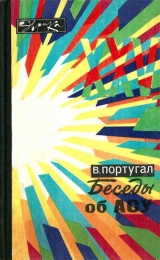
Текст книги "Беседы об АСУ"
Автор книги: Виктор Португал
Жанр:
Технические науки
сообщить о нарушении
Текущая страница: 9 (всего у книги 13 страниц)
Массовое производство – это идеал организации, управления и экономичности, это мечта каждого, кто занят в управлении производством. К сожалению, идеалов очень мало и не на всех хватает. Кроме того, не все изделия промышленности нужны народному хозяйству в количестве 660 тысяч штук в год. Так, средних токарных станков достаточно примерно 12 тысяч штук в год. В этом случае создавать главный сборочный конвейер с ритмом выпуска в 20 минут (такой ритм обеспечивает выпуск 12 тысяч станков в год, 50 штук в день), в общем, нецелесообразно. 50 станков в день можно собрать и непосредственно в сборочном цехе, не затрачивая средства на установку конвейера с дорогостоящим оборудованием. Делается это так.
Бригада сборщиков начинает монтировать несколько станков сразу и доводит монтаж до конца. Естественно, что для этого нужны детали и узлы станков. Механические цехи и цехи узловой сборки должны поставлять в день 50 комплектов этих деталей. Изготовление их тоже ведется не так, как в массовом производстве: здесь одной операцией рабочего не загрузишь, 12 тысяч деталей он может обработать меньше чем за месяц, а что ему делать в оставшиеся месяцы? Переходить к другой операции? В этом случае теряется преимущество узкой специализации рабочего – он должен учиться делать эти другие операции, которых может быть десяток, иногда несколько десятков.
Можно организовать работу, конечно, и так: рабочий обработал сначала 12 тысяч одних деталей, потом 12 тысяч других и т. д. Абсурд такой организации очевиден. Последняя деталь при таком управлении появится лишь в конце года, и все ранее изготовленные изделия должны лежать и ждать эту деталь. А ведь на сборку каждый день должно прибывать 50 комплектов!
Вот почему изготовление 12 тысяч деталей расчленяется на куски – партии. Каждый рабочий в течения какого-то времени обрабатывает сначала партию одних деталей, потом других, третьих и т. д. Потом цикл начинается снова. Все детали сдаются на склад, который и выдает на сборку по 50 комплектов в день и следит за комплектностью своих запасов.
Выпуск станков, как уже замечено, тоже осуществляется партиями. Их еще называют сериями, за что все производство получило название серийного.
Конечно, серийное производство менее эффективно, чем массовое. Во-первых, из-за оборудования: оно должно быть универсальным, то есть настраиваться и переналаживаться на десяток различных операций, а универсальное оборудование менее эффективно, чем узкоспециализированное, рассчитанное на массовое производство. Во-вторых, при переходе от одной операции к другой производительность труда рабочего падает: он ведь тоже «переналаживается». Можно добавить и «в-третьих» и «в-четвертых».
Но серийное производство тем не менее существует по объективным причинам и, несмотря на меньшую эффективность по сравнению с массовым, наверняка будет существовать и впредь.
Планирование в серийном производстве в основном сводится к двум элементам. Первый – это определение оптимальных размеров партий обрабатываемых деталей, собираемых узлов и станков. То, что эта задача непростая, видно из следующих соображений. С одной стороны, «чем больше, тем лучше»: увеличение размеров партии благоприятно сказывается на увеличении производительности труда (рабочие привыкают) и на сокращении времени переналадок. С другой стороны, «чем меньше, тем лучше»: большие партии деталей занимают много места для хранения, что увеличивает затраты и «замораживает» много материала и труда – все это лежит без пользы. Вот и приходится выбирать некоторое среднее решение – оптимальный размер партии.
