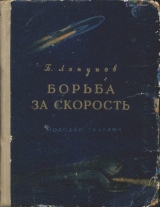
Текст книги "Борьба за скорость"
Автор книги: Борис Ляпунов
сообщить о нарушении
Текущая страница: 3 (всего у книги 17 страниц)

РОЖДЕНИЕ МАТЕРИАЛА
Бумага, говорят, все стерпит! На бумаге любую машину построишь.
Как-то раз видел я человека, который строил на бумаге машины. Рисовал он на листочках необыкновенные сверхскоростные самолеты, сверхглубоководные подводные лодки, фантастические межпланетные корабли, машины чудовищных скоростей…
Тщательно вычерченный и разрисованный цветными карандашами, этот сказочный мир машин не похож был на сказку. Казалось, стоит только воплотить его в металл – и он оживет. Помчатся, как метеоры, самолеты и ракеты, с неслыханной скоростью завертятся станки и турбины, на дно океана отправятся «Наутилусы» наших дней…
Человека, о котором я рассказал, я не выдумал. Он сидел рядом со мной в читальном зале библиотеки и строил свой бумажный мир машин. Наверное, это был художник, придумывавший иллюстрации к какому-нибудь научно-фантастическому роману.
Автор такого романа обязательно расскажет в нем о «новом сплаве огромной прочности», который инженеры будущего создали для новых чудесных машин. И он будет прав. Новые машины, машины больших, скоростей, – это и новые металлы.
Не только машины из фантастического романа, а и машины инженера-проектировщика останутся на бумаге, если не из чего будет их построить.
В истории техники подобные случаи бывали. Почти полтораста лет назад изобрели новый двигатель – газовую турбину. Вот его идея: струя горячего газа вращает турбинное колесо с лопатками. Простой задуман был двигатель: ни цилиндров с поршнями, ни шатунов с кривошипами, ни парового котла. И быстроходный в то же время, потому что в нем одно только движение – (вращение.
Однако прошло целых сто лет, прежде чем построили первую такую турбину. И еще около полувека потребовалось, чтобы поставить ее на ноги, сделать полноправным двигателем в технике.
Почему же так много времени пошло на это?
Одна причина в том, что такой двигатель не сразу понадобился. Пока старые двигатели хорошо служат, пока нет нужды в новых, они и не появляются. Но была и другая важная причина: если бы даже и захотели, не из чего было бы построить новый двигатель. Для него нужны новые материалы – прочные и в то же время жаростойкие, чтобы выдержать большие нагрузки при высокой температуре.
А ведь даже всего полвека назад выбор у инженера был невелик: чугун, железо да обыкновенная сталь. Инженер сегодняшнего дня из них; мало что смог бы построить: для наших современных быстроходных машин эти материалы не годятся.
Почему? Чтобы на это ответить, нужно вспомнить о прочности.
Что такое прочность? И как ее оценить, как узнать, насколько прочен металл?
Дело, казалось бы, нехитрое. Веревка рвется, если ее с большой силой потянуть за концы.
На каждый квадратный сантиметр сечения веревки, когда ее растягивают, действует определенная сила – напряжение. Оно все возрастает, и наступает момент, когда внешние растягивающие силы становятся больше сил внутренних, сил сцепления молекул между собой. Веревка разрывается. Напряжение стало больше допустимого – того, которое материал еще выдерживает, не разрушаясь.
Нагрузки, которые приходится испытывать деталям машин, разнообразны: это и растяжение, и изгиб, и кручение, и сжатие. Все они вызывают напряжения в металле.
Можно рассчитать, какими будут эти напряжения. Но как узнать, выдержит ли их металл?
