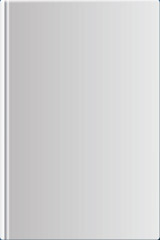
Текст книги "Отечественные автоматы (записки испытателя-оружейника)"
Автор книги: А Малимон
Жанры:
Прочая документальная литература
,сообщить о нарушении
Текущая страница: 31 (всего у книги 40 страниц)
Штатного АК это касалось в меньшей степени. Энергичнее работала более массивная подвижная система, лучше была отработана технология. Открытый щиток выдвинул для конструкторов непростую проблему, а поэтому новшество «дотошных» испытателей не сразу встретило одобрение со стороны автора образца. Озадачены были и представители ГАУ А.А. Григорьев, В.С. Дейкин, присутствовавшие на испытаниях. Для них, как и для испытателей полигона, которым не только полные отказы, но и отдельные задержки приходилось редко видеть в данной системе, указанный факт был полной неожиданностью. Для Головного заказчика и конструктора это угрожало затяжкой срока подготовки автомата к войсковым испытаниям.
В ходе длительного дискуссионного обсуждения данного вопроса все пришли к единому мнению, что открытый щиток в системе АК является реально возможным условием боевой эксплуатации этого образца, при которой частые «манипуляции» со щитком-переводчиком не всегда возможны и оправданны.
Автор автомата приступил к разработке пылезащитного устройства не с ручным управлением, а с автоматической его работой при каждом выстреле.
Осень 1957 года была не самым счастливым временем в жизни безусловно талантливого конструктора-оружейника А. С. Константинова. Он доработал свой автомат, «провалившийся» при втором заходе на конкурсные испытания, устранив недостатки в работе ударно-спускового механизма. На третьих полигонных испытаниях его образцы показали вполне удовлетворительные результаты. Но это был уже «утешительный» заезд на полигон конструктора, закончившего свою работу с чувством исполненного долга. Завершение работы доставило ему чисто профессиональное удовлетворение.
Месяцем раньше для изготовления серийной партии с целью проверки в производстве и определения возможности постановки на массовое изготовление полигоном был рекомендован легкий автомат Калашникова. При этом должна была быть произведена дополнительная его доработка. Но в ГАУ принято было решение провести войсковые испытания опытной серии, поскольку на них по опыту прошлого выявляются отдельные недостатки, которые не проявляются в специфических полигонных условиях (арх. № 2591-57, стр. 76). Вопрос этот увязывался с отработкой легкого ручного пулемета одноименной конструкции для войсковых испытаний, который полигоном в том же отчете рекомендовался для дополнительной доработки без рекомендации на серию.
По пулеметам должно быть отдельное рассмотрение вопроса, сейчас же можно сказать только то, что в образце Калашникова была сложной проблема обеспечения необходимой служебной прочности и эксплуатационной долговечности магазина на 75 патронов.
ГАУ принято решение произвести доработку пулемета в ходе изготовления опытной серии, войсковые испытания которой намечено провести одновременно с легкими автоматами.
В ходе совместной отработки образцов и изготовления серийных партий в автомате и пулемете обеспечена унификация затворной рамы с затвором, возвратной пружины и деталей ударно-спускового механизма. Вес подвижных частей за счет утяжеления затворной рамы увеличился с 483 до 527 г (арх. № 2663-58, стр. 63), однако они еще не «дотянули» до веса откатных частей штатного АК (585 г до начала работ по его общему облегчению).
В автомате введен автоматически работающий щиток (в дополнение к щитку переводчика), обеспечивающий постоянную закрытость щели под рукоятку перезаряжания под действием специальной пружины. Он открывается только при стрельбе в период отката частей под воздействием рукоятки перезаряжания на верхний скос щитка.
После наката частей щиток возвращается в исходное положение. Одновременно с этим улучшена закрытость внутренней полости ствольной коробки за счет обеспечения более плотного прилегания крышки к боковым стенкам коробки. На крышке с этой же целью на задней стенке экстракционного окна сделана отбортовка, что впоследствии выдвинуло весьма сложную проблему устранения трещин в этом месте.
