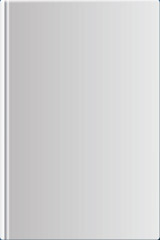
Текст книги "Отечественные автоматы (записки испытателя-оружейника)"
Автор книги: А Малимон
Жанры:
Прочая документальная литература
,сообщить о нарушении
Текущая страница: 33 (всего у книги 40 страниц)
Работы по снижению веса акм
Вес автомата 3,1 кг, утвержденный Правительством, был максимальным достижением конструктора по облегчению системы АК при ее модернизации. Он не учитывал веса магазина, но включал в себя вес пенала с принадлежностями и шомпола, размещаемых на оружии. Строго выдерживать этот вес в массовом производстве, особенно в тех случаях, когда выявлялась необходимость упрочнять отдельные детали, было непростой задачей.
В построительных чертежах значился чистый вес автомата 3,02 кг, не учитывающий веса принадлежностей. По статистическим данным за 1961 год (арх. 51–61, стр. 5) этому требованию удовлетворяло 16 % выпускаемых автоматов, остальные имели превышение веса в пределах 30–60 г. Но и превышение веса 20–30 г уже усложняло процесс сдачи готовой продукции заказчику. Такие автоматы принимались в сопровождении утвержденных актов, в отдельных случаях требовалось и разрешение ГАУ. От завода требовались мероприятия как по повышению прочности деталей, так и по снижению общего веса изделия, которые взаимно ограничивали реальные возможности решения каждой из этих задач.
Доработка автомата по вкладышу ствольной коробки (добавление веса 19 г), нижней антабке, креплению рукоятки и другие внесенные изменения дали прибавление веса автомата около 55 г. Но вес отдельных автоматов мог увеличиваться еще и за счет колебаний в толщине листового металла, применяемого при штамповке и не подвергаемого дополнительной размерной механической обработке, дающих добавление веса наиболее крупных деталей до 30 г.
Колебания в весе деревянных деталей, изготовляемых из фанерных плит, в зависимости от плотности материала и уровня пропитки смолой уже готовых деталей, как показала практика, составляли примерно 35 г (арх. 51–61, стр. 7).
Большие колебания характеристик применяемых материалов трудно поддаются конструкторскому учету при проектировании изделий, что отражается на неточности первоначально задаваемых весовых характеристик как отдельных деталей, так и собранного изделия в целом.
Проведенные работы по облегчению ряда деталей и узлов (арматуры ствола, возвратного механизма, цевья и др.) позволили снизить вес автомата примерно на 70 г. Достигнутый уровень облегчения АКМ, при котором в 1963 году он стал удовлетворять нормативным требованиям (арх. 201-63, стр. 23), не обеспечивал еще необходимой стабильности данной весовой характеристики в текущем массовом производстве.
Добытые с трудом граммы, подчас за счет кропотливого и скрупулезного удаления «лишнего» металла во многих деталях путем введения облегчающих отверстий, пазов, выемов и т. п., а вместе с тем и введение дополнительных технологических операций по механической обработке, постепенно растрачивались на различные доработки не только по выявленному в производстве, но и по замечаниям войск. Если впоследствии оказывалось, что облегчение той или иной детали привело к снижению ее служебной прочности, то ослабленные места вновь заполнялись металлом. С учетом уже сделанного в повышении запаса долговечности нуждались кожух ствольной коробки, на боковых стенках которого изредка появлялись трещины, крышка коробки, затыльник приклада и другие детали (арх. 51–61, стр. 129). Металлическое армирование гнезда в прикладе для пенала с принадлежностью, который в результате износа дерева заклинивался в прикладе и трудно извлекался, не получило конструкторского завершения ввиду увеличения веса приклада.
Завод неоднократно обращался в ГАУ и отраслевое министерство с предложением по снижению нормативных весовых требований по автомату (арх. 51–61, стр. 51). Предлагалось, в частности, установить нормативный вес АКМ не более 3,1 кг, но без пенала с принадлежностью, шомпола и магазина. Принадлежность предлагалось разместить в сумке для магазинов. Предложение не получило одобрения. «В мирное время автомат нередко эксплуатируется с одним магазином, и сумка с запасными магазинами может отсутствовать», – таким было возражение военного представителя.
