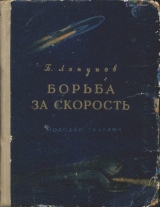
Текст книги "Борьба за скорость"
Автор книги: Борис Ляпунов
сообщить о нарушении
Текущая страница: 6 (всего у книги 17 страниц)
Отполированная искрой деталь не будет иметь даже самых мельчайших трещинок, которые неизбежно оставляет резец, фреза, шлифовальный круг, – этих очагов возможных неприятностей для детали, когда она попадает в работу. В этом причина упрочения поверхности при электроискровой обработке.
Так, пройдя диском или другим «инструментом» над поверхностью детали, можно обработать ее и притом вдвое-втрое быстрее, чем при механической обработке. Не нужен громоздкий станок, не нужны резец, фреза, сверло.
Новый станок, быть может, придет на смену старому. Электромашиной мы называли соединение мотора и инструмента. Еще нет подобного короткого названия этому станку – станку для искровой обработки: привычным именем «инструмент» нельзя назвать непривычное – электрическую искру.
Электрическая искра режет, строгает, шлифует, полирует металл. Она может сделать невозможное: вырезать отверстие в металле любой формы – трудная, а подчас и невыполнимая задача для механической обработки. Она может, если поменять местами электроды, не вырывать из детали металл, а наносить его: твердый сплав – на резец, металлическое покрытие – на защищаемую от износа или коррозии деталь.

Дефектоскопы. Сверху вниз: ультразвуковой, рентгеновский, магнитный.
В электроискровой обработке мы имеем дело с новым, принципиально новым инструментом – электрическим током. Поэтому, и с новыми, качественно новыми станками, методами, способами покорения металла.
Техническая мысль находит и другие способы получения деталей быстроходных машин. Она использует опыт и таких отраслей промышленности, которые к высоким скоростям имеют довольно отдаленное отношение.
Что общего, скажем, между газовой турбиной и ювелирными изделиями? Конечно, ничего.
Но опыт «сверхлегкой» ювелирной промышленности натолкнул инженеров на полезные мысли. Лопатку газовой турбины сложной формы бывает трудно обработать на станке. Изготовить же ее нужно исключительно точно. И здесь пригодился способ, которым пользовались ювелиры, – способ литья высокой точности, или прецизионного литья.
Жаропрочный металл, идущий для лопаток газовых турбин, плавят в электрической печи. Печь выложена огнеупорным материалом. Высокочастотный ток нагревает трубчатую спираль, изнутри охлаждаемую водой. Расплавленный металл должен быть чистым, и его предохраняет от окисления защитная газовая атмосфера: в печь подают инертный газ, который не соединяется с металлом.
Модель лопатки заливают легкоплавким сплавом, изготовляя таким путем форму для будущей отливки. Форму эту делают разъемной – из двух половин. Разняв ее и вынув модель, заливают в форму под давлением воск. Он заполняет все углубления. Снова вынимают модель – уже восковую, заливают огнеупорной формовочной массой и просушивают ее.
Остается теперь залить металл – и воск вытечет наружу, чтобы уступить место жаропрочному сплаву. Когда сплав застывает, отливку очищают от формовочной массы, и, после тщательного контроля ее качества, лопатка готова. Бывает, что после этого не нужна больше никакая обработка – так точно изготовлена лопатка.
Точное литье нашло сейчас широкое применение в технике.
Борьба за скорость – это борьба за точность, за микроны и граммы.
Микронами измеряется зазор в подшипнике, куда подается масло. Стоит отклониться на несколько микрон, и правильный ход смазки нарушается: в этом месте неизбежен перегрев – злейший враг подшипника. Точность здесь необходима.
Подшипник и лопатка турбины, шлифовальный шпиндель и ротор воздушной турбинки, все части быстроходных машин должны быть изготовлены с той точностью, какой требуют условия их работы.
Для этого необходим контроль.
