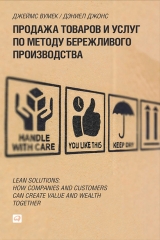
Текст книги "Продажа товаров и услуг по методу бережливого производства"
Автор книги: Джеймс Вумек
Соавторы: Дэниел Джонс
Жанры:
Экономика
,сообщить о нарушении
Текущая страница: 8 (всего у книги 20 страниц) [доступный отрывок для чтения: 8 страниц]
Как традиционная торговля решает проблему предоставления нужных вам товаров
Подсказываемый простым здравым смыслом способ повысить уровень обслуживания – разместить крупные запасы на всех уровнях сбытовой сети и соответствующей системы производства. Эти запасы начинаются с полок в дальней секции магазина (во многих магазинах-складах типа Home Depot и Costco запасы хранятся на высоких стеллажах, до которых покупатель не может дотянуться). Также они хранятся на распределительном складе розничной компании, на складе оптовика (особенно запасы продукции, не занимающей много места), на складе готовой продукции производителя в месте производства и (в виде компонентов) во многих точках на всем пути обратно к сырью и материалам{36}36
В последние годы многие розничные компании также попытались повысить уровень обслуживания, отобрав функцию размещения заказа у управляющих отдельных магазинов, создав региональные распределительные склады и организовав снабжение всех магазинов с этих складов, а не напрямую со складов поставщиков (возможно, самый яркий тому пример – Wal-Mart). Это позитивные изменения, но в сочетании с традиционными системами управления информацией и редкими поставками они вряд ли приведут к существенному повышению уровня обслуживания.
[Закрыть]. Чтобы поддерживать постоянный ассортимент товаров, магазин и все другие участники логистической цепочки стараются своевременно возобновлять заказы, для этого они используют сложные прогнозы будущего спроса. Задача экономить на погрузочно-разгрузочных работах и транспортировке вынуждает закупать большими партиями и нечасто.
На помощь здравому смыслу приходят информационные технологии и сканеры штрих-кода (на замену которым скоро придет радиочастотная идентификация, RFID). В результате каждый, кто связан с потоком предоставления товаров и услуг, может узнать, как идут продажи и где находятся все запасы. И все же эти методы еще не обеспечивают высокого уровня обслуживания, поскольку все равно каких-то товаров хронически не хватает, а каких-то оказывается в избытке.
Чтобы понять, почему так происходит, нам нужно составить карту текущего состояния обеспечения магазина товарами и проследить их путь через каждую «петлю закупок» назад, через производство, к сырью и материалам.
Первый шаг для директора продуктового магазина – примерно оценить объем продаж каждого товара (что легко сделать, имея данные кассовых аппаратов) и заказывать необходимое количество товара, возможно, раз в неделю, делая корректировки на известные периоды роста и падения продаж (например, в первый летний праздничный выходной продажи безалкогольных напитков наверняка возрастут).
Пока что все ясно.
Но затем начинаются проблемы. Продуктовый магазин получает нужные товары не напрямую с завода-поставщика, а с распределительного склада своей компании, обслуживающего несколько магазинов. А этот склад тоже получает товары не напрямую от производителя, а с распределительного склада оптовика. Запасы готовой продукции существуют по крайней мере в четырех пунктах: в продуктовом магазине, на распределительном складе сети магазинов, на распределительном складе оптовика и на складе готовой продукции завода-изготовителя.
Так кто же будет размещать заказ? Директор магазина на основании данных продаж и предположений о будущем спросе? Управляющий распределительного центра сети магазинов на основе дополнительных расчетов объемов потребления по группе магазинов? Или же специалист по закупкам головного офиса розничной компании, суммирующий заказы многих магазинов и нескольких распределительных центров?
Кто примет заказ на стороне поставщика? Его распределительный склад? Завод? Или головной офис поставщика, в котором специалисты по планированию пытаются составлять планы производства и отгрузок для всей компании?
