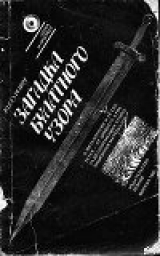
Текст книги "Загадка булатного узора"
Автор книги: Юрий Гуревич
сообщить о нарушении
Текущая страница: 7 (всего у книги 14 страниц)
Златоустовская сталь
Павел Петрович Аносов родился в 1799 году в Петербурге в семье мелкого чиновника горного департамента. В 1810 году по ходатайству деда Льва Собакина, механика Камско-Воткинских заводов, был определен в Петербургский горный кадетский корпус, который был тогда единственным высшим учебным заведением, готовившим специалистов горного дела. Павел Аносов окончил его в 1817 году с Большой золотой медалью. В конце этого же года молодой шихтмейстер прибыл на Златоус-товские заводы в качестве практиканта. Вряд ли он знал тогда, что пройдет путь от практиканта до горного начальника Златоустовских заводов и директора оружейной фабрики, что здесь, в Златоусте, он создаст свою теорию производства литой стали и овладеет вековой тайной получения булата. Начал же он с того, что в 1819 году представил дипломную работу «Систематическое описание горного и заводского производства Златоустовского завода».
В то время Златоустовский завод, хотя и имел уже устаревшее оборудование, но являлся металлургическим предприятием с полным циклом. Чугун выплавляли в доменной печи с двумя горнами, воздух в которые подавался цилиндрическими мехами, приводящимися в действие водяными колесами. Кроме передела на железо и сталь, чугун использовали для литья как в песчаные ила глиняные формы, так и в металлические. Отливали кричные молоты, наковальни, колеса, ядра, бомбы, а также гири, горшки, сковородки и другую хозяйственную утварь. В те годы говорили, что «вся Россия печет блины на уральских чугунах» (сковородах).
Для переработки чугуна в кричное железо и «уклад» (сырцовую сталь) на заводе действовали две кричные фабрики с 12 горнами. Каждый горн имел свой особый кричный молот, приводимый в действие водяным колесом. Для изготовления сортового железа работала специальная передельная фабрика с прокатными и резными станами для получения мерной полосы. Сравнительно небольшое количество стали, шедшее на инструменты и холодное оружие, готовилось из «уклада», который подвергали цементации (науглероживанию). Процесс цементации железа производился в специальных томильных печах при температуре около 1000 °C и длился 7–8 суток. Завод изготовлял 11 сортов железа и стали.
Оружейная фабрика, работающая на заводе, славилась уже не только в России, но и далеко за ее пределами. Златоустовские мастера изготовляли холоднее оружие высокого качества; шашки, сабли, палаши, саперные и охотничьи ножи. Эти изделия успешно конкурировали с европейскими образцами. В то же время инструментальная сталь по своему качеству уступала английской. Это главным образом объясняется тем, что, когда Аносов приехал на Златоустовский завод, там литой стали еще не изготовляли.
Секрет получения литой стали в России первой четверти XIX века являлся достоянием отдельных мастеров. Серьезных успехов в этом деле, как уже было отмечено, добился С. И. Бадаев (Камско-Воткинский завод). Он сконструировал специальную печь, имеющую два отделения – цементационное и тигельное. Кричное полосовое железо подвергалось цементации и после этого расплавлялось в тиглях. Затем производилась вторичная цементация полученной стали при помощи карбюризатора, состоящего из различных сортов угля, перемешанного с белой глиной, мелом и минеральными добавками. «Энциклопедический лексикон» Плюшара за 1835 год об инструментальной бадаевской стали говорил, что она лучше знаменитой «гунцмановской» (английской).
Литую цементованную сталь высокого качества получал также Нижегородский заводчик Полюхов. По заключению монетного двора сталь Полюхова «… оказалась на дело инструмента годная и прочную сыпь имеет мелкую и ровную». Оригинальный способ производства литой стали разработал управитель Велетминского завода Пономарев. Тигельные процессы производства стали появлялись на Верхне-Исетском, Невьянском, Каслинском и других заводах. Этому способствовало распространение отражательных (пламенных) печей, в которые помещали тигли со сплавляемыми материалами. Путем сжигания дров, а потом кокса в струе подогретого воздуха в таких печах удавалось получать температуру до 1500"С.