В отношении обеспечения весовых данных облегченного АКМ на требуемом уровне (3,1–3,193 кг) оружейное производство работало на пределе своих возможностей. Над ним постоянно «висела» проблема снижения веса, которая получила «усиление» в связи с появлением требований по доведению его нормативной живучести до уровня более «тяжелого» своего предшественника.
Работы по снижению веса автомата, как и многие другие конструкторские исследования, завершались экспериментальной проверкой в опытном цехе завода, являвшемся главной производственной базой отдела главного конструктора завода, который в годы Великой Отечественной войны и в послевоенное время (1940–1958 гг.) возглавлял талантливый оружейник и опытный конструктор В.И. Лавренов. В последующие годы после А.П. Митрофанова, Н. Н. Колпикова и Е.Н. Назарова (1958–1966 гг.) ОГК продолжительное время (1966–1988 гг.) возглавлял И.Е. Семеновых, с 1988 г. – Н.А. Безбородое.
В особо напряженные периоды времени по конструкторской отработке и изготовлению первых серийных партий новых видов оружия (1955–1965 гг.) опытный цех возглавляли К.И. Колосков, А.А. Казаков, Г.М. Туков. В последующие годы их сменили Г.Г. Ованисян, В.Д. Павелкин.
Постоянными «обитателями» особой опытной мастерской цеха, являвшейся и экспериментальным центром, и своеобразной конструкторской лабораторией в сложное для разработчиков нового оружия время, был главный конструктор стрелкового оружия М.Г. Калашников со своими ближайшими помощниками В.В. Крупиным, А.Д. Крякушиным и В.Н. Путиным, конструкторы Е.Ф. Драгунов со своим помощником Ю.К. Александровым, А.И. Нестеров, Г.Н. Никонов.
В числе нового пополнения оружейных конструкторов, проверявших свои творческие замыслы в опытной мастерской, были В.В. Камзолов, В.А. Лекомцев, В.М. Калашников, И.А. Говязин и многие другие.
Качественное изготовление первых войсковых серий новых образцов оружия под руководством опытных мастеров А.В. Пирогова, Г. Файзулина, Г.Т. Коробейникова, А.С. Новоселова, Н.Д. Сычева обеспечивали труженики опытного цеха: слесари-сборщики П.Н. Бухарин, Е.В. Богданов, В.И. Шипулин, А.Т. Анисимов, В.Г. Леонтьев, токари Н.А. Стерхов, Г.Д. Михайлов, фрезеровщики Г. Габдрахманов, А.Д. Пермяков, ложейник П.М. Пермяков, стрелок-испытатель С.Я. Шестов.
Оружие, изготавливаемое умелыми руками этих мастеров своего дела, выдерживало конкурсные испытания различных уровней и принималось на вооружение армии.
Глава 16Курс на дальнейший технический прогресс в оружейных технологиях
Развитие технологий по механической обработке деталей
Ижевскому заводу как передовому предприятию отрасли по дальнейшему развитию производства со значительным сокращением трудоемкости выпускаемых изделий и на этот раз поставлена повышенная задача. Она коснулась и оружейного производства.
По автомату АКМ в ближайшее пятилетие, начиная со второго года массового его выпуска, требовалось снизить трудозатраты в расчете на одно изделие с 21 до 14 нормо-часов (арх. 2-61, стр. 103). Значительное снижение трудозатрат планировалось получить за счет совершенствования технологий.
Снижение трудоемкости механической обработки деталей требовало отказа от ранее принятого принципа дифференциации обработки и перехода к ее концентрации с применением более сложного оборудования. На оружейном производстве в основу механической обработки стал закладываться принцип максимальной обработки при одной установке детали за счет применения автоматических линий, агрегатных и многоинструментальных станков, что в свою очередь требовало максимального облегчения заготовок с минимальными припусками на обработку.
Получившие к этому времени широкое распространение заготовки в виде поковок новым требованиям в полной мере не удовлетворяли. Их применение было неизбежным при изготовлении очень важных и конструктивно не простых деталей (вкладыш, затвор, рама и др.).