Второй элемент – это определение запасов, или, как говорят производственники, заделов. Устанавливаются эти запасы так. Из цехов на склад постоянно поступают партии деталей и узлов. Склад каждый день должен выдавать на сборку определенное количество (в нашем примере 50) их комплектов. Цель планирования и заключается в том, чтобы точно намечать, когда именно на склад должны поступать детали и узлы, чтобы не происходили перебои в выдаче их на сборку. Зная длительность циклов изготовления изделий, можно рассчитать даты выдачи комплектов на сборку, вернее, определять самые поздние даты выдачи, после которых наступает аварийная ситуация. Сдвигая эти даты на более ранние или более поздние сроки, определяют тем самым величину необходимых запасов и заодно решают задачи по оптимизации загрузки ресурсов цеха.
Таково серийное производство.
Но есть в семье типов производства и совсем «урод» – это индивидуальное производство. Ярким примером его может служить опытное производство какого-нибудь крупного научно-исследовательского института или конструкторского бюро, которое по заказу промышленности разрабатывает и доводит до опытных образцов несколько сот различных изделий в год. К этому же типу относятся и такие предприятия, как судостроительные заводы, хотя продукция их совсем иная. Горьковский завод «Красное Сормово», например, изготавливает сухогрузные суда сериями примерно по десяти штук, и тем не менее каждое судно делается индивидуально и запускается в производство раз в полгода. В этих условиях сразу изготовить одинаковые детали на все суда невозможно, так как к последнему судну хранить их придется чуть не пятилетку.
Каковы же характерные черты у индивидуального производства?
Во-первых, оборудование на нем самое универсальное, на котором можно выполнять разнообразные операции. Во-вторых, рабочие также универсалы и, как правило, высокой квалификации, способные достаточно качественно выполнять все мыслимые операции. В-третьих, все работы практически уникальны и, следовательно, очень трудоемки, так как исполнителю приходится, кроме самой операции, подолгу налаживать оборудование.
Можно назвать еще ряд черт, которые также показывают, что индивидуальное производство крайне неэффективно. Но и обойтись без него тоже нельзя: наладить массовое производство не прошедших испытания изделий нельзя, а потребность народного хозяйства в некоторых из них крайне остра. Поэтому и такой «неэкономичный» тип производства завоевал право на существование. Более того, в настоящее время две трети предприятий машиностроения имеют индивидуальное и мелкосерийное производство, причем количество таких предприятий все время увеличивается. Объясняется это тем, что сейчас, в эпоху научно-технической революции, число новых типов установок, машин, приборов и аппаратов, новых изделий все время растет, и растет быстрее, чем растет число предприятий, предназначенных для их изготовления.
Единственное средство увеличения эффективности индивидуального производства – это некоторое искусственное повышение серийности. Достигается оно объединением одинаковых или даже только похожих деталей из разных изделий в более или менее крупные партии. И если такое объединение возможно, то к нему прибегают; прибегают, даже если это связано с увеличением запасов.
Какое же отношение типы производства имеют к многообразию моделей планирования? Ведь три типа производства, помноженные на два вида длительности производственного цикла, дают всего шесть возможных вариантов организации системы планирования на предприятии.
Увы! Названы лишь три числа объемов, которые ярко выражают типы производства: 660 тысяч – массовое, 12 тысяч – серийное, одно изделие – индивидуальное. Но какая пропасть лежит лишь между единицей и 12 тысячами! Если выпускается изделие в количестве 500 штук в год, то как назвать такое производство? Индивидуальное оно или серийное? А если 1000 штук? Конечно, люди придумали им разные названия: мелкосерийное производство, среднесерийное, крупносерийное. Но дело ведь не в словах! Дело в том, что вслед за определением объемов выпуска изделий наука об организации производства немедленно выдает такую «смесь» методов организации, что ни индивидуального, ни серийного производства в ней не узнаешь. А каждый тип организации производства требует своей методики планирования, так что появляются и совершенно неповторимые системы планирования, полностью индивидуализирующие процессы управления предприятием! Вот чем вызвано к жизни «системотворчество».
