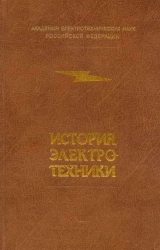
Текст книги "История электротехники"
Автор книги: авторов Коллектив
Жанр:
Технические науки
сообщить о нарушении
Текущая страница: 40 (всего у книги 78 страниц) [доступный отрывок для чтения: 28 страниц]
Начальный период. Индукционный нагрев проводников основан на физическом явлении электромагнитной индукции, открытом М. Фарадеем в 1831 г. Теорию индукционного нагрева начали разрабатывать О. Хэвисайд (Англия, 1884 г.), С. Ферранти, С. Томпсон, Ивинг. Их работы явились основой для создания техники индукционного нагрева. Так как при индукционном нагреве теплота выделяется в проводящем теле – слое, равном глубине проникновения электромагнитного поля, то появляются возможности точного управления температурой для обеспечения качественного нагрева при высокой производительности. Другим преимуществом является бесконтактность нагрева.
Индукционные канальные печи с открытым каналом. Одна из первых известных конструкций индукционной канальной печи (ИКП) была предложена С. Ферранти (Италия) в 1887 г. Печь имела керамический канал, а плоские катушки индуктора были размещены над и под этим каналом. В 1890г. Е.А. Колби (США) предложил конструкцию печи, у которой индуктор охватывает круговой канал снаружи.
Первую промышленную печь со стальным сердечником и индуктором, размещенным внутри канала (рис. 7.7), создал в 1900 г. Кьеллин (Швеция). Мощность печи 170 кВт, емкость до 1800 кг, частота 15 Гц. Питание от специального генератора пониженной частоты, что необходимо из-за низкого значения коэффициента мощности. К 1907 г. в эксплуатации находились 14 подобных печей.

Рис. 7.7. Эскиз индукционной печи с открытым каналом, созданной Кьеллииым1 – канал; 2 – индуктор; 3 – магнитопровод
В 1905 г. Рёхелинг-Роденхаузер (Германия) сконструировал многофазные канальные печи (с двумя и тремя индукторами), в которых каналы соединены с ванной, питание от сети 50 Гц. В последующих конструкциях печей использовались также закрытые каналы для плавки цветных металлов. В 1918 г. В. Рон (Германия) построил вакуумную ИКП по типу печи Кьеллина (давление 2–5 мм рт.ст.), что позволило получить металл с лучшими механическими свойствами.
В связи с рядом преимуществ печей с закрытым каналом развитие печей с открытым каналом приостановилось. Однако были продолжены попытки использования таких печей для плавки стали.
В 30-х годах в США для переплава скрапа нержавеющей стали использовалась однофазная ИКП емкостью 6 т с открытым каналом и питанием от генератора мощностью 800 кВт и частотой 8,57 Гц. Печь работала в дуплекс-процессе с дуговой печью. В 40–50-е годы в Италии применялись ИКП с открытым каналом для плавки стали емкостью 4–12 т, изготовленные фирмой «Таглиаферри». В дальнейшем от использования таких печей отказались, так как они уступали по своим характеристикам дуговым и индукционным тигельным сталеплавильным печам.
Индукционные канальные печи с закрытым каналом. С 1916 г. стали разрабатываться вначале опытные, а затем промышленные ИКП с закрытым каналом. Серия ИКП с закрытым каналом разработана фирмой «Аякс – Уатт» (США). Это шахтные однофазные печи с вертикальным каналом для плавки медноцинковых сплавов мощностью 75 и 170 кВ∙А и емкостью 300 и 600 кг. Они явились основой для разработок ряда фирм.
В те же годы во Франции были изготовлены шахтные печи с горизонтальной трехфазной индукционной единицей (мощностью 150, 225 и 320 кВт). В Англии фирма «Дженерал электрик лимитед» предложила модификацию печи с двумя каналами на индуктор, при их несимметричном расположении, что вызывает циркуляцию расплава и снижение перегрева.
Печи Э. Русса (Германия) выпускались с двумя и тремя каналами на индуктор (вертикальное и горизонтальное исполнение). Э. Руссом также была предложена конструкция сдвоенной индукционной единицы (ИЕ), подключаемой к двум фазам.
