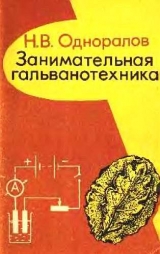
Текст книги "Занимательная гальванотехника: Пособие для учащихся"
Автор книги: Николай Одноралов
Жанры:
Химия
,сообщить о нарушении
Текущая страница: 5 (всего у книги 5 страниц)
Примером такого раствора может служить следующий.
В 1 л воды растворено цитрата натрия 70 г, хлорида аммония 50 г, хлорида или сульфида никеля 25 г, гипофосфата натрия 10 г. На 1 л этого раствора вводится 150 мл 25-процентного раствора аммиака, который следует периодически, в течение процесса никелирования, добавлять для сохранения постоянного значения концентрации водородных ионов (pH 10). Температура раствора 82–87 °C. В процессе никелирования изделий из алюминия и его сплавов следует вводить 0,3 г сульфата аммония на 1 л раствора.
Скорость осаждения никеля в таком растворе составляет 10–12 мкм/ч. Можно взять раствор, содержащий в 30 г сульфата никеля 10 г гипофосфата натрия при (pH 5). Процесс химического никелирования можно вести или до полной выработки раствора и его замены, или с регулярным введением в раствор израсходованных компонентов. Хорошее качество покрытия и прочность его сцепления с основным металлом во многом зависят от тщательности предварительной подготовки поверхности изделий.
Перед никелированием изделия из алюминия и его сплавов вначале промывают в чистом бензине, подвергают 3—5-минутному травлению в 1—2-процентном растворе гидроксида натрия при 60–70 °C, затем осветляют в азотной кислоте (300–400 г кислоты на 1 л воды) в течение 2–3 мин при комнатной температуре, а затем промывают в воде. После промывки изделия немедленно погружают в раствор для никелирования.
При никелировании латунных и бронзовых изделий подготовка включает тщательное обезжиривание в чистом бензине, промывку в холодной воде и травление в смеси серной и азотной кислот. Для этого составляют раствор из 72 мл азотной кислоты, 4 мл хлорводородной кислоты, 544 мл воды и 380 мл серной кислоты (вливается в раствор последней, при этом тонкой струей).
Изделия лучше всего погружать в раствор для никелирования на хлорвиниловой ленте или трубке; никелирование производят в стеклянной или эмалированной посуде. Подогрев ванны для никелирования можно осуществлять на водяной бане. Никелированные детали промывают в воде и сушат в древесных опилках нехвойных пород.
ДЕКОРАТИВНАЯ ОТДЕЛКА ИЗДЕЛИЯ «КРИСТАЛЛИТОМ»
Этот способ декоративной отделки является комбинированным – гальваническим и термическим.
Получение «кристаллита» основано на декоративном эффекте, получаемом при выявлении кристаллов олова при тонком его нанесении на поверхность изделий.
Предварительно изделия покрываются оловом гальваническим способом.
Для этого готовят электролит следующего состава (г/л):
Сульфат олова… 54
Серная кислота (ρ —1,84)… 50—80
Сульфат натрия… 50
Фенол или крезол… 2—10
Столярный клей… 2—3
Температура раствора 15–20 °C. Плотность тока 2 А/дм2. Анод оловянный. После нанесения пленки олова изделия промывают в холодной проточной воде, а затем в горячей и высушивают.
Затем изделия помещают в электропечь для получения кристаллов олова. Температура нагрева изделий 300–350 °C, время выдержки изделий в печи 15–20 мин.
Медленное остывание изделий после нагрева дает более крупные размеры кристаллов, быстрое – более мелкие. Резкое охлаждение отдельных частей поверхности изделия, например дутье через трубку на поверхность расплавленной пленки олова, дает красивые искусственные центры кристаллов, напоминающие причудливые цветы, звезды и т. п. орнаменты.
После термической обработки оловянной пленки производят выявление кристаллов, что осуществляют в этом же электролите, завешивая изделия на 5—10 мин на анод. При этом плотность тока должна быть 0,2–0,5 А/дм2. Повышенная плотность тока может вызвать «затухание» игры кристаллов. Изделия с проявленным кристаллическим рисунком тщательно промывают в холодной, а затем в горячей воде, высушивают и покрывают цветным прозрачным нитролаком.