А как насчет стимулирования спроса? Предположим, что менеджер по закупкам розничной компании получит прекрасную возможность заказать дополнительное количество данной продукции в связи с тем, что поставщик произвел ее слишком много. Или поставщик попытается улучшить свои показатели в конце финансового года и предложит скидку тем, кто приобретет больше товаров сейчас, а не потом. Кто будет решать, имеет ли эта сделка смысл, где должен храниться дополнительный запас и кто будет следить за его обновлением?
И в самом деле, много вопросов. Когда мы сводим все это воедино на рисунке, показывающем, что происходит в потоке предоставления товаров и услуг («Как системы обеспечения сами усиливают колебания спроса»), то всегда обнаруживаем одно и то же. Существует множество точек размещения заказов, нередко друг другу противоречащих. Заказы размещаются обычно нерегулярно. Поставки осуществляются редко и непредсказуемо и больше отвечают потребностям логистических компаний, чем потребителя. Существует множество стимулов к созданию запасов и других факторов, влияющих на цикл размещения и выполнения заказа. Все это означает, что подлинный спрос потребителя просто растворяется. И чем дальше от потребителя мы продвигаемся по этой логистической цепи, тем более призрачной становится связь между реальным спросом и информацией, которую имеет тот или иной участник об этом спросе.
На этой карте потока обеспечения мы можем видеть, что колебания спроса усиливаются, как показывают графики над каждым пунктом хранения. Они отражают динамику числа заказов, получаемых за период на тот или иной товар. Чем дальше от потребителя, тем больше колебания. Кажется, что спрос подобен цунами, которое распространяется все дальше и дальше от эпицентра – реального спроса потребителя. И это притом, что реальные нужды потребителей магазина практически не меняются. Нет никакого потребительского землетрясения, которое порождало бы эти волны. Почему же всех так лихорадит?
Что обращает на себя внимание, так это многочисленные системы управления заказами, рекомендующие закупки на каждом шагу. Тем не менее многим менеджерам приходится игнорировать эти рекомендации в попытке преодолеть отклонения, возникшие в той или иной точке потока обеспечения (их действия показаны на рисунке иконками с телефонами и прерывистыми линиями, обозначающими информационный поток). В результате мы имеем, пользуясь языком специалистов по теории информации, низкое отношение сигнала (т. е. ценной информации) к шуму (т. е. ошибочным данным). Это приводит к раздуванию потребности в запасах на протяжении всего потока обеспечения (нередко называемых запасами на всякий случай) и низкому уровню обслуживания конечного потребителя. Поразительно, но это происходит во всем мире!{37}37
Это описание покажется знакомым читателям, наслышанным о «Пивной игре» – командных упражнениях по управлению запасами, получившими известность благодаря книге Питера Сенге «Пятая дисциплина: Искусство и практика самообучающейся организации» (М.: Олимп-Бизнес, 2003.) В чем мы расходимся с Сенге, так это в нашем решении этой проблемы.
[Закрыть]

Как благодаря бережливому процессу обеспечения вы можете получить именно то, что вы хотите, и с более низкими затратами
Бережливое мышление решает эту проблему, переворачивая всю традиционную логику. Следует создать в потоке обеспечения единственное место, где определяется график закупок, значительно повысить частоту пополнения запасов в каждой точке, восполнять только то, что было куплено недавно (если не прогнозируется существенный рост спроса в будущем), а также – если это вообще возможно – «сжать» поток обеспечения и приблизить производство к месту продаж.
