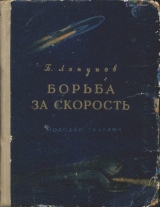
Текст книги "Борьба за скорость"
Автор книги: Борис Ляпунов
сообщить о нарушении
Текущая страница: 4 (всего у книги 17 страниц)
Но стоит только снять нагрузку, исчезает и рисунок. Ею можно сохранить, «заморозив» напряжения. Это не литературное, а чисто техническое выражение. Их «замораживают», но не холодом, а… теплом. Модель тогда делают из каркаса и заполнителя.
Каркас – «скелет» – тугоплавкий, при нагреве не плавится, но меняет форму под нагрузкой.
Внутри же «скелета» материал плавится и заполняет эту своеобразную форму. Застыв, он сохраняет те изменения, которые произошли с каркасом. Теперь можно охладить модель, и жидкий материал затвердеет. Остается только, остановив вращение модели, призвать на помощь оптические приборы, и застывший рисунок предстанет перед ними, как моментальная фотография.
А вот другой способ.
Напряжения вызывают перемещения частиц материала: деталь растягивается, изгибается, скручивается. Эти перемещения, или, как говорят, деформации, не произвольны, а связаны между собой. Зная деформации, можно определить и напряжения.
Как же определить деформации?
Тут приходится искать обходные пути. Ведь перемещения настолько малы, что глазом их заметить и измерить, да еще в быстродвижущейся детали, невозможно.
Но надо все же эти ничтожные изменения уловить, а затем их можно будет усилить, сделать заметными, и по ним уже судить о напряжениях.
Деталь покрывают особым лаком. Когда деталь работает, появляются деформации и лак растрескивается. Опасные места, где сильнее всего деформируется деталь, где напряжения максимальны и выдают себя трещинками.
На детали в разных местах приклеивают особым клеем кусочки тонкой бумаги. К бумажкам, в свою очередь, приклеены тончайшие проволочки. Через них идет ток.
Когда деталь деформируется, с ней вместе, повторяя все ее движения, вытягивается или сжимается и проволочка. Ее длина меняется, а поэтому меняется и сопротивление идущему по ней току. Эти еле заметные изменения усиливаются усилителем. По ним можно судить о напряжениях.
Так деталь «докладывает» исследователю о своей работе.
Можно заставить отчитываться и целую машину.
Так делают, например, в авиационной технике – при испытании самолетов.
Модель самолета помещают в трубу, где искусственно создается воздушный поток. При этом, как и при всяком испытании модели, пользуются подобием явлений: по поведению модели можно, применяя расчеты, судить и о работе большой машины.
На модели самолета, помещенной в воздушный поток, изучают, как будет работать настоящий самолет, какие будут действовать на него в полете силы. Зная эти силы, можно рассчитать самолет на прочность. Затем в лаборатории прочности испытывают под нагрузкой и отдельные детали и весь самолет. Он, этот опытный самолет, еще не поднимаясь в воздух, обречен на гибель. Но гибель его не напрасна: теперь конструкторы знают все опасные места, а зная врага, легче с ним бороться.
Но вернемся к материалам для быстроходных машин. Какие еще неожиданности таят они для конструктора?
Вот несколько любопытных примеров. Оказывается, сплавы повышенной прочности обладают повышенной чувствительностью к резким изменениям формы детали. Какая-нибудь выточка, канавка или переход от одного диаметра к другому – все это вызывает увеличение напряжений в этих местах, а значит, и опасность разрушения.
Но ведь сложная форма детали с такими «опасными» местами – не прихоть конструктора, не произвол.
Как же быть? Образец из нового, высокой прочности сплава сдаст экзамен на «отлично». А за сделанную из того же самого сплава деталь сложной формы ручаться нельзя.
«Где тонко, там и рвется», – говорит пословица. И бывали случаи, когда в таком «тонком», опасном месте и рвались валы турбин, разлетались на куски быстроходные электромоторы и центрифуги.
Теперь, пожалуй, не покажется преувеличением утверждение ученых, что ответ на вопрос, почему отличаются по прочности образец металла и деталь из него, – это одна из важнейших задач современной техники, техники больших скоростей, давлений, температур, требующей высокопрочных материалов.
Намечаются и используются пути борьбы с вредными «скоплениями» напряжений.
