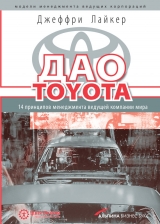
Текст книги "Дао Toyota: 14 принципов менеджмента ведущей компании мира"
Автор книги: Джеффри Лайкер
Жанры:
Деловая литература
,сообщить о нарушении
Текущая страница: 5 (всего у книги 29 страниц) [доступный отрывок для чтения: 11 страниц]
Применяя TPS, в первую очередь следует оценить производственный процесс с точки зрения потребителя. Первый вопрос в TPS всегда один: «Чего ждет от этого процесса потребитель?» (Речь идет как о внутреннем потребителе, который работает с изделием на последующих операциях производственной линии, так и о конечном, внешнем потребителе.) Таким образом определяется ценность. Посмотрев на процесс глазами потребителя, вы поймете, на каких стадиях добавляется ценность, а на каких – нет. Это применимо к любому процессу: производству, обмену информацией или обслуживанию.
Рассмотрим пример ручной сборки шасси грузовика на сборочной линии (см. рис. 3.1). Оператор производит много действий, но лишь немногие из них добавляют изделию ценность, которая важна для потребителя. В данном случае выявлено лишь три операции, которые добавляют ценность. Ряд других операций также необходим, хотя они не создают ценности. Например, оператор должен протянуть руку, чтобы взять инструмент. Задача состоит в том, чтобы на операции, которые не добавляют изделию ценность, затрачивалось как можно меньше времени. Для этого инструменты и детали должны подаваться как можно ближе к месту сборки.
Toyota выявила семь основных видов потерь – действий или затрат, не добавляющих ценности при осуществлении производственных и бизнес-процессов, которые перечислены ниже. Эти потери возможны не только на производственной линии, но и при разработке продукта, принятии заказов и в делопроизводстве. Существует и восьмой вид потерь, который я добавил к списку.
1. Перепроизводство. Производство изделий, на которые не поступало заказа, ведет к избытку запасов и порождает такие потери, как излишек рабочей силы и складских помещений, а также затраты на транспортировку.
2. Ожидание (потери времени). Рабочие, которые наблюдают за работой автоматического оборудования, простаивают в ожидании очередной рабочей операции, инструмента, деталей и т. д. или просто сидят без работы из-за отсутствия деталей, задержек в ходе обработки, простоя оборудования и нехватки мощностей.
3. Лишняя транспортировка или перемещение. Перемещение незавершенного производства на большие расстояния, порождающее неэффективность при транспортировке, а также перемещение материалов, деталей и готовых изделий на склад и со склада.
4. Излишняя обработка. Ненужные операции при обработке деталей. Неэффективная обработка из-за низкого качества инструмента или непродуманного конструктивного решения, которая влечет за собой лишние движения и ведет к появлению дефектов. Потери, вызванные завышенными требованиями к качеству.
5. Избыток запасов. Избыток сырья, незавершенного производства или готовых изделий увеличивает время выполнения заказа, вызывает моральное старение продукции, ведет к повреждению готовых изделий, затратам на транспортировку и хранение, задержкам и проволочкам. Кроме того, избыток запасов мешает выявлению таких проблем, как несбалансированность производства, задержки поставок, дефекты, простои оборудования и длительная переналадка.
6. Лишние движения. Все лишние движения, которые приходится делать сотрудникам в процессе работы: поиски того, что нужно, необходимость тянуться за инструментами, деталями и т. п. или заниматься их укладкой. Сюда же относится ходьба.
7. Дефекты. Производство дефектных деталей и исправление дефектов. Ремонт, переделка, отходы, замена продукции и ее проверка ведут к потере времени и сил.
8. Нереализованный творческий потенциал сотрудников. Потери времени, идей, навыков, возможностей усовершенствования и приобретения опыта из-за невнимательного отношения к сотрудникам, которых вам некогда выслушать.
