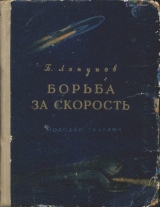
Текст книги "Борьба за скорость"
Автор книги: Борис Ляпунов
сообщить о нарушении
Текущая страница: 7 (всего у книги 17 страниц)
Теперь теория, строгий расчет пришли им на помощь.
Так советский ученый решил труднейшую задачу борьбы за долговечность подшипника скольжения для скоростных машин.
Подшипники высокоскоростных машин быстро нагреваются, и чтобы уменьшить нагрев, применяют смазку с меньшей вязкостью, более жидкую, чем масло, например керосин.
Но есть и другие жидкости, еще менее вязкие. Нельзя ли применить для смазки, скажем, воду? Ведь ее применяют для смазки подшипников с текстолитовыми вкладышами на прокатных станах.
Попробовали. Результат – подшипник, изготовленный из прочной стали, через несколько часов сдал, не выдержал, так велик был износ.
Трение растет со скоростью. И даже в жидкости оно будет таким значительным, что подшипник работать не сможет – сгорит.
Можно ли все же найти смазку с малой вязкостью, которая не нагревалась бы так, как масло, служила бы дольше, чем вода?
Да. Это совершенно другая смазка. Газовая. Воздушная – в первую очередь.
Я видел такой опыт.
Ротор и корпус центрифуги – аппарата для очистки жидкостей – включили в электрическую цепь. Жидкость подводится в центрифугу по трубке и впрыскивается в ротор, похожий на шпиндель сверлильного станка. Когда ротор вращается, жидкость центробежной силой расплескивается по стенкам и облегает их тонким слоем. Осадок из примесей отлагается на стенках и удаляется, а очищенная жидкость проходит через ротор и выплескивается наружу. Так все время проходит жидкость через это «чистилище», вращающееся с бешеной скоростью – 20 тысяч оборотов в минуту. Есть центрифуги и на 150 тысяч оборотов.
Ротор в верхней части соединен передачей с электромотором, а нижней, «пятой», упирается в подпятник – чашечку, в которую он входит, как пестик в ступку. Между пятой и подпятником – крошечный зазор.
Нет вращения, и под собственной тяжестью ротор слегка провисает, упирается в подпятник, замыкает электрическую цепь. В цепи появляется ток.
Включили двигатель, ротор начал набирать обороты, и через несколько секунд прибор показал, что цепь разорвана. Тока нет!
Это значит – появился воздушный промежуток, воздушная «подушка» между пятой и подпятником, и ротор «всплыл» в воздухе, как пробка в воде.
Тончайший слой воздуха разделяет теперь трущиеся поверхности. На ярком свету можно даже увидеть эту прослойку из воздуха, но в том, что она существует, нас наглядно убеждает и стрелка гальванометра, упорно стоящая на нуле.
Выключен двигатель, и обороты падают. Тока все еще нет. Постепенно уменьшается толщина воздушного слоя. Все медленнее вращается ротор. 600 оборотов в минуту… 500… 400… И только тогда начинает рваться слой смазки. Пята касается подпятника. Стрелка уходит от нуля. Цепь снова замкнута. И наконец ротор останавливается.
Инженерам пришлось остановиться на числе оборотов 21 тысяча в минуту не потому, что не выдерживал подшипник. Не выдерживала ременная передача от мотора к ротору – перетирался ремень.
А подшипник с газовой смазкой может безотказно работать при сколь угодно большом числе оборотов.
– Валы на опорах с воздушной смазкой могут вращаться с неограниченной скоростью, – говорит советский ученый С. А. Шейнберг, который разработал теорию и конструкцию таких опор – подшипников с газовой смазкой.
Подшипники с воздушной смазкой появились в последние годы и за рубежом. Но конструкторы решали задачу их смазки сложным путем – применяя сжатый воздух. Воздух принуждали идти в подшипник под давлением. Значит, нужен источник питания сжатым воздухом, а это усложняет конструкцию. Значит, работа всей машины зависит от бесперебойной подачи сжатого воздуха.

