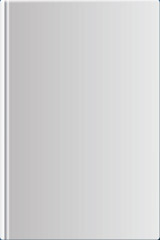
Текст книги "Отечественные автоматы (записки испытателя-оружейника)"
Автор книги: А Малимон
Жанры:
Прочая документальная литература
,сообщить о нарушении
Текущая страница: 35 (всего у книги 40 страниц)
Инструментом, обеспечивающим необходимый профиль канала ствола и патронника, является оправка, изготовленная из твердого сплава ВК-20, со спиральными выступами на цилиндрической поверхности и утолщением на конце с наружным профилем по форме патронника ствола. Цилиндрическая часть оправки длиною 40 мм в поперечном сечении представляет собою зеркальное изображение профиля канала ствола.
Нарезной канал и патронник при редуцировании образуются в результате обжатия металла вокруг инструмента – оправки при высокочастотной ковке ствольной заготовки двумя парами симметрично расположенных бойков. Число ударов в одну минуту – 1200. Максимальная степень обжатия металла по канальной части ствола около 40 %.
Регулируемая скорость подачи заготовки в ковочной машине SHK-10 обеспечивалась в пределах от 0 до 36 мм/сек. Осевое вращение заготовки – 40–60 об/мин. Оптимальный режим в пределах 52–56 об/мин.
Редуцированный канал ствола и патронник по своей чистоте не требовали дополнительной обработки перед хромированием. Включение на непродолжительное время «обратного тока» для очистки и некоторого разрыхления поверхности в целях повышения ее адгезионной способности при наложении хрома сливалось с операцией хромирования.
Первая партия ковочных машин SHK-10 группой специалистов Ижевского завода принималась у австрийской фирмы GFM в период с сентября по декабрь 1971 года. Зам. главного механика завода И.Ф. Зуев со своим помощником М. Мусиным, зам. главного технолога Б.Н. Андреев и ведущие специалисты этой службы В.С. Письменский, В.А. Никитин и Л.Ф. Мокрушин в течение этого времени производили не только техническую приемку машин, но и участвовали в отработке технологии ковки стволов АКМ. Одновременно производилось и уточнение чертежа на ствол с учетом технических возможностей ковочной машины, которая также в процессе сдачи заказчику дорабатывалась.
Был момент, когда фирма была не в состоянии удовлетворить требования Советской стороны в точности исполнения чертежных размеров по канальной части ствола и патроннику, считая их чрезмерно жесткими.
В разгар конфликта, когда был начат разговор о возможном расторжении контракта, В.А. Никитину – главному специалисту по канальной части ствола, пришлось возвращаться на свой завод для изучения возможностей изменения требований чертежа на ствол с учетом предложений австрийской стороны и согласования их со своим заказчиком.
Согласие заводских служб на изменение чертежа, не получившее пока еще одобрения внешних испытательных организаций, касалось изменения допусков на точность изготовления 4 и 5-го конусов патронника ствола в связи с местным непроковом в переходной части, (увеличения допуска примерно на 0,02 мм), а также скругления полей нарезов канальной части ствола.
После приемки первой партии ковочных машин SHK-10 руководители фирмы GFN отметили, что впервые встретились с такой строгой требовательностью приемщиков, вследствие чего конструкция машин будет улучшена.
Были также разговоры о том, что только в России существует строгий прямоугольный профиль нарезов оружейных стволов, что в других странах он делается более плавным.
После приемки в 1977 году второй партии ковочных машин у австрийцев на одной из них с согласия советской стороны была произведена опытная, ковка стволов калибра 4,5 мм для фирмы «Koval Arms» (Великобритания) с положительными результатами.
На Ижевском заводе австрийские ковочные машины стали осваиваться в 1972 году, первоначально на стволах калибра 7,62 мм для системы АКМ. Освоение производилось той же группой приемщиков машин у австрийцев под руководством главного инженера завода Б.Ф. Файзулина, являвшегося и главным инициатором внедрения ковочной ствольной технологии в массовое производство, его заместителя О.И. Собина и главного технолога М.И. Миллера.
Своевременное освоение нового прогрессивного метода нарезания стволов в массовой технологии имело весьма важное значение для дальнейшего технического развития оружейного производства.
Первые стволы, изготовленные по новой технологии, по боевым качествам показали вполне обнадеживающие результаты, однако в ходе освоения выявилась необходимость корректировки данного процесса и внесения некоторых дополнительных конструктивных изменений по стволу.
