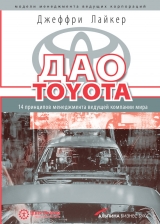
Текст книги "Практика дао Toyota. Руководство по внедрению принципов менеджмента Toyota"
Автор книги: Джеффри Лайкер
Соавторы: Дэвид Майер
сообщить о нарушении
Текущая страница: 13 (всего у книги 46 страниц) [доступный отрывок для чтения: 17 страниц]
Глава 6
Стандартизация процессов и процедур
Носит ли стандартизация принудительный характер?Упоминание стандартизированной работы вызывает в памяти образы специалистов по организации производства с секундомерами в руках. Они одержимы повышением производительности и наводят ужас на рабочих, сражаясь за каждую секунду и выжимая из людей последние силы. Расписанная по минутам жизнь, где суровый босс следит, чтобы никто ни на йоту не отступал от правил. Разгул бюрократии, которая подавляет человеческую волю и творческое начало и превращает людей в автоматы.
Однако существует и иной взгляд на стандартизацию. Масааки Имаи в своей новаторской работе пишет, что без стандартизации нет кайдзен[6]6
Masaaki Imai, Kaizen: The Key to Japan’s Competitive Success, New York: McGraw-Hill/Irwin, 1986 [Масааки Имаи. Кайдзен: Ключ к успеху японских компаний. – М.: Альпина Бизнес Букс, 2005]. – Прим. пер.
[Закрыть]. Стандартизация – это отправная точка для непрерывного совершенствования. Как рассказывается в Дао Toyota, Пол Адлер проанализировал производственную систему Toyota (TPS) с точки зрения теории организации[7]7
Paul S. Adler, «Building Better Bureaucracies», Academy of Management Executive, 13:4, November 1999, 36–47.
[Закрыть]. Он обнаружил, что Toyota удается избежать большей части незапланированных негативных последствий бюрократии, поскольку она сумела создать так называемую «поощряющую бюрократию», где наряду со стандартизацией имеет место расширение полномочий сотрудников. Мы представляем себе бюрократию как «принуждающую» систему, которая мешает людям быть гибкими и совершенствоваться. Однако поощряющая бюрократия Toyota дает прямо противоположный результат – она предусматривает гибкость и инновацию, имеющие долгосрочные последствия.
Введение стандартизированных процессов и процедур – важнейшее условие устойчивой эффективности. Лишь при наличии стабильного процесса можно приступить к непрерывному творческому совершенствованию. Как мы уже показывали в предыдущих главах, разработка стандартов начинается на ранней стадии внедрения бережливого производства и продолжается в ходе развития и совершенствования бережливых операций. Создание стандартизированных процессов опирается на определение, наглядность (визуальные показатели) и последовательное применение методов, дающих наилучший результат. Стандартизация – не оторванный от других метод, который применяется через заданные промежутки времени, органическая часть непрерывного процесса выявления проблем, создания эффективных методов и поиска путей применения этих методов. Стандартизация не навязывается людям извне, но осуществляется по их инициативе. Самый значительный вклад в стандартизацию вносят те, кто выполняет работу и знает ее во всех подробностях.
Мы уже не раз говорили, что наша цель – помочь вам усвоить основные принципы и концепции дао Toyota. Повторяем, в наши намерения не входит создание очередного учебника по применению инструментов бережливого производства. Процесс, который в Toyota называют «стандартизированной работой», так важен для производственной системы в целом, что ему посвящена треть внутреннего документа Toyota TPS Handbook[8]8
TPS Handbook, 1989 by Toyota Motor Corporation.
[Закрыть]. И это понятно, стандартизированная работа и прочие стандарты работы – основа непрерывного совершенствования.
Здесь мы сталкиваемся с еще одним заблуждением в отношении TPS. Пока не выработаны стандарты для какой-либо операции, заниматься ее совершенствованием невозможно. Подумайте сами: если в нестандартизированный (непродуманный и хаотический) процесс были внесены усовершенствования, что именно вы усовершенствовали? Его хаотичность? Или вы просто добавили еще один возможный вариант выполнения работы, что только увеличило хаос? Если работник творчески совершенствует свою работу, но это не закрепляется стандартом, процесс пойдет лучше, лишь пока его выполняет именно этот человек. Результатами его усовершенствований не сможет воспользоваться никто другой. Если за усовершенствованием следует стандартизация, возникает основа, позволяющая персоналу непрерывно совершенствовать процесс. Так закладывается фундамент обучающейся организации.