В СССР в 30-е годы ИКП по типу печей фирмы «Аякс – Уатт» стали выпускаться на Московском электрозаводе. В 50-е годы ОКБ «Электропечь» разработало печи для плавки меди и ее сплавов емкостью 0, 4–6,0 т, а затем и 16 т. В 1955 г. на заводе в г. Белая Калитва пущена ИКП для плавки алюминия емкостью 6 т.
В 50-е годы в США и Западной Европе ИКП стали широко применяться в качестве миксеров при плавке чугуна в дуплекс-процессе с вагранкой или дуговой электропечью. Для увеличения мощности и снижения перегрева металла в канале разрабатывались конструкции ИЕ с однонаправленным движением расплава (Норвегия). Тогда же были разработаны отъемные ИЕ. В 70-е годы фирма «Аякс магнетермик» разработала сдвоенные ИЕ, мощность которых в настоящее время достигает 2000 кВт. Подобные разработки в те же годы выполнены и во ВНИИЭТО. В разработках ИКП различных типов активно участвовали Н.В. Веселовский, Э.П. Леонова, М.Я. Столов и др.
В 80-е годы развитие ИКП в нашей стране и за рубежом было направлено на увеличение областей применения и расширение технологических возможностей, например применение ИКП для получения труб из цветных металлов методом вытягивания из расплава.
Индукционные тигельные печи. Так как индукционные тигельные печи (ИТП) малой емкости могут эффективно работать только на частотах выше 50 Гц, то их создание сдерживалось из-за отсутствия соответствующих источников питания – преобразователей частоты. Тем не менее в 1905–1906 гг. ряд фирм и изобретателей предложили и запатентовали ИТП, к ним относятся фирма «Шнейдер – Крезо» (Франция), О. Цандер (Швеция), Герден (Англия). В это же время конструкцию ИТП разработал А.Н. Лодыгин (Россия).
Первую промышленную ИТП с искровым высокочастотным генератором разработал в 1916 г. Э.Ф. Нортруп (США). С 1920 г. эти печи стала выпускать фирма «Аякс электротермию). В это же время ИТП с питанием от вращающегося искрового разрядника разрабатывает Ж. Рибо (Франция). Фирма «Метрополитен – Виккерс» создала ИТП высокой и промышленной частоты. Вместо искровых генераторов использовались машинные преобразователи с частотой до 3000 Гц и мощностью 150 кВ∙А.
В.П. Вологдин в 1930–1932 гг. создал промышленные ИТП емкостью 10 и 200 кг с питанием от машинного преобразователя частоты. В 1937 г. он же построил ИТП с питанием от лампового генератора. В 1936 г. А.В. Донской разработал универсальную индукционную печь с ламповым генератором мощностью 60 кВ∙А.
В 1938 г. для питания ИТП (мощность 300 кВт, частота 1000 Гц) фирма «Броун – Бовери» использовала инвертор на многоанодном ртутном вентиле. С 60-х годов стали использоваться тиристорные инверторы для питания индукционных установок. С увеличением емкости ИТП стало возможным эффективное применение питания током промышленной частоты.
В 40–60-х годах ОКБ «Электропечь» разработало несколько типов ИТП: повышенной частоты для плавки алюминия емкостью 6 т (1959 г.), чугуна емкостью 1 т (1966 г.). В 1980 г. на заводе в г. Баку изготовлена печь емкостью 60 т для плавки чугуна (разработка ВНИИЭТО по лицензии фирмы «Броун – Бовери»). Большой вклад в разработку ИТП во ВНИИЭТО внесли Э.П. Леонова, В.И. Кризенталь, А.А. Простяков и др.
В 1973 г. фирма «Аякс магнетермик» совместно с исследовательской лабораторией фирмы «Дженерал моторе» разработала и ввела в эксплуатацию горизонтальную тигельную печь непрерывного действия для плавки чугуна емкостью 12 т и мощностью 11 МВт.
Начиная с 50-х годов стали развиваться специальные виды индукционной плавки металлов:
вакуумная в керамическом тигле;
вакуумная в гарнисаже;
вакуумная в холодном тигле;
в электромагнитном тигле;
во взвешенном состоянии;
с использованием комбинированного нагрева.