Оружейным производством был взят курс на отработку технологий получения более рациональных облегченных заготовок методом литья, спекания порошкового материала, объемной чеканки, профильного проката, прессования и другими прогрессивными методами.
Литье по выплавляемым моделям. Применение точных прогрессивных заготовок являлось одним из основных факторов, определяющим развитие технологий и трудоемкость изготовления изделия.
Наиболее широкое применение в производстве автоматов получили точные заготовки, изготовляемые методом литья по выплавляемым моделям. Широкомасштабная работа в этом направлении была начата в начале 50-х годов с участием научно-исследовательских организаций Ф. А. Куприянова, В.П. Ананьева и завода Н.И. Палладина, осваивавшего литьевую технологию для широкого массового производства оружейных деталей.
Изготовление литьем точных заготовок, не требующих большой механической обработки перед сборкой изделия, особенно громоздких и сложных по своей конфигурации, обладающих и большой металлоемкостью, позволяло снизить технологическую трудоемкость изготовления деталей в массовом производстве при существенном сокращении расхода металла.
Первые технологические опыты были начаты во второй половине 50-х годов на 4-х деталях автомата (сектор переводчика, кольцо цевья, фиксатор металлического приклада, защелка магазина) (арх. 2576-57, стр. 167).
Получить качественные отливки этих деталей с первого раза не удалось. Первая партия отливок получилась крайне неудачной. Детали имели некачественную поверхность и грубое искажение размеров. По внешнему виду они напоминали литье в землю, что было связано с низкой температурой плавления неудачно выбранного модельного пластмассового материала. Потребовались корректировка и совершенствование технологии литья.
В Ижевском филиале технологического института эту работу возглавлял директор Б. Ф. Файзулин, который несколько позже руководил и внедрением литьевых заготовок в производство автоматов АКМ в роли главного инженера завода, где шел массовый их выпуск.
Особо большие трудности разработчикам новой технологии пришлось преодолевать при изготовлении литьем массивных и сложных по форме деталей арматуры ствола АКМ, подвергающихся сильному тепловому воздействию при стрельбе (в особенности газовая камора). Немало хлопот доставляла и отработка методов контроля качества литья.
Освоение производства деталей АКМ из литьевых заготовок производилось в цехе, возглавляемом В. П. Ионовым. Процесс этот протекал длительное время. Сложным было достижение взаимного согласия между производством и представителями заказчика по вопросам использования деталей из литья на сборке автоматов.
Литьевые детали, сохраняя размерные характеристики, предусмотренные для изготовления методом фрезерования, по предварительным техническим расчетам имели примерно на 20 % ниже запас прочности, что порождало главные сомнения у приемщиков в отношении эксплуатационного качества таких деталей. Были большие сомнения в качестве литья громоздких деталей в смысле наличия в них скрытых от наблюдения и трудно выявляемых пороков литьевого металла. Особенно в начальной стадии их внедрения, когда при отработке массовой технологии по недосмотру контролеров на сборку автоматов просачивались детали с отдельными поверхностными дефектами. Все сомнения в отношении прочности литьевых деталей исчезли не только в результате многочисленных испытаний автоматов на живучесть, но и когда Б.Ф. Файзулин с начальником механического цеха В.П. Ионовым провели руководителя военной приемки по всей технологической цепочке изготовления литья.
После этого было дано окончательное добро на изготовление первой большой опытной партии автоматов с литьевыми деталями. В числе деталей арматуры ствола была и газовая камора, в отношении приемлемости литьевого качества которой было больше всего сомнений.
Детали арматуры ствола были в числе первых, переведенных после многочисленных испытаний на изготовление литьем по выплавляемым моделям. Это дало большой технологический и экономический выигрыш производству. В дальнейшем на изготовление из литьевых заготовок были переведены многие другие детали: колодка приклада, сектор переводчика, автоспуск, кольцо цевья, кольцо и наконечник рукоятки ножа-штыка.
Всего к 1963 году было отработано 9 деталей АКМ для изготовления литьем (арх. 201-63, стр. 23).
Мелкие нагруженные детали сложной конфигурации, требующие повышенной точности изготовления, труднее осваивались в массовом литьевом производстве. Им труднее было конкурировать по точности изготовления и механической прочности с деталями, изготовляемыми чисто механической обработкой, где легче осуществлять подбор металла необходимого качества, выгодно использовать направление волокон металла и другую положительную специфику этой технологии.
