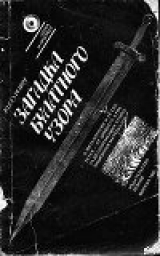
Текст книги "Загадка булатного узора"
Автор книги: Юрий Гуревич
сообщить о нарушении
Текущая страница: 11 (всего у книги 14 страниц)
Вторая группа секретов относится к искусству ковки и получению булатных узоров. Многие приемы ковки булата сегодня осмыслены и познаны, воспроизведены почти все известные булатные узоры. Но тут еще последнее слово не сказано, работы в этой области продолжаются.
Третья группа секретов касается чистоты исходных материалов, обеспечивавшей особый химический и фазовый состав углеродистой стали, вырабатываемой в древности. Эти секреты современная наука также постепенно раскрывает.
Четвертая группа секретов включает термическую и химико-термическую обработку стали. Многовековой опыт металлообрабатывающего ремесла позволил оружейникам найти оптимальные режимы термомеханической обработки, цементации, закалки и отпуска стали, которые они держали в секрете. За время, прошедшее с тех пор, термическая обработка стали превратилась в стройную науку. Пользуясь современными теоретическими и экспериментальными методами анализа, можно раскрыть многие секреты, касающиеся термообработки древнего булата.
Наконец, пятая группа секретов касается отделки булатного оружия. Здесь следует решительно признать: воспроизведение методов шлифовки и полировки древних клинков – дело для нас чрезвычайно трудное. Поэтому пока еще никому не удалось достичь легендарной упругости булатных клинков.
Исходя из секретов производства булатной стали сегодня можно достаточно убедительно ответить на вопрос: что такое булат? Но ответ этот будет не прост.
Булат – это углеродистая заэвтектоидная сталь. Булат не только углеродистая сталь, булат – сталь сверхуглеродистая, близкая по составу к чугуну. Булат не только сверхуглеродистая сталь, булат – сталь особо чистая, без посторонних примесей. И наконец, булат – высокоуглеродистая сталь, обладающая неравновесной структурой, с ярко выраженной макро– и микронеоднородностью. Булат – слоистая сталь. Очень твердые слои с высоким содержанием углерода чередуются в булате со слоями, мало насыщенными углеродом и поэтому пластичными. В процессе ковки все слои переплетаются, образуя характерный естественный рисунок. Булат – узорчатая сталь. Структура булата после применения специальных методов ковки, термомеханической обработки и отделки обеспечивает ему необычайно высокие механические свойства. Булат – сталь, обладающая одновременно высокой твердостью, прочностью, вязкостью и упругостью. Чередование мягких и очень твердых участков на лезвии клинка превращает его в микропилу и обеспечивает самозатачиваемость. Булат – сталь, обеспечивающая необычайную остроту лезвия клинка и его самозатачиваемость. Таким образом, в понятие «булат» вкладывается целый ряд характерных особенностей этой замечательной стали.
ГЛАВА ПЯТАЯ
СТАРЫЕ ЗНАКОМЫЕ
Пусть человек пользуется прошедшими веками как материалом, на котором возрастает будущее…
Жан Гюйо
Наследники булата
Холодное оружие давно потеряло ценность, а с ним ушли в прошлое и булаты. Еще раз подчеркнем: в сравнении с высокопрочными и вязкими легированными сталями булат не представляет ничего выдающегося.
Кроме того, для всех рассмотренных способов производства булатов характерна сложная и длительная технология, которая к тому же не позволяет получать изделия точных размеров и формы. Для требуемой макроструктуры (узора) булата и придания изделию нужных размеров и формы необходима дополнительная механическая обработка. Практическая невозможность изготовления слитков булата массой более 30–50 кг без существенного нарушения требуемой физической неоднородности делает процессы приготовления стали, аналогичной древнему булату, очень дорогими и поэтому экономически невыгодными для современного производства.
