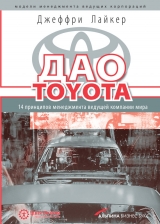
Текст книги "Дао Toyota: 14 принципов менеджмента ведущей компании мира"
Автор книги: Джеффри Лайкер
Жанры:
Деловая литература
,сообщить о нарушении
Текущая страница: 10 (всего у книги 29 страниц) [доступный отрывок для чтения: 11 страниц]
Объединение людей и оборудования по принципу специализации порождает еще одну проблему: изделие, нужное потребителю, не привязано к одному отделу. Чтобы превратиться в то, что требуется потребителю, оно кочует по разным отделам. Проектированием, снабжением и финансированием занимаются разные отделы. Через эти отделы проходит множество потоков создания ценности, поэтому каждый раз, когда изделие передается в очередной отдел, возникает задержка. Поток единичных изделий предполагает, что вы последовательно выстраиваете все технологические операции в единую линию, которая позволяет выполнить заказ потребителя в кратчайшие сроки.
На рис. 8.1 схематично представлена компьютерная фирма, состоящая из трех отделов. Один отдел изготавливает системные блоки, второй производит мониторы и подсоединяет их к системному блоку, а третий тестирует готовые компьютеры (на самом деле, при изготовлении компьютера в технологической цепочке задействовано множество компаний и отделов). При такой структуре транспортный отдел считает целесообразным за один раз перемещать партию в 10 единиц. Каждый отдел затрачивает на единицу одну минуту, следовательно, партия компьютеров проходит каждый отдел за 10 минут. Без учета времени перемещения между отделами на изготовление и тестирование первой партии в 10 единиц будет затрачено 30 минут. На то, чтобы подготовить первый компьютер к отгрузке и отправке потребителю, уйдет 21 минута, несмотря на то что создание добавленной ценности в процессе его изготовления занимает всего три минуты.
В системе, созданной Óно, эффективность отдельного процесса или работы транспортного отдела не определяет идеальный размер партии. Идеальный размер партии при бережливом подходе неизменен – это одно изделие. Óно не пытался оптимизировать использование людей и оборудования в изолированных отделах. Первый завод Toyota работал именно по методу заводов Ford. Но это не давало нужных результатов, ведь Toyota не могла соперничать с Ford по объемам производства и экономии, обусловленным масштабами производства. Поэтому Оно решил оптимизировать поток материала, чтобы он быстрее проходил через завод. Это означало уменьшение партии. И чтобы сделать это, проще всего было разрушить барьеры между отделами и вместо островков, которые специализировались на отдельных операциях, создать рабочие ячейки, объединенные по изделиям, а не по процессам.
На рис. 8.2 представлен тот же самый процесс изготовления компьютеров, организованный по принципу рабочей ячейки, через которую проходит поток единичных изделий. Если бы за этот процесс принялся Óно, он взял бы в одном отделе оборудование, необходимое для изготовления системного блока, в другом отделе оборудование для изготовления монитора и испытательный стенд из отдела тестирования и выстроил из этих операций последовательную цепочку. Иными словами, он создал бы ячейку для потока единичных изделий. Потом он убедился бы, что операторы не создают запасы между данными тремя операциями. Например, тот, кто делает системные блоки, не должен приниматься за изготовление очередного блока, пока не будет изготовлен монитор для предыдущего блока и пока из этих двух сборочных узлов не будет создано готовое изделие. Иными словами, никто не должен производить сверх того, что понадобится немедленно. В результате за 12 минут операторы подобной ячейки изготавливают 10 компьютеров. К тому же такой бережливый процесс позволяет подготовить к отгрузке первый работоспособный компьютер всего за три минуты вместо 21. Эти три минуты и представляют собой чистое время создания добавленной ценности. Поток позволил избавиться от перепроизводства и запасов.
