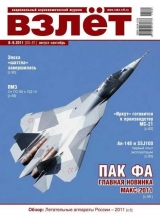
Текст книги "Взлёт 2011 08-09"
Автор книги: Взлет Журнал
Жанры:
Транспорт и авиация
,сообщить о нарушении
Текущая страница: 8 (всего у книги 13 страниц)
Алексей Михалев: «Двигателю пятого поколения нужен завод пятого поколения»
Одной из заметных новинок авиасалона МАКС-2011 должен стать новый пассажирский лайнер Ту-204СМ – глубоко модернизированный вариант известного пассажирского самолета, отвечающий самым современным требованиям к безопасности полетов, топливной эффективности и экологической безопасности. Во многом Ту-204СМ обязан этим своей силовой установке – новым двигателям ПС-90А2, производство которых освоено на Пермском моторном заводе. А в будущем предприятие перейдет на выпуск еще более совершенных двигателей нового поколения. Первый в этом семействе – ПД-14 – предназначен для установки на перспективный ближне-среднемагистральный лайнер МС-21. О том, как завод готовится к производству ПД-14 и что представляет собой его производственная программа сегодня, накануне МАКС-2011 мы попросили рассказать управляющего директора ОАО «Пермский моторный завод» Алексея Михалева.

Алексей Борисович, с какими результатами завершил Пермский моторный завод 2010 г., и какие планы стоят перед ним на 2011-й?
2010 г. для Пермского моторного завода был в целом успешным. В частности, было выпущено 24 новых двигателя ПС-90А всех модификаций и 62 отремонтировано; произведено 36 промышленных газотурбинных установок, отремонтировано 45. Объем продаж превысил 16,3 млрд руб.
Кроме того, в 2010 г. ПМЗ приступил к серийному выпуску новых изделий – авиационных двигателей ПС-90А2 и газотурбинных установок мощностью 25 МВт, – а также к работе по созданию перспективного двигателя пятого поколения ПД-14.
Эти итоги, безусловно, можно считать положительными. Во-первых, на предприятии продолжился рост объемов продаж (с 14,1 млрд руб… в 2009 г. до 16,3 млрд руб. в 2010-м). Во-вторых, ПМЗ продолжает осваивать и выпускать новую продукцию, участвует в перспективных проектах, тем самым создает задел на будущее.
В 2011 г., по сравнению с 2010 г., объем производства должен вырасти на 15 %. Соответственно, запланирован и рост выручки – до 18,3 млрд руб. Планом этого года предусмотрен выпуск 23 двигателей семейства ПС-90А (в т. ч. четырех ПС-90А2) и 53 газотурбинных установок (47 – на базе двигателя ПС-90А и шести – на базе Д-30). Вырастут существенно и объемы ремонта: предполагается отремонтировать 76 ПС-90А, восемь Д-30, а также 45 ГТУ на базе двигателя ПС-90А и 13 – на базе Д-30.
За первые шесть месяцев этого года нами уже выпущено 10 новых двигателей семейства ПС-90А и 17 газотурбинных установок, выполнено большое количество ремонтов.

В среднесрочной перспективе, до 2020 г., на ОАО «Пермский моторный завод» прогнозируется дальнейший устойчивый рост объемов производства. Это будет происходить за счет активного продвижения на рынок как существующей продукции (ПС-90А, ГТУ мощностью от 2,5 до 25 МВт), так и новой продукции, в частности двигателя ПД-14 и новых типов ГТУ. Кроме того, будет расти объем ремонтных работ. Прогнозируемый объем выпуска продукции в 2020 г. оценивается в 31 млрд руб.
Каково сегодня соотношение объемов выпускаемой продукции по авиационной и энергетической тематике и будет ли оно изменяться в дальнейшем?
Последние пять лет объемы производства по этим направлениям примерно равны. В прошлом и в текущем году отмечается небольшое преобладание наземной тематики. Динамика заказов ГТУ демонстрирует устойчивый рост, а потребности в двигателях ПС-90А, как вам известно, зависят от ситуации на рынке авиаперевозок и от состояния и тенденций развития всей отечественной авиационной отрасли.
