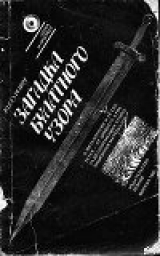
Текст книги "Загадка булатного узора"
Автор книги: Юрий Гуревич
сообщить о нарушении
Текущая страница: 8 (всего у книги 14 страниц)
Перламутровая теория булата
Первые исследования микроструктуры литого металла привели Д. К. Чернова к открытию закономерностей кристаллизации стального слитка. Это являлось крупным научным достижением, открывающим путь к получению качественных сталей. Все же Д. К. Чернов и Н. Т. Беляев в конце концов поняли, что дендритная теория булатного узора несостоятельна.
Подвергая ковке сталь, нагретую до различных температур, Чернов устанавливает связь между температурой ковки, микроструктурой стали и ее механическими свойствами. Он открывает критические температурные точки, переход через которые существенно изменяет строение и свойства стали. Одна из этих точек, обозначаемая им буквой а, соответствовала темно-вишневому цвету нагретой стали, вторая точка b – красному цвету каления.
Вот как Д. К. Чернов характеризует эти замечательные точки: «Сталь, как бы тверда она ни была, будучи нагрета ниже точки «а», не принимает закалки, как бы быстро ее ни охлаждали, напротив того, она становится значительно мягче и легче обрабатывается пилою». Таким образом, критическая точка «а» характеризует минимальную температуру, от которой сталь начинает принимать закалку. И напротив, «сталь, будучи нагрета ниже точки «b», не изменяет своей структуры – медленно или быстро после того она охлаждается. Как только температура возвысится до точки «b», масса стали быстро переходит из зернистого (или, вообще говоря, кристаллического) в аморфное (воскообразное) состояние». «Аморфная» – это мелкозернистая структура стали, которая надежно обеспечивает ей высокие свойства.
Открытие критических точек превращения стали сделало возможным научно объяснить процессы, происходящие в стали при ее закалке и отпуске. Изучение под микроскопом микроструктуры отожженной и закаленной стали приводит Д. К. Чернова и Н. Т. Беляева к новой гипотезе, объясняющей природу булата. Теперь они представляют булатный узор как «видимый простым глазом перлит». Чтобы понять, что такое перлит и каким образом он может быть связан с булатным узором, необходимо более подробно ознакомиться с превращениями в железоуглеродистых сплавах при их нагревании и охлаждении.
Железо существует в двух полиморфных модификациях: а-железо, которое устойчиво при температурах ниже 910 °C и выше 1390 °C и Y-железо, устойчивое в интервале температур 910°–1390 °C. Кристаллическая решетка а-железа – объемно-центрированный куб, а Y – железа – гранецентрированный. Изменение кристаллической решетки при нагревании и охлаждении называется полиморфизмом. Открытие Д. К. Черновым в 1868 году критических точек превращения стали есть не что иное, как открытие полиморфизма железа.
Мы уже говорили о том, что железо с углеродом образует химическое соединение – цементит (карбид железа). В середине прошлого века английский ученый У. Робертс-Остен показал, что углерод способен также растворяться в твердом железе. В честь его твердый раствор углерода в Y – железе назвали аустенитом. Твердый раствор углерода в а-железе называется ферритом. И в аустените, и в феррите углерод растворим в ограниченных количествах.
С понижением температуры падает растворимость углерода в аустените и феррите, и избыточный углерод выделяется из раствора в виде цементита. В связи с этим Д. К. Чернов указывал, что критические точки превращения аустенита в феррит при охлаждении стали и феррита в аустенит при ее нагревании зависят от содержания в стали углерода. Этим самым он впервые дал представление о диаграмме состояния железоуглеродистых сплавов. В дальнейшем благодаря работам А. П. Ле-Шателье (1850–1936), А. А. Байкова (1870–1946), Н. Т. Гудцова (1885–1957) и других ученых эта диаграмма была построена.
Что же такое диаграмма состояния? Диаграмма состояния – это графическое изображение областей устойчивости фаз в зависимости от температуры и состава сплава. На рис. 2 показан левый нижний угол диаграммы железо – углерод. По оси ординат отложена температура сплава, по оси абсцисс – содержание (концентрация) углерода в железе.