Суперцентрифуга.
Иной путь, простой и оригинальный, нашел советский ученый. Не нужно подавать воздух в подшипник. Не нужен сжатый воздух, и отпадает все, что с ним связано, – усложнение машины, ненадежность работы.
Подшипник может сам питать себя воздушной смазкой.
Нет вращения, и вал – «шип» – лежит в подшипнике, касаясь его. В зазоре между ними воздух. Но зазор этот не сплошной, не кольцевой – пока шип лежит в подшипнике.
Вал начинает вращаться. Он захватывает воздух, увлекает его за собой, гонит в узкую часть зазора, туда, где вал касается подшипникового кольца.
Растут обороты, и все сильнее вгоняет вал «под себя» воздух. При 400–500 оборотах в минуту воздух уже настолько собрался с силами, настолько сильно давит там, что вал не выдерживает. Он приподнимается и продолжает вращаться, уже не касаясь подшипника. Упругая воздушная подушка не дает ему опуститься. Вал «всплывает» в воздухе.
Теперь вместо трения шипа о подшипник есть только трение воздуха о воздух, одного воздушного слоя по другому. А это трение ничтожно – ведь вязкость воздуха очень мала – в 100 раз меньше, чем, например, у керосина. Поэтому малы и потери на трение. Поэтому и мал нагрев – этот главный бич подшипника на больших скоростях. Всего на 1,5–2 градуса повышается температура при воздушной смазке.
И так как вал сам увлекает воздух в смазочный зазор, не нужно заботиться о питании подшипника смазкой. Появляется воздушная подушка – и дальше все идет само собою, «как по маслу».
Подшипник, который сам себя смазывает, – это самый простой из всех подшипников.
Кстати, есть и подшипники с масляной смазкой, которые сами себя смазывают.
Такие подшипники создала порошковая металлургия.
Спрессованный под давлением подшипник из железа и графита получается не сплошным, а пористым, подобно губке. Как губка впитывает воду, так и пористый подшипник впитывает своими микроскопическими порами масло. При работе оно постепенно выдавливается из этих крохотных «масленок» и смазывает подшипник.
Но долго работать без смазки пористый подшипник не может. Как выжатую губку, его нужно снова наполнить. И остается главное – масло, нагревание и все связанные с ними беды. Для очень больших скоростей пористый подшипник не годится.
Воздушная смазка выводит нас из тупика, куда заводят большие скорости. Она оправдала себя в работе. И сейчас советские заводы выпускают быстроходные машины с подшипниками на воздушной смазке. Таковы, например, суперцентрифуги на 21 тысячу оборотов.

Подпятник с воздушной смазкой (разобран).
Там, где отказывает обычный подшипник, ему на смену приходит новый, простой и надежный, с воздушной смазкой, который отлично работает при сверхвысоких скоростях. Надо отметить, что применять его можно пока лишь там, где невелики нагрузки.
Прежде чем создать такой подшипник, пришлось немало поработать. Ведь то, что мы рассказали о нем, – это идея, принцип, а от идеи до конструкции – путь далекий. Теория и опыт, расчеты и испытания, поиски наилучшего решения – таков этот путь.
Нужно было узнать, когда и как возникает воздушная подушка, как работает с ней подшипник, не мешает ли ему трение металла о металл.
Нужно было воплотить идею воздушной смазки в реальную конструкцию, с учетом всего, что говорили теория и опыт.
Чтобы появилась воздушная подушка, нужен зазор. Величина его должна быть переменной. Она должна меняться – там, куда вал увлекает за собой воздух, быть меньше. Только тогда, вгоняя воздух в суженный зазор, и можно его сжать, уплотнить, создать упругую подушку. Только тогда и может вал отделиться от опоры и повиснуть в воздухе.
Хорошо, если подшипник цилиндрический.
Там это условие выполняется само собою.