К сожалению, нередко, работая с компаниями, которые внедряют бережливые процессы, мы слышим просьбу «заняться стандартизированной работой», словно речь идет о независимом инструменте, который можно запросто освоить в соответствии с графиком внедрения («По плану теперь мы должны заняться стандартизированной работой»). Одно из подобных заявлений прозвучало примерно так: «К октябрю мы должны разобраться со стандартизированной работой». На это последовал ответ: «Разумеется, мы можем это сделать, но стандартизированная работа – это инструмент, и подобно любому инструменту она имеет конкретное назначение и применяется для достижения конкретных целей».
В одной компании внедрение стандартизированной работы отставало от плана внедрения бережливого производства. Решение: нанять на лето школьного учителя, который распишет процедуру стандартизированной работы для всех операций. Результат: повсюду развешаны красиво оформленные карты стандартизированной работы, но стандарты никто не соблюдает. Разумеется, если вам хочется развесить повсюду листы бумаги, заполненные информацией, – дело ваше, однако реальной ценности вы этим не создадите. В ваших силах использовать стандартизированную работу для сокращения потерь, улучшения процесса работы и непрерывного совершенствования. Выбор за вами.
Мы говорим о стандартизации как об одном из «этапов», однако на самом деле стандартизация должна применяется непрерывно, о ней следует помнить при разработке любого метода работы. Подобно прочим составляющим TPS данная концепция чрезвычайно важна, но чтобы применять стандартизацию надлежащим образом, ее следует тщательно осмыслить. Стандартизация – не комплект документации, который требует подготовки и тщательного контроля. Это средство обеспечения максимально эффективной и стабильной работы и основа устойчивости процесса. Без стандартизации такие инструменты, как шесть сигм и иные современные методы снижения вариации, бесполезны.
Стандартизированная работа или нормирование труда?Пожалуй, из всех концепций бережливого производства наибольшее количество заблуждений и ошибок связано именно со стандартизацией. Корни этой проблемы восходят к стремлению получить максимальную прибыль за счет разбивки всего задания на составляющие и распределения этих составляющих между работниками, в чем весьма преуспел Фредерик Тейлор. История нормирования труда во многих отраслях (в первую очередь в автомобильной промышленности) – это история борьбы. Стандарты тех лет предназначались прежде всего для того, чтобы карать работников за низкую производительность.
Такой подход породил ряд легкоузнаваемых «игр» и попыток обмануть систему. Основным итогом стало противостояние между рабочими и менеджментом. Вместо стремления работать на общую цель, создавая возможно лучший продукт для потребителя, мы видим противоборство двух групп, которые ведут себя как антагонисты: менеджмент стремится как можно точнее регламентировать работу, чтобы установить нормы затрат труда и заставить каждого работника им следовать, а работники намеренно иначе работают, когда за ними наблюдают, чтобы к ним предъявляли более низкие требования, которые несложно выполнить. При этом менеджмент использует «стандарты», принимая решения, касающиеся производства, с учетом «нормативно допустимых затрат времени» и тому подобных показателей, в основе которых лежат нормы производительности. Цель – обеспечить, чтобы производственные рабочие «отработали» положенное количество часов. Если это выполняется и нормы затрат соответствуют запланированным (либо план перевыполняется), накладные расходы на контроль считаются оправданными, что теоретически обеспечивает получение целевой прибыли.
С точки зрения рабочих, трудовые нормы – это показатель «напряженности» их труда, который учитывает, сколько сил нужно потратить на выполнение работы. Кроме того, рабочие интуитивно понимают, что все люди обладают разным потенциалом и система ориентируется на самый низкий уровень возможностей. При таком подходе работающие медленно успешно справляются с работой, а более проворные могут добиться более высокой производительности или при желании «освободить» часть своего времени, работая быстрее других.