Здесь слово предоставляется теоретическим расчетам, которые проверяются опытом. Образец из металла укрепляется в зажимах испытательной машины. Растет напряжение. Сначала металл стойко сопротивляется нагрузке. Металлический стерженек слегка удлиняется, он как бы поддается силе, но еще крепка – связь между его частичками, еще велики внутренние силы. Потом металл перестает удлиняться, хотя нагрузка растет. В металле идут невидимые глазом процессы. И вдруг в одном месте, примерно в середине, он начинает утончаться и сразу рвется.
Отмечено напряжение, при котором разорвался образец. Это предел прочности. Зная его, конструктор сможет сделать машину прочной. Он так рассчитает каждую деталь, чтобы нигде действующее напряжение не превысило этого предела. Мало того, он намеренно обеспечит «запас прочности», сделает части машин более прочными, чем нужно.
Каким брать этот запас, вопрос далеко не праздный. Ведь расчетом всего не предусмотришь. Еще недавно зарубежные инженеры называли этот запас «коэффициентом незнания». Я не знаю, что может случиться, и потому застраховываюсь от аварии – вот что это значило.
А о прошлом и говорить не приходится. Громоздкие, тихоходные машины прошлого века, да и начала настоящего – вот результат такой перестраховки. Незнание – ее причина.
Однако случалось, что машины выходили из строя, хотя нагрузки не превышали допустимых, а запас прочности, казалось бы, гарантировал от неожиданностей. Части машин разрушались гораздо раньше, чем рассчитывали. Жизнь машины внезапно обрывалась.
Причину стали искать – и нашли в условиях работы самих машин.
Нагрузка не остается все время постоянной. Она меняется или по величине, или по направлению. Металл детали может, например, то растягиваться, то сжиматься и притом много раз за время работы машины.
Напряжения в лопатках турбин меняются в минуту от 3 до 200 тысяч раз!
И металл «устает». Слабые места – те, прочность которых ниже, чем у остальных, начинают сдавать. А такие слабые места всегда есть, потому что металл состоит из множества мельчайших кристалликов, которые не все одинаково прочно связаны друг с другом.
Стоит такому непрочному соединению разрушиться, и усталостная трещинка растет, пока, наконец, вся деталь не ломается.
Советские исследователи, изучавшие свойства металлов, пришли к выводу, что усталостная прочность зависит от многих причин, среди которых немалое место занимает тщательная обработка поверхности. И здесь слово предоставляется технологам, которые находят способы бороться с усталостью, упрочняя поверхность деталей.
Исследования советских ученых в области прочности имеют важнейшее значение в борьбе за долговечность машин.

В лаборатории прочности.
Без преувеличения можно сказать, что новая высокоскоростная техника во многом обязана своим рождением успехам науки о прочности металлов.
Из года в год, из десятилетия в десятилетие растут напряжения в машинах.
Еще сравнительно недавно мы имели дело с нагрузками в 1–2 тонны на квадратный сантиметр. А уже сейчас нагрузка выросла до 4 тонн, и не за горами время, когда и эта нагрузка увеличится еще в 2–4 раза.
Ведь непрерывно растут скорости в машинах. Их части двигаются иногда со скоростью винтового самолета. Пройдет еще немного времени, и они будут двигаться со скоростью реактивного самолета. И если бы инженер прошлого века попробовал построить современную машину, используя для этого обычные марки стали, железо и чугун, эта машина разлетелась бы на куски. Когда, например, работает мощная паровая турбина, на лопатки турбинного колеса действует сила в десятки тонн. Она стремится оторвать лопатки, разрушить турбинное колесо.
Однако металл турбины выдерживает эту огромную нагрузку. Он работает, кроме того, при высокой температуре – пар поступает на лопатки перегретым примерно до 500° и даже выше. Можно ожидать, что в ближайшие годы температура пара в турбинах возрастет до 700–800°, а газа в газовых турбинах – до 1000°.
Пар или газ разъедает металл, потому что действует на него химически. А когда пар остывает, мельчайшие водяные частички, несущиеся со сверхзвуковой скоростью, истирают металл, разрушая его.