Когда вал не вращается, он касается цилиндра, и зазор при взгляде на него «в профиль» имеет форму серпа. Вал начнет вращаться, он погонит воздух в узкий конец «серпа». Появится воздушная подушка. И вал приподнимает сам себя – «всплывает».
А если подшипник другой формы? Например, как у подпятника в центрифуге? Нужно было создать такую конструкцию опоры, чтобы выполнялось основное условие воздушной смазки – зазор переменной толщины.
С. А. Шейнберг сделал так.
На круглой металлической пластинке – колодке – он расположил по радиусам ребра. Эти ребра, возвышаясь над ней, не дают верхней тонкой пластинке плотно прилегать к колодке. Затем он соединил их винтами. Там, где ребер нет, пластинки сошлись вплотную. Там, где есть ребра, они не могли сойтись. В результате верхняя пластинка изогнулась, на ней образовались волны.
Появились волны, появился зазор переменной толщины – то, что было нужно.
Когда пята будет вместе с ротором вращаться, она загонит воздух в этот зазор, сожмет его – и возникнет воздушная прослойка. Всего несколько тысячных долей миллиметра отделяет пяту от подпятника, но этого достаточно, чтобы весь ротор вращался в воздухе и трение почти исчезло.
Сотни часов может работать подшипник с воздушной смазкой при огромных числах оборотов с ничтожными потерями на трение, ничтожным нагревом.
Так ведется борьба с трением в машинах, где скоростям сейчас ведут счет на десятки тысяч оборотов.
Их требует промышленность. Ведь в некоторых шлифовальных станках шпиндель делает 100 тысяч и больше оборотов в минуту. Ведь широко применяется теперь сверхскоростное фрезерование.
Советскими инженерами созданы сверхскоростные шпиндели для расточки и шлифовки небольших отверстий – на 120 тысяч, а в опытных образцах и на 200 тысяч оборотов в минуту.
Большая скорость здесь совершенно необходима – без нее нельзя добиться нужной чистоты обработки.
Очень высокие скорости необходимы не только для шлифования.
Летчику и моряку нужны гироскопические приборы – креномер, гирокомпас и другие, в которых с большой скоростью вращается волчок. Скорость вращения волчков в этих приборах доходит до нескольких десятков тысяч оборотов в минуту.
Гироскоп – основа автопилота, который без помощи человека ведет по заданному курсу самолет или ракету.
Отклонение от курса – рамка гироскопа, соединенная с корпусом самолета или ракеты, замыкает контакт электрической цепи. Включаются моторы, поворачивающие рули, – и самолет снова на верном курсе.

Гироскоп и его применение.
Скорости самолетов выросли за последние годы. Ракета движется с максимальной скоростью 5 000 километров в час. Нужна повышенная чувствительность гироскопических приборов, высокие скорости вращения гироскопа.
Бороться с трением приходится не только в подшипнике.
Всюду, где касаются друг друга движущиеся части машин, – есть трение.
Цилиндр и поршень, шестерни зубчатых передач – таких примеров, таких пар можно было бы привести множество, самых разных. А общее у них одно– трение, вызывающее износ.
Трение – это прежде всего тепло. Им можно добывать огонь: нагрев при трении воспламеняет головку спички. Если металл плавится легко, то трущаяся поверхность не замедлит расплавиться. Расплавленные частички такого металла приварятся к другому металлу.
Трение отрывает мельчайшие частички с металлической поверхности и портит ее.
В новой машине трение на первых порах бывает даже полезно. Детали «прирабатываются», «привыкают» друг к другу, как приспосабливаемся мы к новой обуви. Но скоро оно начинает свою разрушительную работу и в конце концов выводит машину из строя. За машиной поэтому нужно все время следить – не истерлись ли ее части.
Не надо забывать также, что машина работает не в пустоте. Ее окружает воздух, она имеет дело с водой, или паром, или горячими газами. Это ослабляет металл. Он становится менее стойким к износу.