Почему при наличии потока «быстрее» означает «лучше»
Часто нам кажется, что ускорение процесса ведет к снижению качества, быстрее – значит, небрежнее. Но поток ведет к совершенно противоположному результату – как правило, качество повышается. На рис. 8.1 и 8.2 показан дефектный компьютер, монитор которого перечеркнут. На этапе тестирования его не удалось включить. При выпуске большой партии по схеме, представленной на рис. 8.1, к моменту выявления проблемы в работе будет не менее 21 изделия, и не исключено, что все они будут иметь тот же дефект. Если это дефект, который допущен по вине отдела, выпускающего системные блоки, то отдел тестирования узнает об этом лишь через 21 минуту. На рис. 8.2, когда дефект обнаружен, в работе находятся всего два компьютера с таким же дефектом, и на то, чтобы выяснить, на какой операции допустили ошибку, уйдет всего две минуты. Таким образом, при производстве крупных партий незавершенное производство может лежать между отдельными операциями неделями, и с момента, когда был допущен дефект, до момента, когда его обнаружат, могут пройти недели и даже месяцы. Но след уже «остынет», и выявить причину появления дефекта будет почти невозможно.
Та же логическая цепочка применима к любому технологическому или бизнес-процессу. Если вы позволите изолированным отделам делать свою работу партиями и передавать эти партии в другие отделы, задержки с завершением работы вам гарантированы. Не обойдется и без бюрократических проволочек, чиновники начнут устанавливать стандарты для каждого отдела и для отслеживания потока будет создано множество позиций, не имеющих отношения к созданию добавленной ценности. Бо́льшую часть времени проекты проведут в ожидании действий или решений. Это приведет к неразберихе и низкому качеству. Подберите нужных людей, которые создают добавленную ценность, определите последовательность операций и пропустите проект через созданную цепочку, позаботившись о том, как состыковать их действия, и вы получите темп, производительность и нужное качество.
Время такта: пульс потока единичных изделий
В соревнованиях по гребле важную роль играет рулевой, который сидит на корме и покрикивает «и раз, и раз, и раз». Он координирует деятельность всех гребцов, следя за тем, чтобы они действовали слаженно и гребли с одной скоростью. Что происходит, если один из гребцов действует быстрее других? Верно, порядок нарушается, и лодка движется медленнее. Избыток силы и скорости замедляет движение.
Нечто подобное происходит в любой работе, идет речь о производстве или об оказании услуг. Если отдельный участок работает с избыточной производительностью, он завалит другие отделы горами запасов и бумаг, что приведет к неразберихе и замедлению процесса. Деятельность подразделений должна быть скоординирована. Как определить, с какой скоростью должна работать созданная вами ячейка для потока единичных изделий? Какой должна быть мощность оборудования? Сколько понадобится людей? Для этого нужно определить время такта.
Немецкое слово takt означает ритм или темп. Время такта определяется потребительским спросом – темпом приобретения изделий. Если рабочий день составляет 7 часов 20 минут (440 минут), 20 дней в месяц, а потребитель приобретает в месяц 17 600 единиц продукции, значит, в день нужно выпускать 880 единиц, то есть одно изделие за 30 секунд. При правильно организованном потоке единичных изделий каждая стадия процесса должна занимать 30 секунд. Если работа пойдет быстрее, это приведет к перепроизводству, если медленнее – в процессе появится узкое место. Понятие «такт» используется, когда нужно определить темп производства и не допускать, чтобы рабочие отставали от него или слишком торопились.
Непрерывный поток и время такта проще всего применять при серийном производстве товаров или услуг. Однако при творческом подходе эти концепции применимы к любому повторяющемуся процессу, если составить перечень его стадий и выявить и устранить потери (см. главу 21). В конце этой главы приводится пример такого перечня на судоремонтном предприятии ВМФ США. Я и мои коллеги в процессе работы сталкивались с массой других примеров: заполнение накладных при проектировании судов, проверка людей службой безопасности верфи ВМФ, прием новых членов в профессиональное объединение, возмещение расходов служащим, работа с претендентами на рабочие места… Вы сами можете найти множество других примеров. Разумеется, концепцию времени такта и потока единичных изделий проще всего применить к многократно повторяющимся операциям обслуживания, которые предполагают определенную стабильность времени цикла на единицу, но дао Toyota не предполагает поиска только легких путей.
Преимущества потока единичных изделий
Создание потока единичных изделий предполагает широкую программу мероприятий по устранению всевозможных мýда (потерь). Рассмотрим подробнее некоторые преимущества потока.