Однако, как и все новое, литая сталь часто встречала недоверие со стороны многих металлургов. Объяснялось это тем, что способы ее выплавки и разливки были недостаточно совершенны, и иногда металл получался либо низкого качества, либо очень высокой стоимости. Так, например, мастер из Золингена Петр Каймер пытался ввести на Златоустовском заводе литую сталь. Он обставлял свою работу большой таинственностью, к плавкам готовился долго и за два года работы выдал всего 9 пудов относительно годной стали. А обошлась его сталь в 10–15 раз дороже цементованной. По этим и другим причинам государственный департамент часто отказывался выдавать привилегии на способы производства тигельного металла. Между тем многие поступающие изобретения имели, очевидно, немалую ценность. Это подтверждает недавно установленный факт, что из всех русских архивов бесследно исчезли описания различных приемов получения стали, применявшихся в то время на заводах страны.
Проанализировав имеющийся опыт различных способов выплавки стали для оружия и инструмента, П. П. Аносов пришел к выводу, что только литая сталь может обладать необходимыми свойствами. «Литая сталь, – писал он, – имеет преимущество перед выварною и цементною из тех же первых материалов, полученных как по равномерному, так и более тесному или химическому соединению частей углерода с железом». Так, П. П. Аносов, исходя из чисто научных соображений, обосновал целесообразность тигельного производства. Предварительные опыты по получению литой стали окончательно убеждают его: только организация тигельного производства коренным образом улучшит качество стального оружия и инструмента на Златоустовском заводе.
Аносов хорошо себе представлял, что производство литой стали складывается из следующих операций:
«Устройство печей, приготовление плавильных горшков, плавка, отливка в формы и ковка». Поэтому он начал с устройства пламенных печей. Им был спроектирован отапливаемый углем горн для печи с подогревом восьми тиглей одновременно и сооружен корпус с восемью такими печами. Печи для выплавки тигельной стали эксплуатировались на Златоустовском заводе до начала XX века, то есть чуть ли не 100 лет!
Одной из самых трудных задач во времена Аносова являлась организация производства тиглей – «плавленных горшков», как их называли. Производство глиняных тиглей было хорошо известно, так как они применялись для литья цветных металлов, а позднее – для переплавки чугуна. Мастер Боткинского завода Федор Мезенцев даже придумал ручной винтовой штамп для приготовления «плавиленных горшков». Но для приготовления литой стали требовались тигли очень высокой огнеупорности. Такие тигли выписывались из-за границы, из города Пассау в Баварии, около которого находились залежи высокоогнеупорной глины. Цена их была очень высокой. Поэтому Аносов пришел к выводу, что «иностранные горшки особенно в столь отдаленном месте, как Златоуст, были бы слишком дороги для стального производства, и, не заменив их своими, успех был бы безнадежен».
А горшки из челябинской глины как будто и обладали достаточно большой огнеупорностью, но постоянно трескались при высоких температурах. Исследование причин образования трещин показало, что они получались вследствие расширения частиц глины: при высоких температурах одни частицы «давили» на другие. Аносов понял, что трещины в горшках являются результатом большой усадки, которую давала глина при нагревании. Для предупреждения трещин было необходимо добавить к глине «тело, которое бы уменьшило… способность сжимания». Аносов делает анализ заграничной глины и находит, что этим «телом» являлся графит. В пассауских горшках сама природа позаботилась соединить глину с графитом. Итак, для предупреждения трещин тигля в челябинскую глину надо добавить графит. Но где его взять?
ГЛАВА ТРЕТЬЯ
СНОВА ТАЙНА
Река истины протекает через каналы заблуждении.
Р. Тагор
Рецепт есть, булата нет
На рабочем столе Владимира Ильича Ленина, в его кабинете в Кремле лежит нож для разрезания бумаг – это подарок златоустовских рабочих, сделанный Ленину в 1921 году. Стальной клинок ножа украшен тонким чернением и эмалевым орнаментом. Ручка черного дерева – отличной ручной работы. На лезвии ножа изображены корпуса оружейной фабрики и вытравлена надпись: «Товарищу Ленину. Златоустовская оружейная фабрика». Окантовка рисунка и надпись выполнены золотом.
Ленин хорошо знал златоустовскую сталь и ценил ее высокое качество. Он очень любил свой охотничий «булат», клинок которого был изготовлен еще в конце XIX века. Этот нож в деревянных ножнах, с рисунком на лезвии, изображающим два ружья, охотничью сумку и оленьи рога, был преподнесен ему в апреле 1920 года, в честь его пятидесятилетия рабочими Златоуста.