Порошковая металлургия. В начале 70-х годов Ижевским заводом совместно с другими организациями проведена большая исследовательская работа по изучению возможностей изготовления нагруженных деталей сложной формы, в том числе и деталей стрелкового оружия, методом горячего прессования из порошковых композиций на железной основе.
Большое внимание тогда этому вопросу уделялось и в зарубежных странах.
Исследовательскими коллективами Э.В. Верховцева, Ф.А. Куприянова и Б.Ф. Файзулина были начаты работы по внедрению порошковой металлургии и в производство деталей АКМ.
Технологически обоснована возможность изготовления около 10 деталей автомата из спеченных заготовок, однако прочность таких деталей по результатам первых опытов не всегда удовлетворяла предъявляемым требованиям.
Это относилось в первую очередь к статически нагруженным деталям (гайка винта рукоятки и металлического приклада, и др.), подвергаемым воздействию ударных нагрузок в процессе эксплуатации оружия.
Трудности отработки стабильной технологии изготовления деталей и методов контроля качества спеченного материала без разрушения детали, обуславливали и нестабильность их прочностных качеств при выборочных контрольных проверках в реальных эксплуатационных условиях.
Из спеченных заготовок стали изготовляться шептало одиночного огня, задний зацеп магазина, некоторые детали штыка-ножа. Поиск путей по расширению возможностей применения данной технологии продолжался и на новой модификации системы АК.
Применение фасонного профильного проката дало положительные результаты при изготовлении шептала одиночного огня и защелки замедлителя. Не утратила своего значения в общем техническом прогрессе технологий и штамповка деталей во всех ее видах.
Применение стальной ленты с обеспечением непрерывной подачи к штамповочному агрегату с помощью специальных станков-автоматов позволило полностью автоматизировать процесс изготовления некоторых деталей. Были созданы поточные механизированные линии холодной штамповки деталей магазина, кожуха и крышки ствольной коробки.
Оригинальным было решение вопроса по изготовлению пенала для принадлежностей штамповкой заготовки из листа с последующей ее гибкой на специальном станке-автомате.
Из станка-автомата выходит готовый пенал, в котором грани заготовки по образующей цилиндра пенала неразъемно сцеплены между собою соединением типа ласточкиного хвоста.
Попытка применить штамповку для образования поршневого утолщения штока затворной рамы за счет высадки горячего металла пруткового материала потерпела неудачу.
С внедрением данной технологии в массовое производство при испытаниях стрельбой пошли массовые поломки штоков. Причиной явилась неоднородность структуры металла по длине детали, связанная с местным перегревом металла и образованием концентрации напряжений в переходной зоне – от малого диаметра штока к большому диаметру поршня.
Применение пластмасс
В начале 50-х годов в отечественном машиностроении общего и специального назначения активизируются работы по расширению области применения пластических масс, особенно в тех случаях, когда применение других материалов затруднено или невозможно (приборы высокочастотной техники, радиотехники, радиолокации, телевидения и пр.).
Особую роль в решении ряда специальных задач, связанных с внедрением новой техники, решают специфические свойства пластмасс, которыми они обладают в отличие от других материалов.
Пластические массы представляли собою новый конструкционный материал, обладающий малым удельным весом, высокими изоляционными свойствами, хорошо противостоящий коррозии и, как правило, не требующий механической обработки. Стойкость этого материала против коррозии позволяла решать новые проблемы химического машиностроения и производства.
Форсирование внедрения пластмасс в машиностроение диктовалось и большими их экономическими преимуществами. Практика машиностроения того времени показывала, что одна тонна пластических масс заменяла в среднем около трех тонн цветных металлов, освобождая их для использования в тех случаях, когда они не могут быть заменены другими материалами.
Применение пластмасс позволяло разрабатывать новые технологические процессы, исключающие дорогостоящую механическую обработку и обеспечивающие возможность замены пластмассами не только цветных, но и черных металлов.