Современная техника нашла много других способов выплавки сталей и сплавов. Легированные стали с широким диапазоном изменения физических и механических свойств получают по сравнительно простой технологии в многотонных сталеплавильных агрегатах. К булату остался сегодня только исторический интерес. Но идеи, заложенные в выборе сходных материалов для получения булата, в способах его производства, в его строении и свойствах, живут до сих пор. То, к чему древние ремесленники пришли эмпирически и чего П. П. Аносов добился кропотливым и упорным трудом, сегодня служит металлургам научной основой для получения материалов с высокими физико-механическими и служебными характеристиками.
Сначала на базе исследований булата были разработаны многие классические идеи металлографии стали и сплавов; а затем – и приемы его приготовления, и высокие свойства его необыкновенной структуры начали широко использоваться при разработке самых различных технологических процессов получения сталей, сплавов и композиционных материалов.
В проблемной лаборатории Донецкого политехнического института некоторое время назад появился удивительный нож. Для того чтобы заточить его лезвие, понадобился алмазный круг, обычный наждак не брал. После рубки ножом толстых гвоздей на его поверхности не оставалось даже царапины. Но самое удивительное, что этот нож, так же как и булат, был сделан не из легированной стали, а из простого сплава железо – углерод.
Впрочем, сплав был не такой уже простой, он содержал 3,5 % углерода. По составу это был чугун… Несмотря на это, сплав отлично ковался и прокатывался. Резцы и фрезы из него неплохо обрабатывали сталь и не уступали по прочности инструменту из легированной инструментальной стали. Как тут не вспомнить легендарные рельсы из Катав-Ивановска, которые так помогли уральцам в тяжелые времена Отечественной войны!
Только теперь свойства чудо-ножа можно легко научно объяснить. Нож был приготовлен из сплава, специально очищенного от вредных примесей и мельчайших частиц неметаллических включений. А в этих условиях карбидам железа выпадать трудно.
Электронно-микроскопический и масс-спектрографический анализы показали, что углерод в сплаве находится в необычном аморфном состоянии, при котором он, увеличивая прочность и твердость металла, не делает его хрупким. Предвидение П. П. Аносова о различном состоянии углерода в железе и влиянии этого состояния на качество стали научно подтвердилось.
Уже не раз подчеркивалось: П. П. Аносов был уверен, что своими высокими свойствами булат обязан чистоте исходных материалов – железу и графиту. Читатель, очевидно, помнит, что при получении железа кричным или пудлинговым процессом значительная часть поверхности металла, так же как и при получении чугуна в доменной печи, контактировала с жидким шлаком. Шлак, как губка, впитывал и растворял вредные примеси и неметаллические включения, обеспечивая тем самым высокую чистоту пудлинговой стали.
Как уже отмечалось, современную сталь получают многоступенчатым процессом. Простейший из них – это доменная печь, а затем сталеплавильный агрегат, мартен, электропечь или кислородный конвертер. Готовую сталь разливают в слитки. Такая схема получения стали высокопроизводительна, но она часто не обеспечивает необходимую чистоту металла по вредным примесям. Что касается неметаллических включений, то мало того, что их трудно удалить во время плавки, они еще в значительных количествах попадают в сталь из материалов сталеплавильных агрегатов и ковша. Поэтому в наши дни чистота стали еще более актуальна, чем в аносовские времена.
Как же металлурги решают эту проблему? А все так же: пытаются использовать для очистки стали от ненужных компонентов ее взаимодействие с жидким шлаком.
Сначала такие процессы организовывались непосредственно в сталеплавильных агрегатах путем так называемого диффузионного раскисления. Его сущность состоит в продолжительном рафинировании металла в печи под восстановительным шлаком. В период рафинирования жидкая сталь взаимодействует со шлаком, в результате чего он отбирает у нее кислород и серу. Оказалось, что скорости этого процесса очень малы из-за относительно небольшой поверхности соприкосновения рафинирующего шлака с металлом.