Вакуумные индукционные печи (ВИП) до 1940 г. применялись только в лабораторных условиях. В 50-х годах некоторые фирмы, в частности «Хереус», стали разрабатывать промышленные ВИП, единичная емкость которых стала быстро возрастать: 1958 г. – 1–3 т, 1961–5 т, 1964–15–27 т, 1970–60 т. В 1947 г. МосЗЭТО изготовил первую вакуумную печь емкостью 50 кг, а с 1949 г. начал серийное производство ВИП емкостью 100 кг. В середине 80-х годов производственное объединение «Сибэлектротерм» по разработкам ВНИИЭТО изготавливало модернизированные ВИП емкостью 160, 600 и 2500 кг для плавки специальных сталей.
Индукционная плавка химически активных сплавов в гарнисажных печах и печах с медным водоохлаждаемым (холодным) тиглем стала применяться в 50-х годах. Печь с порошкообразным гарнисажем была разработана Н.П. Глухановым, Р.П. Жежериным и др. в 1954 г., а печь с монолитным гарнисажем – М.Г. Коганом в 1967 г. Идея индукционной плавки в холодном тигле предложена еще в 1926 г. в Германии фирмой «Сименс – Гальске», но применения не нашла. В 1958 г. В ИМЕТ совместно с ВНИИ токов высокой частоты им. В.П. Вологдина (ВНИ-ИТВЧ) под руководством А.А. Фогеля проведены опыты по индукционной плавке титана в холодном тигле.
Стремление снизить загрязнение металла и тепловые потери в холодном тигле привели к использованию электромагнитных сил для отжатия металла от стенок, т.е. к созданию «электромагнитного тигля» (Л.Л. Тир, ВНИИЭТО, 1962 г.)
Плавка металлов во взвешенном состоянии для получения особо чистых металлов была предложена в Германии (О. Мук) еще в 1923 г., но не получила распространения из-за отсутствия источников питания. В 50-е годы этот метод начал развиваться во многих странах. В СССР много работали в этом направлении сотрудники ВНИИТВЧ под руководством А.А. Фогеля.
Плавильные ИКП и ИТП комбинированного нагрева стали применяться с 50-х годов вначале с использованием мазутных и газовых горелок, например ИКП для переплава алюминиевой стружки (Италия) и ИТП для чугуна (Япония). Позднее получили распространение плазменно-индукционные тигельные печи, например разработанная ВНИИЭТО в 1985 г. серия опытно-промышленных печей емкостью 0,16–1,0 т.
Установки индукционной поверхностной закалки. Первые опыты по индукционной поверхностной закалке проведены в 1925 г. В.П. Вологдиным по инициативе инженера Путиловского завода Н.М. Беляева, которые были признаны неудачными, так как в то время стремились к сквозной закалке. В 30-х годах В.П. Вологдин и Б.Я. Романов возобновили эти работы и в 1935 г. получили патенты на закалку с использованием токов высокой частоты. В 1936 г. В.П. Вологдин и А.А. Фогель получили патент на индуктор для закалки шестерен. В.П. Вологдин и его сотрудники разрабатывали все элементы закалочной установки: вращающийся преобразователь частоты, индукторы и трансформаторы (рис. 7.8).

Рис. 7.8. Закалочная установка для последовательной закалки
1 – закаливаемое изделие; 2 – индуктор; 3 – закалочный трансформатор; 4 – преобразователь частоты; 5 – конденсатор
С 1936 г. Г.И. Бабат и М.Г. Лозинский на заводе «Светлана» (Ленинград) исследовали процесс индукционной закалки с использованием высоких частот при питании от лампового генератора. С 1932 г. закалка током средней частоты стала внедряться фирмой ТОККО (США).
В Германии в 1939 г. Г.В. Зойлен осуществил поверхностную закалку коленчатых валов на заводах фирмы АЕГ. В 1943 г. К. Кегель предложил специальную форму индуктирующего провода для закалки зубчатого колеса.
Широкое применение поверхностной закалки началось с конца 40-х годов. За 25 лет с 1947 г. ВНИИТВЧ разработал свыше 300 закалочных устройств, в том числе введены в эксплуатацию автоматическая линия для закалки коленчатых валов и установка для закалки железнодорожных рельсов по всей длине (1965 г.). В 1961 г. пущена первая установка для закалки шестерен из стали пониженной прокаливаемости на автозаводе им. Лихачева (ЗИЛ) (технология разработана К.З. Шепеляковским).
Одним из направлений развития индукционной термообработки в последние годы стали технологии закалки и отпуска труб нефтяного сортамента и газопроводных труб большого диаметра (820–1220 мм), строительных арматурных стержней, а также упрочнения железнодорожных рельсов.