Для обеспечения возможности редуцирования произведено уточнение режима термообработки ствольной заготовки с учетом упразднения подкалки казенной части ствола на более высокую твердость. По длине ствола произведено выравнивание твердости. На утолщенной казенной части твердость понижена, а на остальном участке она несколько повышена. С учетом положительного опыта электрогидравлического нарезания стволов в чертеже произведено скругление внутренних и наружных углов нарезов радиусом 0,8 мм.
Процесс редуцирования в результате наружного обжатия заготовки при ковке оставляет в канале остаточные напряжения противоположной дорнированию реактивной направленности. Эта особенность редуцирования, как и при дорнировании, должна была учитываться при выполнении технологических операций по наружной механической обработке ствола.
Применение редуцирования, даже с учетом свойственной этому процессу недостаточно четкой проковки последних конусов патронника в зоне перехода к нарезной части, не сказалось на изменении прочностных, баллистических и боевых характеристик ствола, включая и большие перепады температур окружающей среды.
Но некоторые сомнения в этом все же возникали. Связанные с этим дополнительные сравнительные испытания автоматов с редуцированными и дорнированными стволами в специализированных исследовательских организациях подтвердили ранее сделанные выводы в пользу редуцирования (арх. 900-73).
Редуцирование каналов стволов с одновременным изготовлением патронника дало снижение трудоемкости изготовления этой детали по сравнению с дорнированием канала и изготовлением патронника путем обработки металла резанием примерно на 40 %. Не страдало при этом и качество изготовленных стволов, боевые свойства и эксплуатационная долговечность.
Применение редуцирования сокращало потребности в производственных площадях по ствольному участку, при этом повышалась и общая культура производства. Но не только в этом состоят преимущества данной технологии. Снижение трудоемкости изготовления ствола на 40 % не являлось высшим предельным достижением данного процесса в области технологий.
В условиях уменьшения калибра оружия, когда трудоемкость обработки канальной части ствола прежними методами резко возрастает, в не меньшей мере возрастает и преимущество редуцирования.
При определенных условиях оно может оказаться единственным методом изготовления стволов малого калибра без особых технологических сложностей.
Это показали предпринятые в конце 60-х годов поиски рациональной технологии изготовления стволов калибра 5,60 (5,45) мм. Полученный на Ижевском заводе при освоении редуцирования стволов АКМ технологический опыт, который был первым в отечественном оружейном производстве стволов среднего калибра, послужил базовой основой для проверки возможности применения этого метода и к стволам малого калибра.
Стволы калибра 5,45 мм. Первоначально этот калибр в перестволенных автоматах АКМ имел цифровое значение 5,60 мм, как диаметр канала, измеряемый по дну нарезов. В дальнейшем при перерасчете на диаметр по полям он перевоплотился в калибр 5,45 мм, каким он стал известен по автомату АК-74.
Многие оружейники и патронщики считали, что калибр 5,6 мм целесообразно было бы оставить без изменений, только считать его диаметром канала ствола не по нарезам, а по полям, как во всем оружии. Это создавало бы лучшие возможности для разработки пуль специального назначения.
Широкими технологическими исследованиями, проведенными на Ижевском заводе (И.А. Самойловым и В.А. Никитиным) в конце 60-х годов с участием организаций В.М. Сабельникова и В.И. Лазарева (инв. 5044-70), установлено, что из всех известных способов получения нарезов (строжка шпалером, дорнирование, редуцирование и ЭГН) лучшими и примерно равноценными между собой являются редуцирование и электрохимическое нарезание (ЭХН, ранее именовавшееся ЭГН). Поиски лучшей технологии и опыт изготовления первых партий стволов калибра 5,45 мм, предназначенных для новых автоматов различных конструкций, обнаружил резко возросшие по сравнению с калибром 7,62 мм технологические трудности выполнения операций по механической обработке глубокого канального отверстия.
Более трудоемкой с увеличением затрат времени стала операция правки стволов вследствие ухудшения видимости теневого треугольника в узком канале, обозначающего нарушение прямизны детали. В связи с уменьшением диаметра обрабатываемого отверстия соответственно снизились и прочностные качества канального инструмента (сверл, разверток, шпалеров, шустов), его жесткость и эксплуатационная долговечность. Наиболее резкие проявления и связанные с этим технологические трудности имели место при сверлении первоначального отверстия диаметром 4,8 мм, где стойкость инструмента в связи с увеличением продольных и крутильных колебаний была особенно низкой.