Кто Ваши основные заказчики по авиационной тематике в этом году? Сколько двигателей семейства ПС-90А уже поставлено с начала года?
Нашим заводом на сегодня выпущено уже 360 двигателей ПС-90А всех модификаций. В настоящее время на крыле работают 210 двигателей в 16 авиакомпаниях, которые и являются конечными потребителями двигателей. Основные из них – это «Аэрофлот», СЛО «Россия», «Ред Вингс», «Владивосток Авиа», «Волга– Днепр» и «Полет». Несколько самолетов, оснащенных ПС-90А, приобрели зарубежные компании – «Кубана» (Куба), «Силк Уэй» (Азербайджан), «Эр Корье» (КНДР). Недавно у нас в заводском учебном центре закончили подготовку иорданские авиационные специалисты. Им предстоит обслуживать двигатели ПС-90А76. Как вам, наверное, известно, ВВС Иордании приобрели в России два новых самолета Ил-76МФ.
Заказчиками ПС-90А в 2011 г. являются Объединенная авиастроительная корпорация, самолетостроительные предприятия ВАСО и КАПО, Управление делами Президента РФ, азербайджанская авиакомпания «Силк Уэй». На сегодня им уже поставлено 10 из 23 заказанных на этот год двигателей.
Каков сегодня ресурс выпускаемых заводом двигателей семейства ПС-90А и ведутся ли работы по его увеличению? Какие мероприятия для этого реализуются?
Двигатель ПС-90А является двигателем четвертого поколения и эксплуатируется по так называемой «стратегии № 2». Это означает, что для него не устанавливаются фиксированные назначенный и межремонтный ресурсы. Двигатели эксплуатируются по реальному техническому состоянию, т. е. в пределах ресурсов основных деталей (диски, валы, лопатки вентилятора, детали подвески двигателя, корпус камеры сгорания). Оценка состояния этих деталей выполняется на основании показаний автоматизированной системы диагностики двигателя. Показания системы диагностики считываются после каждого полета, а ряд параметров контролируется экипажем в процессе полета.
Назначение ресурсов основных деталей проводится в соответствии с планами управления ресурсами. Необходимые мероприятия по увеличению ресурсов расписаны как для нашего завода, так и для предприятия-разработчика – ОАО «Авиадвигатель», а также ряда предприятий смежников, поставляющих покупные комплектующие изделия.
На сегодня средняя наработка по парку двигателей ПС-90А до снятия в ремонт составляет 6000–6500 часов. А лидерный двигатель наработал в ОАО «Аэрофлот» без ремонта 9936 часов.
Как завод участвует в программе создания перспективного семейства двигателей для гражданской и транспортной авиации ПД-14? Определено ли уже окончательно, как будет строиться производственная кооперация с другими предприятиями ОДК при последующем серийном производстве ПД-14?
В 2010 г. завод изготовил первые образцы деталей ПД-14, которые были использованы в газогенераторе-демонстраторе двигателя. Он успешно прошел испытания в конце 2010 г. В текущем году Пермскому моторному заводу предстоит снова изготовить детали газогенератора– демонстратора – уже следующей генерации, а также изготовить узлы и детали полноразмерного двигателя-демонстратора ПД-14. Пермский моторный завод определен как головной изготовитель ПД-14. Это означает, что основные узлы нового двигателя будут производиться именно силами ПМЗ, остальные мы будем получать от предприятий-партнеров, участвующих в кооперации.
Рабочие лопатки вентилятора будут изготавливать наши партнеры из Уфы. Для этого ОАО «УМПО» приобретен новейший комплекс импортного оборудования – прессы, печи и т. д. Сейчас полным ходом идет освоение этого комплекса.
Модуль компрессора низкого давления закреплен за коллективом НПО «Сатурн». Причем, модуль подпорных ступеней данного компрессора проектируется в ходе совместной работы конструкторов ОАО «Авиадвигатель» и НПО «Сатурн».
Турбину низкого давления для ПД-14 поручено спроектировать специалистам конструкторского бюро «Мотор» (Уфа) и ОАО «Авиадвигатель». А серийным изготовителем данной турбины станет коллектив УМПО.