И последний удар по классификациям и систематизациям наносит тот факт, что чистых типов производства вообще в природе не бывает – на любом предприятии присутствуют практически все типы производства: от крупносерийного, иногда массового до индивидуального. Станкостроительный завод «Красный пролетарий», например, кроме крупносерийного производства среднего токарного станка, изготавливает еще около 4 тысяч шестишпиндельных полуавтоматов в год и более сотни наименований специальных токарных станков – от одного до нескольких десятков штук каждого наименования. Каким термином характеризовать его производство? Какие методы применять при построении системы планирования?
Конечно, методы есть. Но они опять сводятся к «индивидуализации» системы планирования. И так практически на всех предприятиях. По-видимому, это неизбежно.
Зависимость системы планирования от типа производства позволяет понять причину отсутствия успеха и в типизации проектов АСУ. Какая уж тут типизация, если каждое предприятие представляет собой уникальный «коктейль» типов производства.
Есть, правда, робкая надежда, что все это пережитки прошлого, и, как всякие пережитки, сойдут со сцены, и новые предприятия будут создаваться с «чистым» типом производства. Однако действительность рассеивает эти мечты. Волжский автомобильный завод – новейшее предприятие, на котором, по определению, должно быть только массовое производство, – тоже изготавливает серии запасных частей и еще всякую всячину почти по всему спектру типов производства.
– Тип производства, по-видимому, оказывает влияние не только на межцеховое планирование?
– Естественно. И формирование производственной программы, и межцеховое планирование, и в особенности внутрицеховое должны соответствовать типу производства.
– А почему «в особенности», как вы сказали, для внутрицехового планирования?
– По ряду причин.
Наиболее сильное влияние на внутрицеховое планирование тип производства оказывает, во-первых, потому, что именно в цехе проявляются особенности организации, так как здесь расположены поточные линии, станки и прочие рабочие места, так как здесь осуществляется обработка и движение заготовок, деталей, узлов, то есть всего, что носит общее название предметов труда. Во-вторых, если на предприятии, как правило, сосуществуют различные типы производства, то цехи стараются специализировать не только по типу производства, но даже по отдельным изделиям производственной программы, если это возможно. На том же станкостроительном заводе «Красный пролетарий» есть механические и сборочные цехи для крупносерийного и такие же цехи для мелкосерийного производства, то есть эти два типа производства практически обособлены. Таким образом, если межцеховое планирование ориентируется на некоторую индивидуальную для данного предприятия смесь типов производства, то внутрицеховое планирование разрабатывается для более или менее чистого типа. Возможны, правда, смеси типов производства и внутри цеха, но это встречается реже.

В-третьих, цех представляет собой самостоятельную хозяйственную единицу и имеет право сам формировать систему планирования, что дает определенный простор для учета специфики производства.
Можно перечислить еще ряд немаловажных причин, но и так ясно: организация внутрицехового планирования в очень большой степени зависит от типа производства.
Целью внутрицехового планирования является доведение плана до каждого рабочего места, то есть дальнейшая конкретизация производственной программы предприятия. Практически этот этап планирования состоит в переходе от планового задания цеху на месяц, которое было сформировано в процессе межцехового планирования, к плановому заданию для каждого рабочего на каждую смену. Если в качестве объектов межцехового планирования рассматривались детали и партии деталей, то во внутрицеховом планировании объектом является операция – работа, которую один рабочий выполняет, однажды наладив свой станок, подготовив свое рабочее место.
При массовом производстве в том или ином цехе изготавливается обычно один или несколько типов деталей, требующих для своего создания очень небольшого количества операций. В силу этого имеется возможность за каждым рабочим закрепить лишь одну операцию. Планирование в таком цехе будет в основном заключаться в определении количества операций и количества готовых деталей и узлов, которые надо произвести за смену. Дело это относительно простое, производственной информации приходится перерабатывать не так уж много, поэтому при создании автоматизированной системы управления на предприятии задачи автоматизации внутрицехового планирования для этого типа производства в число первоочередных вряд ли войдут.