Делая это, сторонники бережливого мышления создают вытягивающие системы, благодаря которым сам потребитель сигнализирует, что и когда ему нужно. Когнитивная информационная управленческая система заменяется на рефлексивную. Допустим, вы дотронетесь до раскаленной плиты. Неужели ваш мозг интерпретирует сигналы, полученные в этот момент от ваших нервных окончаний, таким образом: «Это плита. Похоже, она включена. Мой палец лежит на горелке. Он начинает дымиться. Наверное, мне будет очень больно. Может быть, мне следует все же убрать свой палец?» Скорее всего, ваши рефлексы сами сделают то, что нужно, и чем горячее плита, тем быстрее вы отдернете палец, не прибегая при этом ни к каким консультациям с центральным процессором у вас в голове.
Очевидно, что вы так и поступите. И тем не менее адепты информационных систем потратили теперь уже почти век (начиная с эпохи перфокарт в двадцатые годы) на изобретение централизованных компьютерных систем обработки информации. Подобным образом работает и система закупок в нашем примере с продуктовым магазином. Но есть надежда оптимизировать весь процесс с помощью петель обратной связи, позволяющих получать точную информацию о текущих условиях, а также с использованием сложных алгоритмов, дающих центральному мозгу руководить всеми действиями на всех точках внутри системы.
Наш образец – компания Toyota славится на весь мир прекрасной организацией и надежностью своих производственных и логистических процессов. У нее самые информативные петли обратной связи при минимальном шуме. Тем не менее она давно пришла к выводу, что централизованные системы управления никогда не добиваются такой эффективности, на которую рассчитывают их архитекторы. Шум понемногу все равно накапливается, и система деградирует. И как только рассылаемые во все точки указания начинают расходиться с реальными потребностями, менеджеры начинают регулировать систему вручную в каждой точке, что приводит к быстрому снижению эффективности всей системы.
Можно попытаться перебороть эту тенденцию, собирая все больше и больше информации. Переход на радиочастотную идентификацию – шаг в этом направлении. Но мы советуем уменьшить зависимость от информации и упростить логику принятия решений. В идеале необходимо, чтобы информация поступала с предыдущего на следующий этап вверх по потоку, и все. На последующем этапе нужно просто пополнять запас, исчерпанный на предыдущем.
Чтобы это сработало, крайне важно повысить периодичность заказов, поступающих вверх по потоку, наряду с периодичностью поставок, идущих вниз{38}38
В идеале поток информации будет тесно переплетаться с потоком сырья и материалов. Toyota, например, использует сигналы канбан, посылаемые вверх по потоку той же петлей пополнения запасов, которая приносит затребованные материалы через ту же петлю пополнения запасов. За стенами завода Toyota и на расположенных неподалеку заводах ее поставщиков электронный канбан сменяют традиционные карточки канбан. Полное описание рефлексивной системы вытягивания Toyota см. в кн.: Art Smalley, Creating Level Pull: A Lean Production-System Improvement Guide for Production-Control, Operations, and Engineering Professionals, Brookline, MA: Lean Enterprise Institute, 2004.
[Закрыть]. Этому способствует внедрение бережливой логистики, которая делает возможным частое пополнение запасов товаров (а нередко и информации, если поставщики расположены неподалеку), а также сжатие потока обеспечения в пространстве и времени{39}39
Описанная в главе 4 «Бережливого производства» система распределения запчастей Toyota – по-прежнему самый полный пример. Примерно 60 % ее поставщиков запчастей изготавливают и отгружают ежедневно региональным распределительным центрам Toyota в Северной Америке то, что эти центры поставили автомобильным дилерам в предыдущий день (Бережливое производство, с. 377).
[Закрыть].
Почему другие поставщики пока этого не сделали? Главная причина в том, что компании на всех уровнях типичного потока обеспечения следят за затратами в каком-либо пункте (стоимостью товара, приобретенного у поставщика там, где он размещается) и общими затратами на закупки по конкретному подразделению, а не за общими затратами по каждому продукту. Например, отдел закупок обувной компании обращает внимание прежде всего на стоимость пары обуви и выбирает поставщика из Вьетнама. Отдел логистики интересуют затраты на доставку с фабрики на склад розничной компании в расчете на одну пару обуви, и он чаще всего выбирает вариант доставки морем, но крупными партиями. Отдел продаж создает специальный счет для «себестоимости реализованной продукции», руководствуясь существующим в отрасли практическом правилом, что затраты на поддержание остатков не должны превышать 10 % всех торговых издержек. И похоже, что иногда компании не имеют возможности учесть стоимость недопродаж и затраты, связанные со снижением лояльности покупателей из-за отсутствия нужных товаров на полках.