Лопатки турбины могут к тому же вибрировать, колебаться с большой частотой, так как пар или газ поступает на них прерывистой струей.
Пожалуй, если бы я попробовал перечислить и объяснить все, что мы требуем от металла турбины, это заняло бы целую главу. А коротко это займет одну строчку: прочность – механическую, химическую, вибрационную, тепловую.
Таким прочным металлом располагает современный инженер.
Железо выдерживает напряжение всего 2 тонны на квадратный сантиметр. А теперь существуют сплавы железа – стали, выдерживающие 20 тонн на квадратный сантиметр. В 10 раз удалось увеличить прочность железа! Прочность легких авиационных алюминиевых сплавов в 8 раз больше, чем у чистого алюминия.
Сплавы жаропрочные переносят температуры до 1000°. Сплавы холодостойкие не теряют прочности при температурах, близких к абсолютному нулю, к минус 273°. Технике нужны сплавы для работы при давлении в сотни и тысячи атмосфер и при глубоком вакууме, когда давление близко к нулю, – и такие сплавы есть теперь.
Этот перечень можно значительно продолжить.
Словом, выбор у современного инженера неизмеримо больше, чем у его предшественников. Прочность – одно из главнейших свойств, важных для машиностроителя, – выросла у основных материалов в 5– 10 раз.
Как добилась техника таких успехов?
Учение о свойствах и поведении металлов стало путеводной звездой для металлургов, создателей новых сплавов. Новые способы исследования и испытаний дали им возможность заглянуть во «внутренний мир» металла. И все это позволяет ныне «управлять» металлом, менять его свойства сознательно, в нужную нам сторону.
Может быть, слово «управлять» и вызовет улыбку, когда речь идет не о машине, а о мертвом металле. Но какое еще слово могло бы так же точно выразить то, что творят металлурги!
В центробежных воздушных машинах (компрессорах) металл работает при десятках тысяч оборотов в минуту. Он обладает огромной прочностью при невысоких температурах.
В камерах сгорания ракетных двигателей металл работает при 1000°. Он жаростоек при небольших нагрузках, ведь камера неподвижна.
Но как сделать прочный металл жаростойким, а жаростойкий прочным? Как создать жаропрочный сплав, нужный турбинам?
60 тысяч оборотов в минуту и больше развивают опытные газовые турбины. При этом диски турбин раскаляются докрасна, так что светятся в темноте. Центробежная сила стремится разорвать диск, вырвать, из гнезд лопатки, расшвырять их, как камни из гигантской пращи.
Иногда случались такие аварии турбин, когда части машин находили за несколько километров от электростанций. Прочный металл, накаленный докрасна, перестает быть прочным.
История создания каждою нового сплава – это повесть о творческих исканиях, упорном труде целого коллектива людей и в то же время «коллектива наук», потому что в создании новых металлов принимают участие физики и химики, теплотехники и металловеды.
В каждом новом сплаве не только химические элементы. В нем: не только доли процента углерода и марганца, молибдена и кобальта, проценты хрома, никеля и вольфрама. В нем еще и другое, что не измеришь процентами, что не запишешь химическими формулами. Это новаторство советских инженеров, содружество людей науки и производства – великая сила нашею технического прогресса.
А о том, насколько успешен их труд, говорят Сталинские премии, каждый год отмечающие достижения ученых и производственников… В числе лауреатов Сталинских премий – создатели новых чудесных сплавов.
Мы научились управлять свойствами сплавов, создавать их «по заказу», чтобы строить множество нужных нам машин, которые работают все быстрее, которые не боятся самой тяжелой, самой трудной работы..
…Чудесный сплав! Пожалуй, раньше он и впрямь показался бы чудом.
Возьмем, например, тот же сплав для лопаток газовых турбин. Создать такой сплав – труднейшая задача.