Исчерпав возможности улучшения качества стали в сталеплавильных агрегатах, ученые и инженеры предложили внепечной способ ее очистки от вредных примесей. Еще в 1925 году советский инженер А. С. Точинский успешно рафинировал сталь жидкими синтетическими шлаками после слива ее из печи в ковш. Первые опыты по такой обработке стали в СССР были проведены в 1928 году, но не получили распространения из-за того, что предложенные в то время синтетические шлаки не обеспечивали должной десульфурации стали. Позднее опыты были продолжены во Франции, где Р. Перрен более успешно решил поставленную задачу.
Наиболее эффективного рафинирования металла жидкими синтетическими шлаками достигли ученые С. Г. Воинов, А. Г. Шалимов, Л. Ф. Косой, Е. С. Калинников в 1958–1962 годах. Суть предложенного ими способа заключается в следующем. В ковш вначале заливают необходимое количество синтетического шлака требуемого состава, а затем на этот шлак по возможности с большей высоты мощной струёй выпускают металл из сталеплавильного агрегата. Жидкий синтетический шлак разбрызгивается, и его капли «прилипают» к металлу. В результате этого поверхность соприкосновения металла и шлака неизмеримо возрастает, что и приводит к быстрому удалению из стали серы и неметаллических включений.
Промышленный опыт применения новой технологии рафинирования металлов подтвердил его эффективность для малолегированных сталей, выплавляемых в мартеновских печах или кислородных конвертерах. Однако, как оказалось, поверхность взаимодействия жидкой стали со шлаком и в этом случае недостаточно велика. По этой и другим причинам требуемого качества некоторых легированных сталей получить не удалось.
И тогда в Институте электросварки им. Е. О. Патона группой исследователей (Б. И. Медовар, Ю. В. Латаш, Б. Н. Максимович) под руководством академика Б. Е. Патона был разработан оригинальный способ получения высококачественной стали с помощью того же жидкого шлака. Новый процесс получил название электрошлакового переплава. В его основу был положен электрошлаковый процесс плавления расходуемых электродов в сочетании с принудительным формированием слитка в металлическом (медном) водоохлаждаемом кристаллизаторе (изложнице).
Созданная установка оказалась удивительно простой. По тонкой многометровой колонке движется держатель с расходуемым электродом, сделанным из выплавляемой марки стали. Электрод медленно опускается в медный кристаллизатор с расплавленным в нем синтетическим шлаком специально подобранного состава. В начале плавки после подачи электрического тока между кристаллизатором и электродом образуется дуга, горящая под слоем твердого сыпучего флюса. Флюс, расплавляясь, образует электропроводный жидкий шлак, который полностью шунтирует дугу. Начинается бездуговой процесс, получивший название электрошлакового. Выделяемое тепло медленно плавит стальной электрод, и капли жидкого металла, проходя через толщу шлака, попадают в кристаллизатор, где постепенно наращивается стальной слиток. Благодаря тому что каждая капля жидкого металла проходит через шлак, поверхность взаимодействия стали со шлаком огромная, и это обеспечивает достаточно полную очистку стали от ненужных компонентов.
Так вот, в Донецком политехническом институте использовали установку электрошлакового переплава для получения сплава железа с углеродом. Для этой цели стальной расходуемый электрод заменили графитовым, а в синтетический шлак порциями подавали металлизованные железные окатыши (комки руды, содержащие металлическое железо и его окислы). Окислы железа восстанавливались, железо плавилось, насыщалось углеродом, очищалось шлаком от вредных примесей и неметаллических включений и стекало в кристаллизатор. Так древний одностадийный способ получения незагрязненного вредными примесями высокоуглеродистого сплава был осуществлен на современной научно-технической основе.
Однородность или неоднородность?
Как мы уже выяснили, в начале XIX века существовали два совершенно противоположных подхода к природе стали, обеспечивающих ее высокое качество. Ле-Шателье и Карстен, известные западноевропейские металлурги, полагали, что хороший металл должен обладать однородной структурой: «Чем красивее структура, тем она хуже с точки зрения практики». П. П. Аносов считал, что чем неоднороднее металл, чем более подчеркивается неоднородность рисунком, тем выше свойства стали.
Современная наука подтвердила правомерность обоих этих взглядов. Каждый из способов был использован для получения высокопрочных материалов.