То ли дело серийное производство. Здесь количество наименований деталей в цехе уже значительное – достигает сотен. Каждый рабочий выполняет от десятка до нескольких десятков операций. Объемы информации становятся значительными – здесь и данные о технологическом процессе, и о нормативах времени выполнения операций, и нормы расхода материалов, и сведения о наличии материалов, заготовок, инструмента и прочего материального обеспечения производства.
При составлении плана такого цеха необходимо каждому рабочему указать, какую конкретную работу и в какую смену он должен делать в процессе производства детали, как эта деталь проходит по технологической линии, состоящей из десятка станков. Планирование в этом случае представляет собой довольно сложную задачу, к тому же больших размеров, и решить ее можно только на ЭВМ, что дает значительный эффект за счет оптимизации плана и за счет увеличения оперативности планирования.
После всего сказанного создается впечатление, что в индивидуальном и мелкосерийном производстве без автоматизации внутрицехового планирования вообще не обойтись. В самом деле, огромная номенклатура изготавливаемых деталей подавляет, и человек не может даже охватить взглядом всю производственную информацию. В цехе, скажем, судостроительного завода за месяц изготавливается до 80 тысяч разных деталей, и определить, какой рабочий какую деталь и когда будет делать, можно разве что по простым правилам типа – «загружай свободного рабочего любой работой». Надежда только на ЭВМ; кажется, именно она со своими огромными вычислительными возможностями способна, во-первых, хранить все эти гигантские объемы информации; во-вторых, составлять календарные планы выполнения каждой операции на каждом рабочем месте. А он, кажется, так необходим, поскольку здесь, в индивидуальном производстве, номенклатура из месяца в месяц меняется, и, чтобы выполнить в такой быстро меняющейся обстановке производственную программу, этот огромный календарный план надо составлять на каждый месяц.
Все это так, и тем не менее самая ожесточенная дискуссия по вопросу применения ЭВМ во внутрицеховом планировании завязалась именно в связи с индивидуальным производством.
Возражения противников автоматизации здесь довольно весомы. Во-первых, индивидуальное производство очень неустойчиво и изобилует срывами, говорят они, в нем много разных деталей, много различных заготовок и материалов, много различного инструмента, – это создает условия для бесчисленных мелких нарушений, вроде отсутствия нужного инструмента, недостаток материала, срыв сроков подачи заготовок; к этому добавляются нарушения, общие для всех типов производства, – отсутствие рабочих на работе по уважительным причинам, поломки станков и прочее. Так что отличный, тщательно составленный на ЭВМ календарный план – эта огромная бумажная простыня в несколько метров длиной – сразу же начинает срываться. В первый день из него выполняется только 80–90 процентов запланированных операций, во второй – 60–70; в третий – 50 процентов, а дальше на него и просто не обращают внимания, так как он уже никакого смысла не имеет. А бессмысленный план – это хуже, чем вообще отсутствие плана, ибо такой вдобавок еще дискредитирует идею автоматизации планирования, дескать, машина – дура, черт знает что напланировала, а ты тут ломайся, выкручивайся! Так что огромная работа по составлению календарного плана проводится впустую.
Во-вторых, этот план и составить не так просто. Чтобы учесть в пооперационном календарном плане такой большой объем данных, надо затратить очень много времени (даже на ЭВМ!). Заниматься же им надо сравнительно часто – не реже одного раза в месяц. В-третьих, при составлении такого календарного плана приходится сталкиваться с нехваткой необходимой информации и отсутствием точных норм длительности выполнения каждой операции. Если в массовом и серийном производстве время точно отнормировано, то в индивидуальном производстве установление его часто осуществляется по аналогии, по типичности работ на группу однородных деталей. Фактически же эта «однородность» чисто условная, и нормы весьма приблизительно отражают реальные затраты времени на производство операции.