1. Встраиваемое качество. Поток единичных изделий значительно упрощает встраивание качества. Каждый оператор одновременно является контролером и старается решить проблему на месте, не передавая ее на следующую стадию. Даже если он пропустил дефекты и они прошли дальше, их обнаружат очень быстро и проблема будет немедленно выявлена и исправлена.
2. Подлинная гибкость. Если оборудование становится частью производственной линии, наши возможности использовать его для других целей сократятся. Но время выполнения заказа сокращается до предела, а значит, мы более гибко реагируем на запросы потребителя, изготавливая то, что ему действительно нужно. Вместо того чтобы неделями ждать, пока система, которой дан заказ, выдаст продукцию, мы можем выполнить заказ в течение нескольких часов. Переход на новый ассортимент продукции, которого требует изменение потребительского спроса, осуществляется при этом почти мгновенно.
3. Повышение производительности. Когда работа была распределена по отделам, вам казалось, что так вы добиваетесь максимальной производительности, поскольку эффективность работы оценивалась по загрузке людей и оборудования. На самом деле трудно определить, сколько людей требуется для изготовления заданного количества единиц продукции при крупносерийном производстве, поскольку производительность не оценивается с точки зрения работы, добавляющей ценность. Кто знает, каковы потери производительности, когда люди «загружены» производством избыточных деталей, которые потом придется отправить на склад? Сколько времени теряется при поисках дефектных деталей и ремонте готовых изделий? Если существует ячейка для потока единичных изделий, работа, не добавляющая ценности, вроде перемещения материалов сводится к минимуму. Вы сразу видите, кто перегружен, а кто остался без дела. Очень легко составить калькуляцию работы, добавляющей ценность, и подсчитать, сколько людей требуется для достижения заданной производительности. Когда речь идет о переводе поставщика, работающего по системе массового производства, на линию, организованную в соответствии TPS, Центру поддержки поставщиков Toyota (Toyota Supplier Support Center) в каждом случае удается добиться повышения производительности труда не менее чем на 100 %.
4. Высвобождение площадей в цехе. Когда оборудование распределено по участкам, значительные площади между ними пропадают, хотя большая их часть занята запасами залежами запасов. В ячейке для потока единичных изделий все блоки подогнаны друг к другу, а запасы почти не занимают места. Если производственные площади используются более эффективно, можно избежать строительства новых мощностей[17 – Кроме того, можно существенно сэкономить на аренде и эксплуатации помещений, а в ряде случаев – на налогах. – Прим. науч. ред.].
5. Повышение безопасности. Корпорация Wiremold, которая одной из первых в Америке стала применять TPS, добилась образцовых показателей безопасности и была удостоена множества государственных наград за безопасность. Однако когда в компании решили взяться за преобразование крупносерийного производства в поток единичных изделий, было решено, что специальная программа повышения безопасности не нужна. Реорганизацию возглавил Арт Бирн, бывший президент компании, изучавший TPS и понимавший, что поток единичных изделий автоматически приведет к повышению безопасности благодаря уменьшению количества материала, который нужно перемещать по заводу. Уменьшение объема грузов позволяет избавиться от вилочных погрузчиков, часто являющихся причиной несчастных случаев. Объем контейнеров, которые нужно поднимать и перемещать, также уменьшится, а значит, снизится число несчастных случаев при подъеме контейнеров. Если заниматься потоком, безопасность повышается сама собой, даже если не уделять ей особого внимания[18 – Более подробный анализ преобразования Wiremold в компанию с бережливым производством приводится в книге Better Thinking (Emilani Bob, Stec David, Grasso Lawrence & Stodder James. Kensington, CT: Center for Lean Business Management, 2002).].
6. Повышение морального духа. В Wiremold при организации бережливого производства обнаружили, что с каждым годом моральное состояние сотрудников улучшается. До преобразований лишь 60 % сотрудников при проведении опросов заявляли, что работают в хорошей компании. Этот показатель рос с каждым годом и на четвертый год преобразований превысил 70 % (Emilani, 2002). Поток единичных изделий ведет к тому, что бо́льшую часть времени люди заняты созданием добавленной ценности и могут быстро увидеть плоды своего труда, а видя свои успехи, чувствуют удовлетворение.