В последние годы с большим успехом развивается совершенно новое направление производства «однородных» сплавов – получение так называемых аморфных металлов. Жидкий сплав охлаждают с огромной скоростью, благодаря чему он переходит в твердое состояние, минуя кристаллическую фазу. Свойства таких «стеклообразных» металлов очень высокие. Так, например, прочность аморфного сплава железо – углерод – фосфор в 10 раз больше обычного (кристаллического). Кроме того, подобно железу, падавшему на Землю из космического пространства, аморфные сплавы обладают высокой стойкостью против атмосферной коррозии.
И все-таки слоистая структура булата и способы ее получения лежат в основе технологии производства материалов, также превосходящих по прочности обычные «однородные» стали. Для того чтобы понять природу упрочнения слоистых материалов, давайте мысленно проделаем такой эксперимент. Возьмем кусок картона я попробуем его разорвать. После этого наклеим на картон обычную бумагу и вновь испытаем его прочность на разрыв. Как, по-вашему, она увеличилась? Ответ настолько ясен, что вопрос, вероятно, вызовет улыбку читателя.
Между тем только в 30-е годы нашего столетия было обнаружено, что прочность двух сваренных между собой пластинок из твердой и мягкой стали значительно выше прочности каждой из них в отдельности. Такой эффект повышения прочности слоистого материала считался крупным научным открытием нашего времени!
Алексей Максимович Горький часто показывал своим гостям три небольших металлических бруска. Это первые самозатачивающиеся резцы, сделанные в 1926 году талантливым ученым и изобретателем А. М. Игнатьевым – большим другом писателя. Каждый резец состоит из нескольких металлических слоев разной твердости. Булатную структуру инструмента автор изобретения заимствовал у… бобров. Он заметил, что самозатачивающиеея зубы бобров и других грызунов состоят из твердых наружных слоев и мягких внутренних. Изобретение А. М. Игнатьева было в свое время запатентовано в США, Англии, Франции и многих других странах.
Сегодня слоистые материалы находят широкое применение в химической, электротехнической, машиностроительной, пищевой и других отраслях промышленности, а также в ювелирном деле и медицине. Представителями их являются биметаллические изделия, листы и ленты, изготовляемые металлургической промышленностью. Такие изделия привлекают не только прочностью, но и высокими физико-химическими свойствами материала в целом. Основой для большинства биметаллов является обычная низкоуглеродистая сталь, плакированная (покрытая) коррозионно-стойкими и кислотоупорными сплавами, никелем, кобальтом и титаном. Толщина покрытия обычно составляет 10–50 % от общей толщины. Эксплуатационные свойства таких биметаллов изменяются в широких пределах.
В качестве основы для покрытия применяются также углеродистые и легированные стали и чугуны. Знаменательно, что, подобно булату, двухслойные и трехслойные углеродистые легированные и инструментальные стали нашли широкое применение для производства различного инструмента, промышленных ножей, пил, штампов, лемехов и лущильников тракторных плугов.
Как тут не вспомнить заключительные строки сочинения П. П. Аносова «О булатах»: «Оканчиваю сочинение надеждою, что скоро… наши земледельцы будут обрабатывать землю булатными орудиями, наши ремесленники выделывать свои изделия булатными инструментами, одним словом, я убежден, что с распространением способов приготовления и обработки булатов они вытесняют из употребления всякого рода сталь, употребляемую ныне на приготовление изделий, требующих особенной остроты и стойкости».