Современная техника располагает целым арсеналом методов и аппаратов, позволяющих выпускать детали заданной точности и заданного качества – быстро и надежно.
Электроавтоматы-контролеры, созданные советскими инженерами, не пропускают ни одной детали, если ее размеры отклоняются больше, чем это допустимо. Они «ощупывают» деталь электрическими «щупальцами» – контактами, и если деталь изготовлена неточно, подают ее в предназначенное для брака место. Контролер-автомат работает быстро: за час он проверяет несколько тысяч деталей.
Существуют и автоматы, которые контролируют не готовую деталь, а весь ход ее изготовления. Они предупреждают появление брака заранее. Автомат следит за режущим инструментом, «проверяя» его работу и даже управляя им: регулирует скорость и выключает станок, когда обработка закончена. Таким путем можно, например, изготовить с требуемой точностью кольцо шарикоподшипника, не допуская брака.
И вот деталь изготовлена. Изготовлена точно. Но чтобы быть уверенным за нее, нужно еще заглянуть внутрь металла, посмотреть – нет ли там случайно уцелевших трещинок, посторонних примесей и прочих вредных очагов, которые могут погубить машину. Конечно, качество металла проверялось и до этого. Однако металл проходил через массу превращений: его нагревали, охлаждали, резали, шлифовали, обдували дробью, – чего только не приходилось ему перенести! Могла затаиться где-нибудь крохотная язвочка. Ее надо обнаружить. На помощь приходят дефектоскопы. Невидимый свет и неслышимые звуки стали охотниками за дефектами.
Невидимые лучи – ультрафиолетовые, рентгеновские, гамма-лучи, испускаемые радиоактивными веществами, – находят притаившиеся дефекты в металле. Испытуемую деталь погружают в ванну с раствором флюоресцирующего вещества: если на поверхности есть трещины, то это вещество останется в них. При облучении ультрафиолетом оно будет светиться и выдаст тайну местонахождения трещин.
Неслышимые звуки – ультразвуки – проникают внутрь детали и определяют, какой и где притаился в ней дефект.
Своеобразный «локатор» посылает звуковые волны высокой частоты, которые проникают внутрь детали и, отражаясь, дают изображение на экране «локатора». Если на пути волны встретится трещина или другой дефект, изображение на экране немедленно сообщит об этом, изменив свою форму.
Можно было бы рассказать еще о многих подобных методах.
Приборы, созданные советскими учеными и инженерами, помогают изготовлять детали машин точно и надежно. И этот вклад в нашу технику – тоже вклад в борьбу за скорость, как и все, о чем мы говорили здесь, все, из чего складывается покорение металла.


ВРАГИ СКОРОСТНЫХ МАШИН
Множество самых разнообразных машин создано человеком.
Но какими бы разными они ни были, почти все они имеют одну общую, небольшую по сравнению с самой машиной деталь.
«Мал золотник, да дорог», – говорит пословица. Можно смело сказать, что без этой детали не было бы современной техники.
Без нее не было бы двигателей и, значит, самолетов и автомашин, судов и паровозов, тракторов и танков. Не было бы станков. Без нее не мог бы существовать мир машин.
Ведь почти в каждой машине есть вращающиеся части, есть вращение, быстрое или медленное.
В часовых механизмах встречается скорость вращения, равная точно одному обороту в год. А есть электромотор на 120 000 оборотов в минуту. Части некоторых станков должны вращаться медленно, как будто нехотя. И есть станки для сверления малых отверстий, где патрон совершает в минуту 100 000 оборотов.
Там, где вращение, там должна быть и деталь, о которой мы говорим, – подшипник.
Подшипник позволяет нам бороться с одним из самых страшных врагов машины – трением.
Трение – явление известное, все его знают, все к нему привыкли и не замечают. Поэтому нередко, чтобы показать, что оно для нас значит, рисуют воображаемый мир без трения. Это поистине был бы страшный мир, где ветер и волны, раз появившись, никогда не утихнут, где нельзя ходить и ездить, и даже носить одежду нельзя.
