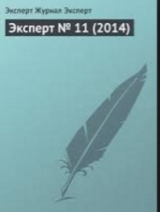
Текст книги "Эксперт № 11 (2014)"
Автор книги: Автор Неизвестен
Жанр:
Публицистика
сообщить о нарушении
Текущая страница: 7 (всего у книги 14 страниц)
Главный заказчик
24 января 2013 года на стане в Новокузнецке была прокатана первая сертификационная партия самых распространенных на железных дорогах России рельсов типа Р65, но изготовленных уже по новой технологии. За этот год комбинат восстановил почти все сертификаты соответствия на рельсовую продукцию, которую производил на прежнем оборудовании (большая его часть была демонтирована в ходе модернизации). А в ноябре прошлого года сертифицировал рельсы Р65 по категории ДТ 350 (так называемые рельсы общего назначения дифференцированно термоупрочненные с прокатного нагрева). В декабре для РЖД было отгружено 10 тыс. тонн рельсов нового типа – правда, 25-метровых («стометровки» пришлось резать на четыре части). А уже в марте «Евраз ЗСМК» должен поставить РЖД первую партию (около 15 тыс. тонн) 100-метровых рельсов. Опытные образцы прошли испытания на полигоне в подмосковной Щербинке. Отработаны и технологии перевозки такой нестандартной продукции – для этого на Ярославском электровозоремонтном заводе произведены специальные сцепы, состоящие из семи платформ.
Еще в мае 2012 года Evraz Group и РЖД подписали меморандум о сотрудничестве, в котором были сформулированы основные условия пятилетнего контракта. «У нас есть долгосрочное соглашение. Оно живое, меняется в зависимости от ситуации, от спроса, от инвестиционной программы РЖД. Я думаю, в этом году мы отгрузим в адрес РЖД не более ста тысяч тонн стометровых рельсов», – прогнозирует Алексей Юрьев. В целом же по 2017 год включительно Evraz Group должна поставить РЖД рельсовую продукцию на сумму около 90 млрд рублей. Этот объем включает в себя и поставки 100-метровых рельсов.
На комбинате рассчитывают уже в этом году нарастить объемы проката в РБЦ с 450 тыс. тонн (итоги прошлого года) до 1 млн тонн, то есть вывести цех на проектную мощность. «В процессе эксплуатации стана и всей технологической линии производства рельсов идет отладка нового оборудования, совершенствуется калибровка валков, проходит процесс обучения работы на новом современном оборудовании, корректируется технология. Заказами на рельсовую продукцию комбинат обеспечен в полном объеме», – сообщает сибирский региональный центр корпоративных отношений «Евраза». Выйти на 1 млн тонн проката в год на предприятии рассчитывают именно за счет рельсов, хотя возможности стана позволяют производить и другую продукцию, в том числе строительного сортамента. До 80% объемов производства будет направлено в адрес РЖД, включая широкую номенклатуру тех же Р65 (усовиковые и остряковые рельсы, контррельсы и т. п.). Еще 5–7% продукции – рельсы для метрополитенов (в первую очередь московского), остальное – трамвайные рельсы и экспорт.
Впрочем, поставки за рубеж – дело не из легких. По словам Алексея Юрьева, основные зарубежные рынки сбыта для новокузнецких металлургов – США, Канада и Европа. Сложность в том, что в этих странах российские сертификаты не действуют – нужно получать документы на соответствие локальным нормам, проходить проверки. «Получение разрешительных документов для поставки рельсовой продукции требует значительного времени в связи с необходимостью целого ряда исследований и испытаний из-за повышенных стратегических требований к данному виду продукции», – объясняет Юрьев. Да и вообще, модернизация стана, подчеркивает он, проводилась прежде всего в интересах внутреннего рынка.
