской труппе Н. К. Садовского. Выступала в оперных театрах Петрограда (1914—16), Винницы (1919—22), Харькова (1923—35) и Киева (1935—53). Л.-В. обладала сильным чистым голосом, высокоразвитой вокальной техникой, создала яркие, отличающиеся национальным колоритом образы – Варвара («Богдан Хмельницкий» Данькевича), Настя и Терпелиха («Тарас Бульба» и «Наталка-Полтавка» Лысенко), Одарка («Запорожец за Дунаем» Гулак-Артемовского) и др. Исполняла партии классического репертуара. С 1944 профессор Киевской консерватории. Государственная премия СССР (1946). Награждена орденом Ленина и 3 др. орденами.
Лит.: Поляков А. И., М. I. Литвиненко-Вольгемут, Київ, 1956; Швачко Т. А., Mapiя Литвиненко-Вольгемут, Київ, 1972.

М. И. Литвиненко-Вогельмут.
Литвинов (город в Чехословакии)
Ли'твинов (Litvínov), город на С. Чехословакии, в Чешской Социалистической Республике, в Северо-Чешской области 23 тыс. жителей (1971). Ж.-д. узел. Один из центров промышленности в Северо-Чешском угольном бассейне. Крупный нефтехимический комбинат (в Залужи); текстильная промышленность.
Литвинов Дмитрий Иванович
Литви'нов Дмитрий Иванович [17(29).12.1854, Москва, – 5.7.1929, Ленинград], советский ботаник. Окончил Московское техническое училище (1879). Учёный хранитель Ботанического музея АН в Петербурге (с 1898 до конца жизни). Изучал флору высших растений Европейской части России, Кавказа, Средней Азии, Сибири, Маньчжурии. Ряд трудов по исторической географии растений, в частности по происхождению флоры степей и южных сосновых боров («Геоботанические заметки о флоре Европейской России», 1891). Продолжил издание «Гербария русской флоры», начатое С. И. Коржинским.
Соч.: Библиография флоры Сибири, СПБ, 1909.
Лит.: Городков Б. Н., Д. И Литвинов, «Природа», 1929, № 11.
Литвинов Максим Максимович
Литви'нов Максим Максимович (настоящая фамилия и имя – Баллах Макс; партийный псевдоним – «Папаша», Максимович, Феликс и др.) [5(17).7.1876, Белосток, ныне в Польше, – 31.12.1951, Москва], советский государственный и партийный деятель, дипломат. Член Коммунистической партии с 1898. Родился в семье служащего. С 1898 вёл социал-демократическую пропаганду в рабочих кружках г. Клинцы Черниговской губернии. В 1900 член Киевского комитета РСДРП. В 1901 арестован, в 1902 один из организаторов и участников побега 11 «искровцев» из Лукьяновской тюрьмы Киева; эмигрировал в Швейцарию. Агент «Искры», ведал транспортировкой газеты в Россию; член Администрации Заграничной лиги русской революционной социал-демократии. После 2-го съезда РСДРП (1903) – большевик, член Рижского, Северо-западного комитетов партии и Бюро комитетов большинства. Делегат 3-го съезда РСДРП (1905); участвовал в организации первой легальной большевистской газеты «Новая жизнь» в Петербурге. В 1907 секретарь делегации РСДРП на Штутгартском конгрессе 2-го Интернационала. С 1908 секретарь Лондонской группы большевиков; представитель от большевиков в Международном социалистическом бюро. В феврале 1915 по поручению ЦК РСДРП выступил на конференции социалистов стран Антанты в Лондоне с заявлением (проект составлен В. И. Лениным), осуждающим империалистическую войну. В 1918 назначен дипломатическим представителем РСФСР в Великобритании, но Британское правительство не признало его полномочий и задержало как заложника; Л. был обменен на арестованного в России английского разведчика Локкарта. В 1918—21 член коллегии Наркоминдел; в конце 1918 от имени Советского правительства в Стокгольме выступил с мирными предложениями к державам Антанты (так называемая Декларация Литвинова); в 1920 полпред в Эстонии. С 1921 заместитель наркома иностранных дел, одновременно член коллегии НК РКИ и заместитель председателя Главконцесскома. В 1922 заместитель руководителя советской делегации Г. В. Чичерина на Генуэзской конференции (апрель – май), затем глава делегации на Гаагской конференции (июнь – июль), председатель Московской международной конференции по разоружению (декабрь). В 1927—30 глава делегации в Подготовительной комиссии к конференции по разоружению в Женеве. В 1930—39 нарком иностранных дел СССР; содействовал установлению дипломатических отношений с США, приёму СССР в Лигу Наций, в которой представлял СССР в 1934—38. Л. был выдающимся советским дипломатом, умело проводившим ленинскую внешнюю политику. В 1941—1943 заместитель наркома иностранных дел, одновременно посол СССР в США и в 1942—43 посланник СССР на Кубе. Участник Московской конференции министров иностранных дел СССР, США, Великобритании в октябре 1943. Делегат 8, 14—18-го съездов партии; на 17—18-м съездах партии избирался членом ЦК ВКП(б). Член ЦИК СССР. Депутат Верховного Совета СССР 1—2-го созывов. Автор многих работ по вопросам внешней политики СССР. Награжден орденом Ленина и орденом Трудового Красного Знамени.
Соч.: Внешняя политика СССР. Речи и заявления. 1927—1935, М., 1935; Неопубликованные письма М. М. Литвинова В. И. Ленину (1913—1915 гг.), там же, 1966, №4.
Лит.: Ленин В. И., Полн. собр. соч., 5 изд. (см. Справочный том, ч. 2, с. 450); Гнедин Е., Революционер-дипломат ленинской школы, «Новый мир», 1970, № 2, с. 256—261 (библ.); Шейнис З. С., В Генуе и Гааге. (Страницы дипломатической деятельности М. М. Литвинова), «Новая и Новейшая история», 1968, № 3—4.

М. М. Литвинов.
Литвинов Степан Васильевич
Литви'нов Степан Васильевич (1785, Барнаул, – 1848, там же), русский изобретатель паровых машин. С 12 лет начал службу в канцелярии Колывано-Воскресенских заводов, позднее работал на Нерчинских заводах. Создал роторную воздуходувку с непрерывной подачей воздуха в печи (1805) и «двоедувный мех» – прототип поршневого компрессора двойного действия (1817). В 1817—27 сконструировал паросиловые установки, в которых впервые предложил ряд прогрессивных решений: прямоточный котлоагрегат, пароперегреватель, двухступенчатое парообразование и др.
Лит.: Савельев Н. Я., Выдающийся паротехник-барнаулец – Степан Васильевич Литвинов и его паровые машины, Барнаул, 1950.
Литвин-Седой Зиновий Яковлевич
Литви'н-Седо'й, Литвин Зиновий Яковлевич (Звулон Янкелев) (партийный псевдоним Седой, Виллонен, Иголкин, Быстров) [4(16).3.1879, Коломна, – 15.10.1947, Москва], советский и партийный деятель. Член Коммунистической партии с 1897. Родился в семье рабочего. Рабочий-металлист. В революционном движении с 1893. Участник Московского рабочего союза. Вёл партийную работу в Москве, Коломне, Тамбове, Петербурге, Н. Новгороде, Тбилиси. Неоднократно подвергался арестам и высылкам. В 1905 член МК РСДРП; в декабре, во время Московского вооруженного восстания, начальник штаба боевых дружин на Пресне, сражался на баррикадах, был ранен. В 1906 в Финляндии секретарь военно-революционной организации РСДРП. Делегат 4-го съезда партии. В июле 1906 участник восстания моряков в Свеаборге. До 1917 в эмиграции во Франции, Канаде, США. В 1917 член Киевского горсовета. В 1918 комиссар 121-го стрелкового полка, участвовал в боях за Царицын (Волгоград). В 1919—21 работал в Центральном управлении военных сообщений, затем в НКПС. В 1921—39 директор хлопчатобумажного техникума в Москве. Бессменный член Московского совета. Делегат 10, 11, 13—16-го съездов партии. На 10-м съезде РКП(б) избирался членом ЦКК. С 1939 персональный пенсионер. Автор ряда воспоминаний о Московском вооруженном восстании в дек. 1905. Награждён орденом Красного Знамени.
