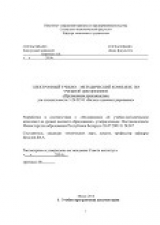
Текст книги "Электронный учебно-методический комплекс по учебной дисциплине "Организация производства" для специальности 1-26 02 01 "Бизнес-администрирование""
Автор книги: Юрий Веселов
сообщить о нарушении
Текущая страница: 6 (всего у книги 10 страниц)
Модульная единица 2.5. Организация инструментального хозяйства
Учебный элемент 2.5.1. Состав, задачи и структура хозяйства
Запас инструмента в денежном выражении может составлять до 40 % от общей суммы оборотных средств. Поэтому работа цехов, участков и рабочих мест зависит от своевременного обеспечения их различным инструментом. От качества и стойкости применяемого инструмента зависят использование материальных ресурсов, производительность труда, себестоимость продукции и другие показатели.
Инструментальное хозяйство – это совокупность общезаводских и цеховых подразделений предприятия (отделов, групп, цехов, участков), занятых определением потребности, приобретением, проектированием, изготовлением, ремонтом и восстановлением инструмента и оснастки, их учетом, хранением, выдачей в цехи и на рабочие места, а также техническим надзором за условиями использования. Инструментальное хозяйство предприятия состоит из следующих подразделений:
1) инструментальный отдел – занимается определением потребности в инструменте, устанавливает нормы его износа, расхода и запаса, составляет график производства инструмента, организует его ремонт, осуществляет технический надзор за его эксплуатацией и руководит всеми инструментальными службами;
2) инструментальный цех – осуществляет изготовление (при необходимости ремонт и восстановление) инструмента;
3) центральный инструментальный склад (ЦИС) – осуществляет прием, хранение, подготовку и выдачу инструмента в инструментально-раздаточные кладовые;
4) цеховые инструментально-раздаточные кладовые (ИРК) – получают инструмент из ЦИСа, осуществляют его хранение, выдачу на рабочие места, в заточку и ремонт;
5) база восстановления инструмента – занимается сортировкой и восстановлением инструмента;
6) ремонтные отделения (базы, участки) в цехах;
7) заточные отделения в цехах.
Основными задачами инструментального хозяйства являются:
– своевременное снабжение участков и рабочих мест необходимым инструментом;
– своевременный ремонт, восстановление и заточка инструмента;
– повышение качества инструмента и его рациональная эксплуатация;
– снижение затрат на приобретение, изготовление, хранение и эксплуатацию инструмента.
На предприятиях используются следующие формы организации инструментального хозяйства:
♦ централизованная;
♦ децентрализованная;
♦ смешанная.
Структура и функции органов управления инструментальным хозяйством определяются типом, характером и масштабом производства. Структура органов управления инструментальным хозяйством на средних и малых предприятиях имеет существенные различия:
во-первых, сокращается количество подразделений с соответствующим расширением функций каждого подразделения;
во-вторых, происходит передача некоторых функций другим подразделениям предприятия – отделу главного технолога, отделу снабжения, аппарату инструментального цеха и т. п.
Учебный элемент 2.5.2.Планирование потребности и обеспечения предприятия инструментом
Для решения этой задачи необходимо, во-первых, установить номенклатуру потребного инструмента, во-вторых, определить расход инструмента по каждому типоразмеру, в – третьих, определить запас и оборотный фонд инструментов и оснастки на все предприятие в целом. Номенклатура специального инструмента устанавливается по картам технологических процессов, универсального инструмента в серийном и массовом производстве – по картам применяемости инструмента, а в единичном и мелкосерийном – по картам типового оснащения инструментом рабочих мест. В этих картах указывается процент применения каждого вида инструмента, т. е. удельный вес машинного времени обработки данным видом инструмента в общем машинном времени работы станка. Для бесперебойного обеспечения инструментом и оснасткой рабочих мест необходимо поддерживать их запасы на определенном уровне, не ниже минимально допустимого. Чаще всего это достигается с помощью двух методов: «max – min» или «на заказ». Сущность метода «max – min» заключается в том, что запас инструмента в ЦИС не должен превышать установленный максимум величины и не быть ниже минимальной величины, равной резервному (страховому) значению. Для этого необходимо, чтобы при достижении определенной величины запаса инструмента выдавался заказ на пополнение инструментом или получение его со стороны. Величина запаса инструмента, при достижении которого выдается заказ на очередную партию инструмента, называется точкой заказа.