Тайити Óно считал основным видом потерь перепроизводство, поскольку именно оно порождает большую часть остальных потерь. Если компания на любой стадии производственного процесса изготавливает больше изделий, чем нужно потребителю, это неизбежно ведет к избыточным запасам на последующих стадиях производства: детали лежат и ждут очередного этапа обработки. Приверженцы массового или крупносерийного производства могут спросить: «Ну и в чем проблема? Пусть люди и оборудование делают свое дело, производят детали». Проблема в том, что избыток запасов, которые скапливаются, ожидая следующей стадии обработки, влияет на поведение сотрудника, у которого исчезает стимул к постоянному совершенствованию. Зачем беспокоиться о профилактическом обслуживании оборудования, если его простой не приводит к нарушению процесса сборки? Зачем переживать из-за небольших отклонений качества, если дефектные детали отправляются в общую кучу? А когда дефектная деталь наконец поступит на следующую операцию, где рабочий попытается использовать ее при сборке, обнаружится, что негодные детали производятся уже несколько недель, но об этом никто не знал, ведь они дожидаются своего часа уже давным-давно[9 – Концепция работы, добавляющей и не добавляющей ценность, хорошо изложена в книге: Джеймс П. Вумек, Дэниел Т. Джонс. Бережливое производство: как избавиться от потерь и добиться процветания вашей компании. – М.: Альпина Бизнес Букс, 2004. Авторы вводят понятие потока создания ценности – концепцию, которая представляет собой квинтэссенцию бережливого мышления применительно к производственной системе Toyota.].
На рис. 3.2 эти потери представлены на простой координате времени для процесса литья, механообработки и сборки. При традиционном технологическом цикле бо́льшая часть времени, затраченного на обработку материала, представляет собой потери. Эта диаграмма знакома всем, кто участвовал в семинарах по бережливому производству или TPS, и я не буду тратить время на подробные комментарии. С точки зрения бережливого производства сначала следует составить карту потока создания ценности в соответствии с траекторией перемещения материала (информации) в ходе интересующего вас процесса. Чтобы получить полное представление, лучше всего пройти маршрут самому. Составьте схему такого перемещения и подсчитайте время и расстояние, и вы получите схему, которая называется «диаграммой спагетти». Даже те, кто бо́льшую часть жизни проработал на производстве, поражаются полученным результатам. На рис. 3.2 видно, что мы растягиваем очень простые процессы обработки изделия до такой степени, что выявление операций, добавляющих ценность, становится непростым делом.
Я нашел поразительный пример, подтверждающий вышеописанное, когда работал консультантом в компании, которая производила стальные гайки. Участники семинара – инженеры и менеджеры – уверяли, что их компании бережливое производство ничего не даст, слишком уж прост процесс. Рулонная сталь нарезается на куски, в них пробиваются отверстия, после чего заготовки проходят термообработку и укладываются в коробки. Заготовки обрабатываются на станках-автоматах со скоростью сотни гаек в минуту. Когда мы проследили за потоком создания ценности (а значит, и за операциями, в ходе которых не создавалась добавленная ценность), стало понятно, что заявление сотрудников компании звучит просто смехотворно. Мы начали с площадки приема грузов, и каждый раз, когда казалось, что процесс уже завершен, приходилось вновь обходить весь завод, чтобы добраться туда, где проходила очередная стадия обработки. В какой-то момент гайки на несколько недель увозили с завода для термообработки, поскольку по подсчетам руководства заключить контракт на эту работу было выгоднее, чем обрабатывать гайки самостоятельно. В конце концов, оказалось, что процесс изготовления гаек затягивается на недели, а то и на месяцы. При этом большинство технологических операций занимает несколько секунд, за исключением термообработки, которая проводится в течение нескольких часов. Мы подсчитали долю времени, которое затрачивается на создание добавленной ценности, для разных видов продукции и получили показатели от 0,008 % до 2–3 %. У всех округлились глаза! При этом оборудование часто простаивало, станки работали вхолостую, а вокруг громоздились залежи заготовок. Какой-то сообразительный менеджер решил, что заключить контракт на техническое обслуживание с другим предприятием дешевле, чем нанимать людей на полный рабочий день. Таким образом, когда станок ломался, починить его часто было некому, не говоря уже о профилактическом обслуживании. В результате ради эффективности на одном участке поток создания ценности замедлялся и растягивался из-за незавершенного производства, запасов готовых изделий и времени, затраченного на выявление проблем (дефектов), снижающих качество. В итоге предприятию не хватало гибкости для удовлетворения изменяющихся требований потребителя.
