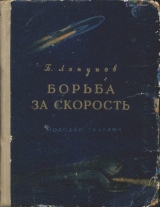
Текст книги "Борьба за скорость"
Автор книги: Борис Ляпунов
сообщить о нарушении
Текущая страница: 8 (всего у книги 17 страниц)
Сначала думали, что в этом виновата сварка. Эту мысль, однако, скоро пришлось оставить: разрывы появлялись и там, где швов поблизости не было. Решили сделать стенки потолще, но… аварии продолжались.
Тогда стали внимательно исследовать места поломок и заметили, что металл там уставал, прочность ею падала. Наблюдения за давлением воздуха, идущею из компрессора, объяснили причину усталости металла. Оказалось, что воздух пульсировал, давление его менялось много раз в секунду. Это и было причиной поломок. Когда воздушную камеру сделали из мягкой стали, лучше переносящей частые колебания давления, аварии прекратились, и срок службы камеры намного увеличился.
Тщательно, шаг за шагом изучают инженеры работу камеры сгорания. И если современные газотурбинные двигатели служат десятки и сотни часов, этим могут гордиться наряду с конструкторами, металлургами и инженеры-химики, физики, теплотехники – творцы «огненного дыхания» газовой турбины.
Наиболее ответственная деталь турбины – это лопатка.
Каждая лопатка растягивается центробежной силой, превосходящей ее вес в десятки тысяч раз. Да вдобавок она еще все время находится в потоке горячих газов и нагревается до высокой температуры. Лопатка может поэтому «поползти», удлиниться и довольно значительно. Тогда она заденет за кожух и авария неизбежна.
Даже камеру сгорания, где непрерывно бушует поток раскаленных газов, нельзя сравнить по условиям работы с турбиной. Тем более нельзя сравнить с нею компрессор, хотя как в турбине, так и в компрессоре, развиваются большие центробежные силы.
Турбине приходится гораздо тяжелее, чем другим частям газотурбинного двигателя – вот какой можно сделать вывод. Значит, материал для нее должен быть особо прочным и способным сохранять свои свойства при высоких температурах.
Чтобы яснее себе представить, насколько трудной была эта задача, ознакомимся с требованиями трех инженеров.
Инженер-металлург скажет нам: металл для турбины при высоких температурах не должен разрушаться и изменять своих свойств.
Инженер-технолог предъявит свои требования: нужно, чтобы металл для турбины можно было ковать, прокатывать, отливать, сваривать и обрабатывать на станках.
А инженер-конструктор потребует, чтобы этот самый металл выдержал как можно более высокую температуру: чем выше температура, тем лучше работает двигатель.
Когда изыскания материалов для газовых турбин еще только начинались, существовали сплавы, выдерживающие температуру «всего» около 500° и пригодные только для паровых турбин.
Дальнейшая работа над этими сплавами была по существу сражением за каждый лишний десяток градусов. Об этой борьбе мы с вами говорили, когда речь шла о рождении материалов. Правда, в авиационных турбокомпрессорах, турбины которых работают на отходящих газах двигателя, температура доходит до тысячи градусов. Но их жизнь коротка. Для газотурбинных же двигателей долговечность – важнейшее требование. Срок их службы должен исчисляться сотнями часов, а у газовых турбин электростанций – десятками тысяч часов.
Поведение металла стали исследовать при постепенно повышающейся температуре и больших центробежных нагрузках.
Перепробованы были всевозможные варианты различных добавок, которые могли бы придать сплавам нужные свойства, и в результате удалось создать жаропрочные сплавы для газовых турбин.
В настоящее время для изготовления лопаток применяются сплавы никеля и хрома, а также сталь с добавками никеля, хрома и марганца.
Диски турбин, которым приходится работать в более легких условиях, делаются из стали, содержащей небольшие добавки хрома, марганца, никеля, молибдена.
Для лопаток турбины испытывались и другие материалы. В Германии пытались, например, из-за недостатка дефицитных металлов применять керамические материалы и даже армированный фарфор с металлической решеткой внутри для увеличения прочности, подобно железобетону. Они смогли бы выдержать значительно более высокую температуру, чем металл. Однако прочную керамическую лопатку, не разрушающуюся при огромных центробежных нагрузках, создать нелегко, и дальше опытов пока дело не пошло.