Рис. 2 Диаграмма железо-углерод
Рассмотрим подробнее представленную часть диаграммы. Линия GS ограничивает область существования аустенита. Точки этой линии показывают начало превращения аустенита в феррит при охлаждении сплава и окончание превращения феррита в аустенит при нагревании. С увеличением концентрации углерода в аусте-ните до 0,8 %, температура начала его превращения в феррит падает, и по достижении этой концентрации (точка S) она соответствует 727 °C. Поэтому при охлаждении сплавов с содержанием углерода более 0,02 % и менее 0,80 % в интервале температур 911–727° происходит превращение аустенита в феррит, а при нагревании – феррита в аустенит. Таким образом, в области между линиями GS и PS структура сплавов всегда двухфазная, состоящая из феррита и аустенита. Аустенит полностью превращается в феррит при охлаждении сплава ниже температуры 727 °C (линия PS). Эта же температура определяет начало превращения феррита в аустенит при нагревании сплава.
В правой части диаграммы линия SE также ограничивает область существования аустенита. Точки этой линии показывают, что с падением температуры растворимость углерода в аустените уменьшается. С понижением температуры от 1147 до 727 °C предельная концентрация углерода в аустените изменяется от 2,11 до 0,8 %. Поэтому при охлаждении сплавов указанных составов до температур ниже 1147 °C из аустенита выпадает цементит. В области между линиями SE и SK структура сплавов двухфазная, состоящая из аустенита и цементита.
При температуре 727 °C концентрация углерода в еустените определяется точкой 5 на линии PSK и соответствует 0,8 %. Предельная концентрация углерода в феррите при этой же температуре определяется точкой Р на линии PSK, она соответствует всего 0,02 % углерода. Следовательно, аустенит, содержащий 0,8 % углерода, при охлаждении сплава до 727 °C превращается в феррит, содержащий 0,02 % углерода. Избыток углерода выделяется из аустенита в виде цементита. Таким образом, при температуре 727 °C аустенит распадается одновременно на две фазы: феррит и цементит. Эти фазы выделяются в виде механической смеси. Превращение аустенита в феррито-цементитную смесь при 727 °C характерно для всех сталей.
Распад аустенита при 727 °C на феррит и цементит называется эвтектоидным превращением, а получающаяся в результате распада феррито-цементитная структура – эвтектоидом. Невооруженным глазом увидеть феррито-цементитную смесь невозможно. Под микроскопом, при увеличениях в десятки и сотни раз, двухфазная структура эвтектоида напоминает перламутр, сложенный из светлых пластинок феррита, чередующихся с темными пластинками цементита. Поэтому двухфазная структура эвтектоида была названа перлитом.
Стали, содержащие углерода до 0,8 %, называются доэвтектоидными. После медленного охлаждения их структура состоит из феррита и перлита. Стали, содержащие углерода более 0,8 %, называются заэвтектоидными. Их структура после медленного охлаждения состоит из перлита и включений цементита. В стали, содержащей 0,8 % углерода, весь аустенит превращается в перлит, поэтому после медленного охлаждения структура такой стали будет представлять собой пластинчатый перлит. Такая сталь называется эвтектоидной.
Если сравнить пластинчатый перлит с узором клинка кинжала, сделанного из аносовского булата (см. фото 3), то мы увидим: внешнее сходство поразительное! Теперь совершенно понятно, почему Д. К. Чернов и Н. Т. Беляев пытались связать булатный узор с перлитной структурой стали. Н. Т. Беляев даже пробовал классифицировать перлит по признакам булатного узора…
Перлитом можно не только объяснить узор булата, но и обосновать его свойства. Дело в том, что феррит является пластичным и вязким материалом, а цементит – твердым и прочным. Так же как и булат, перлит как будто совмещает в себе прямопротивоположные качества: пластичность и твердость, вязкость и прочность!
Итак, Д. К. Чернов и Н. Т. Беляев выдвинули гипотезу: булатный узор – перлит, полученный каким-то неизвестным способом, обеспечивающим рост пластинок феррита и цементита до таких размеров, что они видны невооруженным глазом. Однако никакого экспериментального материала, связывающего перлит с булатным узором, получить не удалось. Металлурги ни разу не получали перлита, в котором бы величина пластинок феррита и цементита была бы соизмерима с булатным узором.