Установки сквозного нагрева. Применение индукционного нагрева металлов для различных целей, кроме плавки, на первом этапе носило поисковый характер. В 1918 г. М.А. Бонч-Бруевич, а затем и В.П. Вологдин применили для нагрева анодов электронных ламп при их вакуумировании (дегазации) токи высокой частоты. В конце 30-х годов в лаборатории завода «Светлана» проводились опыты по использованию индукционного нагрева до температуры 800–900°С при обработке стального вала диаметром 170 и длиной 800 мм на токарном станке. Использовался ламповый генератор мощностью 300 кВт и частотой 100–200 кГц.
С 1946 г. в СССР начались работы по использованию индукционного нагрева при обработке давлением. В 1949 г. введен в эксплуатацию первый кузнечный нагреватель на ЗИЛе (ЗИСе). Эксплуатация первой индукционной кузницы начата на Московском заводе малолитражных автомобилей (МЗМА, позднее АЗЛК) в 1952 г. Интересная двухчастотная установка (60 и 540 Гц) для нагрева стальных заготовок (сечение – квадрат 160x160 мм) под обработку давлением была запущена в Канаде в 1956 г. Подобная же установка разработана в ВНИИТВЧ (1959 г.). Промышленная частота используется при этом для нагрева до точки Кюри.
Для прокатного производства в 1963 г. ВНИИТВЧ изготовил нагреватель слябов (габариты 2,5x0,38x1,2 м) мощностью 2000 кВт на частоту 50 Гц.
В 1969 г. на металлургическом заводе фирмы «Маклаут стил корп.» (США) применен индукционный нагрев стальных слябов массой около 30 т (габариты 7,9x0,3x1,5 м) с использованием шести технологических линий (18 индукторов промышленной частоты общей мощностью 210 МВт).
Индукторы имели специальную форму, обеспечивающую равномерность нагрева сляба. Работы по применению индукционного нагрева в металлургии велись также и во ВНИИЭТО (П.М. Чайкин, С.А. Яицков, А.Э. Эрман).
В конце 80-х годов в СССР индукционный нагрев использовался приблизительно в 60 кузнечных цехах (прежде всего на заводах автотракторной и оборонной промышленности) с общей мощностью индукционных нагревателей до 1 млн. кВт.
Низкотемпературный нагрев на промышленной частоте. В 1927–1930 гг. на одном из уральских оборонных заводов начались работы по индукционному нагреву на промышленной частоте (Н.М. Родигин). В 1939 г. там с успехом работали достаточно мощные индукционные нагревательные установки для термообработки изделий из легированной стали.
В ЦНИИТмаше (В.В. Александров) также проводились работы по применению промышленной частоты для термообработки, нагрева под посадку и т.д. Ряд работ по низкотемпературному нагреву выполнен под руководством А.В. Донского. В НИИжелезобетона (НИИЖБ), Фрунзенском политехническом институте и других организациях в 60–70-х годах проводились работы по термообработке железобетонных изделий с использованием индукционного нагрева на частоте 50 Гц. ВНИИЭТО также разработал ряд промышленных установок низкотемпературного нагрева для подобных целей. Разработки МЭИ (А.Б. Кувалдин) в области индукционного нагрева ферромагнитной стали были использованы в установках для подогрева деталей под наплавку, термообработки стали и железобетона, обогрева химических реакторов, пресс-форм и др. (70–80-е годы).
Высокочастотная зонная плавка полупроводников. Метод зонной плавки был предложен в 1952 г. (В.Г. Пфанн, США). Работы по высокочастотной бестигельной зонной плавке в нашей стране начались в 1956 г., и во ВНИИТВЧ был получен монокристалл кремния диаметром 18 мм. Созданы различные модификации установок типа «Кристалл» с индуктором внутри вакуумной камеры (Ю.Э. Недзвецкий). В 50-е годы изготовление установок для вертикальной бестигельной зонной плавки кремния с индуктором снаружи вакуумной камеры (кварцевой трубы) осуществлялось на заводе «Платиноприбор» (Москва) совместно с Государственным институтом редких металлов (Гиредмет). Начало серийного производства установок «Кристалл» для выращивания монокристаллов кремния относится к 1962 г. (на Таганрогском ЗЭТО). Диаметр получаемых монокристаллов достиг 45 мм (1971 г.), а позднее и свыше 100 мм (1985 г.)