Что же такое трение? Все ли ясно здесь?
До сих пор еще нет полной и ясной картины. Многого не удалось объяснить. Но многое уже изучено, объяснено, и наши ученые стремятся разгадать тайны трения, чтобы им управлять – пользоваться трением, когда оно нужно, или бороться с ним, когда оно мешает.
Ведь трение не только враг, оно и друг. Без него, например, не было бы ременных передач и не было бы тормозов.
И все же трение в машинах чаще всего враг. За его помощь, когда она нужна нам, приходится платить – и довольно дорого.
Так получается потому, что трение мешает движению и вызывает износ машин.
Трение – неизбежный спутник движения. Едва только начинается движение, появляется и трение.
Как бы мы ни старались сделать поверхность металла гладкой, на ней все равно останутся шероховатости, невидимые простым глазом. Но их легко увидеть глазом вооруженным.
В журналах нередко помещают фотографии-загадки. На одном из таких снимков виден как будто край обломанной пластинки, с зазубринами и неровностями. Пожалуй, можно подумать, что это кусочек старой пилы, источенной, изъеденной ржавчиной.
На самом же деле это гладкая, тщательно отполированная поверхность, снятая при сильном увеличении.
Даже самая гладкая, зеркальная поверхность металла, которую мы сглаживали с величайшей тщательностью, – шлифовали, полировали, притирали, – будет покрыта «рытвинами», «ухабами». Они очень малы эти «гребешки». Их высота может доходить всего лишь до 0,02—0,03 микрона, то-есть 2–3 стотысячных долей миллиметра.
И все же они есть.
При движении одной поверхности по другой шероховатости цепляются друг за друга, мешают двигаться. Зазубринки частично обламываются, и происходит разрушение трущихся поверхностей – возникает трение.
На то, чтобы его преодолеть, тратится энергия.
Это потерянная для нас энергия – она переходит в тепло и расходуется на износ. Вот почему мы и стремимся уменьшить трение, которое разрушает наши машины.
Но не только шероховатость поверхностей – причина трения.
Казалось бы, чем лучше обработана поверхность, тем меньше должно быть и трение. Это и в самом деле бывает так. Но – до известного предела.
Между двумя очень гладкими поверхностями, где трения почти не должно быть, оно, наоборот, получается колоссальным. Гладкие полированные пластинки прилипают друг к другу. Иногда удается даже сварить два гладких металлических брусочка под прессом, не плавя металл.
Значит, дело не только в микроскопических зазубринках поверхности, не только, как говорят, в ее микрогеометрии. Нужно идти глубже, внутрь металла, чтобы объяснить механизм простого лишь на первый взгляд явления – трения.
Там, где поверхности соприкасаются друг с другом, появляются силы взаимодействия, сцепления молекул.
Чем глаже поверхность, тем плотнее они сомкнутся, тем сильнее эти молекулярные силы. Выходит, чересчур большая гладкость не уменьшает, а увеличивает трение.

Трение: (1) сухое и (2) жидкостное (увеличение).
Однако, как не бывает идеально гладкой, так и не бывает и идеально чистой поверхности. Поверхностные молекулы имеют соседей не со всех сторон и поэтому, как мы уже знаем, могут притягивать молекулы из окружающей среды. Поверхность служит своеобразной ловушкой для молекул газов, паров, жидкостей. Поверхностный слой состоит из разрушенных обработкой и трением кристаллов металла, обладающих повышенной активностью. Он легко окисляется – даже нержавеющая сталь и золото могут покрываться пленкой окислов, когда поверхность разрушается трением. И продукты износа – металлический порошок – это не чистый металл, а крупинки его, покрытые «скорлупой» окисей.
Всегда металл покрыт тончайшей пленкой окисей и захваченных молекул. Выходит, сухого трения, трения металла о металл в чистом виде не бывает.
