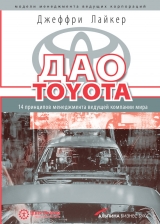
Текст книги "Практика дао Toyota. Руководство по внедрению принципов менеджмента Toyota"
Автор книги: Джеффри Лайкер
Соавторы: Дэвид Майер
сообщить о нарушении
Текущая страница: 17 (всего у книги 46 страниц) [доступный отрывок для чтения: 17 страниц]
Выравнивание графика с устойчивым многократным повторением питча в течение дня расценивается как передовая практика бережливого производства. Определенный уровень выравнивания необходим уже на этапе стабилизации (см. главу 4), чтобы иметь базис для расчетов времени такта и сформировать основной поток. На начальных стадиях питч, как правило, имеет большую продолжительность: нередко он равен рабочему дню. Такая величина питча обеспечивает фундамент для стабилизации, ее достижение не столь непосильная задача. Попытки преждевременно установить более краткий питч могут выявить слишком много проблем – с которыми существующая система не сможет справиться.
ЛОВУШКА
Остерегайтесь «аналитического паралича»
Стараясь как можно точнее определить уровень выравнивания, легко впасть в состояние «аналитического паралича». В работе имеет место несколько факторов, которые делают точное определение практически невозможным. Во-первых, как часто говорят о взаимных фондах: «Показатели в прошлом не гарантируют таких же показателей в будущем». Мы строим планы на будущее, опираясь на прошлые результаты, но это не значит, что они будут именно такими. Во-вторых, закон больших чисел означает, что чем больше объектов мы включаем в исследование, тем меньшее влияние оказывает каждый из них. Если мы рассматриваем совокупность значений объемов производства за год, случайные всплески сказываются на общем среднем значении не столь ощутимо. На языке неспециалиста это значит, что, если мы имеем дело с достаточно большой выборкой, «шум» отфильтровывается. В-третьих, информация, которую вы анализируете, может оказаться некорректной. Она может отражать не фактический спрос, а заказы, которые генерирует внутренняя система планирования потребностей в материалах (MRP) для удовлетворения «спроса». На количестве таких заказов сказывается множество факторов, и этот показатель далеко не всегда отражает фактический спрос. Наконец, как вы увидите далее, занимаясь выравниванием ассортимента продукции в целом с целью обеспечить необходимый баланс, неизбежно приходится вносить некоторые незначительные поправки. Мы рекомендуем выбрать ориентировочно приемлемый объем каждого вида продукции и приниматься за выравнивание процесса. Каким бы тщательным ни был ваш анализ, впоследствии вам непременно придется вносить коррективы.
ПОДСКАЗКА
Определите кратное для структуры выравнивания
Оптимальна структура выравнивания, кратная двум, т. е. структура повторяется ежедневно, через день, каждый четвертый день или максимум каждый шестой день. Если суточный спрос, умноженный на шесть, дает такой низкий объем производства изделия, что работать с ним по-прежнему нецелесообразно, вам придется снизить время наладки или перевести данное изделие в «другую» категорию, пока время наладки не снизится до необходимого уровня. В нашем примере изделия, спрос на которые был примерно в два раза меньше, чем на те, что изготавливались ежедневно, производились через день. Изделия, спрос на которые составлял примерно четверть от спроса на изделия, изготавливаемые ежедневно, производились каждый четвертый день.
Помимо питча выравнивания требуют еще три составляющих:
1. Объем выпуска, т. е. количество определенного вида продукта, которое следует произвести в течение заданного отрезка времени (питча).
2. Ассортимент, т. е. соотношение количества разных моделей, изготавливаемых в течение питча, например изделий A, B, C и т. д.
3. Последовательность изготовления продукции, которая представляет собой порядок изготовления заданного объема при заданном ассортименте. Этот порядок может предполагать последовательное изготовление нескольких изделий одной модели, например A, A, A, B, B, B, C, C, C, или носить иной характер, скажем A, C, A, B, A, C.