7. Сокращение запасов. Не вкладывая капитал в запасы, которые лежат мертвым грузом, вы можете использовать его на что-то иное. При этом вы сэкономите еще и на банковских процентах, которые необходимо выплачивать за замороженные в запасах средства. Вы также избежите морального старения[19 – Дополнительный эффект достигается за счет снижения затрат на хранение, сокращения (помимо морального) физического старения материалов с учетом срока годности, а также снижения дефектов от излишних погрузочных и транспортировочных операций. – Прим. науч. ред.] запасов.
На рис. 8.3 представлен традиционный цех, где оборудование сгруппировано по типу. Одним из инструментов, которые можно использовать для схематического изображения траектории движения материалов, является «диаграмма спагетти». Если мы нанесем на схему поток перемещения материалов в цехе, то получим нечто напоминающее спагетти, которые беспорядочно перемешаны на тарелке. Продукт бессистемно перемещается в разных направлениях. Работа отдельных участков при перемещении продукта не согласована. Никакие графики и планы не могут устранить вариабельность, присущую системе, в которой материал перемещается беспорядочно.
На рис. 8.4, где представлена ячейка бережливого производства, мы видим иную картину. Оборудование сгруппировано в соответствии с потоком материала по мере его превращения в готовое изделие. При этом оборудование размещено в форме буквы U, так как такая компоновка способствует эффективному перемещению материалов и людей и облегчает обмен информацией. Можно организовать ячейку в виде прямой линии или буквы L. В данном случае мы показали траекторию движения двух человек, которые обслуживают ячейку. Что делать, если спрос снизится вдвое? Оставьте на ячейке одного оператора. Что делать, если спрос удвоится? Поставьте на обслуживание ячейки четырех человек. Разумеется, для того чтобы обслуживать разные технологические операции, люди должны быть подготовлены к совмещению профессий, таковы требования заводов Toyota.
Почему сложно создать поток
Вам кажется, что как только вы создадите ячейки для потока единичных изделий, жизнь немедленно наладится и все проблемы и несчастья исчезнут? Даже не надейтесь! Если вы начнете мыслить категориями бережливого производства, на какое-то время жизнь станет куда труднее, по меньшей мере, пока вы не научитесь постоянно совершенствовать процесс. Тайити Óно говорит:
В 1947 году мы выстроили станки в параллельные линии, а кое-где скомпоновали их буквой L и попытались поставить одного рабочего на три-четыре станка в соответствии с технологическим маршрутом. Хотя речь не шла о сверхурочной работе, рабочие отчаянно сопротивлялись. Станочникам не понравилось, что новая планировка требует от них совмещения профессий. Им не понравился переход от системы «один оператор – один станок» к системе «один оператор – много станков для различных операций». Их можно было понять. К тому же обнаружились и другие проблемы. Когда стало понятно, какого рода эти проблемы, я смог решить, в каком направлении следует двигаться. Хотя я был молод и энергичен, я решил не настаивать на немедленных, радикальных переменах, но запастись терпением (Ohno, 1988).
Если при традиционном массовом производстве на одном из этапов процесса произойдет сбой, например, понадобится длительное время для переналадки станка, кто-то не выйдет на работу по болезни или выйдет из строя оборудование, другие «независимые» стадии процесса будут осуществляться, как прежде, поскольку у вас предостаточно запасов. Когда вы увязываете отдельные операции, создавая поток единичных изделий, если происходит сбой на одном участке, останавливается вся ячейка. Либо вы плывете вместе, либо все вместе идете ко дну. Так почему бы не облегчить себе жизнь и не создать резервный запас? Однако любые запасы – скопления материала или виртуальные скопления информации, которые подолгу ждут своего часа, – препятствуют выявлению проблем и неэффективности. Запасы вырабатывают дурную привычку обходить проблемы. Если вы избегаете решения проблем, вы не совершенствуете процессы. Поток единичных изделий и непрерывное совершенствование (кайдзен) идут рука об руку! Если ваш конкурент решится ступить на трудный и тернистый путь бережливого подхода, никакие запасы вам не помогут, вас ждет банкротство. Минора, бывший президент Toyota Motor Manufacturing и ученик Тайити Óно, говорит:
Тому, кто запустил производство по системе потока единичных изделий, не удается держать желаемое количество изделий, поэтому поначалу все обескуражены и не знают, что предпринять. Но это заставляет людей думать: как можно получить нужное количество? В этом сущность TPS, можно сказать, что мы намеренно приводим людей в замешательство, чтобы они были вынуждены изменить своей подход к проблеме.
