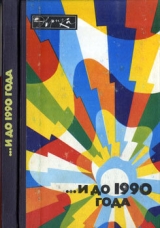
Текст книги "...И до 1990 года"
Автор книги: В. Федченко
сообщить о нарушении
Текущая страница: 8 (всего у книги 13 страниц)
Бесстрастные слова «увеличился», «возросло» не должны создать иллюзию простоты сделанного. Все это – результат вдохновенного труда больших коллективов ученых, инженеров, рабочих, свидетельство высокого научно-технического потенциала нашей страны, которая первой в мире начала строить газовые магистрали такого большого диаметра.
Как же сказалось изменение параметров газопровода на его производительности? Она возросла в 3—3,5 раза и составила весьма внушительную цифру – 30—35 миллиардов кубометров газа в год. При этом более чем в два раза сократилась себестоимость перекачки газа.
Ясно, не сделай мы такого скачка, пришлось бы при тех же масштабах добычи строить раза в три-четыре больше ниток газовых магистралей. Обернулось бы это многими миллиардами рублей дополнительных капиталовложений, огромными затратами и без того нелегкого труда.
Планы развития экономики и на ближайшую перспективу предусматривают высокие темпы прироста добычи газа. Он нужен нам все в больших и больших количествах.
В этой пятилетке из Западной Сибири, которая еще долго будет оставаться нашей основной нефтегазодобывающей базой, надо передать на огромные расстояния сотни миллиардов кубометров газа.
Если строить магистрали, одна нитка которых пропускает 30—35 миллиардов кубометров, то нам придется ежегодно вводить в эксплуатацию один газопровод (из двух ниток) протяженностью 3—3,5 тысячи километров, строительство которого обходится в несколько миллиардов рублей! Нельзя не считаться и с тем, что значительную часть весьма протяженных трубопроводов предстоит прокладывать на Севере, в тундре, через реки, болота и топкие озера, в неустойчивых грунтах, в зонах вечной мерзлоты, вести строительство в условиях продолжительной и суровой зимы, короткого и дождливого лета.
Какой же должна быть стратегия развития трубопроводного транспорта, чтобы по возможности уменьшить огромные материальные и трудовые затраты?
Экономика отвечает однозначно: необходимо дальнейшее повышение производительности газовой магистрали. Другого пути нет. Ведь альтернатива такому решению – прокладка дополнительного числа ниток параллельных газопроводов.
Казалось бы, самое простое – еще увеличить диаметр труб. Действительно, это весьма эффективный способ: скажем, сделаем трубу в три раза большего диаметра, и примерно в девять раз повысится ее пропускная способность.
Но опыт сооружения газопроводов и технико-экономические расчеты убеждают, что на сегодня уже достигнут оптимальный диаметр труб и дальнейшее его увеличение пока нецелесообразно.
Значит, остается другая возможность: повысить давление перекачки газа, скажем, до 100—120 атмосфер. Это окажется особенно эффективным, если сочетать повышение давления с охлаждением газа. Ведь при снижении температуры уменьшается его объем, что, естественно, тоже повышает производительность газопровода.
Многого ли мы добьемся, если по трубопроводу в 1420 миллиметров будем перекачивать умеренно охлажденный газ, примерно до минус 20° С, под давлением, например, 120 атмосфер? Расчеты показывают, что производительность газопровода увеличится примерно в два раза.
Конечно, это огромный эффект, ведь может отпасть необходимость в сооружении второй нитки газопровода.
Так за чем же дело стало?
На пути реализации этой идеи немало трудностей, и главная из них – обеспечение надежности трубопровода.
Магистральный газопровод представляется весьма простым техническим сооружением. Действительно, проложены трубы, и газ по ним подается потребителям. При движении из-за того, что поверхность стенок труб не идеально гладкая, он тормозится, теряет часть энергии. Приходится на трассе газопровода примерно через каждые 100 километров ставить компрессорные станции, «подбадривающие» газ.
