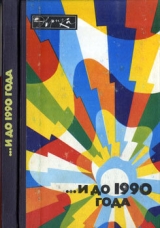
Текст книги "...И до 1990 года"
Автор книги: В. Федченко
сообщить о нарушении
Текущая страница: 7 (всего у книги 13 страниц)
Но что с того, что в ковше будет получена относительно чистая сталь, если во время транспортировки ее к месту, где находится форма, в процессе разливки она снова загрязнится от взаимодействия с газами окружающей атмосферы, огнеупорными материалами ковша, с самой формой. Даже если всего этого и удастся избежать, что, конечно, требует усложнения и, соответственно, удорожания технологического процесса, на пути получения качественной отливки встает еще один весьма опасный противник: большая скорость кристаллизации металла в изложнице, форме.
В жидком металле все его составляющие, в том числе и примеси, были распределены равномерно. Но теперь при охлаждении они затвердевают не одновременно, да и сами кристаллы образуются не сразу во всем объеме, а начинают расти от стенок формы к центру отливки. В результате металл оказывается неоднородным по химическому составу, развивается ликвация, настоящий бич литейного производства. К тому же из-за неминуемой усадки металла при затвердевании и выделении газов в нем появляются поры, раковины, пузыри Со всеми этими дефектами ведут упорную борьбу. Но устранить их полностью невозможно. И ясно, что если слиток оказывается неоднородным по составу и структуре, то неоднородным будет он и по свойствам.
Итак, классической сталелитейной технологии присущ принципиальный недостаток: операции приготовления разделены операцией заливки. К тому же требуется разливка и быстрое затвердевание довольно больших масс металла. Именно с этим и связано ухудшение свойств литого металла.
Конечно, немало случаев, когда свойства такого металла удовлетворяют технику, и поэтому соответствующие детали, изделия получают непосредственно методом литья. Но чаще всего приходится отказываться от такого прямого пути. И тогда вначале отливают слиток, а затем с помощью его ковки или прокатки стараются устранить доставшуюся от литья дурную наследственность, улучшая тем самым качество металла, главным образом его прочность. И наконец, из такой деформированной заготовки – поковки или проката – изготавливают на металлорежущих станках требуемое изделие.
Но даже этот многоступенчатый процесс, за который приходится расплачиваться весьма дорого (заметьте, ежегодно у нас только в машиностроении при обработке поковок в стружку превращается более 8 миллионов тонн металла), нередко оказывается несостоятельным перед лицом требований, выдвигаемых новой техникой. И причина этому – недостаточная чистота исходного металла.
Первыми, кто «загнал в тупик» традиционную металлургию, были атомная и реактивная техника. Именно они, переживавшие в начале 50-х годов период своего становления, предъявили к конструкционным материалам, и прежде всего к специальным сталям и сплавам на основе железа, никеля и кобальта, исключительно высокие требования. Понадобились металлы, способные в невиданных ранее условиях радиации, высоких температур, давления, в агрессивных средах обеспечить абсолютно надежную работу изготовленной из них техники. А это значило, что надо суметь выплавить почти идеально чистый металл. Способы классической металлургии оказались непригодными.
Стало ясно, что для удовлетворения особо строгих требований металл, получаемый в обычном сталеплавильном агрегате, следует подвергнуть вторичному переплаву, в процессе которого он практически бы полностью очистился от вредных примесей. И добиться этого удастся только в том случае, если будет найден способ совмещения операции получения и операции затвердевания рафинированного жидкого металла.
Ключ к решению поставленной задачи дала сварка.
Еще в конце прошлого века один из пионеров сварочной техники, Н. Славянов, изложил основные принципы дуговой плавки расходуемых электродов, обратил внимание на металлургию процесса сварки. Именно эти идеи и были использованы при создании процесса вакуумно-дугового переплава, или, как его сокращенно называют, ВДП.
Вначале этот способ применяли для изготовления слитков титана, циркония и сплавов на их основе, в которых так нуждались атомная промышленность и реактивная техника. А затем в США начали использовать и для улучшения качества специальных сталей.