ДЕКОРАТИВНАЯ ОТДЕЛКА ИЗДЕЛИЙ, ИМИТИРУЮЩАЯ АГАТ
Перед декоративным покрытием изделие должно быть отполировано до блеска. После этого изделие тщательно обезжиривают и обрабатывают в электролите следующего состава (г/л):
Оксид хрома (VI)… 30-400
Ацетат бария… 5-10
Ацетат цинка… 2-5
Ацетат кальция… 4-8
По существу указанный процесс является разновидностью хромирования.
Хромирование в указанном электролите происходит при температуре 22–40 °C, плотностью тока – 30—100 А/дм2.
Указанная плотность тока является очень высокой для тех источников тока, которыми располагают школы, а тем более в домашних условиях, поэтому этим способом можно отделывать изделия небольших размеров – в 2–3 см2.
Продолжительность обработки 10–20 мин. После хромирования поверхность изделия имеет темно-синий цвет с рисунком в виде волнообразно расположенных серо-голубых полос, напоминающих текстуру агата, при этом общий фон покрытия подернут легкой матовой дымкой. Для получения блестящей поверхности изделия покрывают тонким слоем прозрачного лака.
ДЕКОРАТИВНАЯ ОТДЕЛКА ИЗДЕЛИЙ ИЗ АЛЮМИНИЯ И ЕГО СПЛАВОВ
Декоративная отделка изделий из алюминия и его сплавов в настоящее время очень распространена.
Этим способом отделывают разнообразные галантерейные изделия, броши, серьги, браслеты, а также хлебницы, коробки различного назначения: для папирос, табака, ниток, корпуса от часов и т. п. Наиболее распространенным видом отделки является их окраска, имитирующая золото. Но часто изделия окрашивают и в другие, самые разнообразные цвета.
Этот вид обработки алюминия часто называют анодированием, потому что изделия завешивают в электрическую ванну не на катод, как обычно, а на анод. На катод завешивают свинцовую пластинку. Наиболее хорошо обрабатываются этим способом изделия из чистого алюминия, но можно качественно обработать и сплавы алюминия, которые после обработки лучше окрашиваются в темные цвета – черный, синий, коричневый и т. п.
Для обработки алюминия и его сплавов обычно производят три основные операции: вначале подготовленные, как обычно, изделия полируют химическим или электрохимическим способом, затем анодируют, после чего окрашивают в анилиновых красителях, применяемых для окраски шерстяных материй. При анодировании следует придерживаться следующей технологической схемы.
Обезжиривание. Для обезжиривания изделий применяется следующий состав (в г/л):
Гидроксид натрия… 10—15
Тринатрийфосфат… 20—30
Карбонат натрия… 20—25
Температура состава 80–90 °C. Изделия выдерживают в ванне 1–2 мин. Ванна для этого процесса может быть изготовлена из железа.
Для удаления щелочи изделия после обезжиривания промываются в горячей воде (70–80 °C), затем в холодной проточной.
При обезжиривании изделий возможно растравление их поверхности. Причиной этого могут быть передержка изделий в ванне, перегрев ванны или перенасыщение обезжиривающего состава щелочью. Для устранения дефекта следует соответственно сократить время выдержки изделий в ванне, понизить температуру ванны или ослабить концентрацию щелочи в составе.
Осветление. Обезжиренные и промытые изделия обычно имеют матово-серый цвет, для удаления этого налета изделия осветляют, выдерживая в 50-процентном растворе технической азотной кислоты (ρ – 1,32) в стеклянном или керамическом сосуде в течение 1–2 мин при температуре 18–20 °C.
Для удаления азотной кислоты с поверхности изделия промывают в холодной проточной воде. Обе операции-обезжиривание и осветление – следует производить в вытяжном шкафу, так как во время обработки выделяются вредные пары.