Лит.: В рядах московских большевиков, в кн.: На баррикадах, М., 1955.

З. Я. Литвин-Седой.
Литгоу
Ли'тгоу (Litgow), город в Австралийском Союзе, в штате Новый Южный Уэльс. 12,8 тыс. жителей (1970). Ж.-д. станция. Центр добычи каменного угля. Металлургическая, текстильная, швейная промышленность.
Литейная лихорадка
Лите'йная лихора'дка, лихорадка литейщиков, латунная лихорадка, профессиональное заболевание, возникающее при вдыхании паров различных металлов (цинка, меди, латуни, железа и др.). Начинается с озноба, повышения температуры тела до 39°С, чувства стеснения и боли в груди, головной боли, головокружения, общей слабости, сухого кашля. Обычно при прекращении контакта с вредоносным фактором все болезненные явления исчезают. Предполагают, что пары металлов (например, цинка) в организме быстро превращаются в окись, которая из-за своей высокой дисперсности глубоко проникает в дыхательные пути. Будучи носителем большого электрического заряда, она вступает в связь с клеточными белками, вызывая их денатурацию. Изменённые белки, всасываясь в кровь, обусловливают возникновение лихорадки. Экспериментальные исследования и наблюдения показали, что после перенесённого приступа Л. л. остаётся временный «иммунитет», когда больные оказываются более устойчивыми к вредоносному фактору. Однако часто повторяющиеся приступы Л. л. могут привести к истощению организма.
Лечение: постельный режим, сердечные средства, внутривенное введение глюкозы, при подозрении на вторичную инфекцию – антибиотики.
Профилактика: улучшение санитарно-технических условий труда; работы, связанные с электросваркой, плавкой, разливом металла, должны проводиться в отдельном помещении, оборудованном общей приточно-вытяжной вентиляцией. Применение индивидуальных респираторов и спецодежды. После работы – обязательный горячий душ.
Я. О. Ольшанский.
Литейная модель
Лите'йная моде'ль, приспособление, предназначенное для получения в литейной форме рабочей полости будущей отливки. Л. м. является, как правило, частью модельного комплекта. Л. м. могут быть неразъёмными (для простых по конфигурации отливок) или же состоять из двух и более частей. В индивидуальном производстве их изготавливают из дерева или пластмасс, в массовом и крупносерийном – из металла и пластмасс. При получении отливок методом литья по выплавляемым или газифицируемым моделям применяют разовые Л. м. из легкоплавкого состава или пенопласта.
Литейная форма
Лите'йная фо'рма, применяемая в литейном производстве форма для получения отливок. В Л. ф. заливают расплавленный материал (металлический или каменный). Материалами для изготовления Л. ф. служат кварцевый песок, бентонит, глина и др. (см. Стержневая смесь, Формовочная смесь), а также металлы (см. Литьё в кокиль, Литьё под давлением).