В чем же сущность этого процесса? В вакуумной камере между концом расходуемого электрода – это и есть переплавляемая металлическая заготовка, полученная в обычном сталеплавильном агрегате, – и лункой жидкого металла, образующейся в водоохлаждаемой изложнице, куда собирается расплавленный металл, горит дуга. По мере расплавления электрода в кристаллизаторе наплавляется слиток переплавленного металла.
Таким образом выполняется непременное требование к технологии получения высококачественной отливки: приготовление жидкого металла и его затвердевание в виде слитка происходят в едином агрегате. При этом благодаря вакууму и направленной кристаллизации, которой обеспечивается оптимальная скорость, создаются благоприятные условия для глубокой очистки металла от примесей и образования плотной структуры.
Так идеи сварки обогатили металлургию технологией вторичного переплава, которая сыграла в тот период очень важную роль в обеспечении новой техники сплавами особо высокого качества.
Но новый процесс оказался дорогим; для его осуществления необходимы уникальные источники постоянного тока, высоковакуумные мощные насосы. Мог ли он при этом стать основным способом и для массового производства высококачественных сталей, жаропрочных сплавов, которые в несравнимо больших количествах нужны современной технике? На Западе пошли именно по пути широкого использования ВДП, ибо альтернативы такому способу просто не знали. Иначе решили эту проблему советские ученые и инженеры.
Забегая вперед, скажу, что созданная у нас технология электрошлакового переплава получила полное признание и за рубежом, в частности в США, где уже серьезно потеснила вакуумно-дуговой переплав и продолжает наступление на его позиции.
В истории открытия явления, которому суждено было стать основой целой суммы новых технологий, в том числе и электрошлакового переплава, не последнюю роль, как это уже не раз бывало в науке и технике, сыграл «его величество случай».
Произошло это в конце 40-х годов на заводе «Запорожсталь». Здесь инженеры Института электросварки имени Е. О. Патона, участвуя в восстановлении разрушенной во время войны домны, налаживали автоматическую сварку под флюсом вертикальных швов ее кожуха.
И вот однажды случилось нечто весьма странное. Погасла дуга, а сварка тем не менее не прекращалась! Сомнений в том, что плавление сварочной проволоки продолжается, быть не могло – приборы ясно показывали: в сварочной цепи идет ток. А раз так, то оставалось предположить только одно: электрический ток, проходя через жидкий шлак, нагревает его настолько, что выделяемого тепла достаточно для плавления металла. Роль дуги взял на себя шлак!
Открытие электрошлакового процесса, то есть явления генерирования теплоты в расплавленном шлаке при прохождении через него электрического тока, имело далеко идущие последствия.
Вначале был разработан бездуговой сварочный процесс, который получил название электрошлаковой сварки – ЭШС.
Эта первая ЭШ-технология, начавшая применяться для сварки толстого металла, вызвала подлинную техническую революцию в машиностроении.
Один из руководителей нашей промышленности, В. Малышев, говорил, что без электрошлаковой сварки мы не смогли бы после войны в невиданно короткие сроки не только восстановить тяжелую индустрию, но и создать могучий промышленный и оборонный потенциал нашей Родины.
Новый процесс, который за рубежом назвали «Русская сварка», был удостоен на Всемирной выставке в Брюсселе золотой медали «Гран-при». Многие страны приобрели лицензии на советское изобретение, купили аппарат для ЭШС.
Электрошлаковая сварка стала вне конкуренции при создании уникальных по массе и размерам деталей для тяжелого, энергетического и металлургического машиностроения. Именно в этих областях техники наиболее резко проявляется тенденция роста единичной мощности агрегатов. Вспомните турбогенераторы мощностью в миллион киловатт и более, домны, выплавляющие за сутки свыше 10 тысяч тонн чугуна, станы, которым под силу прокатывать стальной лист шириной более пяти метров...
Для изготовления традиционным путем подобной техники необходимы прежде всего громадные слитки, масса которых достигает нескольких сот тонн, а следовательно, нужны печи, способные выплавить такое количество металла, кроме того, мощнейшее кузнечно-прессовое оборудование, чтобы слиток превратить в поковку, огромные термические печи и другое оборудование.