Поверхность металла обработана. Этим разрушены кристаллические решетки в тонком обработанном слое. Металл с поверхности уже не тот, что был и что остался внутри. Он легче поддается окислению, становится более хрупким, искрашивается.
Некоторые сплавы обладают самозащитой против окисления. На них появляются тончайшие пленки окислов, не дающие окислению идти дальше, в глубь металла. Эту самозащиту стремятся усилить. В те – сплавы, которые должны работать в тяжелых условиях, где окисление неизбежно, вводят добавки, способствующие образованию защитной пленки.
Детали смазывают, чтобы уменьшить трение и износ. Смазка необходима, но она отчасти приносит и вред, хотя это и кажется странным на первый взгляд.
Слой смазки прилипает к поверхности, увлекает за собой другие слои – и смазка заполняет зазор.
Как мы знаем, проникая в мельчайшие трещинки на поверхности металла, смазка «расклинивает» их, увеличивает, помогает износу «портить» поверхность.
Мы – в который раз! – встречаем противоречие. Обрабатывая металл, невольно разрушаем его поверхность. Стремясь уменьшить трение, а значит, износ, смазкой увеличиваем его.
И задача технолога, инженера состоит в том, чтобы примирить эти противоречия. Обрабатывая и смазывая металл, сделать износ как можно меньше.
Правильным выбором смазки, способа ее подачи смягчают неизбежный вред, стараются предотвратить сильное разрушение поверхности, сделать износ равномерным, постепенным. Добавляют к смазке присадки, улучшающие ее свойства.
Графит расслаивается чешуйками, которые легко скользят друг по другу. Он, кроме того, мягок и не вредит металлу. Попадая между трущимися поверхностями, чешуйки графита заполняют трещинки, сглаживают неровности, и износ уменьшается. Поэтому некоторые машины вместо масла стали смазывать графитом.
Бороться с износом помогают и новые способы обработки поверхностей, о которых мы говорили, когда речь шла о покоренном металле.
Сколько же врагов скоростных машин мы уже знаем?
Сопротивление воздуха, трение и износ, нарушение устойчивости работы, иногда тепло, которого выделяется слишком много. Все они по-новому, сильнее проявляют себя на больших скоростях. Борьба с ними – важнейшая задача современной техники.
И ее успешно решают советские инженеры.


ТЫСЯЧИ ОБОРОТОВ В МИНУТУ
С каждым годом быстрее вращаются валы машин, быстрее двигаются станки, быстрее летают самолеты. Кто же дает жизнь машинам, приводит их в движение?
Двигатели, или приводы, как их называют машиностроители. Без них мир машин был бы мертв. Не было бы и быстроходных машин без быстроходных двигателей.
Тысячи оборотов в минуту стали привычной меркой в технике сегодня. Со скоростью 10 тысяч оборотов в минуту вращается вал токарного станка-автомата. 20–30 тысяч оборотов делают современные прядильные веретена. Число оборотов авиационной газовой турбины, установленной на скоростном реактивном самолете, достигает 15 тысяч в минуту.
В небольших сверлильных станках число оборотов доходит до 20 тысяч. Турбина турбодетандера – аппарата для сжижения воздуха – вращается со скоростью 40 тысяч оборотов в минуту. Шпиндели фрезерных деревообрабатывающих станков и гироскопы в приборах делают до 60 тысяч оборотов в минуту.
Есть сверхскоростные приводы, у которых числа оборотов могут доходить до 120–150 тысяч в минуту. Они вращают шлифовальные шпиндели и ультрацентрифуги.
История создания двигателей больших скоростей – яркий пример той борьбы с трудностями, которую ведет современная скоростная техника.
Все, о чем мы говорили, рассказывая о задачах, возникающих перед творцами высокоскоростных машин, находит здесь свое применение.
Оглянемся в прошлое, познакомимся с биографией теплового двигателя.
«Огонь слугою машинам склонить», – мечтал великий русский техник Иван Ползунов, – чтобы «облегчить труд по нас грядущим».