Снижало это и рабочую подачу инструмента. Увеличилась опасность поломки сверл из-за закупорки отверстий стружкой, что требовало повышенного внимания при наблюдении за процессом сверления. Это исключало возможность многостаночного обслуживания. Частая смена инструмента, ухудшенные условия отвода стружки не только снижали производительность технологических операций, но и косвенно влияли на качество обработки отверстий.
Поломки инструмента были свойственны и технологии сверления глубоких отверстий диаметром 6,45 мм под операцию дорнирования стволов калибра 7,62 мм, где по технологии предусматривалась специальная операция по удалению поломавшихся сверл примерно у 5 % ствольных заготовок.
Но при диаметре отверстия 4,8 мм поломки сверл существенно участились с одновременным увеличением и затрат времени на извлечение обломков инструмента из ствола.
Гладкая строжка, применявшаяся для улучшения чистоты канала и выравнивания его геометрических размеров, отличалась крайне низкой производительностью для стволов любых калибров, а калибра 5,45 мм в особенности.
Сверление отверстия диаметром 9,1 мм с последующей обработкой гладкого канала до размера 10,2 мм под редуцирование было куда проще.
Трудоемкость канальных операций по стволам калибра 5,45 мм применительно к процессу редуцирования по сравнению с технологией дорнирования стволов АКМ калибра 7,62 мм была меньше примерно на 60 %.
Метод одновременного редуцирования канала ствола и патронника был признан наиболее приемлемым для массового производства стволов. Он обеспечивал достаточно высокую точность получаемых размеров, исключая некоторые погрешности по 4 и 5-му конусам патронника, не оказывающие влияния на эксплуатационные качества оружия.
Качественное состояние канального отверстия не уступало ЭХН. Снижение трудозатрат по сравнению с методом ЭХН обеспечивалось более чем в 1,5 раза.
Положительный опыт освоения редуцирования в ствольном производстве был использован Б.Ф. Файзулиным и В.С. Письменским при переводе на процесс редуцирования изготовление корпуса дульного тормоза автомата АК-74 из сортового трубчатого проката. Это снизило общие затраты массового производства на изготовление дульного тормоза примерно на 50 %.
Истории поисков рациональной технологии изготовления автоматных стволов начала 50-х годов известна также попытка применения прессованных заготовок с наличием гладкого канального отверстия, образованного методом прессования горячего металла. Применение такой заготовки исключало из технологического процесса глубокое сверление канального отверстия.
Способ получения прессованной заготовки разработан в технологическом институте инженером Залесским. Сущность ее прессования заключалась в продавливании горячего металла из закрытого объема через отверстие (очко) штампа. Для образования канального отверстия на конце пуансона имеется оправка, входящая в сечение очка до начала выдавливания из него металла.
Серией технологических опытов и проведенными испытаниями «установлена принципиальная возможность применения полых заготовок для изготовления стволов» (арх. 2224-51, стр. 230). Изготовленные из прессованных заготовок стволы на завершающем этапе отработки данной технологии по своим баллистическим характеристикам, прочности и живучести не уступали стволам, изготовленным по штатной технологии (арх. 2440-51, стр. 14).
Полигоном они были рекомендованы «для проверки технологичности (в процессе изготовления серийной партии) и более широких испытаний служебных качеств» (арх. 2771-53, стр. 138).
В ходе производства в стволах из прессованных заготовок обнаруживались отдельные дефекты по канальной части, трудноустранимые технологией.
С учетом этого фактора, а также в связи с развернувшимися работами по совершенствованию штатной и созданию других новых технологий, работы по прессованным заготовкам в то время не получили дальнейшего развития.
Хромирование деталей
Всего две детали автомата подвергались хромированию – ствол по канальной части и патроннику и шток, главным местом которого был газовый поршень. Отработка технологии хромирования этих деталей потребовала значительного объема экспериментальных исследований с пропуском через поточное производство больших опытных партий деталей с тщательным контролем технологических процессов, производством многочисленных осмотров и измерений.
Повышение толщины покрытия канала ствола являлось в то время одним из общепризнанных способов повышения прочности и износоустойчивости хромового слоя, особенно хорошо зарекомендовавшим себя на стволах крупного калибра.
Многолетний опыт хромирования оружейных стволов показывал, что свойства хромового покрытия с увеличением его толщины значительно изменяются в сторону улучшения. Уменьшается пористость, улучшаются защитные свойства хрома как антикоррозионного покрытия, повышается способность против износа и эрозии.