Конструкторы так проектируют машину, чтобы не было резких переходов – от большей толщины к меньшей, от одной формы к другой. Плавные переходы вместо резких, закругленные формы вместо острых. Избегать скопления, концентрации напряжений – таков девиз конструктора.
Идя таким путем, лишь сравнительно немного изменив конструкцию одного электромотора, конструкторы получили возможность увеличить нагрузку в полтора раза без вреда для машины.
Технологи находят способы увеличивать прочность поверхностных слоев металла. Упрочняя поверхность детали, они делают металл более выносливым, как бы «бронируют» его. Не усложняя состава сплава, говорят они, мы делаем его более стойким.
И техника широко применяет сейчас различные способы повышения прочности, которые помогают бороться с вредным влиянием концентрации напряжений.
Рядом с опасным местом, за которое боятся больше всего, делают надрез. Это покажется с первого взгляда странным: вместо того чтобы повышать прочность, ее нарочно уменьшают, да еще как! Рядом с какой-нибудь большой выточкой делают выемку, как будто намеренно портя деталь.
Замечено, что даже клеймо, которое ставят на готовую деталь из прочного сплава, вредит ей. Оно может стать тем самым тонким местом, которое рвется: с него начнется разрушение. Поэтому вместо клейма принятую деталь контролер отмечает особыми чернилами.
Место, где есть углубление, трещина, выемка, – это ранка, которая может перерасти в язву.
Так почему же нарочно портят деталь?
Оказывается, выемки служат для «отвлечения» напряжений от самых опасных мест. Они принимают на себя удар и тем самым понижают напряжение там, где опасность всего сильнее. Верно говорят, что клин клином вышибают. Конечно, их делают не произвольно, а так, чтобы и в самом деле не повредить детали. Такие выемки, надрезы именуют «разгружающими».
Одной лишь прочностью не ограничиваются требования конструктора к материалу. Яркий пример тому – самолет.
Нигде, пожалуй, так остро не стоит вопрос о легкости материала, как в авиации.
Прочным, но легким должен быть материал крылатой машины. В самолетостроении широко применяются легкие металлы.
Алюминиевые сплавы – основной материал у авиастроителей. Они почти в три раза легче стали. Прочность же их может быть такой, как у углеродистой стали. Они достаточно стойки против коррозии – врага металлов.
Еще более легки магниевые сплавы. Над тем, чтобы увеличить их прочность и стойкость против коррозии, работают сейчас металлурги. Они создали для авиации сплав «электрон» – из магния, цинка, алюминия и марганца. Они создадут и еще более легкие, прочные и стойкие сплавы. Другие элементы менделеевской таблицы придут им на помощь.
Таков, например, бериллий – легкий, стойкий, прочный металл для авиации завтрашнего, а отчасти уже сегодняшнего дня.
«За бериллием будущее! Геохимики, ищите новые месторождения в гранитных массивах нашей страны! Химики, научитесь отделять этот легкий металл от его спутника алюминия! Технологи, сделайте легчайшие сплавы, не тонущие в воде, твердые, как сталь, упругие, как резина, и стойкие, как платина!» – говорил академик Ферсман.
Сверхлегкие, сверхпрочные, сверхстойкие, сверхжароупорные сплавы для сверхбыстроходных машин создадут советские металлурги.
В новой, высокоскоростной технике применяются не только металлические, но и неметаллические материалы.
Пластмассы сейчас распространены так широко, что это даже дало повод назвать наш век – век радио, электричества, атомной энергии – веком пластмасс. Изделия из пластмасс мы встретим всюду: на нашем письменном столе и на одежде, в комнате и на улице.
И в машиностроении, в быстроходных машинах пластмассы находят свое место. Вот лишь один пример наиболее частого применения пластмасс.
Слыхали ли вы, с каким лязгом срабатывают зубчатые шестерни, когда шофер грузовика включает передачу?
Шум при работе зубчатых шестерен растет с ростом скорости. Возникла новая проблема – борьба с шумом быстроходных передач. Они есть, например, в станках. С каждым годом все больше и больше станков у нас переводится на скоростное резание металла. Поэтому и задача не из таких, чтобы про нее забыть.
Она решается разными путями. Один из путей – бесшумные шестерни из пластмассы.
Легкая, но прочная шестерня из пластмассы допускает на больших скоростях передачу больших нагрузок. Это кажется парадоксом – пластмасса прочнее стали, но это так.