Весьма важная задача, которую должны решить пермские моторостроители, – это производство турбины высокого давления. Предусмотрено, что все турбинные лопатки – и рабочие, и сопловые – будут изготавливаться путем монокристаллического литья. Ранее этот прогрессивный способ литья уже был внедрен при изготовлении турбинных лопаток двигателя ПС-90А2, и сейчас данный опыт пригодился.
Если же говорить в целом, то буквально каждый из узлов двигателя ПД-14 обязан иметь существенные преимущества по сравнению с тем, что было раньше. Причем это касается не только технических характеристик, но и таких важнейших экономических показателей, как минимальные трудоемкость и себестоимость.
Какая модернизация производственных мощностей ПМЗ запланирована в рамках освоения выпуска ПД-14: какие новые технологические процессы потребуется внедрить, какое оборудование закупить? Что уже сделано, каковы источники финансирования этих работ?
В рамках проекта ПД-14 работа идет в нескольких направлениях: это замена оборудования, разработка новых технологий, строительство и реконструкция зданий и сооружений, обучение персонала.
Поскольку ПД-14 – абсолютно новый для предприятия продукт, то простой заменой оборудования не обойтись. Любой, самый высокотехнологичный станок ничего не даст, если нет разработанной технологии, высокопрофессиональных специалистов, зданий, которые бы отвечали современным требованиям технической безопасности.
Например, в прошлом году в рамках проекта ПД-14 мы, в частности, приобрели установку для лазерной резки и выполнения перфораций, роботизированный комплекс для напыления, вакуумную печь. Было принято решение, что новое оборудование целесообразно разместить в одном здании. Специально для этого была проведена глубокая реконструкция одного из производственных цехов. Кроме того, было организовано обучение специалистов, работающих на данном оборудовании. Сейчас идет процесс загрузки новых станков, разрабатываются технологии для обширной номенклатуры деталей.
Еще один пример – строительство нового производственного комплекса. В нем будет два отделения: в одном расположится подготовительный участок, в другом – уникальная для России установка для нанесения теплозащитных покрытий методом электронно-лучевого напыления (фирма ALD, Германия). Начатое в 2010 г. строительство корпуса уже завершено, сейчас идет монтаж установки ALD, к концу года должны быть завершены пусконаладочные работы. В течение ближайших 2–3 лет будет укомплектовываться оборудованием подготовительный участок. В результате этого комплексного подхода мы получим замкнутый цикл производства.
Другими словами, реализуя программу технического развития предприятия, мы не просто меняем оборудование, мы меняем производственные процессы, выстраиваем их по принципам «бережливого производства», сводя к минимуму затраты, добиваясь максимальной эффективности.
Финансирование программы технического перевооружения идет как за счет собственных и заемных средств, так и в рамках Федеральной целевой программы «Развитие гражданской авиации до 2020 г.». В частности, на подготовку производства ПД-14 согласно ФЦП в 2009 г. было выделено 380 млн руб., в 2010 г. – 550 млн руб., в 2011 г. планируется потратить 1 млрд руб.


В чем, по Вашему мнению, заключается стратегия дальнейшего развития ОАО «ПМЗ»? Что такое «Программа 2020» и какие основные положения она содержит?
Анализ рынка показывает, что в среднесрочной перспективе спрос на продукцию Пермского моторного завода будет продолжать расти. Сегодня и семейство двигателей ПС-90А, и семейство газотурбинных установок промышленного применения востребованы на рынке. Готовится серийное производство ПД-14. Объемы производства будут увеличиваться, но вместе с тем будут ужесточаться и требования заказчиков к качеству продукции. Мы понимаем, что двигателю пятого поколения нужен завод пятого поколения, поэтому и была разработана стратегия развития предприятия до 2020 е, которая предполагает существенную модернизацию производства. Необходимо менять принципы работы, обучать имеющийся персонал, внедрять новые технологии.
Модернизация Пермского моторного завода будет проходить в трех направлениях: развитие Центров технологических компетенций (ЦТК), работающих на всю структуру Объединенной двигателестроительной корпорации, совершенствование существующих производств и технологий, а также создание технопарка.
