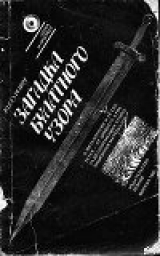
Текст книги "Загадка булатного узора"
Автор книги: Юрий Гуревич
сообщить о нарушении
Текущая страница: 12 (всего у книги 14 страниц)
Твердые, как алмазы
Очень высокая прочность и большая твердость материала достигается в искусственных композициях, которые еще в большей степени повторяют структуру булата. Принцип их создания давно известен. Подобно тому как в природном бамбуке мягкая целлюлозная матрица упрочняется жесткими и прочными нитями окиси кремния, принцип создания искусственных композиций заключается в сочетании (соединении) разнородных материалов. Еще в Древней Греции при строительстве Парфенонского храма широко использовались комбинированные материалы. Мраморные колонны храма армировались железными стержнями. В XVI веке при постройке храма Василия Блаженного в Москве знаменитые русские зодчие Барма и Постник применяли каменные плиты, армированные стальными полосами. Давно известен железобетон, который состоит из бетона, работающего на сжатие, и стальной арматуры, работающей на растяжение.
Новые композиционные материалы отличаются от обычных традиционных сплавов прежде всего булатной неравновесной структурой и очень высокими механическими свойствами.
Длительное время в качестве инструмента для обработки твердых материалов использовали алмаз. В производстве лампочек накаливания для волочения вольфрамовой нити применяли исключительно алмазные фильеры. Особенно дорого стоили алмазные фильеры для протяжки проволок больших диаметров. Естественно, что дорогостоящие и дефицитные алмазы всячески старались заменить каким-либо другим по возможности равноценным и дешевым материалом.
В начале XX века появились исследования, показывающие, что алмаз можно заменить твердыми и тугоплавкими, но более дешевыми карбидами металлов. Лучше всего для этой цели подходил карбид вольфрама. Попытки применить литой карбид вольфрама но дали положительных результатов – изделия имели низкую прочность и высокую хрупкость. Дальнейшие поиски показали, что хрупкость карбида вольфрама можно несколько уменьшить при сохранении высокой твердости посредством добавления железа, никеля и лучше всего кобальта. В 1923 году в Германии патентуется способ спекания карбида вольфрама с применением в качестве цементирующей связки кобальта до 10 %. В более поздних патентах содержание кобальта увеличивается ДО 20 %.
Положительный опыт использования твердых сплавов при волочении вольфрамовой проволоки открыл широкий путь для применения этого материала не только для фильер, но и в других областях техники в качестве твердосплавного режущего инструмента. Так, изделие, предназначенное для одной узкой цели – производства лампочек накаливания с вольфрамовой нитью, – получило совершенно непредвиденное вначале универсальное значение.
Впервые спеченный твердый сплав для режущего инструмента был получен на основе монокарбида вольфрама и кобальта в 1923–1925 годах германской фирмой «Осрам» по патенту немецкого инженера Шрёттера. В 1926 году промышленное производство таких сплавов под названием «видиа» было начато фирмой «Крупп». Видиа оказался очень хорошим материалом для металлорежущих резцов, наконечников для напайки на сверла, пластинок для фрез, пил, зенкеров и разверток. Благодаря новому композиционному материалу оказалось возможным обрабатывать резанием такие стали и чугуны, из которых раньше можно было получать изделия только ковкой или литьем. Новый материал, как в свое время быстрорежущая сталь, произвел революцию в машиностроении.
В Советском Союзе появление спеченных инструментальных твердых сплавов относится к 1929–1930 годам, когда на Московском электроламповом заводе были изготовлены первые образцы такого сплава на основе карбида вольфрама и кобальта под названием «победит». Второй советский сплав на хромомарганцевожелезной основе был самым дешевым твердым сплавом из всех известных в мире. Долгое время, вплоть до Великой Отечественной войны, он был известен под названием «сталинит» и имел большое распространение. Его широко применяли для наплавки деталей с целью предохранения от сильного износа при истирании, особенно для покрытия зубьев врубовых машин, всевозможных дробящих механизмов, экскаваторов, шнеков. Одна из марок этого сплава (сталинит-2) по сопротивлению истиранию превосходила лучший зарубежный сплав – вокер.
Современная технология получения твердых сплавов состоит в следующем. Порошки карбида вольфрама и кобальта тщательно перемешивают, формуют в заготовки и спекают в вакууме при температуре 1400–1500 °C. При этой температуре появляется жидкая фаза па основе кобальта, которая «склеивает» частицы карбида и обеспечивает получение компактного материала. Так же как и железо в булате, добавка кобальта к карбиду позволяет получить материал, обладающий одновременно высокой твердостью и достаточной прочностью и вязкостью.