Совершенствование процесса: традиционный подход и подход с точки зрения бережливого производства
При традиционном подходе к совершенствованию процесса учитывается прежде всего локальная эффективность – «посмотри на оборудование, на операции, добавляющие ценность, и сделай период безотказной работы длиннее, рабочий цикл короче, а где можно – замени человека автоматом». В результате эффективность отдельной операции возрастает, но это не оказывает ощутимого влияния на поток создания ценности в целом. Важно помнить, что большинство процессов включает очень незначительное число операций, добавляющих ценность, и совершенствование только этих операций не играет решающей роли. Проанализировав процесс с точки зрения бережливого производства, мы увидим огромные резервы, которые можно использовать, устраняя потери и свертывая этапы, не добавляющие ценность.
Если перестраивать производство с точки зрения бережливого мышления, основной потенциал совершенствования – устранение огромного числа операций, где не создается добавленная ценность. При этом время, которое затрачивается на создание добавленной ценности, также сокращается. Это будет видно, если взять процесс, подобный изготовлению гаек, и создать ячейку, работающую по принципу потока единичных изделий.
В бережливом производстве ячейка представляет собой совокупность людей и станков или рабочих мест, организованных и действующих в соответствии с последовательностью технологических операций. Ячейки создаются для обеспечения потока единичных изделий (услуг), которые одно за другим проходят различные технологические операции, например сварку, сборку, упаковку. Скорость такой обработки определяется нуждами потребителя, которого нельзя заставлять ждать.
Вернемся к примеру с производством гаек. Если мы создадим ячейку, где операции выполняются в линейной последовательности, и будем передавать одну гайку или небольшие их партии от одного оператора к другому в потоке единичных изделий, в этом случае то, на что уходили недели, можно будет сделать за несколько часов. Этот пример не является необычным. Компании по всему миру вновь и вновь демонстрируют, какие чудеса творит поток единичных изделий: растет производительность, повышается качество, уменьшается объем запасов, высвобождаются площади, время выполнения заказов сокращается. Каждый раз результаты превосходят все ожидания, и каждый раз это кажется чудом. Именно поэтому ячейка, работающая по принципу потока единичных изделий, – основа основ бережливого производства. Он позволил Toyota устранить бо́льшую часть потерь всех восьми видов.
На практике конечной целью бережливого производства является организация потока единичных изделий применительно ко всем видам работ, будь то проектирование, прием заказов или само производство. Все, кто на собственном опыте узнал, какие возможности открывает философия бережливого производства, становятся его горячими приверженцами и стремятся избавить от потерь всю окружающую действительность, применяя этот принцип к каждому процессу – от управления до технологии. Однако необходимо помнить, что, так же как и любой другой инструмент или процесс, подобные ячейки следует использовать с умом. Представьте, что завод по производству гаек создал ячейку для нарезки стали и пробивания отверстий в заготовках. Для этого завод приобрел дорогое компьютеризированное оборудование, которое постоянно ломается. Это приводит к простоям и потерям рабочего времени. При этом гайки по-прежнему увозят с завода для термообработки, и прежде, чем они вернутся, проходят недели. Повсюду, как и раньше, лежат запасы. Цеховые рабочие, видя колоссальные потери, смеются над такой «бережливой ячейкой», которая не имеет ничего общего с принципами бережливого производства.
Схема «Дом TPS»: целостная структура, а не совокупность приемов и методов
Десятки лет Toyota успешно применяла и совершенствовала TPS, не документируя теорию своей производственной системы. Рабочие и менеджеры постоянно осваивали новые методы и совершенствовали старые, применяя их на практике. В пределах относительно небольшой фирмы был хорошо налажен обмен информацией, поэтому о лучших методах и системах быстро узнавали на других заводах, а затем и на предприятиях-поставщиках. По мере того как методики Toyota продолжали совершенствоваться, становилось понятно, что перед Toyota всегда будет стоять задача обучения поставщиков. Поэтому Фудзио Тё, ученик Тайити Óно, разработал простую схему в виде дома.