Мы сказали лишь о необходимом оборудовании, но не надо забывать, что и сам процесс изготовления таких слитков, а затем поковок исключительно сложен, связан с колоссальными затратами времени и труда, и при всем этом успех далеко не всегда гарантирован.
Хотя ежегодная потребность в слитках-гигантах не столь велика – максимум несколько десятков, – на создание необходимого для их производства оборудования пришлось бы затрачивать сотни миллионов, а то и миллиардов рублей.
Да, пришлось, не будь электрошлаковой сварки, которая позволила решить задачу иным способом, никогда не применявшимся в мировой практике.
Мы предложили соединить несколько слитков относительно небольшой массы с помощью ЭШС, а затем полученную заготовку подвергнуть ковке.
Идея поначалу вызвала серьезное недоверие, и это понятно, так как никто еще сварные заготовки не подвергал ковке. Сварка всегда была лишь одной из завершающих операций. Но опасения в данном случае были напрасны. Методом электрошлаковой сварки швы получались столь высокого качества, что именно в местах соединения изделие оказывалось наиболее прочным.
Иллюстрируя вначале возможности сварки, я уже приводил пример, как новая технология позволила решить проблему изготовления вала ротора сверхмощного турбогенератора. К этому добавлю лишь, что в Советском Союзе с помощью электрошлаковой сварки изготовлены уже сотни тысяч тонн самых различных конструкций и во всех случаях без ущерба для их надежности.
Вскоре после появления электрошлаковой сварки в нашем институте занялись изучением свойств сварного шва, получаемого этим способом.
Всесторонние исследования не оставили у нас никакого сомнения в том, что электрошлаковый процесс позволяет получить металл с уникальным сочетанием свойств. Металл шва был химически однороден, прочен и одновременно пластичен, чистый и плотный, со здоровой структурой, без дефектов, его физические и механические свойства были практически одинаковыми во всех направлениях. Этот металл по всем характеристикам не только превосходил обычный литой металл (а ведь он сам был литым), но и по многим свойствам оказывался даже лучше деформированного.
Стало ясно, что электрошлаковая сварка как бы смоделировала великолепный процесс вторичного переплава, в котором так нуждалась новая техника. Теперь оставалось конструктивно оформить процесс, чтобы электрошлаковый сварной шов как таковой можно было извлечь из сварного соединения, то есть отделить от соединяемых им кромок и во много раз увеличить его массу, превратив в слиток требуемых размеров.
К 1955 году обе эти задачи удалось успешно решить. Институт электросварки имени Е. О. Патона выдал путевку в жизнь уже второй по счету электрошлаковой технологии. На сей раз электрошлаковому переплаву – ЭШП.
Родилась технология, которая несравнимо проще вакуумно-дугового переплава и при этом ничуть не уступает ему по качеству получаемого слитка.
Острая нужда в особо чистом металле, с одной стороны, а с другой – простота и эффективность электрошлакового переплава определили исключительно высокие темпы распространения новой технологии. Трудно, наверное, найти еще примеры, когда бы крупное техническое новшество столь же стремительно проделывало путь от научных экспериментов до заводских цехов, как это случилось с ЭШП. В 1956 году в Институте электросварки имени Е. О. Патона спроектировали и построили первую в мире опытно-промышленную печь для электрошлаковой выплавки слитков; в 1958 году такая печь начала работать на заводе «Днепроспецсталь» имени Н. А. Кузьмина. А еще через год здесь возник первый в мире цех ЭШП.
С этого момента фактически и начинается история новой отрасли промышленности – специальной электрометаллургии, занимающейся производством металла особо высокого качества и особо высокой надежности.
И хотя вслед за электрошлаковым переплавом в нашем институте были созданы и другие переплавные процессы, скажем, электронно-лучевой, плазменно-дуговой, которые, по сути, решают одну и ту же задачу рафинирования жидкого металла и последующей его принудительной кристаллизации, основой спецэлектро-металлургии был и остается ЭШП.
Замечательные свойства металла, получаемого электрошлаковым переплавом, стали лучшей рекламой этому методу. Наращивание мощностей ЭШП носило буквально лавинный характер. Прошло всего несколько лет – и практически на всех отечественных заводах качественной металлургии и на некоторых предприятиях цветной металлургии работали электрошлаковые печи. У нас в стране построены крупнейшие специализированные цехи, оснащенные десятками таких печей. В Советском Союзе с помощью ЭШП ежегодно производят многие сотни тысяч тонн самых различных марок стали, сплавов.