Умели ли в Златоусте делать булат в конце XIX века? Однозначно ответить на этот вопрос трудно. Целесообразнее внимательно проанализировать некоторые исторические факты.
Незаменимым помощником П. П. Аносова при изготовлении булатных слитков был выдающийся стальных дел мастер Николай Иванович Швецов. Он был родом из крепостных, потомственных «варовщиков» (сталеваров). Его дед Макар Швецов варил железо на якорной фабрике Боткинского завода. Отец Николая Ивановича был куплен екатеринбургским начальством и привезен в Златоуст. За проявленное усердие в работе Николай Иванович получил «вольную», которая освобождала его семью от «телесного наказания за провины». Н. И. Швецов грамоте обучен не был, но лучше его никто не мог «прочитать» родословную любой стали. Осмотрев кусок металла, он мог определить, как выплавлена сталь, как откована, равномерно ли нагрета под ковку, правильно ли закалена. По излому стали и размеру ее зерен он безошибочно предсказывал ее свойства.
После того как П. П. Аносов в 1847 году стал томским гражданским губернатором, начальником Алтайских горных заводов и уехал из Златоуста, Н. И. Швецов продолжал плавить булат. Он был человеком скрытным и приемы изготовления узорчатой стали держал при себе. Четверо его сыновей работали на Златоустовском заводе, но секреты производства булата он доверил только старшему – Павлу.
Павел Николаевич Швецов с семи лет уже ходил с отцом на завод. После окончания горнозаводской школы он освоил профессии слесаря, токаря по сверлению ружейных стволов и машиниста воздуходувной машины. Лишь в 1880 году он стал сталелитейным мастером и проработал на этой должности почти 45 лет. Высокого роста, худой и седой, в очках и фартуке, он напоминал колдуна, когда смешивал различные порошки при составлении шихты для варки стали. Павел Николаевич был человеком строгого и молчаливого нрава, он никогда никому не объяснял, что и зачем делает. Он сам плавил сталь, сам изготовлял из нее клинки и различный инструмент, сам определял их структуру и качество.
В 50-х годах прошлого века производство булатной стали на Златоустовском заводе резко сократилось, ее готовили только по специальным заказам. Это, возможно, было связано с тем, что в это время горный инженер П. М. Обухов организовал широкое производство тигельной стали для отливки пушечных стволов. Есть также сведения, что вплоть до 1875 года отдельные заготовки булата, сделанного ещё во времена П. П. Аносова, хранились на заводском складе и употреблялись только для такого инструмента, которому нужна была очень высокая твердость и стойкость.
П. Г. Бояршинов, который с 1902 года работал на заводе рядом с П. Н. Швецовым, рассказывал о таком случае. В 1905 году, возвращаясь с русско-японской войны, в Златоусте остановился какой-то высокий чин, Офицер обратился к управителю завода с просьбой сделать ему такую шашку, которая бы рубила все существующие в заграничных армиях клинки, оставаясь целой и невредимой. Офицер объяснил: он поспорил с ехавшими с ним в поезде иностранными военными, утверждая, что шашки, изготовленные златоустовскими мастерами, имеют значительно более высокое качество, чем лучшие заграничные. Управитель завода и приехавший офицер уговорили П. Н. Швецова заняться этим заказом. П. Г. Бояршинов и мастер К. К. Моисеев помогали своему учителю отливать слиточки булата.
В печи Сименса на 28 тиглей булат готовили только в одном тигле, который ставили в самое горячее место печи. В тигель с булатом загружали не более 8 кг шихты, в то время как в тигли с обыкновенной сталью закладывали 30–32 кг металла. После окончания плавки сталь медленно охлаждали. Полученный слиточек в виде хлебца медленно подогревали до красного каления, надрубали зубилом и раскалывали под молотом пополам. С половинок снимали внешнюю корку, подогревали на горне и клали разрезанной плоскостью на наковальню. Ковали заготовку на полосу сечением 25Х40 мм, из которой специальными приемами делался клинок. Нагрев под закалку и отпуск осуществляли в ваннах с расплавленным свинцом. Для травления клинка применяли пивной уксус в смеси со слабой соляной кислотой.
Подобным образом в конце 1905 года Швецов отлил много слиточков булата разного состава, делал из них клинки, но качество их ему пока не нравилось. Таким образом, у П. Н. Швецова булат получался не всегда.
«Прихожу я однажды на работу, – вспоминал П. Г. Бояршинов, – а Павел Николаевич вынимает из шкафа грубо отполированный клинок и говорит: «Вот это наконец-то то, что надо. Наши шашки рубит. А раз наши рубит, то обязательно будет рубить и заграничные».