Высокочастотная плавка оксидов. В начале 60-х годов Ф.К. Монфорт (США) провел плавку оксидов в индукционной печи (выращивание монокристаллов ферритов при использовании токов высокой частоты – радиочастот). Тогда же А.Т Чэпмен и Г.В. Кларк (США) предложили технологию переплавления поликристаллического оксидного блока в холодном тигле. В 1965 г. Ж. Рибо (Франция) получил расплавы оксидов урана, тория и циркония при использовании радиочастот. Плавка этих оксидов происходит при высоких температурах (1700–3250 °С), и поэтому требуется большая мощность источника питания.
В СССР технология высокочастотной плавки оксидов разработана в Физическом институте АН СССР (A.M. Прохоров, В.В. Осико). Оборудование разрабатывали ВНИИТВЧ и Ленинградский электротехнический институт (ЛЭТИ) (Ю.Б. Петров, А.С. Васильев, В.И. Добровольская). Созданные ими установки «Кристалл» в 1990 г. имели общую мощность свыше 10 000 кВт, на них производились сотни тонн оксидов высокой степени чистоты в год.
Высокочастотный нагрев плазмы. Явление высокочастотного разряда в газе известно с 80-х годов XIX в. В 1926–1927 гг. Дж.Дж. Томсон (Англия) показал, что безэлектродный разряд в газе создается индуцированными токами, а Дж. Таунсенд (Англия, 1928 г.) объяснял разряд в газе действием электрического поля. Все эти исследования проводились при пониженных давлениях.
В 1940–1941 гг. Г.И. Бабат на заводе «Светлана» при дегазации электронных ламп с использованием высокочастотного нагрева наблюдал плазменный разряд, а затем впервые получил разряд при атмосферном давлении.
В 50-е годы в разных странах проводились работы по высокочастотной плазме (Т.Б. Рид, Ж. Рибо, Г. Баркхофф и др.). В СССР они велись с конца 50-х годов в Ленинградском политехническом институте (А.В. Донской, С.В. Дресвин), МЭИ (М.Я. Смелянский, С.В. Кононов), ВНИТВЧ (И.П. Дашкевич) и др. Исследовались разряды в различных газах, конструкции плазмотронов и технологии с их использованием. Были созданы высокочастотные плазмотроны с кварцевой и с металлической (для мощностей до 100 кВт) водоохлаждаемой (создана в 1963 г.) камерами.
В 80-х годах высокочастотные плазмотроны мощностью до 1000 кВт на частоты 60 кГц – 60 МГц применялись для получения особо чистого кварцевого стекла, пигментного диоксида титана, новых материалов (например, нитридов и карбидов), особо чистых ультрадисперсных порошков и разложения отравляющих веществ.
7.1.4. ДИЭЛЕКТРИЧЕСКИЙ НАГРЕВНачальный период. Впервые эффект нагрева диэлектрика в переменном электромагнитном поле зафиксировали в 1864 г. Э.В. Сименс (Германия) и в 1886 г. И.И. Боргман (Россия) – исследовался нагрев стеклянной стенки конденсатора (лейденской банки) при заряде и разряде.
Диэлектрический нагрев первоначально нашел применение в медицине. В 1891 г. Ж.А. д'Арсонваль (Франция) обнаружил термическое воздействие переменного электромагнитного поля на человека. Р. фон Зейнек (Германия) в 1899 г. открыл возможность использования электромагнитных полей частотой свыше 200 кГц для нагрева тканей тела и лечения. С 1906 г. использование диатермии стало быстро распространяться, и до настоящего времени диэлектрический нагрев широко используется для физиотерапии.
В 1925 г. А. Эсау (Франция) заметил, что передатчик большой мощности метрового диапазона, т.е. сверхвысокочастотные (СВЧ) волны, вызывал ощущение нагрева у персонала и предложил использовать СВЧ-волны для терапии. Совместно с Е. Шлипхаке он провел испытания на животных и людях.
В 1930 г. И. Петцольд (Германия) исследовал влияние частоты на глубину прогрева.
Диэлектрический нагрев нашел широкое применение, несмотря на сложность и высокую стоимость оборудования, так как позволяет нагревать непроводящие однородные материалы с высокой скоростью и равномерностью, а неоднородные материалы – избирательно, например, при сушке или склеивании.