Немаловажным является вопрос: как ЭВМ распределит работы между исполнителями? Оборудование в цехе сведено, как правило, в однородные группы: токарные станки, фрезерные, сверлильные и т. д. И если деталь необходимо обрабатывать на токарном станке, то в принципе ее можно обрабатывать на любом станке токарной группы. Но это только в принципе. Реально же приходится принимать во внимание габариты станка, степень его изношенности, влияющую на точность изготовления, квалификацию рабочего, наконец, личные качества рабочего, которые определяют его индивидуальную производительность при выполнении конкретной работы. И чтобы ЭВМ могла эффективно распределить работы, надо всю эту информацию «выучить» у мастеров и ввести в нее. А это очень трудоемко.
Примерно так противники автоматизации внутрицехового планирования аргументируют свою позицию и делают вывод, что пока его следует оставить в ведении людей, специально подготовленного персонала.
Но и сторонники автоматизации имеют в запасе довольно сильную аргументацию.
Основной их козырь – это «человеческие факторы» в управлении (уже появился и такой термин!). Номенклатура индивидуального производства настолько велика, что ни один мастер не может спланировать выполнение всей производственной программы целиком. Он «видит» ее только по частям и, естественно, принимает лишь некоторые локальные решения и, следовательно не может предвидеть всех их последствий, и говорить о какой-нибудь «рациональности» его решений, тем более об оптимальности, бессмысленно. ЭВМ же с составлением такого плана справится без труда.
Что касается распределения заданий по рабочим согласно их способностям, то в этом деле возможности ЭВМ превышают возможности мастера и преимущество оказывается на стороне машины. Действительно, допустим, что мастеру, хорошо знающему производительность труда каждого рабочего, необходимо распределить работу так, чтобы суммарная производительность участка была максимальной. Для этого ему потребуется, как уже говорилось, решить задачу исследования операций – «задачу о назначениях»! А решить ее без ЭВМ он (да и не только он!) не в силах и в лучшем случае поступит по простому правилу: «загружай рабочего с наибольшей производительностью», которое никогда не приводило к оптимальному распределению. ЭВМ же и экономико-математические методы при наличии соответствующей информации помогут ему довольно легко (трудоемкость решения «задачи о назначениях» для машины невелика) найти оптимальное решение.
Наконец, сильным аргументом является и такой факт. Мастеру, как и любому человеку, присущ некоторый субъективизм. В условиях индивидуального производства и связанной с ним нечеткостью нормирования существующие нормы выработки оказываются различны по напряженности их выполнения. Это приводит к тому, что все работы как бы делятся на «выгодные» и «невыгодные». Распределяя их, мастер вольно или невольно поручает «выгодные» одним, а «невыгодные» другим и может неосознанно создать неблагоприятный нравственный климат на участке. Экономико-математические методы совершенно исключают такую неприятную ситуацию, так как при распределении работ ставят во главу угла такой объективный критерий, как максимизация суммарной производительности участка.
Что касается трудностей, связанных с недостатком внутрицеховой информации, то они преодолимы. Если информация существует, то она может быть зафиксирована и на машинных носителях – это доказал весь опыт автоматизации управления.
Серьезной является проблема устойчивости производства и связанная с ней проблема достоверности планирования и надежность планов. Но и здесь больше аргументов за автоматизацию планирования, чем против. Во-первых, нет никакой необходимости составлять план на месяц, если можно планировать работу и на более короткий промежуток времени, вплоть до смены (ЭВМ с ее громадной возможностью вычислять это позволяет). Во-вторых, производство – это объект, движущийся к цели – к выполнению производственной программы, а календарный план – это управляющее воздействие, которое направляет его по некоторому пути к этой цели. По теории управления такая система не может эффективно функционировать без обратной связи. Роль обратной связи на производстве играет учет выполнения плановых заданий. Если при составлении каждого последующего плана оперативно учитывать результаты выполнения предыдущего, то это существенно повысит его достоверность, и он станет действенным инструментом управления. Процесс составления последующих плановых заданий с использованием учетных данных в теории называется регулированием, а вся система с обратной связью – системой с оперативным управлением. Следовательно, и наша автоматизированная система внутрицехового планирования, чтобы быть эффективной, должна строиться как система оперативного управления.