Литейное производство
Лите'йное произво'дство, одна из отраслей промышленности, продукцией которой являются отливки, получаемые в литейных формах при заполнении их жидким сплавом. Годовой объём производства отливок в мире превышает 80 млн. т, из которых около 25% приходится на СССР (1972). Методами литья изготовляется в среднем около 40% (по массе) заготовок деталей машин, а в некоторых отраслях машиностроения, например в станкостроении, доля литых изделий составляет 80%. Из всех производимых литых заготовок машиностроение потребляет примерно 70%, металлургическая промышленность – 20%, производство санитарно-технического оборудования – 10%. Литые детали используют в металлообрабатывающих станках, двигателях внутреннего сгорания, компрессорах, насосах, электродвигателях, паровых и гидравлических турбинах, прокатных станах, с.-х. машинах, автомобилях, тракторах, локомотивах, вагонах. Значительный объём литых изделий, особенно из цветных сплавов, потребляют авиация, оборонная промышленность, приборостроение. Л. п. поставляет также водопроводные и канализационные трубы, ванны, радиаторы, отопительные котлы, печную арматуру и др. Широкое применение отливок объясняется тем, что их форму легче приблизить к конфигурации готовых изделий, чем форму заготовок, производимых др. способами, например ковкой. Литьём можно получить заготовки различной сложности с небольшими припусками, что уменьшает расход металла, сокращает затраты на механическую обработку и, в конечном счёте, снижает себестоимость изделий. Литьём могут быть изготовлены изделия практически любой массы – от нескольких г до сотен т, со стенками толщиной от десятых долей мм до нескольких м. Основные сплавы, из которых изготовляют отливки: серый, ковкий и легированный чугун (до 75% всех отливок по массе), углеродистые и легированные стали (свыше 20%) и цветные сплавы (медные, алюминиевые, цинковые и магниевые). Область применения литых деталей непрерывно расширяется.
Историческая справка. Производство литых изделий известно с глубокой древности (2—1-е тысячелетия до н. э.): в Китае, Индии, Вавилоне, Египте, Греции, Риме отливали предметы вооружения, религиозного культа, искусства, домашнего обихода. В 13—14 вв. Византия, Венеция, Генуя, Флоренция славились своими литыми изделиями. В русском государстве в 14—15 вв. отливались бронзовые и чугунные пушки, ядра и колокола (на Урале). В 1479 построена в Москве «пушечная изба» – первый литейный завод. В царствование Ивана IV созданы литейные заводы в Туле, Кашире и др. городах. В 1586 А. Чохов отлил «Царь-пушку» (около 40 т). При Петре I изготовление отливок увеличилось, были созданы литейные заводы на Урале, Юге и Севере государства. В 17 в. чугунные отливки экспортировались за границу. В России созданы замечательные образцы литейного искусства: в 1735 «Царь-колокол» (свыше 200 т) И. Ф. и М. И. Маториными, в 1782 памятник Петру I «Медный всадник» (22 т) Э. Фальконе, в 1816 памятник К. Минину и Д. М. Пожарскому В. П. Екимовым, в 1850 скульптурные группы Аничкова моста в Петербурге П. К. Клодтом и др. Одна из самых крупных отливок в мире – шабот (нижняя часть, воспринимающая удар) парового молота (650 т) изготовлена в 1873 на Пермском заводе. Известно мастерство литейщиков старых русских заводов – Каслинского, Путиловского, Сормовского, Коломенского и др.
Первые попытки научного обоснования некоторых процессов литья сделали в своих работах Р. Реомюр, М. В. Ломоносови др. учёные. Однако до 19 в. при литье использовали ранее накопленный многовековой опыт мастеров. Лишь в начале 19 в. были заложены теоретические основы литейной технологии, были применены научные методы в решении конкретных производственных задач. Труды Д. Бернулли, Л. Эйлера, М. В. Ломоносова послужили прочной базой для разработки и совершенствования литейной технологии. В работах русских учёных П. П. Аносова, Н. В. Калакуцкого и А. С. Лаврова были впервые научно объяснены процессы кристаллизации, возникновения ликвации и внутренних напряжений в отливках, намечены пути к повышению качества отливок. В 1868 Д. К. Чернов открыл критические точки металлов. Его труды продолжили А. А. Байков, А. М. Бочвар, В. Е. Грум-Гржимайло, позднее Н. С. Курнаков и др. русские учёные. Большое значение для развития Л. п. имели работы Д. И. Менделеева.