Полирование. Предварительно изделия, имеющие на поверхности грубую шероховатость, забоины, царапины и т. п. дефекты, следует отшлифовать мелкой шкуркой, а затем отшлифовывать электрохимическим или химическим способом. При отсутствии указанных дефектов изделия полируют электрохимическим или химическим способом.
Приведем химический способ, как наиболее простой.
Готовят смесь кислот следующего состава (в г):
Ортофосфорная кислота (ρ – 1,71)… 300 г
Серная кислота (ρ – 1,84)… 600 г
Азотная кислота (ρ – 1,50)… 70—100 г
Температура смеси 115–120 °C. Ванны для химической полировки изготовляют из свинца или из нержавеющей стали. Полирование следует вести в вытяжном шкафу или под интенсивной вытяжкой. Время выдержки изделий в ванне 1–2 мин. После химического полирования изделия промывают горячей, а затем холодной проточной водой и завешивают в ванну анодирования.
Анодирование (оксидирование) производят, как указывалось, на аноде. Предварительно к изделию плотно прикрепляют алюминиевую проволоку для электрического контакта и загружают его в ванну. Ванна анодирования состоит из 18—20-процентного раствора серной кислоты. Плотность свежеприготовленного электролита при температуре 20 °C—1,13—1,14. Напряжение тока должно быть не ниже 7–8 В. Плотность тока 0,8–1,2 А/дм2.
Время анодирования 15–20 мин. Температура раствора не должна быть выше 25 °C. Расстояние между изделием и завешенной на катод свинцовой пластинкой 150–200 мм. Корректируют электролит добавлением соответствующего количества серной кислоты до получения указанной выше плотности электролита. При составлении ванны и корректировании следует осторожно обращаться с серной кислотой. Серную кислоту можно вливать только в воду, а не наоборот. При этом вливать серную кислоту нужно осторожно тонкой струей. Для поддержания температуры электролита не выше 25 °C ванну с электролитом можно поместить в бак с водой для охлаждения.
Для анодирования применяется пластмассовая ванна, например из винипласта, свинцовая или железная, прочно покрытая изнутри эмалью. После анодирования изделия вынимают из электролита и, тщательно промыв в холодной воде, окрашивают в заданный цвет.
Окрашивание оксидированных изделий. Качество окрашивания оксидированных изделий во многом зависит от качества красителей и режима окрашивания, температуры, концентрации раствора и цветов красителей.
Окрашивание анодированных – оксидированных изделий происходит за счет адсорбции красителей оксидной пленкой. Оксидная пленка, полученная анодированием, отличается микропористостью, в которую в процессе окрашивания проникает краситель и задерживается в ней. Оксидная пленка лучше всего поглощает красящие вещества непосредственно после оксидирования. Для окрашивания изделий берут растворы красителей, концентрация которых колеблется от 0,5 до 3 %.
Для окраски в желтый, коричневый, а также в светло-зеленый и светло-синий цвета вполне достаточна концентрация красителя 0,5–1 %. Для окраски в черный цвет применяется более концентрированный раствор 2—3-процентный.
Для приготовления красящего раствора рекомендуется смешать краситель с небольшим количеством дистиллированной воды до образования кашицы, растереть в фарфоровой ступке и затем при перемешивании добавить к ней необходимое количество воды. Рекомендуется нагреть в течение короткого времени раствор до кипения, чтобы краситель полностью растворился. В случае образования пены ее следует снять.
Для приготовления красящего раствора можно применять мягкую или умягченную воду, так как содержащиеся в жесткой воде кальциевые и магниевые соли могут образовать с некоторыми красителями нерастворимые в воде соединения. При добавлении в раствор воды с большей жесткостью может произойти выпадение красителя из раствора в осадок. Если в процессе крашения образуется осадок, то красящий раствор необходимо профильтровать через хлопчатобумажную ткань. Изделия погружаются в краситель, нагретый до 50–60 °C.
В зависимости от выдержки изделий в красителе можно получить более светлые или темные тона.
Уплотнение окрашенной оксидной пленки. Для уплотнения оксидной пленки и удержания в ней красителя изделия кладут в горячую воду (80–90 °C) и выдерживают в ней 25–30 мин. В процессе уплотнения поры пленки сжимаются и удерживают краситель.
