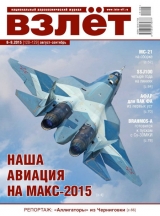
Текст книги "Взлёт, 2015 № 08-09(128-129)"
Автор книги: Автор Неизвестен
Жанры:
Транспорт и авиация
,сообщить о нарушении
Текущая страница: 6 (всего у книги 12 страниц)
Новый Ил-76МД-90А назван именем Виктора Ливанова

15 августа 2015 г. в Ульяновске прошла торжественная церемония присвоения имени Виктора Ливанова новому серийному военно-транспортному самолету Ил-76МД-90А, изготовленному на АО «Авиастар-СП». Первый полет этой машины с серийным №0105 состоялся в Ульяновске накануне, 14 августа. Виктор Ливанов (1943-2014) с 1988 по 2014 гг. руководил Авиационным комплексом им. С.В. Ильюшина, с 2007 г. являясь его генеральным директором, а затем и Генеральным конструктором. Именно по его инициативе и под его руководством была реализована программа разработки глубоко модернизированного самолета Ил-76МД-90А и запуска его в производство на ульяновском заводе «Авиастар-СП».
Генеральный директор ОАО «Ил» Сергей Вельможкин отметил на церемонии, что инициатива присвоения самолету почетного имени является достойной оценкой труда Виктора Владимировича Ливанова. «Когда этот проект начинал свою реализацию, и мы возобновляли производство самолета Ил-76, никто не верил, что это возможно сделать. Но благодаря нашим совместным усилиям, благодаря труду заводчан-ульяновцев, мы смогли это сделать. Вдвойне приятно, что этому самолету присвоено имя нашего руководителя Виктора Владимировича Ливанова. Те люди, которые непосредственно работали на этой машине, знают, сколько своего труда, времени, сколько души этот человек вложил во всю эту программу. Поэтому присвоение этого имени является достойной оценкой труда Виктора Ливанова».
Генеральный директор АО «Авиастар-СП» Сергей Дементьев, в свою очередь, отметил роль Виктора Ливанова в освоении серийного производства самолета Ил-76МД-90А. «Виктор Владимирович был человеком незаурядным и выдающимся, он внес неоценимый вклад в развитие отечественного самолетостроения, повышение обороноспособности нашей страны. Во многом благодаря этому человеку ульяновское предприятие, где освоено серийное производство самолета Ил-76МД-90А, обрело свое третье рождение».
Присутствовавший на мероприятии командующий Военнотранспортной авиацией России генерал-лейтенант Владимир Бенедиктов сообщил, что после завершения программы испытаний Ил-76МД-90А, носящий имя Виктора Ливанова, поступит в Центр боевой подготовки и переучивания летного состава Военно-транспортной авиации в Иваново, став первым самолетом такого типа в ВТА. «Летный, инженерно-технический и преподавательский состав Центра уже прошел переучивание на новый тип самолета и готов начать переподготовку на него строевых летчиков Военно-транспортной авиации России», – сообщил генерал Бенедиктов.

Напомним, первые два серийных Ил-76МД-90А (№0103 и 0104), изготовленные на «Авиастаре» в прошлом году, переданы в ноябре 2014 и апреле 2015 гг. на ТАНТК им. Г.М. Бериева, где на их базе будут созданы новые авиационные комплексы специального назначения. Первый же летный образец Ил-76МД-90А (№0102), впервые взлетевший в Ульяновске в сентябре 2012 г. и прошедший в 2013 г. первый этап Государственных совместных испытаний, в настоящее время находится на доработках на заводе, в рамках которых оснащается новыми комплексами связи, обороны и другим оборудованием в соответствии с уточненным техническим заданием заказчика. Как сообщил Сергей Дементьев, после завершения этих работ до конца нынешнего года он должен поступить на второй этап ГСИ, прохождение которого позволит официально принять Ил-76МД-90А на вооружение Военно-транспортной авиации России.
В производстве окончательной сборки АО «Авиастар-СП» сейчас находится следующий серийный Ил-76МД-90А (№0108). В ближайшее время он должен быть передан на наземные, а затем и летные испытания, после чего также будет сдан до конца года заказчику и поступит в ивановский Центр подготовки авиационного персонала ВТА.