Доводка автомата до законченного вида проводилась уже на полигоне. Экспериментальными стрельбами проверялись некоторые разновариантные элементы конструкции отдельных деталей с целью выбора лучшего варианта из них. Проверялись, в частности, затворные рамы с косым и прямым ударом о ствольную коробку в конце наката, различные варианты замедлителей (анкер и полуанкер), проводились и некоторые другие исследования (арх. № 2663-58, стр. 63).
Выбор был остановлен на прямом ударе рамы и замедлителе с полным анкером, типа ранее уже испытывавшегося. При официальных полигонных испытаниях эти же автоматы в затрудненных условиях, включая и все виды запыления, показали достаточно надежную работу. При повторении испытаний в условиях запыления с открытой щелью под рукоятку перезаряжания (при снятом автоматическом щитке и опущенном щитке переводчика) были отказы в работе автоматов.
Конструкторская борьба с самопроизвольными отделениями крышки ствольной коробки в особых, не часто встречающихся эксплуатационных условиях привела к тому, что крышка стала трудно отделяться и принудительным способом – как у образцов АК-47 первых серийных выпусков. Поэтому автором системы была разработана специальная защелка крышки, смонтированная на измененном направляющем стержне возвратной пружины.
В результате произведенных доработок вес автомата увеличился до 3,1 кг, что ГАУ признало приемлемым для этапа изготовления опытной серии и проведения войсковых испытаний (арх. № 2663-58, стр. 88). Учитывались также технические трудности по дальнейшему облегчению системы, достигнутые результаты по решению этой же проблемы при разработке образцов, основанных на других принципах устройства автоматики, а также желательность сохранения взаимозаменяемости всех разбираемых узлов и механизмов легкого автомата со штатным АК-47.
Уменьшение весовой нагрузки на солдата с учетом 4 комплектных магазинов составило 1,1 кг, что наряду с достигнутым улучшением кучности стрельбы явилось основным итогом модернизации системы АК. Модернизация повысила ее боевые и маневренные качества, сохранив основные положительные свойства штатного АК-47 (простоту устройства, удобства обслуживания, надежность в работе), заложенные в ненарушенной принципиальной схеме устройства.
Положительные качества легкого автомата и его преимущества перед штатным образцом отмечают и войсковые комиссии, рекомендовавшие его для принятия на вооружение взамен АК-47 с предварительным устранением отдельных эксплуатационных недостатков. По результатам обобщения материалов войсковых комиссий, проведенных ГАУ (арх. № 2733-59, стр. 63), легкий автомат Калашникова вместе с ручным пулеметом одноименной авторской разработки Постановлением Совета Министров СССР от 8.04.59 года принят на вооружение Советской Армией. Ему присвоено наименование: «7,62 мм модернизированный автомат Калашникова (АКМ)» (арх. № 2699-59, стр. 70). Этим же Постановлением регламентированы и основные характеристики легкого автомата: вес с магазином без патронов – 3,1 кг ± 3 %; длина оружия – 760 мм; прицельная дальность – 1000 м; начальная скорость пули – 715 м/с; емкость магазина – 30 патронов.
Заводу в этом же году предстояло произвести полную подготовку производства к массовому выпуску новых автоматов и изготовить первую серийную партию с расчетом полного перевода производства на новый выпуск в следующем году.
Послевойсковая доработка образца к этому времени, естественно, закончена не была. Ее предстояло совмещать с подготовкой производства и продолжать уже в период освоения модернизированной системы. Доработка включала в себя не только улучшение эксплуатационных качеств модернизированного образца, но и технологическое усовершенствование.
Некоторое усложнение в конструкции и связанные с этим отдельные недостатки обусловили нововведения: замедлитель курка, пылезащитное устройство и новая защелка крышки ствольной коробки. Отработка этих узлов в период подготовки к войсковым испытаниям полностью завершена не была, но, несмотря на это, войска положительно оценили нововведения и рекомендовали их доработать.
