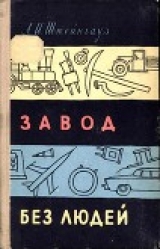
Текст книги "Завод без людей"
Автор книги: Александр Штейнгауз
сообщить о нарушении
Текущая страница: 8 (всего у книги 10 страниц)
Электроника – очень молодая отрасль науки и инженерной техники. Еще, пожалуй, не существует точного определения ни самого понятия, ни круга задач и предмета электроники. Но это не мешает ей бурно развиваться.
Для решения своих задач электроника использует многие физические, электротехнические и электромеханические устройства. Именно благодаря этому электроника становится одним из главнейших орудий в деле автоматизации разнообразнейших процессов. Только в связи электроники с электромеханикой и механикой можно видеть причину ее универсального применения. Потому что механика всегда была и будет основой основ подавляющего большинства технических устройств.
Я люблю читать фантастические повести и рассказы. Только люблю хорошие, умные читать. А иногда попадаются наивные, технически и художественно безграмотные книги. Читаешь – и не знаешь, удивляться им или возмущаться. Помню, прочитал я одну из них, переводную, про изобретателя. У этого изобретателя в доме все было автоматизировано, прямо-таки не дом, а помещение для спиритических сеансов: двери сами открывались, из шкафов выдвигались ящики, автомобиль без шофера ездил, автоматически включался и выключался свет.
Как только я начал читать про автоматические дверцы шкафов и прочую чепуху, меня такая злость взяла, что я и читать эту книжонку бросил. А вместо этого принялся мысленно сочинять свой научно-фантастический роман, в котором автор недочитанной мной книжки попал в описанную им автоматизированную квартиру. Дверцы шкафа и обычные двери автоматически открывались и били его.
И прочие приключения пришлось испытать этому писателю. Только после этого я успокоился.
Гораздо хуже бывает, когда в жизни встречается такой обуреваемый страстью к стопроцентному охвату автоматизацией человек. Дай ему только свободу и возможность, и он миллионы рублей истратит для автоматизации никому не нужных вещей.
Ведь автоматика и электроника очень дороги. Необыкновенно дороги. И их выгодно применять только там, где без них нельзя обойтись и где их применение полностью себя оправдывает и окупает. Автоматизировать же дверцы буфета, за которыми спрятано двести граммов любительской колбасы да банка «Бычков в томате», – абсурд. Помимо того, что эта автоматизация встанет гораздо дороже всего содержимого буфета и самого буфета в придачу, она еще займет порядочно места и будет потреблять порядочное количество электроэнергии. И, главное, бессмысленно ее применять! Что, у людей будущего рук не будет, что ли?!

Незадачливый изобретатель.
Вот стоит токарный револьверный станок. На нем не револьверы, конечно, делают. Это станок-полуавтомат, то есть такой, в котором для производства смены операций и холостых ходов необходимо участие человека. Назван он револьверным потому, что у него вместо задней бабки стоит поворотная, револьверная, головка, в которой закреплен набор инструмента, необходимый для производства нужных операций по обработке металла. При нажатии на специальный рычаг головка поворачивается в нужной последовательности и подходит к заготовке, начиная обработку.
За станком работает молодая женщина. Каждое движение точное, рассчитанное. Все движения следуют одно за другим со строгим и сложным ритмом. Работница уже выработала в себе автоматизм движений и словно слилась со станком; даже может петь или мечтать о чем-нибудь. Она может часть своего внимания переключить на это, потому что станок делает сам почти все.
Но, к сожалению, еще не все. И приходится станок обслуживать человеку, станочнику. Станочник это уже не токарь-универсал и не имеет высокой квалификации. Он станочник. Его можно обучить за очень малое время. Скажем, за месяц или даже меньше. Работа почти автоматическая и, конечно, очень напряженная.
Стоит в таком случае применить автоматизацию? Несомненно! И это будет благородная и важная задача – автоматизировать станок, освободить человека от выполнения роли автомата при станке.
Давайте посмотрим на другой станок. Ну хотя бы на одношпиндельный токарный автомат.

Одношпиндельный револьверный станок.
