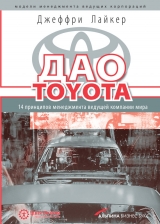
Текст книги "Дао Toyota: 14 принципов менеджмента ведущей компании мира"
Автор книги: Джеффри Лайкер
Жанры:
Деловая литература
,сообщить о нарушении
Текущая страница: 11 (всего у книги 29 страниц) [доступный отрывок для чтения: 11 страниц]
Многие компании и их подразделения, которые занимаются обслуживанием, работают в соответствии с собственным внутренним графиком. Этот график составлен так, как удобно им. Производя детали, товары и услуги в соответствии с собственным графиком или планом, они выталкивают продукцию потребителю, которому приходится накапливать запасы.
Как вам уже известно, подход Toyota не предусматривает управления запасами, он нацелен на их устранение. С самого начала Toyota ориентировалась на систему вытягивания запасов с учетом текущего потребительского спроса, предпочитая ее системе выталкивания, которая пытается предугадать спрос. Вытягивание в подходе Toyota – это идеальное состояние производства «точно вовремя»: давать потребителю (который может пониматься как очередная стадия производственного процесса) то, что нужно, когда нужно и в нужном количестве. Вытягивание в чистом виде – это поток единичных изделий, о котором рассказывалось в главе 8. Если вы принимаете заказ потребителя и изготавливаете одно изделие в соответствии с этим заказом, используя при этом ячейку для потока единичных изделий, – это будет самая бережливая система на свете. Иными словами, ее функционирование на 100 % обслуживает спрос при нулевых запасах. Но поскольку поточный процесс, который превращает сырье в готовый продукт, не может проходить без помех, без некоторого количества запасов не обойтись. Как мы узнаем в главе 10, равномерное распределение нагрузки иногда вызывает необходимость в определенном количестве запасов готовой продукции.
Интернет-служба, которую мы привели в качестве примера, не является системой с нулевыми запасами. Здесь имеются запасы, которые называют буферными. Усовершенствованная интернет-служба просит вас сообщить, когда вы приступили к использованию очередной единицы продукции, чтобы компания могла пополнить ваши запасы. Она поставляет вам то, что вы взяли. По такому методу работает большинство супермаркетов. Супермаркеты фактически представляют собой склады, но работают они особым образом. На полках лежит строго определенное количество запасов с учетом прошлого и прогнозируемого покупательского спроса. Потребители приходят и берут с полок нужные продукты. Служащий супермаркета периодически проверяет, что взято с полок, и пополняет запас продуктов. Он не просто набивает полки запасами и заказывает продукты напрямую у производителя, чтобы потом разложить их на полках. Служащий отправляется на склад супермаркета, где находится небольшое контролируемое количество запасов, которые пополняются по мере расходования. Супермаркеты, в которых работа налажена должным образом, – пример системы вытягивания. Да, здесь есть резервный запас, но вместо пополнения этих запасов в форме выталкивания по графику здесь просто следят за тем, что требуется потребителю, и пополняют запасы, не давая им иссякнуть. TPS тоже не является системой с нулевыми запасами. Она работает с ограниченным резервом материалов, и этот резерв пополняется по системе вытягивания.
Принцип – вытягивание потребителем и пополнение
В 1950-е годы Тайити Óно и его коллеги были потрясены, увидев, какую важную роль играют супермаркеты в повседневной жизни американцев. Эта система заинтересовала розничных торговцев в Японии, и они взяли ее на вооружение, а Óно продолжал заниматься ее изучением.
Хотя с самого начала Óно признавал во многих случаях необходимость запасов, чтобы поток шел без сбоев, он видел, что работа участков, которые производят изделия по графику и выталкивают их дальше, ведет к перепроизводству и создает огромные залежи запасов. При системе выталкивания производство товаров ведется по заранее составленному плану (графику), а это значит, что заказы на изготовление продукции и заказы на поставку определяются ожидаемым потребительским спросом. Производство, невзирая ни на что, работает по графику, и это ведет к потерям. Но спрос потребителя может внезапно измениться, и все пойдет не так, как планировалось. Что же дает такой график?
