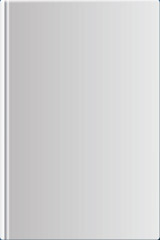
Текст книги "Отечественные автоматы (записки испытателя-оружейника)"
Автор книги: А Малимон
Жанры:
Прочая документальная литература
,сообщить о нарушении
Текущая страница: 27 (всего у книги 40 страниц)
Необходимость проведения большого количества испытаний опытных ударников потребовала разработки специальной установки с механическим приводом, позволяющим производить предварительные сравнительные испытания деталей без стрельбы.
Технологические трудности нового метода изготовления были связаны с операцией правки деталей после прессования выема под штифт. Потребовалось ограничение перегибов детали в одну сторону (не более 4 раз) и величины ее прогиба (не более 1,2 мм) (арх. № 2518-56, стр. 36).
Опытные ударники, изготовленные по новой технологии, при испытании на полигоне холостыми спусками с использованием пневматического прибора, разработанного М.В. Зарубиным, по сравнению со штатными показали повышение живучести, а метод получения выема прессованием вместо обработки металла резанием с точки зрения обеспечения более высокой прочности детали признан более прогрессивным (арх. № 2512-56, стр. 32). Указанное мероприятие также было внедрено в массовую технологию, хотя, как и предыдущие, не обеспечивало необходимого повышения живучести ударника. Дальнейший поиск продолжался с привлечением подведомственных отраслевому министерству организаций.
Но в это же время над производством «нависла» другая проблема, и тоже связанная с ударником. Это были срабатывания капсюля патрона от инерционного накола бойком ударника со сдвоенными выстрелами при переводчике, поставленном на одиночный огонь.
Инерционные наколы впервые были отмечены в 1952 году и первоначально проходили по учету как «сдвоенные выстрелы», которые по характеру проявления нельзя было отличить от «сдвоенных», связанных с неисправной работой спускового механизма. Но когда выстрелы стали получаться при заряжании оружия без нажатия на спуск, то стало очевидным, что с неисправной работой механизма спуска «сдвоенные выстрелы» ничего общего не имеют. При автоматической стрельбе на слух они не обнаруживались, требовался осмотр гильз, которые в данном случае имели выпучивание капсюля под бойком. Частота проявления инерционных наколов на производстве составляла примерно 0,003 % для всех применявшихся партий патронов. На полигоне они проявлялись реже.
Полигонными исследованиями заводских автоматов, давших инерционные наколы при сдаточных стрельбах, каких-либо особенностей, способствующих их проявлению, не обнаружено (арх. № 2576-57, стр. 84). Их причиной, по мнению полигона, являлось неблагоприятное сочетание повышенной инерционной скорости ударника с повышенной чувствительностью ударного состава капсюля– воспламенителя (К/В) патрона.
Ничего нового не выявлено и при исследованиях на заводе. Установлено, что вероятность проявления «сдвоенных» возрастает при скоростях удара бойка более 3 м/с. Расчетами установлено, что ударник при этом обладает кинетической энергией примерно 4,6 кгм и «ее снижение без изменений по скоростям затворной рамы и массе ударника является проблематичным» (арх. № 2679-57, стр. 14). При экспериментальных исследованиях «сдвоенные выстрелы» удавалось получать искусственным путем при утяжеленном до 11,3 г ударнике и усиленной возвратной пружине.
В ходе исследования данного вопроса Е.И. Смирнов предложил использовать опыт производства по изготовлению карабинов Симонова, где вершина бойка имеет горизонтальную площадку диаметром 0,9–1,0 мм со скруглениями граней радиусом 0,4–0,5 мм (арх. № 2331-53, стр. 52). Предложение зам. начальника УСВ заводом было учтено и с некоторыми уточнениями внесено в построительные чертежи. Однако этим мероприятием полного исключения инерционных наколов не достигнуто (арх. № 2396-54, стр. 98).