Рождение конкурента
Причина того, что Evraz Group пришлось спешить с обновлением прокатного производства, – появление нового серьезного конкурента внутри страны. Группа «Мечел» в июле прошлого года запустила на своем заводе в Челябинске стан, аналогичный новокузнецкому (правда, закалка там происходит по иной технологии, с помощью полимеров). Цех и трехкилометровый конвейер на промплощадке Челябинского меткомбината были построены с нуля и обошлись «Мечелу» в 715 млн долларов. Теперь там тоже могут производить длинномерные рельсы и балки длиной до 100 метров (мощность всего стана – 1,1 млн тонн готовой продукции в год). В РЖД планировали в 2014 году закупить у челябинских металлургов 100–130 тыс. тонн стометровых рельсов (у «Евраза», впрочем, больше – 600 тыс. тонн). По соглашению 2008 года ежегодные закупки РЖД рельсов различных типов у «Мечела» до 2030 года планировались на уровне 400 тыс. тонн. Что не удивительно, ведь конкурента Evraz Group в лице «Мечела» РЖД, можно сказать, создали своими руками: еще в 2007 году железнодорожная монополия предложила российским металлургам создать такие производства. Откликнулся тогда и довел дело до конца один Игорь Зюзин , крупнейший акционер «Мечела».
Управляющий директор «Евраз ЗСМК» Алексей Юрьев: «Отказ от масла и переход на воздух при закаливании рельсов резко снижают попадание вредных веществ в окружающую среду»
Фото: Виталий Волобуев
Однако «Мечел» пока не сертифицировал свои рельсы по российским стандартам, и «Евраз ЗСМК», такой сертификат уже получивший, выиграл время. «С точки зрения наличия производственно-технологической цепочки – да, появился конкурент. С точки зрения компетенций, опыта и наличия значительного количества высококвалифицированных узких специалистов, в совершенстве владеющих спецификой производства рельсовой стали и проката рельсов, – преимущество у наших металлургов», – уверенно заявляет начальник рельсобалочного цеха в Новокузнецке Андрей Лапченко .
В «Евразе» прогнозируют, что новый стан в Челябинске будет в основном ориентирован на выпуск более понятного для «Мечела» строительного проката – стальных балок, которые используются при возведении зданий, а также мостов, дорог и прочей инфраструктуры. Как уже отмечал «Эксперт» (см. «Как застоялась сталь», «Эксперт Урал» № 49 за 2013 год), рынок балок не столь маржинальный, как рынок рельсов. Зато он динамично растет, и занять эту нишу проще и быстрее: только с 2009 по 2012 год потребность страны в таком виде проката выросла более чем вдвое, притом что импорт этой продукции в Россию увеличился в четыре раза. Теперь каждый пятый погонный метр используемых в России балок произведен либо в Польше, либо на Украине, и именно на замещение этой доли импорта нацелился «Мечел». Впрочем, этим же будут заниматься и в Новокузнецке – в РБЦ специально сохранили участок бывшего «короткомера», на котором можно и сейчас производить балки, швеллера, круглые или квадратные в сечении заготовки и т. п.
Индустриализация 2.0
Два этапа модернизации РБЦ обошлись Evraz Group в 18 млрд рублей. Отладка стана еще продолжается. Примечательно, что около 80% всего установленного в цехах оборудования – иностранного производства. Введенная в строй еще в 2006 году нагревательная печь с шагающими балками – итальянская, фирмы Techint, сам стан – немецкой компании SMS Meer, установка дифференцированной закалки – американская. Российского оборудования в Новокузнецке немного, а самое высокотехнологичное – иностранного производства. «Оборудование надо поставить, запустить, так провести пусконаладку, чтобы получить быстрый результат. Мы должны быстро окупить свои вложения, – объясняет Алексей Юрьев. – К сожалению, я вынужден констатировать, что где-то потеряны компетенции, где-то – люди, отсюда и крен в сторону зарубежных поставщиков».
Тем не менее проектирование нового РБЦ велось собственными силами «Евраза». Инженеры и технологи несколько лет двигались от участка к участку, находя для них оптимальные решения. Под каждое звено подбирались наиболее эффективные производители оборудования. Стоит вспомнить, что сам КМК в далекие 1930-е строился по проекту американской Freyn Engineering Co., который, правда, был сильно переделан Иваном Бардиным и его командой в сторону увеличения мощностей (с 400 тыс. тонн до 1,5 млн тонн чугуна в год). Так что аналогия просматривается: и тогда, и сейчас металлургический гигант был построен на основе передовых мировых технологий и на оборудовании, заказанном за границей, но российскими руками и мозгами.