Но при всей внешней конструктивной простоте очень трудно обеспечить надежность газовой магистрали. И это прежде всего относится к трубам. Приходится считаться с тем, что на каждом участке магистрали между двумя компрессорными станциями под землей находится стокилометровый стальной цилиндр, в котором запасено огромное количество энергии – более 10 миллионов кубометров газа под высоким давлением. И этот газ, естественно, стремится разорвать трубу, вырваться наружу. Такие подземные аккумуляторы энергии тянутся на многие тысячи километров. Надо учитывать и то, что газопроводы работают в суровых климатических и почвенно-гидрологических условиях, когда угроза разрушения от колебаний температур, коррозии становится особенно сильной. И при всем этом зарытый в землю трубопровод нет возможности осмотреть, освидетельствовать с помощью приборов. Значит, нельзя обнаружить каких-либо дефектов в металле на стадии их зарождения.
При аварии маленькая трещина, распространяясь по трубопроводу со сверхзвуковой скоростью, может разорвать его в клочья или развернуть в лист. Протяженность таких лавинных повреждений иногда достигает десятка километров. Аварии сопровождаются взрывами, пожарами, загрязняют окружающую среду. Устранение последствий – дело непростое, особенно если трасса пролегает на Севере, в сильно заболоченной местности, куда по бездорожью надо оперативно доставить трубы, всевозможную технику.
Проблема надежности трубопровода сегодня центральная. И ясно, что переход к более высоким давлениям газа делает ее еще сложнее.
Надежность газовой магистрали зависит от многих факторов, в частности, в очень большой степени от качества сварки. Но главный ключ к проблеме – у металлургов. Нужна сталь, свойства которой наиболее полно соответствовали бы условиям работы трубопровода.
Задача эта непростая. Силы, которые действуют на трубопровод, таковы, что если в металле возникает трещина, то независимо от его прочности она обязательно разовьется. И разрушение неминуемо. Но если труба будет сделана из стали, сочетающей высокую прочность с вязкостью, которая сохраняется и при низких температурах, то положение изменится. Разрушение, если оно и появится, не будет уже хрупким и распространится не на тысячи метров, а ограничится метрами, десятками метров.
Почему так важна вязкость стали?
Представим себе, что в трубе появилась трещина. Из-за разрушения начинает падать давление газа, уменьшаются и напряжения в металле. Если сталь достаточно пластична, то трещина как бы вязнет в ней, лишенная необходимых для своего развития напряжений. Когда же вязкость стали мала, то напряжения в ней падают медленнее, чем развивается трещина, и избыточная энергия, накопленная в металле, расходуется на распространение разрушения, которое носит хрупкий характер и оказывается весьма протяженным.
Конечно, наряду с высокой прочностью и вязкостью сталь должна еще и хорошо свариваться, сохраняя это свойство и при низких температурах. Ведь сварка – главный технологический процесс при сооружении газопровода.
Лучше всего таким требованиям удовлетворяет низкоуглеродистая сталь с добавками ниобия, молибдена и никеля. Но одного легирования еще недостаточно. Чтобы из слитка получить лист нужной толщины и с требуемыми свойстами, из которого потом сделают трубу, приходится прибегать к особому виду обработки: на стане контролируемой прокатки. Здесь с помощью целой системы автоматики очень точно выдерживаются температурные интервалы промежуточных пропусков листа через валки стана, температура конца прокатки и величина последнего обжатия. Этот строго регламентированный режим обработки позволяет получить металл с такой структурой и размером зерен, которые и обеспечивают ему необходимое сочетание свойств.
Затем листы с помощью валковой формовки или на очень мощных прессах формуют так, что получаются цилиндрические заготовки, из которых и сваривают трубу.
Изготовление трубопровода, надежно работающего при давлении 75 атмосфер, связано с преодолением значительных трудностей – и технических и экономических. Объясняется это тем, что сталь, из которой приходится делать такие трубы, сегодня остродефицитная и дорогая. К тому же изготовить из нее лист толщиной 16—20 миллиметров с нужными механическими свойствами можно лишь на станах контролируемой прокатки, которых во всем мире насчитываются единицы; у нас их тоже мало.
Как же осуществить переход на еще более высокие давления – на 100—120 атмосфер, с которым связана перспектива развития газовой индустрии?
