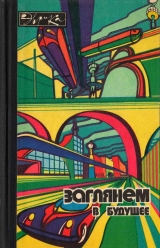
Текст книги "Заглянем в будущее"
Автор книги: Александр Китайгородский
Соавторы: Арон Кобринский,Натан Кобринский,Николай Семенов,Николай Петрович,В. Молярчук,Игорь Петрянов-Соколов
сообщить о нарушении
Текущая страница: 4 (всего у книги 16 страниц)
Фронт научно-технического прогресса сейчас имеет такую протяженность и продвигается с такой скоростью, что нет ни возможности, ни даже смысла пытаться побывать на всех его участках, даже если речь идет не обо всем производстве в целом, а только об отдельных его отраслях.
Единственный путь, который нам остается, – это выбрать одну из наиболее важных отраслей и попробовать охарактеризовать ближайшее будущее этой отрасли, определить главное направление, по которому идет ее развитие.
Марксизмом-ленинизмом научно доказано, что исторически исходным пунктом создания материально-технической базы социализма и коммунизма является крупное машинное производство.
Машиностроение – сердцевина такого производства, поставляющего ему необходимые орудия труда и обеспечивающего эффективное высокопроизводительное выполнение технологических процессов. Современные тенденции науки и техники показывают, что основным направлением в развитии орудий труда является последовательная замена машин, требующих ручного управления, автоматами.
Итак, автоматизированное машинное производство, автоматизация технологических процессов – вот та база, которая должна образовать прочный фундамент будущего коммунистического общества. Теперь мы добрались до одной из важнейших проблем научно-технического прогресса, на решение которой сейчас партия и правительство направляют большие средства и концентрируют усилия нашего общества.
Автоматизация – вот тот важнейший участок, на котором фронт научно-технического прогресса продвигается быстрыми темпами. Автоматизация уже глубоко проникла в самые различные отрасли производства. Сегодня существуют автоматизированные электростанции, нефтеперерабатывающие и химические заводы, автоматизированные участки. Только за первые два года девятой пятилетки в промышленности СССР внедрено более трех тысяч автоматических линий, проектируются, строятся и внедряются сотни и тысячи типоразмеров автоматических машин и оборудования, обрабатывающих металл, пластмассы, дерево, изготавливающих пищевые продукты, лекарства, папиросы, сигареты, спички, посуду – сотни, тысячи наименований изделий, которые во все расширяющемся ассортименте требуются в сферах производства и потребления.

Но для нас сейчас важно не столько убедить себя и читателя в том, что уровень автоматизации производства непрерывно возрастает. Главная наша задача состоит в том, чтобы вскрыть определенное противоречие, свойственное этому процессу, и указать пути его преодоления, по которым идет современное производство.
Десятки тысяч осин и елок поступают на лесопилки спичечных фабрик. И ежедневно вывозятся с фабрик вагоны ящиков, наполненных коробками спичек.
Автоматы делят бревна на чурки определенной длины, с помощью широких ножей «развертывают» чурку в бесконечную ленту, примерно так же, как раскручивают бинт, прессуют эту ленту стопками и рубят из нее так называемую соломку. Соломка должна быть пропитана специальным составом, чтобы спичка горела без тления; затем ее надо высушить, очистить, отполировать и отделить брак. Только после этого начинается процесс превращения соломки в спички.
Все это делают автоматы. А к моменту, когда спичка готова, другие автоматы изготавливают и подают к набивному автомату коробки. Можно сказать, что к коробку спичек на довольно долгом пути его изготовления не притрагивается рука человека, так же, как она не притрагивается к продукции хлебозавода-автомата, к пакету молока, коробке консервов.
Между сырьем и готовой продукцией выстраивается целый комплекс узкоспециализированных автоматов, автоматических линий, автоматического оборудования. Только благодаря этому вы можете в любом табачном киоске за одну копейку купить красивую коробочку довольно сложной конструкции (попробуйте присмотреться, как она устроена!), набитую пятьюдесятью спичками.