Это были основные узловые вопросы усовершенствования АКМ в период его подготовки к массовому выпуску. Наиболее сложным в доработке оказалось пылезащитное устройство. Еще в предвойсковой период было замечено, что скрытый под переводчиком автоматический щиток склонен выползать из своей щели на величину, большую, чем необходимо для обеспечения нормальной разборки системы.
Под щиток попадала рукоятка перезаряжания, что препятствовало отделению затворной рамы. Пылезащитное устройство было также чувствительно к загрязнению – при попадании пыли не исключалась возможность заклинивания щитка в нижнем положении. Это был основной эксплуатационный недостаток, обусловленный конструктивной схемой механизма пылезащиты. Решение вопроса пылезащиты подобным способом – с открыванием щитка экстракционного окна затворной рамой, в этот же период времени было более удачно реализовано в ручных пулеметах Калашникова (ПК) и тульского конструктора Г.И. Никитина под штатный винтовочный патрон. Но там при закрывании экстракционного окна ствольной коробки происходит не подъем, а опускание щитка вниз в свободном пространстве не только под действием своей автономно работающей пружины, но и собственного веса без торможения другими деталями.
Отечественная и зарубежная оружейная практика подтверждают тот факт, что подобные механизмы работают более надежно, если перемещение их деталей имеет замкнутую силовую кинематическую связь с ведущим энергетическим звеном на протяжении всего цикла работы.
Устранение недостатков по пылезащите автомата встретило определенные трудности, и автор системы в посылаемых на полигон первых доработанных образцах делает попытку отказаться от автоматического щитка, рассчитывая добиться положительного результата другими путями.
В конечном счете оно так и получилось, но при первых двух полигонных испытаниях (арх. № 2733-59, стр. 49; арх. № 2731-59, стр. 229) автоматы при сухих деталях в условиях запыления работают крайне ненадежно: от 2 до 5 % задержек или полные отказы по причине недокрытий затвора. Поэтому упразднение автоматического щитка полигон признал нецелесообразным, и ГАУ потребовало продолжить доработку (арх.№ 2733т59, стр.32). Но продолжение доработки даже с учетом создания новых конструктивных схем не принесло успеха и на этот раз.
Решить данную задачу в короткий срок в условиях надвигающегося периода массового производства АКМ было весьма сложно и проблематично. Столкнувшись с рядом больших трудностей в создании технологичной и удовлетворяющей требованиям эксплуатации конструкции пылезащитного устройства, завод обратился в ГАУ с просьбой «считать дальнейшую работу по изысканию приемлемой конструкции автощитка перспективной, но не ограниченной каким-либо сроком» (арх. № 2718-59, стр. 174).
Ход производства АКМ показал, что эта работа была отложена навсегда.
Образцы от первых серийных партий выдерживают испытания на полигоне во всех затрудненных условиях, включая и запыление, при открытом щитке-переводчике, показывая практически равноценные результаты с АК-47.
Испытатель завода Н. А. Афанасов, а вслед за ним в своем отчете и испытатель полигона объяснили этот факт внедрением в производство большого количества технологических мероприятий, улучшивших надежность работы образца (арх. № 2783-60, стр. 90). Способствовало этому и повышение энергетического баланса системы, в том числе и связанного с увеличением веса затворной рамы.
Полигон не одобрил для внедрения в валовое производство автоматический щиток, доработанный после войсковых испытаний, ввиду его конструктивного несовершенства, признав одновременно целесообразным продолжение работ в этом направлении.
Введенный на период конкурса дополнительный щиток прекратил свое существование. В дапьнейшем испытания автоматов на заводе и полигоне стали проводиться при открытом щитке-переводчике, что было узаконено и соответствующими методиками испытаний. Отдельные автоматы в условиях запыления работали на пределе своих возможностей, давая задержки в стрельбе. В таких случаях на заводе производилось исследование причин, принимались меры в производстве, более тщательно контролировалось соблюдение технологии испытаний по автоматизированной системе запыления.