Названные составляющие перечислены в порядке от простого к сложному. Учитывая исходное состояние процесса, вам, возможно, придется начать с простейшего выравнивания объема и структуры ассортимента на основе достаточно длительного питча, равного продолжительности смены или рабочего дня. Мы то и дело слышим, как кругом на все лады превозносят поток единичных изделий и последовательное выравнивание производства, однако текущая ситуация может сделать достижение этой цели для вашего предприятия делом далекого будущего. Не забывайте, что Toyota понадобилось 50 лет, чтобы достичь таких результатов, как сегодня, при этом компания считает, что во многих отношениях она до сих пор не совершенна. Главное – сделать усилие, чтобы добиться ощутимого улучшения, и оценить, на что вы способны, но не надрываться, иначе дело кончится провалом.
Начните с анализа фактического производства или объема продаж для каждого продукта в течение последних 12 месяцев. Так вы определите, что значит высокий, низкий и средний объем спроса. Нанесите фактические показатели на график, который в отличие от обычной таблицы цифр даст возможность наглядно увидеть «средневзвешенный показатель». Минимумы и максимумы позволят вам увидеть лишь амплитуду, а несколько пиковых значений могут исказить представление о среднем. Нанесение фактических показателей на график позволит вам визуально определить оптимальные позиции для выравнивания.
Окончательное решение о выравнивании объема в определенной мере носит субъективный характер. В большинстве случаев в Toyota выбирают показатель, составляющий примерно 80 % максимального спроса (если данный всплеск спроса не представляет собой единичный случай), поскольку разницу между 80 и 100 % можно компенсировать за счет сверхурочной работы (восемь часов в неделю). Для расчета времени такта используется показатель выровненного спроса. В предыдущей главе мы говорили о времени такта как о расчетном параметре. Если при определении выровненного объема спроса показатель в 80 % кажется вам недостаточно достоверным, лучше ошибиться в сторону небольшого завышения спроса. На практике, когда вы определяете количество, которое удовлетворит предполагаемый выровненный суточный спрос, оно оказывается либо слишком большим, либо слишком маленьким, либо в точности соответствующим спросу (что менее вероятно). Проблема в том, что определить это заранее довольно сложно из-за вариации в производстве («туман»). Как только процесс стабилизируется, «туман» слегка рассеивается и правильный уровень делается более очевидным, что позволяет легко внести нужные поправки.
Уже первый цикл выравнивания позволит частично избавиться от потерь, вызванных попытками угнаться за колебаниями спроса, и позволит высвободить дополнительные мощности, не доступные раньше. Многие компании обнаруживают, что даже первичное выравнивание позволяет им «идти в ногу» с заказами, и убеждаются, что предыдущие предположения о спросе вели к перепроизводству. В такой ситуации можно либо сократить объем ресурсов, либо, если возможно, увеличить объем продаж.
Рассмотрим конкретный пример. Данные таблицы 7–1 представляют собой упрощенный вариант реальной ситуации, однако сами понятия применимы и к более сложным условиям. В приведенном примере мы занимаемся выравниванием производства 10 деталей, обозначенных буквами от A до J, спрос на каждую из которых колеблется. Спрос на изделия, попавшие в категорию «прочие», меньше, чем у перечисленных выше, и составляет в среднем 125 единиц, выравнивание применительно к отдельным видам этих деталей не производится. Общий суточный объем для всех видов продукции, включая «прочие», выровнен. На самом деле объем производства «прочих» изделий варьируется, что позволяет увеличить или сократить общее времени работы, если фактический спрос больше или меньше запланированного. Эти коррективы не отражаются на результатах выравнивания для изделий A-J.

Структура производства разработана с учетом требуемых объемов производства деталей, применительно к которым производилось выравнивание. Данная структура призвана свести к минимуму негативные последствия переналадки (процесс был оптимизирован, но продолжительность переналадки пока превышает желаемую). Детали A-C производятся каждый день (КД), а детали D-F производятся через день (ЧД). Детали G-J производятся каждые четыре дня (К4Д – да-да, мы знаем, что наша задача производить каждую деталь каждый день, но до этого мы еще не дошли!).

Один из вариантов структуры выравнивания представлен в таблице 7–2. Суточная потребность, составляющая 1318 единиц продукции, была округлена на незначительную величину – до 1325. Как мы уже говорили, это не столь важно, поскольку имеет место вариация количества деталей в категории «прочие». Такая структура является более ровной и позволяет ежедневно производить некоторое количество «прочих» деталей. Если среднее количество заказов на «прочие» систематически превышает указанное количество, можно рассмотреть иную структуру.