Но прежде чем воспользоваться преимуществами автоматизированного процесса, необходимо создать тот самый комплекс оборудования, который этот процесс обеспечивает. Конечно, можно представить себе узкоспециализированные заводы-автоматы, производящие только автоматы для производства спичек, и другие заводы-автоматы, которые выпускают только автоматы для изготовления сосисок, и третьи – только для конфетных автоматов и т. д.
Однако наивность такой картины машиностроительного производства очевидна с первого взгляда. Ведь спички и хлеб, газеты и книги, мануфактура, гвозди и электролампочки производятся ежегодно, ежедневно и ежечасно миллионами и миллиардами штук, экземпляров, метров и килограммов, причем конструкция этих изделий сравнительно проста и годами и десятилетиями остается неизменной либо меняется не очень существенно. В этих условиях строить для их производства автоматические линии, цехи, заводы-автоматы имеет прямой смысл. А машины и автоматическое оборудование, выпускающие подобную массовую продукцию, нужны в несоизмеримо меньших количествах, зачастую их приходится строить в единичных образцах или сериями в тысячи, сотни или десятки штук. И, кроме того, они, как правило, чрезвычайно сложны по конструкции, нередко состоят из тысяч и десятков тысяч деталей, «морально» очень быстро устаревают, в силу чего должны непрерывно совершенствоваться. Это, в свою очередь, неизбежно связано с изменениями их устройства, принципов действия и конструкции.
Чем шире внедряется в различные отрасли производства автоматизация, тем шире номенклатура необходимых для этого машин, автоматов и автоматических линий, устройств, приборов.
Ясно, что создавать для их производства узкоспециализированное оборудование бессмысленно. Если же для их проектирования, изготовления и модернизации пытаться использовать обычные универсальные методы, средства и технику, то производство автоматического оборудования потребует затрат таких средств, времени и квалифицированного человеческого труда, что «овчинка не будет стоить выделки».
В этом и состоит противоречие, свойственное широкому внедрению автоматизации. А разрешить его можно лишь единственным путем. Массовая продукция выпускается и будет выпускаться высокопроизводительными автоматическими и автоматизированными производствами, принципы создания которых уже становятся общепринятыми, традиционными. А оборудование для этих производств должно производиться с использованием новых, нетрадиционных методов и техники.
Эти методы и техника должны быть высокоэффективными, когда речь идет о производстве и обработке деталей и изделий, выпускаемых и единичными образцами, и малыми и большими сериями. Они должны быть готовы к быстрому переходу от производства одного вида продукции к другому виду, от деталей одного типа к деталям другого типа. Эти методы и техника должны совмещать в себе гибкость и приспосабливаемость обычного универсального оборудования, обычных токарных, фрезерных, расточных и других станков, требующих для своего обслуживания квалифицированных станочников, с точностью и производительностью автоматических машин, действующих без непосредственного участия человека.
За истекшую четверть века такие методы и техника также разработаны. Это методы цифровой автоматизации: машины, станки и оборудование с цифровым управлением.
Современный станок с цифровым управлением работает по программе, носителем которой обычно служат специальные магнитные ленты, примерно такие же, что используются в магнитофонах.
Невидимые глазу сигналы, записанные на эти ленты, управляют движением всех рабочих органов станка, движением резца, фрезы, заготовки. В результате этих движений производится обработка изделий.
Универсальные станки обычного типа можно сравнить с роялем. На нем можно исполнять самые различные произведения, но… нужен квалифицированный пианист. Станкам нужен токарь, фрезеровщик. Узкоспециализированный автомат можно сравнить с шарманкой, пусть самой высококлассной по исполнению. Она играет всегда одну и ту же мелодию. А станки с цифровым управлением – нечто вроде магнитофона. Чтобы его пустить в ход, нужна только программа – лента, несущая набор отметок. Станок «поймет» их и автоматически обработает соответствующее изделие. А если понадобится обработать другое изделие, то достаточно заменить ленту, установить новую заготовку, заменить инструмент.
Такой автомат действительно приобретает в значительной мере те свойства, которыми обладает система, состоящая из универсального станка и высококвалифицированного станочника, – приобретает универсальность. А производительность этого автомата несравненно выше – он не утомляется, не отвлекается, ему не надо «привыкать» или «переучиваться» при переходе от обработки одного изделия к обработке другого.