Многие компании, в которых мне приходилось бывать, внедряя поток, делали одну из двух ошибок. Первая заключалась в том, что поток был не настоящим. Второй ошибкой был немедленный отказ от потока, как только возникали проблемы.
Примером псевдопотока была перестановка оборудования. Сдвинув блоки оборудования вместе, в компании создавали внешнее подобие ячейки для потока единичных изделий, но на каждой стадии продолжали заниматься серийным производством, не задумываясь о времени такта, которое определяется потребителем. Выглядело это как ячейка для потока изделий, но работа шла по старинке, по принципу серийного производства.
Will-Burt Company в Орвилле, штат Огайо, изготавливает различные изделия из стальных заготовок. Одним из изделий, которые производятся в больших объемах, является семейство телескопических стальных мачт, которые используются в фургонах для радаров или съемочных бригад. Каждая мачта имеет свои особенности в зависимости от сферы применения, поэтому все изделия разные. Эта компания назвала процесс изготовления мачт ячейкой и считала, что создала у себя бережливое производство. Когда я как консультант по бережливому производству помогал организовать анализ процессов, управляющий производством предупредил нас, что ассортимент деталей столь разнообразен, что нам вряд ли удастся усовершенствовать существующий поток.
В течение недельного семинара по кайдзен была проанализирована текущая ситуация, и оказалось, что мы имеем дело с классическим псевдопотоком[20 – Семинар проводили Джеффри Ривера, бывший старший консультант по бережливому производству в Optiprise, Inc., и Эдуардо Ландер, мой докторант в Мичиганском университете.]. Время, необходимое для создания одной мачты (время обработки, добавляющей ценность), составляло 431 минуту. При этом единицы оборудования, которое использовалось для производства каждой мачты, были расположены так далеко друг от друга, что приходилось перемещать большие паллеты с мачтами с помощью вилочных погрузчиков с одного рабочего места на другое. На каждом рабочем месте лежали запасы незавершенного производства. Полное время выполнения заказа от сырья до готового изделия, учитывая длительность пребывания в состоянии незавершенности, составляло 37,8 дня. Бо́льшую часть этого времени занимало складирование трубчатых заготовок и готовых изделий. Если говорить о времени обработки на заводе, на работу, которая занимала 431 минуту, от распиловки до завершающей стадии – сварки – уходило четыре дня. Перемещаясь в пределах завода, каждая мачта преодолевала расстояние в 1792 фута (546 метров. – Прим. науч. ред.). Для решения этих проблем было предложено разместить блоки оборудования ближе друг к другу, обрабатывать изделия по одному, одно за другим, отказаться от использования вилочного погрузчика между операциями (для перемещения изделий между операциями, которые было невозможно осуществлять рядом, была сконструирована специальная тележка, высота которой соответствовала уровню рабочего места). Кроме того, было предложено оформлять отдельный заказ-наряд на каждую мачту вместо комплекта заказов-нарядов на комплект мачт. Результатом этих изменений были значительное сокращение времени выполнения заказа (см. рис. 8.5), уменьшение запасов и экономия производственных площадей.
Помимо прочего, было проверено, сколько времени уходит на размещение заказа-наряда, и это позволило получить дополнительный положительный эффект, ликвидировав старый метод. Накопление партий заказов-нарядов порождало множество потерь; и когда такой системе был положен конец, время сократилось с 207 минут до 13 минут. На рис. 8.6 изображен поток до и после недельного практического семинара по кайдзен. Видно, что ситуация «до» в действительности представляет собой псевдопоток. Единицы оборудования вроде бы расположены рядом, но ничего похожего на поток единичных изделий на самом деле нет. Сотрудники, работающие на заводе, не вполне понимали, что такое поток, и не осознавали, что имеют дело с псевдопотоком. Ситуация «после» качественно улучшилась, что удивило и обрадовало всех в компании. Они были потрясены, что это удалось сделать всего за неделю.