Постиндустриальный профиль
В стене технологического тоннеля бывшего КМК, пролегающего под его 25 железнодорожными ветками, покоится тело прораба А. М. Заева. Он завещал похоронить себя на месте работы, чтобы не разлучаться с делом всей своей жизни даже после смерти. Сегодня того небывалого воодушевления и душевного подъема, свойственных легендарной стройке, которая стала символом броска технической революции через Урал, уже не встретишь. Новокузнецк, до начала индустриализации бывший маленьким уездным городком, понемногу обрастает древней историей и готовится отмечать свое 400-летие. Восстановлена Кузнецкая крепость, с ее каменной стены открывается великолепный вид на город металлургов, доминантой которого по-прежнему остаются заводы.
Несмотря на это, Новокузнецк мало похож на промышленный город в отличие, к примеру, от Нижнего Тагила, – о его индустриальной начинке напоминает разве что черный от угольной пыли снег вдоль дорог. Да вечерняя дымка – смесь промышленных выбросов («запах денег», – шутят горожане, объясняя приезжим происхождение неприятных ароматов). В ней особенно колоритно светятся неоновые вывески торгово-развлекательных центров и ресторанов, а также деревья в Саду металлургов. Возможно, именно сдвиг в сознании, произошедший после крушения советской производственной идиллии и резкого падения престижа рабочих профессий, позволил городу пережить трансформацию НКМК. А также спокойно оценивать перспективы закрытия других местных предприятий – от цементного завода до Новокузнецкого алюминиевого.
«Беда нашей экономики в том, что мы привыкли все грузить эшелонами. Если мы эшелон сегодня не отправили – значит день прожит зря. Это неправильно. Предприятия должны быть эффективными и производить ровно столько продукции, сколько действительно нужно», – уверен мэр Новокузнецка Сергей Кузнецов . Судьба КМК убеждает в его правоте: ведь бизнес в случае с рельсобалкой все сделал, по сути, самостоятельно, ориентируясь лишь на спрос и требования базового заказчика.
Однако индустриальный профиль, который в Новокузнецке сегодня воспринимают как некое тяжкое наследие, не так уж и плох. Советские гиганты не бесперспективны: их промплощадки вполне пригодны для размещения новых производств. И это благо, а не проклятие. Ведь постиндустриальное будущее все же должно быть построено на индустриальной основе.
Новокузнецк – Новосибирск
Без мартеновских печей Александр Попов
Западно-Сибирский металлургический комбинат (ЗСМК) моложе НКМК почти на три десятилетия. Логично, что большая металлургия в Новокузнецке в итоге сохранилась именно на его площадке, расположенной в 25 км от центра города с учетом розы ветров и санитарно-защитной зоны.
section class="box-today"
Сюжеты
Промышленность:
«Людей зажжет сам факт того, что они делают большое дело»
Кузнецкая металлургическая революция
/section section class="tags"
Теги
Западно-Сибирский металлургический комбинат
Промышленность
Эффективное производство
Сибирь
Спецдоклад "Освоение Сибири"
/section
Две доменные печи там проходят всего лишь третью кампанию (так называют 15-летний период, в течение которого печь работает без остановок – до капитального ремонта), а первая, запущенная еще в 1964 году, сейчас является самой современной. Да и сам комбинат исторически был современным и технологичным предприятием – здесь, к примеру, никогда не было мартеновских печей, а мощности еще в советские годы запускались на основе АСУ. В прошлом году комбинат, несмотря на сокращение спроса на сталь по всему миру, произвел 6 млн тонн чугуна и выплавил более 6,84 млн тонн стали – рекорд, в последний раз установленный лишь по итогам далекого 1990 года. В составе объединенного «Евраз ЗСМК» это предприятие сейчас называют площадкой строительного проката, имея в виду, что основной вид производимой здесь продукции – арматура, проволока, швеллеры, уголки и т. п., всего около ста наименований.