Применение инструмента из спеченных твердых сплавов на основе карбида вольфрама и кобальта имеет огромное значение для промышленности. С помощью этого материала удалось в несколько раз повысить скорость резания при обработке металлов по сравнению со скоростями, применявшимися при использовании быстрорежущей стали. Замена стали «твердосплавными булатами» в производстве металлической проволоки повысила в 1000 раз стойкость волок – приспособлений, через калиброванные отверстия которых тянут проволоку.
При замене стальных штампов на твердосплавные их стойкость возрастает в 50–100 раз. Значительное применение получили твердосплавные буры, используемые в горном деле. Их стойкость в десятки раз выше, а скорости бурения в несколько раз больше, чем у стальных.
Повышение производительности труда при применении твердых сплавов во многих отраслях техники обеспечивает высокую эффективность работы дорогостоящего и дефицитного вольфрама. Так, например, по данным советского ученого В. И. Третьякова, инструментом из твердого сплава, имеющего в своем составе 1 кг вольфрама, можно обработать в 5 раз больше металла, чем инструментом из быстрорежущей стали с тем же количеством вольфрама.
В последнее время получают распространение твердые сплавы на основе карбида титана с никель-молибденовой связкой. Сравнительно дешевый и недефицитный карбид титана в ряде операций обеспечивает достаточно высокую стойкость режущему инструменту.
Несмотря на эти достижения, поиск путей повышения износостойкости режущего инструмента продолжается. Одним из новых и важных источников решения этой проблемы является технология нанесения нитридных и карбидных износостойких покрытий на режущий инструмент, в том числе твердосплавный.
Харьковские инженеры-изобретатели А. Романов, Л. Саблев и А. Андреев разработали метод нанесения таких покрытий потоками высокотемпературной плазмы. Износостойкость обработанного в вакуумной камере потоками плазмы режущего инструмента в 3–6 раз больше, чем у обычного. Повышение стойкости объясняется образованием тонкой, но очень прочной пленки из нитрида или карбида титана на режущей кромке инструмента. Для реализации прогрессивной технологии в промышленных условиях создана специальная установка. И не случайно эта установка известна под названием «Булат»…
«Булат» получит широкое применение в одиннадцатой пятилетке. В «Основных направлениях экономического и социального развития СССР на 1981–1985 годы и на период до 1990 года» указано: «Организовать производство в широких масштабах новых видов инструмента, в том числе с применением износостойких покрытий…» Структура, обеспечивающая сотни лет назад высокие режущие свойства булата, повторилась в современных твердых сплавах и износостойких покрытиях.
И все-таки полностью твердые сплавы заменить алмаз не могут. Только алмазные волоки способны длительное время противостоять разрушающему действию движущейся металлической проволоки. Стойкость алмазных волок в тысячи раз больше стальных, и они практически незаменимы при волочении тонких проволок из высокопрочных сплавов, особенно в тех случаях, когда требуется точная окружность, постоянство диаметра сечения и гладкая поверхность. Нити парашютной ткани протягиваются только с помощью алмазных волок. Они обеспечивают нити необходимую гладкость, которая гарантирует своевременное и быстрое раскрытие парашюта.
Примечательно, что первый цех алмазного инструмента в нашей стране был создан в конце прошлого века Константином Сергеевичем Алексеевым (Станиславским), которого мы знаем как выдающегося режиссера и основоположника системы воспитания актера. На московской фабрике «волоченого и плащеного золота и серебра», где начиналась его трудовая жизнь, выпускали тончайшую проволоку, канитель (тонкую витую проволоку), серебряные и золотые изделия из них. В производстве применялись чугунные волоки, с помощью которых процесс вытяжки тонкой проволоки был очень длителен («канительным» – как теперь говорят). Применение алмазного инструмента затруднялось в связи с тем, что вплоть до конца XIX века производство волок из драгоценных камней было монополией западных фабрикантов, в основном французских и итальянских. К. С. Станиславский едет за границу, знакомится с производством алмазного инструмента и по возвращении в Москву организует цех по изготовлению алмазных волок. На состоявшейся в 1900 году Всемирной промышленной выставке в Париже продукция золото-канительной фабрики получила высшие награды, а Константин Сергеевич был награжден медалью с дипломом выставки.