Цифровые методы автоматизации как нельзя лучше отвечают двум сформулированным ранее принципам. Они не только обеспечивают экономию дорогостоящего ручного труда, они обеспечивают удовлетворение все растущих требований к разнообразию продукции машиностроительного производства – разнообразию, которое, в свою очередь, диктуется все растущими потребностями в отношении разнообразия потребительских благ.
Станки и оборудование с цифровым управлением эффективно решают одну из важнейших задач автоматизации машиностроительного производства. Вот почему созданию этих систем уделяется такое внимание как у нас в стране, так и за рубежом.
У читателя может возникнуть естественный вопрос: а как быть с программами, откуда их брать?
Станки с цифровым управлением – детища электронных цифровых вычислительных машин ЭВМ. ЭВМ берут на себя львиную долю труда при подготовке программ, и только благодаря этому идея цифрового управления машинами могла быть воплощена в жизнь. Как участие человека в работе обычных станков сделало их универсальными, так «участие» электронных вычислительных машин сделало универсальными автоматы с цифровым управлением.
Четверть века назад была начата их разработка. Лет пятнадцать назад первый этап создания станков нового типа был более или менее завершен. В 1960 году во всем мире насчитывалось, вероятно, не больше 200–300 станков с цифровым управлением. В 1962 году в США находилось в эксплуатации 1500 станков с цифровым управлением, в 1964 – свыше 4000, в 1967 – 10 000, к настоящему времени свыше четверти всех выпускаемых станков оснащается системами цифрового управления. Эта картина широкого развертывания фронта работ в области цифровой автоматизации характерна не только для США и нашей страны, но и для ряда других высокоразвитых стран. Именно она и определила одно из важнейших направлений в области научно-технического прогресса за истекшую четверть века. Но, как ни много уже достигнуто в этой области, сделаны лишь первые шаги. Возможности методов и средств цифровой автоматизации не только не исчерпаны, их применение фактически только еще началось. Можно с уверенностью сказать, что в 2000 году инженеры и технологи на наше оборудование с цифровым управлением, на его современные возможности и широту использования будут смотреть примерно так же, как современные авто– и авиастроители смотрят на первые автомобили и аэроплан братьев Райт, то есть с доброй и насмешливой улыбкой.
Предстоящая четверть века будет характеризоваться в первую очередь гигантским количественным скачком в области производства станков и машин с цифровым управлением, расширением их типажа и номенклатуры. Станки типа так называемых «обрабатывающих центров», оснащенные целыми наборами режущего инструмента, включающими десятки резцов, сверл, метчиков, разверток и т. д., могущих без перестановки заготовки выполнить над ней по заданной программе десятки различных операций, высокоточные и высокопроизводительные станки для изготовления самых сложных деталей и изделий из легких сплавов и из высоколегированных сталей, для механической обработки, для газовой резки и штамповки. Подобное оборудование сейчас разрабатывается, уже имеется на производстве и будет строиться многими тысячами.
Но главное, конечно, не в этом количественном скачке, неизбежность которого очевидна сейчас.
Цифровая автоматизация, пусть пока очень робко, но уже захватывает самые различные звенья технологического процесса.
Технологический процесс машиностроительного производства – это не только обработка деталей. Это длинная цепь операций и действий, включающая самые различные этапы: и непосредственно разработку самого процесса, и выборы оптимальных режимов резания, и распределение припусков на обработку деталей, и контроль заготовок перед обработкой, и контроль обработанных деталей, и сборку изделий.
Сейчас выполнение многих из этих процедур требует применения человеческого труда – труда квалифицированного и в больших количествах. В ближайшей перспективе этот живой труд должен быть и будет заменен системами, действующими на «цифровых механизмах».
На нескольких примерах попытаемся показать читателю новые идеи, принципы их применения, которые сегодня разрабатываются и совершенствуются, а в недалеком будущем получат широкое применение в машиностроительном производстве.
* * *
Программу для станков с цифровым управлением считает ЭЦВМ. Все данные для подготовки программы сегодня задает человек. Первое, второе, третье, сотое изделие станок обрабатывает по одной и той же программе.