По существу, он очень близок к токарному револьверному станку.
Но теперь вместо человека им управляет специальный программный механизм. Этот программный механизм приводится в движение самим станком и, в свою очередь, управляет рабочими органами станка. На долю человека остается только настраивать и регулировать станок, включать и выключать его, подавать прутки металла и разгружать бункер, в который сбрасываются готовые детали. Можно автоматизировать и питание станка и сбор готовых деталей. Тогда человек полностью освободится от тяжелой и однообразной работы. Он должен будет выполнять работу по управлению станками-автоматами, по их наладке. Такой труд совсем другого рода – умный, высококвалифицированный. И, что не менее важно, применение станка-автомата позволяет значительно увеличить производительность труда.
Автоматика полным ходом вводится и у нас и в капиталистических странах. Но цели введения автоматики в странах капитала и в социалистических странах разные. Мы, в нашей стране, действительно стремимся облегчить труд людей, освободить их от выполнения тяжелой физической работы. И это – наша главнейшая задача. Для этого и коммунизм строится. А вот в капиталистических странах, в частности в США, многие люди, от которых зависит развитие промышленности, спокойно смотрят на существование тяжелого физического труда. Их беспокоит главным образом повышение прибыльности работы. И они вводят автоматизацию там, где это необходимо для повышения прибылей. Если при этом тяжелый физический труд остается, их такое не тревожит.
Но есть в США честные ученые и инженеры, которые хотят облегчить жизнь и труд своим соотечественникам. Надо думать, их большинство, таких, умеющих много и великолепно работать, изобретательных и настойчивых людей. Никто не собирается умалять их достоинств. Но дело-то в основном не в них, а в тех, на кого приходится работать этим ученым и инженерам. Дело в капиталистах, им же нужно только одно – прибыль. И если удается инженерам и ученым не только в США, но и в других капиталистических странах создать машину, облегчающую труд рабочего и в то же время дающую прибыль, значит, удача, повезло рабочим? Да только необязательно! Каждая новая машина, повышающая производительность труда, при капитализме грозит рабочему более страшным, чем самый тяжелый физический труд, – безработицей.
И часто получается в капиталистических странах так, что честный инженер или ученый, создававший машину с самыми лучшими намерениями, оказывается виновником того, что многие-многие люди не радуются ее появлению, но, наоборот, оказываются без работы или под угрозой ее потери. Конечно, фактически виноваты в этом не изобретатели, а сама капиталистическая система.
Вот что недавно писал в журнале «В защиту мира» М. Инкер:
«Сами конструкторы „мыслящих“ машин, по-видимому, не вполне отдают себе отчет в том, какие возможности сулит все то, что они изобретают. С точки зрения технической, автоматизация приводит к огромной экономии времени, к сокращению всяких простоев или задержек, вызываемых административными и прочими неполадками. Что касается чисто экономической области, то автоматизация снижает себестоимость продукции, однако объем производства должен поддерживаться на высоком уровне, а сбыт происходить бесперебойно, всякие колебания рынка грозили бы дорогостоящей остановкой автоматических заводов. Плановое производство становится настоятельной необходимостью во всех странах, избирающих путь автоматизации, но известно, что планирование хозяйства не при всех экономических системах возможно в одинаковой степени.
О масштабах возможных социальных последствий до сих пор еще идут споры, и люди по-разному реагируют на это, в зависимости от того, кто перед нами, хозяин предприятия или рабочий, заставляет его автоматизация менять свой род занятий или нет».
И далее:
«Но вот дирекция решает автоматизировать изготовление блока цилиндров и поршней, все операции по хромированию и покраске. Сразу несколько тысяч квалифицированных и подсобных рабочих оказывается за воротами завода.
Именно в таком плачевном положении оказались недавно рабочие английской автомобильной промышленности. Причина не в замедлении темпов или полном прекращении производства. Наоборот, к автоматизации прибегают, чтобы производить больше, лучше, быстрее и дешевле. Именно эту цель и ставили перед собой, несомненно, английские предприниматели, но цель английских рабочих заключалась в том, чтобы иметь „работу и хлеб“ и даже, пожалуй, „несколько меньше работы и больше хлеба“. При существующей в Англии системе выявилось такое резкое расхождение между целями предпринимателей и рабочих, что в результате вспыхнул острый социальный конфликт».