Второй ошибкой, которую допускают те, кто внедряют поток, является отказ от избранного курса. Как только становится ясно, что создание потока может привести к определенным издержкам, компания отказывается от принятого решения. Это может произойти в любой из перечисленных ниже ситуаций:
• Остановка одного из блоков оборудования приводит к тому, что вся ячейка прекращает работу.
• Переналадка одного из блоков оборудования занимает больше времени, чем предполагалось, и замедляет работу ячейки в целом, поскольку производство останавливается.
•При создании потока приходится вкладывать деньги в технологическую операцию, которая раньше осуществлялась на другом предприятии (например, термообработка), чтобы производить ее на месте.
Я видел, как в подобных случаях компании отказывались от применения потока. Они считали, что поток – отличная вещь, пока преимущества уменьшения размера партии изделий и поточной системы вам демонстрируют на теоретической модели. Но он далеко не так хорош, когда мы опробуем его в деле, и видим, что он немедленно вызывает разного рода неприятности и издержки. Когда создана ячейка для потока единичных изделий, ее обслуживание требует дисциплины, а это для многих производственных компаний – вещь невозможная, поскольку они не сознают в полной мере, сколько сложностей и проблем сопряжено с непрерывным совершенствованием. Однако в долгосрочном аспекте эти неприятности и кратковременные издержки непременно окупаются, приводя к поразительным результатам.
Занимаясь любым процессом, Toyota старается создать подлинный поток единичных изделий, избавившись от потерь, о чем говорит принцип 2: процесс в виде непрерывного потока способствует выявлению проблем. Создать поток – значит, связать воедино операции, которые ранее были разобщены. Когда такая связь создана, команда работает более слаженно, система оперативно реагирует на проблемы, связанные с качеством, процесс становится управляемым, а незамедлительное решение проблем становится насущной потребностью, вынуждая людей думать и развиваться. В конечном счете, для подхода Toyota основное преимущество потока единичных изделий заключается в том, что он заставляет людей думать и совершенствоваться.
Делая акцент на необходимости думать, Toyota расшифровывает название своей производственной системы, TPS, как «Thinking Production System» («Думающая производственная система»). Ради выявления проблем Toyota готова остановить производство, зная, что это заставит членов команды найти решение. Запасы скрывают проблемы и позволяют откладывать их решение в долгий ящик. При подходе Toyota проблема решается сразу же, как только она обнаружена. В главе 11 (посвященной дзидока) рассказывается об этом более подробно.
Пример из практики: описание процессов на заводе по ремонту кораблей ВМФ
Прекрасным примером того, как поток единичных изделий можно применить в работе ремонтного предприятия, служит кораблестроительный завод ВМФ в Пьюджет-Саунд. Здесь начали применять поток единичных изделий осенью 2001 года. Завод занимается не строительством, а ремонтом кораблей ВМФ – от подводных лодок до авианосцев. Ремонт каждого корабля носит уникальный характер, поэтому работа осуществляется в тесном контакте с инженерами, которые диагностируют проблему и составляют задание для предстоящих ремонтных работ. Техническая документация, включая инструкции по выполнению работ, складывается в папку, которая передается на завод, чтобы квалифицированные рабочие могли выполнить соответствующий ремонт. В результате, чтобы выполнить свою работу, механикам приходилось заниматься оформлением допусков, вопросами финансирования и другой бумажной работой. Папка с инструкциями часто становилась узким местом в процессе планирования и вела к дополнительным затратам.
Чтобы усовершенствовать процесс, был проведен недельный практический семинар по кайдзен. Ему предшествовала основательная подготовка. Велись приготовления к реорганизации, в офисе было выделено помещение под межфункциональную ячейку, которая должна была заниматься производственными заданиями. В центре внимания семинара были составление карты существующего процесса и разработка нового процесса. В ходе пошагового анализа процесса были выявлены потери, включая переделку, избыточные системы, различные носители информации (например, сводные ведомости), ожидание бланков, проверка, лишние проверки и утверждения, непродуманная система регистрации документов, отсутствие необходимых справочных материалов, лишнее хождение, ожидание и неполнота информации.