Общее замечание. В процессе обработки к изделиям при обезжиривании, оксидировании и крашении прикасаться руками без перчаток не следует, так как в местах прикосновения могут образоваться пятна.
ПОЛУЧЕНИЕ «ЭМАЛИ» НА АЛЮМИНИИ И ЕГО СПЛАВАХ
В последнее время был разработан новый способ защитно-декоративной отделки алюминия. Этот способ известен под названием «эматалирование». Сущность его заключается в электрохимическом получении непрозрачных оксидных пленок на алюминии и его сплавах в растворе, состоящем из щавелевой, борной и лимонной кислот и оксалата титан-калия.
Эматаль-пленки относятся к непрозрачным, молочно-эмалевидным декоративным покрытиям. Они могут быть блестящими или матовыми, бесцветными или окрашенными. Эматаль-пленки отличаются хорошей износостойкостью и коррозийной устойчивостью в атмосферных условиях.
Повышенная твердость и износостойкость приближают эматаль-пленки по свойствам к хромовым покрытиям. По виду эматалированные изделия напоминают эмалированные или пластмассовые, но имеют перед ними ряд преимуществ: лучшее сцепление, меньшую толщину слоя, они не трескаются и не откалываются при ударе, сжатии и т. п.
Эматалирование, кроме получения пленок с улучшенными свойствами, имеет и другие положительные стороны. Так, предъявляются пониженные требования к чистоте обрабатываемого алюминия, к качеству полировки поверхности. Вместе с тем не надо забывать, что не обязательно применять электрополирование (как, например, при широко распространенном процессе отделки алюминия под цвет золота).
Эматаль-пленки, как и другие анодные пленки, окрашиваются в водных растворах органических красителей. Благодаря светло-серой окраске пленки цвет ее при крашении смягчается и может иметь все нюансы от нежного тона до глубоких сочных тонов.
Эматаль-пленки из вышеуказанных электролитов можно получить различной толщины в пределах 8…13 мм в зависимости от времени выдержки в ванне и других факторов. Пленки указанной толщины получаются обычно в течение 25–30 мин. Важным фактором для получения хороших непрозрачных пленок является правильный выбор алюминиевых сплавов. Литейные сплавы, которые могут дать качественную эматаль-пленку, должны быть следующего состава (%):
Меди… менее 2
Цинка >> 8
Магния >> 8
Никеля… менее 1
Железа >> 1
Марганца >> 1
Из листового алюминия эматалированию подвергаются алюминий марок АД1, АМц, АМгЗ, АВ, АВП и некоторые марки медистого алюминия, если содержание меди в нем не превышает 2 %. В литейных сплавах, применяемых для эматалирования, содержание примесей не должно превышать: меди – 2 %, цинка – 8 %, магния – 8 %, никеля – 1 %, железа – 1 %, марганца – 1 %.
Наиболее пригодным для эматалирования является литейный сплав: алюминий – цинк – магний (цинка 5 %, магния 1,5–2 %).
Оксидные пленки, полученные эматалированием на разных деформируемых сплавах, могут иметь различные оттенки от светло-серого до темно-серого.
Для придания эматалированным изделиям необходимой декоративности рекомендуется их слегка полировать. С этой целью может быть использована паста на основе оксида алюминия и венской извести следующего состава (в процентах по массе):
Пасты на основе оксида хрома не рекомендуются, так как на эматалированной поверхности, даже при тщательном обезжиривании, остаются зеленые пятна.
Для эматалирования рекомендуется хромовоборный электролит. Процесс эматалирования в хромовоборном электролите состоит из следующих операций:
1. Полировка. 2. Обезжиривание в органических растворителях. 3. Протирка ветошью. 4. Монтаж на подвески. 5. Обезжиривание химическое. 6. Промывка в горячей воде. 7. Промывка в холодной проточной воде. 8. Осветление. 9. Промывка в холодной проточной воде. 10. Эматалирование. 11. Промывка в холодной проточной воде. 12. Обработка в растворе азотной кислоты. 13. Промывка в холодной проточной воде. 14. Промывка в дистиллированной воде. 15. Крашение. 16. Промывка в холодной проточной воде. 17. Уплотнение. 18. Демонтаж с подвесок. 19. Сушка. 20. Глянцовка на чистом бязевом круге. 21. Контроль.