Вот, например, что заявил производственный директор английских автомобильных заводов «Стандард моторс» Аллен Дик при увольнении 2900 рабочих: «Мы затратили четыре миллиона фунтов стерлингов не для того, чтобы держать на заводе прежнее количество людей».
В ответ на увольнение своих товарищей рабочие объявили стачку, которая в Англии получила название «первой стачки эры роботов». При поддержке рабочих многих предприятий эта стачка была выиграна. Но так бывает далеко не всегда, и многие рабочие в капиталистических странах понимают это. Вот что написал французский рабочий-металлист с завода «Орн»:
«Мы знаем опасность роста производительности: снижение заработной платы по сравнению с количеством выжатого труда и безработица. В 1952 году на нашем заводе работали 900 рабочих, производивших 700 тонн в месяц. В 1956 году было 590 рабочих, и производили они 1200 тонн. Продукции стало на 500 тонн больше, а рабочих на 360 человек меньше. Новая реконструкция предполагает дальнейшее увеличение продукции и сокращение персонала… Вот почему, товарищи, надо поставить машину на службу человеку. Сегодня же она служит лишь тому, чтобы обогащать тресты, вроде нашего, уменьшает покупательную способность населения, приводит к навязыванию невыносимых темпов и преждевременному изнашиванию рабочих».
У нас машина служит всему народу. Мы не боимся автоматизации производства. Мы приветствуем ее и огорчаемся, что она внедряется не так быстро, как хотелось бы. Но с каждым годом она начинает играть все более важную роль в самых различных областях промышленности. Множество ученых, инженеров, рабочих, крупнейшие научно-исследовательские институты, заводы – все занимаются исследованиями и созданием разнообразнейших автоматических устройств.
Автоматизация только начинается, ведь мы еще многого не знаем и не умеем. Мы не знаем, как заменить человека во множестве случаев. А в тех случаях, когда мы уже знаем, мы часто не можем это сделать достаточно хорошо, надежно и дешево.
А о стоимости и выгодности введения автоматизации надо очень много думать в каждом случае, прежде чем ее применить. Не то, вместо того чтобы помочь народу стать богаче, можно лишь растратить лишние средства. А мы не имеем на это права. Мы должны по-настоящему, по-хозяйски беречь наши деньги, деньги, созданные нашим трудом, трудом всего нашего великого народа.
Сейчас автоматизация распространяется все шире и шире. В производстве, в частности в металлообрабатывающей промышленности, ее особенно выгодно применять, когда приходится вести обработку очень больших количеств однородной продукции, то есть при массовом производстве.

Автоматическая станочная линия для обработки блока цилиндров.
Именно массовое производство подготовило базу для широкого внедрения автоматизации в промышленность. Помимо экономических предпосылок, массовое производство способствовало возникновению и развитию автоматизации и тем, что оно подготовило должную организацию промышленности: поточный метод, расчленение производственных операций на простейшие, которые легко выполнять специализированными станками и уже легко автоматизировать.
Многие предприятия, выпускающие массовую продукцию, используют большое количество автоматических станков. Таких станков было уже порядочно и перед второй мировой войной. Но развитие промышленности требовало все большей и большей автоматизации. От отдельных станков-автоматов стали переходить к целым линиям автоматических станков, объединенных между собой единым транспортным устройством и общим для всей линии темпом работы. Такие линии получили название автоматических.
Первая автоматическая линия была пущена перед самой войной, в 1939 году. Она была построена на Сталинградском тракторном заводе. Ее создал рабочий этого завода И. П. Иночкин.
Вот что пишет об Иночкине журналист И. Пешкин:
«Иван Иночкин поступил на Сталинградский тракторострой сразу после военной службы. Служил он не в строевой части, а в оружейной мастерской в Сестрорецке. Там он приобрел квалификацию слесаря. Ему приходилось ремонтировать пулеметы, знаменитые „Максимы“, и это было первым его знакомством с автоматикой.