Следующий на очереди – самолет №0109, на котором уже завершены работы по стыковке основных агрегатов планера. Одновременно на заводе идет изготовление и сборка агрегатов первого летного образца перспективного самолета– заправщика Ил-78М-90А. Как сообщил генеральный директор «Авиастара» Сергей Дементьев, эту машину планируется выкатить с окончательной сборки к лету следующего года, а первый полет ее может состояться в августе 2016 г. На предприятии ведутся работы по изготовлению деталей и агрегатов следующих серийных Ил-76МД-90А в рамках полученного в октябре 2012 г. заказа Минобороны России на 39 самолетов, проработана организация современной поточной линии сборки, которая позволит повысить темпы изготовления Ил-76МД-90А к концу десятилетия до 18 машин в год. По словам Сергея Дементьева, уже с 2017 г. завод может приступить к экспортным поставкам Ил-76МД-90 – серьезный интерес к ним проявляет ряд стран. А.Ф.
Взлетел модернизированный L-410NG

29 июля 2015 г. с аэродрома чешской компании Aircraft Industries (принадлежит российской Уральской горно-металлургической компании) в г. Куновице поднялся в первый полет прототип модернизированного 19-местного самолета местных воздушных линий L-410NG (регистрационный номер OK-NGA). Пилотировал машину экипаж в составе летчиков-испытателей Петра Яроцкого и Станислава Скленаржа, на борту также находились инженеры по испытаниям Зденек Коничек и Михал Сум. В первом полете экипаж проверил основные летнотехнические характеристики машины, работу двигателей и бортовых систем.
L-410NG представляет собой дальнейшее развитие сегодняшнего серийного L-410UVP-E20. Среди основных его отличий от предыдущей модели – применение интегральных крыльевых топливных баков, благодаря чему емкость топливной системы возросла почти вдвое, а дальность полета – с 1400 до 2600 км (продолжительность полета – с 4,5 до 9 ч), двукратное увеличение объема переднего багажного отсека в сильно удлинившейся носовой части фюзеляжа, выросшая более чем на 20% (с 1710 до 2200 кг) коммерческая нагрузка, более мощная силовая установка и новый комплекс авионики. Максимальная взлетная масса L-410NG возросла, по сравнению с серийным L-410UVP-E20, с 6600 до 7000 кг, крейсерская скорость – с 386 до 420 км/ч.
Самолет оснащается двумя более мощными двигателями H85-200 с воздушными винтами AV725, развивающими взлетную мощность 850 л.с. (ранее на L-410UVP-E20 применялись двигатели M601E-21 и H80 мощностью 750-800 л.с.). Кабина экипажа стала полностью «стеклянной» – в ней используется самое современное оборудование от Garmin.
Завершить сертификацию модернизированной модели знаменитой «элки» в компании планируют к 2017 г., после чего L-410NG должен поступить в серийное производство с планируемым объемом выпуска до 30 машин в год. Среди потенциальных покупателей собственники чешской компании из нашей УГМК рассматривают действующих операторов L-410, которые захотят увеличить свой парк. Назначение машины – местные и региональные перевозки – не изменилось, при этом на коротких расстояниях эксплуатант сможет использовать сегодняшние L-410UVP-E20, а на более дальних – новые L-410NG. АБ.
Памяти Б.Н. Слюсаря

Когда этот номер уже готовился к сдаче в печать, печальная весть пришла из Ростова– на-Дону. 13 августа 2015 г. на 74-м году жизни скончался председатель совета директоров ПАО «Роствертол» Борис Николаевич Слюсарь. С его именем связана вся новейшая история ростовского вертолетного завода, который Б.Н. Слюсарь возглавлял в качестве генерального директора с 2000 по 2014 гг., да и всего отечественного вертолетостроения в целом.
Практически всю свою жизнь Борис Слюсарь посвятил родному «Роствертолу». Придя на завод в 1960 г. слесарем-сборщиком, он последовательно прошел все ступени служебной лестницы – от мастера до заместителя и первого заместителя генерального директора предприятия. В 2000 г., в тяжелейшие для «Роствертола» годы после «лихих 90-х», стал его генеральным директором. Именно в это время под непосредственным руководством Бориса Слюсаря в Ростове происходило, по сути, возрождение завода, который приступил к освоению производства новых боевых вертолетов Ми-28Н, запуску в серию модернизированных Ми-35М, восстановлению серийного выпуска тяжелых Ми-26. В результате, после буквально штучного производства вертолетов в 90-е, «Роствертол» восстановил свой статус мощного серийного предприятия, производящего сегодня по полсотни и более машин в год и являющегося одним из лидеров холдинга «Вертолета России».