Пластмасса в несколько раз легче чугуна или стали, поэтому она меньше подвержена действию центробежной нагрузки при вращении. И пластмассовые шестерни, как и части подшипников, мы встретим в быстроходных машинах.
Если говорить о такой быстроходной машине, как самолет, то в нем мы встретим много деталей из пластмассы.
Стекло в кабине, которое не разбивается от удара, и ручка управления, лопасть воздушного винта и детали электрооборудования, баки для масла и бензина и очень многое другое делаются из пластмасс.
Все больше и больше проникают в технику изделия, изготовленные спеканием и прессованием металлических порошков. Таким же способом готовят изделия из керамики, скажем, кирпичи. И способ этот назвали металлокерамикой. Его применяют для приготовления твердых сплавов.
Растет прочность сплавов – труднее их обрабатывать. Резать металл можно лишь резцом из более стойкого металла. Нельзя резать той же сталью, которую нужно обработать.
Простую, обычную сталь можно резать инструментальной, легированной сталью, содержащей повышенное количество углерода и другие элементы. Но прочность сплавов все растет. Появились быстрорежущие стали. Однако и их твердости не всегда хватало, чтобы резать новые прочные сплавы.
Тогда им в помощь создали специальные сплавы для резцов. Их готовят прессованием и спеканием тугоплавких карбидов металлов (вольфрама и титана) – химических соединений их с углеродом – и добавляют к ним кобальт. Карбиды как бы цементируются кобальтом.
Резцы твердые, как алмаз, дает металлокерамика. Не только резцы, но самосмазывающиеся подшипники с мельчайшими порами – «масленками», тормозные колодки самолетов и многое другое, нужное технике. Достаточно сказать, что на современном большом самолете сотни различных деталей приготовлены из металлических порошков.
Металлокерамика, как и другие отрасли современной металлургии, нужна высокоскоростной технике.
Новые материалы для машин создают советские ученые и инженеры.
Металлургия нашей страны добилась больших успехов. Вот лишь один пример из работ лауреатов Сталинских премий.
Инженеры завода «Русский дизель» и работники одного из научно-исследовательских институтов создали сверхпрочный чугун. Из этого дешевого чугуна можно изготовлять многие детали машин, которые до последнего времени делались стальными, например коленчатые валы и другие части быстроходных двигателей.
В чугуне есть графит. Крошечные графитовые пластинки ослабляют чугун, и, чтобы упрочить его, чугун подвергают сложной, длительной и дорогой тепловой обработке. Тогда удается превратить пластинки графита в шарики и повысить прочность чугуна.
Создать высокопрочный и дешевый чугун было нелегко.
«Долго продолжались кропотливые опыты и испытания, начатые в маленьких лабораторных печах и перенесенные затем в литейные цехи, – рассказывает руководитель работ лауреат Сталинской премии Б. С. Мильман. – Наконец, было установлено, что при определенных условиях магний или его сплавы, добавляемые к жидкому чугуну, вызывают в нем образование нужных включений графита.
Но здесь нам пришлось столкнуться с новой трудностью. Дело в том, что магний кипит при более низкой температуре, чем температура жидкого чугуна. Введенный в жидкий чугун, он быстро испаряется. Пары его, выделяясь из литья, могут вызвать выброс жидкого металла из ковша.
Поднявшись над поверхностью чугуна, эти пары сгорают, образуя ослепительно белое пламя.
Дальнейшие опыты и исследования позволили решить задачу введения магния в литье.
Была разработана совершенно безопасная технология получения сверхпрочного чугуна в производственных условиях».
В моем рассказе нет, конечно, полной картины. Рассказать о всех трудностях и путях создания материалов для быстроходных машин невозможно. Я хотел бы, чтоб вы почувствовали, насколько это важно и трудно.
Рождению новых, улучшению старых материалов обязана техника многими своими успехами.
Полвека тому назад на каждую лошадиную силу развиваемой авиационным двигателем мощности приходилось 20 килограммов веса. Сейчас авиадвигатели развивают мощность до 3 тысяч лошадиных сил. Значит, такой двигатель должен был бы весить 60 тонн! А он весит теперь лишь около тонны. Этого добились благодаря прочным, но легким материалам.
Дизельмотор за полвека удалось облегчить почти в 250 раз. Паросиловую установку на электростанции – в 25 раз. Это позволили сделать прочные, но легкие материалы.