Как же обрабатывают алмаз, если он самый твердый из известных материалов? Долгое время алмазы служили только для украшений, но обрабатывать их не умели, и изделия из них выглядели порой весьма тускло. В 1475 году голландец Людвиг Беркен открыл способ гранить, шлифовать и полировать алмазы при помощи порошка этого же драгоценного минерала. Он впервые обработал для бургундского герцога Карла Смелого крупнейший алмаз лимонного цвета, придав ему форму, напоминающую розу. Затем был отполирован легендарный алмаз «Санси», купленный в свое время П. Н. Демидовым и привезенный в Россию. После полировки камни, сверкающие всеми своими гранями, стали очень красивыми. С того далекого времени по сей день алмазы обрабатывают алмазным же инструментом.
На станке, подобном токарному, алмазную заготовку обтачивают острыми выступами другой такой же заготовки. Распиливают, шлифуют или сверлят алмаз алмазным порошком, нанесенным на быстро вращающийся инструмент. В последнее время для ускорения обработки применяется вибрация инструмента с ультразвуковой частотой.
При обработке алмаза алмазными резцами в отходы превращается больше половины драгоценного кристалла. Таким образом, процесс обработки алмаза очень трудоемкий и дорогой. Но это еще не все. Оказывается, механическим способом алмаз удается обрабатывать не во всех направлениях. Особенности кристаллической решетки алмаза делают его неодинаково твердым в разных плоскостях. Поэтому алмаз поддается механической обработке только по «мягким» направлениям, и распиливать его можно лишь так, чтобы плоскость среза соответствовала расположению атомов углерода в плоскостях куба и ромбододекаэдра.
В последнее время для обработки алмаза начали использовать луч лазера, который выжигает вещество. Импульс света делает в алмазе воронку. Серией импульсов, направленных в одну точку, алмаз сверлят, а располагая импульсы в ряд – режут. При лазерной обработке поверхность воронок трескается из-за сильных термических напряжений. Слои алмаза, нарушенные лазером, приходится удалять с помощью все той же механической обработки.
Ученые долгое время искали новые эффективные способы обработки алмаза. Один из таких способов, существенно упрощающий изготовление традиционных изделий из алмаза и открывающий новые возможности его обработки, найден в Якутском филиале Сибирского отделения АН СССР. Он основан на явлении, давно известном металлургам, – растворении алмаза в железе. Помните, как П. П. Аносов вводил алмаз в сталь, надеясь получить новую форму существования в ней углерода? Зная об этом, нет причины удивляться тому, что железом можно резать алмаз!
Каждый атом углерода в структуре алмаза соединен со своими соседями четырьмя прочными связями, называемыми ковалентными. Природа этих самых прочных связей определяется небольшим размером атомов углерода. С другой стороны, благодаря своему небольшому размеру, атомы углерода при соответствующей температуре способны проникать в решетку металлов, образуя твердый раствор внедрения. Растворять в себе углерод могут не все металлы, а только те, атомы которых имеют недостроенную внутреннюю электронную оболочку. Они называются переходными металлами. Из переходных металлов лучше всего в твердом состоянии углерод растворяет железо, никель и кобальт.
Много лет назад во Франции для подтверждения углеродной природы алмаза был проделан следующий эксперимент. Алмаз положили на брусок железа, который нагрели в нейтральной среде до 1000 °C. В месте контакта с алмазом мягкое железо науглеродилось и превратилось в сталь. Этот опыт хорошо объясняет, почему железо в ряде случаев не удавалось обрабатывать алмазными резцами.
Читатель уже, наверное, догадался, как можно железом резать алмаз. Действительно, если положить на алмаз железную проволоку и нагреть в вакууме эту систему, то атомы углерода начнут «внедряться» в железо, алмаз будет растворяться, и проволока его разрежет! Но беда в том, что процесс растворения углерода в железе не бесконечен. Проволока сравнительно быстро насытится углеродом, и процесс «резания» сначала резко замедлится, а потом прекратится совсем. Следовательно, из железной проволоки надо все время убирать углерод, тогда она не будет терять своих режущих свойств. Но как это сделать? Якутские ученые дали исчерпывающий ответ на этот вопрос.
Дело в том, что при растворении алмаза в железе происходит разрыв прочных ковалентных связей, которые существуют между атомами углерода в решетке алмаза. В твердом растворе внедрения, который образуется в железе при 1000 °C, углерод практически находится в атомарном состоянии, испытывая лишь слабое химическое взаимодействие с металлом-растворителем. Поэтому растворенные в железе атомы углерода значительно более активны, чем в алмазе. При температуре «резания» (1000 °C) алмаз не способен взаимодействовать с водородом или углекислым газом, а растворенный в железе углерод хорошо с ними взаимодействует. Реакция протекает на поверхности металла и сопровождается образованием газообразных продуктов: метана или окиси углерода.