Для таких давлений понадобятся трубы с еще более толстой стенкой – от 22 до 50 миллиметров. Они, понятно, будут значительно тяжелее, а значит, существенно увеличится расход и без того дорогой стали. Чтобы из такого листа отформовать трубу, потребуются прессы-гиганты. И все это в конечном счете приведет к тому, что рост стоимости труб и оборудования опередит экономический эффект от увеличения производительности газопровода.
Ясно, что надо искать другой подход к этой проблеме.
И тогда ученые Института электросварки имени Е. О. Патона обратились к ранее выдвинутой идее многослойных конструкций.
Применительно к трубе это означало, что делается она не монолитной, из толстого листа, а многослойной, из относительно тонкой рулонной стали. При этом используется не остродефицитная дорогая сложнолегированная сталь, а низколегированная, производство которой освоено отечественной металлургией.
В чем же смысл перехода от трубы с монолитной стенкой к многослойной?
Известно, что если взять совершенно одинаковые стальные заготовки, скажем, слиток, разделенный на две части, а затем одну из них прокатать до толстого листа, а другую выкатать в тонкий лист, то последний окажется прочнее и пластичнее; при этом чем тоньше лист, тем ниже температура, при которой он сохраняет вязкость. Словом, весь комплекс свойств, столь важных для обеспечения надежной эксплуатации трубопровода, у тонкой стали лучше, чем у толстой.
И если набрать пакет – а это и есть многослойная конструкция – из тонких листов, то он сохранит все преимущества тонкого листа – больше прочность, больше вязкость. Свойства каждого слоя не зависят от суммарной толщины конструкции. Значит, можно получать стенку с любой наперед заданной прочностью. При этом необходимая прочность будет достигнута при меньшей толщине, чем в случае монолитного металла.
Таким образом, разделив толщу металла на слои, мы тем самым умножили его прочность и вязкость.
Именно идея многослойной конструкции помогла в свое время успешно решить задачу изготовления сосудов высокого давления.
В энергетике, во многих химических производствах нужны реакторы, колонны, различные аппараты, способные выдерживать температуру в сотни градусов и давления в сотни атмосфер. Только в таких экстремальных условиях удается проводить некоторые технологические процессы, получать нужные вещества, материалы. Но чем выше поднимались давления, тем больше приходилось увеличивать толщину стенок сосудов, тем труднее и дороже становилось изготовление сосудов с монолитной стенкой, а в ряде случаев и просто невозможным. И то, что оказалось не под силу традиционным способам изготовления сосудов, удалось сделать, используя многослойную конструкцию.
На заводе «Уралхиммаш» в Свердловске создано уникальное производство сварных многослойных сосудов. За последние годы здесь изготовлено более 200 сосудов высокого давления, в том числе колонн синтеза аммиака, реакторов гидрокрекинга нефти с толщиной стенки до 400 миллиметров. Это 70—80 слоев, толщиной по 5—6 миллиметров каждый. Давления в этих аппаратах достигают 400 атмосфер, а температура – 400 градусов. Эти цифры сами по себе говорят о сложности эксплуатации таких аппаратов, но надо сказать, что надежность их чрезвычайно высока и ни одной аварии, ни одной неприятности с ними не произошло. Несомненно, многослойным сосудам высокого давления принадлежит большое будущее.
Использование многослойных труб позволит сравнительно просто решить проблему перехода к сооружению магистралей на более высокие давления. Действительно, если необходима труба, способная выдержать более высокое давление, чем предусматривалось раньше, то достаточно намотать один-два или более дополнительных слоев. Иными словами, из одной и той же дешевой стали можно получать трубы, рассчитанные на любые требуемые давления.
Можно пойти и по другому пути – изготавливать многослойные трубы с теми же прочностными характеристиками, что у труб со сплошной стенкой. А так как для этой цели будет взята не сложнолегированная дорогая сталь, а низколегированная, более дешевая, то понятно, что стоимость труб, сохранивших заданную прочность, окажется существенно меньше.
Широкие испытания многослойных труб в полевых условиях, в том числе и на Севере, убедительно свидетельствуют об их несомненных достоинствах и преимуществах перед трубами с монолитной стенкой.
