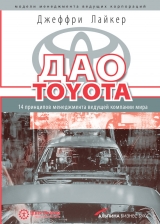
Текст книги "Практика дао Toyota. Руководство по внедрению принципов менеджмента Toyota"
Автор книги: Джеффри Лайкер
Соавторы: Дэвид Майер
сообщить о нарушении
Текущая страница: 15 (всего у книги 46 страниц) [доступный отрывок для чтения: 17 страниц]
В ведомости производительности процесса (здесь не показана) фиксируется мощность оборудования, используемого в процессе. Время цикла оборудования, т. е. количество времени, необходимое на обработку одного изделия, следует учитывать, принимая во внимание запланированные простои при смене инструмента и переналадке. В первую очередь это относится к станочным операциям, где имеет место износ инструмента и не обойтись без его замены, однако ведомость применима и к таким операциям, как литье под давлением и штамповка, где необходимо учитывать время переналадки. Такая ведомость – полезный инструмент выявления операций, представляющих собой узкие места.
Использование этого документа очень похоже на планирование загрузки производственных мощностей, которым занимается большинство инженеров-технологов при выборе оборудования. Основная цель – определить, соответствует ли мощность оборудования потребностям производства. Расчеты производятся с учетом времени полезной работы, времени цикла на единицу продукции и потерь времени при смене инструмента или иных видах переналадки.
Проблемы разработки процедуры стандартизированной работыПомимо попыток разработать процедуру стандартизированной работы, опираясь на перечисленные выше мифы, сложности возникают при попытках стандартизировать всю работу, а не ее составляющие, а также работу с большой вариацией. В большинстве случаев работа представляет собой набор задач, выполняемых одним человеком.
К примеру, задачей оператора может быть сборка какого-либо изделия. При этом он сам подбирает и доставляет необходимые материалы и подает готовые изделия на следующую операцию. Сборка изделия является относительно единообразной работой, которую несложно задокументировать, но как быть с остальными видами работ? Они осуществляются непоследовательно, иногда однократно в течение нескольких циклов. Как соединить эти два абсолютно разных вида работ в ведомости стандартизированной работы? Обычно это попросту невозможно. Элементы работы, необходимые для сборки продукта, добавляют ценность и подлежат стандартизации. Как правило, операторы в Toyota не занимаются ни подбором материала, ни транспортировкой готовой продукции, поскольку эти виды деятельности отвлекают от работы по добавлению ценности. Транспортировкой материалов и деталей занимается другой работник, например транспортный рабочий, и его работу стандартизуют отдельно.
В главах 4 и 5 мы рассказывали о необходимости изолировать вариацию, чтобы обеспечить возможность стандартизации. Следующий пример иллюстрирует сложности при стандартизации работы, которой присуща высокая вариация. Общее правило: сначала изолировать вариацию и лишь потом приступать к стандартизации.

В данном случае работа оператора представляет собой обслуживание двух автоматических резательных станков, которые нарезают и обрабатывают заготовки стального прутка.
Первая операция состоит в проверке качества и обслуживании станка (удаление металлической стружки и перемещение готовой продукции). Оператору приходится регулярно осматривать некоторое количество деталей. Такие проверки представляют собой повторяемую операцию, которая выполняется каждый час (стандартное время цикла).
Вторая операция представляет собой установку прутка. Эта работа тоже постоянно повторяется, однако время цикла варьируется в зависимости от вида изготавливаемых деталей в диапазоне от часа до двух.
Третья операция – это наладка станка и замена инструмента при его износе и при переходе с одного вида изделий на другой. Данный вид работы повторяется раз в несколько часов, а периодичность выполнения этой операции отличается высокой вариабельностью.
Таким образом, работа включает как регулярно повторяемые операции однотипного характера, так и операции, отличающиеся высокой вариабельностью времени выполнения. Когда все они производятся на одном рабочем месте, установить четкую последовательность операций, которая поддается стандартизации, невозможно. Дело осложняется тем, что каждый оператор отвечает за два станка. Если один из них нуждается в переналадке, а в другой требуется установить пруток, станок, требующий переналадки, простаивает, пока не освободится оператор. Если оба станка одновременно нуждаются в переналадке, один из них ждет своей очереди. Нередко потерянное таким образом время составляет несколько дней. Если оба станка работают и оператор занят только первой операцией, у него остается лишнее время, которое он проводит в ожидании. Получается, что при таком сценарии и станок, и оператор простаивают в ожидании.