Сдал П. Н. Швецов клинок на оружейную фабрику, сделали там из него шашку, отполировали, красиво отделали, поставили марку завода и послали тому самому офицеру. А через некоторое время управителю завода пришло письмо, в котором сообщалось, что пари офицер выиграл, а мастера за выполнение заказа благодарит и награждает вместе с помощниками деньгами.
В Златоустовском музее можно увидеть поковку булата, приготовленную П. И. Швецовым. Сохранились также образцы его клинков с ярко выраженным волнистым рисунком (фото 4). Но самое важное, что в этом музее хранится записная книжка П. Н. Швецова, в которой он отмечал составы шихты и результаты опытных плавок. Начало записей относится к 1883 году. Из них можно заключить, что автор готовил в тиглях не только булат, но и сплавы с кремнием, молибденом, ванадием, титаном и изучал их свойства. Интересно, что в этих же тиглях из руд и сырых материалов приготовлялись ферросплавы.
Еще в 1884 году П. Н. Швецов сплавлял железо с хромом и получал высокохромистую нержавеющую сталь. Он плавил также быстрорежущую инструментальную сталь, которую называл «самозакалкой». В 1903 году завод заключил договор с австрийской фирмой «Бр. Беллер» на поставку инструментальной стали марки «рапид». Особые пункты договора охраняли исключительное право фирмы на рецепты приготовления этой стали и на сбыт ее в России и за границей в течение последующих 10 лет. В короткий срок в Златоусте было освоено производство стали «рапид», но при этом выяснилось, что «самозакалка» Швецова ей не уступает. Договор с фирмой был досрочно расторгнут, на заводе начали плавить швецовскую инструментальную сталь, которая долгое время была известна под названием «рапид-самокалка».
В записной книжке Швецова часто упоминается «Ломъ булата» или «булат». Помечено, что свойства булата достигались при плавке шихты, состоящей из 1,5 фунта кричного железа, 0,25 фунта зеркального чугуна, 1,5 золотников синеродистого калия и 0,5 золотников марганцовистого чугуна. В 1906 году П. Н. Швецов продал рецепты приготовления булата дирекции Златоустовского завода. Рецепты были, а булата – не было. После 1905 года в Златоусте никто делать булата уже не умел. Секрет его получения вновь оказался безвозвратно потерянным…
Чем же объяснить, что еще при жизни П. Н. Швецова перестали плавить узорчатую сталь? Ответ на этот вопрос сравнительно прост. Дело в том, что в начале XX века изобретают и начинают широко применять легированные стали. Физико-механические свойства таких сталей гораздо выше не только углеродистых, но и булатных. Нет ничего удивительного, что ещё француз Беотье и другие западные металлурги принимали за булат хромистую сталь.
Старожилы Златоуста любят рассказывать такой случай. В 20-е годы кавалерийские сабли и шашки делались уже из стали, содержащей примерно 3 % хрома. Однажды на завод попал известный военный кавалерист и, увидев булатные сабли, поинтересовался, насколько лучше они современных. Ему разрешили «рубануть» современной шашкой по булатной и… на булатной сабле осталась зазубрина! Хром, молибден, вольфрам и другие легирующие элементы так повышают твердость и прочность стали после закалки, что булату с ней тягаться не под силу. Вот почему легированные марки стали, получаемые тигельным процессом, часто принимали за булат. Так, например, мастер К. К. Моисеев утверждал, что ему приходилось лично в 1920–1925 годах плавить «булат» следующего состава (в%): углерод – 1,55–1,44; хром – 0,7–0,8; марганец – 1,52–1,64; вольфрам – 0,69–0,86. Конечно, свойства этой легированной стали не уступали булату!
Таким образом, в начале XX века легированные стали позволяли получать холодное оружие и инструмент очень высокого качества. Необходимость приготовления булата полностью отпала.
Узорчатая сталь? Сколько угодно!
В XIX веке последователи Аносова, известные русские металлурги П. М. Обухов, А. С. Лавров, Н. В. Калакуцкий развивали его идеи о получении совершенной стали, искали научные обоснования металлургических процессов. Так, например, А. С. Лавров изучал строение стального слитка, впервые применил алюминий для удаления кислорода из стали, выдвинул идею подогрева верхней части слитка термитными смесями для того, чтобы уменьшить его усадку и увеличить выход годного металла. Совместно с Н. В. Калакуцким он открыл и объяснил ликвацию стали – неравномерное распределение примесей в объеме слитка. Работы Аносова и его последователей продолжил выдающийся ученый-металлург Д. К. Чернов, обобщения и открытия которого в начале XX века завершили формирование металлургии как пауки.