В годы Советской власти Л. п. развивалось ускоренными темпами: в 1922 впервые налажено производство отливок из алюминиевых сплавов, в 1929 – из магниевых; с 1926 производилась реконструкция существовавших литейных цехов и строительство новых. Строились и вводились в эксплуатацию литейные цехи с высокой степенью механизации, с выпуском отливок до 100 тыс. т и более в год. Одновременно с перевооружением и механизацией Л. п. в СССР проводилось внедрение новой техники, создавались основы теории рабочих процессов и методы расчётов литейного оборудования. В 20-е гг. начала формироваться советская научная школа, основателями которой являются Н. П. Аксенов, Н. Н. Рубцов, Л. И. Фанталов, Ю. А. Нехендзи и др.
Технология литейного производства. Процесс Л. п. многообразен и подразделяется: по способу заполнения форм – на обычное литьё, литьё центробежное, литьё под давлением; по способу изготовления литейных форм – на литьё в разовые формы (служащие лишь для получения одной отливки), литьё в многократно используемые керамические или глиняно-песчаные формы, называется полупостоянными (такие формы с ремонтом выдерживают до 150 заливок), и литьё в многократно используемые, так называемые постоянные металлические формы, например кокили, которые выдерживают до нескольких тыс. заливок (см. Литьё в кокиль). При производстве заготовок литьём используют разовые песчаные, оболочковые самотвердеющие формы. Разовые формы изготовляют с помощью модельного комплектаи опоки (рис. 1). Модельный комплект состоит из собственно литейной модели, предназначенной для получения в литейной форме полости будущей отливки, и стержневого ящика для получения литейных стержней, оформляющих внутренние или сложные наружные части отливок. Модели укрепляют на модельных плитах, на которых устанавливают опоки, заполняемые формовочной смесью. Заформованную нижнюю опоку снимают с модельной плиты, переворачивают на 180° и в полость формы вставляют стержень. Затем собирают (спаривают) верхнюю и нижнюю опоки, скрепляют их и заливают жидкий сплав. После затвердевания и охлаждения отливку вместе с литниковой системой извлекают (выбивают) из опоки, отделяют литниковую систему и очищают отливку – получается литая заготовка.
Наиболее распространено в промышленности производство отливок в разовых песчаных формах. Этот способ применяется для изготовления из различных сплавов заготовок любых размеров и конфигурации. Технологический процесс литья в песчаные формы (рис. 2) складывается из ряда последовательных операций: подготовка материалов, приготовление формовочных и стержневых смесей, изготовление форм и стержней, простановка стержней и сборка форм, плавка металла и заливка его в формы, охлаждение металла и выбивка готовой отливки, очистка отливки, термообработка и отделка.
Материалы, применяемые для изготовления разовых литейных форм и стержней, делятся на исходные формовочные материалы и формовочные смеси; их масса равна в среднем 5—6 т на 1 т годных отливок в год. При изготовлении формовочной смеси используют отработанную формовочную смесь, выбитую из опок, свежие песчано-глинистые или бентонитовые материалы, добавки, улучшающие свойства смеси, и воду. В стержневую смесь обычно входят кварцевый песок, связующие материалы (масло, смола и др.) и добавки. Приготовление смеси производят в определённой последовательности на смесеприготовительном оборудовании; ситах, сушилах, дробилках, мельницах, магнитных сепараторах, смесителях и т. п.