Электрошлаковый переплав получил признание во всем мире. Показательно, например, что вскоре после международной конференции сталелитейщиков, которая проходила в 1969 году в американском городе Питтсбурге, где об ЭШП советские ученые прочитали доклад, в журнале «Железный век» появилась статья под названием «Готовы вы или нет, но он здесь» с подзаголовком «Патоновский ЭШП дебютирует в США». И надо сказать (об этом я уже упоминал), что именно в США, где созданы огромные мощности по вакуумно-дуговому переплаву, наш ЭШП занял подобающее место и продолжает применяться все шире. А вообще Советский Союз продал в крупнейшие страны Запада более 20 лицензий, получил более 600 зарубежных патентов по электрошлаковой технологии и оборудованию для нее. ЭШ-печи работают во Франции, Японии, Швеции, США, Польше, Румынии, Болгарии и многих других странах.
Нас нередко спрашивают: почему вы, сварщики, занимаетесь спецэлектрометаллургией? Неужели мало у нас металлургов? Ответить на этот вопрос нетрудно.
Прежде всего надо учесть, что никто в столь большой степени не был заинтересован в получении особо чистых металлических материалов, как сварщики.
Чем чище металл, подлежащий сварке, или чем чище присадочный материал (сварочная проволока), тем выше качество сварочного шва и соединения в целом, тем меньше в металле шва и в околошовной зоне различного рода дефектов. Работоспособность и долговечность конструкций, их способность надежно противостоять сложному воздействию различных физических и химических факторов также во многом определяется степенью чистоты свариваемого металла. Вот почему сварщики раньше представителей других специальностей ощутили необходимость повышения чистоты и однородности сталей и сплавов, используемых в сварных конструкциях. И это нашло отражение в оформлении уже самых первых способов электрической дуговой сварки, изобретатели которой не обошли стороной вопросы надежной защиты зоны сварки.
Существенно и то, что сварщики располагают более мощным, чем металлурги, арсеналом средств воздействия на качество металла. Правда, оружие сварщиков отличается весьма скромными параметрами: дуга мощностью всего в несколько киловатт или десятков киловатт, шлаковая ванна, объем которой измеряется лишь несколькими кубическими сантиметрами, и т. д. и т. п. Действительно, по сравнению с современной многотонной электродуговой печью «сталеплавильный агрегат» сварщика не более чем микромир. Тем не менее здесь действуют те же факторы, проявляются те же закономерности, развиваются те же физико-химические процессы и обменные реакции, что и в агрегатах большой металлургии. Но все эти процессы, все эти реакции при сварке протекают чрезвычайно интенсивно, значительно быстрее, чем в металлургии.
При сварке плавлением действует очень своеобразный электрометаллургический агрегат, своего рода комбайн. В нем буквально в считанные секунды протекают процессы расплавления металла, раскисления или окисления и, главное, его глубокого рафинирования, а затем кристаллизации. Причем если в металлургическом производстве процессы получения жидкого металла и его последующей кристаллизации, как уже подчеркивалось, разделены обязательной операцией разливки, то при сварке оба процесса – получение жидкого металла и затвердевание его в виде слитка – совмещены в едином агрегате.
Как же осуществляется электрошлаковый переплав, благодаря каким механизмам, действующим в электрометаллургическом комбайне, получается металл высочайшего качества? Опустим, конечно, технические подробности, которых здесь немало, и расскажем лишь о главном, что составляет суть электрошлаковой технологии.
Прежде всего напомним в самых общих чертах, как происходит ЭШП.
Расходуемый металлический электрод (а это и есть металл, который предстоит переплавить), подключенный к источнику тока, погружают торцом в расплавленный электропроводный шлак. Под действием тепла, которое выделяется в нем при прохождении тока, электрод плавится и капли металла, просочившись сквозь толщу шлаковой ванны, опускаются на ее дно, образуя металлическую ванну. Все это происходит в водоохлаждаемой форме, где металл постепенно, направленно – снизу вверх – кристаллизуется. По мере оплавления электрод подается в шлаковую ванну, и благодаря этому объем жидкого металла в форме непрерывно восполняется.