Во многих странах мира занимаются проблемой борьбы с лавинными разрушениями. Одно из сложившихся в последнее время направлений – создание всевозможных ловушек. Они врезаются в магистраль из монолитных труб и должны, как показывает само название, поймать трещину, задержать развитие разрушения.
И для этой цели многослойная конструкция оказалась весьма эффективной. В нашем институте такие ловушки созданы. Провели на Севере натурные испытания. И убедились, что эти ловушки способны абсолютно надежно остановить лавинную трещину любого типа – и хрупкую, и вязкую. Трещина, встретив на своем пути ловушку, кольцуется в ней и останавливается.
Многослойные ловушки предполагается устанавливать в магистральных газопроводах из монолитных труб на определенном расстоянии друг от друга. Это позволит использовать и монолитные трубы, изготовленные из сравнительно дешевых сталей.
Как же практически получают трубу с многослойной стенкой?
Для этого на барабан, наружный диаметр которого выбирают равным внутреннему диаметру будущей трубы, наматывают стальную ленту толщиной 4—6 миллиметров; число витков определяют в зависимости от требуемой прочности. Например, у трубы диаметром 1420 миллиметров при давлении 75 атмосфер слоев будет 4—5, при 100 атмосферах – 4—6, при 120 атмосферах – 5—7 слоев и т. д. Закрепляют слои сваркой.
Производительность способа намотки достаточно высока, а это непременное условие для такого массового процесса, как изготовление труб.
Необходимо, чтобы длина многослойных труб была бы, как и монолитных, в пределах 12 метров, иначе их затрудительно будет перевозить по железной дороге. Ширина рулонной стали определяется возможностями станов непрерывной прокатки. К сожалению, не существует станов, которые могли бы прокатывать полосу двенадцатиметровой ширины. Поэтому приходится собирать трубу из отдельных цилиндрических заготовок – обечаек – и сваривать их друг с другом.
Для развития производства многослойных труб существенно, что станы непрерывной прокатки отличаются очень высокой производительностью и поэтому легко удовлетворят потребность в исходной заготовке. Так, стан непрерывной прокатки «2000» Череповецкого металлургического завода за год дает 6 миллионов тонн рулонной стали.
Организация массового конкурентоспособного производства многослойных труб дело непростое. Нужно создать новое оборудование, отработать все технологические операции.
С этой целью на Харцызском трубном заводе (Донецкая область) на опытном участке создали производство многослойных труб. А в конце прошлого года на Выксунском металлургическом заводе вступила в строй первая очередь первого в мире цеха, рассчитанного на 14 выпуск в год миллиона тонн таких труб. Примерно каждые четыре минуты здесь будет изготавливаться двенадцатиметровая многослойная труба большого диаметра.
Все, о чем здесь рассказано, результат большого труда научных, инженерных и производственных коллективов многих организаций страны. Вместе с Институтом электросварки имени Е. О. Патона над созданием многослойных труб, их испытанием, изготовлением технологического оборудования трудились коллективы Украинского ВНИКТИ трубной промышленности (Днепропетровск), Укргипромеза, Электростальского завода тяжелого машиностроения, ВНИИМЕТМАШа, ВНИИ строительства магистральных трубопроводов, ВНИИ природных газов и другие.
Решение проблемы создания труб с многослойной стенкой – пример революционного вклада, который может внести наша наука в реализацию важнейших народнохозяйственных программ
Проблемы и надежды (Академик Я. Колотыркин)
То, что на стыках традиционных наук, ставших уже классическими, зарождаются и начинают жить науки молодые и весьма активные, – явление нередкое. Родившись, они начинают быстро развиваться, набирать силу, получают все большее распространение в практике, позволяя обществу совершить очередной виток вверх по спирали научно-технического прогресса. Все это естественно и закономерно в извечном стремлении человечества к вершинам познания.
Рассказывает академик Яков Михайлович Колотыркин
Одной из таких относительно молодых и активных наук является и электрохимия, само название которой достаточно объясняет, между какими соседями разместилась сфера ее обитания.