Для уменьшения нагрева лопатки можно устроить полыми и через них пропускать поток воздуха.
Охлаждающий воздух подводится к диску турбины, омывает его с двух сторон, а затем поступает внутрь лопатки через отверстие у ее основания. Полые лопатки изготовлять, конечно, сложнее, чем сплошные. Зато при опытах удавалось повысить таким образом допустимую температуру газов до 1000° и более.
Очень сложно охлаждение лопаток жидкостью.
Можно применить газовое охлаждение, создавая защитную газовую пленку со стороны нагреваемой поверхности. Лопатка изготовляется тогда из пористого материала, полученного спеканием металлической пудры. Газообразный водород или азот под давлением вытесняется на поверхность и защищает лопатку от перегрева.
На бумаге все это выглядит, конечно, несравненно проще, чем на деле. Пока что применялось лишь воздушное охлаждение лопаток авиационных газотурбинных двигателей.
Теперь предоставим слово технологам.
Как сделать лопатку точно и быстро, придав ей нужную форму, и обеспечить высокую чистоту поверхности? Типичная лопатка турбины – это изогнутая поверхность с хвостовиком, которым она вставляется в паз на диске.
Такая форма нужна для плавного обтекания газовой струей. Так как при этом струя еще и поворачивает, то возникает сила, действующая на лопатку и движущая турбину.
Для обработки лопаток сложных форм сконструировали специальные станки; существовавшие ранее не удовлетворяли инженеров. Новые станки позволили вести обработку значительно быстрее.
Но на этом не остановились. Лопатки изготовляют также штамповкой и литьем высокой точности – прецизионным.
Для проверки, насколько правильно они сделаны, применяются различные способы. Расскажем об одном из них, где используется оптика, своеобразное кино.
На экране вычерчена лопатка в профиль. Настоящую лопатку ощупывают наконечники, двигающиеся один сверху, другой снизу. Тени их видны на экране. И если наконечники точно идут по изображению на экране, лопатка сделана правильно.
Далее надо изготовить турбинный диск. Для него тоже разработаны жаропрочные сплавы.
Затем диск и лопатки надо соединить между собой. Их можно соединить, например, «елочкой». Хвостовик лопатки делают с трапецевидными зубцами, а в ободе диска турбины устраивают вырезы такой же формы, так что лопатка плотно входит в диск. Иногда лопатки прикрепляют сваркой.
Теперь остается укрепить направляющие лопатки на кожухе турбины. Они неподвижны и размещены между каждой парой ступеней турбины – рядов лопаток. Есть они и в осевом компрессоре. Их назначение – выпрямить поток воздуха или газа при ею движении от ступени к ступени.
Когда турбина готова, смонтирован компрессор, камеры сгорания и все вспомогательные механизмы, можно приступить к испытаниям.
Как же производятся испытания газотурбинных двигателей?
Мы в испытательной лаборатории, в кабине наблюдения, напоминающей дот.
Это железобетонная труба, с полуметровыми стенками, со звуконепроницаемой прослойкой, с двойными смотровыми окнами из бронестекла.
Закрытые переходы соединяют кабину с машинными залами и другими помещениями лаборатории – для защиты от шума и возможного взрыва или пожара.
Из кабины наблюдения управляют на расстоянии всеми установками. Приборы показывают, что происходит в машинном зале.
Обороты, давления, температуры, скорости – все это мы узнаем, не выходя из железобетонной крепости.
На силовой станции лаборатории имеется несколько мощных паровых турбин, которых хватило бы для целого миноносца.
Турбины вращают компрессоры, подающие сжатый воздух, и те компрессоры, которые надо испытывать.
На прочном железобетонном фундаменте установлена газовая турбина. Сжатый воздух идет в камеру сгорания, и горячие газы поступают в турбину. Выхлопные газы из нее отводят по круто изогнутой трубе, чтобы быстрее затормозить поток.
Турбины с очень большим числом оборотов – свыше 30 тысяч – испытывают на разрушение в толстостенных стальных камерах.