Новая защелка крышки ствольной коробки, доработанная по результатам войсковых испытаний, полигоном и ГАУ была одобрена для внедрения в производство. В конструктивном и технологическом отношениях она была сложнее штатной, особенно по возвратному механизму. Требовалась коренная перестройка технологии практически уже налаженного производства.
Ввиду технологических неудобств и сложности перестройки производства на изготовление новой защелки повышенной трудоемкости при наличии в ней и отдельных эксплуатационных недостатков (сложность разборки, склонность к засорению), завод просит согласия ГАУ не внедрять это изменение в производство (арх. № 130-62, стр. 19).
Согласие было получено, внедрение не состоялось. Учитывалось то обстоятельство, что самопроизвольное отделение крышки в условиях падения оружия с большой высоты на дуло ствола – крайне редкое событие, а также намерение решить поставленную задачу более простым способом, без усложнения конструкции оружия. Фиксация крышки в дальнейшем была улучшена за счет изменения профиля фиксирующего выступа основания возвратного механизма.
Основное в работе замедлителя – обеспечение на стабильном уровне необходимого времени замедления срабатывания курка по окончании наката частей как дающего стабильное улучшение кучности стрельбы.
Контроль межциклового времени по каждому изделию в массовом производстве не производился, но случаи нарушения стабильности по кучности стрельбы увязывались с работой замедлителя (арх. № 2716-59, стр. 94). Частое повторение таких случаев послужило поводом для дополнительных исследований данного механизма на полигоне (арх. № 2804-60, стр. 53) по специальному заданию ГАУ. Исследованиями установлено, что наиболее эффективная работа замедлителя обеспечивается при увеличении межциклового времени, в среднем на 7-13 мс, при достижении им общей величины порядка 16–20 мс.
Исследования Л.Г. Левина и М.Б. Махатова также показали, что внедряемый в АК замедлитель курка является одним из наиболее приемлемых методов увеличения межциклового времени в нужных пределах по сравнению с увеличением массы курка или созданием специального механизма его перехвата с использованием преднамеренно увеличенного отскока затворной рамы. Однако в период развернутого массового производства АКМ начались «нападки» на замедлитель с участием отдельных КБ и даже специализированных по оружейной тематике исследовательских организаций. Без достаточных оснований ставилась под сомнение полезность данного механизма с точки зрения улучшения кучности стрельбы.
Начали поступать и конкретные предложения по исключению замедлителя из конструкции АКМ. В производственном отношении это давало бесспорные выгоды. Упрощалась конструкция и изготовление УСМ. С производства снималась забота по исключению периодически появляющегося большого износа деталей с образованием наклепа металла на замедлителе и курке по местам их контактного взаимодействия, по борьбе с зависаниями курка на замедлителе, а также с поломками этой детали, особенно при попытке приспособить ее к ранее выпущенным автоматам АК-47.
Исключались и микротрещины в кожухе ствольной коробки по месту удара замедлителем, которые изредка замечались в конце испытаний системы на полную живучесть.
Но как быть тогда с кучностью стрельбы, которая и при наличии замедлителя не всегда укладывается в требуемые минимальные нормы?
Это сдерживало автора системы и производство от реализации предложений по упразднению замедлителя, несмотря на то, что ее улучшение достигалось только при стрельбе с наличием упоров.
Характерно, что с предложением по упразднению замедлителя в системе АК выступил и конструктор Г.А. Коробов (арх. № 2772-60, стр. 8). Инициатор использования подобного механизма в применении к автомату собственной конструкции Г.А. Коробов предположительно считал, что при стрельбе из неустойчивых положений без наличия упоров замедлитель в применении к системе АК должен отрицательно влиять на кучность стрельбы. Дополнительным обоснованием предложения Коробова было «упрощение изготовления УСМ и улучшение служебной эксплуатации автомата».
Сравнительная проверка возникших сомнений в отношении полезности замедлителя, проведенная полигоном на большом количестве автоматов, взятых из текущего производства АКМ, подтвердила ранее сделанные выводы в пользу замедлителя, который при стрельбе с упора давал улучшение кучности примерно в 2 раза (арх. № 2783-60, стр. 9). Подобные проверки проводились и в дальнейшем, и все с одними и теми же результатами.