На тракторный Иночкин попал незадолго перед пуском. Он участвовал в монтаже американского оборудования, а затем остался работать на участке гидравлических станков фирмы „Ингерсол“. Эти станки были трудны в наладке, но работа на них не требовала никакой квалификации – только ставь и снимай детали.
Иночкин довольно быстро овладел этими машинами. „Ингерсолы“ работали хорошо, они слушались Иночкина, но он был ими недоволен. Часами Иночкин простаивал возле подопечных станков и наблюдал, как рабочие их „кормят“. Однообразная, отупляющая работа! Весь цикл обработки детали совершается без всякого участия рабочего, но рабочий, словно каторжник к тачке, прикован к станку.
Так не поручить ли „кормление“ станков какому-то механизму? Аналогия с пулеметом, на котором лента „кормит“ ствол, только дала толчок мысли – что надо бы сделать.
Иночкин решил создать „механическую руку“. Попытка механически воспроизвести цикл движений человеческой руки была вполне естественной. Иночкин шел тем же путем, каким шли многие создатели новых машин. Вспомним, что предшественник стефенсоновского локомотива имел ноги, которые он попеременно поднимал, как лошадь. Сделать „механическую руку“ оказалось непростым делом. Изобретатель познал много горьких поражений, но не сдался.
Первая „механическая рука“ оказалась слишком сложной. Вторая была немногим проще. Снова думы, наблюдения, догадки… И наконец явилась новая, удивительно простая идея: использовать в качестве средства транспортировки деталей обыкновенную цепную передачу. Иночкин обратил внимание на конфигурацию деталей – это были пальцы гусеницы, – они имели форму тел вращения. Раз так, то они могут сами переходить, точнее – перекатываться со станка на станок.
На этом принципе и была построена первая в нашей стране к, как утверждают, – во всем мире – автоматическая линия».
Автоматические линии сейчас начинают очень широко применяться во многих отраслях промышленности: при изготовлении деталей двигателей внутреннего сгорания, подшипников, для резки листового металла; применяют их очень широко при изготовлении электронных и осветительных ламп, на хлебопекарных заводах, на заводах радиотехнической промышленности, в полиграфии, в кондитерской промышленности, словом, – везде, где только происходит выпуск массовой продукции.
Особенно выгодно строить автоматические линии и даже целые заводы для выпуска не просто массовой продукции, но и стабильной, такой, которая выпускается почти неизменной или вовсе неизменной в течение длительных промежутков времени. Таковы, например, подшипники. Они выпускаются уже долгие годы и, вероятно, не скоро будут заменены какими-либо другими, более эффективными устройствами. Во всяком случае пока такие устройства не изобретены и в них даже не ощущается особой необходимости. Значит, для производства подшипников можно изготовлять даже очень дорогое, сугубо специализированное оборудование: оно окупит себя.
Советские инженеры добились выдающихся успехов в деле создания автоматических линий для производства подшипников.
В начале первой пятилетки в нашей стране не было подшипниковых заводов. Подшипники, как и многое другое, в те годы мы вынуждены были завозить из-за границы. Когда встал вопрос о строительстве советского подшипникового завода, многие специалисты не верили, что завод этот будет работать. Они боялись, что такое тонкое, сложное и необыкновенно точное производство не может быть налажено у нас. Они думали, что в нашей стране не найдется для этого достаточно квалифицированных людей.
Действительно, таких людей в те годы очень не хватало. И поэтому строительство и оборудование первого подшипникового завода, так же, как и Сталинградского тракторного и Горьковского автомобильного и Днепрогэса и многих других строек первой пятилетки, пришлось вести с помощью иностранных специалистов и фирм. Шведы и американцы не стали оказывать нам техническую помощь в производстве подшипников. Тогда пригласили группу итальянских инженеров.
19 января 1932 года был выпущен первый советский подшипник. В этот день состоялся пуск Первого Государственного подшипникового завода.