Эти и другие положительные качества пластических масс достаточно глубоко проанализированы и освещены в докладах участников «Уральского совещания по проблемам развития промышленности пластических масс и их внедрения в машиностроение Урала» (арх. 3987-53), проведенного Уральским филиалом АН СССР в феврале 1953 года по инициативе Свердловского обкома ВКП(б) (Первый секретарь А.М. Кутырев).
На данном совещании по свойствам пластмасс и их использованию было заслушано 18 докладов представителей научных учреждений АН и предприятий промышленности, почти столько же по вопросам производства пластмасс.
Отработаны конкретные предложения по дальнейшему развитию производства и использованию пластмасс для представления Правительству страны. Всем заводам, выпускающим изделия из пластмасс, рекомендованы и конкретные отдельные технологии.
«Пластические массы как новые машиностроительные материалы открывают исключительно большие возможности в борьбе за снижение себестоимости машиностроительной продукции при одновременном снижении веса машин и улучшении их качества» – отмечается в материалах «Уральского совещания» (арх. 3987-53).
Широкое применение нашли пластмассы и в стрелковом оружии, в том числе и в производстве деталей автомата АКМ и его комплектующих изделий. Первые исследования были проведены в конце 50-х годов.
Проектирование первых пластмассовых деталей производилось в организации С.С. Розанова, там же производилось их изготовление, испытания и первые доработки. Подбор материалов и отработка технологий производились с участием института пластмасс имени Д.Г. Губарева.
Первые исследования лабораторий пластмасс B.C. Подмосковного и С. Е. Булденкова и вариантные конструкторские разработки показали возможность замены деревянных деталей автомата пластмассовыми (арх. 2663-59, арх. 2772-60).
Продолжение исследований расширило диапазон возможного применения пластмасс для изготовления деталей стрелкового оружия.
По автомату АКМ в начале 60-х годов представлялось возможным перевести на изготовление из пластмасс более 7 деталей, однако форсирование этих работ сдерживалось высокой стоимостью наиболее приемлемых по прочностным качествам термореактивных прессовых материалов (арх. 40–61, стр. 85), что существенно снижало экономические выгоды от внедрения пластмасс, получаемые за счет применения новых, более рациональных технологий.
Отраслевое Министерство вынуждено было обращаться в Госплан СССР с предложением по снижению отпускных цен на пластмассы.
Лидирующее положение при освоении пластмасс на АКМ занял магазин, несмотря на то, что работы по нему были начаты несколько позже по сравнению с деталями самого автомата.
Производство магазинов шло в больших количествах, а это предвещало и большие экономические выгоды по сравнению с другими деталями. Для изготовления корпуса магазина и подавателя стали применяться стеклопластики типа АГ-4В и АГ-4С светло-коричневого цвета.
Нужная прочность деталей из этих материалов, успешно конкурирующих с прессованной фанерой, обычной древесиной, а также с некоторыми видами сталей и сплавов, достигнута за счет стекловолокнистого наполнителя (арх. 822, 824-64, 66).
Повышению прочности способствовало также применение наиболее выгодной ориентации волокон материала при укладке его лент в процессе подготовительных операций перед прессованием.
Применение специальных прессформ при изготовлении корпуса магазина с зеркальным изображением его внутреннего и наружного профиля обеспечивало достаточную точность и стабильность получаемых размеров, что особенно важно было для внутренней полости магазина и его горловины.
Отсутствие технологических операций, свойственных изготовлению магазинов из листового металла (штамповка, сварка и пр.), делали технологию с применением пластмасс более рациональной и экономически выгодной.
Магазин с пластмассовыми корпусом и подавателем был легче стального примерно на 130 г и тяжелее варианта из алюминиевого сплава АМГ-5В на 20 г.
В ходе производственного освоения и отработки технологии прессования пластмассовый магазин дорабатывался в направлении повышения служебной прочности по нижней части корпуса и загибам («крыльям») приемника, а также повышения износоустойчивости внутренней передней стенки корпуса с устранением скалывания пластмассы от инерционного воздействия пуль патронов (арх. 1293, 1300, 1314-62 и 63-го г.).
Пластмассовый подаватель оказался прочнее, чем из алюминиевого сплава, который не обладал достаточной жесткостью и при работе деформировался.