В таблице 7–3 представлена альтернативная структура, где все детали, производимые в режиме ЧД, изготавливаются в один и тот же день наряду с производством деталей в режиме КД. Производство деталей в режиме КД осуществляется по-прежнему – они изготавливаются изо дня в день. Детали, производимые в режиме ЧД и К4Д, обеспечивают возможность маневра в зависимости от потребностей процесса. К примеру, в данном случае вся совокупность деталей, производимых в режиме ЧД, изготавливается в один и тот же день. Возможны и иные варианты структуры. Цель – обеспечить оптимальный выровненный объем структуры по горизонтали, т. е. по каждой детали в пределах заданного временного интервала – выровненный общий объем деталей по вертикали и выровненную структуру на протяжении питча. Эта структура определяет последовательность изготовления деталей A-J. Выравнивание в хронологическом аспекте осуществляется в пределах заданного воспроизводимого интервала. В нашем случае структура повторяется каждые четыре дня и производство каждого изделия выровнено в пределах четырех дней. Обычно временное окно при выравнивании в Toyota составляет месяц, в его основе лежит воспроизводимая структура одного дня. Примечание: линия основной сборки автомобилей применяет структуру выравнивания, ориентированную на высокую периодичность питча с учетом ассортимента изготавливаемых автомобилей, а вспомогательные операции, которые производят детали, пополняя супермаркет или «резерв для отбора», работают в соответствии с иной структурой выравнивания, производной от основной.
Заметьте, что в соответствии с альтернативной структурой общий объем в первый, третий, пятый и седьмой день превышает целевой суточный показатель. Это не слишком серьезная проблема, поскольку количество остается в разумных пределах (обычно максимальное отклонение не превышает 10 %). При работе с фактическим спросом в большинстве случаев не удается добиться таких равномерных показателей, как в этом примере. Для начала попытайтесь выровнять показатели насколько возможно. Создав условия для производства по выровненному графику, вы сможете получить более основательное представление о фактической потребности и соответствующим образом откорректировать структуру выравнивания.
Составить выровненный график куда проще, чем производить продукцию в соответствии с планом! Скорее всего, поначалу вы обнаружите множество препятствий, мешающих придерживаться графика. Следует систематически выявлять и устранять эти препятствия, чтобы обеспечить стабильность (отследить причины, создающие помехи для хейдзунка, и применить метод решения проблем для их устранения). Теперь выровненный график следует считать «голосом потребителя». Правда, потребителя не совсем реального – речь идет о соглашении, которое представляет нужды потребителя, выровненные на благо вашего процесса.
Поскольку речь идет о потребителе, вы должны измерять и отслеживать свою способность его удовлетворить. Если в какой-то момент времени вы не можете обеспечить заданный объем, ассортимент или последовательность, это эквивалентно «невыполненному заказу» (т. е. неудовлетворенному потребителю, хотя, возможно, речь и не идет о невыполнении фактического заказа). Вам следует приучить людей относиться к хейдзунка как к голосу потребителя и как к важнейшей задаче, стоящей перед потоком создания ценности.
Пошаговое выравнивание и развитие хейдзункаПоздравляем! Добравшись до этого этапа построения бережливого производства, вы должны быть готовы к тому, что самое интересное только начинается. После того как усовершенствования стандартизованы, процессы стабилизированы и связаны в поток создания ценности, вы приступаете к циклу непрерывного совершенствования. Да-да, вам придется проходить через все это вновь и вновь, до бесконечности. Хорошая новость в том, что с каждым успешным проходом очередного витка спирали непрерывного совершенствования путь дальше становится все проще, поскольку вы набираетесь опыта, а сопротивление переменам слабеет. Теперь любые изменения будут приносить прямую пользу процессу в целом. Иными словами, на смену «карманным» преобразованиям, которые не отражались на общем результате, придут усовершенствования, которые будут позитивно сказываться на эффективности всего потока создания ценности.