Еще недавно газовые турбины применялись только как вспомогательные двигатели, а теперь газовая турбина позволяет реактивным самолетам догонять звук. В этом заслуга и создателей новых жаропрочных сплавов.
Ракетные двигатели, развивающие мощность в полмиллиона сил при скорости в 5 тысяч километров в час, двигатели сверхзвуковых самолетов и в будущем межпланетных кораблей – в этом достижения не только конструкторов, но и металлургов, создателей жаростойких и прочных сплавов.
Какие бы быстроходные машины мы ни взяли – турбины и станки, авиадвигатели и гироскопические приборы, воздуходувки и электромоторы, – заслуга в их создании наряду с представителями других отраслей науки и техники металлургов, металловедов, ученых-прочнистов.
Успехами советской металлургии мы заслуженно гордимся. Без достижений металлургии и науки о прочности материалов была бы невозможна и современная высокоскоростная техника.


ПОБЕДА НАД МЕТАЛЛОМ
На одном из моторостроительных заводов, в цехе, где обрабатываются шейки коленчатого вала, произошел такой случай. Двое рабочих занимались шлифовкой валов. Работали оба одинаково, детали получились хорошего качества, и мастер у обоих принял работу. Когда собрали моторы, оба вала установили на свои места, а затем на испытательном стенде моторы начали испытывать.
И тут произошла странная вещь. Валы, изготовленные совершенно одинаково: в одном и том же цехе, на одинаковых станках и одинаково хорошо отшлифованные, повели себя по-разному.
Один работал нормально. Другой же «капризничал»: его заедало, смазка выдавливалась, – словом, не работа, а брак.
Моторы остановили, разобрали, валы осмотрели. Действительно, обработаны они одинаково, только один рабочий снимал стружку шлифовальным кругом, двигая его слева направо, а другой делал то же, передвигая круг справа налево. Какая, подумаешь, разница! Результат-то ведь один и тот же.
Но когда на валы попала смазка, она повела себя по-разному: на одном из валов держалась, на другом – быстро вытекала по тем еле заметным спиралькам, которые остались после обработки. Эти спиральки располагались так, что открывали маслу дорогу, а с уходом масла вступало в свои права трение – грозный враг машины. И вал отказывался работать.
Оказывается, обрабатывая металл, можно и испортить его, если не глядеть в будущее детали, не видеть ее в работе.
Заглянуть в будущее здесь означает – определить предварительно, насколько шероховатой станет деталь после «приработки», когда трение еще не вредно, а полезно. Если бы на валу, о котором мы говорили, были заранее сделаны штрихи не в одну сторону, а крест на крест, – масло не вытекало бы сразу, износ не был бы столь велик.

Обработка поверхности металла.
Обработка меняет свойства поверхности металла. Но как же узнать, какой станет поверхность в работе?
Это сделал лауреат Сталинской премии профессор П. Е. Дьяченко. Он разработал способы определения наилучшего, как говорят, оптимального качества поверхности, помогающие технологам бороться с износом.
Найдены методы получения гладкой поверхности металла.
Таких способов обработки – их называют чистовыми – есть теперь несколько.
Замечено было, что при обточке детали резцом с большой скоростью поверхность получается более гладкой. Особенно чистой получается она, если снимать тонкую стружку: тогда резец не успевает повредить поверхностный слой, заметно нагреть его. Так происходит дело при точении в тонко-расточных станках, на которых обрабатываются, например, детали реактивных двигателей. Дело это не только тонкое, но и точное: деталь вращается в станке со скоростью в несколько тысяч оборотов в минуту, без всяких колебаний, резец понемногу и плавно врезается в металл. Вся обработка ведется автоматически – только автомат и может выполнить такую сложную, точную работу.
Подобным способом, снимая тонкий слой стружки, фрезеруют детали на станках для тонкого фрезерования.
Когда нужна еще более гладкая поверхность, у технолога есть в запасе другие способы.
Он может обратиться к помощи абразивов – материалов, состоящих из твердых режущих зерен, вкрапленных в связующую массу. Простейший абразив – точильный камень или наждачная шкурка. Зерна абразива – это своеобразные резцы, которые срезают неровности на поверхности детали.