Трение, когда одна поверхность движется, скользит по другой, названо трением скольжения. Это самый большой враг машин, быстро разрушающий металл. Чтобы побороть его, нужно тратить много энергии.
Этому врагу ученые и инженеры объявили войну.
Чтобы трущиеся поверхности не истирались, их нужно разъединить, ввести посредник, который уменьшил бы трение. Такой посредник – смазка.
Масло прилипает к поверхностям, не дает им касаться друг друга, и, вместо «сухого» трения металла о металл, возникает трение «жидкостное» между отдельными слоями смазки. А оно во много раз меньше.
Русский ученый почетный академик Н. П. Петров, разработавший основы теории жидкостной смазки, подчеркивал, что «если жидкий слой, смазывающий два твердых тела, вполне отделяет их друг от друга, то непосредственного трения твердых тел уже очевидно не может быть».
На вал надета втулка. Она неподвижна, на нее опирается вал. В маленький зазор между валом и втулкой непрерывно поступает смазка. Это подшипник скольжения, где трение уменьшается смазкой, которая подается через смазочное отверстие втулки и заполняет зазор. Под действием переменных нагрузок вращающийся вал колеблется, а потому расстояние между втулкой и валом получается переменной величины.
Почему масло обладает удивительной способностью – уменьшать трение?
Даже очень тонкая масляная пленка разделяет трущиеся поверхности и выдерживает нагрузку, которая к ним приложена.

Действие «снегового» клина.
Сани легко скользят по снегу. Их полозья выдерживают вес саней и всего, что в них находится. Но видано ли, чтобы сани ехали по снегу задом наперед? Нет, так не бывает. Под передним загнутым краем полоза образуется клиновой зазор, куда подминается снег. Снег уплотняется, и «снеговой» клин не дает саням проваливаться, помогает им ехать.
А теперь вернемся к подшипнику скольжения. В нем тоже есть клиновой зазор – между валом и втулкой. Туда тоже – только уже не подминается, а нагнетается масло. Вязкое, прилипающее к металлу масло трудно сжимаемо. Попав в клиновой зазор, оно приподнимает втулку, которая и всплывает в масле. Масляная пленка разделит трущиеся поверхности, не даст им соприкасаться, возьмет на себя нагрузку, приобретет, как говорят, «несущую способность». Это приводит к уменьшению трения.
Но здесь не все обстоит просто. Даже тончайший слой смазки, толщиной всего в несколько молекул, действует как клин, раздвигая трущиеся поверхности. Трение уменьшается. Однако в то же время молекулы смазки ухитряются попадать довольно глубоко внутрь поверхностного слоя, в сверхмикроскопические трещинки. Тем самым разрушается, портится поверхность, увеличивается износ.
При трении молекулы металлов, оказывается, путешествуют – переносятся с одной трущейся поверхности на другую, внедряются в нее.
Так можно было заметить, что внутрь стального вала попадают молекулы бронзы, точнее, тех элементов, из которых бронза состоит. Они пробирались туда даже через слой масла.

Подшипник скольжения.
Стальная шейка вала при работе подшипника нагревается неравномерно – местами сильнее, местами слабее, почему и говорят о «местном» перегреве. И когда масло попадает в перегретую зону, оно разлагается, выделяя углерод. На маленьком участке поверхность дополнительно науглероживается. Но затем сильно нагретая крохотная стальная площадочка быстро охлаждается: перегрев возникает и исчезает, появляясь в разных местах. Науглероженная сталь, таким образом, подвергается закалке, твердость маленького участочка шейки повышается.
Тут же рядом может происходить обратное явление: если нагретая стальная поверхность охлаждается медленнее, – а так тоже бывает, – тогда твердость стали понижается.
Это приводит к тому, что появляются места, резко отличные по свойством друг от друга. Поверхностный слой коробится, кусочки его выламываются. Конечно, перед этими словами надо поставить еще «микро» – микрокоробление, микрокусочки, ибо речь идет о крошечных участках металла.
