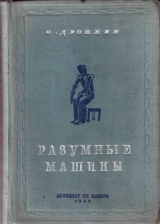
Текст книги "Разумные машины (Автоматы)"
Автор книги: Олег Дрожжин
сообщить о нарушении
Текущая страница: 14 (всего у книги 17 страниц)
Стальные стеклодувы
Сигарная машина Р. Паттерсона поражает своею сложностью и разумностью движений.
Но, пожалуй, еще более сложный вид имеют бутылочные машины Оуэна и в особенности Редферна.
Изготовление бутылок до недавнего времени производилось ручным способом. Погружая стеклодувную трубку в расплавленное стекло, мастер набирал нужное количество стеклянной массы и выдувал из нее шар. Потом шар помещался в бутылочную форму, где превращался в грубое подобие бутылки. Эту недоделанную бутылку, вынув из формы, удлиняли, держа просто на весу, и снова помещали в форму. Вдувая воздух внутрь сосуда, мастер заставлял его принять окончательный вид бутылки.
Самый искусный мастер мог изготовить таким способом в день до двухсот бутылок. При этом ему помогали еще четыре человека.

Стеклодув выдувает шар, который потом превратится в бутылку.
Работа мастера-стеклодува на бутылочном заводе относится к числу самых тяжелых, сильно подрывающих здоровье.
В конце XIX столетия в бутылочном производстве появляются первые машины: дутье легкими начинает заменяться механическим дутьем. Однако, человек продолжает играть все еще существенную роль в изготовлении бутылок.
Только в начале текущего столетия появились такие автоматы, которые смогли полностью заменить человека. Первой была машина американца Оуэна.
Десять лет труда, надежд и разочарований. Поиски средств для опытов. Лишения. Чуть не голод. Наконец, в 1907 г. мечта Оуэна воплотилась в действительность: он получил патент на машину-автомат, изготовляющую бутылки без участия человека. Немолодой уже, изобретатель от радости готов был прыгать, как пятилетний мальчик.
– Моя машина, – говорил он, – избавит бутылочников от каторжной работы и обогатит владельцев стекольных заводов. Она быстро завоюет мир!
Однако, жизнь встретила новую машину иначе, чем ожидал изобретатель. Патент Оуэна купили немецкие стекло– заводчики и… положили его под сукно, чтобы похоронить замечательное произведение изобретательской мысли. Они полагали, и нс без основания, что автоматы Оуэна, если только их пустить в работу, наделают бутылок так много, что цена на них сильно понизится и владельцы стекольных заводов, несмотря на увеличенный выпуск, не будут иметь прежних прибылей.

Бутылочная машина Оуэна (карусельный тип).
Германия таким образом была лишена возможности пользоваться машиной Оуэна. Но в США ее начал строить завод Грэхэма. Конкуренция Америки очень скоро вынудила немецких стеклозаводчиков последовать ее примеру. Однако, в Германии был организован специальный союз фабрикантов бутылок, который стал контролировать распространение машин Оуэна в Германии, стараясь, чтобы их выпускалось как можно меньше.
Все же в 1934 г. почти все бутылки в Германии были изготовлены автоматами Оуэна.
Эта машина очень похожа на карусель, деревянные лошадки которой так привлекают ребят. Места лошадок в автомате Оуэна занимают шесть одинаковых бутылочных машин. Карусель с машинами вращается возле ванной печи с расплавленным стеклом. Как только какая-либо машина – например № 1 – окажется над ванной, она выпускает трубку и набирает порцию стеклянной массы. Во время вращения машина проделывает с этой порцией стекла то же, что и живой стеклодув. К концу оборота машина спускает на конвейер совсем готовую, еще горячую бутылку. Очутившись к этому моменту над ванной, машина № 1 снова опускает в нее трубку и таким образом начинает изготовление новой бутылки. То же самое проделывают и остальные машины карусели.
Обслуживается автомат всего двумя рабочими, не имеющими квалификации стеклодува. За десятичасовой рабочий день шестикорпусный робот дает 15 000 литровых бутылок. Он заменяет работу почти четырехсот человек.
Еще более совершенную машину для изготовления бутылок сконструировал англичанин Редферн в 1930 г. Машина Редферна, подобно автомату Оуэна, тоже похожа на карусель, но устройство ее гораздо сложнее. Диаметр этой карусели – 6 м, высота – 5 м, вес ее – 40 тонн. Вся карусель состоит из пятнадцати самостоятельных машин, изготовляющих бутылки. Действует она так же, как и автомат Оуэна.
Машина Редферна может делать от полутора до шести оборотов в минуту. При наибольшей скорости вращения она изготовляет 5 400 бутылок в час и заменяет работу 1 400 человек.
Эта машина может изготовлять бутылки пятнадцати различных видов и десяти различных емкостей. Электромотор, вращающий машину, имеет всего лишь 15 лошадиных сил. Для обслуживания машины требуются два неквалифицированных человека.