Схема «Дом TPS» (см. рис. 3.3) широко известна тем, кто занимается производством. Почему именно дом? Потому что дом – это целостная структура. Чтобы дом был крепким и прочным, должны быть крепки и прочны крыша, опоры и фундамент. Слабое звено может разрушить всю систему. Существуют разные версии этой схемы, но основные принципы неизменны. Сначала цели: отличное качество, низкие затраты и предельно короткое время выполнения заказа, – это крыша. Затем идут две внешние опоры: система «точно вовремя», которая является самым известным атрибутом TPS, и дзидока, цель которой – не допустить передачи дефектных деталей на следующую стадию процесса и освободить людей от машин, то есть обеспечить автоматизацию с человеческим интеллектом. В центре системы – люди. И наконец, составляющие, которые являются фундаментом: стандартизированные, стабильные и надежные процессы и хейдзунка, то есть такой производственный график, при котором колебания объемов и ассортимента будут минимальными. Сбалансированный график хейдзунка поддерживает стабильность системы, помогая свести запасы к минимуму. Резкие всплески производства одного вида продукции за счет исключения из ассортимента других изделий приведут к дефициту деталей либо потребуют создания значительных запасов.
Каждый элемент дома важен сам по себе, но еще важнее взаимосвязь между ними. Система «точно вовремя» сводит к минимуму запасы, что позволяет устранить многие проблемы в процессе производства. Поток единичных изделий обеспечивает последовательное изготовление изделий со скоростью, соответствующей запросам потребителя. Сведение запасов к минимуму означает, что дефекты качества выявляются немедленно. Этому способствует метод дзидока, который позволяет остановить производственный процесс. Чтобы возобновить производство, рабочие должны незамедлительно решить проблему. Фундаментом дома служит стабильность. Казалось бы, работа при минимальных запасах и возможность остановить производство порождают нестабильность. Но такая система заставляет рабочих принимать срочные меры. При массовом производстве, если станок остановился, спешить некуда: придет время, и его починит отдел технического обслуживания, а между тем производство идет своим чередом, используя резервный запас деталей. При бережливом производстве, если оператору необходимо остановить оборудование для решения проблемы, один за другим останавливаются остальные участки, и положение становится критическим. Поэтому все участники процесса стремятся как можно быстрее совместными усилиями решить проблему, чтобы снова запустить оборудование. Если проблема повторяется, менеджмент делает вывод о том, что ситуация критическая и, возможно, настало время уделить внимание системе всеобщего ухода за оборудованием (или всеобщей эксплуатационной системе, TPM – Total Productive Maintenance), чтобы научить сотрудников чистить, проверять и обслуживать оборудование. Для того чтобы такая система работала бесперебойно, требуется высокий уровень стабильности. В центре дома – люди, поскольку добиться необходимой стабильности можно лишь благодаря их неустанному совершенствованию. Людей следует обучить замечать потери и выявлять первопричины проблем. Отыскать первоисточник проблемы помогает метод многократной постановки вопроса «Почему?». С проблемой следует разбираться на месте, увидев ситуацию своими глазами (генти генбуцу).
В некоторых версиях этой модели фундамент включает ряд других принципов подхода Toyota, например уважение к человеку. В перечень целей сама Toyota обычно включает лишь затраты, качество и дисциплину поставок, но на самом деле на предприятиях компании в Японии практикуется более широкий подход к целям (качество, затраты, дисциплина поставки, безопасность, моральный дух) с некоторыми вариациями. Toyota никогда не жертвует безопасностью рабочих ради производства. У нее просто нет такой необходимости, поскольку устранение потерь не имеет ничего общего с созданием стрессовых условий и не угрожает безопасности. Вот что писал об этом Óно[10 – Из неопубликованного внутреннего документа Toyota «High Quality with Safety: Kanban and Just-in-Time» («Высокое качество и безопасность: канбан и система „точно вовремя“»), Тайити Óно.]:
Разумеется, нас интересует любой метод, который позволяет сократить количество человеко-часов на производстве, а значит, сократить затраты, но основой основ для нас является безопасность. Порой усовершенствование не учитывает требований безопасности. В таком случае надо вернуться на исходные рубежи и еще раз обдумать поставленную задачу. Бездействие недопустимо. Поставь задачу по-иному и иди вперед.