Чтобы изолировать вариацию, было решено перераспределить выполнение операций, поручив их разным операторам. Первую задачу поручили работнику, который отвечал теперь за обслуживание и проверку качества на десяти станках. Вторую операцию – установку прутка – выполнял второй работник, который тоже отвечал за десять станков, наладкой всех десяти станков занимались еще два человека. В результате такого перераспределения обязанностей «высвободился» один оператор, что позволило создать должность лидера команды для дополнительной поддержки линии.
Еще один позитивный результат состоял в том, что теперь наладкой оборудования занимались два человека и это позволило снизить общее время наладки. Вследствие этого размеры партии снизились, повысилась частота перехода с одного изделия на другое, а общий объем запасов сократился. Благодаря появлению должности лидера команды рабочие места отсутствующих больше не пустовали, что обеспечивало стабильный выход продукции изо дня в день. Станки были оснащены сигнальной системой андон, чтобы оператор мог своевременно установить новые заготовки и станок не простаивал. Кроме того, сигнал андон оповещал оператора о том, что в ближайшее время понадобится наладка станка или смена инструмента. Такие сигналы позволяли операторам заранее подготовить необходимый материал и инструменты. В результате преобразований общая производительность процесса возросла на 30 %.
Аудит стандартизированной работыКак уже говорилось выше, распространен миф о том, что описание стандартизированной работы должно висеть на видном месте, чтобы оператор мог сверяться с ним, выполняя свою работу. На предприятиях Toyota такое описание обычно вывешивается в проходе, а не перед оператором, поскольку в первую очередь эти сведения интересуют лидера команды и лидера группы, которые проверяют соблюдение стандартов.
Но разве аудиты не означают, что менеджмент использует принудительные меры, а сама стандартизированная работа представляет собой проявление бюрократической косности? В обстановке враждебности любые проверки порождают конфликты и напряжение. Однако в условиях, где первоочередное внимание уделяется устранению потерь для лучшего обслуживания потребителя, аудиты стандартизированной работы служат средством поддержания стабильности процесса. Они объединяют менеджмент и рабочих. Операторы часто отклоняются от стандартной процедуры, когда видят проблемы и ищут «обходные пути». Аудит со стороны менеджмента обеспечивает выявление коренных проблем и их оперативное исправление, что позволяет возобновить работу в соответствии со стандартом.
ПОДСКАЗКА
Чтобы привыкнуть к новому методу, нужно время
Изменение метода работы (стандартизированная работа) требует времени на адаптацию. Расстаться с прошлым бывает непросто, поскольку наше тело продолжает действовать по привычке. Так, если вы сменили автомобиль с механической коробкой передач на машину с АКПП, какое-то время ваша рука будет непроизвольно тянуться к рычагу переключения передач (не обнаруживая его на прежнем месте!). Пока оператор не адаптируется к новому методу, следует оказывать ему постоянную поддержку.
Аудит в Toyota могут инициировать два обстоятельства. Первое – проблема. Что стало причиной дефекта? Почему оператор систематически отстает? Часто наблюдение за оператором на протяжении нескольких циклов и сравнение его действий со стандартной процедурой работы позволяет выявить истоки проблемы. Второе – настало время аудита. Наряду с графиком профилактического обслуживания в Toyota существует график аудитов рабочих стандартов. Чтобы провести профилактический ремонт, в Toyota не ждут, пока станок сломается. Точно так же необязательно ждать, пока оператор допустит ошибку, чтобы проверить, соблюдается ли процедура стандартной работы.