Сегодня идет активная работа в рамках создания ЦТК «Производство турбинных лопаток». В мае этого года завершилось строительство нового производственного корпуса № 120, в котором будет размещена уникальная для России установка фирмы ALD для нанесения теплозащитных покрытий на турбинные лопатки. Оборудование уже поступило на завод, к концу 2011 года должны быть завершены пуско-наладочные работы.


Параллельно с установкой нового оборудования ведутся работы по освоению ряда современных технологий создания лопаток. В итоге в течение трех лет на ОАО «Пермский моторный завод» будет создан замкнутый цикл производства турбинных лопаток. Преимущество ЦТК заключается в том, что ПМЗ сможет выпускать качественные лопатки не только для собственных нужд, но и для других предприятий ОДК и даже зарубежных компаний. Кроме того, до 2016 г. планируется создать ЦТК по выпуску камер сгорания и корпусов.
Будут изменены и существующие производственные схемы. Появится отдельное производство роторов турбин и компрессоров, будут реорганизованы и технологически обновлены сборочное и ремонтное производства. Эти изменения позволят сократить цикл изготовления продукции, улучшить качество продукции, повысить управляемость производственными процессами. Например, сегодня в ремонте двигателя задействовано 16 цехов: только на оформление бумаг и транспортировку деталей уходит значительная часть рабочего времени. Объединение ремонтного производства под одной крышей позволит нам ликвидировать не только эти, но и многие другие издержки.
Еще один крупный проект – модернизация испытательной базы в поселке Новые Ляды. Для обеспечения бизнес– плана выпуска двигателей ПС-90А, ПД-14 и газотурбинных установок в 2012–2020 гг. принято решение о реконструкции испытательного стенда № 1 и строительстве новых испытательных стендов № 5 и 6. Уже проведен тендер на разработку проектной и рабочей документации, определен типовой проект для новых испытательных стендов.
В ходе реконструкции завода предполагается высвободить более 30 % производственных площадей, на которых разместится технопарк. В планах ПМЗ создание управляющей компании «Технопарк – Пермские моторы», которая в течение трех лет будет предоставлять инновационным предприятиям производственные площади и различные услуги по льготной цене.
Одним словом, в ближайшее время на ПМЗ будет реализовано большое количество проектов. Разумеется, в связи с этим значительное внимание будет уделено развитию кадрового потенциала. У нас разработана программа удержания кадров, поощрения производственной, рационализаторской, научно-технической инициативы. Уверен, мы сумеем создать единую команду и успешно реализовать поставленные перед нами задачи.

Андрей ФОМИН
«Иркут» готовится к производству МС-21
Основным перспективным проектом отечественного самолетостроения в области гражданской авиации в ближайшее десятилетие должна стать программа создания и производства семейства ближне-среднемагистральных пассажирских авиалайнеров МС-21, рассчитанных на перевозку от 150 до 210 человек. На предстоящем авиасалоне МАКС-2011 вниманию специалистов и широкой публики впервые в России будет представлен полноразмерный макет пассажирского салона и кабины пилотов МС-21, а также натурные образцы элементов крыла будущего лайнера, которое будет полностью выполняться из композиционных материалов.
Согласно распоряжению Президента России от 6 июня 2010 г. головным исполнителем программы разработки и производства самолетов МС-21 является Научно-производственная корпорация «Иркут». Постройка опытных образцов, а затем и всех серийных самолетов семейства МС-21 будет вестись на Иркутском авиационном заводе, являющемся филиалом корпорации «Иркут». О том, как готовится предприятие к выпуску МС-21, редактору «Взлёта» довелось увидеть своими глазами во время июльской поездки на завод.
Сегодня Иркутский авиационный завод – одно из крупнейших предприятий отечественного самолетостроения, а если говорить об объеме производства, то, наверное, лидирующее в отрасли. В настоящее время в Иркутске строятся многоцелевые сверхманевренные истребители Су-30МКИ различных вариантов и учебно-боевые самолеты Як-130. Как сообщил генеральный директор Иркутского авиационного завода – вицепрезидент корпорации «Иркут» Александр Вепрев, в 2010 г. предприятие изготовило 38 истребителей семейства Су-30МКИ (включая комплекты для лицензионной сборки в Индии), а также девять Як-130.