При многослойном хромировании, по мнению некоторых гальванистов, качество покрытия должно было дополнительно улучшаться и за счет предполагаемого уменьшения напряжения в хроме, однако на стволах калибра 14,5 мм этого преимущества не выявлено (арх. 461-56).
В отечественной оружейной практике повышение живучести стволов за счет повышения толщины слоя хрома до 0,4 мм на диаметр достигнуто на 7,62-мм станковом пулемете Горюнова (СГМ), работающем по сравнению с автоматом в более жестком эксплуатационном режиме, но… в сочетании с дорогостоящей высоколегированной ствольной сталью 30ХНВФА, содержащей хром, никель, ванадий, молибден, вольфрам.
Проблема повышения живучести пулеметных стволов на заводе А.А. Дементьева была решена в результате многолетних поисковых работ, проводившихся технологами данного предприятия с участием многих научно-исследовательских организаций. В результате этих работ живучесть ствола СГМ, составлявшая ранее 30–40 % от установленной минимальной нормы, была повышена в 3–4 раза.
Но применение дорогостоящей стали для стволов автоматов, изготовлявшихся в несравненно больших количествах и почти вдвое меньшими нормами живучести системы по сравнению с пулеметом СГМ, было непозволительной роскошью. Заимствование опыта пулеметного производства в решении указанной ствольной проблемы по автомату экономически не оправдывало себя.
По стволам автоматов продолжался поиск иных путей повышения прочности химпокрытия. Но заводом предпринималась также не увенчавшаяся успехом попытка избавиться от дефектов хромирования путем упразднения самого хрома. За счет применения другой марки стали (45Х), хорошо работающей на истирание, мало подвергающейся коррозии и хорошо поддающейся механической и термической обработке (арх. 2099-49, стр.129). С металлургической стороны эта сталь мало отличалась от обычной углеродистой стали 50А, применявшейся в ствольном производстве.
Полигонные испытания показали снижение живучести стволов, и работы по этой стали были прекращены. Возможность продолжения работ в данном направлении со стороны ГАУ не исключалась.
Исследования по стволам автомата без химпокрытий канала получили свое продолжение в 70-х годах в поисках Ижевских металлургов высокопрочного и жаростойкого материала для тонкостенного леинирования канальной части стволов малого калибра.
Сколы и шелушения хрома буквально терзали производство АК-47 с самого начала его организации. Скрашивания хрома на дульной части ствола обнаруживались после первых же технологических испытаний стрельбой (арх. 181-51). До 1950 года процесс хромирования ствола длился 95-120 минут и наслоение хрома при этом составляло 0,08-0,13 мм на диаметр.
При такой толщине хрома была значительная отбраковка стволов и готовых автоматов по дефектам хромового покрытия. Исправляемый брак по сколам хрома в дульной части достигал 80 %. Исправление стволов согласно протокольным Решениям Управлений ГАУ и Министерства производилось путем дополнительной подрезки и закругления дульной части ствола по канальному отверстию.
Предупредительные попытки ликвидировать данный брак за счет изменения геометрии дульного среза ствола и улучшения качества механической обработки положительных результатов не дали.
В результате наблюдения за сколами хрома в процессе испытаний автоматов на живучесть, проведенных по данному вопросу специальных исследований, а также учета опыта эксплуатации другого автоматического оружия с хромированными стволами заводом совместно с институтом Ф. А. Куприянова был сделан вывод о возможности уменьшения толщины хрома до 0,04-0,06 мм без опасности снижения живучести ствола и ухудшения коррозионной стойкости покрытия канала. По результатам сравнительных испытаний стволов с различной толщиной хрома тонкослойное хромирование было внедрено в производство.
В результате улучшилось качество поверхности хромового слоя, равномернее стало наслоение хрома по каналу, резко сократилась отбраковка стволов по сколам хрома на дульном срезе, в 1,5–2 раза сократилось время хромирования. Одновременно с этим сократилось время расхромирования и повторного хромирования при исправлении брака по хрому.
Были трудности и в отработке технологии хромирования штока рамы, в частности, поршневой его части. При отложении хрома 0,02-0,03 мм на цилиндрической части поршня, на его торцё откладывался хром толщиною 0,005-0,01 мм, что оказалось недостаточным для обеспечения долговечности покрытия в требуемых нормах.
По торцу поршня хром скалывался и разрушался с образованием прогаров на поверхности в виде темных точек. Увеличение толщины покрытия и раздельное хромирование цилиндрической и торцевой части поршня положительных результатов не дали (арх. 2224-51, стр. 227, арх. 199-50).