В 1878 году Д. К. Чернов описал характер затвердевания (кристаллизации) стали и показал особенности перехода ее из жидкого в твердое состояние. Он разработал схему образования кристаллов в жидком металле, исходя из того, что они состоят из дендритов – древовидных образований. Чернов собрал большую коллекцию кристаллов, которые были извлечены из стальных слитков. Некоторые из них достигали размеров 3–5 мм.
Однажды полковник А. Г. Берсенев, служивший приемщиком на металлургическом заводе, нашел в груде стального лома на шихтовом дворе огромный кристалл. В собрании Чернова это был самый крупный дендрит – он весил почти 3,5 кг и имел длину около 40 см. Вскоре он стал широко известен как «кристалл Чернова».
Величину дендритов Д. К. Чернов связывал с условиями охлаждения стали: «Если расплавленную в тигле сталь вы будете при охлаждении приводить постоянно в сильное сотрясение, достаточное для того, чтобы все частицы ее приходили в движение, тогда слиток будет иметь чрезвычайно мелкие кристаллы, – писал Д. К. Чернов, – если же эту сталь оставить без всякого сотрясения и дать массе спокойно и медленно охлаждаться, тогда у вас эта же сталь получится в крупных, хорошо развитых кристаллах».
Склонность стали к кристаллизации, форма кристаллов и их взаимное расположение зависят не только от условий кристаллизации, но и от химического состава стали, степени ее загрязнения вредными примесями. Чем меньше примесей в стали, тем легче получить при кристаллизации ее крупные кристаллы. Исходя из этого, Д. К. Чернов считал, что первоначальная крупная кристаллическая структура является первоосновой булатного узора. Это утверждение как будто совпадало с рекомендациями П. П. Аносова, который писал, что «для получения совершенного булата» необходимы особой чистоты материалы, «сильный жар во время плавки», «медленное охлаждение тигля» и «наименьшее нагревание при ковке».
По указанию Д. К. Чернова его сотрудники не раз пробовали плавить булат. Они брали железо, чистое по фосфору и сере, сплавляли его с серебристым графитом в присутствии окалины и флюса, сильно нагревали и медленно охлаждали в огнеупорных тиглях. Поверхность слитков шлифовали, полировали и травили кислотой. И действительно, слитки имели ярко выраженные древовидные узоры. Елочки со стройными стволами и строго симметричными ветвями отбрасывали серебристые тени и были очень красивы. Слитки разрезали, вновь шлифовали, полировали, травили, и узоры повторялись, они были присущи всему объему металла.
Остался, казалось бы, пустяк: известными приемами ковки сплести стволы и ветви узора так, чтобы получить рисунок, характерный для булатов. Но как раз это не получалось. Д. К. Чернов твердо установил, что нагрев стали под ковку до обычных температур (800–1100 °C) невозвратимо уничтожает дендритные узоры…
Для того чтобы сохранить узоры, необходимо ковать сталь при достаточно низкой температуре, считал Д. К. Чернов. Если это соблюдено, то нарушения кристаллического строения не происходит, в «сплетения» кристаллов должны изменить свой вид так или иначе, более или менее в зависимости от направления и степени вытягивания при обработке. Поэтому, выковав пластинку и вытравив кислотой ее шлифованную поверхность, получают узор иного вида, с красивыми линиями или вроде фибр дерева, например дуба. Однако найти температуру ковки, при которой бы сохранялись узоры, не удавалось. И Чернов долго считал, что искусство древних кузнецов основывалось на знании секретов пластической деформации стали при «наименьшем нагревании».
Позднее Чернов объяснял свойства булата не только «сплетением» кристаллов, но и ликвацией углерода. Когда булатный слиток остывает, то первой начинает кристаллизоваться более тугоплавкая малоуглеродистая сталь. Между дендритами этой стали располагаются возникающие позже кристаллики менее тугоплавкой высокоуглеродистой стали. Поэтому и получается сложное переплетение твердых и пластичных кристаллов. Описанное явление сегодня широко известно как дендритная, или внутрикристаллическая, ликвация углерода.
Дендритная ликвация углерода и легирующих элементов оказывает значительное влияние на свойства легированных сталей после горячей деформации. Этому явлению, открытому Д. К. Черновым, уже в наше время посвящено немало научных работ.