В сумме это дает 47 машин, что составляет более половины всех произведенных в прошлом году самолетов в России.
С 2007 г. в рамках программы международной кооперации «Иркут» приступил к поставкам западноевропейскому концерну «Эрбас» компонентов для сборки самолетов А320. На заводе было освоено производство трех агрегатов для лайнеров семейства А320 – ниши передней опоры шасси, килевой балки (основной силовой элемент нижней части фюзеляжа в районе центроплана) и направляющих закрылков. Объемы поставок «Эрбасу» неуклонно возрастают. Так, если в 2007 г. ему были переданы две первые ниши шасси, то в 2008-м – уже 21, в 2009-м – 82, а в 2010-м – 104. Поставки килевых балок начаты в 2008 г. (первые четыре изделия), в 2009 г. в Тулузу из Иркутска ушло уже 34 балки, а в 2010-м – 71. Учитывая, что в 2009–2010 гг. «Эрбас» поставлял на рынок примерно по 400 самолетов машин семейства А320 в год, то каждый четвертый из них сегодня уже оснащается «иркутской» нишей передней опоры шасси, а каждый шестой – килевой балкой.
Выполнение заказов для «Эрбаса» в свое время стало толчком для начала радикальной модернизации производственных мощностей и технологических процессов Иркутского авиазавода. Начались закупки самого современного оборудования, подготовка для работы на нем персонала, внедрение строжайших систем контроля качества выпускаемой продукции. Как заявил президент «Иркута» Алексей Федоров, за шесть лет в модернизацию производства на заводе уже было вложено 10,8 млрд руб. (около 360 млн долл.), что стало первым и весьма внушительным шагом на пути подготовки к выпуску перспективных лайнеров МС-21.
В ходе первого этапа технического перевооружения уже осуществлен переход на современную нормативную базу (внедрено более 2200 стандартов), внедрены цифровые методы проектирования и подготовки производства, обновлено более 280 единиц оборудования – станочного парка, лабораторий, испытательной базы. Внедрена современная система менеджмента качества (требования EN9100), освоены современные глобальные логистические схемы и технологии «бережливого производства». В итоге, в 2010 г. выработка продукции на одного работника завода достигла 4,2 млн руб. – это лучший показатель в российском авиастроении.
Решительная революция произошла в области информатизации производства: внедрены цепочки сквозных CAD/CAM/ CAE/PDM технологий для математического моделирования аэродинамических обводов самолета, инженерного и кинематического анализа изделий, проектирования в 3D и изготовления деталей с последующим автоматизированным контролем качества с использованием контрольно-измерительных машин, безэталонного изготовления оснастки на базе 3D моделей, окончательной сборки с использованием лазерно-оптических средств, разработки конструкторской и технологической документации и данных и их использования для управления предприятием. На сегодня «Иркут» уже располагает более чем 1300 рабочими местами для конструкторской и технологической подготовки на базе CAD/CAM/CAE/ PDM технологий.

Президент корпорации «Иркут» Алексей Федоров: «Выпуск компонентов для «Эрбаса» заставил начать техническое перевооружение Иркутского авиазавода, которое стало первым этапом подготовки к производству МС-21»

Производство килевой балки для самолетов А320 на ИАЗ

Иркутскими нишами передней опоры шасси сегодня оснащается уже каждый четвертый лайнер семейства А320
Серьезная модернизация проведена в заготовительно-штамповочном и механосборочном производстве, где уже внедрены технологии, необходимые для производства МС-21. В их числе раскрой заготовок на оборудовании с ЧПУ, продольная обтяжка обшивок габаритами до 7,2х2 м, гибка прокаткой обшивок размером до 7,8х2 м, поперечная обтяжка обшивок габаритами до 4х2,5 м, обработка прямолинейных профилей длиной до 7 м, формовка, штамповка и доводка деталей, высокоскоростная обработка алюминиевых сплавов (максимальные размеры заготовок 6х2 м при толщине до 200 мм), титана и стали (2х2 м, толщина до 200 мм), обработка прямых алюминиевых профилей длиной до 10 м и панелей из алюминиевых сплавов длиной до 23,5 м, дробеметное поверхностное упрочнение деталей из алюминиевых сплавов.