Благодаря энергии и организаторскому таланту Б.Н. Слюсаря за последние несколько лет на «Роствертоле» были проведены серьезная структурная реорганизация службы подготовки производства, внедрение новых технологических процессов, обновление станочного парка, оснащение цехов современной компьютерной техникой и новейшим программным обеспечением. За счет этого удалось в кратчайшие сроки запустить в производство новые модификации вертолетов – Ми-28НЭ, Ми-28УБ, Ми-26Т2.
Трудно переоценить роль Б.Н. Слюсаря в заключении ряда крупнейших экспортных контрактов холдинга «Вертолеты России»: Борис Николаевич так умел организовать прием на заводе потенциальных заказчиков – от представителей министерств обороны до руководителей государств – и объяснить им все преимущества выпускаемой «Роствертолом» продукции, что заключение сделок не заставляло себя долго ждать. Яркие примеры тому – подписание в 2012-2013 гг. крупных контрактов на новейшие ростовские вертолеты Ми-28НЭ и Ми-26Т2, чьи экспортные поставки стартовали совсем недавно.
Борис Николаевич всегда был рад гостям на заводе. Касалось это и нас, журналистов. Главному редактору «Взлёта» посчастливилось за последние годы несколько раз побывать на «Роствертоле», и нельзя не отметить тот радушный прием, который оказывал генеральный директор, и ту открытость, которую он проявлял в беседах.
...Б.Н. Слюсарю было всего 73 года. Он любил жизнь, любил людей, был полон надежд и всегда был готов к новым свершениям. Бориса Николаевича будет очень не хватать всем нам.
Андрей ФОМИН
МС-21 обретает плоть

Важнейшим событием нынешнего года в гражданском авиастроении России должно стать завершение сборки первого летного образца перспективного ближне-среднемагистрального пассажирского самолета МС-21, создание которого ведет корпорация «Иркут». Нынешним летом на Иркутском авиационном заводе полным ходом шла стыковка фюзеляжа первого МС-21-300, и к моменту проведения авиасалона МАКС-2015, как ожидается, эти работы будут завершены. Самолет строится в широкой кооперации предприятий Объединенной авиастроительной корпорации, с активным участием других отечественных поставщиков и ряда зарубежных партнеров. Согласно действующим в настоящее время планам, первый полет МС-21-300 намечен на середину 2016 г., а завершения процедуры сертификации и начала серийных поставок можно ожидать в 2018 г.
Корпорация «Иркут» является головным исполнителем программы разработки и производства перспективных пассажирских самолетов нового поколения МС-21 согласно распоряжению Президента России от 6 июня 2010 г Постройка опытных образцов, а затем и всех серийных самолетов семейства МС-21 будет вестись на Иркутском авиационном заводе, являющемся филиалом корпорации «Иркут».
Схема производственной кооперации при постройке МС-21 выглядит, в основном, следующим образом. За Иркутским авиационным заводом закреплено изготовление фюзеляжа и окончательная сборка самолета. Металлические панели отсеков фюзеляжа с Ф1 по Ф5, подкилевой отсек и отсек вспомогательной силовой установки, а также весь комплект дверей (11 штук на самолет) поставляет в Иркутск ульяновское АО «Авиастар-СП». В Ульяновске осуществляется и сборка хвостового оперения, панели и силовые элементы которого из полимерных композиционных материалов изготавливаются Обнинским НПП «Технология» холдинга «Химкомпозит». Панели центроплана, лонжероны и интегральные панели крыла изготавливаются из полимерных композиционных материалов по прогрессивной инфузионной технологии на новом предприятии «АэроКомпозит-Ульяновск», а композитные носовую и хвостовую части консолей крыла, механизацию и рули поставляет казанское «КАПО-Композит» (ульяновская и казанская производственные площадки входящего в состав ОАК предприятия «АэроКомпозит»). МС-21 должен стать первым отечественным гражданским самолетом с полностью композиционным крылом. В целом доля полимерных композиционных материалов в конструкции МС-21 составляет около 30%. В кооперации по изготовлению мотогондол двигателей ПД-14 задействовано ВАСО, которое поставляет для МС-21 также створки шасси, обтекатели крыла, закрылков и другие агрегаты из стеклопластика и пилоны двигателей.