Ведь это должен быть не только жаропрочный сплав, иначе говоря, прочный при нагреве. Он и на холоде должен быть прочным. А то может случиться, что нос вытащишь, хвост увязнет: металл, прочный на жаре, потеряет прочность на холоде, станет ломким, хрупким.
Сплав для лопаток должен иметь высокую «усталостную прочность», как можно меньше уставать.
Кончаются ли на этом требования к сплавам?
Нет.
Если пар разъедает лопатки, то о горячих газах, где мною к тому же кислорода, и говорить не приходится. Самый жаропрочный, с высокой усталостной прочностью сплав не выдержит, если попадет в струю горячего воздуха. Лопатки постепенно покроются окалиной. Окалина – язва на металле. Лишь благородные металлы избавлены от нее. Но не сделаешь же турбину из золота или платины! А другие металлы и сплавы окисляются. Этого нельзя допустить.
Но предположим, что с трудностями мы справились. Всё? Нет, далеко не все.
Надо помнить, что новый сплав придется обрабатывать – ковать, штамповать, сваривать, резать на станках.
Неожиданности здесь могут подстерегать на каждом шагу.
Прочные сплавы обычно очень сложны по составу. Иногда до десяти различных элементов входят в такой сплав. Каждый из них вносит что-нибудь свое: один помогает бороться с окислением, другой облегчает ковку, третий повышает усталостную прочность.
И вместе они помогают решать одну задачу: создать нужный для нашей машины материал.
Теперь еще раз вопрос: всё? Нет. Одним лишь усложнением состава задачу полностью не решишь. Здесь приходит на помощь другой способ управления сплавом, его свойствами.
Способ этот – тепловая обработка. Он так же стар, как и сами металлы.
Закаливать металл умели очень давно. Закаленный металл – уже другой металл, с другими свойствами. До закалки он мягок, после – тверд и хрупок.
Тепловая обработка, нагрев и охлаждение – могучее средство управлять металлом. Раньше здесь шли вслепую. Русские металлурги, проникшие во внутренний мир металла, разгадали его тайны. Знание дало возможность выбирать правильный путь, в подлинном смысле слова управлять металлом.
Закаленный – нагретый и быстро охлажденный – клинок срубает молодое деревцо. Тем же клинком, если его нагреть и медленно охладить, нельзя срубить и прутик.
В чем же здесь секрет?
Металлы состоят из кристаллов – зерен. «Кирпичики» – кристаллы, оказывается, могут менять свою форму при нагреве или охлаждении. Меняются при этом и свойства металла.
Конечно, на деле не все обстоит так просто, как мы сказали, но основа, суть такова.
В технике, однако, редко пользуются чистыми металлами. Их соединение, сплав – вот с чем обычно имеет дело инженер.
Когда рождается сплав, происходят сложнейшие превращения.
Бывает, что атомы металлов соединяются, образуя химические соединения. Эти соединения могут «цементировать» весь сплав, делать его прочным. Прочная основа служит в нем как бы скелетом.
Разными добавками, разной тепловой обработкой можно получить и разное внутреннее строение сплава, разные его свойства.
Известно, например, что хром стоек к окислению. При окислении сначала на нем получается тончайшая пленка из окисла. Это «самозащита» металла. Он сам предохраняет себя от разрушения – дальше окисление не идет. Вводя в сплав хром, мы повысим стойкость сплава. Вот почему хром есть во всех марках нержавеющей стали.
Вольфрам в железных сплавах соединяется с углеродом. Химические соединения углерода и вольфрама – карбиды– придают сплаву высокую твердость. Вот почему вольфрам мы встретим в инструментальной стали, где твердость – первое требование. Ведь резцами из такой стали режут металлы.
Разве неудивительны эти, идущие по воле человека, превращения металлов? Чистых металлов известно около 70. А наша техника применяет несколько сот марок сплавов с самыми различными свойствами.

Легирующие примеси в высококачественных марках стали.