Паровая машина, созданная Ползуновым, была первым двигателем, заставившим тепло работать на фабриках и заводах. Началось владычество «его величества пара». Паровая машина освободила фабрики от власти рек, от господства водяного колеса.
Но шло время. Наступал век электричества. Бурно растущей промышленности требовался новый мощный двигатель, быстроходный привод для генератора электрического тока. Появилась паровая турбина. Она и стала таким приводом, открыв электричеству широкую дорогу.
Осталось все, что связано с получением пара, – топка, котел и вспомогательные механизмы. Но у турбины нет цилиндра с поршнем, как в паровой машине. Пар вращает турбинное колесо.
Отпала надобность в громоздких стальных руках – шатунах с кривошипами, которые превращали движение поршня во вращение вала машины. Сразу, без этих посредников, получалось вращение. Слово «турбина» и происходит от слова «турбо», что значит «вихрь».
Быстроходнее стал паровой двигатель. Турбина, работающая непрерывно, без толчков, без вынужденных остановок поршня на его пути в цилиндре, смогла развивать большую мощность, лучше использовать тепло. На крупных кораблях, электростанциях, там, где нужны десятки тысяч лошадиных сил, появились паровые турбины.
Сейчас свыше четырех пятых всей электроэнергии в нашей стране дают станции, на которых работают паровые турбины.
На наших заводах строятся паровые турбины мощностью 100 тысяч киловатт.
Давление пара в котле доходит до 90 атмосфер. Нужно было научиться сваривать стальные листы толщиной в 10 сантиметров, чтобы изготовить детали мощной турбины высокого давления. Из таких листов сваривали детали весом около полусотни тонн.
Турбина делает 3 тысячи оборотов в минуту. Концы лопаток ее двигаются по окружности быстрее звука. Такой скорости – 420 метров в секунду – еще не было ни в одной из строившихся когда-либо ранее паровых турбин.
При постройке этой турбины были использованы новейшие достижения в обработке металла.
Штамповка, которая позволяет экономить металл; скоростное резание, которое дает чистую поверхность; электрические способы обработки; упрочение поверхности деталей – все это применяли технологи.
Все способы испытания металлов использовали они, чтобы построить надежную машину.
Вот лишь несколько интересных цифр. 43 тысячи деталей есть в турбине. Больше 8 тысяч инструментов – режущих и мерительных – потребовалось, чтобы их изготовить. 5 200 разных технологических процессов разработали технологи, чтобы построить турбину.
Конструкторы, технологи, рабочие успешно оправились с задачей создания быстроходной мощной паровой турбины.
Товарищ Сталин поздравил советских турбостроителей с выдающимся достижением и пожелал им дальнейших успехов «в деле обеспечения технического прогресса в советском энергомашиностроении».
На Ленинградском металлическом заводе имени И. В. Сталина изготовлена уникальная турбина сверхвысокого давления мощностью в 150 тысяч киловатт. «Турбиной мира» назвали ее строители.
«Турбина такой мощности создаётся впервые в мире, что свидетельствует о зрелости советской науки и техники», – сказал Л. П. Берия в докладе о 34-й годовщине Великой Октябрьской социалистической революции.
Почти одновременно с паровой турбиной родился другой тепловой двигатель.
В паровой турбине нет стальных рук – шатунов, в ней непосредственно получается вращение.
Но есть ведь еще и другой посредник – сам пар, есть топка и котел.
Уже давно задумывались инженеры над тем, как бы от него избавиться. Однако идти здесь пришлось не прямым, а обходным путем.
Топку поместили внутри двигателя, в его цилиндре. В цилиндр подавали топливо и воздух. Получалась горючая смесь, ее зажигали, и газы, расширяясь, с силой двигали поршень. Так появились двигатели внутреннего сгорания – легкие и достаточно мощные. А с ними появились самолеты и автомобили, тепловозы и теплоходы, тракторы и многие другие машины. Огромная армия этих двигателей работает в каждой стране.