Если на алмаз поместить тонкую железную пластинку и нагревать ее до указанной температуры в атмосфере водорода, углерод начнет растворяться в железе и за счет диффузии двигаться в направлении поверхности пластинки. Достигнув ее, он «найдет» водород и, соединившись с ним, образует метан, который тут же покинет пластинку. Растворяя углерод алмаза своей нижней поверхностью и передавая его газу верхней, пластинка будет равномерно погружаться в алмаз. Скорость погружения, она же скорость резания, будет зависеть от температуры, толщины пластинки, состава, давления и скорости протекания газа над пластинкой. А форма образующейся в алмазе полости с вертикальными стенками будет полностью соответствовать выбранной форме погружаемого в него железа или сплава на его основе.
Термохимическим способом обработки алмаза в Якутском институте геологии «гравировали» на его кристаллах всевозможные рисунки, вырезали шестеренки, делали отверстия заданного диаметра. Были разработаны также термохимические методы шлифовки и обработки некоторых видов поликристаллических алмазных пеков. Так система железо – алмаз нашла практическое применение почти через полтораста лет после опытов П. П. Аносова.
Легче алюминия и прочнее стали
Исследование свойств различных композиционных материалов показало, что не только по прочности, но и по другим физико-механическим свойствам они превосходят каждый компонент, входящий в их состав. Созданы композиционные материалы, выдерживающие большие нагрузки, подвергающиеся большому тепловому воздействию, выдерживающие частые и резкие смены температур. Например, введением волокон асбеста в керамику можно повысить в несколько раз ее способность выносить тепловые удары. Волокна асбеста, как стальная арматура железобетона, связывают зерна огнеупора и удерживают их при резких перепадах температур от распада. Если изготовить трубку из керамической массы шамота, добавив в качестве высокотемпературного связующего скелета волокна каолина, то термостойкость шамота возрастает в десятки и даже сотни раз, Без подобных материалов сегодня немыслимы атомоходы, сверхзвуковые самолеты и космическая аппаратура.
Волокнистые композиционные материалы конструируются из металлической или керамической основы и упрочняющего волокна различного строения. Для получения волокон в зависимости от необходимых свойств используют самые разнообразные материалы: проволоку из молибдена или вольфрама, жаропрочной и жаростойкой стали, окись алюминия, каолин, графит, различные бориды, карбиды и нитриды. Каждый из таких волокон обеспечивает материалу определенный комплекс свойств. Введение волокон в матрицу чаще всего осуществляется методом формования волокон и порошка материала для матрицы или пропиткой волокон жидким металлом матрицы.
Очень напоминают технологию приготовления сварочного булата методы производства волокнистых композиционных материалов, упрочненных проволокой. Такие материалы разделяются на армированные проволоками, армированные сетками и армированные проволочными волокнами ограниченной длины. В последнем случае отдельные проволочные волокна располагаются в матрице в виде включений.
Прочность кобальта, нихрома и других сплавов, армированных вольфрамовой или молибденовой проволокой при температурах 300–1100 °C, повышается в несколько раз. Армирование серебра волокнами окиси алюминия повышает его прочность в 5 раз. Алюминий, упрочненный волокнами окиси кремния, имеет прочностные свойства лучших алюминиевых сплавов. По данным ряда исследований, введение в вольфрам частиц тугоплавких окислов или карбидов и боридов повышает его длительную прочность и срок службы в 25–50 раз.
Все большее значение приобретают в технике композиционные материалы, армированные монокристаллами – усами или нитевидными кристаллами. Нитевидные кристаллы повышенной прочности встречаются и в природе. К таким кристаллам можно отнести нефрит – разновидность минерала актинолита (лучистого камня, от греч. «актис» – луч, «литое» – камень). Нефрит состоит из игольчато-лучистых, иногда волосовидных агрегатов. Его цвет может меняться в зависимости от содержания в нем закиси железа от светлых зеленовато-серых тонов до темно-зеленых. С древнейших времен нефрит ценят как необычайно прочный поделочный камень. В Самарканде в мавзолее Гур-Эмир выделяется строгой красотой темно-зеленое нефритовое надгробие Тимура.
Мы уже рассказывали об огромной прочности металлических усов. Однако наиболее прочными из всех известных материалов являются графитовые нитевидные кристаллы – их прочность на растяжение достигает 20000 МПа, а модуль упругости составляет 106 МПа. И все это при относительной легкости материала. Известны два способа получения усов графита: в дуге с графитовыми электродами, горящей при высоком давлении, и при термическом разложении углеводородов.