Между тем поставщики только выиграют, и более высокая себестоимость пары обуви будет скомпенсирована снижением затрат на хранение запасов и уменьшением потерь от нелояльности клиентов. Так они могли бы сократить свои затраты по всему потоку обеспечения для каждого товара и в то же время увеличить свои продажи и рыночную долю.
Как организовать быстрое пополнение запасов
Мы описываем вовсе не чисто гипотетические выгоды. Поразительный пример того, чего можно достичь, показала одна компания, за развитием которой мы наблюдали в течение нескольких лет. Возможно, вы помните, что в нашей предыдущей книге «Бережливое производство» мы рассказывали о замечательном кругосветном путешествии скромной банки колы от сырья до клиента продуктового магазина Tesco в Великобритании{40}40
Бережливое производство, глава 2, с. 61–72. В 1996 г., когда мы готовили этот пример, Tesco только что стала одним из спонсоров Исследовательского центра бережливых предприятий школы бизнеса Кардиффского университета с целью апробировать идеи бережливого мышления в пищевой промышленности. Сегодня, спустя девять лет после десятков пилотных проектов и проектов по внедрению системы, Tesco весьма близка к созданию непрерывного потока для производства напитков в банках и уже применила эти идеи ко многим товарам повседневного спроса в своих потоках обеспечения. Приводимый здесь пример основан на результатах многочисленных экспериментов с потоком создания ценности, проведенных совместно с Tesco Дэном Джонсом, а также исследователями из Кардиффа Ником Ричем и Дэвидом Симонсом. Подробное описание этих экспериментов см. в статье Daniel Jones and Philip Clarke, “Creating the Customer Driven Supply Chain”, ECR Journal, Vol. 2, № 2, Winter 2002.
[Закрыть]. Всего это путешествие заняло 319 дней.
Только на то, чтобы эта банка попала с завода по розливу на полку магазина, потребовалось 20 дней. При этом она хранилась в пяти различных точках, решения о размещении заказов принимались в шести точках, а коэффициент усиления колебаний спроса составил 4:1 (т. е. колебания спроса на заводе по розливу в четыре раза превысили колебания реального спроса покупателей в магазине). Уровень обслуживания составил 98,5 %, что было бы эквивалентно 55 %-ному выполнению заказа для корзины из 40 необходимых продуктов (обратите внимание, что этот показатель намного превысил средний уровень обслуживания в розничной торговле в то время).
Вскоре после того как мы подготовили этот пример в 1996 г., Tesco решила усилить свои позиции в торговле пищевой продукцией, обеспечив более высокий уровень обслуживания и снизив в то же время свои затраты. Грэхем Бут, бывший тогда директором по поставкам Tesco, обратился к Дэну Джонсу и его исследовательской группе Кардиффской школы бизнеса с вопросом, как Tesco может применить логистические методы компании Toyota, чтобы снизить свои затраты времени и сил. Как всегда, Дэн предложил совершить прогулку, чтобы изучить типичный поток обеспечения для колы. Он настойчиво рекомендовал Грэхему пригласить руководителей других служб (розничной торговли, закупок, финансовой и сбыта), а также руководителей производственных служб и директоров по цепочке поставок компании – поставщика колы Britvic.