Машина Вестлаке для изготовления ламповых колб (карусельный тип).
Приблизительно лет десять назад карусельный автомат Оуэна был приспособлен к производству стеклянных баллонов – колб для электрических ламп. Несколько таких автоматов установила у себя на заводе американская фирма Кернинга.
Несмотря на то, что новые машины легко давали в час 3 000 колб – 50 колб в минуту, их производительность показалась владельцам фирмы все еще недостаточной. Тогда по их заданию опытная заводская лаборатория сконструировала и построила в 1929 г. новый автомат, который стал изготовлять 20 000 ламповых колб в час – около 350 колб в минуту. Для обслуживания этого автомата требуется только три человека.
Устройство этого единственного в мире автомата фирма Кернинг держит в строжайшем секрете.
– Он побивает всех наших конкурентов. Он делает нам, если хотите, не колбы, а деньги. И мы хотим пользоваться им только сами, – заявил как-то технический директор фирмы, отказывая советским инженерам в разрешении на осмотр завода.
Было известно только, что автомат Кернинга не карусельного типа, а конвейерного. Но и этих более чем скудных сведений оказалось достаточно, чтобы возбудить творческую мысль советских изобретателей.
С 1930 г. за конструирование конвейерного автомата для выработки ламповых колб взялся наш изобретатель К. Е. Витрин, имевший до того около двадцати изобретений.