Сапфир – одна из форм существования оксида алюминия. Нитевидные волокна сапфира получают из расплавленной окиси алюминия. Устройством для вытягивания волокон служит молибденовый капилляр, укрепленный на дне молибденового тигля. Расплав окиси алюминия при температуре плавления 2050 °C поднимается по капилляру, захватывается затравкой, с помощью которой вытягивается волокно. Вытягивание волокон диаметром 0,1–0,5 мм производится с достаточно большой скоростью. Прочность сапфировых волокон при растяжении достигает 2600 МПа.
К сожалению, до настоящего времени не разработаны эффективные методы введения нитевидных кристаллов в различные матрицы. Не изучены также в достаточной мере методы предотвращения взаимодействия и достижения необходимой степени сцепления нитевидных кристаллов с матрицей. Это в значительной мере препятствует достижению высокого уровня упрочнения и позволяет использовать только малую часть чрезвычайно высоких свойств нитевидных кристаллов. Кроме того, производство нитевидных кристаллов пока еще очень сложно, и они еще очень дороги.
Правда, в настоящее время освоено промышленное производство усов сапфира и карбида кремния. Цена за последнее время на них снизилась более чем в 200 раз. Волокна сапфира характеризуются высокой химической инертностью к металлам, что дает возможность использовать их в качестве упрочнителей никелевых, кобальтовых, титановых и других сплавов для работы при высоких температурах. Нитевидные кристаллы сапфира (прочность 7000 МПа) и карбида кремния (прочность – 12000 МПа) в будущем станут широко использоваться в качестве армирующих материалов.
Для эффективного использования волокон, как уже отмечалось, необходимо решить проблему хорошего сцепления твердых и прочных нитевидных кристаллов с мягкой и пластичной металлической матрицей. Разрешима ли эта проблема? Оказывается, да! Недавно было найдено, что покрытие из сплава железо – никель – кобальт, нанесенное на поверхность усов сапфира вакуумным напылением, обеспечивает достаточно прочное сцепление волокон этого материала со сплавом никель – палладий. Установлено также, что предварительная обработка поверхности углеродных волокон или нанесение на них барьерного слоя металлов, карбидов или нитридов значительно улучшает их смачиваемость металлом матрицы, а следовательно, и прочность сцепления с ней.
В связи с этим весьма перспективным становится композиционный материал на основе углеродного волокна. Хотя углеродное волокно известно более 70 лет, интерес к нему возник сравнительно недавно, после того как был разработан процесс получения высокопрочных и высокомодульных углеродистых волокон из полиакрил-нитрида. Этим методом при низкотемпературной графитизации получают углеграфитные волокна прочностью 3500 МПа. Углеграфитные волокна выпускаются в виде нитей, содержащих 1000–2000 элементарных волокон.
Давайте представим себе, что ученые и инженеры нашли метод получения дешевых углеграфитных волокон, а еще лучше – нитевидных кристаллов графита, и разработали эффективную технологию армирования такими кристаллами алюминия или пластмассы. Такой материал может быть в 2–6 раз прочнее легированных сталей и гораздо легче самого легкого металла – алюминия. Но этого мало, материал на основе алюминия должен легко подвергаться горячей деформации при 500–550 °C, а на основе пластмассы – 100–120 °C. Последний можно «ковать», например, нагревая в воде или паре.
Автомобиль из такого материала будет в 3–4 раза легче, его сумеет поднять один человек… Кроме того, в любых погодных условиях кузов автомобиля не будет подвержен атмосферной коррозии, а расход горючего сократится в несколько раз. Фантазия? Нет. Фирма «Форд» уже сделала опытный образец такого легкового автомобиля – его стоимость составила 3,5 миллиона долларов!
Появление сравнительно дешевых автомобилей из прочных и легких композитов – дело недалекого будущего. Получение и применение композиционных материалов в промышленности развивается быстрыми темпами. Так, первый высокопрочный композиционный материал, армированный нитевидными кристаллами, был получен в 1961 году, а в 1975 году такие композиции уже применялись в газотурбинных двигателях, корпусах глубоководных аппаратов в качестве пропитанных тканей, тросов, кабелей и других изделий. Есть все основания надеяться, что скоро композиты будут армировать волокнами с пределом прочности 7000–15000 МПа, а промышленность в достаточно большом количестве будет производить дешевые композиционные материалы на их основе. Итак, будущее за материалами со структурой типа булата.