В связи с этим Н. Т. Беляев выдвигает новую гипотезу: булатный узор является результатом структурного равновесия между ферритом и цементитом. Поводом для этой гипотезы послужили опыты металлурга Г. Геренса, который обнаружил в перлите белых чугунов структурно-свободный цементит. Рассматривая условия, предложенные Аносовым для отжига «литых булатов», Н. Т. Беляев находит, что они в точности совпадают с опытами Геренса. Гипотезу Н. Т. Беляева поддерживает известный металлург начала XX века В. П. Ижевский.
Нагревом заэвтектоидной стали (1,4–1,8 % углерода) выше перлитного превращения (727 °C) и длительной выдержкой при температурах ниже перлитного превращения (720°–700 °C) удается получить резкую ликвацию углерода. В стали появляются участки структурно-свободного феррита и групповые скопления коагулированных (сгруппировавшихся) частиц цементита.
Казалось бы, металлурги наконец-то получили ключ к разгадке тайны булатных узоров. Но, увы, вскоре сами авторы гипотезы признают ее несостоятельность: хорошо известно, что булатные узоры сохраняются и после закалки стали в то время, как структура «феррито-цементитного узора» после закалки на мартенсит традиционными способами сохраниться не может. Чтобы это хорошо понять, необходимо сделать еще один экскурс в металловедение и познакомиться с основами теории закалки и отпуска стали.
Что же происходит при закалке стали? Свойства стали зависят от ее структуры. Оказывается, структура стали данного химического состава изменяется после нагревания и последующего охлаждения с той или иной скоростью. При нагревании сплава железо – углерод до температур, соответствующих области выше линии GSE (см. рис. 2), он приобретает аустенитную структуру. При разных скоростях охлаждения аустенита получают разные структуры охлажденной стали.
Если эвтектоидную сталь (0,8 %, углерода) медленно охлаждать от температур выше 727 °C, то произойдет полный распад аустенита с образованием пластинчатого перлита. Распад аустенита можно условно разделить на следующие процессы:
1. Превращение аустенита в феррит. Этот процесс состоит в перегруппировке атомов железа таким образом, что решетка гранецентрированного куба Y-железа переходит в решетку объемно-центрированного куба а-железа.
2. В результате смещения атомов углерода и пересыщения этим компонентом твердого раствора из него выделяются частицы цементита (карбида железа).
3. Выделившиеся частицы цементита растут и образуют прослойки в феррите.
Как мы уже говорили, после медленного охлаждения углеродистая сталь имеет структуру пластинчатого перлита, хорошо видимую под микроскопом при увеличении в 100 раз. При ускорении охлаждения до 50° в секунду третий процесс превращения не успевает закончиться, поэтому размеры пластинок цементита уменьшаются, и они становятся различимы только при увеличениях в тысячи раз. Такая структура в честь английского ученого конца XIX – начала XX века Г. К. Сорби была названа сорбитом.
При ускорении охлаждения до 100° в секунду полностью успевает завершиться только второй процесс превращения, а третий останавливается в самом начале. Теперь уже пластинки цементита видны лишь при громадных увеличениях в десятки тысяч раз. Они различимы только под электронным микроскопом. Такая структура в честь французского химика Л. Ж. Трооста (XIX – начало XX века) названа трооститом.
Наконец, при скорости охлаждения аустенита больше критической (порядка 150–200° в секунду) уже и второй и третий процессы распада не успевают совершиться; завершается лишь перегруппировка атомов железа, а углерод вынужденно остается в твердом растворе а-железа, сильно пересыщая его. Такая структура в честь немецкого металловеда А. Мартенса (вторая половина XIX – начало XX века)" названа мартенситом. Мартенситной структуре соответствует наиболее высокая твердость и прочность стали. Таким образом, если перлит, сорбит и троостит – двухфазные структуры, представляющие собой смесь феррита и цементита, то мартенсит – структура однофазная, это твердый пересыщенный раствор углерода в а-железе.