Машина советского изобретателя Витрина для изготовления ламповых колб (конвейерный тип). 1 – ванна с расплавленным стеклом; 2 – вал; 3 – вал с углублениями; 4 – углубления; 5 – стекло; 6 – порции стекла для колб; 7 – платформочки конвейера K1; К2 – второй конвейер с дутьевыми механизмами; 13 и 14 – формовочные механизмы конвейера К3; 10 – выдуваемые колбы; 17 – вращающийся диск, срезающий готовые колбы.
Большой опыт и острая изобретательская мысль дали блестящий результат – машина в течение трех-четырех лет была спроектирована. В мае 1935 г. этот автомат начали строить на опытном стеклозаводе в Рязани.
Производительность автомата, по расчетам К. Е. Витрина, будет не меньше кернинговского: он сможет выпускать в сутки полмиллиона ламповых колб – ровно в два раза больше того, что сейчас дают все наши стекольные заводы вместе взятые. Для обслуживания автомата Витрина также потребуется три человека.
Машины-комбайны
Слово «комбайн» вошло в обиход русского языка совсем недавно – лет шесть назад, когда в СССР в первый раз были ввезены сложные сельскохозяйственные хлебоуборочные машины – комбайны.
Еще совсем недавно уборка хлеба и получение из колосьев чистого зерна были делом длительным и кропотливым. Десятки женщин, вооруженных полукруглыми ножами-серпами, не разгибая спины, медленно двигались по полю, срезая охапку за охапкой золотистые стебли пшеницы и связывая их в снопы.
На скрипящих телегах перевозился убранный хлеб во дворы крестьян, где начиналась молотьба цепами. Это были длинные палки, к которым на ремнях прикреплены короткие. Взявшись за длинные палки, короткими колотили (молотили) по хлебным колосьям, выбивая из них зерно.
Заключительная часть работы состояла в отделении чистого зерна от половы и мякины. Для этого лопатой при ветре подбрасывали смесь зерна и мякины вверх. Ветер относил легкую мякину в сторону, а тяжелое зерно падало тут же на месте. Все эти операции производились крайне медленно и требовали большой затраты человеческих сил.
Комбайн полностью механизировал уборку и разделку хлеба. Он состоит из двух машин, объединенных в одно целое, – из косилки и молотилки.
Косилка, устроенная наподобие парикмахерской машинки для стрижки волос, срезает хлеб и подает его по конвейерной ленте в молотилку. Здесь бьющие механизмы и ряд колеблющихся сит отделяют зерно от соломы и половы. Чистое зерно после этого ссыпается в бункер – ящик для временного хранения, а солома и полова выбрасываются в поле. По временам к комбайну подъезжают грузовые автомобили, в которые на ходу из бункера ссыпается зерно. Автомобили доставляют обмолоченный хлеб на склады.
Большой современный комбайн заменяет пятьсот рабочих, действующих серпами и цепами.
Вместе с машинами мы взяли из Америки и обозначающее их слово «комбайн». По-английски (американцы говорят на английском языке) «combine» (читается – комбайн) значит объединять, соединять, комбинировать. Так как уборочная машина представляет собою соединение, комбинацию косилки и молотилки, то ее и назвали просто комбайном или, точнее, хлебоуборочным комбайном в отличие от других сложных комбинированных машин, которые за последние годы начинают появляться и в промышленности.
С примерами промышленных комбайнов мы уже встретились. Это были сигароделательная машина Паттерсона и бутылочные машины Оуэна и Редферна. Но ими дело не ограничивается.
В 1934 г. у нас в СССР на заводе № 1 имени Калинина в Москве была сконструирована и построена машина-комбайн для разделки рыбы.
Обычно эта работа производится вручную, требуя многих рабочих. Советская машина «ЖК» все операции механизировала. Выловленная рыба укладывается на транспортер – движущуюся ленту, – который подает ее к машине. Здесь сначала отрезается голова, потом рыба попадает в стальные руки вращающегося барабана, которые вскрывают брюшко, удаляют внутренности и обрубают плавники и хвост. На этом заканчивается разделка, и рыба поступает в ванну для промывки.
Производительность машины – 60 рыб в минуту, 3 600 в час. Счет рыбам машина ведет сама. Один такой рыборазборный комбайн заменяет не менее шестидесяти человек.
Спустившись в шахты Донецкого бассейна, мы найдем там каменноугольные комбайны, изобретение советских инженеров. Добыча угля под землею – крайне тяжелая работа. Согнув спину под нависающим сводом или лежа на боку, забойщики кайлом (киркой) вырубают угольный пласт. Другие рабочие наваливают добытый уголь на тележки, которые по рельсам отвозятся к подъемникам для доставки на поверхность.
Такой способ добычи каменного угля не мог долго сохраниться в пролетарском государстве, одна из величайших целей которого – всемерное улучшение условий труда. Центральный комитет ВКП(б) в июле 1931 г. постановил ввести самую широкую механизацию добычи угля. И в шахтах появились новейшие машины – врубовые, отбойные молотки, транспортеры, электровозы.
Но этого было мало. Партия сочла необходимым создание сложных, комбинированных машин, еще более облегчающих труд человека и повышающих производительность. И советские изобретатели, соревнуясь между собою, создали целых четыре системы интересных каменноугольных комбайнов.
В 1935 г. были построены и прошли испытания два типа комбайнов: один работы инженера Раменского и научного сотрудника Угольного института Яцких, другой механика Бахмутского.
Оба комбайна выполняют все основные операции добычи: зарубку, отбойку, навалку и доставку к конвейеру.

Угольный комбайн советских изобретателей Раменского и Яцких. 1 – башенка; 2 – горизонтальная пластина – верхний бар; 3 – нижний бар; 4 – вертикально режущая штанга; 5 – сетчатый транспортер; 6 – электромотор.
Комбайн Яцких и Раменского, названный по первым буквам их фамилий «ЯР», начал работу 24 октября 1932 г. в шахте № 12 Брянского рудоуправления, треста «Кадиев– уголь». В продолжение более чем двух лет «ЯР» действует без единой аварии. Для обслуживания комбайна требуется всего четыре человека. Вгрызаясь в угольные пласты своими стальными зубами и содрогаясь многометровым туловищем, «ЯР» заменяет ручную работу ста человек.
Менее удачной была работа комбайна Бахмутского. Опыт обнаружил в нем несколько слабых мест, над усовершенствованием которых изобретатель сейчас усиленно работает.
Остальные два комбайна еще не закончены изготовлением.
В деле создания угольных комбайнов советская изобретательская мысль идет самостоятельными путями. Капиталистический мир подобных машин не имеет.
Интереснейшие комбайны мы увидим у наших новейших доменных печей на заводах Магнитогорска, Липецка, Кузнецка, Тулы. Эти доменные печи представляют собой сооружения высотою в десятиэтажный дом. Ежесуточно в верхнее отверстие каждой домны засыпается до двухсот пятидесяти вагонов шихты, состоящей из руды, кокса и известняка, смешанных в надлежащей пропорции.
Человеческие мускулы с этой колоссальной работой справиться не могут. Тут не обойтись без машины. И наш Харьковский электромеханический завод сконструировал замечательный доменный подъемник, загружающий в домну пять поездов шихты с такою же легкостью, как домашняя хозяйка засыпает в трубу самовара полкило угля.