Замедлитель продолжал свою жизнь в автомате АКМ вплоть до прекращения его производства. Не исключен он был из данной конструкции и при перевоплощении ее в новую модификацию.
Применение легких сплавов
Магазин – единственный сборный узел автомата, который удалось перевести на изготовление из легкого сплава. Впоследствии по заводской индексации он стал самостоятельным изделием, входящим в состав войсковой комплектации автомата. Внешне, казалось, все это просто было сделать, фактически решение этой проблемы потребовало большого объема конструкторских и технологических исследований и связанных с ними различного вида испытаний.
За счет применения легкого сплава на алюминиевой основе вес магазина по сравнению со стальной конструкцией снижен с 320–330 г до 170–180 г, что с учетом полной комплектации автомата запасными магазинами позволило существенно снизить и общий боевой вес автомата, заметно уменьшив весовую нагрузку на солдата.
Отработке и производственному освоению легкого магазина со средним весом примерно 165 г ГАУ придавало особо важное значение. «Из общего облегчения автомата 1050 г – 600 г падает на магазины», – отмечается в письме УСВ с одновременной просьбой ускорить освоение легкого магазина в массовом производстве.
Но освоение нового магазина трудно поддавалось ускорению, что было связано с достаточно объективными причинами. Поисковыми работами по исследованию возможностей использования легких сплавов для изготовления автоматных магазинов Ижевский завод совместно со специализированными научными организациями в области материалов и технологий занимался в течение ряда лет. Длительные поиски приемлемого материала, проводившиеся с участием организации Ф.А. Куприянова, сопровождались проверкой прочности многих легких сплавов на алюминиевой основе (Д16АМ, Д16АТ, АМГ-5, Д16АБМ). Войсковая серия магазинов для легких автоматов была изготовлена из сплава Д16АБМ.
Сварка корпуса из тонколистового алюминиевого сплава и обеспечение его необходимой жесткости, объемная штамповка зацепов и усилителей корпуса с постоянным трещинообразованием и низкой стойкостью штампов составляли основную технологическую трудность в изготовлении легкого магазина на протяжении всего периода его конструкторской и технологической отработки.
Длительные поиски приемлемых способов изготовления легкосплавного магазина не только удлиняли сроки его отработки, но и в известной мере создавали торможение в подготовке опытной серии легких автоматов для войсковых испытаний.
«Технологию, обеспечивающую качественную сварку при изготовлении магазинов из сплавов Д16АБМ, отработать не удалось, завод и сейчас обращается за помощью в различные научные организации», – обращается завод в ГАУ с просьбой об удлинении сроков изготовления серии легких автоматов (арх. № 2663-58, стр. 9). В отработку технологии сварки входила и разработка новых сварочных машин и другого оборудования. Разработка и освоение комплексной технологии производится с участием организаций Спиридонова, Куприянова, Лазарева, Розанова (арх. № 2396-54, стр. 215; арх. № 130-62, стр. 192).
Магазин из термообрабатываемого сплава Д16АБМ, показавший по сравнению с ранее испытывавшимся в войсках из сплава АМГ-5 лучшую прочность (арх. № 2664-58, стр. 47, 35), был одобрен ГАУ для освоения в массовом производстве. Однако опыт его освоения показал, что он не обладает еще достаточной служебной прочностью, механической прочностью защитного покрытия, а сам сплав и достаточной коррозионной стойкостью (арх. № 831-61). В связи с этим завод приступил к созданию более жесткой конструкции магазина из сплава АМГ-5В, легированного ванадием. Введены ребра жесткости на боковых стенках корпуса, усилен передний зацеп, его объемная штамповка стала проводиться в два перехода с промежуточной обрубкой по контуру и дополнительным отжигом, так как при штамповке в один переход с одновременной формовкой внешнего профиля зацепа и его гибкой в соответствии с профилем передней стенки магазина был большой процент технологического брака по трещинам.