Растут обороты… Диск вращается все быстрее, пока, наконец, не разлетается на куски. Обломки ударяются в стенку камеры и замыкают контакт. В тот же момент включается яркая лампа и кинокамера, приспособленная для съемки с большой скоростью. На снимках видно, где началось разрушение, какое оно. Счетчик показывает, сколько оборотов выдержала турбина.
Отдельно испытываются на разрушение и лопатки турбин. Лопатку помещают между двумя электромагнитами. То в один, то в другой магнит посылают ток. Магниты попеременно ее притягивают, пока от быстрой вибрации она не разрушится.
В лаборатории испытания камер сгорания воздуходувки подают воздух, а мощные насосы – топливо из подземного хранилища. Точные приборы отмечают расход топлива и бдительно следят за поведением пламени. Затухает пламя – и они автоматически выключают подачу топлива, чтобы случайно не взорвались остатки его в камере, стенки которой сильно нагреты.
Испытываются и другие части газотурбинного двигателя – подшипники, регуляторы, топливная и масляная аппаратура, а затем и весь двигатель в целом. Его устанавливают на стенде. Две-три сотни измерений одновременно приходится производить при испытаниях.
Авиационную турбину можно заставить работать на разных «высотах» в «высотной» камере, откуда постепенно выкачивается воздух.
Можно заставить двигатель работать во влажном и сухом воздухе, чистом и засоренном, теплом и холодном.
Все это нужно для того, чтобы знать, как поведет он себя в самых различных условиях.
Но вот испытания окончены, устранены все неполадки.
Остается еще один серьезный экзамен – проработать несколько часов подряд, как на настоящем самолете: «набирать высоту», «летать», «снижаться», давать самую малую и самую большую мощность.
Устраивают и летные испытания на «летающих лабораториях» – специально оборудованных самолетах.
Затем двигатель полностью разбирают и осматривают, изучают «отчет» о его работе – записи приборов.
И если все в порядке – он получает «путевку в жизнь».
Ведется работа и над другими газовыми турбинами – для железнодорожного, речного и морского транспорта.
Пока газовая турбина на электростанции еще помощник паровой. Но газотурбостроение шагает вперед, и скоро мы увидим газовую турбину там как полноправного хозяина. Это не значит, конечно, что в будущем паровая турбина не будет применяться в энергетике.
Не надо забывать, что теперь электростанции используют дешевое – твердое топливо, а газовые турбины пока нуждаются в более дефицитном – жидком топливе.
Вот почему газовая турбина только тогда будет широко применяться на фабриках энергии, когда она сможет работать на твердом топливе – угле.
В нашей стране ведутся успешные работы по подземной газификации угля. Советские ученые и инженеры построили первые станции подземной газификации, снабжающие промышленность газом. У нас впервые была построена турбина для работы на газе, получаемом из угля.
И недалеко то время, когда осуществятся пророческие слова Ленина:
«Газ приводит в движение газовые моторы, которые дают возможность использовать вдвое большую долю энергии, заключающейся: в каменном угле, чем это было при паровых машинах. Газовые моторы, в свою очередь, служат для превращения энергии в электричество, которое техника уже теперь умеет передавать на громадные расстояния».
Газовая турбина на каменном угле – дешевом топливе – будет двигателем будущего.
Быть может, газовая турбина будет одним из первых двигателей, использующих атомную энергию. Возможно, со временем турбинные установки, работающие на «атомном» горючем, будут широко применяться в промышленности и на транспорте.
Атомная энергия даст тепло, нужное для получения пара или горячего воздуха, питающих паровые или газовые турбины. Турбины смогут вращать воздушные винты, гребной винт судна, колеса локомотива или автомобиля.
Газовая турбина – новая глава в истории тепловых двигателей. Эта глава еще только начинается, и невозможно предугадать, сколько трудностей предстоит преодолеть, пока мы дойдем до последней ее страницы.
Нужно будет строить мощные турбины для электростанций, для промышленности и транспорта, совершенствовать их, создавать турбины на твердом топливе.
Газовая турбина, дающая нам новые скорости и мощности, займет вскоре свое место в новой технике нашей страны, победоносно строящей коммунизм.
Продолжается борьба за скорость и в других областях техники, создающих двигатели для наших машин.