Организация планирования по цехам заключается в том, что для каждого цеха по каждому типоразмеру инструмента установлен лимит расхода на определенный период. Выдача инструмента ведется в пределах установленного лимита по лимитным картам.
Модульная единица 2.6. Организация ремонтного хозяйства
Учебный элемент 2.6.1. Задачи, состав, структура управления и формы организации ремонтного хозяйства
В процессе эксплуатации машины и оборудование подвергаются физическому и моральному износу: теряется работоспособность, точность. Их прежние качества восстанавливаются путем ремонта, под которым понимается возобновление в первоначальной, натуральной форме отдельных частей и деталей машин, износившихся в процессе работы предприятия.
Ремонтное хозяйство – это совокупность общезаводских и цеховых подразделений, осуществляющих комплекс мероприятий по ремонту, уходу и надзору за состоянием оборудования, в результате чего решаются следующие задачи:
обеспечивается постоянная рабочая готовность всего оборудования;
удлиняется межремонтный срок оборудования;
повышается производительность труда ремонтных рабочих и снижаются затраты на ремонт.
Практика показывает, что затраты на ремонт и обслуживание оборудования постоянно увеличиваются, растут мощности ремонтных служб и численность ремонтных рабочих. Эти обстоятельства выдвигают задачи организации ремонта оборудования в ряд наиболее актуальных проблем. Ремонтное хозяйство возглавляется главным механиком предприятия, в функции которого входят:
♦ паспортизация и аттестация оборудования;
♦ разработка технологических процессов ремонта и их оснащения;
♦планирование и выполнение работ по техническому обслуживанию и ремонту оборудования;
♦модернизация оборудования;
♦ совершенствование организации труда работников, занятых в этой службе.
Ремонтное хозяйство состоит из:
–отдела главного механика (ОГМ);
–ремонтно-механического цеха (РМЦ);
–цеховых ремонтных бюро (ЦРБ);
–службы цехового механика;
–смазочного и эмульсионного хозяйства;
–складов оборудования и запасных частей.
В ОГМ обычно создаются следующие структурные подразделения:
– конструкторско-технологическое бюро (группа), выполняющее конструкторские и технологические работы, связанные с модернизацией, ремонтом и уходом за оборудованием (проектные работы, организация чертежного хозяйства, разработка технологических процессов, проектирование оснастки и т. п.);
– планово-производственное бюро (группа), занимающееся планированием работы цехов ОГМ, материальной подготовкой ремонта, диспетчерским руководством и анализом работы цехов;
– бюро (группа) планово-предупредительного ремонта (ППР), если эта система принята на предприятии. В этом случае в его функции входят общее руководство и контроль за соблюдением системы ППР, разработка планов-графиков ремонта, ведение нормативного хозяйства и т. д.
Различают три формы организации ремонта: централизованную, децентрализованную и смешанную. При централизованной форме все виды ремонта и технического обслуживания производит ремонтно-механический цех предприятия. При децентрализованной форме ремонт и техническое обслуживание оборудования производится силами цеховых ремонтных баз. Здесь же изготавливают новые и восстанавливают изношенные детали и узлы. При смешанной форме организации ремонта трудоемкие работы, такие, как капитальный ремонт и модернизация оборудования, изготовление запасных частей и восстановление изношенных деталей и узлов, производятся в ремонтно-механическом цехе предприятия, а техническое обслуживание и текущий ремонт оборудования осуществляется в цеховых ремонтных базах.
Такой ремонт и обслуживание обычно выполняется комплексными бригадами слесарей, закрепленных за отдельными участками.
Учебный элемент 2.6.2. Методы организации ремонта
В практике работы предприятий чаще всего применяются три метода организации ремонта.