Встал вопрос и о коррозионной защите. При изыскании стойкого антикоррозионного покрытия большой интерес представляло глубокое анодирование. По мнению некоторых специалистов, оно должно было решить вопрос повышения жесткости магазина (арх. № 2579-57, стр. 72). Однако впоследствии выяснилось, что эту технологию применять нельзя, так как в зазоры по местам сварки попадает серная кислота электролита, которая в дальнейшем вызывает коррозию сплава АМГ-5В (арх. № 2654-57, стр. 26).
Лучшим оказалось анодно-лаковое покрытие, которое по механической прочности коррозионной стойкости показало преимущества перед параллельно проверявшимися оксидно-лаковым («голубое оксидирование») и фосфатно-лаковым покрытиями (арх. № 129 стр. 44).
Конструктивные упрочнения, обеспечившие доведение служебной прочности легкого магазина до уровня стальной конструкции (арх. № 50–61, стр. 213), и анодно-лаковое покрытие были одобрены ГАУ для внедрения в серийное производство. Новый магазин стал легче стального в среднем на 150 г. Внедрение процесса анодирования оказалось весьма трудоемким и сложным (арх. № 130-62, стр. 192): не удается полностью удалить раствор хромового ангидрида из щелей, швов, зазоров, который выступает при хранении изделия, оставляя коричневые полосы; невозможен передел забракованных анодно-лаковых деталей по причине растравливания сварных точек; невозможность повторного анодирования деталей вызывает необходимость подлакировки оголенных участков, что не обеспечивает механическую прочность покрытия.
Встречавшиеся технологические трудности преодолевались с участием научных организаций. Отработка конструкции и технологии изготовления легких магазинов была завершена в 1961 году, а в 1962 году начат их серийный выпуск в необходимых количествах (арх. № 31–61).
При подготовке массового выпуска магазинов в числе 29 единиц нового оборудования спроектировано и изготовлено 16 сварочных машин различных типов для производства шовной и точечной сварки. Этому предшествовала специальная исследовательская работа, в которой принимали участие инженеры Технологического института Петрань и Григорьев (арх. № 841-59). Была обоснована техническая целесообразность применения специальных сварочных машин, обеспечивающих, в отличие от стандартных общего назначения, высокую точность, качество сварки и снижение трудоемкости изготовления с большой экономической эффективностью.
Разработано и техническое задание на проектирование и изготовление таких машин. В период отработки штампосварной конструкции легкого магазина заводом проверялась возможность изготовления корпуса магазина и подавателя из алюминиевого сплава методом литья под давлением (арх. № 2507-56).
Положительные результаты получены только по подавателю. Исследованием данного вопроса в других организациях установлено, что в отлитых под давлением деталях наблюдается характерная воздушная пористость металла. В алюминиевых и магниевых сплавах по этой причине не применяется термообработка, так как при нагреве под закалку на поверхности детали образуются вздутия. Перспективным признано литье в вакууме, при котором удаляется воздух.
Наряду с работами по облегчению магазина производились также поиски новых путей и по дальнейшему облегчению конструкции самого автомата за счет применения более легких материалов. Поиски лучших материалов, обладающих приемлемыми удельным весом и прочностными качествами, ведут те же научные организации Спиридонова и Куприянова. Об этом сообщает оружейным предприятиям зам. министра оборонной промышленности С. Зверев (арх. № 2625-57, стр. 7). Работы по практической реализации результатов этих поисков особенно активизировались в начале 60-х годов не только по автомату, но и другим видам автоматического оружия.
По ускорению развертывания исследовательских работ, связанных с применением титана и магния, а также сплавов на их основе, для изготовления вооружения и другой техники были приняты постановления Совета Министров СССР и РСФСР в конце 50-х годов (арх. № 2699-59, стр. 10).
Большие исследования по данному вопросу с участием предприятий оборонной промышленности в конце 50-х годов были проведены на полигоне ГАУ С.И. Угорским и В.И. Симониным на различных образцах автоматического оружия, включая и систему АК.