Во многих машинах встретим мы электромотор – основной промышленный привод. Огромные станки и портативный ручной инструмент, центрифуга и гироскоп, шлифовальный шпиндель и веретено приводятся в движение электромотором.

Ручные инструменты со встроенными электромоторами.
Как же электротехники заставили якорь электромотора делать те тысячи и десятки тысяч оборотов в минуту, которые нужны быстроходным машинам? Ведь еще сравнительно недавно можно было говорить всего о 3 тысячах оборотов – не более.
Быстроходный электромотор работает на токе повышенной частоты. 50 раз в секунду меняет свое направление ток в осветительной сети. 50 периодов в секунду – его частота. 3 тысячи оборотов дает мотор на токе такой частоты.
Электротехники повышали частоту в 2, 3, 4 раза – и во столько же раз вырастало число оборотов мотора. А вместе с тем конструкторы снижали вес мотора, уменьшали его размеры. Быстроходный мотор более компактен и легок, чем тихоходный. Почти в 8 раз меньше стал весить мотор, работающий на токе повышенной частоты.
И это позволило мотору забраться туда, куда он раньше попасть не мог, – в ручной инструмент. Это позволило ему «врасти» в быстроходные машины – появились электромашины, где мотор и машина соединились в одно целое.
Электрошпиндель и электродрель, электросверло и электрометчик, электрогравировальный и полировальный инструмент применяются в цехах автомобильных, самолетных и других заводов.
Быстроходные электромоторы работают теперь в станках для обработки дерева и металла.
Инженерам-электрикам пришлось, создавая такие моторы, решать сложные задачи. Раньше, например, им не нужно было особенно заботиться об охлаждении – мотор не нагревался слишком сильно. А теперь быстроходный – мотор так нагревается, что иногда требуется охлаждение водой.
Чтобы корпус мотора быстрее охлаждался, его делают снаружи ребристым. Ребра увеличивают поверхность, а это ускоряет отдачу тепла в воздух. Устраивают «вентиляцию»: канавки для воздуха в якоре мотора, вырезы-окна для «проветривания» в корпусе электромашины. На ее вал, кроме того, сажают вентилятор. Сама себя обдувая воздухом, она лучше охлаждается.
Потребовалось разработать надежные подшипники для быстроходных моторов, обеспечить их точную установку, хорошую смазку, обезопасить эту смазку от перегрева.
И появились моторы невиданных еще скоростей, дающие 18 тысяч, 48 тысяч оборотов в минуту. Созданы промышленные образцы моторов на 120 тысяч оборотов.

Сверхбыстроходный электромотор на 120 000 оборотов в минуту.
Сверхскоростные моторы – большое достижение нашей техники. Из лабораторий и институтов они придут на заводы.
Высокие и сверхвысокие скорости – это новый рост производительности труда, новые технологические процессы, которых не было раньше.
Для того чтобы получить большие окружные скорости, можно воспользоваться не одним электрическим током.
Там, где ток, – там и нагрев. А где нагрева быть не должно, нужен и другой привод, не электрический, а пневматический.
Силой воздушной струи воспользовались инженеры, чтобы получить огромные числа оборотов. Очень легкие воздушные турбинки небольших размеров вращают шпиндели шлифовальных станков и авиационные гироскопы. Их широко применяют и в ручных инструментах.
Турбинный диск с лопатками делается из алюминиевого сплава. Прочность и легкость сочетает в себе такой сплав. Он выдерживает нагрузки от центробежной силы при вращении маленькой турбинки со скоростью от 10 тысяч до 100 тысяч оборотов в минуту – в разных машинах по-разному.
При работе турбинка почти не нагревается. В этом ее преимущество перед электромотором. Но есть у нее и недостаток – она не выдерживает строго постоянного числа оборотов. Ее и применяют там, где с этим можно мириться.
Подшипники, приспособленные для больших скоростей, точно изготовленные, с надежными сепараторами, стойко выдерживают огромные числа оборотов. В воздушных турбинках встречаются и упрощенные быстроходные подшипники без сепараторов и внутренних колец. В них можно применить также подшипники с газовой смазкой.