Закалка стали состоит в ее нагреве на 30–50 °C выше температуры начала устойчивости аустенита и быстром охлаждении. Обычно при закалке стремятся получить мартенситную структуру. Для устранения больших напряжений в стали, получающихся под действием резкого охлаждения при закалке, сталь после закалки подвергают отпуску. Отпуск стали заключается в ее нагреве до температур ниже 727 °C и последующем охлаждении. При отпуске структура стали из мартенсита закалки переходит в мартенсит отпуска, троостит отпуска или сорбит отпуска. Пластичные и вязкие своиства стали после отпуска улучшаются, а твердость и прочность падают.
Совершенно понятно, что булатные клинки, знаменитые своей твердостью и режущими свойствами, по крайней мере в поверхностных слоях закаливались на мартенсит. Под микроскопом мартенсит представляет собой игольчатую структуру. Иглы мартенсита располагаются закономерно, образуя углы в 60 или 120°. Поэтому после закалки булата пластинчатая структура перлита сохраняться не может. Все же, как будет показано в дальнейшем, на основе феррито-мартенситной структуры можно получать композиционные стали с высокими свойствами.
Выдающийся ученик и последователь Д. К. Чернова в области металловедения и термообработки Н. И. Беляев хорошо понимал недостатки теории, объясняющей булатный узор «структурным равновесием феррита и цементита». Он писал: «Знакомство наше с микроструктурой стали не только не помогало, а скорее мешало разобраться в этом интересном вопросе, так как приводило или к абсурдному объяснению узора булата развитием пластинчатого перлита до размеров, видимых простым глазом (профессор Чернов и др.), или к объяснению узора булата с точки зрения структурного равновесия».
В 1911 году Н. И. Беляев, наиболее обстоятельно изучивший к этому времени вопрос о булате, приходит к совсем пессимистическим выводам: «Грустно сознавать, что современная наука не вооружена еще настолько, чтобы ясно и определенно ответить на вопросы: что такое булат с его непременным спутником – узором и чем, собственно, объясняются те высокие механические свойства, какими обладают изделия, изготовленные из булата…».
ГЛАВА ЧЕТВЕРТАЯ
ТРЕТЬЕ РОЖДЕНИЕ БУЛАТА
Новое – это хорошо забытое старое.
Поиск продолжается
Юрий Иванович Люндовский – коренной житель Златоуста. На плане дома, который в 1837 году перестраивал его дед, мастеровой казенных заводов Григорий Люндовский, стоит подпись самого «управителя Златоустовскими заводами П. Аносова». Подпись скреплена печатью заводской конторы. Печать была сделана из горного хрусталя.
Юрий Иванович начал трудовую деятельность на Златоустовских заводах в 1931 году. Будучи главным металлургом завода, он работал в здании с медной доской у входа: «Центральная заводская лаборатория. Основана в 1836 году П. П. Аносовым». По чугунным ступенькам, по которым не раз ходил изобретатель русского булата, он ежедневно подымался к себе в кабинет.
Со школьной скамьи Люндовский мечтал найти утерянные секреты и выплавить узорчатую сталь. В его семье хранилась железная трость деда – необыкновенно легкая, витая, сделанная из железных полос, заготовленных для производства сварочного булата. Он собрал и хранил все те немногочисленные образцы русского булата, которые можно было найти на заводе.
Ю. И. Люндовский в конце 30-х годов повторил опыты Д. К. Чернова и добился путем замедленного охлаждения слитка получения крупных дендритов в малом объеме металла. Умеренно холодная ковка таких слитков позволяла получать слабо проявляющиеся узоры.
В 20–30-х годах тщательно изучал материалы, относящиеся к производству булата, племянник Павла Николаевича Швецова – Василий Николаевич, который с 1896 года служил мастером фасонно-литейного цеха. Он был высокообразованным человеком, увлекался историей уральских заводов, выплавкой тигельной стали, производством огнеупоров. Сохранились печатные работы В. Н. Швецова, посвященные этим вопросам.
Любопытен такой факт. Николай Швецов, который работал с Аносовым, был безграмотным крепостным крестьянином. Его сын – Павел Швецов окончил начальную горнозаводскую школу, что по тем временам считалось большим везением. Василию Швецову, в 1904 году закончившему Уральское горное училище, Советская власть дала возможность получить экстерном высшее образование – он был инженером-металлургом. А его внук Сергей Швецов, ныне научный работник, готовится к защите кандидатской диссертации.