Таким образом, первое и важнейшее условие, без которого немыслимо создание эффективного процесса переплава, и здесь строго выполняется: все три операции – плавление, разливка и кристаллизация металла – происходят одновременно и в одном месте.
Электрошлаковый переплав можно сравнить с театром одного актера. Действительно, здесь все роли играет шлак. А точнее – сразу пять. Он заменил электрическую дугу и служит нагревательным элементом, тепло которого, во-первых, плавит электрод, а во-вторых, обогревает кристаллизующийся металл, что улучшает структуру слитка. Шлак надежно защищает расплавленный металл от окружающей атмосферы. Еще одна его функция – образовывать на поверхности отливки тонкую корочку – гарнисаж, что в итоге также способствует формированию здоровой отливки, без рыхлости и усадочной раковины; кроме того, отливка получается с такой чистой поверхностью, что, как правило, не нужна и механическая обработка. И последняя по счету, но, конечно, не по значению, – это рафинирующая роль шлака. Ее он выполняет на всех стадиях контакта с металлом: и соприкасаясь с оплавляющимся электродом, и когда капли жидкого металла проходят через шлаковую ванну, и на ее границе с металлическим расплавом.
За считанные секунды в шлаковом «чистилище» протекают реакции рафинирования, не достигающие такой степени глубины даже за многие часы обработки расплавов в сталеплавильной печи. В чем же причина такой быстротечности металлургических процессов при электрошлаковом переплаве? Прежде всего в мелкокапельном расплавлении электрода. Именно поэтому поверхность контакта расплавленного металла со шлаком в сотни и даже тысячи раз больше, чем при традиционной выплавке стали.
При ЭШП из металла удаляются газы, неметаллические включения, вредные примеси, в числе которых и главный враг стали – сера. Например, после электрошлакового переплава конструкционных сталей общее количество примесей в них снижается в 3 раза и более. И наконец, отметим, что процесс ЭШ-переплава создает исключительно благоприятные условия для кристаллизации металла. Количество жидкого металла все время остается таким небольшим, что ликвации – самому страшному для качества отливки процессу – просто негде разыграться. А характер отвода тепла от стенок формы и непрерывное поступление сверху жидкого металла с подогревом его служат гарантией того, что отливка, которая образуется из непрерывно снизу затвердевающего металла, получается отличного качества.
О масштабах применения ЭШП в нашей стране уже говорилось. Приведу лишь несколько цифр, которые наглядно показывают, какую выгоду народному хозяйству приносит использование сверхчистого металла. Так, подшипники железнодорожных вагонов, сделанные из стали ЭШП, позволяют вдвое увеличить межремонтный пробег. Подсчитано, что на каждой тонне шарикоподшипниковой стали, выплавленной в ЭШ-печи, удается сберечь более 300 рублей. На каждом буровом долоте, сделанном из стали ЭШП, экономится за счет повышения долговечности около 100 рублей. А ведь таких долот ежегодно требуется более миллиона штук.
Одна из самых замечательных технологий, изобретенных когда-либо человеком, несомненно, литье. До гениальности простая идея – получать из жидкого металла практически без отходов сразу готовое изделие, – казалось, должна была гарантировать литью безраздельное господство. Но по мере усложнения техники, не имея возможности обеспечить нужные свойства металлу, литье все больше и больше уступало свои позиции, и прежде всего ковке. А там, где оно продолжало лидировать, во многом подрывало свою репутацию, нагромождая вокруг отливки чуть ли не такие же по весу, идущие затем в отходы литники, прибыли. С их помощью литье пыталось справиться со своими «болезнями».
Ведущая роль
Но вот появилась совершенно новая литейная технология – ЭШП, которая впервые позволила сделать то, о чем еще можно было только мечтать; получать отливки со свойствами поковки. А раз так, то стали реальными и надежды на возвращение литью утраченных позиций.