Но не все так хорошо. С этого момента совершенствование будет достигаться постоянным ужесточением требований ко всем операциям с целью сокращения времени выполнения заказа, повышения гибкости и стабильности, снижения уровня запасов и укрепления позиций вашей компании в долгосрочной перспективе. Эффект от таких действий будет постепенно возрастать, и каждый этап совершенствования будет давать прирост, границы которого будут находиться в заданных пределах. Созданная система позволяет определить желаемый результат и гарантировать его достижение.
Этот метод повышает нагрузку на поток создания ценности и вызывает разрыв его слабого звена, что порождает нестабильность. Обнаружение слабого звена позволяет мобилизовать ресурсы для решения выявленных проблем. Этот цикл повторяется вновь и вновь, как показывает модель спирали непрерывного совершенствования в главе 3 (рис. 3–4). В ходе каждого последующего цикла совершенствования выявляются все менее значительные проблемы. Таковы хорошие и плохие новости. Плохая новость состоит в том, что устранять проблемы будет все труднее. Хорошая новость в том, что вы добьетесь значительной оптимизации процесса, а уровень вашей квалификации будет расти по мере повышения сложности проблем.
Пошаговое выравниваниеПосле завершения связывания потока создания ценности к отдельным его участкам начинают предъявлять повышенные требования. Помните, что происходит с потоком создания ценности, если скорость процесса, задающего ритм, меняется? Этот процесс задает новый ритм всех остальных процессов в потоке создания ценности. Если выровненный график, который задает определенную ассортиментную структуру продукции, меняется, необходимо откорректировать все процессы таким образом, чтобы обеспечить поддержку новой структуры ассортимента.
Такое пошаговое выравнивание или уплотнение потока создания ценности стимулирует совершенствование. Речь идет о планируемом, управляемом процессе, при котором совершенствование идет вполне определенным образом. Так, если объем запасов в супермаркете сократился, это окажет определенное влияние на процесс-поставщик. Это может потребовать, к примеру, более частых переналадок, а как следствие – сокращения ее продолжительности. Любое изменение стандартного элемента потока создания ценности порождает потребность в совершенствовании.
Точки управленияВ связанном потоке создания ценности существуют особые точки управления, которые воздействуют на другие процессы в потоке. Поскольку отдельные операции в потоке создания ценности связаны, изменения в одном месте (точке управления) требуют изменения всех процессов, снабжающих эту точку. Так как точка управления служит важнейшей операцией в потоке создания ценности, надо строго следить за ней для обеспечения стабильной работы потока создания ценности, а управление этой точкой поможет вам понять, как извлечь из всего потока создания ценности максимум возможного.
Одна из основных точек управления – выровненный график. Он представляет собой основу для времени такта. Работа задающего ритм процесса основана на времени такта, поэтому заданный ритм передается на все остальные операции. Зная точку управления, менеджеры могут эффективно выявлять неполадки в работе и заниматься непрерывным совершенствованием.
Если процесс, задающий ритм, стабильно производит заданный объем продукции и обеспечивает производство заданной ассортиментной структуры в нужной последовательности в соответствии с выровненным графиком, поток создания ценности удовлетворяет требования потребителя (следующий этап – это сокращение затрат). Однако если процесс, задающий ритм, не отвечает требованиям выровненного графика, этот процесс будет первым участком, где следует постоять в кругу. Этот удобный наблюдательный пункт даст возможность оценить, обеспечено ли надлежащее снабжение процесса, задающего ритм. Если нет, продвигайтесь к началу потока, чтобы выявить слабое звено. Если да, проверьте, не препятствует ли работе процесса, задающего ритм, одна из следующих за ним операций. (Правила запрещают перепроизводство, а значит, если процесс, задающий ритм, блокируется идущим за ним процессом, это будет заметно сразу.) Визуализация связи между процессами позволяет быстро выявить помехи в потоке, облегчая управление потоком создания ценности.
Точка управления для запасовТакой точкой управления является канбан. Сокращение числа карточек[11]11
Канбан не обязательно имеет форму карточки, он может быть и в электронной форме. – Прим. науч. ред.