Ремонт по потребности, т. е. по мере отказа оборудования. Это может вызвать срыв выполнения планового задания, брак продукции и т. д. Увеличиваются время и затраты на ремонт оборудования в связи с износом сопряженных деталей. При этом методе работу ремонтно-механического цеха невозможно планировать. Метод по дефектным ведомостям - выполняется осмотр оборудования и составляется дефектная ведомость, в которой отражается, что и когда надо ремонтировать. Заранее служба главного механика здесь также не может планировать ремонтные работы. Третий метод организации ремонтного хозяйства базируется на системе технического обслуживания и ремонта (СТОиР). Она представляют собой совокупность организационно-технических мероприятий по уходу, надзору, обслуживанию и ремонту оборудования, по заранее составленному плану. В основе этой системы лежат принципы плановости и профилактики. Цель этого метода – предупредить остановку оборудования из-за возможных отказов и аварий. Эти система включает в себя:
уход за оборудованием основными рабочими в начале и в конце смены, что повышает их ответственность за состояние оборудования. Кроме того, за состоянием оборудования повседневно наблюдают дежурные слесари, электрики, смазчики, устраняющие возникшие мелкие неисправности;
техническое обслуживание, включающее комплекс операций по поддержанию работоспособности оборудования: осмотры выполняются дежурными слесарями 1-2 раза в месяц, промывки, проверки на точность, последние производятся наладчиком или слесарем совместно с представителем отдела технического контроля;
Время простоя оборудования в ремонте сокращается при использовании прогрессивных методов ремонта, в первую очередь узлового и последовательно-узлового. Сущность узлового метода состоит в том, что узлы и механизмы, требующие ремонта, снимают и заменяют новыми или заранее отремонтированными. При последовательно-узловом методе узлы, требующие ремонта, заменяются запасными (оборотными) не одновременно, а последовательно во время перерывов в работе станка (например, в нерабочие смены). Этот метод применим для ремонта оборудования, имеющего конструктивно обособленные узлы, которые могут быть отремонтированы и испытаны раздельно. Система ППР как основной вариант СТОиР оборудования представляет собой совокупность запланированных организационных и технических мероприятий по уходу, надзору за оборудованием, его обслуживанию и ремонту с целью предотвращения нарастания износа и потери производительности, предупреждения аварий и, следовательно, поддержания оборудования в работоспособном состоянии в течение периода его эксплуатации. Система ППР позволяет выполнить все ремонтные работы строго по графику, согласованным с планом производства, своевременно подготовить все необходимые для ремонта запасные части и материалы, что сокращает время выполнения работ и снижает стоимость ремонта. ППР применяется для оборудования:
многочисленного, однотипного и имеющего существенный износ;
современные методы диагностики которого не позволяют оценить его техническое состояние.
В противном случае целесообразно применять другой вариант СТОиР в виде ТОР, который основан на предварительной диагностике и ремонтам по необходимости.
Учебный элемент 2.6.3 Нормативы системы ППР
При системах ППР и ТОР объемы и содержание работ планируются и строго соблюдаются независимо от фактического состояния оборудования. Эти системы базируются на точно установленных нормативах. Нормативы системы ППР:
– длительность ремонтного цикла и его структура;
– продолжительность межремонтного и межосмотрового периодов;
– категория сложности ремонта;
– ремонтная единица;
– нормы затрат рабочего времени, материалов и простоев оборудования в ремонте.
Все нормативы дифференцированы по группам оборудования.
Ремонтный цикл (Тр.ц.) – это промежуток времени от ввода оборудования в эксплуатацию до капитального ремонта или между двумя капитальными ремонтами. Он измеряется оперативным временем работы оборудования. Время простоя в ремонте в цикл не включается. Период времени между двумя смежными капитальными ремонтами называется межремонтным циклом. Его величина определяется сроком службы основных частей оборудования. Средние и текущие ремонты, а также межремонтное обслуживание проводятся между двумя смежными капитальными ремонтами. Чередование этих ремонтов в определённой последовательности, через регламентированные отрезки времени, называется структурой межремонтного цикла. Пример структуры межремонтного цикла:
С К С К
Т Т Т Т Т Т Т Т Т
К – капитальный ремонт; С – средний; Т– текущий.