В 20-е годы металлургия окончательно формируется в самостоятельную науку. В технической литературе появляется много статей, посвященных теоретическому обоснованию технологии производства легированных сталей, их термической обработке. В это время вновь пробуждается интерес к булату, появляются новые данные о его химическом составе, макро– и микроструктуре, делаются многочисленные попытки получить сталь с узорчатой структурой.
Ю. И. Люндовский исследует имеющиеся у него образцы булата, полученного П. Н. Швецовым. Он изучает его микроструктуру, устанавливает, что она характеризуется крупными включениями цементита высокой твердости, подтверждает, что в стали мало серы и других вредных примесей. На заводе еще можно было найти достаточно чистое пудлинговое железо, древесноугольный чугун и серебристый графит. Возлагаются надежды получить узорчатую сталь путем сплавления этих компонентов по режимам, описанным Аносовым. Многочисленные опыты к успеху не приводят. Правда, удалось овладеть приемами ковки булата и повторить их на обычных сталях. Узор почти не проявляется, но свойства изделий, особенно твердость и прочность, ощутимо повысилась.
В журнале «Уральский техник» за 1924 год была напечатана статья В. Н. Швецова «Литой булат». В ней описываются способы получения узорчатой стали. Автор считает, что лучшие узоры получаются при сплавлении железа и чугуна с небольшими добавками… серебра. Большое внимание уделено охлаждению слитка: по окончании плавки тигель, вынутый из печи, рекомендуется ставить в горячую золу, засыпать его ею со всех сторон, за исключением крышки, и оставлять до полного охлаждения. Описываются приемы ковки булата, обеспечивающие, по мнению автора, узор на клинке в виде елочки. Исследования образцов булатных изделий в статье не приводятся.
В 20-е годы в Златоусте стремился получать булат горный инженер П. А. Иванов. В его опытах принимал участие старейший мастер завода К. К. Моисеев. В записках В. Н. Швецова отмечается, что Иванов подгонял состав булата под «швецовский», вводя в шихту соответствующее количество марганца и хрома. В 30-е годы делались многочисленные попытки получить булат на основе работ В. Н. Швецова, П. А. Иванова, К. К. Моисеева. Ни одна из них успехом не завершилась.
В 1949 году Златоуст праздновал 150-летие со дня рождения П. П. Аносова; в городе был заложен ему памятник. Теперь на высоком пьедестале из красноватого полированного гранита, обрамленного литым орнаментом, возвышается бронзовая фигура величайшего русского металлурга.
Тогда, в 1949 году, в связи с знаменательной датой состоялось Всесоюзное совещание металлургов. Участники совещания посетили бывшую оружейную фабрику. В их присутствии испытывались современные шашки и сохранившиеся булатные клинки. Испытание завершилось не в пользу булата… Все же это событие вновь вызвало интерес к легендарной стали. Златоустовские металлурга твердо решили, что наступила пора объяснить свойства булата и расшифровать природу его удивительных узоров.
Как профессор Виноградов прочитал Аносова
Решить вековую загадку булатного узора взялся Игорь Николаевич Голиков – начальник центральной лаборатории Златоустовского металлургического завода. Он создал творческую группу, в которую вошли П. В. Васильев, М. Ф. Лонгинов, Ю. И. Люндовский и автор этих строк. Выплавлять сталь было решено в тигле индукционной высокочастотной печи. Этот современный агрегат достаточно хорошо моделировал тигельный процесс, который П. П. Аносов использовал для получения булата. В первых опытах было решено воспользоваться рекомендациями изобретателя русского булата и как можно точнее повторить его эксперименты.
Нам было понятно, что свойства булата определяются содержанием углерода в стали и его распределением в железе. Поэтому шихта составлялась из содержащего мало вредных примесей мягкого железа (0,03 % углерода) и серебристого графита.
Во время плавки поддерживался «большой жар» – расплав нагревали до 1600–1630 °C. При таких температурах обеспечивалась высокая степень насыщения металла углеродом. Готовую сталь разливали в чугунные формы. Слиток охлаждали очень медленно. Многократно добиваясь крупной кристаллизации и прекрасно выраженной дендритной структуры слитка, мы ни разу не получали булатного узора. Чего-то в нашей технологии явно не хватало, но чего? Для ответа на этот вопрос было решено еще раз внимательно изучить всю имеющуюся литературу о булате. И вот что обнаружилось.