Можно выдумать сплавы почти невесомые, всплывающие в воздухе, как пробка в воде, и сплавы, в десятки тысяч раз тяжелее стали. Это, конечно, фантазия писателей.
Но если бы лет пятнадцать назад вы сказали металлургу, что можно создать сплав, работающий сотни часов при температуре красного каления, – он наверняка счел бы вас фантазером.
Инженеры, создававшие такой сплав, знали по опыту, что столько-то процентов никеля обеспечат высокую прочность, а столько-то молибдена – стойкость к высоким температурам.
Они знали, что добавка хрома и кремния даст защиту против окисления и при низких и при высоких температурах. Им известно было и то, что для лучшей свариваемости и ковкости желательно иметь в сплаве немного углерода.
И они подобрали состав сплава. Но это было лишь началом работы.
В лабораторной печи сделали пару опытных плавок. Прочность при высокой температуре получилась выше, чем у других сплавов.
Однако ковать и прокатывать новый сплав оказалось очень трудно. Мешала слишком большая его твердость.
Куда же годится материал, который нельзя обработать! Инженеры стали тщательно изучать все свойства нового сплава.
Его испытывали при нагрузках, которые придется выдерживать в настоящей турбине. В специальных машинах подвергали образец «пыткам»: растягивали, изгибали, выкручивали на все лады. Смотрели, как материал ведет себя при длительной работе – много часов подряд. Ведь турбина на электростанции должна проработать непрерывно 100 тысяч часов – одиннадцать с половиной лет!
Конечно, испытывать образец 11 лет – дело немыслимое, но все же инженеры заставили металл сдавать экзамен подолгу, чтобы судить, как он поведет себя при еще более длительной работе.
Нельзя добиться того, чтобы материал совсем не менял своих свойств. Но можно и нужно добиваться того, чтобы изменения эти были медленными, незаметными, не мешающими работе машин.
Нелегкая эта задача, но ее решают наши металлурги.
Они проникают внутрь металла с помощью микроскопа и рентгеновского аппарата, исследуют влияние тепловой обработки на строение и свойства сплава.
Инженеры здесь не одиноки. Наука вооружает их новыми, совершенными методами исследования металлов.
Не только оптический, но и электронный микроскоп с увеличением в 100 тысяч раз становится достоянием металлурга. С его помощью можно увидеть даже отдельные молекулы.
Электронные приборы выдают тайну самых тонких, самых сложных превращений в недрах вещества.
Раньше узнать, нет ли дефектов внутри металла, можно было, только разрезав слиток или деталь. Теперь мы можем «заглянуть» внутрь металла, не разрушая его. Рентгеновский аппарат, магнитный и ультразвуковой дефектоскопы – вот те глаза металлурга, которые видят все изъяны, трещинки, все пороки, видят внутренний мир металла.
Сплав нагревают, выдерживают при определенной температуре и затем охлаждают – по-разному нагревают, по-разному выдерживают, по-разному охлаждают. И опыт и теория показывают, как это делать наилучшим образом.
Так справились и с «упрямым» сплавом, о котором мы говорили. Он стал хорошо поддаваться обработке. Но когда попробовали, как новый сплав сваривается, то испытали жестокое разочарование. Нагрев при сварке вызывал чрезмерную хрупкость и твердость. И сварные швы оказались теми опасными местами, которых всегда стремятся избегать.
Все существовавшие сварочные электроды пришлось забраковать и изготовить новые. Да и самый процесс сварки перестроили заново.
Понадобился и новый припой, так как ни один из имевшихся не был пригоден при высоких температурах. Пайка же, как и сварка, занимает немало места при изготовлении машин.
Затем испытания нового сплава перенесли из лаборатории в заводские цехи.
С высочайшей тщательностью повели плавку на заводе. Литейщики знали, что сплав, работающий при большой температуре, очень капризен. У него повышенная чувствительность к малейшим изменениям в составе.