При массовом производстве бо́льшая часть подразделений старается свести переналадку оборудования, которая необходима для изготовления разных видов продукции, к минимуму. Это ведет к тому, что участок старается изготовить максимальный объем однородных изделий в начале недели, прежде чем понадобится переналадка. Поскольку каждый участок в течение недели строит свою работу как ему удобно, какая-либо координация их действий отсутствует. Чтобы следующий в технологической цепочке участок не остался без работы, необходим буферный запас. Таким образом, каждый из участков работает по собственному графику независимо от остальных, выталкивая материал в буферный запас.
В качестве компромисса между идеальным потоком единичных изделий и выталкиванием Óно решил создать небольшие запасы деталей между операциями и контролировать их объем. Когда потребитель забирает некоторое количество единиц, запас пополняется. Пока потребитель не использовал определенное изделие, оно лежит в запасе и пополнения запаса не происходит. Перепроизводство не выходит за пределы ограниченного количества изделий на полке, а между запросами потребителя и объемом производства устанавливается тесная связь. Но поскольку некоторые предприятия были очень большими, а поставщики деталей находились далеко, Óно нужна была сигнальная система, которая давала бы знать, что сборочная линия использовала имеющиеся детали и нуждается в пополнении запаса. В качестве таких сигналов он использовал очень простые средства: карточки и пустые контейнеры, которые назывались канбан. «Канбан» имеет много значений: знак, карточка, бирка, дверная табличка, плакат, доска объявлений, – а в более широком смысле обозначает какой-либо сигнал. Если к вам вернулся пустой контейнер – канбан, – это сигнал, что его нужно вновь наполнить определенным количеством деталей или же послать карточку обратно с подробной информацией о детали и ее местонахождении. Такая система работы Toyota получила название «система канбан», и ее назначение – управлять потоком материала, обеспечивая бесперебойное функционирование системы «точно вовремя».
Даже сегодня, в мире высокоскоростной электронной коммуникации, когда вы идете по заводу Toyota, который изготавливает и использует в сборке тысячи разных деталей, вы увидите карточки и прочие виды канбан, которые перемещаются по заводу, давая сигнал к производству и поставке деталей. Это замечательный инструмент – простой, эффективный и очень наглядный. Теперь компании всего мира изучают преимущества системы канбан. Они отказываются от сложных компьютерных графиков и планов для ряда этапов процесса. Хотя это может показаться шагом назад, на самом деле все многократно убеждались, что это шаг вперед, поскольку он позволяет компании сократить запасы, и при этом нужные детали всегда под рукой. При этом отпадает необходимость в сложных системах для подсчета точного количества нужных запасов, то есть потерь.
Вытягивание-пополнение в повседневной жизни
Понять концепцию канбан проще всего на примерах системы вытягивания-пополнения в повседневной жизни. Вы регулярно заправляете машину бензином. Заполняете ли вы бак по графику? Не приходило ли вам в голову заполнять его раз в неделю по понедельникам? Сомневаюсь. Заполняя его в таком режиме, вы бы быстро обнаружили, что иногда утром в понедельник в этом нет никакой необходимости, а порой бензин заканчивается задолго до наступления понедельника. По всей вероятности, вы заедете на бензоколонку, когда увидите, что бензин в баке заканчивается. Точно такую же систему вытягивания мы, не задумываясь, используем, когда покупаем все необходимое по хозяйству. Когда мы видим, что запас подходит к концу, это служит для нас сигналом. Мы говорим себе: «Пожалуй, пора пойти и купить еще».
Конечно, не все покупки делаются по системе вытягивания, кое-что приходится и планировать. Возьмем дорогие вещи, скажем, часы Rolex, спортивную машину или умопомрачительные клюшки для гольфа, которые рекламирует Тайгер Вудс. Когда вы покупаете себе нечто особенное, вы должны обдумать, что вам нужно, узнать цены и преимущества разных видов продукции и запланировать сроки покупки. В определенном смысле вы составляете график приобретения, поскольку срочной потребности в данном изделии нет.