В 1919 году в Днепропетровском горном институте защищалась необычная диссертация: «Мягкий булат и происхождение булатного узора». Соискатель, уже немолодой человек, профессор А. П. Виноградов излагал свою теорию природы узорчатой стали. Материалы диссертации были опубликованы в 1928 году в «Научных записках кафедры металловедения и термической обработки металлов». В связи с тем, что к 50-м годам этот сборник стал библиографической редкостью, труд ученого остался малоизвестным.
А. П. Виноградову особыми приемами деформации стали удалось получить на основе дендритной ликвации углерода волокнистую неоднородность, проявляющуюся в виде узора. Однако узор этот оказался не сопоставимым с булатным, поскольку был выражен очень слабо.
«Следует признать, – писал А. П. Виноградов, – что хотя химическая и структурная неоднородность является неизбежной принадлежностью всякой литой стали, однако булаты резко отличаются особенно ярко выраженной химической и структурной неоднородностью». Отсюда вывод: при производстве булатной стали химическая неоднородность подчеркивалась и фиксировалась принципиально другими приемами. Талантливый ученый впервые замечает «эти приемы» в опубликованных трудах П. П. Аносова.
Внимательно изучая «Журнал опытов по приготовлению литой стали и булатов с краткими замечаниями», А. П. Виноградов обратил внимание на то обстоятельство, что при получении булатов металл часто недорасплавлялся. В примечаниях Аносов так и пишет: «не все расплавлялось» или – «несовершенно расплавилось».
Тщательно анализируя условия проводимых П. П. Аносовым плавок булатной стали, А. П. Виноградов убеждается, что основной их особенностью является науглероживание кусочков (обсечков) железа в тигле. Часть из них, взаимодействуя с графитом и печными газами, очень сильно науглероживалась и превращалась в малоуглеродистый чугун. Чугун, температура плавления которого 1200–1300 °C, плавился и стекал каплями на дно тигля. Таким образом, в нижней части тигля скапливался жидкий чугун, а в его верхней части твердые обсечки мягкого низкоуглеродистого железа, температура плавления которых 1500–1535 °C.
Нагрев металла в условиях тигельной плавки во времена П. П. Аносова осуществлялся до температур не выше 1460–1480 °C, поэтому обсечки мягкого железа, погружаясь в конце концов в жидкий чугун, расплавиться не могли. Они могли лишь в твердом состоянии растворяться в чугуне. Плавка заканчивалась в тот момент, когда частички эти полностью в чугуне еще не растворились. Отсюда легко сделать вывод, что П. П. Аносов достигал большой физической неоднородности непосредственно при плавке стали за счет сохранения в основной массе высокоуглеродистого сплава частиц ненауглероженного и поэтому недорасплавившегося твердого железа.
Интересно, что П. П. Аносов понимал эти особенности технологии плавки булата. Он писал: «Искусство мастера в сем случае состоит в том, чтобы остановить работу в то мгновение, когда последний кусочек обсечков начинает расплавляться…» И далее: «При разбитии медленно охлажденных в печи тиглей сплавки казались как бы не совершенно расплавленными, ибо куски железа в некоторых местах сохранили первоначальную форму». В свете новой теории булатного узора эти замечания приобретают глубокий смысл.
Так как прекращение плавки у П. П. Аносова происходило в тот момент, когда в жидкость погружались твердые частицы железа, то последующее понижение температуры при охлаждении сплава в тигле приводило к кристаллизации высокоуглеродистой стали на имеющихся частицах железа, как на готовых центрах. Охлаждение стали в тигле, в котором она плавилась, как бы фиксировало полученную при плавке неоднородность. Недаром на основании своих опытов П. П. Аносов полагал, что переливание из тигля в изложницу порти г сталь.
Более того, по его наблюдению медленное охлаждение стали в тигле способствовало развитию кристаллизации и образованию узоров. Таким образом, процесс плавки и кристаллизации стали у П. П. Аносова неизбежно обусловливал крайнюю химическую, а следовательно, и структурную неоднородность слитка. Деформация при ковке этой неоднородной структуры и являлась причиной булатного узора.