Она родилась на стыке XVIII и XIX столетий и развивалась столь стремительно, что в наши дни ее с полным основанием относят к теоретически наиболее осмысленным разделам человеческих знаний. А вследствие этого теоретического богатства стало возможным чрезвычайно широкое практическое использование добытых знаний.
Сегодня с полным основанием можно сказать, что электрохимия, а точнее – продукция электрохимических производств заняла прочное место в том вещном мире, в котором мы живем. Часть этих вещей всем хорошо знакома, и люди знают, благодаря успехам какой науки стало возможно их производить. Есть вещи, также хорошо знакомые, однако не всякий задумывался над тем, каким путем удается их получать. А есть и такие, о происхождении которых знают в основном специалисты. К ним и относится продукция электрохимических производств.
Трудно предположить в наши дни, как бы обходилось человечество без электрохимии. Не появись в свое время алюминий, поднимались бы в небо современные воздушные лайнеры? Его получают электрохимическим путем. Мог бы человек выйти в космос, не имея на борту кораблей автономных солнечных батарей, сделанных электрохимиками? А подводный флот?
Но вернемся на землю. Без электрохимических источников тока не запускались бы автомобильные двигатели и радиолокаторы, не работали бы транзисторные радиоприемники и магнитофоны, не было бы всевозможных электробатарей и целого ряда изделий ширпотреба, которыми мы привыкли пользоваться! Однако это одна сторона дела, одно направление науки и прикладного ее назначения – создание источников электроэнергии. Есть и другие, не менее важные направления, о которых нам еще предстоит разговор. А пока начнем сначала.
У истоков электрохимии были такие корифеи науки, как Л. Гальвани, А. Вольта, М. Фарадей, С. Аррениус. В ее зарождении и последующем развитии громадную роль сыграли отечественные ученые. И в этой связи как не вспомнить слова великого нашего ученого М. Ломоносова, произнесенные еще за несколько десятилетий до блестящих опытов Л. Гальвани и работ А. Вольта: «Без химии путь к познанию истинной природы электричества закрыт». Удивительна была прозорливость М. Ломоносова, увидевшего в те еще далекие времена внутреннюю связь между химическими и электрическими явлениями. И другой наш соотечественник, Д. Менделеев, также обладал великой прозорливостью. Его труды, а особенно работы в области химической и гидратной теории растворов, сыграли весьма существенную роль в становлении электрохимии. Не понимая или, быть может, не желая понять их значение, некоторые ученые в свое время кинулись обвинять Д. Менделеева чуть ли не в научном консерватизме за его критическое отношение к первым работам С. Аррениуса по электрической диссоциации. Лишь спустя некоторое время академик И. Каблуков впервые, пользуясь сугубо научными аргументами, показал, что именно гидратная теория Д. Менделеева подвела базу под гениальную догадку С. Аррениуса, хотя и не обоснованную научно. Несколько позже к такому же выводу пришел В. Кистяковский. «Откуда берется огромная энергия, долженствующая способствовать разложению электролитов на ионы? – писал он. – Если принять гипотезу Аррениуса так, как она была сформулирована ее основателем, то ей неоткуда взяться».
Здесь мне придется сделать некоторое отступление и кое-что пояснить.
Дело в том, что еще химикам довольно глубокой древности было хорошо известно, что путем смешения отдельных активных веществ можно получить соединения, обладающие совершенно иными свойствами, нежели исходный материал. Им было известно и другое: добавляя определенные вещества в соединение, можно разрушить его или придать ему новые свойства. Всемогущая химия, фигурально выражаясь, покоилась на фундаменте «смешивания».
К этому следует добавить, что химические реакции протекают в зависимости от природы участвующих в них веществ и очень быстро, и очень медленно. Иногда это доли секунды, иногда – часы, месяцы и даже годы. Разумеется, химикам известны были как стимуляторы, ускоряющие процессы взаимодействия, так и антистимуляторы, то есть ингибиторы, замедляющие эти процессы. Но, повторяю, все было основано на смешивании одних веществ с другими.