Многослойные металлы изготовляются несколькими методами. Некоторые из них очень похожи на один из способов приготовления булата. В изложницу (форму), в которую заливают жидкую сталь, помещается несколько попарно скрепленных пластин плакирующего металла на некотором расстоянии друг от друга. Между поверхностями соприкосновения пластин каждой пары расположен слой разделяющего вещества. Заливкой в изложницу жидкого металла получают многослойный слиток, из которого после прокатки и обрезки кромок получают один трехслойный и два двухслойных листа. Подобным образом в изложнице устанавливают большее количество пластин и получают слиток с 5–9 слоями. Можно с полным основанием утверждать, что таким способом можно делать и булат…
Металлические усы
Это произошло в Англии во время второй мировой войны. Новые, весьма необходимые автоматические приборы, использующиеся в военной технике, выходили из строя один за другим – замыкались контакты. Причину замыкания долго найти не могли. Наконец, после тщательного наблюдения установили: виновники аварии – тонкие волоски олова, выступавшие на тончайшей оловянной пленке, нанесенной на сталь. Волоски состригли, и приборы начали работать. Через некоторое время контакты вновь замкнулись, и исследователи опять обнаружили все те же волоски олова. Сколько их в дальнейшем ни «стригли», они вырастали вновь. Волоски были названы усами.
После войны многие ученые начали исследовать причины появления усов, определять их свойства. Ус имел толщину около 1,5 мк. Оказалось, что тончайший ус обладал колоссальной прочностью. Если бы такой волосок имел сечение в 1 мм2, он бы выдержал нагрузку в несколько сот килограммов! Это значит, что прочность металла близка к теоретической. Рентгеноструктурный анализ помог разгадать чудесные свойства усов: они представляли собой почти бездефектные, «идеальные» монокристаллы чистого олова!
Как показали дальнейшие эксперименты, отсутствие дефектов в усах объяснялось условиями их роста и малыми размерами. Они росли столь быстро, что дефекты просто не успевали возникнуть. Стоило увеличить размеры усов, дефекты кристаллической решетки появлялись, и прочность резко падала. Было обнаружено, что усы даже после рождения могут быстро «портиться» за счет появления примесей в результате окисления их поверхности. Поэтому надо было принимать специальные меры для хранения выращенных усов. Поскольку усы состояли из отдельных нитей, их назвали также нитевидными кристаллами.
Сегодня существует более 100 способов получения монокристаллов. Наиболее совершенными свойствами обладают нитевидные кристаллы, полученные осаждением из газовой фазы. В трубчатую печь помещают алундовую или кварцевую лодочку с хлористой солью металла. При нагреве происходит возгонка соли. Через печь пропускают водород, который восстанавливает соль до металла. Нитевидные кристаллы появляются на стенках лодочки в виде пушистых наростов – усов. Рост нитевидных кристаллов связан с влажностью, чистотой и количеством соли, стабильностью режима восстановления. Определяющими всегда являются температура и скорость восстановления.
В Советском Союзе в 60-х годах Е. М. Савицкий с сотрудниками получил нитевидные кристаллы почти всех тугоплавких металлов. В настоящее время получают нитевидные кристаллы чистых металлов размером 2–10 мм и толщиной от 0,5 до 2,0 мк, практически лишенные дефектов кристаллической решетки. Эти монокристаллы обладают прочностью, близкой к теоретической. Так, например, предел прочности монокристаллов железа составляет 13 000 МПа, меди – 3000 и цинка 2000 МПа, в то время как техническое железо имеет предел прочности 300 МПа, медь – 250 и цинк 180 МПа.
Исследование поверхности нитевидных кристаллов показало, что она не имеет микроскопических трещин, остается «атомно гладкой». Кристаллическая решетка усов характеризуется почти полным отсутствием дислокации. Таким образом, отсутствие в металле примесей при определенных условиях обеспечивает бездефектную структуру его кристаллов. Бездефектная структура чистых («однородных») металлов является надежным способом повышения их прочности.
Вот они, современные булаты
С современной точки зрения булат – композиционный материал, состоящий из двух металлических фаз. Одна из фаз – мягкое железо, другая – высокоуглеродистая сталь. Таким образом, булат представляет собой объемное сочетание разнородных компонентов, один из которых пластичный, а другой обладает высокой прочностью.
В «Основных направлениях экономического и социального развития СССР на 1981–1985 годы и на период до 1990 года» предусматривается дальнейшее повышение качества продукции на основе всемерного использования достижений научно-технического прогресса. Большое внимание при этом обращается на улучшение качества металлов и сплавов с целью обеспечения их высокой прочности, износостойкости, долговечности, коррозиестойкости. Одним из перспективных путей решения этих задач является создание композиционных материалов.