Какая разница – на сотую или тысячную долю процента больше добавлено присадок! Какая разница – немного перегреть или недогреть сплав! Но эти маленькие разницы могут быть причиной большой разницы – между годным и негодным сплавом.
И все же сплав из заводской печи не сдал экзамена. Инженеры долго ломали головы, пока доискались причины.
Оказалось, что при плавке попали вредные примеси из облицовки печи. Примеси остались после разливки, затвердели, и результатом был брак.
Металлургам и с этим злом удалось справиться. Они научились получать чистый сплав.
Когда приходится слышать о сплаве с «исключительными» качествами, равных которым еще не было, надо спросить: а применяется он в промышленности? Производится ли он в больших количествах?
И если вам ответят, что это лабораторный сплав, тогда вы смело можете усомниться в его исключительности.
Бывали такие случаи. Сплав из лабораторной печи вел себя прекрасно. И прочность, и твердость, и другие свойства отвечали самым жестким требованиям. Однако на заводе получалось другое, и сплаву приходилось отказывать в «путевке в жизнь».
От лаборатории до производства – еще дистанция немалого размера. И то, что инженеры полностью решают задачу, то, что они научились давать металл, не уступающий лабораторным образцам, – это большое достижение металлургии, которое трудно переоценить.
Комбинируя различные добавки, металлурги получают нужные свойства сплавов. Нередко ничтожные количества некоторых элементов резко улучшают материал. Название «гомеопатическая» металлургия, металлургия малых добавок, к которому прибегают инженеры, верно буквально, без кавычек.
Они добиваются исключительной чистоты сплава, ведут жестокую борьбу с каждой нежелательной примесью, с каждым незваным гостем, попавшим при плавке в сплав.
И каждую плавку они заставляют сдавать трудный экзамен.
Мы как-то упомянули, что нельзя сделать части машины из золота или платины. Но разве только золото и платина дороги? Нет, конечно. Есть и еще дефицитные, дорогие элементы. Они-то как раз и нужны для создания высокопрочных сплавов.
В лаборатории, пожалуй, это не составит проблемы. Там можно проводить опыты хоть с радием. А когда радия потребуется не доли грамма, а килограммы и десятки килограммов! Волей-неволей от него придется отказаться.
Выходит, надо искать заменители дорогих, остродефицитных материалов. Молибден, скажем, заменить более доступным, дешевым марганцем.
А только просто ли это сделать? От изменения состава сплав может измениться так, что его и не узнаешь.
Большие и сложные исследования ведут металловеды, создавая новые сплавы. Это, пожалуй, звучит очень скромно и неопределенно. Но как же все-таки может быть велика эта «большая» работа?
Предположим, что мы захотели бы испробовать все возможные сочетания из двух, трех, четырех и так далее элементов, скажем, до десяти. А в каждом из таких сочетаний мы изменяли бы содержание составных его частей, допустим, 10 раз.
Сколько нужно было бы изготовить образцов? Оказывается, так много, что на испытания их не хватило бы человеческой жизни.
Итак, «большая» работа оказывается бесконечной, а значит, и неосуществимой.
И у нас нет никакой надежды не только довести ее до конца, но и хоть сколько-нибудь заметно продвинуться вперед. Исключается всякая возможность плана, системы. Их заменяет случай.
Долгие годы нужны для того, чтобы изучить, перепробовать хотя бы сплавы всего из двух металлов – двойные. Века нужны, чтобы создать и испытать тройные и четверные сплавы. Чтобы испытать все сплавы из 10 элементов, понадобилось бы столько образцов, что для них не хватило бы массы металлов размерами с земной шар.
Но нельзя ли ускорить эту работу?
Советская наука ответила: можно!
Профессор С. А. Векшинский разработал совершенно новый способ исследования структуры и свойств сплавов.
Мы можем с вами оценить значение способа Векшинского, зная о тех действительно непреодолимых препятствиях, которые стояли перед металловедами.