Завод был оборудован итальянскими станками, их наладкой руководили итальянские специалисты. И станки и консультанты принадлежали капиталистической фирме. И, несмотря на то что станки были установлены на советском заводе, они не изменили своей сущности. Они были запроектированы таким образом, что рабочий, обслуживающий их, становился придатком машины, по существу сам становился машиной. Итальянские консультанты считали такое положение дела правильным. Но наши рабочие и специалисты не могли мириться с ним.
На ГПЗ нашлись люди, которые, подобно Иночкину с СТЗ, начали задумываться над путями облегчения труда советских рабочих. И здесь начали с того же, что делал Иночкин: при передаче деталей от станка к станку стали заменять человека механизмами. Так и на ГПЗ появились первые полностью автоматизированные станочные линии.
В 1955 году на Первом ГПЗ был введен в эксплуатацию цех-автомат, выпускающий подшипники массового применения. Его проектирование было начато пятью годами раньше. В проектировании цеха, создании нового технологического процесса, нового оборудования участвовали сотни инженеров, четырнадцать заводов изготовляли станки, контрольно-измерительные устройства, инструменты.
К сожалению, я не бывал на ГПЗ в послевоенные годы. Поэтому я обращусь к очень интересной статье И. Пешкина. Вот что он пишет о новом цехе-автомате:
«Цех-автомат расположен в отдельном здании. Мы входим в него. Ряды одетых в серые кожухи станков. Возле них нет людей.
Подходим к одному из станков. За прозрачным из плексигласа щитком можно увидеть, как металлические пальцы зажимают кольцо. Вьется, дробится и падает вниз стружка. Работа окончена. Механизм поворачивается, освобождает кольцо, оно покатилось по транспортеру.
Станки работают сами. Все, что необходимо для работы, само приходит к станку; обработанные изделия и стружка сами уходят.
Оборудование и запроектированные технологические процессы несомненно отражают последние достижения технической мысли. На токарных автоматах – высокая концентрация инструмента. Хорошо решена проблема удаления стружки. Агрегаты термической обработки колец (теплом и глубоким холодом) встроены в линии. Высокопроизводительные шлифовальные станки обеспечивают доводку колец до необходимых размеров. „Магазины“, установленные при переходе с токарных станков на термообработку и с последней на шлифование, удачно разрешают труднейшую из проблем – обеспечение бесперебойного действия всего цеха в случае неисправностей в каком-либо звене.
И уж, конечно, наибольший интерес вызывают измерительные станции. На этих участках использованы последние достижения электроники и мерительной техники.
Вот транспортер внес кольцо в остекленный шкаф– контрольно-измерительную станцию, оно проходит первую проверку, затем вторую, третью, четвертую.
Сделаны четыре остановки. Все хорошо? Нет, этот вывод преждевременен. Результат измерений, произведенных каждым из автоматов, остается еще неизвестным, он пока „запоминается“ специальным устройством.
В конце путешествия кольцо подходит к висящему между двумя лотками электромагниту. Результаты измерения „запоминающие“ устройства автоматов передают электромагниту, он взвешивает эти данные и решает, можно ли пустить кольцо на сборку.
Повисев на магните, кольцо ложится на транспортер, который везет его к сборочному автомату. Все ясно: размеры выдержаны. Магнит пропускает и второе кольцо, и третье, и четвертое… Но приходит еще одно кольцо, и магнит бросает его на лоток, оттуда оно попадет уже на „штрафной“ транспортер, который отвезет его в изолятор.
На каком из четырех автоматов обнаружена неточность? Мы этого не знаем. Импульсонакопитель „запомнил“ это кольцо, и магнит беспощадно выбросил его из потока.
А вот еще одно „чудо“ – автомат для сборки шариковых подшипников. При старых методах сборки к шарикам определенной группы подбирали кольца. На автоматической сборке применен обратный принцип: по зазору колец подбираются шарики необходимого размера. Автомат измеряет внутренний диаметр наружного кольца и наружный диаметр внутреннего. Счетно-решающее устройство делает необходимый расчет и дает ответ, какой шарик годится для данной пары колец. Задача решается моментально.
Собранные подшипники сами следуют дальше по предписанному маршруту. Они попадают в антикоррозийные агрегаты. Дальше – упаковочные автоматы. Подшипник заворачивается в промасленную бумагу и укладывается в изящную фирменную коробочку».