В связи с нависшей угрозой прекращения приемки автоматов завод обращается в научно-исследовательский институт С.С. Розанова с просьбой включиться в исследования данного вопроса (арх. № 2576-57, стр. 4). Совместным решением ГАУ и MB в марте 1957 года к работе были привлечены не только названный институт, но и один из патронных заводов. В отношении причин исследуемого явления институт подтвердил выводы, ранее сделанные полигоном. Одновременно институтом обоснована необходимость снижения веса ударника с 6,24 до 4,5 г и введения изменений в технологию изготовления патронов с учетом контроля безопасности К/В (арх. № 2663-58, стр. 41). Предложены уточнения по методике контроля чувствительности капсюлей-воспламенителей к инерционным наколам с разработкой прибора для этого контроля.
Исследователями института И.И. Бабичевым и К.М. Обыденкиным предложена конструкция ударника с плоскопараллельными гранями стержневой части по всей ее длине, отличающаяся от конструкции, ранее разработанной заводом, отсутствием цилиндрического утолщения у заднего торца. Указанный ударник после произведенной заводом доработки в направлении устранения заклинивания в канале затвора и исключения возможности неправильной сборки по результатам заключительных полигонных испытаний (арх. № 2657-58, стр. 106) был внедрен в производство.
Вероятность срабатывания К/В от инерционного накола сократилась до минимума. Безопасность обращения с автоматом повысилась также и за счет понижения чувствительности. К/В. При использовании патронов улучшенного качества в текущем производстве автоматов «сдвоенные выстрелы» (при положении переводчика на одиночном огне) и самопроизвольные при перезаряжении оружия вручную полностью прекратились (арх. № 2558-58, стр. 91).
Вес усовершенствованного ударника с цилиндрической формой бойка, улучшенным профилем головной части и пластинчатой стержневой частью составлял примерно 4,75 г вместо 6,24 г у детали прежней конструкции. Отработка конструкции ударника длилась около 4 лет. Достигнув максимального совершенства, она сохранилась в неизменном виде и в последующих модификациях АК. Конструктивная форма этой детали со всеми ее положительными особенностями стала заимствоваться и при разработке других образцов оружия.
Необходимо отметить еще и тот факт, что в практике заводских испытаний «сдвоенные выстрелы», совершенно иного происхождения и уже не представляющие опасности при служебном использовании оружия, можно было получить искусственным путем в любом совершенно исправном автомате текущего производства. Этим искусством, известным только одному исполнителю, в совершенстве владел один из представителей заказчика Е. В. Ярошенко. И вполне естественно, что в период борьбы с опасными «сдвоенными выстрелами» такие случаи у отдельных работников оружейного производства вызывали беспокойство и озабоченность за работу автомата. В связи с этим В.А. Харьков, возглавлявший отработку конструкции ударника, официально выступил с настоятельным требованием «прекратить игру спусковым крючком как действием, не оправдываемым условиями практического использования оружия». Это требование было оговорено в проекте технических условий на приемку автоматов (арх. № 2096-49, стр. 173).
Об этой не раскрытой в то время «тайне» можно было бы не упоминать, если бы в начале 60-х годов из одного патронного завода не поступило сообщение военного представителя В. Михальченко о случаях автоматической стрельбы из автомата при положении переводчика на одиночном огне. Представлены и автоматы, на которых наблюдалось это явление. При этом отмечалось, что такая стрельба получалась при доведенном до крайнего заднего положения спусковом крючке в условиях, когда затылок приклада упирался в ладонь левой руки, а правой рукой стрелок удерживал автомат за рукоятку управления огнем (арх. № 130-62, стр. 34).
По результатам проверки присланные автоматы оказались технически вполне исправными и не имеющими отступлений по технологии изготовления. При их исследованиях тем же Е.В. Ярошенко установлена возможность самопроизвольного перехода с одиночной на автоматическую стрельбу при не жестком упоре приклада в амортизатор заводского испытательного стенда или в ладонь руки и не плотном удержании автомата второй рукой за рукоятку управления огнем, что расценено как умышленное нарушение правил эксплуатации. При всех других условиях исследования автоматической стрельбы не происходило.