Другим видом покупок, которые не являются безотлагательными и должны планироваться, являются услуги. Например, недавно нам чистили отстойник. Мы не знали, наполнился ли он и пора ли его опорожнить. Поэтому мы просто следовали рекомендациям (которые, скорее всего, являются неточными) – проводить плановую очистку отстойника, то есть действовали по системе выталкивания. Однако теперь в продаже появились устройства, которые позволяют определить наполнение отстойника: когда его содержимое достигает критической точки, устройство подает радиосигнал о том, что пришло время очистки. Если купить такое устройство, можно отказаться от «плановой системы» и перейти на систему вытягивания-пополнения – сигнал к пополнению (в нашем случае, к опорожнению) подается на основании реальной загруженности резервуара, а не по догадке.
Поскольку система вытягивания ориентирована на реальное состояние или расход, Toyota стремится к идеальному пополнению по системе «точно вовремя». Используя канбан, в компании тщательно отслеживают и координируют расход и пополнение тысяч деталей и инструментов, разрабатывают конкретные графики пополнения и правила подачи сигнала к пополнению, подсчитывают максимально допустимое количество запасов и т. п. В большинстве ситуаций в бизнесе система канбан (вытягивания) работает лучше, чем система графиков. Тем не менее она требует небольших резервов, запаса деталей, и эти запасы всегда являются компромиссом. Таким образом, конечной целью является устранение таких запасов и переход к потоку единичных изделий там, где это возможно.
Система канбан в Toyota – вытягивай, где необходимо
Настоящий поток единичных изделий представляет собой систему с нулевыми запасами, которая производит товары только тогда, когда они нужны потребителю. Система, которая ближе всего к этому идеалу, – это разработанная в Toyota ячейка, работающая по принципу потока единичных изделий и изготавливающая изделия на заказ именно к тому моменту, когда они понадобятся. Но поскольку идеальный поток осуществить нельзя, так как состыковать все операции невозможно, как невозможно добиться одинаковой продолжительности всех операций, оптимальным решением является система канбан.
Авторы известной книги о производственной системе Toyota Learning to See (Rother and Shook, 1999) говорят: «Там, где можно, создавай поток, где нельзя по-другому – вытягивай». Если вы хотите создать систему бережливого производства, начинайте каждый новый день с этой фразы. Руководствуясь этим простым принципом, вы добьетесь многого. Когда невозможно создать поток единичных изделий, лучшее, что можно сделать, – создать систему вытягивания с ограниченными запасами.
Рассмотрим систему вытягивания на сборочном предприятии Toyota. Сначала компания собирает заказы от автомобильных дилеров. Отдел управления производством составляет выровненный график. Например, нужно собрать белый автомобиль Camry, потом зеленый Camry, затем красный Avalon и т. д. Каждая из этих машин имеет ряд модификаций. График отправляется в кузовной цех, где изготовленные штамповкой стальные панели (из «супермаркета» предварительно отштампованных панелей) сваривают, то есть изготавливается кузов. Операция штамповки осуществляется очень быстро, она значительно опережает общее время такта сборочного предприятия (обычно время такта предприятия в целом – 60 сек., а на одну панель требуется всего 1 сек.), и встраивать эту операцию в поток единичных изделий нерационально. Поэтому используется система вытягивания. В заданный критический момент, когда кузовной цех израсходовал определенное число стальных панелей, на штамповочный пресс возвращается канбан, который является заказом на новую партию для пополнения запаса.