К сожалению, на перечисленные особенности технологии производства булатной стали не обратил никакого внимания ни один из исследователей работ П. П. Аносова. Не указывал на них также никто из златоустовских мастеров, которые позже плавили булатную сталь. Естественно, что сам П. П. Аносов, не владея современными методами исследования металлов, не мог должным образом оценить степень влияния приведенных выше, на первый взгляд второстепенных, факторов на рисунок булата и его свойства.
После П. П. Аносова производство настоящих булатных клинков на Златоустовском заводе, как уже было отмечено, вскоре прекратилось. Д. К. Чернов объяснял это чрезвычайной сложностью процесса. «Производство узорчатой стали, – писал он, – требует усиленного постоянного наблюдения и преданности делу. В производстве булата очень ясно обнаружилось, какой капризный материал – сталь: малейшее несовершенство в процессе или нечистота материала – и уже сталь получается хуже, с мелким узором». А. П. Виноградов полагал, что причиной прекращения производства булата могло быть несоблюдение основного условия его получения: «прекращать процесс плавления, не дожидаясь полного растворения последних кусочков железа».
Действительно, П. П. Аносов, составив подробное описание приемов приготовления слитков булатной стали, не обратил должного внимания на момент прекращения плавки. Все последующие металлурги, плавившие булат после П. П. Аносова, не могли соблюсти это необходимое условие, обеспечивающее получение узорчатой стали. Поэтому они получали булат эпизодически и, как правило, с очень мелким узором.
Несмотря на то что А. П. Виноградов разработал оригинальную теорию, достаточно убедительно объясняющую природу химической и физической неоднородности булатной стали, его экспериментальные работы были посвящены главным образом вопросу формирования булатных узоров на основании так называемой «полосчатой структуры» низкоуглеродистой стали.
Металлургам давно известно, что после прокатки стали при низких температурах часто получают так называемую «полосчатую структуру», состоящую из участков перлита, чередующихся с видимыми простым глазом полосками чистого железа (феррита). А. П. Виноградов показал, что после низкотемпературной прокатки листовой стали, содержащей 0,30–0,35 % углерода, и продолжительного отжига ее при температуре 800–900 °C с последующим медленным охлаждением в печи полосчатая структура проявляется очень хорошо. Полосчатость в этом случае получается в виде параллельных слоев почти чистого феррита и углеродистой стали с 0,6–0,7 %, углерода. Такая структура стали, по утверждению автора, имитирует «мягкие булаты» Аносова.
Даже при небольшой деформации слоев полосчатой структуры они могут стать волнообразными плоскостями с различной кривизной волн, а главное – могут значительно отклоняться от параллельности к поверхности образца. При достаточной толщине слоев отшлифованные образцы могут давать видимую простым глазом картину разнообразных узоров, характерных для булата. Если такой образец мысленно разрезать плоскостями, параллельными основанию, то они, подобно горизонталям при проектировании холмистой местности на карту, должны образовывать узор. Если слои приближаются к параллельным плоскостям, но не параллельны плоскости шлифа, то получается муаровый рисунок; если же они изгибаются в виде холма или углубления – ониксовидный. Применяя специальные приемы деформации стали – надрубы, разнообразную насечку и осадку, – А. П. Виноградов получал почти все известные рисунки булата.
Несмотря на то что А. П. Виноградов впервые экспериментально показал приемы получения булатного узора и выдвинул убедительно обоснованную теорию, объясняющую природу неоднородности булатной стали, ему не удалось приготовить настоящих булатов на основе высокоуглеродистых сплавов, у которых бы после закалки сохранились узоры. Последнее обстоятельство послужило поводом к критике взглядов А. П. Виноградова.
С целью подтверждения своих предположений А. П. Виноградов провел ряд плавок, в ходе которых путем присадки кусков железа в жидкую ванну пытался создать условия для получения физически неоднородного металла; но результаты этих опытов не были настолько выразительными, чтобы убедить в его правоте. Поэтому видные металлурги считали, что «нерасплавленные кристаллы, очевидно, не являются условием, необходимым для создания неоднородности жидкости», и что теория А. П. Виноградова применима скорее к сварочному булату, чем к литому.