Было ясно, что для этого в процесс ЭШП, приспособленный лишь для выплавки прямоугольных и круглых слитков, необходимо внести такие технологические и конструктивные изменения, которые превратили бы его в универсальный, с точки зрения литейного производства, то есть дали бы возможность получать отливки практически любой формы.
Задача эта была успешно решена в нашем институте в 1967—1968 годах. На основе электрошлакового процесса родилась еще одна очень интересная технология – электрошлаковое литье – ЭШЛ.
С тех пор прошло немного времени, но ЭШЛ уже получило в нашей стране довольно широкое применение. Высокая технологичность, высокий коэффициент использования металла, удивительная простота оборудования и технологии делают ЭШЛ весьма перспективным. Ему не нужны плавильные печи, разливочные ковши, земляные формы и другое оборудование традиционного литья. ЭШ-отливка не имеет прибылей, литниковых систем.
Все это позволяет значительно снизить трудоемкость получения изделий, их стоимость, коренным образом улучшить условия труда. Переоценить этот социальный эффект невозможно, ведь в литейном производстве у нас занято около 700 тысяч человек.
Острота проблемы экономии материальных и трудовых ресурсов делает особенно настоятельным широкое внедрение ЭШЛ. Это связано прежде всего с тем, что при замене поковок отливками на каждой тонне готового изделия экономится более двух тонн металла, причем около половины этого количества – за счет уменьшения объема механической обработки. Нетрудно представить себе, какой это может дать эффект в масштабах страны, если учесть, что на снятие тысячи тонн стружки затрачивается труд 160 рабочих, используется 100 металлорежущих станков, расходуется более 800 тысяч киловатт электроэнергии.
Возможности ЭШЛ и области его применения крайне разнообразны. Оно эффективно при изготовлении уникальных, мелкосерийных и даже (в отдельных случаях) массовых изделий. ЭШЛ широко используется при изготовлении различной арматуры, например, запорных клапанов и задвижек для паропроводов высоких и сверхвысоких давлений тепловых и атомных электростанций, химических и нефтехимических предприятий, литых труб из стали специального состава, деталей судовых дизелей, в металлургическом машиностроении, в производстве крупногабаритных колец, фланцев, сосудов высокого давления.
Создание участков электрошлакового литья доступно сейчас в принципе любому машиностроительному предприятию. Для этого существует оборудование, отработана надежная, высокоэффективная технология, что подтверждено всем опытом применения ЭШЛ.
Необходимость внедрения практически безотходной электрошлаковой технологии подчеркивалась еще на XXV съезде КПСС, а также в специальном постановлении, принятом Советом Министров СССР в 1976 году о развитии ЭШЛ.
В прошлой пятилетке были созданы крупные мощности по электрошлаковому литью практически во всех машиностроительных министерствах. Среди новых установок ЭШЛ уникальные агрегаты для отливки заготовок полубандажей цементных печей массой до 60 тонн, для отливки деталей крупных гидропрессов массой до 80—100 тонн и другие.
Нет никаких сомнений в том, что ЭШЛ будет и дальше развиваться быстрыми темпами как альтернатива кузнечно-прессовой технологии.
Электрошлаковое литье может стать серьезным конкурентом в классической литейной технологии. Но надо решить такую важную и принципиальную задачу, как разработка простых и надежных средств принудительного заполнения литейной формы жидким металлом. Без этого трудно рассчитывать на успешное совершенствование ЭШЛ.
Одно из интересных и перспективных решений задачи, несомненно, использование методов центробежного литья.
Хорошо известны достоинства и недостатки данного способа в его классическом виде, когда в машину заливают металл обычной выплавки. При заливке во вращающуюся форму электрошлакового металла получают деталь с хорошей поверхностью, которая практически не нуждается в механической обработке, с плотной макроструктурой и высокой степенью химической однородности. В этом главное преимущество центробежного электрошлакового литья перед обычным.
Естественно, что для осуществления нового процесса необходимо уметь накапливать требуемое количество жидкого электрошлакового металла, подлежащего заливке в центробежную машину.
В течение ряда лет не удавалось найти приемлемого инженерного решения этой непростой задачи. Ведь сущность электрошлакового процесса состоит не в накоплении металла, а в его непрерывной кристаллизации, соответствующей скорости расплавления твердых электродов или заготовок. Можно сказать, что электрошлаковому процессу (как сварке и наплавке, так и переплаву и литью) прямо противопоказано накапливание жидкого металла.