ПРАКТИЧЕСКИЕ УКАЗАНИЯ ПО ВЕДЕНИЮ ПРОЦЕССА ЭМАТАЛИРОВАНИЯ В ХРОМОВОБОРНОМ ЭЛЕКТРОЛИТЕ
Обезжиривание детален проводят в растворе следующего состава (в г/л):
Тринатрийфосфат… 50
Гидроксид натрия… 10
Силикат натрия… 5
Температура раствора 60–70 °C, продолжительность обработки 2–3 мин.
Обезжиренные и промытые детали осветляются погружением в 30-процентный раствор азотной кислоты при 18–20 °C, затем промываются и эматалируются.
Для эматалирования применяется электролит следующего состава (в г/л):
Оксид хрома (VI)… 30
Ортоборная кислота… 2
Электролит готовится на водопроводной воде.
Процесс ведется следующим образом.
Изделия завешиваются на анодную штангу. Затем включается ток. В течение 5 мин напряжение плавно повышают от 0 до 4 В и поддерживают его 30 мин. Плотность тока при этом должна быть равна 0,4–0,5 А/дм2. По истечении 30 мин напряжение повышают до 80 В, при этом плотность тока устанавливается и до конца эматалирования остается постоянной. Общая продолжительность процесса 60 мин. Температура электролита не должна превышать 50 °C, перегрев ведет к ухудшению качества пленки.
Катоды применяются из нержавеющей стали. Соотношение анодной и катодной поверхностей 2: 1, 3: 1. В процессе работы электролит испаряется, количество его необходимо доводить до первоначального уровня добавлением горячей воды.
Корректирование ведется добавлением оксида хрома (VI) из расчета 10 г на 1 м2 обработанной поверхности.
После эматалирования изделия тщательно промывают в холодной проточной воде, обрабатывают в течение 1–2 мин в 30-процентном растворе азотной кислоты, снова тщательно промывают, сначала в проточной, а затем в дистиллированной воде и окрашивают в водных растворах органических красителей с режимом, указанным в таблице 8.

После окрашивания детали промывают и уплотняют кипячением в течение 30 мин в дистиллированной воде. Исправление брака при крашении сводится к обработке изделий в 50-процентном растворе азотной кислоты, тщательной промывке в холодной проточной воде, затем в дистиллированной воде, после чего изделия опять могут быть окрашены в нужный цвет.
Удаление эматаль-пленки с подвесок и бракованных изделий проводится в 30-процентном растворе гидроксида натрия при температуре раствора 60–70 °C.
Улучшение внешнего вида покрытия эматалированных изделий после уплотнения и сушки достигается глянцовкой на чистом бязевом круге без применения полирующих паст.
ДЕКОРАТИВНАЯ ОТДЕЛКА ИЗДЕЛИЙ ИЗ АЛЮМИНИЯ, ИМИТИРУЮЩАЯ ГРАНИТ
Разнообразные возможности декоративной отделки алюминия оксидированием (анодированием), о котором мы говорили выше, в сочетании с предварительной обработкой листового алюминия, имитирующей гранит, дают очень интересный декоративный эффект (рис. 20).
Для получения на листовом алюминии текстуры, напоминающей гранит, листовой алюминий в виде полос (толщиной 0,3–0,5 мм) предварительно растягивается – удлиняется на незначительную величину, исчисляемую миллиметрами на метр металла, а затем нагревается и по остывании протравливается в смеси кислот. Такая обработка выявляет на поверхности металла кристаллы, образующиеся вследствие рекристаллизации алюминия. При этом размеры кристаллов, получаемых в процессе рекристаллизации алюминия, могут быть получены от 5…20 мм в зависимости от величины растяжения алюминия. Для растяжения концы полосы алюминия зажимают в двух тисках и затем нажимают деревянной скалкой на среднюю часть полосы, проводя скалку взад и вперед. В зависимости от силы нажима алюминий постепенно будет растягиваться. После растягивания алюминиевую полосу помещают в муфельную печь и нагревают до температуры 550 °C в течение 20–30 мин. Указанная термическая обработка вызывает рекристаллизацию растянутого алюминия.