Межремонтное обслуживание проводится без остановки оборудования. В него входят работы по регулярному наружному осмотру, выявлению дефектов и исправлению мелких дефектов и неисправностей оборудования. Текущий ремонт включает проверку крепёжных и регулируемых деталей, смазочных, нагревательных и охлаждающих систем, пусковых приспособлений и передаточных устройств, состояние изоляции, контактов и т.д. Текущий ремонт проводится на остановленном оборудовании.Средний ремонт, который проводится на остановленном оборудовании, охватывает те же работы, что и текущий, но при этом дополнительно ремонтируются отдельные сборочные единицы с заменой части деталей.
Капитальный ремонт является восстановительным и состоит в полной разборке оборудования, замене и ремонте деталей и узлов для обеспечения первоначальных размеров и восстановления работоспособности оборудования для обеспечения требуемой производительности. Межремонтный период Тм – это время (в месяцах) между двумя очередными ремонтами, определяемое по формуле:
T м = T p . ц . /( n c + n м + l );
где пс, пм – число средних и малых ремонтов на один ремонтный цикл соответственно.
Межосмотровый период То – это время (в месяцах) между очередными ремонтом и осмотром, рассчитанное по формуле:
То = Тр.ц. / (п с + п м + п о +1);
Где: по – число осмотров за один ремонтный цикл.
Для оценки сложности ремонта оборудования, его ремонтных особенностей введена категория сложности ремонта R, которая определяется по техническим характеристикам оборудования на основе расчетных формул. В каждой группе оборудования один из агрегатов принят за эталон, которому по СТОиР установлена категория сложности ремонта (в металлообработке за эталон принята R токарно-винторезного станка 16 К 20 по системе ППР равная 11 категории сложности). Категорию сложности любого станка R устанавливают путем сопоставления со станком-эталоном. Категория сложности ремонта (R) записывается в его техническом паспорте.
Для планирования объема ремонтных работ вводится понятие « ремонтная единица» – r (р.е.), т.е. показатель, характеризующий нормативные затраты на ремонт оборудования первой категории сложности. Таким образом, категория сложности ремонта R показывает, во сколько раз трудоемкость ремонта данной модели оборудования превышает трудоемкость ремонтной единицы r. Например, символ 10R означает, что станок относится к 10-ой категории сложности ремонта и у него 10 р.е. Нормы затрат труда по видам ремонта и профилактических операций устанавливаются на одну ремонтную единицу в зависимости от вида работ. Нормы расхода материалов при ремонте оборудования определяются расчетным методом. Расход материалов на ремонт металлорежущего оборудования согласно системе ППР устанавливается в процентах к основной заработной плате ремонтных рабочих. Ремонтная сложность устанавливается раздельно по механической и электрической части оборудования (станка). За единицу ремонтной сложности механической части принята ремонтная сложность условного оборудования, трудоемкость капитального ремонта которого в условиях среднего РМЦ составляет 50 часов. За единицу ремонтной сложности электрической части принята ремонтная сложность условного оборудования, трудоемкость капитального ремонта которого в условиях среднего РМЦ составляет 12,5 часов. Нормативы простоя устанавливаются для определенных условий и дифференцируются для вывода оборудования в ремонт по участкам для различных видов ремонтов и ремонтных операций, различной сменности бригад. Единой системой ППР предусматриваются нормы продолжительности простоя оборудования в ремонте в сутках на 1 р.е. сложности.