Формы и стержни изготовляют на специальном формовочном оборудовании и станках. Насыпанная в опоки смесь уплотняется встряхиванием, прессованием или совместно тем и др. способом. Крупные формы заполняют с помощью пескомётов, реже для изготовления форм используют пескодувные и пескострельные машины. Формы в опоках, заформованные в стержневых ящиках стержни подвергаются тепловой сушке или химическому твердению, например при литье в самотвердеющие формы. Тепловую сушку осуществляют в литейных сушилах, а сушку стержней производят также в нагретом стержневом ящике. Сборка форм состоит из следующих операций: установка стержней, соединение половин форм, закрепление форм скобами или грузами, устанавливаемыми на верхнюю форму и предотвращающими их раскрытие при заливке сплавом. Иногда на форму устанавливают литниковую чашу, изготовленную из стержневой или формовочной смеси.
Плавят металл в зависимости от вида сплава в печах различного типа и производительности (см. Плавильное оборудование). Наиболее часто литейный чугун выплавляют в вагранках, применяют также электрические плавильные печи (тигельные, электродуговые, индукционные, канального типа и др.). Получение некоторых сплавов из чёрных металлов, например белого чугуна, ведут последовательно в двух печах, например в вагранке и электропечи (т. н. дуплекс-процесс). Заливку форм сплавом осуществляют из заливочных ковшей, в которые периодически поступает сплав из плавильного агрегата. Затвердевшие отливки обычно выбивают на вибрационных решёткахили коромыслах. При этом смесь просыпается через решётку и поступает в смесеприготовительное отделение на переработку, а отливки – в очистное отделение. При очистке отливок с них удаляют пригоревшую смесь, отбивают (отрезают) элементы литниковой системы и зачищают заливы сплава и остатки литников. Эти операции проводят в галтовочных барабанах, дробеструйных и дробемётных установках. Крупные отливки очищают гидравлическим способом в специальных камерах. Обрубку и зачистку отливки осуществляют пневматическими зубилами и абразивным инструментом. Отливки из цветных металлов обрабатывают на металлорежущих станках.
Для получения необходимых механических свойств большинство отливок из стали, ковкого чугуна, цветных сплавов подвергают термической обработке. После контроля качества литья и исправления дефектов отливки окрашивают и передают на склад готовой продукции.
Механизация и автоматизация литейного производства. Большинство технологических операций в Л. п. очень трудоёмко, протекает при высокой температуре с выделением газов и кварцесодержащей пыли. Для уменьшения трудоёмкости и создания нормальных санитарно-гигиенических условий труда в литейных цехах применяют различные средства механизации и автоматизации технологических процессов и транспортных операций. Внедрение механизации в Л. п. относится к середине 20 в. Тогда для приготовления формовочных материалов начали использовать бегуны, сита, рыхлители, а для очистки отливок – пескоструйные аппараты. Были созданы простейшие формовочные машины с ручной набивкой форм, позднее стали применять гидравлические прессы. В 20-х гг. появились и быстро распространились пневматические встряхивающие формовочные машины. На каждой технологической операции стремились заменить ручной труд машинным: совершенствовались оборудование для изготовления форм и стержней, устройства для выбивки и очистки отливок, механизировалась транспортировка материалов и готовых отливок, были внедрены конвейеры, разработаны методы поточного производства. Дальнейший рост механизации Л. п. выражается в создании новых усовершенствованных машин, литейных автоматов и автоматических литейных линий, в организации комплексно-автоматизированных участков и цехов. Наиболее трудоёмкие операции при производстве отливок – формовка, изготовление стержней и очистка готовых отливок. На этих участках литейных цехов в наибольшей степени механизированы и частично автоматизированы технологические операции. Особенно эффективно внедрение в Л. п. комплексной механизации и автоматизации. Перспективными являются автоматические линии формовки, сборки и заливки форм сплавом с охлаждением отливок и их выбивкой. Например, на линии системы Бюрер – Фишер (Швейцария) (рис. 3) изготовление форм, заливка их сплавом и выбивка отливок из форм автоматизированы. Успешно работает установка для автоматической заливки форм сплавом на непрерывно движущемся конвейере (рис. 4). Масса жидкого сплава для заполнения форм контролируется электронным аппаратом, учитывающим металлоёмкость определённой формы. Установка снабжена автоматической смесеприготовительной системой, контроль качества формовочной смеси и регулирование смесеприготовления осуществляются автоматическим устройством (системы «Молдабилити-контроллер», Швейцария).