Хорошо, если человек может составить программу так, чтобы получить от станка максимум того, на что этот станок способен в отношении точности и производительности. Было бы хорошо, если бы программист и технолог знали, как будут деформироваться станок, инструмент и изделие в процессе обработки (а такие деформации происходят обязательно). Хорошо, если бы они смогли предсказать, как с течением времени будут изнашиваться резец, фреза или какой либо другой режущий инструмент (а износ инструмента происходит в процессе работы непрерывно). Хорошо, если бы им было известно, как по мере работы разогреваются узлы станка и каково в результате этого нагревания влияние температурных деформаций на результаты работы машины. Вот если бы они все это могли предвидеть и учесть в программе, тогда бы десятое и сотое изделие на станке было бы обработано оптимальным образом. Но ни технолог, ни программист всех этих подробностей не знают сегодня, не будут знать завтра, ни, вероятно, даже в отдаленном будущем. Да и особой необходимости в том, чтобы все это знать во всех подробностях, наверное, не будет.

Создающиеся сейчас так называемые самонастраивающиеся, или адаптивные, системы обеспечат работу станков в оптимальном режиме без вмешательства человека. Они будут уметь накапливать, обрабатывать и использовать информацию для достижения наилучших результатов. Системы специальных измерительных устройств и датчиков, собирающие данные о том, как протекает реальный технологический процесс, как деформируются станок, изделие, режущий инструмент, как изнашивается инструмент и как разогревается вся система, специальные вычислительные устройства, обрабатывающие эту информацию, дадут возможность автоматически корректировать ту исходную программу, которую автомат получил от технолога.
Другими словами, человек как бы задаст автомату цель. А как достичь этой цели, тот научится сам, с помощью искусственных органов чувств и цифровых механизмов. Только первое изделие из партии автомат обрабатывает по программе, заданной человеком. Потом, начиная с этого момента, он начнет накапливать и учитывать опыт работы, совершенствовать программу, обрабатывая второе, третье и последующие изделия с предельной точностью либо в максимальном темпе, либо с наивысшей экономичностью.
Естественно, что тот или иной из этих критериев, которым должен «руководствоваться» автомат в процессе работы, также задает человек. Но весь процесс поиска и настройки на оптимальную реализацию программы, вся та процедура, которая практически неосуществима традиционными методами, то есть на универсальных станках и с участием пусть даже высококвалифицированных операторов, будет выполняться в автоматическом режиме, обеспечивая высокие точности, производительность, экономичность.
Первые опыты по созданию и применению адаптивных систем цифрового управления станками уже проведены. Эти опыты показали высокую эффективность применения такого качественно нового вида оборудования. Несомненно, что в будущем оно получит широкое практическое внедрение.
Но вот изделие обработано по программе. Как убедиться в том, что оно обработано правильно, отвечает во всех подробностях чертежу, заданному конструктором?
Конечно, когда это изделие напоминает простой валик или шайбу, то задача может быть решена сравнительно просто. Если оно выпускается многотысячными, миллионными или миллиардными тиражами, то достаточно поставить специализированные высокопроизводительные контрольные автоматы; в других случаях выгодно обойтись универсальным измерительным инструментом.
Ну а как быть, если изделия обладают сложной конфигурацией, если они становятся все более разнообразными, требования к их точности все повышаются, а сроки изготовления сокращаются и если к тому же недостаточно измерить на этих изделиях 2–3 размера, а необходимо иметь картину точности обработки всех их поверхностей?
Применение традиционных методов контроля, предусматривающих изготовление специальных шаблонов, эталонов, привлечение высококвалифицированных контролеров сопряжены с большими затратами ручного труда, времени и средств, а строить специализированные автоматы для контроля таких изделий так же бессмысленно, как строить специализированные автоматы для их обработки.
Так наметилась еще одна качественно новая область применения техники цифрового управления – контрольные автоматы.
По принципу действия эти машины напоминают станки с цифровым управлением. Только вместо обрабатываемой заготовки на них устанавливаются измеряемые изделия, а вместо режущего инструмента – измерительный орган.