И вдруг появилось электричество – совершенно новое явление, которое понять без помощи химии невозможно. Оказалось, что существуют положительные и отрицательные электрические заряды, движение которых подчиняется определенным законам, что частица химического вещества перемещается в зависимости от того, какой заряд – положительный или отрицательный – она несет. Отталкиваясь от полюса с подобным себе знаком, частица вещества быстрее или медленнее (здесь имеет значение величина полученного заряда) движется к полюсу с противоположным знаком. Так появилась возможность управлять движением заряженных частиц вещества, скоростью этого движения, регулировать направление движения. То есть там, где действовало электрическое поле, наступил определенный порядок.
Все, наверное, знают, что хромирование и никелирование выполняют электрохимическим путем, но не всем известно, что до появления электрохимии ту же работу выполняли сугубо химическим путем.
В наши дни прикладная электрохимия объединяет два очень крупных направления: проведение химических реакций при помощи электричества и получение электрической энергии за счет химических превращений. И в том и в другом направлениях работают мощные производства, давая продукцию, без которой немыслимо наше нынешнее существование, так же как и будущий прогресс.
Остановлюсь на некоторых особенностях электрохимических реакций, которые являются основополагающими как в науке, так и в практике и которые необходимо знать для того, чтобы понимать суть происходящего.
Если обычные химические реакции (окислительные или восстановительные) протекают как бы в одной фазе и зависят от переменных химической кинетики – от концентрации раствора, температуры, – то электрохимия позволила вести процесс как бы в двух стадиях. Она дала процессам новые рычаги управления, поставила их в зависимость от величины электродного потенциала, природы материала электрода и состояния его поверхности. Именно эти рычаги и позволили исследователям и технологам управлять ходом процессов: вести их в намеченном скоростном режиме, с достаточной точностью направлять движение частиц вещества. Это очень важные особенности процесса, ибо они почти полностью исключают рассеивание энергии в окружающую среду и потому являются экологически безопасными. В связи с тем, что при таких условиях энергия не рассеивается, а вся выполняет определенную работу, коэффициент полезного действия процессов исключительно высок. Кроме того, электрический ток чрезвычайно сильный окислитель и восстановитель и потому позволяет вести процессы с такой глубиной, которая недостижима сугубо химическим путем.
Такие вот особенности электрохимии и способствовали широкому использованию достижений этой науки в промышленности.
Было бы, однако, неверным полагать, что, едва родившись, новая наука сразу же стала завоевывать все новые и новые позиции. Это, конечно, не так. Долгое время исследователи шли путем проб и ошибок (кстати, это случается и сейчас), когда теоретические предпосылки далеко не стопроцентно находили подтверждение на практике, когда расчеты показывали одно, а на практике получалось другое.
Дело в том, что классическая наука не умела строить сложных моделей будущих практических процессов. Она могла с достаточной ясностью рассказать о том, что происходит в электролите, когда через него пропускают электрический ток, но она не могла объяснить, какие процессы совершаются в это же время на поверхности электродов, она не могла объяснить кинетику этих процессов. Такой теории не существовало, хотя в гипотезах недостатка не было.
Большой вклад в развитие электрохимии внесли отечественные ученые. Были сформированы мощные научные школы в Москве и Ленинграде, Свердловске и Киеве. Во главе их стали крупнейшие ученые и исследователи В. Кистяковский, П. Федотьев, А. Писаржевский, Е. Шпитальский, А. Фрумкин и О. Есин. Работы именно этих школ дали мощный импульс развитию не только отечественной, но и мировой науки. Главы школ и их многочисленные ученики и последователи сосредоточили свое внимание на ключевых проблемах теоретической электрохимии: изучении особенностей строения границы раздела металла с раствором электролита и исследовании самого механизма и кинетики электродных реакций. Без ясного понимания того, что же происходит на границе электрода и электролита, невозможно было продвижение вперед, невозможно было прогнозировать с достаточной надежностью, как будут развиваться и протекать электрохимические процессы, а следовательно, и строить надежные технологии.
В результате многочисленных исследований и экспериментов постепенно стало проясняться многое из того, чему классическая электрохимия не давала достаточного объяснения, в частности, появилась ясность в том, как протекают процессы, происходящие на границе электрода и электролита. А. Фрумкиным впервые в мировой науке было введено понятие о нулевом потенциале. Именно это понятие и явилось как бы оценочным критерием поведения электрода, раскрывало его адсорбционную и кинетическую сущность.