– Так надо автоматизировать внутрицеховое планирование или нет?
– Если принять во внимание еще некоторые проблемы, которые приходится решать в цехе, то ответ окажется единственным – безусловно, надо.
При составлении внутрицехового плана важным являются связи его с системой материального стимулирования и, конечно же, фактическое распределение работ между рабочими. Кроме них, есть другие серьезные проблемы, о которых лишь вскользь сказано, например, такие, как структура системы внутрицехового планирования, составление сменного задания, и иные.
Предполагается, что внутрицеховое планирование осуществляется в несколько этапов, или, как говорят в асуповской науке, система состоит из нескольких задач. Первый этап решает задачу согласования плана цеха с месячной программой предприятия. Вызван он тем, что цех – это самостоятельная хозяйственная единица со своей целью, которая несколько отличается от цели предприятия. Сейчас, когда роль материального стимулирования понята и поднята до высокого смысла, размер материального поощрения можно считать главной целью цеха. Проще говоря, цех должен работать так, чтобы получить максимум вознаграждения, наибольшую премию.

Поскольку общезаводские органы формируют как производственную программу цеха, так и условия материального поощрения, то, казалось бы, они могли бы так задать цеху производственную программу, чтобы при ее выполнении он получил максимум премии. Однако это не совсем так. Не говоря о трудностях, связанных с правильным заданием условий стимулирования, а также неопределенностями, приводящими к неполной согласованности критериев цеха и завода, есть еще одна причина – цех значительно лучше, чем общезаводские планирующие органы, знает свои ресурсы, их текущие изменения, фактическое состояние, скрытые резервы и т. д. Поэтому, какой бы хорошей ни была бы спущенная сверху производственная программа цеха, ее трудоемкость будет все же отличаться от его производственных мощностей.
А если производственная программа составлена неправильно, то часть рабочих будет перегружена, а часть недогружена. Проблему же недогрузки приходится решать внутри цеха, так как на производстве существует аксиома: рабочий должен быть в достаточной степени обеспечен работой; если он выполнил норму, то обеспечь его работой сверх нормы. Ему нет дела до того, что у вас плохая система планирования. Рабочий хочет хорошо поработать и хорошо заработать. Долг управленческого персонала – обеспечить его работой, необходимой в данный момент предприятию.
А как исполнишь этот долг, если производственная программа цеху скомплектована неправильно? Тут и возникают всякие согласования, всевозможные корректировки и уточнения.
Как поступать в данном случае? Для этого рекомендуется комплектовать цеху производственную программу не жестко, а с некоторой свободой. Сделать это довольно просто.
В производственной программе всегда есть часть деталей, которые должны быть, безусловно, изготовлены, иначе сорвется выполнение производственной программы завода, – это так называемая обязательная номенклатура. Но есть детали, которые без особого ущерба можно изготовить и в следующий месяц. Вот ее-то, эту необязательную часть, и надо расширить. Тогда цех будет иметь возможность некоторого выбора и сможет более правильно строить свою программу. В этом случае может быть сформулирована оптимизационная задача цеха, которая неплохо описывается моделью «линейного программирования», а в качестве критерия может быть взята, например, равномерная загрузка рабочих по профессиям. Ограничениями при таком планировании являются номенклатура и объем. А их общезаводские службы планирования задают жестко.