Технолог намечает на изделии все те участки, которые подлежат измерению; программист составляет соответствующую программу. Затем контролируемое изделие устанавливается в исходное положение, и автомат пускается в ход.
Измерительный орган скользит вдоль измеряемых поверхностей. Если эти поверхности выполнены неточно, измерительный орган, а за ним и приборы автомата регистрируют все отклонения. Как только вся программа «проиграна» – готов документ, зафиксировавший с высокой степенью точности всю картину обработки изделия.
Уже сейчас созданы и пришли на производство первые образцы контрольных автоматов с цифровым управлением. Они позволят значительно ускорить операции контроля самых сложных изделий и полностью исключить при этом субъективные ошибки человека, позволят обойтись без калибров, шаблонов и эталонов. Копии программ контроля можно будет рассылать по многим предприятиям, обеспечивая его единообразие и высокое качество.
Можно не сомневаться, что эти машины займут достойное место в области цифровой автоматизации машиностроительного производства.
Итак, самые различные станки, адаптивные системы, контрольные автоматы – агрегаты, оснащенные цифровым управлением. Но ведь их можно использовать не только порознь! Из них можно построить целые автоматические линии и комплексы. Такие автоматические линии будут качественно отличаться от автоматических линий традиционного типа, предназначенных для выпуска большими тиражами одних и тех же изделий. Линия станков, машин и другого оборудования с цифровым управлением, так же как и каждый отдельный ее агрегат, сочетает гибкость и приспосабливаемость универсального оборудования с точностью и производительностью специализированных автоматов.
Опытные линии станков с цифровым управлением уже построены. Представляется очевидной возможность включить в состав этих линий контрольные автоматы и адаптивные системы, значительно расширив тем самым уровень автоматизации машиностроительного производства и повысив его эффективность и качество. Перспективы внедрения линий и комплексов с цифровым управлением в различные отрасли машиностроения в ближайшую четверть века весьма широки и диктуются всем ходом научно-технического прогресса.
Автоматический комплекс с цифровым управлением может охватить не только процессы обработки и контроля изделий машиностроения.
Представим себе сборочный цех. Пусть здесь идет поточная сборка автомобилей (или других машин). Эта картина впечатляет своей ритмичностью: столько-то минут – автомобиль, еще столько же – автомобиль, еще – автомобиль, автомобиль, автомобиль… Однако она бывает «смазана» однообразием – с конвейера сползают автомобиль за автомобилем, ничуть не отличающиеся один от другого, ни одним из своих многочисленных признаков, ни единой деталью, ни цветом, ну абсолютно ничем. Получается это потому, что вся программа сборки определена на продолжительный срок.

Но ведь это не обязательно. Определение программы сборки и выполнение заказов на автомобили можно поручить цифровой машине. Ей безразлично, запомнить ли заказ на тысячу автомобилей или на один. Кстати, ей нетрудно запомнить и все те особенности машины, на которых настаивает заказчик. И дальше весь процесс сборки направляется цифровыми механизмами. В соответствии с особенностями очередного заказа на конвейер подается то красный кузов, то синий, то обычная «обувь», то тропическая, то обычный радиоприемник, то повышенного класса… Одновременно с этими деталями и узлами идет номер заказа – собранная машина не обезличена, она уже имеет адрес назначения.
Вновь и вновь методами цифровой автоматизации реализуются тенденции, отвечающие закономерностям, требующим экономии живого труда и все расширяющегося разнообразия благ. Следующая четверть века будет наверняка знаменоваться еще более широким внедрением и развитием этих методов. И на этом дело не остановится.
* * *
«Вмешательство» цифровых механизмов в процессы сборки, о которых сейчас шла речь, касалось не основных операций, а вспомогательных, связанных с управлением скоростью главного конвейера, а также конвейеров, подающих на сборку узлы и детали: то синий, то красный кузов, простую или специальную резину и т. д. А непосредственно сборку автомобиля ведут люди. Поступает на сборку автомобиля кузов – они ставят его на шасси, выполняя при этом множество операций, разнообразных движений – быстрых и плавных, размашистых и мелких, сильных и мягких; поступают на сборку колеса – нужны наборы других движений.