В качестве решения было предложено разработать межфункциональную ячейку, чтобы собрать все рабочие инструкции вместе. В результате количество передач документов из рук в руки сократилось, а операции, не добавляющие ценности, были устранены. С учетом потребности в рабочих инструкциях (эти потребности предсказать очень легко) и времени, необходимого для их разработки, было определено время такта. Самым важным являлся отбор сотрудников, которые выполняют основную часть работы, и устранение разделявших их преград. Ячейку создали в офисе, и папка с рабочими инструкциями передавалась с одной позиции на другую в рекордные сроки. Прежде в офисе сотрудники были сгруппированы в соответствии со своими функциями, а помещения разделены высокими перегородками, чтобы у каждого был свой кабинет. Теперь, при наличии ячейки, столы ведущих специалистов располагались вокруг круглого стола. Производственные задания передавались вдоль стола от одного специалиста к другому, образуя поток единичных объектов. Хронометраж времени, уходившего на создание добавленной ценности до и после преобразований, показал потрясающие результаты. Заметьте, что некоторые потери времени на процессы, не добавляющие ценности, неизбежны, например, заполнение ряда бумаг в соответствии с правилами ВМФ, хотя для работы механиков эти бумаги нужны далеко не всегда. Такие затраты времени мы представили в особой графе, отдельно от «времени ожидания», которое представляет собой потери в чистом виде. Результаты реорганизации показаны на рис. 8.7.
Глава 9
Принцип 3: используй систему вытягивания, чтобы избежать перепроизводства
Чем больше в компании запасов… тем меньше надежды, что у нее будет то, что нужно.
Тайити Óно
Представьте, что вы узнали о замечательной службе заказов через Интернет. Теперь все молочные продукты будут привозить вам на дом, да еще с хорошей скидкой. Есть лишь одна сложность – определить количество продуктов на неделю нужно заранее. Компания же может гарантировать только одно – доставку в течение недели. Компания просит вас определиться с заказом заранее, поскольку должна знать, сколько и каких продуктов нужно отгрузить со склада. Это позволит ей распродать все полученные продукты. Продукты будут оставлять у вас на крыльце в специальном контейнере-холодильнике. Вы подсчитываете, сколько яиц, молока и масла вы обычно потребляете в течение недели. Но вы не знаете, в какой день их подвезут. Возможно, это будет понедельник, а может быть – пятница. Поэтому в холодильнике вам приходится держать резервный запас продуктов. Если продукты привозят в понедельник, а у вас в холодильнике уже лежит недельный запас молочных продуктов, вы с трудом находите место для новых. Вы покупаете еще один холодильник и ставите его в гараже. Если вы уезжаете в отпуск и забываете отменить заказ на неделю, вернувшись, вы обнаружите на крыльце контейнер с недельным запасом испорченных продуктов.
Это пример системы выталкивания запасов. Оптовики часто выталкивают в розничную торговлю товары и услуги независимо от того, сможет розничный торговец реализовать их или нет. Розничный продавец, в свою очередь, выталкивает товары и услуги к вам, не интересуясь, необходимы они вам сейчас или нет. В результате у вас скапливается избыточное количество запасов, которые в данный момент вам не нужны, да и сам розничный продавец тоже вынужден держать огромные запасы.
Теперь представьте, что упомянутая интернет-служба, получив множество претензий, решила усовершенствовать систему обслуживания. Они прислали вам специальный передатчик, на котором есть кнопка для каждого из нужных вам продуктов. Когда вы открываете новую бутылку молока или коробку яиц, вы нажимаете соответствующую кнопку. На следующий день вам доставят ровно столько продуктов, сколько вы распаковали. В результате у вас будет одна распечатанная упаковка плюс еще одна. Запасы будут, но очень небольшие. Если вы знаете, что вам понадобится много молока, вы можете просто зайти в Интернет или позвонить, и вам немедленно доставят то, что нужно. Сама компания пересмотрела соглашения с поставщиками молочных продуктов. Если потребители заказывают много продуктов, компания сообщает об этом поставщикам, и они привозят продукты в количестве, которое не превышает требуемое. Это пример системы «вытягивания». Вы получаете то, что вам нужно, только когда понадобится, а розничный продавец заказывает продукты с учетом потребительского спроса. Полагаю, чтобы избежать выталкивания, вы бы согласились заплатить за обслуживание «по требованию» немного больше.