Мысль инженеров шла дальше. Перед ними было два двигателя – паровая турбина и двигатель внутреннего сгорания. Один из них имел шатуны и кривошипы, другой – паровой котел с топкой.
Инженеры стремились создать двигатель, который не имел бы недостатков старых, а обладал их достоинствами.
У нового двигателя, как у турбины, не должно быть цилиндров и шатунов.
У него, как у двигателя внутреннего сгорания, не должно быть котельной, и пар ему не нужен.
Выходит, новый двигатель должен быть турбиной внутреннего сгорания, или, иначе, газовой турбиной[1]1
В разделе о газовой турбине использованы отдельные материалы книги Б. Ляпунова «Газовая турбина» (Госэнергоиздат, 1951).
[Закрыть].
Первая в мире газовая турбина была построена в 1897 году русским инженером П. Д. Кузьминским. Но прежде чем новый двигатель вышел из стен лабораторий и начал применяться в технике, прошло около 40 лет.

Авиационный газотурбинный двигатель.
Вряд ли есть машина, которой различные исследователи, специалисты и не специалисты, занимались бы больше, чем газовой турбиной.
Принцип действия ее несложен, но построить газовую турбину так, чтобы она хорошо работала, оказалось совсем не просто.
В газотурбинной установке три основные части: компрессор, камера сгорания и турбинное колесо.
Компрессор питает камеру сгорания воздухом.
Камера сгорания питает турбину горячими газами, которые вращают турбинное колесо.
Турбина вращает какой-либо механизм (например, генератор электрического тока или воздушный винт самолета), а заодно с ним и компрессор, сидящий на том же валу.
В газотурбинных реактивных двигателях газы, отработавшие в турбине, вытекают в атмосферу, создавая реактивную тягу, которая двигает самолет.
Развитие авиации настоятельно требовало нового двигателя для больших скоростей полета. Таким двигателем могла стать газовая турбина – мощная, быстроходная, легкая. Авиация и явилась первой областью техники, где начали широко применять газовые турбины.
Впервые они появились на самолете уже давно, но как вспомогательные двигатели.
Еще в конце первой мировой войны в военной авиации испытывались турбокомпрессоры, подающие воздух в авиационный двигатель.
Плотность воздуха с подъемом на высоту уменьшается. Поэтому в двигатель попадает все меньше кислорода, нужного для сгорания топлива. Двигатель «задыхается».
На помощь ему приходит турбокомпрессор. Он подает в двигатель столько воздуха, сколько необходимо для нормального сгорания.
Турбокомпрессор – это небольшая турбина, работающая на выхлопных газах авиадвигателя, с компрессором, сжимающим воздух.
На пути создания надежно работающих турбокомпрессоров стояли большие трудности. Выхлопные газы, вытекающие со сверхзвуковой скоростью, бывают нагреты до температуры около 1000°. Турбина турбокомпрессора делает до 30 тысяч оборотов в минуту, и на лопатку ее действует огромная центробежная нагрузка. Она в десятки тысяч раз превышает вес лопатки.
Нужны поэтому особо прочные материалы и, кроме того, охлаждение лопаток и колеса турбины.
Советские инженеры преодолели эти трудности и создали ряд конструкций турбокомпрессоров, вполне оправдавших себя в работе.
Теперь высотные моторы завоевали право гражданства в авиации. Наддув воздуха стал необходимым для работы таких авиационных двигателей.
Во время второй мировой войны газовая турбина применялась на самолете уже не как помощник поршневого мотора, а как основной двигатель.
Этот двигатель, мощный, быстроходный, легкий, компактный, быстро завоевал себе прочное место в авиации. Он помог авиации шагнуть далеко вперед, подойти вплотную к звуковому барьеру. Газовая турбина открыла новую эру в истории авиации – эру больших скоростей.
И ежегодно в День Воздушного Флота любуемся мы стремительным полетом реактивных самолетов, догоняющих звук.
Газовая турбина появилась на самолетах, появляется на судах и тепловозах, она начинает проникать на фабрики энергии – электростанции.