Учебный элемент 2.6.4. Планирование ремонтных работ на предприятии
Повышение рентабельности предприятий требует эффективного использования технологического оборудования. Это означает повышение производительности за счёт уменьшения простоев по техническим причинам при одновременном снижении затрат на СТОиР. Процесс ремонта представляет совокупность организационно-технологических способов частичного (полного при капремонте) восстановления ресурса (свойств) изделия, что позволяет трактовать его как объект организации и планирования. Необходимым условием для выполнения СТОиР является наличие:
– изделий – объектов СТОиР;
– средств СТОиР;
– исполнителей СТОиР (организации, специалисты);
– документации (конструкторской, в том числе эксплуатационной и ремонтной, нормативной, организационной, технологической и др.), устанавливающей требования к составляющим СТОиР и связи между ними. Внешними факторами по отношению к СТОиР являются процессы изнашивания, определяемые режимами эксплуатации, нагрузкой, квалификацией обслуживающего персонала, возрастом оборудования и внешней средой. Требования к СТОиР техники и условиям их выполнения подробно рассмотрены в межгосударственном стандарте ГОСТ 15.601-98 (в РБ введен в действие 01.07.99). Наиболее перспективным с точки зрения полноты использования ресурса элементов оборудования является планирование ремонтов с учетом технического состояния элементов системы. Плановые ремонты оборудования, когда прогнозирующим параметром является время эксплуатации элемента системы, т.е. ППР по функции распределения, могут быть рекомендованы при незначительном разбросе ресурса деталей, техническое состояние которых можно достаточно точно определить по времени эксплуатации оборудования. Кроме того, этот вид ремонта может быть использован для оборудования и его элементов, современные методы диагностики которого не позволяют оценить его ТС. Ремонтные нормативы и нормы расхода запасных частей в этом случае разрабатываются исходя из оптимальных значений ресурса элементов машин. Наиболее распространенные системы планирования ремонтов базируются на структуре ремонтного цикла и оптимизации выбора дат ремонтов при условно постоянной структуре ремонта с целью обеспечения производительности системы на уровне не ниже заданного. Задача заключается в рациональном распределении объемов ремонтных работ и назначение их периодичности таким образом, чтобы обеспечить требования надежности с минимальными затратами времени и средств на ремонт. При агрегатно-узловом способе ремонт разделяется на две фазы: демонтаж определяемого в ремонт элемента системы и монтаж устанавливаемого взамен элемента из оборотного фонда. Время простоя системы из-за ремонта конкретной единицы сокращается до суммы времени демонтажа и монтажа, а собственно ремонт (восстановление) данной единицы не приводит к вынужденному её простою. В плане ремонтных работ определяются следующие основные показатели:
– виды и сроки ремонта по каждому станку (агрегату);
– объем ремонтных работ по цехам и предприятию на месяц и год;
– численность ремонтных рабочих и рабочих, занятых обслуживанием оборудования;
– ФОТ данных рабочих;
– количество и стоимость материалов;
– простои оборудования в ремонте;
– себестоимость ремонтных работ.
Виды и сроки ремонта по каждому станку определяются при разработке планов-графиков проведения ремонтных работ. Затраты на текущий и средний ремонт, межремонтное обслуживание оборудования финансируются за счет текущей себестоимости продукции, а затраты на капремонт и модернизацию осуществляются за счет части амортизации, предназначенной на реновацию основных фондов, а также части чистой прибыли предприятия (фонд накопления).
Модульная единица 2.7. Организация энергетического хозяйства предприятия
Учебный элемент 2.7.1. Значение, структура, задачи, функции энергохозяйства
Любой технологический процесс требует определенного расхода топлива, электрической и тепловой энергии, поэтому промышленные предприятия являются крупнейшими потребителями различных видов топлива и энергии.
Энергетическое хозяйство промышленного предприятия – это совокупность энергетических установок и вспомогательных устройств с целью обеспечения бесперебойного снабжения предприятия различными видами энергии и энергоносителей, таких, как натуральное топливо (газ, мазут и др.), электрический ток, сжатый воздух, горячая вода, конденсат. К основным видам промышленной энергии относятся: тепловая и химическая энергия топлива, тепловая энергия пара и горячей воды, механическая энергия и электроэнергия. Основными задачами энергетического хозяйства являются надежное и бесперебойное обеспечение предприятия всеми видами энергии установленных параметров при минимальных затратах. Энергообеспечение предприятия имеет специфические черты, обусловленные особенностями производства и потребления энергии:
♦ производство энергии, как правило, должно осуществляться в момент потребления;
♦энергия должна доставляться на рабочие места бесперебойно и в необходимом количестве. Перебои в снабжении энергией вызывают прекращение процесса производства, нарушение технологии;
♦энергия потребляется неравномерно в течение суток и года. Это вызвано природными условиями (летние и зимние периоды, день, ночь) и организацией производства;
♦мощность установок по производству энергии должна обеспечивать максимум потребления.