Ученик Чернова Н. Т. Беляев, понимая невозможность превратить в булатный узор дендритную структуру литого металла путем низкотемпературной деформации, несколько иначе излагает взгляды своего учителя на происхождение булатного узора. Он обращает внимание на то обстоятельство, что при медленном охлаждении стали ветви дендритов «состоят из последовательного ряда концентрических оболочек попеременно меняющегося состава, что и влечет за собой появление в вытравленном рисунке булата концентрических очертаний и часто замкнутых фигур». Другими словами, Н. Т. Беляев утверждает, что благодаря дендритной ликвации углерода булатный узор появляется в слитке еще до того, как его подвергают ковке. Поскольку в данном случае выявление дендритной структуры связано с участками, обогащенными или обедненными углеродом, оно должно происходить и после высокотемпературной деформации металла.
Экспериментальной проверкой этой теории булатного узора занялся другой ученик Д. К. Чернова – Н. И. Беляев. Он проковал в пластины два одинаковых куска стали, содержащей 1,35 % углерода, и подверг их длительному отжигу. После этого один кусок ковался при температуре 65°, а другой – при 1000 °C. Оба шлифа были протравлены на дендритную структуру. При высокотемпературной ковке дендритная структура выявлялась после закалки образцов. Это дало основание Н. И. Беляеву связать булатный узор с дендритной ликвацией углерода и подтвердить теорию своего учителя.
В одном Д. К. Чернов и Н. И. Беляев были совершенно правы: они открыли секрет так называемого «литого булата» Аносова. Дело в том, что в трудах П. П. Аносова есть описание способа производства стали, которая изготовлялась в тиглях путем переплава предварительно науглероженного железа и отливалась в формы. Литая сталь подвергалась длительному отжигу без доступа воздуха в специальных тщательно закупоренных ящиках. Аносов скрупулезно исследовал режимы отжига и установил, что правильно отожженная сталь имела чистую поверхность без следов окалины, хорошую вязкость и крупнозернистое строение. На поверхности стали были видны узоры. Аносов писал: «Отожженная сталь, как имеющая узоры, подобно булатным, должна нести и одинаковые с ней названия. Для отличия от настоящего булата я называю ее литым булатом».
Таким образом, узоры, получающиеся после длительного отжига металла, безусловно связанные с дендритной ликвацией углерода, Аносов не считал «настоящими булатными». К аналогичным выводам пришел впоследствии и Н. И. Беляев: «Будучи далек от мысли воспроизвести лучший коленчатый узор индийских мастеров, я тем не менее даю образы того, как, видоизменяя ковку, можно видоизменять узор, делая его более красивым и более совершенным в механическом смысле». Итак, настоящих булатных узоров и Н. И. Беляеву воспроизвести не удалось.
Подчеркнем: работы Д. К. Чернова, Н. Т. Беляева и Н. И. Беляева по кристаллизации стали и дендритной ликвации примесей заложили основу современной теории кристаллизации и показали ее роль в обеспечении качества стали. Позднее мы увидим, что на основе исследований булата были разработаны и другие важные положения металлургии.
Теперь хорошо известно, что дендритная структура наиболее хорошо выявляется в сталях, имеющих значительное содержание углерода (более 0,8 %,) или легирующих элементов. В литом металле она проявляется сравнительно легко, в деформированном – только продолжительным травлением специальными реактивами. Между тем имеется много свидетельств тому, что булатные узоры выявляются весьма слабыми травителями, в том числе и такими, как соки растений и плодов. Даже чистая вода в присутствии воздуха в течение нескольких минут выявляла булатный узор. Поэтому легкость проявления узора всегда считалась отличительным признаком булата. Мы уже знаем, что в лучших булатах узоры вообще выявлялись непосредственно после полировки.
Надо отдать должное Д. К. Чернову, он первым строго научно объяснил природу булата и связал ее со свойствами этой удивительной стали. Он считал, что при затвердевании сталь распадается на два различных соединения железа с углеродом, которые «играют очень важную роль при назначении такой стали на клинки: при закалке более твердое вещество сильно закаливается, а другое вещество остается слабо закаленным, но так как оба вещества в тонких слоях и фибрах тесно перевиты одно с другим, то получается материал, обладающий одновременно и большей твердостью, и большей вязкостью. Таким образом, оказывается, что булат несравнимо выше лучших сортов стали, приготовленной иными способами».