figure class="banner-right"
figcaption class="cutline" Реклама /figcaption /figure
Комбинат работает по классической и самой распространенной ныне в черной металлургии замкнутой схеме, с использованием кислородно-конвертерного метода получения стали. Собственная аглофабрика производит агломерат (в сутки Запсиб «съедает» порядка 450–500 вагонов железорудного концентрата, из которого и готовится агломерат – по сути, оксид железа), который по конвейеру поступает в доменный цех, где в трех печах (их суммарный объем 8 тыс. кубометров) переплавляется в чугун. «Жидкий чугун – это полупродукт, его можно и в чушках продавать. Мы так тоже делаем, но немного. Основная масса чугуна – либо в ковшах, либо в миксерах – идет в два конвертерных цеха, где с помощью кислорода конвертируется в сталь. Дальше ее превращают либо в слиток, который потом будет обжат в блюминге и в итоге станет заготовкой, либо направляют в машину непрерывного литья заготовок. А уже оттуда заготовки идут на прокат, и там мы получаем конечную продукцию», – на пальцах объясняет технический директор ОАО «Евраз ЗСМК» Аркадий Амелин . Кислородно-конвертерные цеха оснащены тремя конвертерами емкостью по 160 тонн каждый и двумя – по 350 тонн. В них чугун смешивают с уже расплавленным металлоломом: эти гигантские ковши сначала раскачиваются, перемешивая ингредиенты, а потом накрываются крышкой и, с шипением и грохотом, становятся сосудом для химической реакции, итог которой – сталь необходимых марок.
Чтобы получить чугун, доменным печам необходимо топливо, в основном кокс, который производится здесь же, на площадке строительного проката «Евраз ЗСМК», на шести коксовых батареях. Недостатков у кокса хватает – и воздух он загрязняет, и стоит непомерно дорого. Однако «разжечь» домны совсем без твердого топлива невозможно, зато можно максимально снизить долю кокса в тонне чугуна. Например, с помощью природного газа (он уже подключен к печам), который стоит дешевле. Но лучше всего – с помощью так называемого пылеугольного топлива (ПУТ). «Мир сейчас процентов на сорок перешел на ПУТ, новые доменные печи без таких установок даже не строятся, – рассказывает Аркадий Амелин. – Германия, к примеру, сократив производство кокса чуть ли не вполовину, увеличила производство стали – все за счет ПУТ. По большому счету, это тот же самый кокс, но дробленый, измельченный. Нидерланды сегодня вдувают 220 килограммов ПУТ на тонну чугуна, американцы, по-моему, 90 килограммов на тонну». «Преимущества этой технологии очевидны, – добавляет управляющий комбинатом Алексей Юрьев . – Прежде всего можно будет использовать энергетические марки углей, которые стоят дешевле коксующихся. Расход кокса в итоге сокращается на 20 процентов, кроме того, можно будет полностью исключить из структуры топливной составляющей природный газ. В итоге эта технология позволяет снизить себестоимость на 5–10 процентов в целом по доменной плавке, это будет наша победа в структуре себестоимости». Сегодня на тонну чугуна на Запсибе уходит около 443 кг кокса, при запуске установки ПУТ его количество сократится до 390 кг на тонну. «Замена не прямая, но все равно это очень выгодно – кокса ведь будет сгорать меньше. И экологический эффект – опять-таки, потому что кокса меньше. Просто за счет сокращения выбросов», – рассказывает главный специалист по технологии доменного цеха Валерий Щипицын .
Строительство установки ПУТ началось в 2011 году, сегодня этот крупнейший на площадке ЗСМК инвестпроект, стоимость которого превысила 7 млрд рублей, завершается – недалеко от цехов доменного производства выросли современные разноцветные корпуса этой установки. Аналогичную технологию Evraz Group уже внедрила на своем комбинате в Нижнем Тагиле, теперь те же специалисты работают в Новокузнецке. Вдувать ПУТ в доменные печи начнут в третьем квартале этого года.