Щит управления шахтным подъемником, изготовленный Харьковским электромашиностроительным заводом. Вид с задней стороны.
В состав этого комбайна-подъемника входят 15 электромоторов, 14 приводов, 450 разных аппаратов и 8 станций управления. Все моторы и аппараты работают строго согласованно и в определенной последовательности, требуемой ходом завалки. Все в такой степени автоматизировано, что для обслуживания подъемника, точнее, для управления им, требуется только один человек. При ручной загрузке было бы занято около трехсот рабочих.
Такими подъемниками теперь оборудованы многие наши домны.
Не нужно думать, что комбайны могут делать только грубую работу – косить и обмолачивать хлеб, дробить и извлекать каменный уголь или отвешивать и поднимать на тридцатиметровую высоту тысячи тонн шихты. Нет, комбайны могут выполнять и тонкую работу.
На заводе американской «Вестингауз лэмп К°» имеется комбинированный автомат, полностью изготовляющий электрические лампы. Он производит все операции, за исключением только одной – навивки спиралей. При трех рабочих этот комбайн за две смены дает 60 000 ламп.
Рядом с ним расположен другой сложный автомат, который занимается исследованием и сортировкой только что изготовленных ламп. Машина сначала измеряет силу света каждой лампы в свечах и потребляемую ею мощность (количество ватт), затем высчитывает, сколько ватт приходится на одну свечу, и сравнивает результат с нормой. Если в лампе все в порядке, она пропускается дальше. Если же расход энергии на свечу превышает норму, лампа бракуется. У этого автомата находится только один рабочий.
Советский изобретатель Самородский недавно сконструировал комбайн, который делает еще более «тонкие» вещи – секундные стрелки для карманных часов. Изготовление таких стрелок вручную было очень кропотливой работой. Физически она не тяжела. Но от человека требуется большое напряжение внимания, чтобы точно приладить крохотные части.

Стрелочный комбайн советского изобретателя Самородского изготовляет секундные стрелки для карманных часов без всякого прикосновения человеческих рук.
Автомат Самородского всю работу механизировал. В одно отверстие автомата поступает латунная лента толщиной в 0,15 мм для стрелок и в другое – латунная трубочка диаметром в 0,6 мм для втулок. Комбайн штампует стрелку из ленты, выправляет ее, пробивает отверстие для втулки, в это же время отрезает втулку от трубочки, штампует цапфы у втулки, затем запрессовывает втулку в стрелку и, наконец, расчеканивает ее, чтобы она плотно держалась. На каждую из этих операций уходит только 0,3 секунды.
В минуту автомат Самородского дает двадцать пять вполне готовых секундных стрелок. Этот крохотный по размерам комбайн установлен на Первом часовом заводе в Москве и один покрывает всю потребность СССР в секундных стрелках.
Два других подобных автомата делают минутные и часовые стрелки.
Бумажная фабрика
От машин-комбайнов современная техника переходит к созданию еще более сложных сочетаний рабочих механизмов, которые превращаются уже в целые автоматические фабрики и заводы, действующие при самом незначительном участии людей.
«Примером как непрерывности производства, так и проведения автоматического принципа может служить современная писчебумажная фабрика» (Маркс, 1867 г.).
До XIX века бумага производилась исключительно ручным способом, который был известен еще древним китайцам. Бумага изготовлялась из тряпья. Вымытые и очищенные от грязи тряпки размельчались в чанах с водою до тех пор, покамест не получалась совершенно однородная жидкая каша – бумажная масса. Потом квадратным ситом с мелкой сеткой эту массу вычерпывали.