Особо быстроходные турбинки для центрифуг дают, как и электромоторы, до 150 тысяч оборотов при подшипниках с жидкой смазкой.
Всего несколько капель смазки в час достаточно для таких подшипников. Ее можно подать и без масленки: струя воздуха большой скорости распыляет смазку и одновременно охлаждает подшипник.
Воздух вращает турбину, помогает смазке и может сам служить для смазки.
При небольшом диаметре вращающегося ротора можно получить чрезвычайно большие, сверхвысокие скорости – до четверти миллиона оборотов в минуту!
А в одном из опытов с крошечным ротором диаметром около сантиметра с газовой смазкой удалось получить свыше миллиона оборотов в минуту!
Это показывает, как велик может быть рост скоростей. Но, конечно, лишь в опытах с миниатюрными приборами можно пока что получать такие сверхвысокие скорости вращения.
Строились воздушные турбинки, рассчитанные на 600–700 тысяч оборотов. Но чем больше оборотов, тем сильнее закручивается воздушный поток, тем труднее становится устойчивая работа. И не выдерживает турбинка, если увеличивается нагрузка, – падает число оборотов.
Практически нам нужны пока обороты в десятки и одну-две сотни тысяч в минуту. Их обеспечивают электромотор и воздушные турбинки там, где нагрузки невелики. Для больших нагрузок на больших скоростях нужны уже не воздушные, а иные турбины – паровые и газовые, вращаемые силой струи пара или газа.
Быстроходный привод – часть высокоскоростной машины, ее сердце.
Какую бы из отраслей современного машиностроения мы ни взяли, везде создание быстроходного привода есть часть – и важнейшая – борьбы за скорость.
Электрические, воздушные и тепловые двигатели служат приводами самых разнообразных быстроходных машин, – от электрического генератора до шлифовального станка, от центрифуги до переносного ручного инструмента, от компрессора до гироскопа.
Нужно не только получить высокую скорость, но и передать ее, чтобы заставить работать все эти машины.

Высокоскоростной внутришлифовальный электрошпиндель.
Машина, по классическому определению Маркса, состоит из трех частей: двигателя, передаточного механизма и машины-орудия.
Двигатель создает движение, передача передает его, а орудие использует, чтобы выполнять полезную работу.
И нужно соединить генератор с паровой турбиной, электромотор – с центрифугой или станком, гироскоп – с воздушной турбинкой, компрессор – с газовой турбиной, чтобы использовать полученное с таким трудом вращение.
Для этого и нужна передача.
Мотор и машину соединяют ремнем, надетым на шкивы, – колеса с ободом. Такую простую передачу видели, конечно, все. Она исправно работает на небольших скоростях, но капризничает, если скорости растут.
Ремень начинает быстро истираться. Он «проскальзывает», «буксует», как колеса автомашины на скользком месте, вытягивается и провисает. От былого натяжения не остается и следа.
Вдобавок, вокруг быстро вращающегося шкива возникают воздушные вихри, сильно мешающие работе. С ними трудно справиться.
Сопротивление воздуха вообще ощутительно мешает при больших скоростях. Опытным путем установлено, что при 2 600 оборотах в минуту мощность привода расходуется так: на борьбу с трением в подшипниках 3,5 процента, а на борьбу с сопротивлением воздуха – все остальное, 96,5 процента! Комментарии, как говорят, излишни.
Лишь примерно до 100 оборотов в минуту с сопротивлением воздуха можно не считаться. Но при сотнях и тысячах оборотов – это серьезный противник.

Шлифовальный шпиндель с воздушной турбинной.
Вот что произошло, когда испытывали впервые новую быстроходную передачу.
Ремень отказывался совсем работать без поддержки натяжным роликом. Он беспомощно провисал, быстро растягиваясь и не поспевая за шкивом, буксовал, а от трения о шкив нагревался так сильно, что резина на нем плавилась. Закапризничав, ремень не хотел сцепляться со шкивом, отпрыгивал от него и, провисая все больше и больше, задевал верхней частью нижнюю и рвался мгновенно.