Аналогичным образом, когда рабочие на сборочной линии берут детали из контейнеров (петли, дверные ручки, стеклоочистители), они извлекают оттуда карточку канбан и кладут ее в «почтовый» ящик. Работник, который отвечает за транспортировку материалов, совершая запланированный обход, забирает карточку и возвращает ее туда, откуда поступают детали, чтобы пополнить запасы деталей, нужных на сборочной линии. Другой ответственный за транспортировку пополняет этот запас, запрашивая детали у поставщика, который их изготавливает. Таким образом, заказ возвращается к поставщику деталей. И так далее. Такая система показана на рис 9.1. Поставщик пополняет запас деталей на заводе. Процесс начинается на сборочном заводе (справа), затем канбан и пустые контейнеры возвращаются на грузовике к поставщику. Поставщик держит небольшой запас готовых деталей в резерве, который используется для того, чтобы наполнить вернувшиеся пустые контейнеры. Когда детали снимают с полок, где держат резерв, их запасы следует пополнить, поэтому канбан и пустые контейнеры поступают на производственную ячейку, где изготавливаются новые детали, которые пополнят резервный запас. Так от потребителя (сборочный завод) поступает информация – заказы на детали в виде канбан. После этого потребитель получает материал, который он запросил, в данном случае, это детали[21 – В большинстве случаев используется два вида карточек канбан: канбан отбора (withdrawal kanban) и канбан заказа (production-ordering kanban). Карточки отбора накапливаются на последующем участке и вместе с пустой тарой отправляются на предыдущий, когда в деталях возникает потребность. Карточки заказа постоянно находятся на предыдущем участке и указывают на количество изделий, которое надо изготовить. Число карточек отбора и заказа должно совпадать. Подробнее: Монден Я. Тоёта – методы эффективного управления. – М.: Экономика, 1989. – Прим. науч. ред.].
Множество деталей и материалов, которые перемещаются по предприятию в едином ритме, представляют собой поистине захватывающее зрелище. На большом сборочном заводе вроде того, что расположен в Джорджтауне, штат Кентукки, перемещаются тысячи деталей. Рядом со сборочной линией стоят небольшие контейнеры для деталей, такие же контейнеры перемещаются вдоль аккуратно уложенных резервных запасов. Трудно представить, как компьютерная система смогла бы так прекрасно управлять слаженным перемещением огромного количества деталей. Но настоящее потрясение испытываешь, узнав, что компьютер здесь ни при чем, а для управления процессом используются маленькие карточки из ламинированной бумаги.
И все же специалисты по TPS недовольны, когда слышат о том, что люди слишком увлекаются канбан, считая его эквивалентом производственной системы Toyota. Канбан – это удивительная идея, и наблюдать за ней в действии – одно удовольствие. Я нередко водил экскурсии по бережливым предприятиям, и говорить о технических деталях и видах канбан можно часами. В какой момент наступает время для канбан? Как подсчитывается число деталей? Что делать, если канбан потеряется? Но не это самое главное. Да, при отладке системы необходимо все это знать, но техническая сторона – не самое сложное. Основная задача – создать самообучающуюся организацию, которая сумеет снизить число карточек «канбан» и таким образом сократить и, в конечном счете, избавиться от резервных запасов. Не забывайте: канбан – это организованная система резервных запасов, а, по мнению Óно, запасы представляют собой потери, идет ли речь о системе выталкивания или о системе вытягивания. Поэтому канбан – это не предмет гордости, а то, от чего вы стремитесь избавиться. Одним из основных преимуществ использования канбан является то, что эти карточки упрощают совершенствование вашей производственной системы. Представьте, что у вас есть четыре контейнера с деталями, и вы напечатали четыре канбан, по одной на каждый контейнер. По правилам контейнер не может перемещаться, если его не сопровождает канбан. Теперь возьмите одну канбан и выбросите ее. Что произойдет? Теперь в системе циркулируют только три контейнера с деталями. Если один из станков сломается, детали на следующем участке закончатся на 25 % быстрее. Возможно, это повысит нагрузку на систему и вызовет простои, но одновременно это заставит команду совершенствовать процесс.
График выталкивания тоже может пригодиться
Принцип 3 (используй систему вытягивания, чтобы избежать перепроизводства) не исключает использования в рамках подхода Toyota системы выталкивания. Есть много примеров использования Toyota запланированного выталкивания. Один из таких примеров – поставка деталей из Японии в США или перемещение деталей в пределах США. При заказе таких деталей Toyota использует традиционную систему календарного планирования с соответствующим временем выполнения заказа, которое позволяет заводу получить детали в соответствии с планом. Конструирование новых изделий также осуществляется по жесткому графику, как я уже отмечал в главе 6.