Но для выявления текстуры кристаллов, которые по форме похожи на зерна гранита, алюминий требуется обработать в травильном растворе. Травление рекристаллизованного алюминия производят в смеси кислот, которая состоит из 1/3 хлорводородной кислоты, 1/3 азотной кислоты и 1/3 воды. Травление следует производить в резиновых перчатках, пользуясь при этом щипцами.
По выявлении кристаллов на алюминии изделие тщательно промывается в воде, после чего алюминий может быть анодирован и окрашен в желаемый цвет.
НАНЕСЕНИЕ ИЗОБРАЖЕНИЙ НА ИЗДЕЛИЯ ФОТОТРАВЛЕНИЕМ
Во многих случаях металлические изделия могут декорироваться нанесением на них изображений в виде рисунков: портретов, пейзажей, орнаментов, надписей и т. п. Для этого может быть успешно использован способ фотографирования.
Для этого способа можно применять различные металлы, но наиболее простым в обработке является алюминий и его сплавы. Сущность фотографирования состоит в том, что металлическую пластину или изделие покрывают светочувствительной эмульсией и высушивают в темноте; затем накладывают фотонегатив – обычно пленочный – и экспонируют, применяя достаточно мощный источник тока.
Под светлыми участками негатива эмульсия закрепляется и становится сравнительно водостойкой, а под темными участками эмульсия остается почти в неизменном виде и при проявлении в воде полностью удаляется. Оставшемуся на металле эмульсионному слою придают химическую стойкость путем химической и термической обработки. Затем пластинку или изделие подвергают химическому или электрохимическому травлению.
Негатив получают контактным печатанием на репродукционной штриховой фотопленке ФТ-30 с оригинала, вычерченного или нарисованного черной тушью на кальке. При фотографировании можно также использовать непосредственно оригинал, выполненный на кальке, однако стойкость такого оригинала и качество фототравления при этом ниже, чем при использовании пленочного негатива.
При создании изображения на пластинах из алюминия или его сплавов пластины заготовляют по размерам фотографируемого изображения с припуском 5…10 мм по периметру. После чего пластина шлифуется и полируется на войлочном круге и обезжиривается уайт-спиритом, а затем венской известью. Хорошо обезжиренная поверхность пластин должна равномерно смачиваться водой.
Для лучшего сцепления эмульсии с металлом пластина подвергается легкому протравливанию в растворе, содержащем вещества (в г/л):
Тринатрийфосфат… 50
Карбонат натрия… 30
Силикат натрия… 5
Температура раствора 50–60 °C, продолжительность обработки 5–6 с. Подготовленную пластину затем устанавливают на центрифугу, скорость которой должна быть в пределах 70… 80 об/мин.
В центрифуге поверхность пластины окончательно промывают водой, затем наносят (поливом) небольшое количество эмульсии, которая должна быть равномерно распределена на поверхности пластины. После, чего эмульсионный слой сушится до исчезновения «отлипа».
Для фотографирования применяется эмульсия следующего состава:
Клей мездровый… 150
Аммиак 25-процентный… 50 г
Дихромат аммония… 30 г
Оксид хрома (VI)… 5 г
Дихромат калия… 3 г
Спирт этиловый… 35 мл
Вода… 1 л
Плиточный мездровый клей предварительно замачивают водой. Варят эмульсию на водяной бане при легком помешивании во избежание захватывания воздуха.
Эмульсии дают отстояться, затем фильтруют ее через вату, обернутую марлей, и хранят в темном прохладном месте. После центрифугирования и сушки эмульсионного слоя пластины накладывают на негатив светочувствительной пленки вниз и в таком виде, следя, чтобы не было взаимного смещения пластин, укладывают их на контактное стекло рамки стола-рефлектора. Пластину с негативом плотно прижимают к стеклу. Затем включают источник света (четыре лампы, по 1000 вт каждая, расположенные в нижней части стола-рефлектора, под контактным стеклом). Одновременно включают вентилятор для охлаждения контактного стекла.