Живучесть ударника с плоскопараллельными гранями стержневой части в окончательном конструктивном оформлении стабилизировалась, но и в этом случае она не в полной мере удовлетворяла нормативным требованиям (арх. № 2443-55, стр. 135). Недостаточной живучестью обладали также пружина выбрасывателя и деревянное цевье. Возможности производства в отношении повышения живучести пружины были практически исчерпаны. Разрушение концов пружин на спайке жил («размочаливание») происходило в результате крайне стесненных и неблагоприятных условий работы этой детали, находящейся постоянно в напряженном состоянии.
Наибольшую силовую нагрузку испытывают концы пружины, где и происходит ее разрушение. Во многих случаях пружины с таким дефектом стояли до конца живучести системы, обеспечивая ее надежную работу. Мероприятия по изменению конструкции пружины (диаметров проволоки и самой пружины, шага навивки и числа жил в тросе) положительных результатов не дали. Некоторое улучшение получено за счет уменьшения длины пружины и расширения гнезда для нее в выбрасывателе (арх. № 2443-55, стр. 135). Оказались малоэффективными и технологические мероприятия, в том числе и по изменению температуры отпуска при термической обработке.
Основными дефектами цевья при испытаниях автоматов были трещины в желобе, возникавшие в результате теплового воздействия ствола. Переход на изготовление этой детали из березовой фанерной плиты вместо натуральной березы не исключил образования трещин во внутренней полости цевья. Учитывая отсутствие реальных возможностей по полному исключению отмеченных дефектов, заказчиком временно разрешалась сдача продукции с пониженной живучестью ударника и пружины выбрасывателя (арх. № 2443-55, стр. 1) с условием комплектации принятых автоматов дополнительными запасными деталями. По цевью допускались незначительные трещины во внутренней полости, не выходящие на наружную поверхность детали и не нарушающие ее служебную прочность. Учитывалось и то обстоятельство, что трещины возникали при весьма жестких режимах испытаний, проводившихся в отличие от реальных условий эксплуатации в ускоренном темпе и в крайне ограниченные сроки.
В письмах заказчику завод не скрывал своего желания привести нормы живучести отдельных деталей в соответствие с фактическим уровнем развития производства. Но реальные возможности производства в этом отношении были учтены главным управлением в технических требованиях на разработку новой, облегченной конструкции автомата, гарантийная норма долговечности службы которого по сравнению со штатным АК-47 была снижена на одну треть. В текущем же производстве АК-47 заказчиком продлялись сроки действия временных соглашений без ослабления требований в отношении продолжения поиска новых путей повышения живучести деталей.
Большие хлопоты доставляли производству трещины на многих деталях, вызывавшие особое беспокойство у представителя заказчика (арх. № 2560-51, стр. 85).
Трещины появлялись значительно чаще поломок. Не всегда являясь предвестником скорой поломки детали, они служили критерием исчерпания ее живучести наравне с поломкой. Их появление часто было неожиданным и не всегда имело причинную связь с общим качественным уровнем производства. Нередко имели место случаи их обнаружения еще до вступления образца в эксплуатацию.
Трещины, обнаруженные на пределе гарантийного ресурса детали и даже несколько переступившие этот предел, означали недостаточный запас ее долговечности, что также требовало разработки предупредительных мероприятий. Борьба с трещинами, как и с поломками, независимо от способа их обнаружения (простым визуальным осмотром или с помощью специального приборного оборудования) являлась предметом постоянной и непрекращающейся заботы производства.
Среди известных причин образования трещин было наличие в отдельных случаях конструктивно обусловленных слабых сторон в отдельных деталях, служащих местом концентрации напряжений в металле. Наиболее характерным в этом отношении являлся левый боевой упор затвора, ослабленный вырезом для прохода отражателя.