Когда менеджеры Toyota составляют календарный план, прежде всего их интересует своевременность. Иными словами, календарный план представляет собой не просто руководящие указания, которых нужно придерживаться по мере возможности. Он определяет предельные сроки, и вы должны сделать все, чтобы уложиться в эти сроки. Поэтому даже при календарном планировании материалы и информация перемещаются без всяких помех. Система календарного планирования работает наиболее эффективно, когда срок выполнения заказа очень мал, поэтому заказ на детали предпочтительно размещать ежедневно, а не раз в месяц. Таким образом, если речь идет о календарном планировании, Toyota старается сократить время выполнения заказа до минимума.
Для календарного планирования Toyota все шире использует компьютерные системы. Например, заказывая детали у поставщиков, Toyota отправляет им электронные канбан, чтобы не заниматься сортировкой и возвращением карточек. Как мы увидим в главе 13, посвященной визуальному контролю, Toyota часто использует компьютерные системы для планирования некоторых операций, но наряду с этим применяет физические носители сигнальной информации, например карточки и белые доски, для того чтобы контролировать процесс визуально. Так, основой планирования материально-технического обеспечения распределительных центров запчастей Toyota является компьютерная система календарного планирования, но контроль операций осуществляется с помощью белых досок.
Если вы применяете подходы Toyota, чтобы создать у себя бережливое производство, вы должны уяснить, что бессмысленно копировать использование конкретных инструментов, чтобы стать похожим на Toyota. Дао Toyota – это философия, а инструменты должны использоваться избирательно и с учетом конкретных обстоятельств. Поймите, что именно философия определяет, во что верить и к чему стремиться. Она – часть более грандиозной системы, которая стремится к гармонии и совершенству, а последние – основа успеха Toyota. Прочитав остальные главы раздела II (Правильный процесс дает правильные результаты), вы увидите, что каждый из этих процессов тесно связан с другими.
Использование вытягивания в офисе GM
Систему вытягивания-пополнения можно эффективно использовать в офисной работе, где она позволит сэкономить деньги и избежать нехватки различных принадлежностей. В большинстве офисов в той или иной форме уже используется система вытягивания. Никто не знает точно, сколько карандашей, резинок или пачек бумаги будет использовано в офисе. Если запланировать заказ всех этих принадлежностей, что-то будет заказано в нужном количестве, что-то – в избытке, а чего-то будет не хватать. Поэтому там, где офисная работа организована должным образом, каждый должен иметь небольшой запас принадлежностей, которыми он пользуется, и следить за ним. Тогда легко пополнить израсходованный резерв.
На фирме General Motors есть Отдел технических связей, расположенный в Калифорнии, который занимается организацией экскурсий по совместному с Toyota предприятию – заводу NUMMI. Прежде всего работники GM, которые приехали ознакомиться со знаменитой производственной системой Toyota на заводе NUMMI, попадают в офис. Поэтому GM превратила его в образцовый офис, организованный по системе бережливого производства. Здесь для пополнения запасов используется образцовая система канбан, в запасе всегда есть все необходимое. Резервный запас всегда лежит в специально отведенном месте на столах рядом с компьютером.
Там, где хранится резервный запас принадлежностей, лежат маленькие карточки канбан, сделанные из ламинированной бумаги, на которых написано, когда их следует использовать. Например, если в бутылочке с аспирином остается лишь четверть ее содержимого, канбан на аспирин кладут в жестянку из-под кофе. В офисе давно стоял холодильник, в котором хранились безалкогольные напитки, и некоторые напитки быстро заканчивались, а других всегда было слишком много. Поскольку дверь холодильника была непрозрачная, было трудно увидеть, какой беспорядок царил внутри. Поэтому офис приобрел большую машину для содовой воды со стеклянной дверью и снял с нее устройство оплаты. Через стеклянную дверь было видно, что делается внутри. На специально помеченные полки поставили разные соки и безалкогольные напитки. Когда определенный напиток заканчивается, вы берете канбан для данного напитка и кладете его в ящик, чтобы его запасы пополнили при очередном заказе.