Деталь и абразивные бруски в станке двигаются в противоположные стороны относительно друг друга. Режущие зерна выравнивают поверхность. И чем сложнее их относительное движение, тем лучше срезаются все выступы, гребешки, тем более гладкой получается деталь. Абразивные бруски могут, например, вращаться и в то же время двигаться взад и вперед. При таком способе получается зеркальная поверхность, на которой еле заметны штрихи от крошечных резцов-абразивов.
А при «сверхотделке» – суперфинише – бруски и деталь могут одновременно совершать более десяти различных движений, колебаться, вращаться, двигаться в разных направлениях. Постепенно ликвидируются все последствия предыдущей обработки. После шлифовки можно зажечь спичку об отшлифованную деталь, потому что на ее поверхности еще остались неровности. После суперфиниша спичка не загорится.
Например, нужно обработать кольцо шарикоподшипника.
Не будем повторять еще раз, насколько важно получить возможно более гладкую поверхность, – особенно, если подшипник работает на больших скоростях.
После шлифовки, полировки и притирки – кропотливой, тщательной обработки – поверхность все же еще неровна. Их немного, этих микроскопических бугорков и впадин, но они есть.
Кольцо зажато в станке и медленно вращается. Внутри по кольцу скользят, плотно прилегая к нему, брусочки, совершая быстрые, незаметные для глаза, колебания – несколько сот в секунду, и в то же время деталь делает ряд других, более медленных движений. Металл не нагревается при этом – на поверхности почти не остается трещинок, неровностей. Она получается гладкой, как зеркало, и очень чистой.
Но нельзя упускать из вида другую сторону дела.
Обработка меняет свойства поверхностного слоя. Внутри металл один, снаружи, с поверхности, он становится другим.
Резец снял стружку и нарушил правильное расположение кристаллов, смял, сломал их. Металл слабеет: он легче поддается разрушающему действию напряжений. Малейшая трещинка может теперь грозить катастрофой.
Твердый и хрупкий чугун, например, после обработки может стать с поверхности мягким, пластичным.
При шлифовке, особенно когда она идет с большой скоростью, обрабатываемая поверхность местами нагревается. При обработке резцом температура может доходить до 1000°! А теплота действует на металл, и может случиться, что свойства металла изменятся в худшую сторону.
Прочные сплавы, из которых делают детали быстроходных машин, – особенно чувствительны к обработке. Вот почему важно упрочить такой сплав с поверхности, сделать его выносливым, парализовать вредное влияние обработки.

Плавка в индукционной электропечи.
Эту задачу решают разными путями.
На помощь призывают химию и электричество, тепло и холод и другие способы покорения металла.
Можно насытить поверхностный слой азотом или углеродом. Сложные химические соединения азота или углерода с металлом укрепят его поверхность, потому что твердость их очень высока. Металлу, ослабленному обработкой, не будет так страшен износ.
Однако не очень-то просто заставить металл соединиться с азотом. Азот с трудом вступает в соединения и то лишь при высокой температуре.
Деталь приходится нагревать в течение нескольких суток в аммиаке – газе, содержащем азот. Прочность заметно возрастает, а размеры азотированной детали изменяются всего лишь на 1–2 микрона.
Технологи одевают металл в «броню», покрывая его слоем другого металла, более прочного.
Такое бронирование часто бывает необходимо потому, что не только обработка разрушает металл, но и та среда, в которой он работает.
Тяжело приходится материалам турбин при их работе. Мы говорили о том, что лопатки паровой турбины работают в струе перегретого пара, в который попадают различные вещества, усиливающие разъедание металла. Лопатки газовой турбины находятся в потоке раскаленных газов, сильно разбавленных воздухом, значит – кислородом, который способствует быстрому ржавлению, разъеданию металла. И лопатки могут быстро выйти из строя, разрушиться, если их не защитить.
Для такой защиты в металл добавляют элементы, повышающие его стойкость к разъеданию – коррозии. Они образуют прочную защитную пленку. Применяют и другие способы.
Металл азотируют. Металл покрывают защитным слоем цинка – оцинкованные изделия не боятся сырости. Хромированные детали лучше сопротивляются износу. Тончайшая пленка окислов хрома не дает окислению проникнуть в глубь металла, разрушить его. Выходит, с окислением борются окислением. Окисляясь, «жертвуя собой», металл покрытия защищает деталь.