Для самолета предусмотрено два типа силовой установки, на выбор заказчика: редукторные турбовентиляторные двигатели PW1400G-JM американской компании Pratt & Whitney и ТРДД высокой степени двухконтурности ПД-14 российской Объединенной двигателестроительной корпорации (головной разработчик – пермский «Авиадвигатель», головной завод-изготовитель – «Пермский моторный завод»). Стойки основных и передней опор шасси для МС-21 изготавливает Нижегородское ОАО «Гидромаш». Интеграцию комплекса авионики, в состав которого входят системы как отечественного (разработки предприятий концерна «Радиоэлектронные технологии»), так и зарубежного производства, и разработку программного обеспечения для него осуществляет подразделение Объединенной авиастроительной корпорации – «ОАК – Центр комплексирования».

Для постройки МС-21 на Иркутском авиазаводе в 2014 г. была смонтирована первая очередь инновационной технологической линии поточной сборки, оснащенная системами позиционирования и лазерного измерения. На ней осуществляется сборка отсеков фюзеляжа, их стыковка и последующая окончательная сборка самолета с использованием современных цифровых технологий. Новейшее оборудование и имеющиеся площади завода позволят в перспективе выпускать в Иркутске до 70 самолетов МС-21 в год.
В постройку в настоящее время уже заложены детали и агрегаты для первых четырех экземпляров самолета – летных, статического и ресурсного. Кроме того, изготовлено значительное число конструктивно подобных образцов элементов конструкции (панели, отсеки, агрегаты) для проведения статических и усталостных испытаний. Первые панели фюзеляжа для МС-21 были изготовлены в Ульяновске и отправлены в Иркутск весной 2014 г До конца года «Авиастар» отгрузил на Иркутский авиазавод полный комплект панелей для отсеков фюзеляжа Ф1 и Ф2 на первый летный образец МС-21-300, в марте 2015 г – комплект панелей на отсек Ф3, в мае – на отсек Ф4. В июле в Ульяновске был готов подкилевой отсек фюзеляжа и велось изготовление отсека ВСУ. К началу июня в Иркутске завершилась сборка отсека Ф1, в котором размещается кабина экипажа, а затем и Ф2, в июле выполнена стыковка Ф1 и Ф2, а в конце месяца к ним был пристыкован отсек Ф3 с центропланом. В августе велись работы по сборке и стыковке оставшихся секций фюзеляжа.
Готовые консоли крыла для первой летной машины ожидают в Иркутске из Ульяновска нынешней осенью, что должно позволить выдержать определенный постановлением правительства от 25 июля 2014 г. срок о завершении сборки планера первого летного образца МС-21-300 до 31 декабря 2015 г Тогда же должен быть готов и экземпляр планера для проведения статических испытаний (МС-21-300СИ). Согласно упомянутому распоряжению правительства, во второй половине 2016 г в Иркутске должны быть построены второй летный МС-21-300 и образец для ресурсных испытаний (МС-21-300РИ).
Базовая версия лайнера МС-21-300, чьи летные испытания с двигателями PW1400G-JM должны начаться в следующем году, рассчитана на перевозку до 211 пассажиров на расстояние до 5900 км. При типовой двухклассной конфигурации салона МС-21-300 сможет принимать на борт 163 пассажира (16 кресел в бизнес-классе и 147 – в «экономе»), при стандартной одноклассной компоновке (шаг кресел – 32 дюйма) – 181. До середины следующего года планируется завершить выпуск рабочей конструкторской документации на модификацию МС-21-200 с укороченным на 5,5 м фюзеляжем, рассчитанную на перевозку до 176 пассажиров на расстояние до 6000 км (135 пассажиров при двухклассной компоновке, включая 12 мест в бизнес-классе, и 153 – при типовой одноклассной с шагом кресел 32 дюйма). Максимальная взлетная масса МС-21-300 определена в 79 250 кг, укороченного МС-21-200 – в 72 390 кг.