Приемлемым оказалось одновременное хромирование всего поршня в один прием, при этом его торец должен был хромироваться только по краям узкой ленточкой. Рациональным оказалось изменение профиля кольцевых канавок поршня. Полукруглые канавки, пришедшие на смену прямоугольному профилю, обеспечили улучшение подготовки поверхности под хромирование, равномерное без наростов наслоение хрома, а также облегчили чистку детали при эксплуатации.
Однако установление оптимальных значений по толщине хромового покрытия еще не определяло нормального хода технологического процесса хромирования. За этим следовал длительный и трудоемкий процесс отработки размерного хромирования со всеми сложностями обеспечения четкого сочетания и соответствия размерных характеристик деталей до и после хромирования, обеспечивающих необходимую точность окончательных выходных размеров. Особые трудности возникали по канальному отверстию ствола и патроннику, у которых более 15 размеров подвергались искажению после нанесения хрома.
Размерное хромирование стволов
Этот термин в исследовательской оружейной практике начала 50-х годов стал фигурировать впервые. Требование по хромированию поверхности деталей до 200 микрон на сторону при допуске на отклонение толщины слоя 5 микрон у многих работников промышленности вызывало недоумение.
В литературе по гальванопластике того времени отсутствовали сведения о размерном хромировании, а следовательно, и само понятие об этом процессе. Многим размерное хромирование представлялось таким процессом, при котором выход годных деталей из хромировочных ванн составляет 95-100 % и не требует дополнительных операций но доводке деталей до нужного размера (шлифовка, дохромирование и т. п.).
Московские заводы «Калибр», ЗИС и другие предприятия размерным хромированием называли освоенный ими процесс покрытия гальваническим хромом наружной поверхности деталей несложного профиля (пробковые калибры, кольца и т. п.) слоем 8-10 микрон с точностью в 2 микрона со средним выходом годных деталей 90–95 %.
В оружейной технологической практике после проведения специальных исследовательских работ и отработки технологий размерным хромированием стали называть «такой процесс, при котором в гальванической ванне по заданному времени хромирования получают заданную толщину хромового покрытия» (арх. 461-56).
Необходимыми условиями размерного хромирования являются стабильность состава электролита и режима хромирования (плотность тока, температура, время). При освоении хромирования каналов стволов требовалось уделение особого внимания износоустойчивости, эрозионной и антикоррозионной стойкости электролитического хрома, его сцепляемости со сталью и другим физико-химическим и прочностным характеристикам, а также учет специфических особенностей хромирования внутренней полости отверстий.
При хромировании отверстий в отличие от наружных поверхностей деталей межэлектродное пространство ограничено размерами самих изделий, что обуславливает применение внутренних анодов также ограниченных размеров.
Одной из основных особенностей хромирования стволов является то, что вследствие низкой рассеивающей способности хромовых электролитов отложение хрома по сечению канала, с прямоугольным профилем нарезов в особенности, происходит неравномерно.
Интенсивное отложение хрома идет на выступах (при толстослойном хромировании с образованием наростов), пониженное – в углублениях (арх. 777-54). В середине поля хром отлагается меньше, чем на углах полей, по дну нареза – больше посредине и меньше в углах у граней полей.
Заводским опытом установлено, что для стволов системы АК толщина хрома по дну нарезов примерно на 0,02 мм меньше, чем на полях. Эта неравномерность отложения хрома особенно заметна при толщине более 0,1 мм, поэтому при толстослойном хромировании профилю канала ствола требуется уделять повышенное внимание.
Свойством хромированной поверхности ствола, толстым слоем хрома в особенности, является и то, что на нем, благодаря более высокой отражательной способности света, по сравнению со сталью более четко высвечиваются дефекты механической обработки подхромной поверхности.
Едва заметные до хромирования дефекты поверхности канала ствола на осажденном хромовом слое становятся более рельефными и подчеркнутыми, причем тем сильнее, чем толще слой хрома. Следовательно, подготовка поверхности под толстое хромирование требует также повышенного внимания (арх. 435-54).
Наряду с положительными свойствами электролитического хрома, при специальных исследованиях (арх. 403-52) выявлен такой его недостаток, как хрупкость и склонность к скалыванию, а также необратимость объемных превращений после первого нагрева с резким увеличением коэффициента линейного расширения и последующей усадкой хрома (0,49 %) после охлаждения. Дальнейшие циклы нагрева и охлаждения уже не изменяют коэффициента линейного расширения и не вызывают усадки хрома.