По характеру использования энергия бывает: технологической, двигательной (силовой), отопительной, осветительной и санитарно-вентиляционной. Для промышленных предприятий наибольшее значение имеет потребление энергии на двигательные и технологические цели. В качестве двигательной силы технологического и подъемно-транспортного оборудования используются главным образом электроэнергия и в небольшом количестве пар и сжатый воздух. Различные виды энергии и энергоносителей применяются на всех стадиях технологии производства изделия. При этом единство и взаимообусловленность технологии и энергетики – наиболее характерная черта большинства производственных процессов промышленного предприятия. В число потребителей электроэнергии необходимо отнести и такие участки производства, как слаботочные средства связи: телефоны, радио, диспетчерская связь. На всех предприятиях – энергопотребителях должен быть составлен энергетический паспорт, который является нормативно-хозяйственным документом, утвержденным по единой государственной форме. В таком паспорте отражаются все основные сведения об энергохозяйстве и производится оценка эффективности использования топливно-энергетических ресурсов по объектам предприятия.
Традиционно руководство предприятий больше внимания уделяет насущным потребностям производства, а не эффективности использования энергии, которую рассматривает больше как проблему техническую, а не управленческую. В то же время управление энергоресурсами есть научный процесс и жизненная необходимость для каждого предприятия. Особенно актуально оно для стран СНГ и Восточной Европы, где энергии на выпуск продукции тратится в 3-5 раз больше, чем в индустриально развитых странах. Возможность работы отечественных предприятий с повышенной энергоемкостью продукции за счет роста цен на выпускаемую продукцию практически исчерпала себя, так как влечет за собой дальнейшее падение их конкурентоспособности. Поэтому Беларусь перешла на политику энергосбережения во всех отраслях экономики и ЖКХ.
Учебный элемент 2.7.2. Энергетические балансы, их классификация и порядок разработки.
Основой рациональной организации энергетического хозяйства на предприятии является планирование производства и потребления энергоносителей на основе энергетических балансов. Энергобаланс является отражением закона сохранения энергии в условиях конкретного предприятия. Он состоит из двух частей: приходной, характеризующей ресурсы энергии всех видов, и расходной, где показано распределение энергоресурсов по направлениям потребления. Приходная и расходная части баланса должны быть равны. Различают сводный и частные балансы отдельных энергоресурсов, плановые и отчетные. Энергетические балансы входят в группу материальных балансов предприятия. Главная цель энергобаланса – определение степени полезного использования энергии и поиск путей снижения потерь и энергосбережения. В результате расчета общей потребности устанавливается лимит по видам топлива и энергии в натуральном и стоимостном выражении для предприятия в целом. Общий расход энергии по предприятию делится на две части – переменную и расходную. Переменную часть, т.е. зависящую от объема выпускаемой продукции, составляет расход всех видов энергии на двигательные и технологические цели.
Постоянная часть, т.е. не зависящая от объема выпускаемой продукции, – это расход на освещение, отопление, вентиляцию и др. Определение потребности предприятия в энергоносителях осуществляется с помощью прогрессивных норм расхода, которые устанавливаются, как в целом по предприятию (укрупненные нормы), так и по отдельным рабочим местам, участкам и цехам (дифференцированные нормы). Основным видом норм являются удельные нормы расхода на единицу продукции (индивидуальные нормы) и групповые нормы расхода на производство единицы объема одноименной продукции. Конкретный состав нормы расхода энергоресурса устанавливается соответствующими отраслевыми методиками и инструкциями.