Завершение сертификационных испытаний МС-21-300 и начало поставок намечаются на 2018 г Портфель твердых заказов на МС-21 в настоящее время включает 175 машин. Из них 50 законтрактованы лизинговой компанией «АвиакапиталСервис» (дочернее предприятие корпорации «Ростех») для «Аэрофлота», а еще 35 (с двигателями ПД-14) – для государственных заказчиков. Договор еще на 50 машин заключен с лизинговой компанией «Ильюшин Финанс Ко.», на 30 – с компанией «ВЭБ-лизинг». В рамках подписанных в августе 2013 г соглашений, эксплуатантами МС-21, заказанных ИФК и «ВЭБ-лизингом», в числе других могут стать авиакомпании «Трансаэро», «ЮТэйр» и «Ред Вингс». Кроме того, у корпорации «Иркут» есть прямой контракт с авиакомпанией «ИрАэро» на 10 самолетов.
«Наша цель к 2020 году – 40% станочного парка авиапрома»
Исполнительный директор Группы СТАН Вадим Сорокин – об импортозамещении в авиационном производстве

Вадим Николаевич, какое место в настоящее время занимает российская авиастроительная отрасль в закупках отечественного механообрабатывающего оборудования? Чем определяются потребности отечественного авиапрома в Вашей продукции?
Российская космическая и авиастроительная отрасли всегда были «локомотивами» прогресса в развитии промышленности, прежде всего – машиностроения. Корпорации, составляющие ядро авиационной отрасли, активно осуществляют программу технологической модернизации производств и переоснащения станочного парка. Только ведущими авиастроительными заводами Объединенной авиастроительной корпорации планируется закупка более 400 станков и обрабатывающих центров нового поколения.
Поскольку возрастают требования к продукции авиационной отрасли, возрастают они и по отношению к оборудованию, на котором она производится. Поэтому значительное внимание мы уделяем созданию новой техники, максимально адаптированной к современным потребностям авиапрома. Эти обстоятельства подталкивают станкостроение к инновационному развитию и повышают эффективность научной и проектно-конструкторской деятельности.
Кто основные покупатели станков Группы СТАН в авиастроении? Какого рода оборудование они приобретают? Можете ли оценить примерный объем поставок в этом году и рассказать о планах на ближайшие годы?
В настоящий момент осуществляется поставка станков на Нижегородский авиастроительный завод «Сокол»: идет замещение импортных станков и обрабатывающих центров аналогичным оборудованием российского производства. И нужно отметить, что сложившаяся ситуация с санкциями, во-первых, сблизила наши позиции с заказчиком в понимании общих проблем, во-вторых, послужила толчком для налаживания утраченных связей и обмена производственным опытом. На НАЗ «Сокол» будет поставлено 36 единиц отечественного оборудования, изготовленного заводами Группы СТАН. Прежде всего, это фрезерные станки и обрабатывающие центры. В связи с ростом количества заказов одно из предприятий Группы – НПО «Станкостроение» – перешло на трехсменный график работы.

Обрабатывающий центр серии S500 разработки «НПО «Станкостроение» (Стерлитамакский станкостроительный завод)
Кроме этого, мы ведем работу практически со всеми предприятиями авиационной отрасли в рамках реализации их планов по техническому перевооружению.
Перспективы поставок оборудования на ближайшие годы зависят от реализации федеральных целевых программ, по которым в подавляющем большинстве идет финансирование технического перевооружения отрасли. Можно сказать, что на сегодняшний момент наши предприятия готовы к тому, чтобы максимально загрузить имеющиеся производственные мощности своих заводов для обеспечения потребностей авиастроения. Мы активно ведем работы по совершенствованию конструкций оборудования и повышению технического уровня. При этом особое внимание уделяется программе импортозамещения в части комплектующих для станков.
Что в настоящее время представляет из себя Группа СТАН? Какие станкостроительные предприятия вы объединяете, какова их специализация?
Сегодня Группа СТАН является ключевым участником программы импортозамещения. По данным ассоциации «Станкоинструмент», на долю Группы приходится порядка 50% выпускаемой в России станкоинструментальной продукции. Необходимо отметить, что современные экономические условия и новая политическая реальность формируют новые тенденции, которые опираются не только на технологический, но и научно-исследовательский потенциал. Каждое предприятие, входящее в состав Группы СТАН, располагает конструкторским и исследовательским подразделениями, которые ведут разработку новых типов оборудования, способного составить достойную конкуренцию на международном рынке. В рамках политики импортозамещения мы выбрали курс на модернизацию технических мощностей предприятий станкостроительной отрасли и комплексное развитие за счет создания синергетического эффекта посредством их объединения. К слову сказать, совсем недавно был проведен независимый аудит технического состояния предприятий Группы одним из крупнейших авиационных заводов страны. Результат осмотра подтвердил высокий уровень и состояние производственных мощностей предприятий Группы СТАН, что, несомненно, является ключевой составляющей создания современного высокотехнологичного металлообрабатывающего оборудования.