Вторая задача в цепи планирования – это составление календарного плана, то есть составление пооперационного плана на месяц. Все высказанные ранее возражения о его бесполезности сводились к тому, что он негоден как руководство к действию. Наверное, это правильно. В системе же планирования ему отводится совсем иная функция. Действительно, то, что плановое задание согласовано со структурой производственных мощностей, еще не означает, что оно будет гладко и без препятствий выполняться. Сложный технологический порядок прохождения деталей может привести к неизбежным пролеживаниям деталей. Если учесть еще небольшие отклонения от сбалансированности, которые иногда допускаются, то может получиться задержка в выпуске важных для сборки деталей. И тем не менее именно в этой ситуации календарный план, являющийся моделью выполнения производственной программы, особенно остро необходим. Полученный на ЭВМ, он заранее указывает на все неувязки, которые могут возникнуть в процессе работы, на ЭВМ же можно заранее «проиграть» его и увидеть, как будет цех работать весь месяц и что произойдет в реальном производстве, он поможет руководству цехом заранее принять меры по расшивке узких мест: добавить, если надо, третью смену, передать работу более квалифицированному рабочему, увеличить приоритет детали. Короче, он поможет наметить наилучший путь выполнения производственной программы. И пусть известно, что из-за мелких нарушений этот путь не будет пройден в точности, но направление его будет правильным. В этом смысл календарного плана.
А для мастера в качестве руководства к действию он, конечно, не годится; не годится и из-за громоздкости и из-за неустойчивости. Руководство к действию создает третья и последняя задача в системе планирования – формирование сменного задания.
Уже говорилось, что календарный план неустойчив. При его составлении на месяц вперед практически невозможно учесть ежедневную обеспеченность производства заготовками, материалами, инструментом, приспособлениями. А другая аксиома производства гласит: нельзя задавать рабочему работу, не обеспеченную материальными ресурсами! Как же быть?
Обычно при формировании сменного задания из календарного плана выбираются те операции, которые на сегодня обеспечены, а необеспеченные откладываются, и вместо них берутся операции из плана следующего дня. В традиционной системе управления вся эта работа выполняется мастером. Следовательно, при передаче ее на ЭВМ фактически делается попытка автоматизировать работу мастера. С этой целью для машины должна быть создана программа, моделирующая работу по планированию квалифицированного работника управления. Но, кроме рутинной части, состоящей в принятии мер для обеспечения материальными ресурсами и по включению в сменное задание обеспеченных операций, эта работа содержит и плохо формализуемые элементы, требующие творческого подхода. Среди них наиболее сложными являются, во-первых, вопросы, связанные с выбором, что включать в сменное задание, если не все работы обеспечены ресурсами; во-вторых, как распределить однотипные работы между рабочими.
Первую проблему «автоматизации мастера» – формирование обеспеченного задания – удается решить более или менее успешно, анализируя календарный план. Поскольку он составлен на длительную перспективу, то из него в сменное задание можно включать операции из последующих дней с тем условием, что в дальнейшем, когда пропущенные операции будут достаточно обеспечены, их можно было бы включить в последующие сменные задания.
Вторая проблема – распределение работ между рабочими – сложнее, зато она вызвала к жизни несколько довольно интересных творческих решений. Суть ее, как уже говорилось, в том, что мастер имеет о производственной программе свое мнение, некоторую «свою» информацию, нигде не зафиксированную, информацию о том, какая работа «удобнее» для какого рабочего. Формально эту информацию можно охарактеризовать так: есть некоторое нормативное время выполнения работы, а есть фактическое время, которое рабочий затрачивает на ее выполнение. Отношение нормативного времени к фактическому называется коэффициентом выполнения норм. Естественно, что даже для одной работы этот коэффициент будет разниться от рабочего к рабочему.
Так вот, мастер знает эти коэффициенты, и первая задача автоматизации предполагает различные схемы «выуживания» у него этой информации. После того как она будет получена, можно решить «задачу о назначениях», улучшив попутно работу мастера за счет оптимизации загрузки участка.
Недостатком такого подхода является необходимость фиксации в памяти ЭВМ большого объема информации. Ведь количество индивидуальных коэффициентов равно произведению числа рабочих на количество работ! Если на участке 20 рабочих и требуется выполнить 500 операций, то необходимо получить и хранить 10 тысяч коэффициентов. Зато явные достоинства – оптимизация плюс объективность.