Особая гордость Иркутского авиазавода – так называемая гальваника – производство по нанесению покрытий и химической обработке деталей. Равных ему в российском авиастроении пока нет ни на одном другом предприятии. В Иркутске на сегодня уже внедрено более 40 специальных процессов – как для текущих проектов, так и для будущего производства МС-21. К ним относятся анодирование деталей из алюминиевых и титановых сплавов, размерное химическое травление алюминиевых деталей, термообработка деталей из алюминиевых сплавов, вакуумная термообработка деталей и узлов из титана, люминесцентный контроль и др. В настоящее время ведутся работы по строительству и оснащению оборудованием гальванических и малярных отделений второй очереди.
Начата модернизация агрегатно-сборочного производства: уже освоен процесс автоматической клепки (она будет одной из ключевых технологий при изготовлении МС-21), внедрены современные технологии агрегатной сборки, которые сейчас используются при производстве компонентов для «Эрбаса», отработана концепция автоматизированной сборки– стыковки.
В результате, на существующих мощностях и площадях Иркутского авиазавода уже сейчас можно строить первые опытные самолеты МС-21 для статических, ресурсных и летных испытаний. Однако для последующего их серийного производства в планируемых объемах (а всего «Иркут» предполагается обеспечить ежегодный выпуск до 60–70 самолетов МС-21 в год) потребуется радикальная модернизация агрегатной и окончательной сборки. На это и будут в основном направлены усилия в ближайшие несколько лет в рамках второго этапа перевооружения завода. Предстоит внедрить технологические процессы автоматической стыковки агрегатов самолета. Предусматривается проектирование и изготовление специализированной линии для агрегатной и окончательной сборки МС-21, для чего будет проведена реконструкция агрегатно-сборочного производства и цеха окончательной сборки. Параллельно будет происходить наращивание мощностей по заготовительно-штамповочному и механосборочному производствам, завершение запуска новых специальных процессов (гальваника, окраска).
На недавнем авиасалоне в Ле-Бурже корпорация «Иркут» заключила соглашение с германской компанией «Дюрр» (DURR Systems GmbH) об организации на площадях Иркутского авиационного завода поточной линии сборки самолетов МС-21. Контракт включает разработку, производство и поставку специального оборудования, а также оказание услуг по проекту поставки линий узловой и агрегатной сборки, стыковки агрегатов планера и окончательной сборки самолетов семейства МС-21. Для этого предполагается выполнить перепланировку и полную реконструкцию цехов, в которых будет выполняться монтаж линии, установить современное оборудование, разработать технологию и провести обучение персонала.

Кооперация предприятий по разработке и производству МС-21
Самые современные сборочные линии будут устанавливаться на существующих площадях завода. Как подчеркнул президент корпорации «Иркут» Алексей Федоров, их размеры вполне позволяют это обеспечить при планируемых годовых объемах серийного выпуска МС-21, и нового капитального строительства для этого не требуется. Цех окончательной сборки Иркутского авиазавода в свое время строился под выпуск самолетов Ан-12, сравнимых по размерам с МС-21. Во время поездки на завод в июле, в сборочном цеху одновременно находилось на разных стадиях готовности более трех десятков самолетов Су-30МКИ и Як-130. По словам Алексея Федорова, линия сборки МС-21 разместится по одной стороне нынешнего сборочного цеха, где пока ведутся работы по истребителям Су-30МКИ. Однако в дальнейшем, во второй половине этого десятилетия, по мере выполнения имеющихся и планируемых сейчас контрактов, производство их будет постепенно снижаться, тем самым высвобождая место в цеху для МС-21. Сборка Як-130 на первых порах будет соседствовать с линией МС-21, не мешая ей, но в случае увеличения объемов производства авиалайнера, может быть переведена в другие цеха завода. Как сообщил Александр Вепрев, такой вопрос уже проработан.