При такой модели стандарты работы устанавливаются исходя из неверно поставленной цели. Стандарт ориентирован прежде всего на нормы затрат, а не на обеспечение оптимального метода работы при минимальных потерях, который позволил бы получить продукт отличного качества при минимальных затратах. Такие нормы используются либо как кнут, чтобы наказывать рабочих за низкую производительность, либо как пряник, чтобы соблазнить их перевыполнить норму (повышение ставок зарплаты с учетом производительности – производная от описанного метода). Эти представления настолько въелись в сознание менеджмента и наемных работников, что введение стандартизированной работы по методу Toyota может оказаться одной из самых трудных задач при освоении бережливого производства. Всем чрезвычайно тяжело расстаться с привычным положением вещей, поскольку каждый научился работать и преуспевать в условиях этой системы. Менеджеры боятся, что усвоение дао Toyota приведет к тому, что подчиненные станут неуправляемыми, выбирая метод работы на свой вкус, а значит, будут работать спустя рукава. Кроме того, они боятся лишиться системы измерений, которая помогала им управлять подчиненными и контролировать их, чтобы добиться успеха. Всем знакомы разговоры такого рода:
Менеджер по производству – мастеру: «Ваш отдел опять превысил нормативы по времени работы. Что вы намерены предпринять, чтобы исправить дело?»
Мастер: «Нашему цеху пришлось выполнить несколько сложных заданий, и мы не уложились в отведенное время. Мы выйдем на работу в субботу и займемся работой попроще. Это поможет исправить положение».
Менеджер по производству: «Ладно. Я доложу об этом директору завода и скажу, что причина была в неудачном сочетании ассортиментных позиций. Я постараюсь, чтобы впредь вам было полегче».
Очевидно, что в данном случае первоочередное внимание ошибочно уделяется измерениям, а не созданию по-настоящему эффективного процесса, который обеспечит устойчивую результативность. Заметьте, что для улучшения показателей мастер собирается заняться «работой попроще». Однако деталь есть деталь, независимо от сложности или простоты ее обработки. Означает ли это, что при выполнении «работы попроще» будут изготавливаться именно те детали, которые нужны потребителю? Похоже, в данном случае это не главное. Обидно, что столько времени и сил тратится впустую только ради того, чтобы выйти на нужные показатели, вместо того чтобы заняться оптимизацией процесса. Менеджеры попадают в порочный круг, из которого нет выхода, поскольку эффективность работы их самих определяется их способностью добиться целевых показателей.
Цель стандартизацииПри традиционной модели производства первоочередной задачей было свести к минимуму затраты на единицу продукции и создать стандартный метод работы, который обеспечивает запланированный уровень затрат (рис. 6–1). Такая модель учитывает «затраты на единицу продукции», в то время как дао Toyota предполагает наращивание возможностей системы в целом и уделяет основное внимание «общим затратам», считая основным показателем успеха сокращение потерь. Традиционный подход изучает движения и время для определения наиболее «эффективной» рабочей процедуры, и на выполнение определенной задачи выделяется «стандартное» время. Обычно за оператором наблюдают и учитывают, сколько времени затрачивается на отдельные движения. Далеко не всегда метод, избранный оператором, оптимален: это всего лишь метод, который применяет оператор, когда за ним наблюдают. Такой процесс порождает «ложный стандарт», который впоследствии используется для определения «эффективности».

Дао Toyota преследует ту же цель, т. е. снижение затрат; однако основное внимание уделяется сокращению потерь в системе (рис. 6–2). Базой непрерывного совершенствования в Toyota считают стандартизацию, т. е. предполагается, что в перспективе результаты будут лучше предусмотренных стандартом. Традиционный подход рассматривает стандарт как самоцель, точно в нем закреплен предельный уровень эффективности, и это препятствует совершенствованию. Это коренное отличие образа мышления – основа множества парадоксальных составляющих бережливой системы. Цели остаются прежними: изготовить высококачественный продукт при минимальных затратах в кратчайшие сроки, однако образ мышления, определяющий достижение этих результатов, диаметрально противоположен тому, что доминировал в массовом производстве последние сто лет. К тому же подход массового производства ограничивает возможности достижения названных целей.