Кроме того, стальная поверхность шейки подвергается нападению кислорода, который врывается в масляный слой подшипника и окисляет ее. На нее действуют и различные химические соединения, имеющиеся в масле, причем по-разному – в зависимости от условий работы подшипника. Выходит, стальная шейка уже становится не такой, что была раньше. На ней – и пленки окислов, и различные химические соединения. Кусочки их отламываются, затрудняя скольжение. Может даже случиться «заедание» трущихся поверхностей, с которыми происходят такие превращения.
Все это очень осложняет картину трения, затрудняет ее объяснение.
Смазка помогает бороться с трением, заменяя сухое трение жидкостным, уменьшая потери энергии.

Действие смазки в подшипнике скольжения.
Но есть и другой путь борьбы. Избавиться от трения скольжения и заменить его другим, во много раз меньшим – трением качения.
На вал плотно надето кольцо. Вместе с валом оно вращается. Другое кольцо, побольше диаметром, неподвижно. Между кольцами по канавкам катятся шарики или ролика. Вместо скольжения вала во втулке – качение шариков по канавкам. Это – подшипник качения. В нем скольжение заменено качением. И трение поэтому уменьшается.
Для разных машин разные бывают и подшипники. Есть шарикоподшипники весом в тонну и весом в доли грамма. Через внутреннее кольцо подшипника-гиганта проедет малолитражный автомобиль, а крошка-подшипник для приборов размером меньше блохи.
Есть подшипники для больших машин, выдерживающие большие нагрузки – в сотни тонн. Есть подшипники, которые переносят вибрации вала или сильные ударные нагрузки.

Подшипник качения (шариковый).
Изготовление подшипниковых шариков или роликов требует большой точности. Они должны быть абсолютно правильной формы и притом совершенно одинаковыми. Иначе подшипники не будут хорошо работать.
Но сделать идеально точный шарик очень трудно, почти невозможно. Еще труднее все шарики изготовить совершенно одинакового размера. Машины, которые их делают, – прессы, станки – не могут решить такую задачу. Неизбежны отклонения, хотя и очень малые.
Надо добиваться, чтобы форма шарика отклонялась от идеальной лишь на очень малую, строго определенную величину. Надо сделать и так, чтобы один шарик отличался от другого тоже не больше, чем можно допустить для хорошей работы подшипника.
Какой же может быть эта величина, этот допуск? Десятитысячные доли миллиметра. Такова здесь мера точности.
Растут обороты, больше становится центробежная сила – растет и нагрузка. Поэтому при большой скорости и самый маленький бугорок, малейшая неровность может стать причиной аварии.
При небольших скоростях подшипник только тогда отказывался служить, когда металл уставал, на что требовалось время. Прежней точности было достаточно раньше. Ее недостаточно теперь.
Технологи смогли обеспечить повышенную точность. Они изготовили отличный подшипник.
Установили его и включили машину. 1 000… 2 000… 5 000 оборотов в минуту… машина выходит из строя. Запах пригоревшего масла показывает, в чем дело. Перегрелся подшипник!
Нагрев при больших скоростях бывает так велик, что его не выдерживают и твердые, закаленные шарики. На их зеркально-гладкой поверхности, как и на кольцах – синеватые цвета побежалости. Твердый металл перестает быть твердым.
Что же произошло?
Раньше считали, что сила трения не зависит от числа оборотов.
Исследования показали, что это не так. Лишь при небольшой скорости трение остается примерно постоянным. Затем оно начинает расти– и тем быстрее, чем больше обороты.
Но чем сильнее трение, тем больше выделяется тепла. Нагрев со скоростью растет, а охлаждение ухудшается.