Однажды холодным январским днем 1997 г. эта группа отправилась вверх по потоку обеспечения для колы от прилавка продуктового магазина через региональный распределительный центр РРЦ Tesco, распределительный центр Britvic, линии розлива колы и склад компании, поставлявшей Britvic пустые банки. По дороге Дэн и его команда из Кардиффа постоянно задавали простые вопросы: «Почему на полках нет товаров? Почему помощник продавца должен заново сортировать товар, вынимая его из решетчатых контейнеров на колесах, только что привезенных грузовиками из РРЦ? Почему нужно держать такие большие запасы в продуктовом магазине, в РРЦ Tesco и в РРЦ Britvic? Почему целые штабели банок ожидают заполнения возле здания завода по розливу?»
Эта прогулка открыла обеим компаниям глаза. Когда Tesco и Britvic изучили совместно нарисованную ими во время прогулки карту этого процесса, то смогли увидеть огромные потери на каждом шагу наряду с огромными возможностями экономии на расходах и одновременного повышения удовлетворенности конечного потребителя. Они также поняли, что экономии на расходах и более высокого уровня обслуживания можно добиться только на основе сотрудничества между двумя компаниями и между службами каждой компании.
Что нужно, чтобы предоставить потребителю то, что он хочет
Проанализировав ситуацию, Грэхем Бут осознал необходимость изменения практически всей существовавшей в Tesco практики доставки товаров от поставщика в магазины. В первую очередь нужно было сделать так, чтобы данные с мест продаж непосредственно влияли на решения об отгрузке, принимаемые в РРЦ Tesco. Тогда конечный потребитель у кассы стал бы своеобразной точкой переключения, задающей темп всему процессу, регулируя поток обеспечения и ликвидируя противоборствующие друг с другом системы планирования.
Затем Tesco повысила частоту поставок в магазины. После нескольких лет экспериментов грузовики Tesco стали доставлять колу из РРЦ во все магазины круглосуточно через каждые несколько часов в количестве, зависящем от того, сколько было продано за последние несколько часов. В результате сроки пополнения запасов уменьшились на один или даже несколько дней, и система начала реагировать на изменение реального спроса потребителей практически в режиме реального времени.
В РРЦ колу теперь получают в тележках на колесах напрямую с завода по розливу. Их выкатывают из грузовика, приехавшего от поставщика, и тут же вкатывают в грузовик, следующий в магазин. В магазине тележки подвозят непосредственно к месту продажи, где они заменяют обычные торговые стеллажи. Это новшество устранило несколько этапов перемещений, когда сотрудники перегружали колу из больших паллет сначала в контейнеры на колесах, в которых ее доставляли в магазин, а потом перекладывали в тележки на колесах и транспортировали ее до стеллажей, куда перекладывали в последний раз. Рисуя свои карты первоначального состояния потока предоставления колы, Tesco обнаружила, что половина ее затрат на управление этим потоком составляли затраты труда на заполнение полок.
Кроме того, новый метод доставки колы в той же тележке на колесах с пункта приема в РРЦ в пункт отгрузки устраняет предыдущие перемещения больших паллет с колой в высотные стеллажи на складе. После длительного ожидания на таком стеллаже колу опускали на уровень пола, где паллеты вскрывали и заполняли контейнеры для отправки в каждый магазин (устранение шагов, связанных с доставкой колы на склад, ее транспортировкой обратно из склада и загрузкой нужного количества для отправки в магазин тоже обеспечило большую экономию на затратах труда).
Для таких товаров повседневного спроса, как кола, РРЦ Tesco теперь, скорее, перевалочный пункт, чем склад, в здании которого товары разных поставщиков проводят всего несколько часов между поступлением и отправкой в магазины. Тем не менее по-прежнему на случай неожиданных всплесков спроса где-то рядом хранится буферный запас полных тележек. Но поскольку этот буферный запас часто пополняется, он невелик.