В основе модели сокращения потерь в рамках бережливого производства лежит особый образ мышления. Во всех организациях есть потери, которые порождаются неупорядоченными действиями и непоследовательными методами. Чтобы устранить потери, необходимо снизить или устранить вариацию внутри процессов. Вариация – это антитезис стандартизации. По определению вариация предполагает невозможность стандартизации. Как рассказывалось в главах 4 и 5, для введения стандартизированной работы нужно изолировать вариацию. Помимо прочего, стандартизация создает базу для сравнения и позволяет отличать стандартный (нормальный) метод от нестандартных (отклоняющихся от нормы) методов. Для оперативного определения эффективности и внесения поправок в режиме реального времени используются методы визуального контроля и прочие инструменты бережливого производства, что обеспечивает стабильное достижение целевых показателей результативности.
Стратегии введения стандартизированных процессов и процедурОсновные средства внедрения стандартизированных процессов и процедур – документация по стандартизированной работе и ряд инструментов бережливого производства, которые использовались на предыдущих этапах (таблица 6–1).

Традиционная политика и процедуры часто препятствуют стандартизации. Возьмем ситуацию с приходом на работу. Стандартизированный процесс предполагает, что рабочий должен обязательно присутствовать на месте. Это значит, что, если кто-то не вышел на работу, отсутствующему следует найти замену, чтобы обеспечить надлежащий ход процесса. Процесс не может функционировать должным образом, если не предусмотрен резерв на случай непредвиденных обстоятельств, например на случай невыхода на работу кого-то из сотрудников. Тем не менее при традиционной системе высший менеджмент редко задумывается о таких проблемах, и мастера изо дня в день лезут из кожи вон, чтобы найти замену отсутствующим рабочим, не располагая стандартизированным методом решения проблемы.
Типы стандартизацииПОДСКАЗКА
Создайте структуру для поддержания стандартизированной работы
Toyota создала систему лидеров групп и лидеров команд. Лидер команды – сотрудник с почасовой оплатой, который отвечает за команду из пяти-семи человек. Лидеры команд следят за соблюдением стандартной процедуры, выявляя отклонения от стандарта (см. главу 11), и при необходимости заменяют отсутствующих. Они нередко участвуют в разработке стандартизированной работы для производства новых моделей. Благодаря лидерам команд описание стандартизированной работы не просто украшает стены, но становится подлинным инструментом непрерывного совершенствования. Любопытно, что в большинстве компаний позиция лидера команды отсутствует.
Введение процесса, который в Toyota обозначают широким понятием «стандартизированная работа», нередко оказывается очень непростым делом. Попытки других компаний применить этот, казалось бы, простой метод оказываются обескураживающе сложными. Разработка стандартизированной работы столь ощутимо отличается от расчета трудовых норм, что едва ли уместно проводить между ними какие-либо параллели. Методы, которые называются «стандартными» в других компаниях, не имеют ничего общего с понятием «стандартизированной работы» в Toyota, которое обозначает метод выполнения работы с минимальными потерями. На самом деле есть множество типов стандартов, и все они объединены в целостный метод, регламентирующий оптимальную рабочую процедуру. В Toyota стандартизованная работа – основной инструмент, регламентирующий методы работы. В ней описывается, кто, когда, где и какую работу выполняет.
Структура взаимосвязей между разными типами стандартов представлена на рис. 6–3 в виде дома. Все стандарты работают на единые цели – обеспечить выполнение работы заданным методом с минимумом затрат и дать работникам исчерпывающую информацию, способствующую повышению навыков и знаний.

Заметьте, что каждый тип стандарта имеет свое назначение, однако работа по стандартизированным методам должна удовлетворять всем названным стандартам. Это не значит, что все они содержатся в документации на стандартизированную работу. Эта документация оговаривает лишь этапы работы, которые ведут к достижению желаемого результата (выполнению прочих стандартов). Позиции прочих стандартов учитываются при инструктаже оператора и представляют собой часть его подготовки, как показано на рис. 6–4.

В основе стандартов качества лежат ожидания потребителя, которые определяют требования к внешнему виду продукта и связаны с такими понятиями, как чистовая обработка/отделка. В том числе это:
• общий внешний вид;
• цветовое решение;
• дефекты, несоответствия (закругленные края, вмятины и т. д.);
• допуски и посадки;
• обработка поверхности;
• ограничения размера и количества дефектов.