[Закрыть] канбан ведет к сокращению общего объема запасов в системе. Такое сокращение следует проводить систематически, как по мере совершенствования процесса, так и для того, чтобы стимулировать потребность в совершенствовании. Количество запасов, необходимое для поддержания процесса, может использоваться как мерило совершенствования. Устойчивое снижение уровня запасов – показатель отлаженного процесса.
ЛОВУШКА
Сокращение запасов – это мерило успеха, но не самоцель
При освоении бережливого производства многие считают сокращение запасов первоочередной задачей. Есть множество способов достижения этой цели, включая разного рода хитрости. Однако лучше поставить задачу создать связанный поток и использовать объем запасов как критерий успеха. Для управления запасами используется канбан, регулируя число карточек канбан, несложно оценить эффективность процесса. Управление запасами с помощью канбан стандартизировано, и возможность недобросовестной манипуляции запасами снижается.
Канбан может влиять и на оборачиваемость запасов. Если количество изделий на одну карточку канбан снижается (например, уменьшается объем контейнера), канбан будет проходить свой «цикл» чаще, ускоряя перемещение запасов в процессе. Кроме того, снижение количества запасов на единицу канбан ведет к повышению уровня гибкости при пополнении запасов и снижает размеры рабочей зоны и объем потерь. Как ни странно, предпочтительно иметь «в системе» больше единиц канбан. Например, если общий уровень запасов составляет 2000 штук, лучше иметь 20 канбан – по одному на 100 изделий, чем 2 канбан – по одному на 1000 изделий. Очень трудно чувствовать спрос, если в системе только две карточки канбан, и каждый раз, когда карточка возвращается, приходится немедленно поставлять следующую партию изделий.
Выровненный график определяет порядок пополненияХейдзунка не только выравнивает все процессы, но и определяет продолжительность питча. Поскольку в течение заданного питча материалы расходуются со стандартной скоростью, можно определить характеристики процесса пополнения запаса материалов. Пополнение запаса материалов подчиняется основной работе, добавляющей ценность, а значит, не следует заниматься определением «траектории» или методов подачи материалов до базовой стандартизации основного процесса.
Приведенный далее пример показывает, как выровненный график определяет процедуру пополнения материальных запасов. Это позволяет стандартизировать работу рабочих, в том числе траекторию их перемещения в течение питча или серии питчей. Общее количество материала стандартизируется, а количество материала в контейнере может регулироваться в зависимости от длительности питча. Для иллюстративных целей мы предполагаем, что в рассматриваемом процессе обеспечен высокий уровень хейдзунка, все изделия изготавливаются в строго определенной последовательности, а общая продолжительность рабочего времени составляет восемь часов. Спрос составляет 400 изделий, а весовые показатели количества каждого вида изделий показаны в таблице 7–4.

ПОДСКАЗКА
Установите питч исходя из имеющихся условий
Если у вас уже есть определенный опыт освоения бережливого производства, скорее всего, вы не станете устанавливать питч продолжительностью в один час. Мы рекомендуем продвигаться вперед, сокращая питч каждый раз наполовину. Если сейчас вы перемещаете материал ежедневно (или питч не определен), начните с питча продолжительностью в одну смену. Когда воспроизводимость процесса улучшится, сократите питч вдвое.
С учетом требуемого количества и весовых показателей количества повторяющаяся структура хейдзунка (которая позволяет свести к минимуму размер партии) такова: ABACABAD – ABACABAD – ABACABAD.
Чтобы определить питч для регулярной работы согласно данной модели, разделим 8 часов на объем спроса (400 изделий) и умножим на количество изделий в модели выравнивания (питч):
28 800 секунд (8 часов) в день / 400 изделий = 72 секунды на одно изделие
Тогда:
72 секунды на одно изделие 3 8 изделий в течение питча = 576 секунд на питч (9 минут 36 секунд), или 6,25 питч-циклов в час.
Предположим, мы хотим, чтобы рабочий занимался подачей материала ежечасно (питч пополнения запаса материала). В таблице 7–5 показаны расчеты количества контейнеров, которое понадобится перемещать, если цикл пополнения запасов будет составлять один час.

На основании требований к перемещению материалов в течение часового цикла можно осуществить стандартизацию работы с учетом маршрута перемещения рабочего и других операций, которые он обслуживает.