Металл покрывают металлом с помощью электричества. В электролитических ваннах, где растворены соли хрома или цинка, никеля или серебра, ток отлагает тончайший слой металла на поверхности детали.
В этих ваннах электричество может не только никелировать или хромировать металлы. Оно может их полировать. Такая полировка одновременно и борьба с коррозией.

Плавка в дуговой электропечи.
Нетрудно понять, почему электролитическую полировку сейчас все шире применяют технологи. Детали часто бывают очень сложной формы. Примером может служить турбинная лопатка, поверхность которой изогнута довольно причудливо. Но это не прихоть конструктора, а результат точного расчета, подтвержденного опытом.
Чтобы отполировать лопатку на станке, нужно полчаса. За то же время электрополировкой можно обработать тысячу лопаток!
Когда электричество наносит покрытие, оно наращивает металл.
Когда электричество полирует, оно, наоборот, снимает слой металла. Тот слой, где есть неровности, царапины, трещины, то, что мешает детали быть гладкой, – удаляется.
Сглаживается поверхность металла.
Следов обработки резцом на ней уже нет, и металл становится более прочным снаружи. Полировка защищает его от коррозии и износа. Почти в полтора раза повышается стойкость режущего инструмента к износу.
Оказалось, что с помощью электричества можно покрыть металл слоем другого металла и не в электролитических ваннах.
Электроискровая обработка – открытие советских ученых Б. Р. и Н. И. Лазаренко – позволяет наносить равный слой металла на металлическую деталь. При этом получается очень прочное покрытие. Так электроискровым способом покрывают резцы слоем твердого сплава.
Оказалось, что вообще электроискровая обработка дает более прочную поверхность, чем механическая. О том, как электрическая искра обрабатывает металл, мы поговорим ниже.

Закалка токами высокой частоты.
Электричество может закаливать поверхность металла.
Вспомним про быстроходные зубчатые передачи. Зубчатые колеса нужно сделать износоустойчивыми. Что же тут, казалось бы, мудреного! Закалить их – и только. Но этим дело лишь испортишь.
Если вся шестерня будет закалена, она станет не только твердой. Она станет и хрупкой. А хрупкая шестерня не выдержит толчков и ударов, неизбежных при работе зубчатой передачи.
Выход в том, чтобы закалить металл лишь с поверхности, не закаляя сердцевины. Твердая «корка» предохраняет от износа, а вязкая сердцевина хорошо сопротивляется толчкам и ударам.
Это и позволяет сделать закалка токами высокой частоты, разработанная лауреатом Сталинской премии В. П. Вологдиным и другими советскими учеными.
Шестерня помещена внутрь нагревательного индуктора высокочастотной закалочной установки. Этот индуктор создает быстропеременное электромагнитное поле. Оно возбуждает токи в металле шестерни, которые растекаются по поверхности, прогревают ее; внутрь же тепло не проходит. Закаливается только тонкий поверхностный слой – то, что нам и нужно.
Как происходит закалка токами высокой частоты, каковы были ее первые шаги?
Вот что рассказывает лауреат Сталинской премии доктор технических наук профессор Г. И. Бабат:
«Наступил долгожданный момент первого испытания. Большая шестерня от коробки передач укреплена внутри нагревательного витка из медной трубки.
Щелкает контактор. Генератор включен. Нагрев начался.
Блестящая полированная поверхность стали темнеет. По ней проходят цвета побежалости: соломенно-желтый, синий, темнобурый.
Измеритель мощности показывает, что сталь потребляет восемьдесят киловатт. Проходит секунда, вторая. Боковая поверхность шестерни начинает светиться вишневым накалом.
И тут – удивительная вещь! – стрелка измерителя мощности идет в обратную сторону. Резко падает поток энергии, потребляемой раскаленным металлом.
Сталь берет теперь в 8 раз меньше мощности, чем мгновенье до того.
Нам повезло, удивительно повезло! Оказалось, что наиболее распространенные марки стали обладают свойством уменьшать свое потребление мощности – „самовыключаться“ из процесса нагрева, как только температура поверхностных слоев изделия достигнет значения, необходимого для закалки… Так сталь сама себя спасает от перегрева…

Электролиз.