Заключение
TPS не просто совокупность инструментов бережливого производства. Все элементы этой сложной системы: система «точно вовремя», ячейки, система «5S» (сортируйте, соблюдайте порядок, содержите в чистоте, стандартизируйте, совершенствуйте[11 – Существуют разные переводы термина «5S» на русский язык, и предлагаемый – один из возможных. Многообразие мнений вызвано, во-первых, различием в интерпретации термина на русском языке и, во-вторых, разными трактовками, принятыми в японских компаниях. Термин «сицуке» (пятое S) здесь было решено переводить как «совершенствуй», руководствуясь как смыслом, который вкладывают в него японцы, так и стремлением сохранить первую букву «С». Смысл сицуке – неуклонно обучать других применению первых четырех S, а также не останавливаться на достигнутом и заниматься совершенствованием первых четырех S. В русской литературе широко распространен другой перевод – «дисциплина»). – Прим. науч. ред.] – инструменты, о которых рассказывается в главе 13), канбан и т. п., – функционируют как части единого целого. Основная задача системы – побудить людей постоянно совершенствовать процесс работы. К сожалению, многие книги о бережливом производстве вводят читателя в заблуждение, описывая TPS как совокупность инструментов для повышения эффективности работы. Задача использования этих инструментов упускается из виду, как и то, что центром системы являются люди. В более широком плане TPS – это применение на практике подхода Toyota. Основное внимание концентрируется на уровне цеха, но принципы этого подхода гораздо шире и применяются не только на производстве, но и при проектировании и оказании услуг.
В следующей главе мы рассмотрим 14 принципов подхода Toyota. Это фундамент культуры Toyota, и именно им посвящена бо́льшая часть этой книги. В главах 5 и 6 мы увидим, как работали эти принципы в процессе создания Lexus и Prius. Вы узнаете, с какими трудностями столкнулась Toyota и как она их преодолевала.
Глава 4
14 принципов дао Toyota: квинтэссенция производственной культуры, лежащей в основе TPS
С момента основания Toyota наш основной принцип – приносить пользу обществу, производя продукты и услуги высокого качества. Практика ведения бизнеса на основе этого принципа сформировала ценности, убеждения и методы работы, которые позволили нам добиться конкурентного преимущества. Совокупность этих методов работы и ценностных ориентаций менеджмента и представляет собой подход Toyota.
Фудзио Тё, президент Toyota (The Toyota Way, 2001)
Подход Toyota – не только инструменты и технологии
Итак, вы ввели у себя систему канбан. (Канбан по-японски – «бирка», «карточка», «квитанция» или «сигнал». Так называется инструмент управления потоком и производством изделий в системе «вытягивания», принятой в Toyota.) Вы подключили андон, устройство для визуального контроля производственной зоны, которое предупреждает рабочих о дефектах, нарушениях в работе оборудования или иных проблемах с помощью световых, звуковых и тому подобных сигналов. Теперь ваши рабочие места выглядят как на заводе Toyota. Но постепенно все возвращается на круги своя, и работа снова идет, как прежде. Вы вызываете консультанта по производственной системе Toyota, который неодобрительно качает головой. В чем же дело?
На самом деле основная работа по внедрению бережливого производства только начинается. Ваши рабочие понятия не имеют о производственной культуре, которая стоит за TPS. Они не готовы неустанно работать над совершенствованием системы и заниматься самосовершенствованием. Дао Toyota существует в первую очередь благодаря людям, которые работают, общаются между собой, принимают решения и развиваются, совершенствуя друг друга и самих себя. Если посмотреть на преуспевающие японские компании, которые работают по системе бережливого производства, сразу заметно, как активно рабочие вносят предложения по усовершенствованию. Но подход Toyota не ограничивается и этим: при этом подходе поощряется, поддерживается и требуется участие всех.