Аудит позволяет выявить отклонение от стандартного метода. Мы часто ошибочно полагаем, что отклонения случаются по вине оператора. Разобравшись, в чем дело, мы можем обнаружить, что причиной отклонения была неисправность оборудования или проблема с продуктом. Смысл проверки в том, чтобы найти причину проблемы и устранить ее.
На многих предприятиях Toyota существует визуальная система для проверки соблюдения стандартов. Каждая рабочая группа использует доску визуального отображения информации с карточками, которая называется «доска камисибай» (книга историй). На заводе NUMMI лидеры групп каждый день проверяют соблюдение требований стандартизированной работы и точность документов по стандартизированной работе в одном из процессов. Это позволяет за месяц проверить каждое рабочее место. При этом на карточке, которая содержит перечень вопросов, помечается, какие отклонения были выявлены и какие меры приняты. На доске предусмотрено специальное гнездо для карточек по каждому процессу. После проверки карточка в порядке очередности аудитов помещается в свободную прорезь соответствующего гнезда. Если в ходе аудита обнаружена проблема, карточка вставляется в прорезь темной стороной наружу – это служит сигналом к принятию мер. Заместители менеджеров ежедневно проверяют доски, чтобы удостовериться, что аудит проведен должным образом. Они наугад вынимают одну из карточек и проверяют соответствие процесса стандартизированной работе совместно с лидером группы. В заводских цехах находится около 90 таких досок.
Сравните эту ситуацию с практикой множества компаний, которые «применяют» стандартизированную работу. Карта стандартизированной работы заполнена по всем правилам и вывешена на видном месте, скорее всего, инженером по организации производства. Порой эти карты оформлены очень красиво и даже содержат фотографии отдельных операций. Они повешены так, чтобы их видел оператор. Этими картами никто не пользуется, зато их можно продемонстрировать посетителям, которые скажут: «Это похоже на бережливое производство».
Стандартизированная работа как базис непрерывного совершенствованияПосле первоначальной стандартизации операций начинается самое интересное. Пришло время спросить: «Каковы дальнейшие возможности?» Теперь ответ дать труднее. Мы должны заново переосмыслить нашу основную цель – выполнять больше работы, добавляющей ценность, с меньшими затратами, иными словами, изготавливать больше изделий, расходуя меньше ресурсов. Не спешите браться за дальнейшие совершенствование. Сначала давайте разберемся, что мы будем делать с нашими достижениями. Важно сориентировать совершенствование на потребности, а не просто заниматься им потому, что оно возможно. Совершенствование как таковое возможно всегда!
К примеру, если вы намерены и дальше сокращать время наладки, что вы будете делать с освободившимся временем? Важно ли вам уменьшить размер партии, повысить гибкость, или вы заинтересованы в наращивании объема? Нередко мы видим компании, которые берутся за сокращение времени наладки, добиваются ощутимых результатов, но не знают, куда девать освободившееся время, и продолжительность наладки мало-помалу возвращается на исходный уровень. Тот же феномен отмечается и при прочих «усовершенствованиях». После усовершенствования вы должны перестроить процесс таким образом, чтобы поддержание достигнутого уровня стало условием дальнейшего успеха. Более высокий уровень должен стать новым стандартом, а от лишнего нужно избавиться. Если в поддержании нового уровня нет необходимости, любые достижения быстро сойдут на нет.
Время такта как расчетный параметрПОДСКАЗКА
На освоение нового стандарта требуется время
Пока люди привыкают к новому методу, производительность нередко слегка снижается. Не спешите возвращаться к прежним методам. Продолжайте наблюдать за происходящим, следя за тем, чтобы работники придерживались нового метода, а любые необходимые поправки вносились немедленно.
Многие затрудняются определить, чем отличается время такта от времени цикла. Время такта – это не инструмент. Это понятие используется при планировании работы и описывает темп потребительского спроса. Чтобы рассчитать данный показатель, нужно разделить время, отведенное на производство изделий, на число изделий, которое запросят потребители в течение данного временного интервала. Полученный результат может, к примеру, говорить о том, что для удовлетворения потребительского спроса каждые три минуты нужно изготавливать одну деталь. Просто? Тем не менее время такта часто понимается неправильно. А определение времени такта для линий, производящих множество разных продуктов, темпы спроса на которые различны, превращается в весьма мудреную задачу.