Доработанными магазинами, изготовленными в организации С.С. Розанова, была укомплектована первая небольшая опытная партия автоматов с пластмассовыми деталями. Однако при дальнейшем изготовлении небольших серийных партий на корпусах магазинов стали встречаться поверхностные дефекты наподобие трещин, которые вначале и воспринимались как трещины, являясь одновременно и одним из браковочных признаков первых пластмассовых магазинов при их освоении в массовом производстве и приемке заказчиком.
Дальнейший ход производства показал, что указанные дефекты явились следствием неотработанности технологии прессования и при испытаниях таких магазинов на полную живучесть кажущиеся «трещины» не получали дальнейшего развития и не приводили к разрушению детали.
Приковывали к себе также внимание отдельные отступления по наружному состоянию пластмассы, возникающие при специальных лабораторных испытаниях (арх. 850-65) Так, например, после длительной выдержки в камере влажности магазины получали незначительное нарушение сплошности поверхностного смоляного слоя.
Многократные же проверки влияния этого фактора на служебные свойства таких магазинов показали, что они сохранялись на прежнем уровне. Замеченные в ходе изготовления и испытаний реальные и кажущиеся дефекты, являющиеся во многих случаях неизбежным спутником технологии, порождали сомнение в отношении достаточности служебной прочности таких магазинов и их эксплуатационной долговечности для длительной войсковой службы.
Неясность степени риска являлась тормозным фактором при приемке магазинов представителем заказчика. Пластмассовый магазин по сравнению с изготовленным из металла требовал новых подходов к оценке своего выходного качества и эксплуатационных возможностей с учетом свойств нового материала и специфических особенностей новой технологии.
Все сомнения были разрешены войсковыми испытаниями. Одновременно с этим после трехлетней войсковой эксплуатации выявлена недостаточная износоустойчивость крыльев магазина (нижней поверхности загибов приемника), связанная, очевидно, не столько со стрельбой, сколько с частыми расснаряжениями магазинов, что является обычным правилом при несении каждодневной боевой службы с автоматом.
Значительный износ внутренней поверхности загибов приемника приводил к тому, что последний патрон не поджимался к ним подавателем и при легком встряхивании магазина выпадал из него. Других замечаний, препятствующих постановке пластмассового магазина на массовое производство, у войск не было.
Первые попытки упрочнения крыльев магазина были связаны с поисками лучшего способа повышения их износоустойчивости за счет армирования поверхности более стойким к износу материалом. Проверялось армирование специальной стеклотканью Т-91, пропитанной смолой Р2М, тремя слоями шифона по всей поверхности крыльев, а также с помощью стальных пластин различной толщины, впрессованных в пластмассу (арх. 890-70 и 1459-71).
По результатам испытаний наиболее эффективным и приемлемым с технологической точки зрения оказалось армирование стальной пластиной толщиной 0,8 мм. Эксплуатационная долговечность магазина повысилась при этом более чем в 4 раза, что признано вполне достаточным.
В целях обеспечения прочного удержания пластин в магазине в них по предложению Б.Ф. Файзулина пробивались отверстия с рваными бахромистыми краями, которые после прессования оказывались проглубленными в пластмассу.
Разработчиками магазина внесено также предложение для войсковых служб по ремонту изношенных магазинов за счет под фрезеровки подавателя по месту упора в ограничитель (арх. 1440-70).
Доработанные магазины прошли многочисленные испытания в различных эксплуатационных условиях, включая многократные большие перепады температур. По эксплуатационным свойствам они не уступали магазинам, изготовленным из алюминиевых сплавов и из стали, а по служебной прочности корпуса даже превосходили их (арх. 1385-67).
Оценив доработку пластмассового магазина по результатам испытаний в различных организациях, ГАУ одобрило его для массового производства и комплектации автоматов, поступающих в войсковую эксплуатацию. Незаконченность некоторых доработок (отслоение пластмассы по месту удара пуль в переднюю стенку, трещины на загибах приемника и пр.) предложено завершить в процессе массового производства.
Наиболее приемлемьм цветом магазина согласно рекомендациям полигона признан черный или темно-коричневый. Но это пожелание получило практическую реализацию несколько позже, с переходом на другую пластмассу и в другую технологию. Сейчас же магазин, изготовляемый прессованием, имел неоднородный бежевый цвет в сочетании светлых и темных тонов.