Чем больше я изучал TPS и проникался дао Toyota, тем лучше я понимал, что это система, которая обеспечивает людей инструментами для непрерывного совершенствования своей работы. Дао Toyota – это доверие к людям. Это своего рода культура, а не совокупность приемов и методов совершенствования и повышения эффективности. Сокращать объем запасов, выявлять и решать скрытые проблемы можно лишь с помощью рабочих. Если они недостаточно ответственны, не понимают стоящей перед ними задачи и не умеют работать в команде, начнутся простои и накопление запасов. Изо дня в день инженеры, квалифицированные рабочие, специалисты по качеству, поставщики, руководители групп и, главное, операторы постоянно занимаются решением проблем, и это позволяет каждому научиться решать их.
Один из инструментов бережливого производства, который учит работать в команде, называется 5S (сортируй, соблюдай порядок, содержи в чистоте, стандартизируй, совершенствуй; подробнее о нем рассказывается в главе 13). Речь идет о комплексе мероприятий по устранению потерь, которые ведут к ошибкам, дефектам и травмам. Самой трудной составляющей 5S является, пожалуй, пятая – «совершенствуй» (стимулируй, поддерживай самодисциплину. – Прим. науч. ред.). Именно этот пункт является решающим условием успеха остальных четырех. Поддержание немыслимо без соответствующего образования и уровня подготовки, а чтобы рабочие соблюдали правила эксплуатации и совершенствовали методы работы и свое рабочее место, их нужно поощрять. Условиями успеха в достижении поставленных целей являются приверженность руководства данным подходам, соответствующая подготовка кадров и производственная культура. Лишь тогда поддержание и совершенствование станут привычным делом для всех, начиная с цеховых рабочих и заканчивая руководством.
В этой главе дается краткий обзор 14 принципов, составляющих подход Toyota. Принципы сгруппированы в четыре категории:
1, философия долгосрочной перспективы;
2, правильный процесс дает правильные результаты (речь идет об использовании ряда инструментов TPS);
3, добавляй ценность организации, развивая своих сотрудников и партнеров;
4, постоянное решение фундаментальных проблем стимулирует непрерывное обучение.
Вторая часть книги также построена с учетом этих четырех категорий, которые в совокупности представляют собой четырехкомпонентную модель дао Toyota, представленную в главе 1. В последующих двух главах я покажу, как работали эти 14 принципов при создании автомобилей Lexus и Prius. Если же вам захочется, забежав вперед, детально ознакомиться с 14 принципами, вы можете прямо сейчас перейти к главе 7. Однако я настоятельно рекомендую вам сначала прочесть то, что изложено ниже.
Можно использовать целый набор инструментов TPS, но при этом следовать лишь некоторым отобранным принципам подхода Toyota. Так вам, вероятно, удастся на какое-то время улучшить показатели эффективности, но эти результаты будут недолговечными. Но если компания, внедряя TPS, соблюдает все принципы подхода Toyota, она обязательно добьется устойчивых конкурентных преимуществ.
Когда я вел курс по бережливому производству, я часто слышал вопрос: «Как применить TPS в моей организации? Мы не занимаемся массовым производством автомобилей; мы изготавливаем мелкие партии изделий по индивидуальным заказам» или: «Мы работаем в сфере обслуживания, поэтому TPS не для нас». Такие рассуждения говорят о том, что люди не понимают главного. Сущность бережливого производства не в том, чтобы копировать инструменты Toyota, разработанные для конкретного производственного процесса. Бережливое производство означает, что нужно разработать принципы работы именно вашей организации и придерживаться их, эффективно создавая добавленную ценность для потребителей и общества. Так ваша компания сможет стать рентабельной и конкурентоспособной. Принципы дао Toyota представляют собой отправную точку. Toyota применяет их не только на сборочных линиях для серийного производства. В следующей главе мы увидим, как некоторые из этих принципов применяются в структурах, которые занимаются оказанием услуг по разработке продукции Toyota.