Среди ключевых этапов формирования производственного потенциала Группы СТАН можно назвать, во-первых, создание ООО «НПО «Станкостроение» на базе старейшего предприятия – Стерлитамакского станкостроительного завода (Башкирия). На заводе осуществляется проектирование и производство высокоточных многофункциональных обрабатывающих центров с системой ЧПУ, предназначенных для всех видов черновой и чистовой обработки деталей любой сложности. НПО «Станкостроение» – единственный в России завод, который предлагает хонинговальные станки нового поколения – на модульной основе с электромеханическими приводами необходимых перемещений с адаптивной системой числового программного управления.
Во-вторых, это вхождение в состав Группы АО «Станкотех», расположенного на площадях завода тяжелых станков в Коломне (Московская область). Предприятие производит тяжелое и уникальное оборудование, прессы, фрезерные, токарно-карусельные станки, зубофрезерные станки, продольнофрезерные обрабатывающие центры, станки для обработки труб.
В-третьих, включение в Группу ООО «Рязанский Станкозавод». Это предприятие производит широкую гамму токарных станков – от универсальных до станков с ЧПУ и многофункциональных токарных обрабатывающих центров. Станкозавод является одним из трех предприятий в мире, производящих станки для глубокого сверления.
В-четвертых, необходимо отметить присоединение к нам ООО «Ивановский завод тяжелого станкостроения». Это предприятие, которое первое в России освоило производство тяжелых горизонтально-расточных станков и обрабатывающих центров с системами ЧПУ. Сегодня предприятие ведет разработку тяжелого многоцелевого станка с выдвижным ползуном ИСК5000 с возможностью 5-координатной обработки крупногабаритных деталей сложной конфигурации массой от 16 до 40 тонн. До этого станки подобного класса выпускались лишь в нескольких странах.
Наконец, нужно сказать о приобретении ООО «Шлифовальные Станки» – единственного отечественного предприятия, производящего современные станки для глубокого шлифования. В новых моделях SXS-DUO используются новые технологии высокоскоростного глубинного шлифования с использованием износостойких кругов.

Многофункциональный двухшпиндельный обрабатывающий центр SXS735-TC2 CNC, запущенный в эксплуатацию в НПО «Сатурн». Предназначен для шлифования и фрезерования деталей из титановых сплавов высокопроизводительным инструментом – эльборовыми и алмазными кругами со скоростью обработки до 90 м/с. Аналогов такому оборудованию в мире практически не существует
Давайте поговорим об общих тенденциях развития станочного парка предприятий авиастроения. Есть ли какая-то специфика у оборудования для авиапрома, по сравнению со станками для других отраслей промышленности?
Станки, применяемые в авиастроении, безусловно, отличаются от оборудования, используемого в других отраслях экономики. Прежде всего, это связано с особенностями материалов, из которых изготавливаются элементы конструкций, и особенностями технологий сборки авиакосмической техники. Анализ потребностей предприятий авиакосмической отрасли в реализации новых конструктивно-технологических решений станочного оборудования – это большая системная задача, которая предполагает совместное участие специалистов авиа– и станкостроения. В конечном итоге, результатом взаимодействия должно стать создание совместных центров компетенций, интегрированных структур нового формата, обеспечивающих не только текущие потребности, но и развитие инновационных технологий и оборудования.
Например, совместно с Технологическим центром ОАК нами определена номенклатура наиболее востребованных для производства обрабатывающих центров, проанализирована номенклатура станков, серийно выпускаемых для авиационных предприятий ведущими производителями США, Европы и Японии. На основе этого анализа были разработаны три модельных ряда обрабатывающих центров, отвечающих всем требованиям к оборудованию нового поколения по показателям качества и производительности. По техническим характеристикам они не уступают известным зарубежным образцам. В частности, учтены особенности обработки материалов деталей авиационной техники. Как пример, благодаря использованию мощных высокооборотных и высокомоментных шпинделей, а также скоростных приводов подач, на нашем оборудовании реализована высокоскоростная обработка деталей из легких сплавов, обеспечивающая большие объемы снимаемого материала. Успешно внедрены технологии снижения негативного воздействия вибраций, автоматической коррекции режимов резания при разности припусков, температурной компенсации структуры станка и рабочих жидкостей при отсутствии стабильности температуры в производственных помещениях.