Нет возможности описать во всех подробностях эту работу. Но суть ее понять нетрудно.
Твердым и жидким металлом наука занималась давно. А вот тот же металл, но в виде газа, точнее пара, выпал из поля зрения металловедов. В этом же оказался ключ решения задачи, которой занялся Векшинский.
Давно известно, что при нагревании металл испаряется. Все быстрее и быстрее двигаются тогда атомы металла. И часть из них уже может преодолеть силы притяжения соседей, оторваться и улететь.
В воздухе, конечно, такой вырвавшийся с поверхности металла атом далеко не улетит. Его «затолкают» встречные молекулы воздуха, он быстро потеряет свою скорость. А если бы могли увидеть его путь при этом, то заметили бы причудливую ломаную линию. Едва он успевает поворачиваться под ударами встречных молекул.
Другое дело – в пустоте. «Пустота», конечно, дело относительное. Но все же наши машины глубокого вакуума, пустоты, создают разрежение до одной тысячемиллиардной доли атмосферы. По сравнению с плотным воздухом у поверхности Земли это действительно пустота.
И вот там-то атомы испаренного металла полетят без помех прямым пучком.
Пусть такой пучок встретит на пути стеклянную пластинку. Тогда, подобно муке, которая, высыпаясь из пакета на стол, ляжет горкой, осядут горкой и атомы на пластинке. Слой атомов металла на пластинке будет неодинаковой толщины: чем дальше от вершины «горки», тем тоньше.
А теперь пусть не один, а два или три пучка от разных металлов направляются к пластинке. Атомы перемешаются, и на ней осядут слои – «горки» из разных атомов.
В разных местах пластинки будут и разные по составу слои. В одном месте будет больше, скажем, никеля, меньше хрома, где-то в другом – наоборот.
На пластинке исследователь получит всю гамму сочетаний составных частей, всевозможные их комбинации. Этого можно достигнуть, и это сделал Векшинский.
Но ведь тогда на стеклянной пластинке откроется перед нами сплав во всем его многообразии. На маленькой пластинке мы увидим большой мир – тысячи разных сплавов, стоит только перейти из одного места пластинки в другое. Передвигаясь по пластинке, мы сразу встретим всю гамму сплавов, которые нужно было бы создавать годами упорного труда.
Но разве слой из атомов разных металлов может заменить настоящий сплав?
Разве сплав на пластинке испытаешь так, как испытывают настоящий сплав?
Оказывается, тончайшие слои на стеклянной пластинке могут заменить исследователю настоящий сплав. Оказывается, можно с помощью специальной аппаратуры испытывать и определять некоторые их свойства.

В экспресс-лаборатории спектрального анализа.
Пользуясь способом Векшинского, можно предсказывать, как поведет себя сплав, как будут действовать на него различные газы, пары, жидкости при различных температурах и давлениях. Можно, например, наблюдать, насколько стоек сплав к такому своему врагу, как коррозия, и помогать бороться с нею. Можно легко увидеть, что происходит с тонким слоем сплава при нагреве, при пропускании тока, при взаимодействии не только металла с металлом, но и с химическими соединениями, иначе говоря, в миниатюре изучать то, что бывает в жизни со сплавом.
Создание металловедческой лаборатории, в которой перед исследователем развертывается картина «большого в малом», где изучаются не громоздкие образцы, а «горки» из атомов, высотою в доли миллиметра, естественно, было сложным и трудным делом.
Так, например, чтобы приготовить совершенно чистый металл для будущего образца, его приходилось переплавлять в пустоте и выдерживать жидким довольно долго, – иначе в нем оставалось много газа, а «газированный» металл для исследований не годился. Испарение должно идти равномерно, и это доставило немало забот. Зачастую поверхность испарителя – металлического шарика – оказывалась как бы изъеденной со всех сторон неравномерным испарением, и сплав получался неправильного состава.