Шарики, катясь по канавке, касаются ее лишь в точке, вернее в крохотной площадке, да и то на очень короткое время. Коснулась площадочка канавки, и до следующего прикосновения она «отдыхает», охлаждается. Тепло успевает рассеяться, площадка – остыть. В конце концов даже такой переменный нагрев приводит к тому, что шарики могут треснуть. Впрочем, при малых и средних скоростях это случается не скоро.
Скорости возросли, резко увеличился нагрев, перерывы в нагреве настолько малы, что шарик не успевает охлаждаться. Все больше и больше накапливается тепла, и твердый металла «размягчается», отказывается нормально работать.
Чтобы усилить отвод тепла от подшипника, смазку подают к нему под давлением, стараются прогнать через него больше смазки, уносящей тепло. В газотурбинных авиационных двигателях, например, где скорости вращения доходят до 15–18 тысяч оборотов в минуту, масло прогоняется через подшипники под давлением до 7–8 атмосфер.
Вообще со смазкой пришлось повозиться инженерам немало. Так, однажды изготовили шпиндель, все учли и проверили, еще раз проверили и запустили станок. Сначала все шло хорошо – обороты растут, смазка происходит нормально.
Прибавили обороты – смазка ухудшилась, станок едва не вышел совсем из строя. И так каждый раз: еще не достигли и половины нужных оборотов, а дальше идти нельзя.
Решили, что смазка, видимо, теряет вязкость, и масляная пленка, эта защита от «сухого» трения, не выдерживает, рвется. Взяли смазку повязче – обороты прибавились.
Все же долгой бесперебойной работы добиться не могли. Смазка сильно нагревалась. Позаботились об искусственном охлаждении подшипника.
Задумались над тем, как подавать смазку. Оказалось, что лучше ее подавать каплями. Всего одна-две капли в минуту – и быстроходный шпиндель работает нормально.
Устроили специальный разбрызгиватель, чтобы подавать масло мелко распыленным. Кроме того, на помощь призвали сам подшипник. Вращаясь, он засасывает масло, а воздух, вихрями кружась вокруг, выбрасывает смазку из подшипника. Подшипник сам перекачивает масло из одного маленького бачка в другой. Остается соединить их трубкой – и маслосистема готова.
Тем не менее подшипник не гарантирован от неприятностей, если обороты очень велики. И инженеры ищут способы улучшить его конструкцию.
Слабое место шарикоподшипника – сепаратор. Это тонкое кольцо с гнездами для шариков, которые не дают им «рассыпаться» как попало между верхним и нижним кольцами подшипника.

Разрез мощной советской паровой турбины высокого давления.
Шарики истирают гнезда сепаратора – и в конце концов он разрушается. Неизбежна авария. Конечно, в этом виноват не один сепаратор: тут и нагрев, и порча трущихся поверхностей, которые начинают «шелушиться». Но все же главное зло в сепараторе, и на него пришлось обратить особое внимание.
Подобрали материал, на который можно положиться. Часто применяют теперь пластмассу – текстолит – и легкие сплавы. Укрепляя слабое место подшипника, отказались от штамповки и от клепки – начали сепаратор делать цельным, гнезда сверлить и отделывать с предельной тщательностью.
С другой стороны, попробовали подшипник еще упростить.
В некоторых образцах избавились от сепаратора. Попытались отказаться от внутреннего кольца. Вместо него на валу сделали желобки, в которых и катятся шарики. Эти подшипники применяются в шпинделях, где скорость вращения доходит до сотни тысяч оборотов в минуту.
Таким путем приспосабливали подшипники качения для работы при больших скоростях.
И в простых и в сложных машинах можно встретить другой подшипник – подшипник скольжения, который должен работать при малых и при больших нагрузках, при низких и высоких скоростях.
Нагрев – враг и этого подшипника.

Высокоскоростные шарикоподшипники.
Исчерпаны ли все средства борьбы с врагом подшипника – перегревом? Нет. К такому выводу пришел советский ученый профессор А. К. Дьячков. Он нашел новый путь для того, чтобы продлить жизнь подшипника скольжения, отодвинуть предел скорости, когда нагрев не позволяет подшипнику работать.