Стоило ремню чуть-чуть перекоситься, как он начинал задевать за выступ – бортик шкива, и вскоре края его превращались в лохмотья. В местах, где были швы, появлялись обрывки ниток. Быстро истираясь, ремень рвался сначала с краев, а затем и весь, как будто он был сделан не из прочного материала, а из бумаги.
На большой скорости разрыв ремня грозит большими осложнениями.
Недаром приходилось помещать при опытах всю передачу в специальном помещении, а за работой ее следить на расстоянии по приборам, как будто испытывался какой-нибудь новый двигатель, вот-вот готовый взорваться.
Опыты показали, как построить быстроходную ременную передачу. Начали с того, что стали испытывать, какие ремни можно для нее применить. Тут ведь не всякий ремень годится.
Ремень нужен прежде всего прочный.
Это, однако, не значит, что можно сделать его толстым. Взять, скажем, да устроить слоеным из нескольких лент. Он должен быть прочным, но тонким и легким. Легкость уменьшает центробежную нагрузку.
Центробежная сила зависит не только от скорости, но и от удельного веса материала – чем он меньше, тем меньше и эта сила.
Изнашиваться быстро ремень не должен. И вытягиваться тоже – иначе и прочный ремень забастует и работать не сможет.
Про скольжение также забывать нельзя. Это один из главных недостатков обычного ремня, если его заставить вращаться с большой скоростью. Нужно, чтобы ремень со шкивом сцеплялся надежно.
Опыты делали с самыми различными материалами: кожей и резиной, кордом и хлопчатобумажной тканью, шелком и трикотажем. Ремни сшивали или склеивали. И лучше всех оказался ремень из ткани или шелка, покрытый лаком.
Но и другие ремни тоже работают неплохо – каждый для своих условий. Скорость примерно до 45 метров в секунду выдерживает кожаный ремень. Тонкий прорезиненный ремень из ткани может служить на скоростях до 50 метров в секунду, а лакированный шелковый или тканевый ремень без швов работает и при 70 метрах в секунду. Такой ремень применяют в быстроходных шлифовальных станках.
Прочным должен быть не только ремень, но и шкив. Стальной шкив выдерживает скорость 150 и даже 200 метров в секунду.
Затем стали искать способ борьбы с провисанием ремня. Какой бы прочный и хороший он ни был, провисания, как и трения, не избежать. Надо постараться сделать провисание как можно меньше. Для этого ремню в помощь дают специальный натяжной ролик.
В быстроходных передачах призвали для этого на помощь и сам мотор. Его устанавливают на площадке, которая может поворачиваться. Под тяжестью мотора площадка опускается, и ремень натягивается.
Сопротивление воздуха уменьшали довольно простым способом, преграждая воздуху путь в передачу, на которую надевали кожух. Шкивы делали сплошные, без спиц.
Пытались не только передачу, но и саму машину сделать такой, чтобы сопротивление воздуха было наименьшим.
Самолету, его частям придают удобообтекаемую, каплеобразную форму. Похож на каплю быстроходный гоночный автомобиль.
Пробовали и шпиндель быстроходного шлифовального станка сделать похожим на каплю. А такой особо быстроходный прибор, как гироскоп, помещают иногда в специальную камеру, откуда выкачан воздух: тогда уж он вообще не страшен.
Быстроходные ременные передачи сейчас применяют в станках, центрифугах и других машинах.
Наряду с ними все шире встречаются в технике машины, где нет ременных передач, где машина и двигатель – одно целое.
Это электромашины, такие, например, как электрошпиндель, в котором электромотор – часть конструкции самой машины.
Это такие машины, как шлифовальная воздушная турбинка, электросверло, в которых привод и машина – одно неразрывное целое.
В них для передачи вращения вал двигателя и вал машины прочна соединяют быстроходной муфтой.
Муфты бывают разные – жесткие и эластичные, пружинные и зубчатые, магнитные, гидравлические и другие, но одинаково в них одно: они связывают оба вала либо наглухо, либо так, чтобы, допуская небольшие смещения, не разорваться, если такое смещение случится.
Муфты должны быть прочными и надежно работать при больших окружных скоростях. В них пришлось отказаться от прокладок из резины или кожи.