Автомобили и самолеты, мотоциклы и велосипеды, радиоприемники и телевизоры, тысячи других машин, их узлов и агрегатов собирают люди. На процессах сборки заняты буквально миллионы людей. Эти процессы требуют, как кажется, чисто человеческих движений и до сих пор практически не автоматизированы. Вот где расходуется гигантское количество человеческого труда. На сборочных линиях и конвейерах этот труд узкодифференцирован. Сборщик может выполнять сложные движения, но, обслуживая одно и то же рабочее место, он от раза к разу их повторяет. Его труд поэтому однообразен и неинтересен. А кроме того, выполнение той или иной операции может быть сопряжено со значительными физическими напряжениями, и тогда труд сборщика оказывается не только неинтересным, но и утомительным.
Автоматизация сборочных работ – вот где резерв повышения производительности труда, необозримое поле приложения идей и методов автоматизации. Так что же, разве до сих пор специалисты не видели необходимости работать в этом направлении?
Конечно, видели! И настойчиво искали решения и средства, которые по своим возможностям и своей «квалификации» отвечали бы сложности и масштабам давно назревшей проблемы.
Токарь, фрезеровщик, шлифовщик – рабочие высокой квалификации; их главная задача – управление станком, обеспечение его точной и производительной работы. Но они должны также устанавливать на станок заготовку и снимать обработанное изделие. Многие изделия, детали и заготовки для них имеют значительный вес: 10–30–50 килограммов. Операции их обработки на станке могут занимать всего лишь несколько минут, и тогда загрузка и выгрузка перерастают в важную проблему.
Квалифицированный труд станочника можно сэкономить, заменив обычный станок станком с цифровым управлением. Об этом мы уже много говорили. Внедрение станков, адаптивных систем и контрольных автоматов с цифровым управлением, как мы уже знаем, – одно из генеральных направлений автоматизации машиностроительного производства. Становление этого направления заняло до сегодняшнего дня круглым счетом четверть века.
Но мы при этом ни одним словом не обмолвились о том, кто же будет обслуживать эти высококвалифицированные станки, контрольные автоматы, линии и комплексы? Кто будет устанавливать на них заготовки, снимать обработанные изделия, ставить и снимать их с контрольных автоматов, передавать со станка на станок? Одним словом, кто будет обслуживать оборудование, автоматизированное цифровыми механизмами по последнему слову техники. Сейчас это делают люди, и труд этих людей по мере того, как повышается уровень автоматизации, становится все менее интересным и более утомительным. А ведь универсальных станков с цифровым управлением, другого машиностроительного оборудования – миллионы, а в перспективе их число должно расти – удваиваться, удесятеряться.
Для автоматизации загрузки и выгрузки машин и автоматов, установки и съема изделий, так же как и для автоматизации процессов сборки, до последних лет было сделано очень мало. Почему?
Если внимательно присмотреться, то окажется, что внешне простые операции установки и съема заготовок и изделий, а также сборки требуют выполнения сложных пространственных движений, характер которых во многом зависит от формы и размеров изделий и существенно меняется при переходе от одного изделия к другому.
В кузнечных цехах изделия куются из раскаленных заготовок. Кузнецу и его подручному требуются, кроме квалификации, большая физическая сила и выносливость, даже при том условии, что сам процесс ковки выполняется машиной-молотом. Раскаленную тяжелую заготовку надо взять клещами, ввести в зону обработки, правильно там сориентировать, поворачивая после одного или нескольких ударов молота…
Окраска изделий обычно производится набрызгиванием. Чтобы предохранить рабочего от вредного действия распыляемой краски, нужна специальная маска; помещение или рабочая зона, где производится окраска, оборудуется специальными защитными устройствами – сложно, дорого, опасно для человека.