Учебный элемент 2.7.3. Политика энергосбережения на предприятии
Реализуется по следующим направлениям:
внедрение энергосберегающих технологий;
совершенствование структуры энергопотребления;
применение нетрадиционных возобновляющихся видов энергии (солнца, ветра);
применение рациональных режимов работы энергопотребителей;
сокращение норм расхода энергии на производство продукции;
усиление контроля и учета расходования энергоресурсов;
исключение непроизводительного расхода и потерь энергоресурсов;
использование системы материального стимулирования и ответственности за энергосбережение;
использование вторичных энергоресурсов;
стандартизация энергосбережения и совершенствование тарифной политики в энергетике.
Государственная политика в области энергосбережения предусматривает комплекс мер по управлению энергоресурсами с целью обеспечения конкурентоспособности предприятий на глобальных рынках.
Модульная единица 2.8. Организация транспортного хозяйства
Учебный элемент 2.8.1. Состав, значение и задачи транспортного хозяйства
Транспортное хозяйство – комплекс технических средств предприятия, предназначенных для перевозки материалов, продукции на территории предприятия и на его подъездных путях.
Транспортное хозяйство предприятия состоит из транспортных средств и устройств общего назначения – депо, гаражи, мастерские, дороги, пути и т.п. На предприятии может использоваться межцеховой, внутрицеховой и межоперационный транспорт.
К межцеховому транспорту относят: электровозы, мотовозы, автомобили, тракторы, электро– и автокары и др. Внутри цеха могут применяться электро– и автокары, транспортеры различного типа (ленточные, цепные, пластинчатые), краны (мостовые, консольные, поворотные),монорельсы, тали, ручные тележки, велосипеды и др. к межоперационному транспорту относят ручные тележки, транспортеры, рольганги, монорельсы, мостовые краны и др. В основные функции транспортного хозяйства предприятия входят: перевозка грузов, погрузочно-разгрузочные работы и экспедиционные операции. Основными задачами транспортного хозяйства являются:
своевременное и бесперебойное обслуживание производства необходимым транспортом;
рациональный выбор и эффективное использование транспортных средств;
механизация и автоматизация транспортных операций;
снижение затрат, связанных с перевозкой грузов, которые в среднем составляют 20-30 % от суммы всех косвенных расходов в себестоимости продукции.
Учебный элемент 2.8.2. Организация перевозок грузов
Погрузочно-разгрузочные, транспортные и складские работы включают комплекс операций перемещения, связанных с изменением положения груза в пространстве, но не изменяющих их физические свойства. Они могут быть ручными, механизированными, комплексно-механизированными и автоматизированными. Перевозка грузов может производиться по разовым и постоянным маршрутам. Разовые маршруты случайны как по направлениям, так и по количеству транспортируемого груза. Постоянные маршруты проходят по заранее установленным направлениям и выбираются с учетом грузопотока и применяемых транспортных средств для выполнения повторяющихся заявок в серийном и массовом производстве. Существуют три системы маршрутных перевозок: маятниковая (односторонняя с грузом или без груза, двухсторонняя с грузом), веерная и кольцевая (цикловая). Формы организации внутризаводского транспорта зависят от мощности грузопотоков и объема грузооборота. Грузопоток – показатель, характеризующий объем перевозок грузов, перемещаемых в единицу времени между двумя пунктами – погрузки и выгрузки. Различают грузопотоки внешние (прибытия и отправления) и внутренние. Сумма отдельных грузопотоков на предприятии представляет собой грузооборот – основной показатель, характеризующий объем транспортной работы на предприятии. Грузооборот – это общее количество грузов, перемещаемых на территории предприятия (цеха) за расчетный период (год, месяц). Расчет грузооборота производится на основе таблиц грузооборотов цехов и общезаводских складов в виде шахматной ведомости. На предприятии разрабатываются схемы грузопотоков, на основе которых по каждой группе грузов производят выбор транспортных средств, их количество и показатели использования, часто с применением экономико-математических методов моделирования с целью оптимизации грузопотоков и грузооборота. Все эти функции выполняет транспортный отдел (служба) в рамках подсистемы АСУП «Транспорт».
Модульная единица 2.9. Организация складского хозяйства