В муфтах высокоскоростных приводов отказались от соединения из двух половин, а соединяют прямо один вал с другим: в одном валу выступ, в другом углубление, как отвертка и вырез в головке винта. Сверху надевают металлическую втулку, плотно охватывающую концы валов. Такая муфта выдерживает до 100 тысяч оборотов в минуту.
Но если один вал соединяется прямо с другим, то нельзя ли и вовсе избежать муфты – вместо двух валов сделать один?
Так нередко делают в небольших быстроходных машинах – шлифовальных шпинделях. На конце вала воздушной турбинки или электромотора помещают шлифовальный круг.

Области применения высокоскоростных приводов.
Мы получили вращение и передали его. Сколько оборотов дал привод, столько же ременная передача или муфта сообщили и машине. Сколько оборотов получено, столько и передано.
Бывают, однако, в технике случаи, когда требуется получить одно, а передать другое число оборотов, иначе говоря, замедлить или ускорить вращение. Это может делать ременная передача. Это делает и зубчатая передача – редуктор.
Авиационная газовая турбина вращается со скоростью, скажем, 15–18 тысяч оборотов. Но если она служит приводом воздушного винта, то такая большая скорость для винта не годится. Винт не выдержит ее и разорвется в куски от огромной центробежной нагрузки. Поэтому обороты нужно уменьшить. Между валом турбины и винтом ставят редуктор.
Редуктор понижает обороты газовой турбины, вращающей генератор электрического тока. Такой редуктор нужен при передаче вращения валу станка, насосам или судовым винтам, колесам паровоза или автомобиля.
Но иногда бывает нужно не понижать, а повышать обороты.
На высотных поршневых авиационных моторах устанавливают нагнетатели, помогающие мотору «дышать». Воздух сжимается крыльчаткой, вращающейся с большой скоростью. Вращаясь, крыльчатка отбрасывает воздух от центра диска, и он сжимается центробежной силой.
Чтобы сжать воздух, нужна скорость 20–30 тысяч оборотов в минуту, а вал поршневого мотора делает всего около 3 тысяч оборотов. И крыльчатку соединяют с валом через зубчатую передачу – редуктор, повышающий обороты в несколько раз.
Быстроходные редукторы широко применяются теперь в технике. Но и здесь большие скорости поставили новые трудности перед инженерами.
Малейшая, вполне допустимая раньше неточность в изготовлении деталей становится грозным врагом при больших скоростях.
Редуктор ведь состоит из нескольких зубчатых колес, и дефекты каждой шестерни сказываются на работе всех остальных. В конце концов может случиться, что редуктор не будет работать.
Шестерни при работе нагреваются, смазка разжижается, увеличивается износ зубьев. Их «заедает», начинается «шелушение», истирание, скалывание, излом металлических поверхностей. В трещинки может попасть масло – и подобно тому, как это бывает в подшипнике – расклинить и разрушить поверхность.
Кроме того, шестерни, даже и весьма точно изготовленные, сильно шумят при работе, потому что под нагрузкой они изменяются в размерах. Хотя эти изменения ничтожно малы, но их бывает достаточно, чтобы появился шум.
Борьба с шумом быстроходных зубчатых передач стала серьезной проблемой.
Инженеры разрабатывают конструкцию редукторов, шумящих как можно меньше, подбирая наиболее благоприятные размеры колес, зубьев, их форму.
Иногда, при небольших нагрузках, применяют бесшумные шестерни из пластмассы.
Испытания шестерен помогают увидеть, как распределяются напряжения в местах зацепления зубьев, как они там концентрируются. Это помогает инженерам проектировать шестерни не «громкоговорящие», а шумящие как можно меньше.
Теперь существуют редукторы, где окружная скорость доходит до 140 метров в секунду. Они могут передавать мощность в несколько десятков тысяч лошадиных сил.
Тщательным изготовлением, испытаниями и опытами, повышением качества материалов добиваются надежной работы быстроходных зубчатых передач.
Быстроходные передачи для быстроходных станков, приборов, механизмов – это часть борьбы за скорость, идущей в машиностроении и металлообработке, приборостроении и авиации. От них во многом зависит наилучшее использование мощности сверхскоростных двигателей – турбин и электромоторов, все шире применяющихся в технике больших скоростей.