По состоянию на прошлый год, совокупный объем инвестиций по программе МС-21 оценивался в 137 млрд руб. (более 4,5 млрд долл.), из которых на ОКР приходилось 97 млрд руб. (чуть более 3 млрд долл.), а на техническое перевооружение предприятий (не только Иркутского авиазавода, но и других заводов, задействуемых в программе) – 40 млрд руб. (1,3 млрд долл.). Однако, как заявил Алексей Федоров, сейчас эти цифры немного пересмотрены, и затраты удастся немного снизить. В организацию новых сборочных линий, по его мнению, еще предстоит вложить около 600 млн долл.
В рамках утвержденной программы кооперации в производстве МС-21, помимо Иркутского авиазавода, будут участвовать ульяновский завод «Авиастар», ВАСО, НПО «Технология» и ряд других предприятий. В Иркутске будут изготавливаться все отсеки фюзеляжа (за исключением хвостового, за который отвечает НПО «Технология»), в Ульяновске – «черное» крыло, в Воронеже – механизация крыла с обтекателями и «черное» оперение. Поставщиками шасси определен нижегородский «Гидромаш», создавший совместное предприятие с «Либхером». Окончательная сборка самолета – полностью в компетенции Иркутского авиазавода, однако дальнейшая «кастомизация» под конкретных заказчиков может вестись в Ульяновске.
В разработке конструкции МС-21 задействован еще более широкий круг предприятий. Инженерный центр корпорации «Иркут», созданный на базе ОАО «ОКБ им. А.С. Яковлева», спроектировал отсеки фюзеляжа Ф1 и Ф3, кессоны крыла и осуществляет общую увязку проекта. ЗАО «ГСС» (разработчик самолета «Суперджет») отвечает за отсеки фюзеляжа Ф2 и Ф4, ОАО «Туполев» – за горизонтальное оперение, механизацию крыла и обтекатели, ТАНТК им. Г.М. Бериева – за вертикальное оперение и хвостовой отсек фюзеляжа.

Гэнеральный директор Иркутского авиационного завода Александр Вепрев: «Имеющихся площадей ИАЗ вполне достаточно для ежегодного выпуска до 70 самолетов МС-21»

Проект линии поточной сборки самолетов МС-21 на Иркутском авиационном заводе
На сегодня уже полностью определена общая конфигурация самолета и основных систем, выполнены аэродинамические, прочностные и другие расчеты и эксперименты, идут испытания прочностных и технологических образцов (в т. ч. прототипа кессона крыла из углепластика), определены поставщики всех бортовых систем и идет заключение долгосрочных контрактов с ними.
Как сообщил Александр Вепрев, закладка первых деталей для опытных образцов МС-21 должна начаться уже в этом году. Всего для участия в сертификационных испытаниях «Иркут» намерен изготовить восемь прототипов МС-21 – шесть летных (в двух вариантах – МС-21-200 и МС-21-300), статический и ресурсный. Первый полет головного опытного самолета намечен на 2014 г., а завершение сертификации и начало поставок – на 2016 г.
Общий объем программы производства самолетов МС-21 всех модификаций в период до 2035 г. определен в 1180 самолетов на общую сумму 1429 млрд руб. в ценах 2010 г. (почти 50 млрд долл.). Программа МС-21 обеспечит занятость 8-10 тыс. человек на заводах в Иркутске, Ульяновске и Воронеже и еще 4–5 тыс. чел. на российских предприятиях – поставщиках комплектующих изделий и материалов.
В связи с этим подготовке новых специалистов на «Иркуте» уделяют самое первоочередное внимание. Этому способствует стартовавшая в 2005 г. программа обновления персонала по непрерывной цепочке «школа – учебное заведение – повышение квалификации – переподготовка». При Иркутском авиазаводе действует отвечающий самым современным требованиям учебно-производственный центр, обеспечивающий сегодня ежегодную подготовку порядка 5000 человек, в т. ч. около 500 новых рабочих. В итоге, на сегодня Иркутский авиазавод укомплектован кадрами на все 100 % (редчайший случай в современном российском авиапроме), а средний возраст работников составляет менее 40 лет, что также является рекордным показателем в отрасли. в

Сборка антенных систем РЛСУ «Барс» для самолетов типа Су-30МКИ