Напряженное состояние в металле в неразъемных креплениях деталей методом клепки, развальцовки или другими подобными способами вследствие образования натяга в соединениях также служило причиной образования трещин. К таким узлам относятся заклепочные соединения кожуха, крепление сухаря во вкладыше, штифтовое крепление штока в раме, крепление флажка фиксатора ствольной накладки, щитка переводчика огня.
Наличие указанных конструктивных особенностей служило причиной образования трещин или создания предпосылок к этому при термической обработке деталей (закалке), нанесении защитных покрытий химическим способом, в частности оксидированием. Обнаруживались они несмотря на тщательный технический контроль, перед поступлением на конвейер сборки и в собранных изделиях при технической приемке на конвейере заказчика. Этому способствовали предусмотренные и не предусмотренные технологией правки деталей после закалки, в том числе и в процессе сборки.
По затвору в качестве предупредительного мероприятия была введена радиусная разрядка у основания левого упора, которая хотя и существенно повысила живучесть детали, но твердых гарантий полного исключения трещин не давала. Подобная радиусная разрядка как метод упрочнения была введена также у основания боевых упоров вкладыша коробки, под заплечиками курка, в стенке отверстия рамы под хвостовик затвора.
В числе других причин понижения живучести деталей были недостаточные прочностные качества применяемых материалов, отдельные отступления по соблюдению установившихся технологий по механической, термической и химической обработке деталей, а также многие другие факторы случайного или неслучайного проявления, характерные для крупносерийного поточно-массового производства.
Практика производства АК-47 конца 50-х годов знает случаи поломки пружин, связанные с низким качеством патентированной проволоки, поставляемой одним из металлургических заводов (арх. № 2695-58, стр. 1, 31). Поломки пружин магазина происходили в процессе технологической правки в сборочной мастерской, возвратных пружин – в процессе стрельбы. Проволока, из которой изготовлялись пружины, обладала склонностью к потере эластичности и переходу в хрупкое состояние в условиях низкотемпературного отпуска или длительного хранения при повышенной температуре.
Испытания на скручивание при входном контроле обнаруживали неоднородность качества проволоки по длине бунта. Была уточнена технология патентирования проволоки на Ижевском металлургическом заводе и контроля ее качества испытаниями на скручивание в состоянии после низкотемпературного отпуска. При этом был использован положительный опыт Белорецкого завода, проволока которого обладала высокими прочностными свойствами.
По часто появляющимся при испытаниях трещинам, причины которых по результатам исследований становились известными, производством принимались необходимые меры и достигались определенные положительные результаты. Более сложной была предупредительная борьба с трещинами, имевшими весьма редкое или вообще разовое проявление (колодка приклада, прицельная колодка, ствол у газовой каморы).
В связи с трудностями полного исключения трещин, появлявшихся на некоторых деталях (затвор, курок, спусковой крючок и др.) на пределе исчерпания живучести системы, завод выступал перед Головным заказчиком с предложением не считать в данном случае дефект браковочным признаком при технической приемке предъявляемых партий изделий. В качестве обоснования своего предложения приводился тот факт, что при продолжении испытаний деталей с трещинами далеко за пределы установленной нормы долговечности поломок не происходило (арх. № 2512-56, стр. 197).
Данное предложение не получило одобрения, видимо, и по той причине, что подобные «привилегии» для отдельных деталей автомата шли в разрез с едиными общепринятыми принципами дефектации оружия как в сфере производства, так и при его войсковой эксплуатации.
Вопрос о трещинах, как и в отношении снижения норм живучести автомата по поломкам деталей, частично получил разрешение в модернизированном АК, где в отдельных местах некоторых деталей стали допускаться микротрещины в конце живучести системы, обнаруживаемые не простым визуальным осмотром, а с помощью специального приборного оборудования – магнитного дефектоскопа. Однако и по облегченному АКМ, в котором, естественно, запас прочности деталей стал ниже, впоследствии был поставлен вопрос о повышении долговечности этой системы до уровня ее предшественника.