Очень близки по своему строению к булату так называемые естественные композиционные стали, представляющие собой композиции из мягкой матрицы и распределенных в ней высокопрочных волокон второй фазы, значительно более прочной, чем сама матрица.
Подобно тому как в древности люди присматривались к волокнам древесины, чтобы научиться ковкой повышать прочность железа, в наше время – стремятся заимствовать у природы строение и свойства композиционных материалов. Только делается это на высокой научной основе. Известно, что древесина представляет собой композицию целлюлозы с лигнином. Волокна целлюлозы обладают высокой прочностью на разрыв, но низкой на срез. Лигнин связывает волокна в единое целое и сообщает древесине жесткость. На этом принципе и были созданы новые материалы, представляющие собой композицию из мягкой основы (матрицы) и высокопрочных волокон или пластин, выполняющих роль ее арматуры. В таком материале, так же как и в древесине, основную часть нагрузки воспринимают волокна, а матрица служит средой, передающей нагрузку от одного волокна к другому.
Во всяком компактном материале, например в легированных сталях и сплавах, нагрузку воспринимает материал в целом. Поэтому возникшая трещина быстро распространяется и приводит к хрупкому разрушению металла. Чем выше прочность материала, тем меньше его сопротивление хрупкому разрушению. В композиционном материале трещина, возникшая при разрушении прочного волокна или пластины, гасится мягкой матрицей. Поэтому наряду с высокой прочностью такие материалы обладают и высокой вязкостью, и в этом отношении они также как бы продолжают традиционные свойства булатной стали.
Любая доэвтектоидная сталь после закалки по определенному режиму может иметь феррито-мартенситную структуру. Но это еще не композиционный материал. Как же превратить его в композит? Для этого необходимо, чтобы участки мартенсита были слоистыми, то есть имели соизмеримые размеры в двух направлениях и намного меньший размер в третьем. Такую структуру получают при помощи термомеханической обработки.
Для получения композиций с направленной феррито-мартенситной структурой доэвтектоидную сталь прокатывают при температуре, обеспечивающей ей двухфазную структуру – аустенит и феррит (рис. 2). Непосредственно после прокатки сталь закаливают, и слои аустенита превращаются в мартенсит, а феррит остается в прежнем состоянии. Это и приводит к образованию композиции из слоистого мартенсита, расположенного в мягкой ферритной матрице.
Так же как и булатная структура, структура композиционной феррито-мартенситной стали обеспечивает увеличение ее прочности более чем в 2 раза по сравнению с обычной сталью такого же состава. Так же как и в булате, прочные, твердые слои мартенсита соединены с мягкой пластичной ферритной матрицей, и в связи с этим композиционная сталь имеет более высокую вязкость и смещение порога хрупкого разрушения к более низким температурам.
Знаменательно, что идеи Д. К. Чернова о возможности получения булатной структуры, используя структуру эвтектоидного или эвтектического типа, практически полностью воспроизведены в так называемых эвтектических и эвтектоидных композициях. Получение этих композиций связано с использованием различных фазовых превращений в сплавах, в частности с кристаллизацией жидкости (эвтектическое превращение) или с превращением в твердом состоянии (эвтектоидный распад). В результате эвтектического превращения в системе образуются две или более твердые фазы, выпадаемые одновременно в виде механической смеси, называемой эвтектикой.
Одним из наиболее изученных и перспективных способов создания композиционных сплавов такого типа является направленная кристаллизация. Этот способ обеспечивает достаточно резко выраженную физически неоднородную структуру со строгой ориентацией фаз в пространстве. В эвтектических композициях реализуется идеальная структура – высокопрочные нитевидные кристаллы армируют пластичную и вязкую матрицу.
Не может быть сомнений в том, что, если бы П. П. Аносову предъявили такую структуру, он ее тотчас же назвал бы булатом…