Так, если просмотреть все основные и вспомогательные процессы машиностроительного производства (а мы ведь договорились ограничиться только этой отраслью производства), то окажется, что, несмотря на относительно высокий уровень автоматизации этой отрасли, она до сих пор требует гигантских затрат человеческого труда. При этом четко намечается, если можно так выразиться, «квалификационное расслоение» этого труда. Меньшая его часть, связанная с созданием и поддержанием автоматизированного оборудования в работоспособном состоянии, требует высокой квалификации, больших знаний, творческого подхода. А для прямого обслуживания этого, казалось бы, уже высокомеханизированного и автоматизированного оборудования необходима, однако, бóльшая часть живого труда. И необходима для выполнения внешне простых однообразных операций, «беда» которых состоит в том, что они требуют «человеческих» движений, что для их выполнения лучше всего приспособлены руки человека. Автоматизацией типично человеческих движений можно назвать проблему автоматизации процессов обслуживания бесчисленного машиностроительного и немашиностроительного оборудования. Она давно уже стала чрезвычайно острой и нашла свое решение в развитии целой новой отрасли техники, которая получила почти официальное название – робототехника.
И если автоматизация и, в частности, цифровая автоматизация составляют один из краеугольных камней научно-технического прогресса XX века, то робототехника и роботизация становятся одним из генеральных направлений научно-технического прогресса на значительно больший промежуток времени.
Мы не будем здесь затрагивать всю проблему робототехники. Она призвана обслуживать не только машиностроительную и другие отрасли производства, но также атомную, космическую и глубоководную отрасли техники. Лишь коротко остановимся на тех представителях робототехники, которые уже появились на производстве и получили название промышленных роботов.
Чтобы наглядно понять, в чем состоит основная особенность машин этого класса, еще раз подчеркнем, что главная цель их создания состояла в том, чтобы получить средство, автоматически воспроизводящее движение руки человека.
Рука человека – механизм, обладающий высокой подвижностью. Особенность этого механизма состоит в том, что он «спроектирован» для выполнения не какого-либо одного особого движения, а бесчисленного множества самых разнообразных движений. Она в этом смысле универсальный рабочий орган.
Промышленный робот также снабжен рабочим органом – механической рукой, – обладающим подвижностью хотя и несравнимо более низкой, чем рука человека, но вместе с тем достаточно высокой, чтобы выполнять довольно сложные «человекоподобные» движения.
Мозг человека – «вычислительная машина», умеющая управлять бесчисленным множеством движений его рук. Промышленный робот оснащается программным устройством – «искусственным мозгом», который, конечно, ни в какое сравнение с живым идти не может. Но его «мощности» достаточно, чтобы использовать возможности механической руки. В это программное устройство, как в программное устройство станка с цифровым управлением, можно ввести ту или иную программу, и в соответствии с этой программой механическая рука будет двигаться, устанавливая и снимая со станка заготовки и изделия, собирая узлы машин, выполняя сварку, ковку, окраску изделий, бесчисленное множество операций и работ, которые сейчас выполняет человек.
Около десяти лет назад началась разработка конструкции промышленных роботов. А сейчас в области их производства и внедрения начался резкий подъем. Миллиардные суммы в ближайшие годы предполагают затратить на развитие робототехники правительства, университеты и фирмы США, Японии и других высокоразвитых капиталистических стран. Широко развертываются аналогичные работы в Советском Союзе и странах социалистического лагеря.
Уже накоплен первый опыт применения роботов на производстве, свидетельствующий о широких возможностях и высокой эффективности этих машин.
Так, в качестве примера приведем опыт одной из автомобильных фирм США, где на линии сборки колес вместо 46 операторов (при двухсменной работе линии) было установлено 23 промышленных робота «Юнимейт». Годовая эксплуатация линии и выполненные на основе результатов ее работы экономические расчеты показали, что полученная прибыль при этом значительно превысила ту среднюю величину прибыли, при которой считается выгодным внедрять новую технику. Д-р Энгельбергер – президент фирмы «Юнимейшн», выпускающей эти роботы, – будучи в Советском Союзе, заявил в техническом докладе, что перспективы их внедрения весьма благоприятны. В качестве обоснований своей точки зрения наряду с тем фактом, что количество заказов на роботы растет, он приводил ряд других доводов, отражающих специфические условия капиталистического мира. Он говорил, что при оценке эффективности роботов надо учитывать, что им не нужна жилплощадь, они не требуют никаких социальных или культурных услуг, расходов на транспорт и т. д. и т. п.