Для массового производства существуют теперь специальные закалочные станки-автоматы. Они вводят закаливаемое изделие в индуктор, автоматически дают требуемую выдержку нагрева, а затем переносят изделие в охлаждающую жидкость (воду, масло, эмульсию), или же охлаждающая жидкость выбрызгивается на нагретое изделие через отверстия в нагревательном индукторе. Такие закалочные автоматы могут быть включены в общую линию станков механической обработки. При этом отпадает иногда необходимость в специальном термическом цехе.
Высокочастотный нагрев удешевляет производство, оздоровляет условия труда, повышает живучесть механизмов».
Химией, теплом, электричеством не исчерпывается, однако, вооружение технолога.
Он может обработать деталь дробью. Если посмотреть, как это делается, то покажется, что совершается преступление. Готовую обработанную деталь бомбардируют градом маленьких стальных или чугунных шариков, размером от 0,5 до 1,5 миллиметра. Они с силой выбрасываются струей сжатого воздуха или лопатками быстровращающейся турбинки.
Обработка дробью упрочняет поверхностный слой на глубину примерно 0,2 миллиметра. Происходит, как говорят инженеры, наклеп – упрочение металла, вызванное изменением свойств его поверхностного слоя.
Долговечность, живучесть детали возрастает в несколько раз.
Кроме обдувки дробью, технолог может применить, если речь идет о детали цилиндрической формы, обкатку роликами, также вызывающую наклеп, а значит, и повышение поверхностной прочности.
Деталь зажата между тремя стальными закаленными роликами. Ролики давят на нее с силой тем большей, чем крупнее деталь. И, держа ее в своих крепких объятиях, они обкатывают ее, «проглаживают», как своеобразный утюг, со всех сторон. Ровная, приглаженная поверхность получается после такой обкатки, притом и более прочная. Иногда утюжка роликами делает поверхность детали такой чистой, что ни шлифовки, ни полировки уже не требуется.

Электрополировка.
Наклепом пользуются и при хорошо известных способах холодной обработки – таких, как ковка, штамповка, прокатка, которые придают металлу повышенную прочность. Штамповка, кроме того, позволяет изготовлять детали очень точно, – и многие детали такой быстроходной машины, как газовая турбина, штампуются.
Холодная обработка, вызывающая наклеп, и горячая обработка – такая, как закалка, упрочняют металл.
Тепло издавна служило человеку для изменения свойств металлов.
Советские ученые поставили ему на службу и холод. На наших металлургических и машиностроительных заводах впервые появился новый помощник человека, обрабатывающий металл. Холод помогает справиться там, где бессильным оказывается тепло.
Он также меняет внутреннее строение металла. Сталь сложного химического состава требует и сложной тепловой обработки. Чтобы закалить такую сталь, нужно добиться перестройки кристаллов в металле. Бывает, что такая перестройка не успевает закончиться, хотя сталь уже остыла. Тепловая обработка завершена, но металл перестроился не весь: остались еще участки незакаленные, мягкие.
Теперь, когда растут скорости, напряжения, давления, температуры в машинах, с таким, казалось раньше неизбежным, недостатком закалки мириться стало нельзя. Но как с ним бороться?
Иностранные ученые бессильны были ответить на этот вопрос. него ответили советские ученые. Надо дать металлу время, чтобы перестройка структуры металла закончилась полностью, чтобы закалка была окончательно завершена, решили они. Для этого металл нужно охладить не как обычно до комнатной температуры, а еще ниже: до 70—100° ниже нуля.
И действительно, в охлажденном металле закалка (скорее уже не закалка, а «замораживание») шла до, конца. Когда же металл вновь нагревался до комнатной температуры, он сохранял приобретенные закалкой свойства. Он становился твердым, и гораздо более твердым, чем только при закалке, потому что теперь в нем не было «мягких» участков, той капли дегтя, которая портила бочку меда.
Обработка холодом позволяет повысить твердость деталей машин иногда почти на треть или на половину. Улучшается качество деталей– например таких, как шестерни, увеличивается срок их службы.
Мы говорили до сих пор о том, как упрочить металл, о том, как для этого инженеры-технологи пользуются теплом и холодом, электричеством и химией, обработкой дробью и обкаткой роликами.
Все это – способы упрочить металл.

Электролитическое рафинирование (очистка).
А теперь нам придется поговорить о том, как уменьшить прочность металла.
Уменьшить прочность? Но борьба за скорость – это борьба и за прочность. Это борьба за прочный металл, который нужен для быстроходных машин. Как же можно бороться с прочностью? И, главное, зачем?