В зависимости от светочувствительности эмульсии копирование продолжается 5–8 мин. Затем пластину проявляют в холодной воде, под душем.
Для увеличения контрастности изображения, а также проверки качества и полноты проявления пластины смачивают водным раствором анилинового красителя; в случае необходимости проявление продолжают. Если проявление происходит медленно и получается «вуаль», можно на короткое время погрузить пластину в воду, подогретую до 30–40 °C.
Проявленную пластину обрабатывают в течение 2–3 мин в растворе, содержащем в 1 л воды 40 г хромовокалиевых квасцов и 100 г дихромата аммония.
После дубления, промывки и сушки пластины подвергают равномерному обжигу при температуре 300–350 °C до перехода эмульсионной пленки в коричневый цвет. При этом эмульсионная пленка окончательно закрепляется, приобретая необходимую химическую стойкость.
Продолжительность обжига 3–4 мин. Затем пластины подвергают травлению в водном растворе состава:
Сульфат меди… 200 г/л
Хлорат натрия… 125 г/л
Хлорводородная кислота… 10 мл
Температура раствора 20–25 °C. Для травления применяют фарфоровые ванны или ванны из пластмассы. Для защиты обратной стороны пластины от травления ее покрывают цапом – лаком. Промытую и просушенную пластину покрывают бесцветным лаком.
ИЗГОТОВЛЕНИЕ МАТРИЦ С ЦЕРОФАНОВЫХ (ВОСКОВЫХ) МОДЕЛЕЙ
Для изготовления художественных изображений на керамике, фарфоре или на органическом стекле применяется метод церофании, заключающийся в изготовлении прозрачных восковых изображений, отличающихся особо низким рельефом; при этом лепят, рассматривая изображение на просвет. Для лепки церопластических моделей применяют: специальную твердую просвечивающую восковую композицию, например следующего состава (в %):
Канифоль… 8
Скипидар… 6
Стеарин… 30
Воск пчелиный… 51
Тальк… 5
Восковую композицию разогревают и наливают равномерным слоем толщиной 2–3 мм на стекло. Для облегчения предварительно прокалыванием с кальки переносят на воск контур требуемого рисунка. В зависимости от толщины слоя восковая композиция пропускает различное количество света, что и выявляет тональные переходы изображения.
Такой способ также дает возможность получить обычным приемом гальванопластики медную негативную форму.
Полученную форму можно использовать различными приемами: в ней можно отформовать органическое стекло, с нее можно получить гипсовую форму для керамики, и, наконец, она может служить непосредственно художественным изделием после нанесения на нее прозрачной эмали.
При использовании формы для изготовления репродукции из органического стекла медную форму наращивают до толщины 2–3 мм в наиболее толстых местах, затем с нее отформовывают под прессом из разогретого листового молочного органического стекла позитивное изображение, которое на просвет будет давать такой же художественный эффект, как и оригинал, изготовленный на воске: более тонкие места пластической массы будут пропускать больше света, а более толстые – меньше, чем и выявится изображение. Такой же живописный эффект получается и на отпрессованном фарфоре.
При использовании формы для изготовления изображений на керамике с нее, как с модели, снимают гипсовую форму, служащую для фарфорового литья. Отлитую или отформованную керамическую массу после сушки и обжига по всей плоскости рельефа заливают потечной глазурью и обжигают. Залитая, обожженная глазурь также тонально воспроизводит церопластическое изображение за счет различной толщины глазури на поверхности рельефа. Форму можно использовать и непосредственно как модель для покрытия прозрачной цветной эмалью, дающей аналогичный живописный эффект, как и на керамике. Перед нанесением эмали матрица должна быть предварительно прокалена при 750–800 °C для удаления поглощенного металлом при наращивании водорода, наличие которого может вызвать вспучивание, пузырение эмали.
* * *