Ориентация была взята на алюминиевые и титановые сплавы, которые по своим прочностным характеристикам и удельному весу считались наиболее перспективными с точки зрения дальнейшего облегчения стрелкового оружия. Наибольшее внимание было приковано к титановым сплавам. При выполнении данной работы впервые рассмотрели возможность облегчения наиболее массивных деталей оружия (ствола и ствольной коробки) за счет применения сплавов на алюминиевой и титановой основе, где выигрыш в весе в случае положительных результатов исследований мог быть получен наиболее ощутимый.
Исследования показали, что изготовление стволов из этих сплавов невозможно из-за малой их стойкости в отношении механического и эрозионного износа каналов, а алюминиевый сплав, кроме того, не обладает необходимой термической стойкостью в случае перегрева, что особенно важно для пулеметных стволов под винтовочный патрон, эксплуатация которых производится в условиях больших тепловых перегрузок.
Повысить стойкость стволов АКМ из алюминиевых сплавов к механическому и эрозионному износу канала за счет применения специальных покрытий оказалось невозможным вследствие большого отклонения в теплопроводности и термическом расширении покрытий, приводившем к нарушению их сцепляемости с основным металлом.
Применение лейнирования путем введения наружных кожухов с целью снижения веса стволов не обеспечивало необходимой их прочности, отрицательно сказывалось на живучести у пулеметных стволов даже с применением лучшего по качеству титанового сплава. По автомату это не давало большого выигрыша в весе, создавая технологические сложности в производстве. Повышенная аккумуляция тепла в металл кожуха создавала перегрев в наружной части ствола, ухудшая эксплуатационные качества оружия.
Применение алюминиевых сплавов признано нецелесообразным не только по стволам, но и по другим деталям стрелкового оружия среднего калибра, за исключением магазинов автомата АК и пулеметных патронных коробок, ввиду недостаточной эксплуатационной прочности.
При эксплуатационных испытаниях ручных пулеметов Дегтярева многократными разборками и переключениями механизмов на полигоне ГАУ выявлен большой износ деталей из алюминиевого сплава, сильно ухудшавший их техническое состояние и эксплуатационную долговечность.
Аналогичный вывод был сделан и в отношении титановых сплавов, но с некоторыми отступлениями в отношении возможности их использования при модернизации существующих и разработке новых образцов оружия. В заключении ГАУ по результатам проведенных полигонных исследований (арх. № 2783-60, стр. 208) отмечается: «При современном качестве титановых сплавов применение их для изготовления высоконагруженных деталей стрелкового оружия с целью облегчения, без дополнительных конструктивных мероприятий по повышению прочности не может быть рекомендовано».
Отмечалась недостаточная прочность ствольных коробок из титанового сплава, под которой понималась их склонность к чрезмерно большому износу боевых выступов с весьма интенсивным увеличением основного зазора по узлу запирания, который протекал в 3–6 раз быстрее по сравнению с установившимися нормами износа для стальных деталей.
В системе АК с титановой ствольной коробкой после испытаний на полную живучесть износ узла запирания оказался в 12 раз больше, чем при стальной детали. Имело место и ухудшение работы оружия, которое обуславливалось низкими антифрикционными свойствами титановых сплавов. Они оказывались недостаточными при проверке па пулемете Никитина даже после специального покрытия деталей никелем, обычно повышающим эти качества титановых сплавов.
Не получили одобрения титановые сплавы и по результатам проверки на Ижевском заводе деталей из сплава ВТ-1 (исключая ствол, коробку, подвижную систему, УСМ), давших облегчение системы на 150 г. При испытаниях они показали недостаточную служебную прочность и эксплуатационную долговечность.
Однако, принимая во внимание проводимые поисковые работы по улучшению качества этого материала, ГАУ не исключало возможности практического применения наиболее прочных титановых сплавов при разработке новых легких образцов стрелкового оружия.
Признаны представляющими «определенный интерес» исследования полигона по химическому никелированию деталей оружия как способу повышения антифрикционных качеств титана.