Однако работа была успешно закончена и в 1946 году удостоена Сталинской премии первой степени.
Применяются и другие методы «скоростного» определения свойств сплавов. С точностью до тысячных, а иногда и до десятитысячных долей процента обнаруживает примеси спектральный анализ. Делает он это так быстро, что назвали его экспрессным анализом.
Создать высокопрочный сплав, как мы знаем, нелегкая задача. Она тем более сложна, что прочные сплавы имеют свои особые свойства, с которыми нельзя не считаться.
Что же это за свойства?
Кое-что о них мы уже говорили, когда рассказывали о создании жаропрочных сплавов. Сплавы «отзываются» на перемену условий – нагрузки, температуры. И надо добиться, чтобы эти изменения шли очень медленно, не мешая работе машины. А, значит, кратковременными испытаниями уже нельзя ограничиться. Нужны длительные испытания, чтобы уверенно строить машину.
И это не все. Можно судить о детали не по самой детали, а по кусочку металла – образцу. Из такого металла потом будут сделаны части машины. И если образец ведет себя хорошо, выдержит все испытания, то и за деталь можно быть спокойным.

Схема стилоскопа – прибора для спектрального анализа стали.
Испытания образцов новых сплавов отвечают металлургу, каким же получился сплав, добился ли он тех качеств, какие требуют от него производственники.
Вот как решили задачу профессор И. И. Корнилов и инженер В. Ф. Проханов.
Вместо сложных и громоздких испытательных машин – небольшой диск. На нем, как зубья в бороне, разместились по кругу металлические палочки – образцы. Диск помещен в электропечь, где можно получить высокую температуру. Он вращается с огромной скоростью.
Во время испытаний образцы на диске изгибаются, как будто тонкие деревца под сильным ветром. Центробежная сила и высокая температура – причина этого. И по тому, как они изогнулись, можно судить о жаропрочности сплава, его стойкости к нагрузкам и температурам.
Но как же увидеть образцы на диске, который вертится со скоростью в 2 000 или даже больше оборотов в минуту? Они сливаются в сплошной блестящий круг.
Заглянем в маленькое окошечко в крышке печи. Мы увидим образцы… стоящими неподвижно. Как будто оборвалась кинолента и на экране все застыло.
Это делает стробоскоп – оптический аппарат, который «останавливает» быстровращающиеся предметы. В стробоскопе предмет освещается лишь тогда, когда он, вращаясь, появляется перед окошечком все время в одном и том же месте. А так как вращение идет очень быстро, глаз не успевает заметить мигание света – для нею изображения сливаются в одно, как кадры на экране. И мы видим освещенный предмет как бы застывшим.
Стробоскоп применяют для изучения быстроходных механизмов. С его помощью наблюдают, например, работу высокоскоростных подшипников. В испытательной машине стробоскоп позволяет увидеть, как ведут себя образцы жаропрочных сплавов.
Часто нужны бывают испытания не только образцов, но и готовых деталей, а иногда и всей машины в целом, в условиях настоящей ее работы.
Испытания же быстроходных машин – дело не простое. Наблюдать за изменениями свойств металла в машине, где детали двигаются с большими скоростями, естественно, труднее, чем в тихоходной машине.
Способов испытаний сейчас известно мною. За напряжениями в быстровращающейся детали можно наблюдать на прозрачных моделях.
Модель, например турбинного диска, делают из прозрачной пластмассы. Диск помещают в печь и вращают с большой скоростью. В пластмассовом диске возникают напряжения – такие же, как и в настоящей турбине. Оптические приборы помогают нам их увидеть, узнать, что происходит с материалом во время работы машины. Яркие радужные рисунки, похожие на причудливую раскраску крыльев какой-нибудь тропической бабочки, показывают «линии напряжений», и по ним можно судить, каковы напряжения, где они больше, где опасные места.