Подобные затраты оправданны, ведь главное для «Евраз ЗСМК» – снижение себестоимости продукции. Деваться комбинату некуда: предприятие расположено в Кузбассе, равноудалено от портов и сильно зависит от железной дороги. «Комбинат был спроектирован полностью под железнодорожный транспорт, но мы сегодня развиваем и автодоставку продукции. Это дешевле, чем в вагонах: каждый месяц мы зарабатываем за счет автодоставки около 30 миллионов рублей», – рассказывает Юрьев. Сегодня с комбината ежемесячно уходит до тысячи тридцатитонных фур, задача – довести их количество до 1,2 тыс. Серьезные инвестиции идут и в энергосбережение. За счет замены изношенных светильников на новые уровень освещенности в подразделениях «Евраз ЗСМК» в среднем вырос до 65%, а сэкономить удалось более 25 млн рублей (в целом эта программа рассчитана на пять лет). Запуск турбины на паровоздуходувной станции позволил сэкономить около 10 млн рублей на закупках электроэнергии. В перспективе еще одну турбину планируется построить на базе коксохима, где также образуются излишки пара. «Цены на собственную электроэнергию получаются в два – два с половиной раза ниже, чем на покупную», – признает Алексей Юрьев.
«Наше географическое положение, которое является преимуществом “Евраз ЗСМК” внутри страны, является недостатком, если сравнивать с производителями Китая, Японии, Кореи и даже Индии и США. Страны Азии постоянно наращивают производство стали, поддерживая достаточно большое предложение на рынке, что в свою очередь оказывает значительное влияние на цены. В этих условиях основные наши конкурентные преимущества – работа с клиентами и снижение издержек производства. Будем осваивать новые виды сталей и новые типоразмеры сортового проката по требованиям потребителя, повышать качество продукции комбината», – говорит о главных целях Юрьев.
Основные драйверы роста в компании видят внутри страны, прежде всего в Сибири и на Дальнем Востоке, где государство планирует реализовать новые крупные инфраструктурные проекты. «Очень вероятно, что внешняя конъюнктура в 2014 году не улучшится, а если и улучшится, то ненамного, – продолжает Алексей Юрьев. – Главная беда мирового рынка металлов – перепроизводство. Металлурги Китая продолжают наращивать производство очень высокими темпами, и мало верится, что в 2014 году их активность снизится. Некоторые надежды на улучшение внутреннего спроса дает начало нового витка реализации масштабных госпроектов – БАМ, чемпионат мира по футболу, ЦКАД, несколько магистральных нефте– и газопроводов. Все эти проекты потребуют значительного количества листового и сортового проката, что позволит сталепрокатным комбинатам увеличить продажи на внутреннем рынке».
Одновременно «Евраз ЗСМК» вкладывает значительные средства в охрану окружающей среды. Только в прошлом году на природоохранные мероприятия было направлено более 171 млн рублей, всего же на экологические программы до 2018 года планируется потратить до 2 млрд рублей. «Главная наша задача – уложиться в предельно допустимые выбросы и сбросы, если говорить о воде и воздухе», – говорит Алексей Юрьев. Но он скромничает. «Модель, к которой мы идем: в городе воздух должен быть чистый, речка должна быть чистая, берега должны быть зеленые, асфальт должен быть ровный, люди должны ходить с улыбками до белых зубов. Новокузнецк должен остаться индустриальным городом, но качество индустрии должно стать другим», – считает мэр Новокузнецка Сергей Кузнецов . Идеология горожан действительно поменялась, а потому советским индустриальным гигантам приходится так или иначе это учитывать. К примеру, областные власти не первый год требуют закрыть цементный завод, дымящий прямо в центре города. Идет ликвидация и первой промплощадки на НкАЗе, самой старой и давно не отвечающей экологическим стандартам. Кстати, ПУТ – показательный пример, когда инвестиции в себестоимость идут параллельно с решением экологических задач. Черная металлургия – очевидно «грязное» производство, но стремиться к золотой середине между ожиданиями горожан и возможностями промышленности стоит.
Сибирское машиностроение живо Александр Попов
«С каждым годом будет все сильнее проявляться запрос на производственный потенциал машиностроителей», – считает Юнус Ислямов, собственник и управляющий новосибирского завода «Труд»
section class="box-today"
Сюжеты
Эффективное производство:
«Беларуськалий» атакует с тыла
Не надо ограничивать рост
Осторожный Шерлок Холмс
/section section class="tags"
Теги
Машиностроение
Эффективное производство
Инвестиции
Долгосрочные прогнозы
Спецдоклад "Освоение Сибири"
/section
«В систему советского отраслевого машиностроения “Металлургмаш” входило 25 заводов – остался только “Труд”. Рецепт очень простой: не воруй у себя и вкладывай в развитие», – говорит Юнус Ислямов, собственник и управляющий новосибирского машиностроительного завода «Труд».