Рассмотрим такой пример: если рабочее время в течение одной смены составляет 400 минут, а спрос составляет 400 изделий за смену, время, которое отводится на единицу продукции (время такта), составляет одну минуту (на каждое изделие). Чтобы удовлетворить спрос, время цикла каждой операции в среднем не должно превышать одну минуту. Если время цикла (фактическое время, которое требуется для выполнения всех действий по одной работе) превышает время такта, данная операция станет узким местом и, чтобы уложиться в график, придется работать сверхурочно. Если время цикла меньше, чем время такта, возникнет перепроизводство или ожидание.
Самая трудная задача – определить потребительский спрос. В большинстве случаев (если вы не поставщик Toyota) спрос имеет значительные колебания. Как определить время такта, если спрос – величина непостоянная? Следует понимать, что время такта служит «точкой отсчета» при планировании работы, и легко представлять, каковы могут быть последствия неправильного определения точки отсчета.
Первым делом следует признать, что время цикла отдельных операций – время, необходимое для выполнения работы, – колеблется не слишком сильно, если они стандартизированы. В примере, который приводился выше, цикл работы оборудования составляет 23 секунды, а время работы оператора и время на ходьбу – 56 секунд. Общее время цикла составляет 75 секунд и может незначительно колебаться в зависимости от скорости работы оператора, который подготавливает детали для автоматической сварки. Это значит, что производительность данного процесса будет достаточно стабильной при отсутствии сбоев, вызванных отказами оборудования. Какое влияние оказывают на данную операцию значительная вариация спроса? Никакого! Время рабочего цикла может варьироваться лишь в пределах нескольких секунд. Как удовлетворить спрос, если он растет? Можно увеличить рабочее время (например, за счет сверхурочной работы, если спрос растет не слишком сильно). Использование понятия времени такта не изменит сложившуюся ситуацию.
Так как же определить спрос и время такта? Выберите показатель спроса, который будет достаточно высок, чтобы потребность была удовлетворена большую часть времени. Допустим, к примеру, что спрос колеблется в диапазоне от 10 000 до 20 000 единиц продукции в месяц, а средний показатель составляет 16 000 единиц в месяц. Какое число следует выбрать? Отчасти это зависит от ситуации, но обычно мы рекомендуем ориентироваться на более высокий показатель. И вот почему. Предположим, что мы используем максимальный показатель – 20 000. Рассчитывая время такта, мы получим при этом более низкий показатель (на изготовление единицы продукции отводится меньше времени). Затем сравниваем время цикла и время такта для выявления расхождения. Смысл такого расчета в том, что чем значительнее расхождение, тем больше требуется усовершенствований, чтобы достичь времени такта, а потенциал совершенствования определяется объемом потерь в процессе.
Сталкиваясь с подобной задачей, сэнсэй Toyota скажет: «Нет проблем», имея в виду, что потерь всегда предостаточно и добиться необходимого усовершенствования, несомненно, можно. Единственная опасность завышения темпов спроса в том, что в этом случае придется потратить больше сил, чтобы выйти на заданное время такта. Вряд ли вам захочется тратить силы впустую, искусственно завышая показатель спроса (тем самым снижая время такта), но это не столь уж серьезная проблема. Если процесс усовершенствован сверх фактической потребности, можно сократить объем ресурсов или заняться расширением продаж.
Время такта определяет единый ритм выполнения всех операций в потоке создания ценности. График загрузки операторов представляет собой действенный визуальный инструмент, который позволяет увидеть соотношение между временем цикла и такта. В некоторых случаях она помогает ответить на вопрос «А что, если?» в отношении потенциальных возможностей процесса. На рис. 6–8 представлен график загрузки операторов, составленный для сравнения времени цикла отдельных операций в потоке создания ценности со временем такта. В данном случае компания хотела увеличить объем производства, чтобы удовлетворить возросший по приблизительным оценкам спрос. В компании хотели знать, насколько значительные изменения потребуются, чтобы выйти на гипотетическое время такта 90 секунд на изделие. Мы видим, что пока в заданное время такта не укладываются две операции.