От автоматической линии недалеко и до полностью автоматизированного завода. Такие заводы, конечно, появились. Одним из первых был советский завод-автомат, выпускающий поршни для автомобильных моторов. В сутки этот завод выпускает от 3000 до 3500 изделий. Все производство обслуживают пять операторов в смену. На заводе-автомате автоматизированы не только производственные операции, но и все операции технического контроля и все подсобные операции.
Этот завод состоит из четырех основных производственных участков: плавильного, термического, участка механической обработки и участка сортировки и упаковки. Все участки связаны между собой транспортерами, которые работают точно в соответствии с ритмом производственных операций.
Давайте подробнее рассмотрим схему завода. Она изображена на рисунке.

Схема автоматического завода по производству поршней.
На завод поставляются алюминиевые чушки. Они хранятся на складе. Со склада чушки подаются по транспортеру в электропечь. Подаются они через строго определенные промежутки времени. В электропечи поддерживается неизменная температура. И, конечно, температура в печи поддерживается с помощью автомата – автоматического регулятора температуры. Из печи расплавленный металл прямо по желобу поступает в разливочную машину. Разливочная машина строго определенными порциями разливает металл в металлические формы – кокили. После заливки металлом кокили переносятся в охладительную камеру, где выдерживается нужный температурный режим. После охлаждения кокиль подается на автомат для отрезания литников – «хвостиков», получающихся из металла, застывающего не в самой форме, а в воронке, через которую заливают металл в кокиль. Отрезанные литники падают на транспортер, переносящий их обратно в печь для переплавки. После обрезки литников заготовки поршней поступают на второй – термический – участок.
Термический участок состоит из конвейерной печи, в которой поршни проходят термическую обработку, и автоматизированного пресса для определения твердости. Печь и пресс соединены транспортером. Пресс производит разбраковку поршней по твердости. Забракованные поршни сбрасываются в ящик, а годные попадают в бункер.
На третьем участке, участке механической обработки, куда поршни попадают под воздействием собственного веса по склизу, имеется первый оператор. Оператор устанавливает приходящие к нему поршни в загрузочные позиции автоматической станочной линии. В линии установлены токарные, сверлильные, фрезерные и шлифовальные станки. Эти станки автоматически выполняют все операции по механической обработке поршней. После обработки поршни транспортером подаются в агрегат, измеряющий их вес и сортирующий их по весу. Далее поршни поступают в автомат, где они лудятся. Отсюда поршни подаются на многопозиционный расточной станок, в котором окончательно растачиваются отверстия под палец поршня. Точность расточки очень высокая – до 0,01 миллиметра. Она автоматически контролируется. Здесь поршни попадают в руки ко второму оператору, перемещающему поршни на конвейер моечной машины.
После расточки отверстий поршня под палец поршни поступают в автоматическую сортировку по классу (по диаметрам отверстий для пальца, по диаметрам юбки поршня). На поршни ставятся соответствующие клейма. Разделенные по классам поршни отдельными потоками отправляются в упаковочный автомат и оттуда на склад готовой продукции.
На заводе имеется диспетчерский пункт. Он оборудован различными средствами сигнализации, учета, управления и контроля, позволяющими диспетчеру следить за всем производством.
Производительность труда при автоматизации, как мы можем видеть, возрастает во много раз, качество же ее, несмотря на то что продукция дешевеет, становится более высоким.
Пока еще подавляющее большинство станков-автоматов для металлообработки – автоматы особого типа. Это автоматы, не умеющие «думать». Если к станку перестанут подаваться заготовки, он не почувствует этого и будет производить те же самые операции, только вхолостую, в лучшем случае остановится. Но если, скажем, заготовки подаются, но какие-то их качества изменились и по ходу дела нужно, например, изменить режим резания, такие станки не сумеют этого сделать. Это происходит потому, что программа работы задана станку раз и навсегда при его проектировании и наладке. Перестроиться применительно к новым условиям и обстоятельствам такой станок не может.