Между тем, если вернуться снова к поставщику колы, то здесь произошли еще более серьезные изменения. Britvic увеличила время активной работы и повысила гибкость своих линий по розливу и теперь может с очень высокой надежностью выпустить мелкими партиями то, что только что заказал потребитель. Это означает: на заводе Britvic по розливу практически нет готовой, ожидающей отправки продукции, но и эта может миновать распределительный склад Britvic (первоначально построенный для решения проблем неожиданного роста заказов вниз по потоку предоставления товаров и услуг и производства партиями вверх по потоку). Вместо этого кола упаковывается прямо на снабженных колесами тележках в конце линии розлива, ее можно вкатить прямо на грузовик Tesco, прокатить через РРЦ Tesco и доставить к месту продажи в магазине с меньшим количеством требуемых операций по хранению и повторной упаковке.
Последний логистический шаг – доставка тележек из РРЦ в магазины Tesco, объезжающим эти магазины по одному и тому же маршруту несколько раз в день грузовиком (так называемым «молоковозом»). В каждом магазине он забирает пустые тележки, а заезжая к поставщикам, возвращает их. На каждой остановке в него загружают полные тележки, и он затем возвращается в РРЦ Tesco, чтобы возобновить цикл. Может показаться, что это хороший способ увеличить пробег грузовиков и логистические затраты, и многие традиционно мыслящие менеджеры, в том числе в Tesco и Britvic, так и думали. Однако на практике эти методы существенно сокращают общий пробег наряду с транспортными затратами и одновременно снижают общие запасы в системе{41}41
Регулярно проводимые в Великобритании обследования показали, что осуществляющие доставку грузовики используются только 28 % всего возможного времени, 20 % времени совершают порожние рейсы и в среднем бывают загружены только наполовину. См. Alan McKinnon et al, “Running on Empty?” ECR Journal, Vol. 3, № 1, Spring 2003. Совершенно иные показатели эффективности у системы одновременной доставки нескольких видов продукции по маршруту молоковоза, используемой поставщиками Toyota и магазинами Seven-Eleven в Японии, при которой поставка и отгрузка строго синхронизированы. См. Hirofumi Matsuo and Yasuaki Takeda, “ECR: A Fresh Look from Japan,” ECR Journal, Vol. 2, № 2, Winter 2002. Если интервалы между рейсами невелики, грузовики делают много остановок и почти всегда перевозят значительный груз, это позволяет значительно уменьшить общее количество километров, которое необходимо проехать, чтобы доставить данное количество сырья и материалов.
[Закрыть].
Все это работает бесперебойно потому, что в течение дня заказы возобновляются только при одном условии: если потребитель забирает банки с колой со стойки на колесах и относит их к кассе, где кассир считывает данные штрих-кода на товаре и тем самым генерирует реальный заказ. С этого момента все шаги вверх по потоку обеспечения просто восполняют изъятое ниже по потоку: если потребители покупают за четыре часа четыре тележки банок с содовой, РРЦ получает сигнал погрузить четыре тележки этих банок на следующий грузовик. Когда эти товары перегружаются на трейлер, поставщику автоматически посылается сигнал изготовить еще четыре тележки банок с содовой для отправки в РРЦ к тому моменту, когда грузовик объедет магазины и вернется с пустыми тележками.
Было бы неправильно, конечно, объявлять эту систему идеальной. Как давно пришла к выводу Toyota, никакой процесс не остается идеальным надолго, и со временем обязательно возникают проблемы. Например, покупатели все еще надеются на скидки, а у поставщиков по-прежнему возникает искушение делать такие предложения, хотя они и отрицательно сказываются на работе логистической системы, провоцируя неожиданные всплески спроса или предложения{42}42
Лучше управлять этими всплесками по отдельности. Мы полагаем, что, когда компании больше узнают о бережливом обеспечении и научатся лучше рассчитывать общие затраты и результаты от подобных акций (которые намного выше, чем подозревают менеджеры, учитывающие только «точечные затраты»), эта практика в розничной торговле постепенно исчезнет. Мы еще вернемся к этому вопросу при обсуждении магазинов-складов в главе 6.