Ручной способ изготовления бумаги, применявшийся до начала XIX столетия. Слева ванна с бумажной массой. Посредине пресс. Справа рабочий собрал стопку готовых листов бумаги.
Каждая взятая порция превращается в лист бумаги. Для этого сито пошатывают из стороны в сторону для лучшего переплетения волокон и удаления воды. На сетке остается бумажная пленка. Ее осторожно снимают и кладут на стол.
Набрав стопку сырых листов бумаги, помещают ее под пресс и отжимают воду. Затем стопку разбирают и отжатые листы для окончательного удаления влаги развешивают на воздухе.
Бумажная мастерская с шестью рабочими за десятичасовой рабочий день изготовляла около 30 кг бумаги.
К концу XVIII века ручной способ изготовления бумаги стал стеснять развитие книгопечатания. Нужно было ускорить производство бумаги и одновременно понизить ее стоимость. Это можно было сделать только с помощью машин.
Первая бумагоделательная машина была создана в 1798 г. французом Луи Робертом, механиком одной из бумажных мастерских возле Парижа. В 1805 г. англичанин Брама внес в эту машину крупное усовершенствование – цилиндрические сита, при своем вращении непрерывно забирающие бумажную массу из чана.
Первая машина Роберта изготовляла бумагу в листах. Сита Брамы позволили выпускать бумагу непрерывной лентой любой длины. Это произвело революцию в бумагоделательной промышленности. Производство бумаги настолько быстро возросло, что встретилось с новым препятствием – недостатком сырья в виде тряпок.
Одно время казалось, что через эту преграду перешагнуть нельзя, что она глухой стеной ограничивает производство бумаги. Однако, давление потребностей печати – книжного и в особенности газетного дела – было столь велико, что «стена» была разрушена. В середине XIX века химия находит способы получать целлюлозу – основное вещество тряпок – из древесины. Это открыло перед бумагоделательной промышленностью неисчерпаемые возможности, так как бумагу стали производить вместо тряпок из дерева.
Уже в 60-х годах прошлого столетия, когда Маркс работал над своим гениальным трудом «Капитал», бумагоделательная машина достигла значительного совершенства.
У головного конца машины устанавливается ванна с бумажной массой, которая непрерывной струей льется на бесконечное сетчатое полотно из тонкой латунной проволоки. Полотно колеблется вправо и влево. От этого бумажная масса равномерно разливается по его поверхности. Кроме того, полотно двигается еще к отжимающим валам машины.
На сетчатом полотне бумажная масса теряет значительную часть своей воды. Дальнейшее удаление воды производится отжимными валами, между которыми проходит бумажная полоса. За отжимными следуют сушильные валы, обогреваемые изнутри паром.
Пройдя между всеми этими валами, бумажная полоса, вполне высушенная, наматывается на скалки, образуя большие катушки.

Бумагоделательная машина середины XIX столетия.
Наблюдая за работой бумажной машины, Маркс приходил в восторг от непрерывности и автоматичности ее работы.
Но машины того времени – детские игрушки по сравнению с тем, что имеется в наши дни.
Современные автоматические бумагоделательные машины, вроде установленных у нас на Балахнинской фабрике возле города Горького и в Кондопоге, – это цепь сложнейших сооружений общей длиною в 150 и более метров.
До текущего столетия бумажные машины приводились в действие паровыми двигателями. Теперь они заменяются электромоторами, число которых в одной машине достигает десятка. Все моторы работают с величайшей согласованностью, при отсутствии которой бумажная лента постоянно разрывалась бы на куски. Согласованность эта создается автоматическим регулятором.

Современная бумагоделательная машина.
В 1850 г. лучшая бумажная машина в сутки выпускала бумажную ленту метровой ширины длиною в 25 км. С валов же современных гигантов бумажная полоса шириною в 7 и даже 10 м сбегает почти со скоростью поезда – 25 км в час. В сутки получается «ленточка» длиною от Москвы до Ленинграда в 600 км и весом в 130 тонн.
Чтобы изготовить такое количество бумаги за один десятичасовой рабочий день вручную, потребовалось бы 35 000 человек. Бумагой, сделанной одной машиной за месяц, можно было бы закрыть сплошной простыней всю Москву.
Советское машиностроение овладело производством этих бумажных машин. Ленинградский завод «Имени второй пятилетки» в 1935 г. дал восемь бумагоделательных машин. Но этого нам мало, и правительство решило построить в Уфе специальный завод, который будет выпускать ежегодно двадцать бумажных машин.