Прессованный из стекловолокнита пластмассовый магазин, созданный объединенными усилиями творческих коллективов предприятий промышленности и научных учреждений, стал основным комплектующим изделием автомата АКМ. Согласно производственной индексации, как и магазин из легкого сплава, он выделен в самостоятельное изделие.
Пластмасса как конструкционный материал с высокими электроизоляционными свойствами была использована также для изготовления монолитной рукоятки ножа-штыка и цельной ножны, используемой в паре с ножом при резке проволоки и проводов, находящихся под напряжением.
Конструкторами Мельниковым и Кутергиным первоначально была разработана цельная рукоятка ножа из волокнита (арх. 50–61, стр. 152), являющаяся основной несущей деталью, воспринимающей собою все нагрузки при действии ножом как штыком. В дальнейшем волокнит был заменен более прочным материалом – стекловолокнитом АГ-4С.
В прежней конструкции рукоятки надежной электроизоляции не обеспеспечивалось, так как на конце стержня ножа крепился металлический наконечник, недостаточно закрытый щечками рукоятки при охвате ее рукой. Недостаточную электроизоляцию обеспечивали и сами щечки с клеевым креплением в случае образования эксплуатационных дефектов.
В новой конструкции нож и наконечник с защелкой раздельно закреплены в рукоятке. Нож закреплен в пластмассе рукоятки с обеспечением некоторой свободы бокового прогиба, наконечник крепится на заднем торце рукоятки винтом, который впоследствии заменен пластмассовой пробкой. Нож и наконечник разделяет слой пластмассы, чем и обеспечивается электроизоляция.
Но этого мероприятия оказалось недостаточно. При эксплуатации ножа в паре с металлической ножной, недостаточная электроизоляция была по съемному резиновому наконечнику. По отзывам войск (арх. 213-63, стр.37) резина наконечника под воздействием затекающей под нее смазки разлагается и разрушается с одновременным ухудшением электроизоляционных свойств. В связи с этим была разработана цельная монолитная пластмассовая ножна из стекловолокнита. В нее впрессован резак с осью для сборки с ножом при резке проволоки. Штык-нож с монолитной рукояткой и пластмассовой ножной был принят для массового производства и снабжения войск. На заключительном этапе совершенствования технологии отработана операция прессования рукоятки вместе с ножом и наконечником.
По самому автомату в бытность АКМ в массовое производство была внедрена только волокнитовая рукоятка в варианте автомата с деревянным прикладом. В варианте складного металлического приклада сохранялась деревянная рукоятка, так как пластмассовая, будучи незащищенной при сложенном прикладе, независимо от вида и качества ее материала не обладала достаточной служебной прочностью.
Замена разборных деревянных деталей автомата пластмассовыми проходила несколько сложнее, чем разработка и освоение в производстве монолитных неразборных узлов, состоящих из металлических и пластмассовых деталей. Конструкторские и технологические трудности были обусловлены не только сложностями монтажа и сборки деталей, изготовленных из разных по механическим свойствам и износоустойчивости материалов.
Необходимо было также учитывать и специфические свойства пластмасс, связанные с повышенной по сравнению с деревом теплопроводностью данного материала. Это вынуждало предпринимать необходимые конструкторские меры по исключению влияния указанного фактора на эксплуатационные качества оружия.
В связи с этим пластмассовым цевью и ствольной накладке были приданы наиболее выгодные конструктивные формы, обеспечивающие наименьшую восприимчивость теплоотдачи ствола и одновременно минимальное тепловое воздействие этих деталей при охвате их рукой.
Конструктивная форма деревянных деталей в пластмассовом исполнении не в полной мере удовлетворяла этим требованиям.
По цевью в качестве термоизолятора применен отражательный металлический экран. По прикладу отрицательную роль играла уже повышенная «холодопроводимость» пластмассы, которая ухудшала эксплуатационные удобства, а в отдельных случаях и возможности ведения точной прицельной стрельбы в морозных условиях.
Требования по устранению этого недостатка в некоторой мере предъявлялись и к металлическому складному прикладу, являющемуся по своей массе худшим аккумулятором тепла или холода по сравнению с пластмассовым.