К такого рода автоматам относятся, например, станки и устройства, которые вырабатывают подшипники массового применения, и станки и устройства автоматического завода, выпускающего поршни. И те и другие очень хороши для решения названных задач, но никаких других они решать не умеют. Да никто от них этого и не требует.
Но возьмем другой случай. Случай автоматизации такого производства, в котором выпускаемая продукция не является неизменной. Ведь создавать для такого производства высокоспециализированные автоматы может оказаться невыгодным или даже невозможным: труд инженеров и рабочих, затраченный на создание таких станков и их внедрение, превысит труд, необходимый для выпуска самой продукции с помощью обычных универсальных станков. Такое положение может часто возникать, например, на станкостроительных заводах, где продукция часто является не только нестабильной, но даже и немассовой. Как поступать в этом случае? Может, и вовсе отказаться от автоматизации?
До последнего времени на эти вопросы не было сколько-нибудь удовлетворительного ответа. И лишь совсем недавно в этом направлении были сделаны первые успешные шаги. Причем идея, на первый взгляд, противоречила всему тому, на чем прежде базировалась автоматизация. Потому что она заключается в отказе от применения высокоспециализированных станков-автоматов и в возврате к станкам универсальным. Самая же главная мысль этой идеи состоит в том, что управление универсальным станком будет поручено не человеку, а автомату – так называемому автомату с программным управлением.
Этот автомат без всяких переделок и изменений можно будет легко и просто переводить на выполнение различных работ. Так как такой автомат управляет универсальным станком, то можно будет осуществлять автоматическое управление весьма разнообразными операциями. И при этом не потребуется строить специальные станки для каждого вида операций. Достаточно лишь управляющему автомату задать новую программу – и сразу можно будет приступать к выполнению работы. Программа же в таком автомате представляет собой либо магнитную, как в магнитофоне, либо бумажную, либо похожую на кинопленку ленту. На такой ленте либо с помощью магнитных полей, либо в виде отверстий или каким-нибудь другим способом наносятся команды – программа управления автоматом и станком.
Противоречит ли такой путь автоматизации старому пути? Нет. Просто каждый из них хорош в своей области.
Очень интересным свойством некоторых автоматических станков с программным управлением является умение «думать». Они по ходу выполняемой работы могут изменять режимы работы и даже изменять последовательность операций. Более того, программы некоторых видов работ не могут быть заранее созданы расчетным путем. В таких случаях станок-автомат отдают в «обучение» к опытному рабочему. Чувствительные элементы автомата подключают к соответствующим частям станка, на котором работает рабочий. Эти чувствительные элементы преобразуют измеряемые данные и приемы работы «учителя» в электрические сигналы и передают их в автомат, запоминающий все операции и их последовательность. После такого «обучения» автомат сам может управлять работой станка.
Не зря эти станки называют «думающими». Они, как человек, могут обучаться у другого автомата или человека. Появились они в последние годы и своим рождением обязаны новейшим достижениям науки и техники. На их основе зародились новые отрасли математики и электроники, занимающиеся созданием математических и логических быстродействующих электронных машин. Одними из важнейших в таких машинах являются запоминающие, или накопительные, устройства. Их емкость в новейших машинах очень велика и позволяет запоминать огромное количество данных. Эти данные могут быть самыми разнообразными, например данными о последовательности операций, совершаемых станком. При работе они выдаются из устройств памяти в виде электрических сигналов в блоки машины, производящие с сигналами логические или математические операции. Полученные результаты могут быть выданы в виде команд управления станком.
Автоматизация применяется не только в машиностроительной промышленности. Не менее широко она применяется в металлургической промышленности, в химической, в энергетике, в связи, на транспорте, в легкой промышленности и в военной технике. Автоматизация стала все больше проникать и в области, непосредственно не связанные с производством; очень много автоматических средств применяется в науке: автоматы производят сложнейшие математические вычисления, сортируют корреспонденцию на почтамтах, сортируют и классифицируют разнообразные архивные материалы, составляют библиографии, ведут бухгалтерские расчеты и учет и еще очень многое. И в этой области машины-автоматы позволяют сократить большое количество труда, переместить работников из сферы управления и обслуживания в сферу производства.