Не надо, конечно, думать, что рождение нового двигателя – газовой турбины – означает конец всех других «старых» двигателей. Каждому из них – свое место. Мы строим и паровые турбины, и поршневые двигатели внутреннего сгорания, и газовые турбины – и все они служат нам.
Газовую турбину считают двигателем будущего, но из будущего она уже перешла в настоящее, и на ее примере я хочу рассказать о сложном и трудном пути создания быстроходного двигателя. Здесь особенно отчетливо видно, как трудна борьба за новую машину.
Займемся сначала турбокомпрессорной частью нашей газотурбинной установки – турбинным колесом и компрессором. Она состоит из похожих по устройству, но работающих по-разному частей.
Это диски с лопатками. Лопатки компрессора имеют такую форму, что воздух, двигаясь вдоль оси компрессора и обтекая их, сжимается.
Есть и «центробежные» компрессоры, где воздух сжимается центробежной силой: лопатки отбрасывают его от центра диска к краям.
Компрессору приходится иметь дело с чистым воздухом, а турбине – с продуктами сгорания топлива, разбавленными воздухом. Поэтому для турбины нужны самые прочные, самые жаростойкие марки стали. Для компрессора же достаточно алюминиевого сплава или обычной стали, способных, однако, выдержать значительные центробежные нагрузки.

Авиационный турбокомпрессор.
С большими трудностями пришлось столкнуться создателям газотурбинного двигателя. Работы хватило всем: и металлургам, и конструкторам, и технологам.
Очень сложную форму, напоминающую раковину улитки, имеет лопатка центробежного компрессора. Это наивыгоднейшая форма, и отклониться от нее – значит, ухудшить работу компрессора.
А как сделать такую лопатку?
Каждую лопасть изгибали вручную молотком на болванке соответствующей формы. Сразу сделать лопатку так не удавалось. Приходилось изгибать ее три-четыре раза, а после каждого изгиба металл отжигать – нагревать, чтобы он сохранил необходимые механические качества.
Нетрудно себе представить, насколько это было сложно и длительно. Самый совершенный двигатель – и самый несовершенный способ его производства. «ЗИМ», изготовляемый в кустарной мастерской!
Руки рабочего заменил пресс, а чтобы не приходилось вытаскивать и отжигать детали, некоторые станки, обрабатывающие лопатки, приспособили для работы при высоких температурах.
Лопатки должны быть изготовлены нужной формы весьма точно. По весу и форме они могут отличаться одна от другой лишь на очень малую, строго определенную величину.
Когда ротор готов, проводят специальные испытания для того, чтобы проверить, как точно он сделан.
Сначала добиваются того, чтобы центр тяжести ротора совпадал с его осью. Если такого совпадения нет, то на диске укрепляют добавочный груз – «противовес» или снимают лишний металл. Иногда бывает достаточно снять или добавить всего несколько граммов металла, и ротор паровой турбины весом в несколько тонн уравновесится.
Но этого еще не достаточно. Неподвижный ротор уравновешен. Однако, вращаясь, он может начать колебаться. Этого допустить нельзя. Колебания в машине, там где их быть не должно, – зародыш аварии. И на специальной балансировочной машине уравновешивают ротор, добиваясь плавного его вращения.
Попробуйте слегка толкнуть отбалансированный ротор, установленный на опорах. Он сделает несколько десятков оборотов. Это говорит о точности его изготовления и сборки.
В роторе компрессора не должно быть ни малейших дефектов.
Компрессор выполняет очень важную задачу – обеспечивает двигатель воздухом. А газотурбинному двигателю нужно большое количество воздуха. Если поршневому мотору требуется на килограмм топлива 15 килограммов воздуха, то авиационной газовой турбине – в 4 раза больше!
Однако если бы весь подаваемый компрессором воздух использовать для сгорания топлива, двигатель не стал бы работать.
Дело в том, что при горении топлива в камере сгорания выделяется очень много тепла. Чем его больше, тем выше получится температура. Она может доходить почти до 1800°.