Свойства электролитического хрома, специфические особенности хромирования не гладких (профильных) отверстий, выявленные в процессе пропуска больших экспериментальных партий стволов по полному производственному циклу, необходимо было строго учитывать не только при отработке рационального профиля нарезов и назначении толщины хрома, но и при разработке приемлемой технологии размерного хромирования стволов.
Отработка размерного тонкослойного хромирования стволов того же калибра и под тот же патрон проводилась одновременно и на других предприятиях оружейной отрасли с учетом конструктивных особенностей изготовляемых изделий.
В связи с тем, что выход годных стволов из хромировочных ванн на разных предприятиях был разным, а долговечность хромового покрытия не отличалась высокой стабильностью, потребовалась разработка унифицированной технологии, учитывающей положительный опыт и потребности каждого из предприятий. Главным связующим звеном между предприятиями и основным разработчиком такой технологии был институт Ф.А. Куприянова (арх. 435-54).
Внедрение в производство согласованной на межзаводском совещании в 1954 году унифицированной технологии сопровождалось проведением дополнительных исследований и внесением отдельных уточнений, учитывающих специфику каждого из производств.
Неизменными и постоянными согласно рекомендации Головного разработчика должны были оставаться состав и температура электролита, рабочая плотность тока, соответствие электропроводностей анодов и электролита и некоторые другие условия хромирования.
Унифицированная технология в отличие от штатной предусматривала лучшую химическую подготовку канала ствола под хромирование за счет обезжиривания детали в горячем щелочном растворе и последующего травления в 8-16 %-м растворе соляной кислоты.
Были внедрены также электроизмерительные приборы для контроля электропроводности анодов и хромовых электролитов. По производству автоматов АК-47 отработка технологии хромирования стволов производилась с участием специалистов-технологов: Я.С. Гамзон, Л.Я. Буровой, И.А. Самойлова, С.М. Положенского, П.М. Стихно, П.Ф. Башкирова, М.В. Клитина, А.К. Сергеева, В.И. Азиатцева (арх. 777-54).
Ими проведен большой комплекс исследований по уточнению и нормализации режимов хромирования, изучению причин образования браковочных дефектов и поиску путей их предупреждения, а также большой объем работ по оснащению хромировочного участка необходимым технологическим оборудованием.
По результатам пропуска первых опытных партий стволов в целях снижения брака по отдельным видам канальных дефектов, связанных как с качеством хромирования, так и с механической обработкой подхромной поверхности, а также применением свинцевания после хромирования (царапины и штрихи от трения тягла стального прутка по поверхности канала) разработаны дополнительные мероприятия по совершенствованию унифицированной технологии. Устранение неравномерности наложения хрома по длине канала ствола достигалось за счет совершенствования хромировочного оборудования и установления соответствия между проводимостью анода (стального освинцованного прутка диаметром в 2–3 раза меньше диаметра отверстия) и проводимостью электролита.
В целях повышения точности получения канальных размеров после хромирования ужесточены допуски на размерные характеристики ствола при механической обработке, вплоть до спаривания инструментов и калибров и их согласования с процессом хромирования.
Одним из важных мероприятий, улучшающим качество подхромной поверхности, было внедрение электрогидравлической обработки взамен шпалерной строжки гладкого отверстия перед операцией дорнирования.
В целом внедрение в массовое производство унифицированной технологии хромирования в сочетании с мероприятиями по повышению точности и чистоты механической обработки канала ствола оказало положительное влияние на качество хромового покрытия, повысив его стабильность и снизив брак по отдельным его видам. Повысилась также культура производства, уменьшился расход хромового ангидрида.
Важным этапом технического развития производства автоматов была отработка с участием научных организаций технологии скоростного размерного хромирования стволов в протоке электролита (арх. 1242-61). Отличительной особенностью этой технологии является принудительное движение электролита в сочетании с автоматическим контролем и регулированием основных параметров режима хромирования при высоких плотностях тока (100–300 ампер на дм2).
Применение движущейся со скоростью 2–5 м/с струи электролита позволило значительно сократить продолжительность операции хромирования за счет повышения плотности тока, которая при естественном протоке электролита находилась в пределах 25–30 ампер на дм2. Внедрение указанной технологии существенно улучшило перспективы коренного усовершенствования всей технологии ствольного производства в направлении его механизации и автоматизации.