[Закрыть]. Но в основном эта система работает хорошо, и, конечно, намного лучше, чем традиционная, которую она собой заменила.
Заменив подсказанную простым здравым смыслом логистическую систему, основанную на сборе информации во многих точках и централизованном управлении, на гораздо более простые и в то же время более совершенные бережливые методы, Tesco создала упрощенный поток обеспечения, показанный на карте будущего состояния процесса («Поставка свежей колы»).

Результаты повышения эффективности оказались просто замечательными. Общее количество перемещений продукции (каждое из которых требует дорогостоящих затрат труда) сократилось со 150 до 50. Общее время цикла, начиная от линии розлива поставщика и кончая потребителем, покидающим магазин с банкой колы в руках, сократилось с 20 до 5 дней. Количество мест хранения запасов уменьшилось с пяти до двух (небольшой буферный запас в РРЦ и стойки на колесах в магазине), а распределительный центр поставщика для этих товаров вообще исчез. Величина колебаний спроса уменьшилась с 4:1 до 2:1, а уровень обслуживания для этой продукции повысился с 98,5 % (уже очень высокого показателя для пищевых товаров) до 99,5 %.
Пока Tesco применила эти методы более чем к половине своих товаров повседневного спроса, а также к сезонным товарам, выпускаемым к Рождеству, Пасхе и к лету. А когда она распространит новую технологию на все их виды, степень «корзинного выполнения заказа» при типичном походе в крупный магазин повысится с 4 до 82 %. Это означает, что неудачным окажется только один поход в магазин из пяти по сравнению с 24 из 25 в среднем по отрасли сегодня. А общие затраты Tesco, ее поставщиков и потребителей – не забывая о затратах времени и нервов потребителей, сэкономленных благодаря тому, что теперь все необходимое можно получить за один поход в магазин – будут существенно ниже. Таким образом, мы имеем решение, устраивающее абсолютно всех.
При старой системе запасы скоропортящихся товаров всегда пополнялись быстро и часто, но с гораздо более высокими затратами. С внедрением бережливых методов все вокруг – включая потребителей – рассматривается по сути как скоропортящийся товар, и общие затраты реально снижаются{43}43
Потоки обеспечения для скоропортящихся товаров также делаются бережливыми, поскольку Tesco участвует в реализации финансируемого британским правительством проекта составления карт потоков обеспечения для мяса, молочной и зерновой продукции на всем пути от потребителя обратно к ферме. См. “David Simmons, Mark Francis, and Daniel T. Jones, Food Value Chain Analysis” в Consumer Driven Electronic Transformation: Applying New Technologies to Enthuse Consumers and Transform the Supply Chain, ed. by Georgis Doukidis et al, Amsterdam: Elsevier, 2005.
[Закрыть].
В ретроспективе подход Tesco кажется логичным и ведущим прямо к цели. Фактически теперь именно он диктуется тем же самым здравым смыслом. Однако чтобы совершить такое преобразование, любая компания нуждается в сильном руководстве. В случае Tesco инициативу взял на себя Грэхем Бут, который умело применил свои дипломатические навыки (предварительно проведя совместную оценку процесса обеспечения), убедив и свои службы, и поставщиков поставить интересы потребителя на другом конце потока создания ценности выше интересов отдельной компании. Сохранению этого нового подхода немало способствовала активная поддержка генерального директора сэра Терри Лихи, настоявшего на том, чтобы Tesco не возвращалась к прошлой практике, даже столкнувшись с определенными проблемами. Как мы увидим в главе 6, постоянная нацеленность Tesco на бережливость своих потоков обеспечения наряду с новым подходом к предоставлению потребителю именно того, что он хочет, именно там, где он хочет, и делает ее лидером глобальной быстро развивающейся индустрии торговли потребительскими товарами.