Вам может показаться, что в маленьком офисе систему вытягивания применять не стоит, ведь это достаточно сложная система, назначение которой – снизить себестоимость. Разумеется, можно провести анализ затрат и результатов и понять, стоит ли она в данном случае затраченного времени. Но это образ мышления традиционного массового производства. Выгода здесь не в сэкономленных центах. Сила производственной системы Toyota в том, что она стимулирует творческий подход и непрерывное совершенствование. Поэтому введение в офисе системы канбан помогло увлечь работников, заинтересовать их в совершенствовании процесса заказа принадлежностей и, в конечном счете, изыскать возможности для создания потока в основной работе. Потери в офисе обычно гораздо больше, чем на производственных предприятиях. Эффект от незначительного усовершенствования процесса, к которому подошли творчески, многократно превысит затраты на его усовершенствование.
Глава 10
Принцип 4: выравнивай объем работ (хейдзунка)
Когда вы внедряете TPS, вы должны начать с выравнивания производства. Это первоочередная обязанность тех, кто занимается управлением производством. Возможно, выравнивание графика производства может потребовать ускорить или отложить отгрузку каких-то изделий, и вам придется попросить кого-то из потребителей немного подождать. Если уровень производства на протяжении месяца остается более или менее постоянным, вы можете применить систему вытягивания и обеспечить сбалансированную работу сборочной линии. Но если уровень производства – выработка – меняется изо дня в день, нет смысла пытаться применить все остальные системы, поскольку в этих обстоятельствах вам просто не удастся стандартизировать работу.
Фудзио Тё, президент Toyota Motor Corporation
Вслед за Dell Computer и другими преуспевающими компаниями многие американские предприятия всеми силами стремятся создать у себя модель производства «сборка по заказу». Они ориентируются только на то, что и когда потребуется потребителю, то есть стремятся создать безупречное бережливое производство. К сожалению, потребители часто непредсказуемы и их заказы меняются ежемесячно, а то и еженедельно. Если вы изготавливаете изделия в порядке поступления заказов, вам придется периодически заставлять сотрудников и оборудование работать на пределе возможностей, производя огромное количество изделий, и платить за сверхурочную работу. После этого будут наступать периоды затишья, людям будет нечем заняться, а оборудование будет простаивать. При такой работе вы не знаете, какое количество комплектующих заказать у поставщиков, и будете вынуждены держать огромный запас того, что может понадобиться потребителю. Вести бережливое производство при таком подходе невозможно. Неукоснительное следование модели «сборка по заказу» приводит к созданию огромных запасов, что скрывает проблемы и, в конечном счете, ведет к снижению качества. Хаос на предприятии растет, а время выполнения заказа увеличивается. В Toyota обнаружили: для того чтобы создать максимально правильное бережливое производство и добиться роста качества обслуживания потребителей, нужно выровнять график производства, не всегда строго следуя порядку поступления заказов.
Ряд компаний, с которыми мне приходилось сотрудничать и которые пытались работать по принципу «изготовление на заказ», чаще всего заставляли потребителя ждать заказанное изделие от шести до восьми недель. При этом в очередь могли вклиниться «особо ценные» клиенты, и их заказы срочно выполнялись в ущерб остальным. Но стоит ли нарушать ритм работы, чтобы выполнить какой-то заказ именно сегодня, если потребитель все равно получит заказанное изделие лишь через шесть недель? Не лучше ли вместо этого собрать заказы и выровнять график производства? Это позволит вам ускорить выполнение заказов, сократить запасы деталей, и все потребители с удовлетворением узнают, что стандартное время выполнения заказов значительно сократилось. Разве это не лучше чередования авралов и простоев, которого требовал принцип «изготовление на заказ»?
Говоря о потерях, менеджеры и рабочие Toyota используют термин «мýда», и устранение мýда является сущностью бережливого производства. Но для организации такого производства важны и два других М, и эти три М представляют собой единую систему. Если заниматься только восемью видами потерь (мýда), это лишь навредит эффективной работе людей и производственной системы. Документ The Toyota Way говорит об «устранении мýда, мýри, мýра» (см. рис. 10.1). Что представляют собой три «М»?