Нам нетрудно понять, что это значит для техники больших скоростей.
Во многих машинах нагрев получается гораздо более сильным, чем может выдержать шарикоподшипник. Не только потому, что растут обороты, нагрузки, растет трение, нагревается вязкая смазка. Многие скоростные машины работают при высоких температурах.
Например, подшипники газовых турбин нагреваются почти до 200 с лишним градусов. Вот почему смазку к ним подают под сравнительно большим давлением. Но даже и этого оказывается мало, и подшипники еще дополнительно охлаждают воздухом.
И не в одних только турбинах тяжело приходится работать подшипнику. Во всех тепловых двигателях, – а их мы найдем всюду, – есть нагрев. Моторы автомобилей, тракторов, танков, – всех машин, где тепло служит человеку, – нагреваются при работе. А в связи с ростом скорости нагрев становится грозным врагом, не только тепловых двигателей, но и всех быстроходных машин, где служат подшипники скольжения.
Как можно увеличить отвод тепла, избежать опасного перегрева? Только ли тем, что повышать давление масла?
После нескольких лет упорной работы нашел ответ на этот вопрос А. К. Дьячков.
Нужно заставить масло само бороться с нагревом: не только смазывать, но и охлаждать подшипник. На первый взгляд – парадокс: масло, которое, нагреваясь, разжижается и теряет несущую способность, должно продлить жизнь подшипника!
Но такова диалектика развития техники. Врага машины при известных условиях можно сделать другом, помощником.
Заглянем внутрь подшипника. Мы говорили о том, что местная толщина масляного слоя между шипом и подшипником – величина переменная. Против отверстия, откуда подается смазка, может оказаться узкое место, где масляный слой всего меньше. Тогда масло, входя в подшипник, неизбежно сначала должно пройти через это самое узкое, самое тесное место. Только потом оно попадает в более широкое «русло» – расширяющееся расстояние между трущимися поверхностями.
Дьячков обратил внимание на то, что подшипник не нагревается всюду одинаково. Возникают «горячие зоны», где происходит перегрев. А здесь-то, как мы знаем, и таится опасность. Падает прочность и стойкость против коррозии подшипникового сплава.
Сколько тепла от нагретого подшипника может масло забрать и унести с собой? Очевидно, тем больше, чем больше пройдет его через подшипник за одно и то же время. Увеличить же подачу масла мешает «ловушка», узкое место у смазочного отверстия. Увеличивая давление, мы помогаем маслу быстрее пройти через это узкое место.
Больше масла пройдет через подшипник, значит, больше оно унесет с собой тепла.
Но можно и избежать «ловушки», сделав так, чтобы масло не попадало сразу в самую узкую часть зазора. Для этого место смазочного отверстия нужно выбрать там, где толщина зазора самая большая. Масло, не задерживаясь, быстрее будет проходить через зазор, а это позволит отводить больше тепла.
Однако нельзя, введя масло в подшипник, хотя бы и наилучшим образом, на этом, кончить и предоставить его превратностям судьбы.
Узкие места еще могут встретиться ему на пути от смазочного отверстия до выхода из подшипника. Причина этого в самой работе машины. Трудно даже перечислить все, что приходится переносить ее частям.
Они подвергаются действию нагрузок и нагрева, которые к тому же не бывают все время постоянны и одинаковы в разных местах. «Сложное напряженное состояние», – так кратко говорят об этом ученые-прочнисты.
Но если трудно все это назвать, то легко указать, к чему оно приводит. К изменению формы деталей: прямая деталь может изогнуться, изогнутая – выпрямиться, круглое отверстие – превратиться в эллиптическое. Прямой вал местами «выпучивается» вверх, местами – вниз.
Конечно, такие изгибы, впадины, выпучивания незаметны для глаза. Лишь чувствительные приборы замечают эти изменения на сотые доли миллиметра, всего на десятки микрон.