А как выглядят на фоне зарубежных конкурентов предложения отечественных станкостроителей – по стоимости, функциональным возможностям, точности обработки деталей?
Безусловно, на качестве станкостроительной продукции сказались годы фактической невостребованности в отечественном оборудовании. О причинах этого можно рассуждать долго, но в настоящий момент необходимы адекватные и достаточно быстрые решения. На сегодня мы принимаем определенные меры по оптимизации системы менеджмента качества продукции, а также совершенствуем технический сервис.
По нашему мнению, претензии, выдвигаемые к качеству отечественного оборудования, в большинстве своем необоснованные. Зачастую они базируются на устаревших сведениях, а иногда и предубеждении, что отечественное станкостроение не способно конкурировать с иностранными производителями. Но результаты последних переговоров с авистроительными предприятиями и анализ нового отечественного оборудования доказывают, что оборудование российского производства по своим эксплуатационным характеристикам отвечает современным требованиям промышленности, в т.ч. и авиастроения.
Но нельзя сказать, что все проблемы решены. Прежде всего, они связаны с общим износом собственной технологической и, особенно, испытательной техники. Кроме этого, как и во всех других отраслях, в станкостроении наблюдается старение квалифицированных инженерных кадров, разрушение институтов отраслевой науки, межотраслевых связей и т.д. Но еще раз – «спасать» нас, кроме нас самих, некому. Сейчас очень важна государственная поддержка и политическая воля руководителей корпораций. В первую очередь – по размещению заказов на отечественных заводах. Очень интересен опыт Китая по квотированию закупок оборудования у местных производителей. Уверен, что вместе мы сможем решить задачу построения эффективных высокотехнологичных производств.
Каковы, по Вашим оценкам, сегодня доли устаревшего советского оборудования, современных импортных и новых отечественных станков на российских авиастроительных предприятиях? Как они, по Вашему мнению, будут меняться в ближайшее время и в более отдаленной перспективе?
Доля оборудования, выпущенного во времена существования Советского Союза, пока еще очень значительна. И процесс его замены должен осуществляться в рамках согласованной межотраслевой технической политики. Отслужившее свой срок и не удовлетворяющее по показателям качества, производительности и экономической эффективности оборудование может с высокой эффективностью использоваться в менее технологичных отраслях, на малых предприятиях, в технопарках, вузах и т.д. Должны быть созданы механизмы рециклинга оборудования. Еще одна задача – восстановление отраслевых служб технического сервиса. Во всем мире в большинстве своем – это малые предприятия, на которых, опять же, может быть использовано это устаревшее оборудование.
В авиастроении, безусловно, смена оборудования должна происходить более интенсивно, чем в других секторах экономики. Повторюсь, авиастроение – это «локомотив» развития всего машиностроения, отрасль, во многом определяющая обороноспособность страны, потенциал научной мысли и технологического развития.

Портальный обрабатывающий центр ОЦП-3000, разработанный АО «Станкотех» совместно с НПО «Техномаш». По оценке разработчиков, текущая потребность в подобном оборудовании у российских предприятий составляет от 50 до 100 единиц
По мере совершенствования технологий доля отечественных станков будет увеличиваться. Согласно федеральной целевой программе, к 2020 г. на долю отечественных производителей придется около 40% поставок станков. И мы уверены, что это в наших силах.
Кто сегодня может работать на поставляемых вами станках? Участвует ли Ваша компания в подготовке специалистов для работы на таком современном оборудовании?
Применение современных технологий обработки материалов, усложнение конструкции оборудования, постоянное совершенствование средств программирования требуют высокого уровня профессиональной подготовки технических специалистов. В рамках реализации обучающих программ мы сотрудничаем с авиационными предприятиями, техническими университетами, средними специальными учебными заведениями.
В частности, нами подписаны соглашения с ведущими техническими и технологическими российскими вузами – МГТУ им. Баумана, «СТАНКИНом», МАТИ, МАИ, Тульским государственным университетом и др.