Вместе с тем для ЭШЛ деталей сложной формы нужно именно накапливать металл, а уже затем сливать его в стационарную или вращающуюся форму.
Как же накапливать электрошлаковый металл?
В нашем институте предложены два варианта устройств для накопления металла, получаемого в результате электрошлакового процесса. Каждое из этих решений имеет свои достоинства и недостатки. Лишь время даст ответ на вопрос о рациональных областях их применения. Но не вызывает сомнений сам по себе факт поистине коренных изменений, которые внесет новая электрошлаковая технология в литейное производство.
Возможность накапливания практически любых объемов жидкого электрошлакового металла полностью снимет ограничения, присущие электрошлаковой плавке расходуемых электродов непосредственно в литейной форме или кристаллизаторе.
Имея жидкий электрошлаковый металл, то есть металл рафинированный, чистый, можно смело и широко использовать для получения отливок наиболее высокого качества весь современный арсенал литейной техники, а также методы прессования и штамповки жидкого металла.
Без преувеличения можно говорить о рождении принципиально новой технологии получения первоклассных отливок на стыке специальной электрометаллургии и литейного производства. Важнейшее достоинство этой технологии – ее безотходный характер, то есть практически полное отсутствие потерь металла.
Внедрение электрошлаковой технологии, ставшей суммой технологий, знаменует подлинную научно-техническую революцию в таких важнейших производствах, как металлургия, машиностроение, открывает перед ними новые, далеко еще не исчерпанные возможности.
И не исключено, что следующим шагом вперед будет использование электрошлакового процесса и в самом сталеплавильном производстве.
Из всех видов топлива самыми быстрыми темпами в Советском Союзе растет добыча газа. Ныне он занимает второе место после нефти в общем производстве топливо-энергетических ресурсов, а вместе с нею покрывает три четверти всех потребностей нашего народного хозяйства в топливе.
Стремительное развитие газовой промышленности отражает постоянное совершенствование топливно-энергетического баланса, от которого зависит вся экономика страны и в конечном счете повышение благосостояния народа.
Голубое топливо играет такую важную роль потому, что оно самый дешевый, универсальный, легко транспортируемый носитель энергии, ценное химическое сырье. Использование газа позволяет интенсифицировать и автоматизировать многие технологические процессы, повышать технико-экономические показатели и в первую очередь производительность труда, качество выпускаемой продукции. Главные потребители газа – энергетика, металлургическая, химическая и цементная промышленность, машиностроение; немало его расходуется и на коммунально-бытовые нужды.
Первый магистральный газопровод Дашава – Львов длиной 68 километров был построен в 1940—1941 годах и имел Трубы диаметром 200 миллиметров. В 1946 году по трубам диаметром 325 миллиметров саратовский газ, преодолевая расстояние в 840 километров, стал поступать в Москву. А сегодня протяженность всех артерий голубого топлива превысила 135 тысяч километров и сравнима с длиной железнодорожной сети. Создана крупнейшая в мире Единая система газоснабжения Советского Союза, которая обеспечивает газом более 4500 городов и поселков городского типа, свыше 80 тысяч сельских населенных пунктов.
За последние 15 лет значительно изменилась география добычи газа. Месторождения, расположенные в европейской части страны, не могли уже обеспечить требуемых приростов добычи газа. Роль лидера перешла к районам Западной Сибири, хотя основные потребители газа по-прежнему находятся в центре и на западе СССР. Поэтому сильно увеличилась протяженность сооружаемых газопроводов, которая нередко достигает нескольких тысяч километров.
Чтобы повысить пропускную способность магистралей, а без этого невозможно было развивать такими высокими темпами газовую индустрию, пришлось, конечно, увеличить диаметр труб и давление газа в них. Если лет десять назад большинство газовых артерий имело диаметр 720 миллиметров и давление газа в них было 56 атмосфер, то теперь диаметр увеличился почти вдвое – до 1420 миллиметров и примерно в полтора раза возросло давление – до 75 атмосфер.