Но для подшипника микрон вещь немалая. Точность изготовления его – 0,2 микрона. Лишь на две десятых микрона можно допустить отклонение от правильной формы. А для больших скоростей нужна еще большая точность. Незаметные, неопасные раньше неровности, которые и увидеть-то можно только в микроскоп, весьма ощутительно дают о себе знать плохой работой, а возможно и аварией подшипника.
Здесь же речь идет о десятках микрон. Изогнется вал в подшипнике– и толщина смазочного слоя может уменьшиться. Появляется «узкое место». Масло перестает течь равномерно, скопляется там, а с ним скопляется и тепло. На больших оборотах, при высоких нагрузках возникает перегрев, возникает опасность аварии.
Такие результаты дали наблюдения Дьячкова. Он определил, как именно меняется форма деталей подшипника в работе, насколько велики ее изменения.
Как же бороться с этой опасностью? Как устранить неизбежные помехи правильному течению масла, быстрому отводу тепла?
«Клин клином вышибают», – говорит пословица. Мы вспомнили ее, когда говорили о разгружающих надрезах. И здесь похожий прием.
Форма исказится, «испортится» в одном месте, у одной детали. Этого избежать нельзя. Но можно исказить ее, «испортить» намеренно в другом месте, у другой детали, так что одно искажение компенсирует другое. Одна деталь – это вал. Он при работе изогнется. Другая деталь – это вкладыш подшипника. В нем нужно заблаговременно сделать выемку такой формы, чтобы толщина масляного слоя между шипом и подшипником не уменьшилась, когда изгиб вала появится.
Предусмотрев изменения формы вала, сделать отверстие вкладыша не круглым, а другим, так, чтобы ответить на все изгибы, впадины, выпуклости. Тогда они будут не страшны. Подшипник заранее подготовлен к ним и сохранит главное – возможность равномерного течения масла, без узких мест, где таится опасность перегрева и аварии.
Созданная Дьячковым теория позволила заранее рассчитывать, какой формы нужно сделать подшипник, чтобы он не боялся масляных «пробок», чтобы масло текло в нем правильно и хорошо отводило тепло.
Это дает конструктору возможность удлинить жизнь подшипника, жизнь машины, увеличить ее быстроходность.
Кажется, все! Но есть еще одна трудность. Она таится в самой смазке.
Здесь наблюдаем случай, который в технике нередок. Мы с ним уже встречались, когда говорили о материалах для быстроходных машин. Это – противоречие одного требования другому. Прочность и легкость – требования противоречивые. Инженерам приходится их мирить друг с другом.
Пришлось и Дьячкову мирить два противоречивых требования к материалу-смазке.
Лучше было бы иметь вязкость смазки побольше, тогда и нагрузку подшипник выдержит большую, – так говорит одно требование.
Лучше было бы иметь вязкость поменьше, тогда маслу легче течь, легче «расклинивать» трущиеся поверхности, – говорит другое требование.
Вязкое масло лучше, но оно легче застревает в подшипнике. С маловязкой жидкой смазкой этого не случится, но тогда подшипник будет «слабосильным». Одно хорошо, другое плохо. Что же предпочесть?
Компромисс. Дьячков разработал способ так выбирать вязкость смазки, чтобы подшипник выдерживал нужные нагрузки и масло в нем не застревало по пути.
Вязкость масла нужно выбрать поменьше, но для каждой машины, для каждого подшипника наилучшую – не слишком большую, но и не слишком малую.
Что ж тут мудреного? Все и так ясно, – можно сказать об этом. Но то, что кажется сейчас простым и ясным, – результат упорною труда, расчетов, опытов.
Раньше конструкторы шли вслепую. «Исправив» подшипник, изменив его размеры, место подвода смазки или вязкость ее, они «вдруг» получали неожиданно хорошие результаты – долговечность подшипника увеличивалась.