Предприятие было создано в 1904 году еще в Новониколаевске (в советское время город стал Новосибирском) на базе мастерских, специализировавшихся на ремонте корпусов речных судов, паровых насосов, оборудования для зерновых мельниц, а также на изготовлении сельхозинвентаря. Начиная с 1930-х годов завод постепенно переориентировался на выпуск оборудования для промывки золотого песка, а к началу войны – на производство обогатительного и технологического оборудования для всей цветной металлургии.
figure class="banner-right"
figcaption class="cutline" Реклама /figcaption /figure
Юнус Ислямов работает на «Труде» с 1974 года – после окончания Томского политеха он попал сюда по распределению мастером парка крупных металлорежущих станков. К моменту краха СССР Ислямов дослужился до главного инженера, а потом ушел в бизнес – торговал металлами. «Вскоре до меня стала доходить информация, что на заводе начались проблемы с получением и выполнением заказов, работникам стали задерживать зарплату. Они начали просить меня вернуться на завод. И я вернулся. На полгода взял на себя исполнение обязанностей директора. Как сейчас помню, прошел по цехам и сказал людям: я подниму завод, но имейте в виду, что и вас заставлю работать. Тогда же я сформулировал четкие принципы взаимоотношений с рабочими, их я придерживаюсь и сейчас: вовремя платить зарплату, налоги, делать отчисления в пенсионный фонд, не забывать о ветеранах и молодежи», – рассказывает Ислямов.
Так с 1993 года он и руководит «Трудом». Более века завод был зажат на небольшом участке Большевистской улицы, одной из главных магистралей Новосибирска. Сосед, завод «Станкосиб», давно превратился в торговый и офисный центр. Аналогичная судьба могла ждать и старейшее предприятие Новосибирска, если бы не Ислямов. «Наверное, помогла упертость, в хорошем смысле этого слова. И удача. Говорят, удача – продукт напряженного поиска и труда. Нужно просто оглядеться вокруг. Ведь мы в России ходим по деньгам. Вскоре после того, как возглавил завод, иду по территории и вижу: вдоль забора лежит титан. Не верю своим глазам. Мне объясняют: да кому сейчас нужен титан? Парадокс: чугунные болванки лежат на складе, а титановые прутки и листы – на улице. Говорю: немедленно занести титан на склад. Более того, мы начали скупать титан, который имелся тогда в городе. И, как показала жизнь, это было правильное решение. Вскоре к нам приехала делегация золотодобывающей компании “Полюс” и сказала, что им нужны электролизеры. Cделаем, говорю. Спрашивают: а титан где возьмете? Так вот он, на складе. Удачи не добивается тот, кто лежит на диване».
Есть и другие факторы успеха. Во-первых, активный поиск новых заказчиков, в том числе за рубежом – в Казахстане, Киргизии, Узбекистане, Армении, Монголии и странах Юго-Восточной Азии. Например, заводу удалось быстро освоить выпуск скрубберов и дизельных насосных установок для монгольских фирм, концентраторов и пластинчатых сгустителей для «Казцинка», отсадочных машин и корытных моек для «Казмарганца» и т. д. Во-вторых – переориентация на производство не отдельных агрегатов, а комплексных установок. «Сейчас никому не нужны, как, например, в советское время флотационные машины или концентрационные столы. Всем нужна конечная продукция – обогатительный комплекс. Поэтому мы расширили номенклатуру изделий в сторону крупнотоннажных машин, мобильных обогатительных фабрик, которые быстро возводятся. Да и окупаются они всего за один-два сезона», – рассказывает Ислямов. По его мнению, росту производства помогла также небольшой размер и мобильность «Труда» («Завод всегда умел быстро переключаться с выпуска одной продукции на другую») и сохранение в его структуре проектно-конструкторского подразделения (ныне – Технологический институт горно-обогатительного машиностроения).