Если две эти операции будут оптимизированы, какой объем усовершенствований необходим, прежде чем будет достигнуто следующее «плато» выравнивания? На рис. 6–9 обозначено следующее «плато». Несколько операций имеют время цикла около 60 секунд. Если сократить время цикла двух самых продолжительных операций до 60 секунд, это позволит потоку создания ценности выдавать одно изделие каждые 60 секунд. Означает ли это, что нужно немедленно взяться за решение данной задачи? Если мы решим ее, несмотря на то что время такта, рассчитанное с учетом фактического спроса, превышает 60 секунд, мы придем к перепроизводству – основному виду потерь.
После сокращения времени цикла двух самых продолжительных операций стало понятно, что фактическое время такта, необходимое для удовлетворения спроса, составляет 80 секунд. Это позволило произвести перегруппировку операций и сократить их число. В нашем случае после сокращения времени шлифовки и полировки общая продолжительность всех операций составила 645 секунд. Если разделить 645 секунд рабочего времени на время такта 80 секунд, мы получим восемь операций с соответствующим временем такта вместо исходных 12. Таким образом, за счет перегруппировки мы можем сократить количество операций на треть, обеспечив время такта 80 секунд. Если речь идет о процессах ручного труда, это означает высвобождение 4 операторов (примечание: эти «лишние» операторы могут быть использованы для создания системы лидеров команд, описанной в главе 10). Интересно отметить, что, если сбалансировать операции, ориентируясь на менее продолжительное время такта 60 секунд, понадобится 11 операторов (645 / 60 = 10,75). Таким образом, повышение скорости может обойтись дороже.
Учитывайте время такта при планировании работы и выборе необходимых усовершенствований. Если вы выбрали слишком большое время такта, вы не удовлетворите спрос, а это хуже, чем выбрать слишком маленькое время такта и превысить спрос (при условии, что для удовлетворения ошибочно определенного спроса вам не понадобилось привлекать дополнительные ресурсы). Всегда проще остановить производство при избыточной производительности, чем увеличить объем производства при недостаточной производительности. Если вы сомневаетесь, лучше ориентироваться на более высокие показатели спроса и меньшее время такта.
Важность визуального контроляПрименение средств визуального контроля – важнейший момент в процессе стандартизации. К сожалению, значение этой составляющей бережливого процесса очень часто недооценивается. Мы нередко слышим: «Они всего-навсего занимаются 5S». Возможно, виной тому примеры средств визуального контроля, которые приводятся чаще всего, скажем разметка пола, которая показывает, где должны стоять контейнеры с мусором и прочие объекты в рабочей зоне. Работники считают подобную разметку лишней – они ведь и так понимают, где что находится! Другой пример – значки, обозначающие место для различных предметов и видов материала. «Мы и так знаем, что и куда класть». Однако когда работника просят рассказать более подробно, например описать процесс поставки материала, назвать его стандартное количество или допустимый минимум и максимум запасов, обычно ответы становятся менее вразумительными.

На рис. 6-10 показано, что средства визуального контроля предназначены прежде всего для того, чтобы определить желаемое «нормальное» состояние (стандарт) и быстро заметить отклонение от стандарта. Как мы видели, на каждом рабочем месте требуется соблюдать массу технических условий и процедур. Добиться того, чтобы каждый работник знал их наизусть, практически невозможно, и даже если записать их в тетрадку, это не поможет немедленно вспомнить их при необходимости.

Нередко люди настолько убеждены, что знают стандарты, что любое визуальное напоминание кажется им излишним. Оценить подлинное знание стандартов несложно. Попросите нескольких работников описать конкретный метод выполнения работы. Есть ли возможность установить, что все делается, как положено? Ситуация на окрасочном участке, описанная ниже, говорит о том, что, если возможность быстро оценить соблюдение стандарта отсутствует, отклонения не замечаются и не прекращаются.
Вот что происходит, когда стандарт всем известен, но не визуализирован.