• Мýда – действия, которые не добавляют ценности. Самое известное М включает восемь видов потерь, упомянутых выше. Это действия, которые увеличивают время выполнения заказа, заставляют совершать ненужные перемещения, чтобы доставить деталь или инструмент, ведут к созданию лишних запасов или заставляют ждать.
• Мýри – перегрузка людей или оборудования. В определенном смысле представляет собой противоположность мýда. Мýри заставляет машину или человека работать на пределе возможностей. Перегрузка людей угрожает их безопасности и вызывает проблемы с качеством. Перегрузка оборудования ведет к авариям и дефектам.
• Мýра – неравномерность. Это «М» в некотором роде является результатом действия первых двух. Временами в нормально функционирующих производственных системах бывает больше работы, чем могут выполнить специалисты и оборудование, а порой работы недостаточно. Причина неравномерности – неправильно составленный график или колебание объемов производства, вызванное внутренними проблемами, например простоями, отсутствием деталей или дефектами. Мýда является результатом мýра. Неравномерность уровня производства вызывает необходимость соответствия имеющихся в наличии ресурсов (оборудования, материалов, людей) максимальному объему производства, даже если на деле его средний уровень значительно ниже.
Представьте, что ваш производственный график допускает резкие колебания, что он неравномерен и ненадежен. Вы решили перейти к системе бережливого производства и думаете только о том, как устранить из вашей производственной системы мýда. Вы начинаете снижать уровень запасов. Затем вы стараетесь обеспечить равномерный ритм работы и сокращаете число людей в системе[22 – Toyota никогда не увольняет и не понижает в должности рабочих, которых пришлось сместить из-за роста производительности. Такой недальновидный шаг, который на первый взгляд позволяет снизить затраты, обязательно вызовет враждебное отношение к компании, и остальные рабочие будут неохотно участвовать в работе по кайдзен в будущем. Для тех, кто лишился места в результате совершенствования производства, Toyota всегда ищет альтернативную работу по созданию добавленной ценности.]. После этого вы работаете над организацией рабочих мест, чтобы устранить лишние движения. Наконец, вы запускаете систему. И с грустью обнаруживаете, что система работает на износ из-за пиков в потребительском спросе, которые заставляют людей и оборудование работать слишком напряженно, а значит – неэффективно! Производство организовано теперь как поток единичных изделий, запасов нет, но темп производства и ассортимент изделий постоянно и резко меняются. Все, чего вы добились, это чрезвычайно нестабильного потока единичных изделий. Ваши рабочие перегружены. Оборудование выходит из строя еще чаще, чем раньше. Вам не хватает деталей. И вы делаете вывод: «Бережливое производство здесь не работает».
Любопытно, что повышенное внимание к мýда – очень распространенный подход при внедрении «инструментов бережливого производства», поскольку выявить и устранить затраты не так уж сложно. Но большинство компаний забывает о более сложном процессе стабилизации системы и достижения «равномерности» – создании сбалансированного бережливого потока. Речь идет о концепции, называемой хейдзунка, которая требует выравнивания рабочего графика. Возможно, это наиболее осознанно применяемый в рамках подхода Toyota принцип. Реализация хейдзунка – предпосылка устранения мýра, а это, в свою очередь, необходимо для устранения мýри и мýда.
Чрезмерная загруженность с последующей недогрузкой ведет к постоянным запускам и остановам и несовместима с высоким качеством, стандартизацией работы, производительностью и непрерывным совершенствованием. Как сказал Тайити Óно:
Медлительная, но упорная черепаха не создает такого количества потерь и куда лучше торопливого зайца, который мчится вперед сломя голову, а время от времени останавливается, чтобы вздремнуть. Производственную систему Toyota можно понять, лишь когда все рабочие становятся черепахами (Ohno, 1998).
От других руководителей Toyota я не раз слышал: «Мы предпочитаем быть медлительными и упорными, как черепаха, нежели прыгать, как заяц». Производственные системы США делают рабочих зайцами. Они работают до изнеможения, а потом устраивают передышку. На многих американских заводах рабочие объединяются попарно – пока один работает за двоих, другой свободен. Если это не влияет на дневную норму выработки, менеджеры смотрят на такое сквозь пальцы.