Решение постоянно действующей и никогда не затухающей проблемы живучести деталей производством обеспечивалось не только за счет конструкторских или чисто технологических мероприятий. Когда указанные меры, будучи полностью исчерпанными, оказывались недостаточными, завод прибегал к замене применяемых материалов более качественными.
Во многих случаях задача решалась путем применения более качественных высоколегированных сталей, но такой материал был в дефиците и, кроме того, дорогой по стоимости, что было хорошо известно и конструкторам – разработчикам оружия, в связи с чем при назначении материала в процессе проектирования деталей ими соблюдался принцип разумной достаточности.
Для стальных деталей автомата, испытывающих сложные ударно-динамические нагрузки, наиболее «ходовым» материалом, буквально выручавшим производство в трудные критические моменты, была весьма дефицитная высоколегированная сталь 25ХНВА, содержащая около 4 % никеля и 1 % вольфрама (арх. № 40–61, стр. 87). Замена на более дешевую сталь была сложным проблемным вопросом, особенно для таких деталей с предельно ограниченной живучестью и на высоколегированной стали, как курок, выбрасыватель, ударник.
Легче решался вопрос с сухарем, по которому простая углеродистая сталь оказалась менее чувствительной к закалочным и оксидировочным трещинам, чем высоколегированная 35ХГСА. По другим деталям потребовались длительные поиски металловедов и металлургов. Постоянная помощь оказывалась оружейным заводам специализированными в области технологий научными организациями и металлургическими заводами.
В конце 50-х годов положение усложнилось тем, что министерство от оружейных заводов требовало в ограниченные сроки снизить нормы расхода сталей и сплавов с содержанием никеля выше 2 % (арх. № 2716-59, стр. 2). Это касалось и изделий АК всех модификаций. К этому времени только затворную раму удалось перевести на сталь 30ХНВА с пониженным содержанием легирующих элементов, а такие детали, как курок, затвор, ударник, выбрасыватель, оси УСМ, продолжали изготавливаться из стали 25ХНВА. Попытки использовать стали 35ХГСА и 40Х для изготовления рамы и затвора не увенчались успехом. Сталь 40Х могла применяться только для изготовления вкладыша.
По новому ГОСТ 4543-57, выпущенному вместо № 4543-48, сталь 25ХНВА для изготовления деталей оружия предусмотрена не была. В качестве ее заменителя была рекомендована еще не проверенная на деталях автомата сталь 30ХН2ВФА, включенная в новый ГОСТ, и сталь 30ХНВА, включенная в ведомственную нормаль. По результатам испытания деталей на живучесть указанные стали применения не нашли. В чертежах продолжала оставаться сталь 25ХНВА, на которой была отработана живучесть деталей новых модификаций системы АК, поскольку приказ ГКОТ по применению новых сталей на завод поступил уже после завершения работ с этими образцами.
Спасительным стало предложение организации Ф.А. Куприянова по применению для изготовления деталей стрелкового оружия (за исключением стволов) дешевой высокопрочной низколегированной стали 30ХРА, не содержащей дефицитных легирующих элементов (арх. № 2658-58, стр. 129). После широких испытаний сталь 30ХРА была одобрена заказчиком и из нее стали изготовляться в массовом производстве автомата 9 деталей подвижной системы и УСМ, включая и наиболее металлоемкие – затворная рама и затвор (арх. № 41–61, стр. 129). В дальнейшем указанная сталь нашла применение и в других образцах оружия. Организация Куприянова совместно с Ижевским металлургическим заводом Д.Ф. Савельева в середине 50-х годов проводила поиски и других низколегированных сталей для изготовления деталей автоматического оружия взамен сталей 50 и 50А, обладающих недостаточной прокаливаемостью при термической обработке (арх. № 2622-56, стр. 1).
По результатам этих работ в ствольном производстве АК-47 и при изготовлении других деталей стали применяться стали 50Р и 50РА, легированные бором (Р) и с уменьшенным содержанием вредных примесей (А).