Все это к концу 1990-х поставило завод перед сложным выбором. «Чтобы развиваться, нам нужны были новые площади. К тому же больших корпусов требовала наша политика – производство обогатительных комплексов. На Большевистской крупногабаритные машины можно было собирать только на улице», – рассказывает Ислямов. В начале 2000-х ему предложили площадку завода «Сибтекстильмаш», на окраине города. «Я до сих пор помню свои ощущения, когда увидел, во что превратился завод. Прямо мурашки по телу от ужаса. Фонари выбиты, в цехах лежит снег, корпуса заморожены, коммуникации разграблены, станки разобраны. Бомжи жгли на заводе костры, чтобы греться. Наверное, экономически выгоднее было бы властям площади “Сибтекстильмаш” продать по частям, но мы предложили инвестиционную программу, и нам поверили», – рассказывает Ислямов. За минувшие годы он сделал невозможное – полностью перевез «Труд» на новую промышленную площадку, разом увеличив площади предприятия в шесть раз. Переезд станков, оборудования и даже «литейки», по оценкам Ислямова, обошелся примерно в 700 млн рублей. Цеха на Большевистской сейчас сдаются в аренду под автосалоны, магазины и сервисные центры; в перспективе там планируется реализовать крупный девелоперский проект.
Перенос завода – само по себе достижение, похвастаться которым могут немногие родившиеся в СССР предприятия. Благодаря переезду «Труд» получил не просто мощный стимул для рывка, но и стал базой для создания целого производственного кластера. Например, под эгидой «Труда» в начале 2000-х возник один из российских лидеров по производству банных и отопительных печей – компания «Термофор» (сейчас производит около 12 тыс. печей в месяц), а после ее ухода на другую площадку тут расположилась фирма «Конвектика» (пока что выпускает до 2 тыс. печей в месяц). Здесь же начинала производить гидромолоты компания «Рапат»; сейчас аналогичную продукцию выпускает другая дружественная «Труду» структура. Некоторые площади сдаются в аренду сторонним производителям; например, в одном из цехов делают модульные здания для вахтовиков (которые оснащают, кстати, печками «Конвектики»).
Объемы производства завода «Труд» с тех пор постоянно растут – так, по итогам 2013 года они составили около 800 млн рублей. «Потенциально на наших новых площадях мы можем производить минимум в четыре раза больше оборудования и деталей», – признает Ислямов. В перспективе «Труд» намерен полностью модернизировать свои мощности: заменить семь сотен единиц устаревшего и малопроизводительного оборудования на 150–200 новых агрегатов. Кроме того, в планах – построить новый и большой литейный цех, поскольку существующий с растущими объемами производства не справляется.
Сильно осложняет развитие предприятия кадровая проблема. «Мы десять лет искали главного технолога – и только недавно нашли. Их просто нет!» – сетует Юнус Ислямов. Сегодня заводу нужны 150–200 квалифицированных специалистов – конструкторов, технологов, станочников высшего разряда, руководителей производства. Остро стоит и вопрос с налогами. «У нас фонд оплаты труда составляет 25–30 процентов от себестоимости, в то время как в торговле – два-три процента. При этом они умудряются еще и платить “вчерную”. Мы, нуждающиеся в наиболее квалифицированных специалистах, оказываемся неконкурентоспособными перед другими отраслями, где заработная плата выше, а требования к специалистам ниже. Идет примитивизация экономики», – рубит правду Ислямов. «Нужно сделать так, чтобы из Москвы народ потянулся в регионы, а не наоборот. Ну соберет Москва всю способную молодежь, а дальше что? Кто будет работать? Китайцы? Так они потом скажут: а вы кто здесь? Нужно изменить политику государства в отношении российского машиностроения, создавать нормальные условия для развития промышленности в Сибири, изменить налоговые режимы, создать гарантии для инвестиций. Но я оптимист. Считаю, что с каждым годом будет все сильнее проявляться запрос на производственный потенциал машиностроителей – иначе и быть не может. Ну какая модернизация экономики без машиностроения?» – задает риторический вопрос владелец «Труда».