Краткая характеристика 14 принципов дао Toyota
Раздел I. Философия долгосрочной перспективы
Принцип 1. Принимай управленческие решения с учетом долгосрочной перспективы, даже если это наносит ущерб краткосрочным финансовым целям.
• Используй системный и стратегический подходы при постановке целей, причем все оперативные решения должны быть подчинены такому подходу. Осознай свое место в истории компании и старайся вывести ее на более высокий уровень. Работай над организацией, совершенствуй и перестраивай ее, двигаясь к главной цели, которая важнее, чем получение прибыли. Концептуальное понимание своего предназначения – фундамент всех остальных принципов.
• Твоя основная задача – создавать ценность для потребителя, общества и экономики. Оценивая любой вид деятельности в компании, учитывай, решает ли она эту задачу.
• Будь ответственным. Стремись управлять своей судьбой. Верь в свои силы и способности. Отвечай за то, что делаешь, поддерживай и совершенствуй навыки, которые позволяют тебе производить добавленную ценность.
Раздел II. Правильный процесс дает правильные результаты
Принцип 2. Процесс в виде непрерывного потока способствует выявлению проблем.
• Перестрой технологический процесс так, чтобы создать непрерывный поток, эффективно обеспечивающий добавление ценности. Сократи до минимума время, которое незавершенная работа находится без движения.
• Создавай поток движения изделий или информации и налаживай связи между процессами и людьми, чтобы любая проблема выявлялась немедленно.
• Этот поток должен стать частью организационной культуры, понятной для всех. Это ключ к непрерывному совершенствованию и развитию людей.
Принцип 3. Используй систему вытягивания, чтобы избежать перепроизводства.
• Сделай так, чтобы внутренний потребитель, который принимает твою работу, получил то, что ему требуется, в нужное время и в нужном количестве. Основной принцип: при системе «точно вовремя» запас изделий должен пополняться только по мере их потребления.
• Сведи к минимуму незавершенное производство и складирование запасов. Держи в запасе небольшое число изделий и пополняй эти запасы по мере того, как их забирает потребитель.
• Будь восприимчив к ежедневным колебаниям потребительского спроса, которые дают больше информации, чем компьютерные системы и графики. Это поможет избежать потерь при скоплении лишних запасов.
Принцип 4. Распределяй объем работ равномерно (хейдзунка): работай как черепаха, а не как заяц.
• Устранение потерь – лишь одно из трех условий успеха бережливого производства. Устранение перегрузки людей и оборудования и сглаживание неравномерности графика производства не менее важны. Этого часто не понимают в компаниях, которые пытаются применять принципы бережливого производства.
• Работай над равномерным распределением нагрузки во всех процессах, связанных с производством и обслуживанием. Такова альтернатива чередованию авралов и простоев, характерных для массового производства.
Принцип 5. Сделай остановку производства с целью решения проблем частью производственной культуры, если того требует качество.
• Качество для потребителя определяет твое ценностное предложение.
• Используй все доступные современные методы обеспечения качества.
• Создавай оборудование, которое способно самостоятельно распознавать проблемы и останавливаться при их выявлении. Разработай визуальную систему извещения лидера команды и ее членов о том, что машина или процесс требуют их внимания. Дзидока (машины с элементами человеческого интеллекта) – фундамент для «встраивания» качества.
• Позаботься о том, чтобы в организации существовала система поддержки, готовая к оперативному решению проблем и принятию корректирующих действий.
• Принцип остановки или замедления процесса должен обеспечивать получение необходимого качества «с первого раза» и стать неотъемлемой частью производственной культуры компании. Это повысит производительность процессов в перспективе.
Принцип 6. Стандартные задачи – основа непрерывного совершенствования и делегирования полномочий сотрудникам.
• Используй стабильные, воспроизводимые методы работы, это позволит сделать результат более предсказуемым, повысит слаженность работы, а выход продукции будет более равномерным. Это основа потока и вытягивания.
• Фиксируй накопленные знания о процессе, стандартизируя лучшие на данный момент методы. Не препятствуй творческому самовыражению, направленному на повышение стандарта; закрепляй достигнутое новым стандартом. Тогда опыт, накопленный одним сотрудником, можно передать тому, кто придет ему на смену.