Нужно отметить, что развитие теории в этот период сильно затруднялось из-за несовершенства экспериментальной техники. Многое не поддавалось измерениям во время экспериментов. Приборы и аппаратура «не успевали» срабатывать, не обладали нужной чуткостью и избирательностью.
Ситуация стала меняться в самое последнее время, когда появилась перспектива использовать в этих исследованиях оптические методы: спектроскопии молекул в двойном слое, электроотражения, эллипсометрии. Это позволило перевести исследования на более тонкий уровень, получить данные о микроструктуре, начать серию экспериментов в области реально действующих систем, а не тех идеальных, с которыми имела дело классическая электрохимия.
В последние десятилетия получены важные доказательства того, что электрохимические реакции, как правило, имеют и химические стадии, которые нередко предшествуют моментам переноса заряда через поверхность раздела электрод – электролит. Химические стадии и являются определяющим фактором протекания процесса во многих случаях.
Эти и другие исследования позволили вскрыть глубинную сущность электрохимических реакций, лучше понять механизм процессов. Они еще более укрепили нашу уверенность в том, что глубоко правы были Д. Менделеев и его ученики, когда говорили, что для глубокого понимания электрохимических явлений необходимо разобраться в химической их сути, непременно ее учитывать. Сейчас можно уже с большой определенностью утверждать, что прогресс в развитии теоретической и прикладной электрохимии в ближайшее десятилетие будет идти именно в русле этого менделеевского направления.
По мере расширения и углубления наших знаний в области теории все более развивается и прикладная электрохимия. Здесь, наряду с традиционными производствами, возникают производства новые, основанные на новых знаниях. Впрочем, и традиционные технологии не остаются стабильными, они совершенствуются, приобретая новые качества.
В этой связи мне хотелось бы коснуться состояния дел в таком направлении электрохимии, как защита металлов от коррозии. Ведь именно об этом сказано в «Основных направлениях экономического и социального развития СССР на 1981 – 1985 годы и на период до 1990 года»: «Разрабатывать и внедрять высокоэффективные методы повышения прочностных свойств, коррозионной стойкости, тепло– и холодостойкости металлов и сплавов, металлических конструкций и труб...»
Благодаря целенаправленным работам советских коррозионистов удалось прояснить многие теоретические неясности, существовавшие прежде. Появилась возможность смоделировать научно обоснованные процессы, которые имеют большую практическую ценность. Электрохимическая теория коррозии вскрыла все закономерности процессов и сумела указать пути повышения сопротивляемости металлов, улучшения способов защиты. Иными словами, нам теперь совершенно ясен механизм самого явления, а это, в свою очередь, позволило найти и новые способы борьбы, создать оригинальные методы защиты.
Их используют для предотвращения коррозии газо– и нефтепроводов, подземных коммуникаций, платформ и трубопроводов морских нефтепромыслов, судов, оборудования и продуктохранилищ химических предприятий, имеющих дело с так называемыми агрессивными средами. Народное хозяйство получает громадный эффект от применения новых способов борьбы с коррозией, сберегая немалое количество металла.
Продолжая мысль о прикладном значении электрохимии, о том месте, какое она заняла в различных областях техники, мне хотелось бы сказать о некоторых основных направлениях, где хотя сделано уже многое, однако предстоит сделать еще больше. Именно здесь нужно сосредоточить в одиннадцатой и двенадцатой пятилетках основные усилия ученых. Причем решать эти задачи требуется ускоренными темпами. Ведь они определены как важнейшие в ряду проблем развития народного хозяйства. В «Основных направлениях» сказано: «...сосредоточить усилия на решении следующих важнейших проблем: ...создание химико-технологических процессов получения новых веществ и материалов с заданными свойствами, научных основ технологий комплексного использования сырья и побочных продуктов, сберегающих энергетические и трудовые ресурсы, использующих замкнутые технологические циклы».
Как решаются эти проблемы современной электрохимией, какие трудности возникают, какие успехи уже достигнуты, какие в связи с этими успехами возникают перспективы – вот об этом мне представляется полезным рассказать.