ПОДСКАЗКА
Храните ценности в надежном месте
Эталонные образцы представляют большую ценность и требуют соответствующего обращения. Их следует хранить в надежном месте, возможно, под замком, и доступ к ним имеет лишь мастер. Когда у оператора сформирован навык оценки, их применяют достаточно редко. На эталонных образцах должна стоять дата и подпись лица, ответственного за качество. Ответственность за сохранность образцов возлагается на производственников. Относитесь к ним как к инвестированному капиталу!
Стандарты качества обычно включаются в ведомости по производственному инструктажу, где подробно описано, какие условия нужно отслеживать, на что именно следует обращать внимание и каковы критерии оценки хорошо/плохо. Для определения основных параметров, которые необходимо отслеживать на производстве, и мест, где такие отклонения наиболее часты, используется информация, полученная при аудитах качества. Это позволяет выработать метод инспектирования в процессе выполнения работы и повышает исходный уровень качества. Подробное описание данного метода инспектирования не включено в документацию на стандартизированную работу, но сам метод упоминается в ней отдельной позицией (осмотрите деталь).
Стандарты качества, требующие визуального контроля продукта, допускают возможность субъективной интерпретации. Так, «приемлемый внешний вид поверхности» можно истолковать по-разному в зависимости от личного истолкования понятия «приемлемый». В таких ситуациях необходимо, чтобы отдел качества обеспечил производство эталонными образцами требуемого уровня качества. Эти образцы позволяют четко договориться о том, что приемлемо, а что нет.
Обычно нормативы по безопасности труда и охране окружающей среды компании подчиняются нормам федерального права и нормам штата. Эти нормативы, как правило, разрабатываются специальными техническими отделами, и изменение таких стандартов менеджерами или сотрудниками допускается лишь с одобрения такого отдела. Однако сотрудникам, которые разрабатывают методы стандартизированной работы, дается возможность ознакомиться с этими требованиями, назначение которых – обеспечить должный уровень безопасности труда и охраны окружающей среды. Рабочая группа или менеджмент отдельного участка могут разрабатывать нормы техники безопасности при выполнении конкретного вида работ. Речь идет, например, о риске получения травмы – пореза или защемления оборудованием. Такие потенциально опасные моменты помечаются в документации на стандартизированную работу специальным значком.
Стандартные технические требованияСтандартные технические требования (спецификации) содержат техническую информацию по надлежащему функционированию оборудования и определенные требования к технологическому процессу, обеспечивающему производство продукта. Примеры таких требований:
• размеры и допуски;
• методы обработки (метод сварки, метод конечной обработки и т. д.);
• параметры работы оборудования (время, температура, давление и т. д.);
• последовательность операций, выполняемых на данном оборудовании;
• информацию о корректирующих мерах.
Стандартные технические требования не входят в документацию на стандартизированную работу. Документы по инструктажу оператора описывают их лишь в том случае, если они не отражены в прочих документах, например чертежах (нет необходимости документировать уже оговоренные стандарты повторно).
Параметры работы оборудования используются для разработки методов его проверки. Такая проверка вменяется в обязанность одному из работников и представляет собой процесс, выполняемый регулярно. В Toyota такой проверкой чаще всего занимается лидер команды. Проверка состояния оборудования производится несколько раз в день через неравные промежутки времени, тем самым обеспечиваются должные условия работы оборудования. Нередко такая проверка проводится перед началом смены, а затем в течение смены в зависимости от критичности оборудования. Задача проверки перед началом смены – обеспечить, чтобы все параметры процесса находились в заданном диапазоне, а оборудование было в рабочем состоянии и готово к эксплуатации.
Информация о корректирующих мерах так же, как и требования спецификации, используется для проверки оборудования. Она содержит подробные пошаговые инструкции о мерах, которые следует предпринять в случае отказа оборудования или проблем в процессе, и включает план действий в случае непредвиденных обстоятельств, в частности определяет возможности использования альтернативного оборудования или эксплуатации оборудования в режиме ручного управления.
Спецификации обычно разрабатываются отделом организации производства или технологическим отделом. На производстве эта информация используется по мере необходимости для разработки ведомостей по производственному инструктажу. Некоторые компании путают эти технические требования со стандартной работой оператора, однако стандартные технические требования не содержат информации об отдельных операциях, временном режиме и оптимальных методах выполнения работы.