Из каких бы сверхтугоплавких материалов не была сделана турбина – она не выдержит такой высокой температуры.
Самые стойкие материалы пока что переносят температуру не выше 900°, и то в таких турбинах, которые рассчитаны на непродолжительный срок службы. Лопатка же современной газовой турбины, не предназначенной для службы в авиации, выдерживает температуру не больше 650°.
Поэтому нужно снизить температуру горячих газов.
Теперь вы, наверное, догадываетесь, почему нельзя весь воздух из компрессора использовать для сгорания. Воздух нужен и для того, чтобы разбавить им горячие газы, снизить их температуру до безопасной для турбины.
И потому поток воздуха из компрессора разделяется в камере сгорания на две ветви: одна, меньшая, идет для сгорания топлива, другая – для снижения температуры газов.
Начиная от входа воздуха в двигатель и далее по воздушно-газовому тракту, температура возрастает. Чистый воздух засасывается компрессором и, сжимаясь, разогревается. Но это не сравнить с тем, что происходит в камере сгорания. Тут уже не обойдешься алюминиевыми сплавами! Камера сгорания делается из жаропрочной стали и обязательно охлаждается воздухом снаружи и внутри.
Кстати, нужно заметить, что чаще всего в газотурбинном двигателе бывает не одна камера сгорания, а несколько – иногда даже полтора десятка. Они «опоясывают» двигатель.
Вместо многих отдельных камер сгорания в авиационных газотурбинных двигателях иногда применяют одну – кольцевую.
Каждая камера – двойная цилиндрическая труба, отдаленно напоминающая самовар. Внутренняя труба называется пламенной. Внутри нее сгорает топливо, а воздух попадает через ряд каналов или кольцевых щелей. В днище установлены форсунки, впрыскивающие топливо.
Воздуха в пламенную трубу подается больше, чем нужно для сгорания. Этот «избыточный» воздух охлаждает внутренность трубы.
Охлаждается труба и снаружи. Ведь она помещается внутри другой трубы, называемой воздушной камерой. Из кольцевого пространства между обеими трубами воздух и направляется в пламенную трубу, которая оказывается, таким образом, в воздушной «рубашке». У стенок температура не превышает поэтому примерно 800°.
Не только от высокой температуры приходится защищать металл.
Горячие газы и кислород, которого немало в избыточном воздухе, могут разрушить нагретые стенки камеры. Для изготовления пламенных труб идет специальная жароупорная, химически стойкая сталь.
Нельзя забывать и того, что при нагревании металл расширяется. Если камеру сгорания закрепить с двух концов, то поломка неизбежна. Поэтому ее закрепляют только одним концом, а другой имеет возможность скользит, удлиняться.
Воздух в камере тщательно перемешивается с горючим. Раскаленные газы встречают струю впрыскиваемого топлива и зажигают его. Однажды зажженное, топливо будет само продолжать гореть.
Продукты сгорания, выходящие из пламенной трубы, смешиваются с потоком воздуха из воздушной камеры, и температура их понижается.
Для нормальной работы камеры необходимо распылить топливо форсунками, зажечь струю топлива, обеспечить устойчивое горение, равномерную подачу воздуха и топлива и перемешивание воздуха о газами.
Чтобы создать удовлетворительно работающую конструкцию камеры сгорания, пришлось производить многочисленные и сложные исследования.
Вот, например, как изучали распыливание топлива. Жидкую частицу трудно измерить. Поэтому через распылительную форсунку вместо топлива разбрызгивали расплавленный парафин и затем собирали быстро затвердевшие мельчайшие его капельки. Просеиванием разбивали частички на группы разных размеров. Надо было определить размеры нескольких тысяч частиц, чтобы решить, как лучше подавать топливо в двигатель и как лучше распылять ею.
При испытаниях камеры сгорания инженеры встретились с непонятными, на первый взгляд, явлениями. Сварной шов на камере после непродолжительной работы двигателя разрывался, как будто стенка была сделана не из прочной стали, а из жести.