Для финишных операций (очистки и зачистки отливок) применяют проходные барабаны непрерывного действия с дробемётными аппаратами. Крупные отливки очищают в камерах непрерывного действия, вдоль которых отливки передвигаются на замкнутом транспортёре. Созданы автоматические очистные камеры для отливок, имеющих сложные полости. Например, фирмой «Омко-Нангборн» (США – Япония) разработана камера типа «Робот». Каждая такая камера представляет собой независимый механизм для транспортировки отливок, который работает автоматически, выполняя команды, поступающие от так называемых модулей управления, расставленных на монорельсовой транспортной системе. В зоне очистки по заранее заданной программе с оптимальной скоростью вращается подвеска, на которую автоматически навешивается отливка. Двери камеры открываются и закрываются автоматически.
При массовом производстве предварительная (черновая) зачистка отливок (обдирка) осуществляется в литейных цехах. Во время этой операции также подготавливаются базы для механической обработки отливок на автоматических линиях в механических цехах. Заключительные операции могут производиться и на автоматических линиях. На рис. 5 показана автоматическая линия японской фирмы «Норитакэ» для зачистки блоков цилиндров автомобиля. Такая линия позволяет обработать 120 блоков за 1 ч.
Возможности механизации и автоматизации Л. п. особенно возросли после разработки принципиально новых технологических процессов литья, например изготовление оболочковых форм, или Кронинг-процесс (40-е гг., ФРГ), изготовление стержней отверждением в холодных стержневых ящиках (50-е гг., Великобритания), изготовление стержней с отверждением их в горячих стержневых ящиках (60-е гг., Франция). Еще в 40-е гг. в промышленности начали применять метод изготовления отливок высокой точности по выплавляемым моделям. За относительно короткий срок все технологические операции процесса были механизированы. В СССР создано комплексно-автоматизированное производство литья по выплавляемым моделям с выпуском 2500 т мелких отливок в год (рис. 6).
Лит.: Нехендзи Ю. А., Стальное литье, М., 1948; Гиршович Н. Г., Чугунное литье, Л. – М., 1949; Фанталов Л. И., Основы проектирования литейных цехов, М., 1953; Рубцов Н. Н., Специальные виды литья, М., 1955; его же, История литейного производства в СССР, 2 изд., ч. 1, М., 1962; Аксенов П. Н., Технология литейного производства, М., 1957; его же, Оборудование литейных цехов, М., 1968.
Д. П. Иванов, В. Н. Иванов.

Рис. 6. Комплексно-автоматизированный цех литья по выплавляемым моделям с годовым выпуском 2500 т отливок в год.

Рис. 3. Автоматическая линия системы Бюрер – Фишер (Швейцария) для изготовления форм, заливки их сплавом и выбивки готовых отливок.

Рис. 1. Основные элементы литейной оснастки при получении отливки в разовой форме: а и б – модельный комплект верхней и нижней полуформы с опокой; в и г – верхняя и нижняя заформованные опоки; д – формовка стержневого ящика; е – литейная форма, подготовленная к заливке; 1 – направляющий штырь; 2 – подмодельная плита; 3 – стол формовочной машины; 4 – стержневой знак; 5 – модель; 6 – головка пескострельной машины; 7 – стержневой ящик; 8 – стержень.

Рис. 2. Основы операции технологического процесса получения отливки в песчаной форме.

Рис. 4. Установка для автоматической заливки форм на конвейере завода Г. Фишер (Швейцария).

Рис. 5. Автоматическая линия зачистки блока цилиндров со шлифовальными агрегатами (фирма «Норитакэ», Япония).