Диэлектрический нагрев токами высокой частоты. В 1930–1934 гг. началась разработка технологии сушки древесины токами высокой частоты (Н.С. Селюгин, Ленинградский филиал ЦНИИ механической обработки древесины). В это же время А.И. Иоффе получил авторское свидетельство на высокочастотную сушку (ВЧ-сушку) древесины. Одно из первых применений – сушка березовых и буковых заготовок на обувной фабрике «Скороход» (г. Ленинград). Позднее диэлектрический нагрев стал применяться и в других странах (Франция, США, Германия).
В 1933 г. Центральная научно-исследовательская лаборатория электромагнитных волн, которая исследовала сушку и стерилизацию фруктов (внедрение в гг. Тирасполе и Краснодаре, 1938–1940 гг.). В 1937 г. П.П. Тарутин (ВНИИзерна) изучал ВЧ-сушку и уничтожение вредителей зерна с применением токов высокой частоты.
В США в 40-е годы развиваются высокочастотный нагрев пластмасс, склеивание древесины и фанеры. Во Франции А. Эсау разрабатывает ВЧ-сушку текстиля и продуктов питания, склеивание древесины и нагрев пластмасс перед прессованием, М. Дескарсин (1946 г.) – нагрев керамики, Ледюк и Дюфур – вулканизацию каучука.
В СССР в 40-е годы продолжались работы по диэлектрическому нагреву. С 1941 г. началось промышленное применение ВЧ-сушки древесины. В ВЭИ исследуют получение с применением диэлектрического нагрева пресс-порошков (Н.В. Александров и В.М. Дегтев) и электроизоляционных материалов (Л.С. Левин). А в НИИ шинной промышленности (Х.Э. Малкина и А.П. Пухов) – вулканизацию массивных шин.
На развитие техники диэлектрического нагрева большое влияние оказали работы А.В. Нетушила, особенно выпущенная под его редакцией монография «Высокочастотный нагрев диэлектриков и полупроводников» (1959 г.).
Большой вклад в промышленное применение диэлектрического нагрева внес ВНИИТВЧ (А.А. Фрумкин, А.В. Дмитриев, Т.А. Шелина):
серийное производство установок для нагрева таблеток пресспорошков (1949 г.);
внедрение высокочастотной сушки пряжи на фабрике им. А.И. Желябова (г. Ленинград); 1953 г.;
начало серийного производства на Ленинградском заводе высокочастотных установок (ЛЗВУ) установок для сварки термопластов (1956 г.);
серийное производство установок для склеивания древесины (1962 г.);
начало опытной эксплуатации конвейерной установки для высокочастотной сушки литейных стержней на Минском тракторном заводе (1969 г.);
серийное производство конвейерных высокочастотных установок (1971 г.);
введение линии для получения пенополистирольной теплоизоляции для холодильников в г. Ереване (1972 г.).
На начало 1966 г. в СССР было изготовлено свыше 12 тыс. высокочастотных установок для диэлектрического нагрева общей колебательной мощностью около 30 МВт. Единичные мощности установок диэлектрического нагрева непрерывно возрастали от единиц до сотен киловатт.
В 80-е годы ВНИИТВЧ разработал высокочастотные установки диэлектрического нагрева периодического действия для сушки различных материалов с питанием от лампового генератора мощностью 60 кВт и частотой 13,56 МГц с использованием для перемещения материала вращающегося кольцевого дна из фторопласта или ленточного транспортера из металлической сетки. Были разработаны также технологические процессы и оборудование для диэлектрического нагрева пористых материалов (пенополистирола, пенополиэтилена, пористых резин) и высокочастотной сварки термопластичных материалов (полихлорвинилов, полистирола, полиакрилатов, искусственных кож).
Нагрев на сверхвысоких частотах (микроволновый нагрев). Нагрев на сверхвысоких частотах (СВЧ) стал применяться после изобретения магнетрона в 40-х годах. В США в 1947 г. появилась первая СВЧ-плита «Радарэндж» с рабочей частотой 2400 МГц (длина волны 12,5 см), установленная в вагоне-ресторане и предназначенная для размораживания и подогрева предварительно приготовленных и замороженных блюд. В начале 70-х годов в США использовалось около 2 млн. бытовых микроволновых печей, в Японии – около 500 тыс.
С 1961 г. в Москве на ВДНХ демонстрировалась печь, созданная ВНИИТВЧ. Ленинградский завод торгового машиностроения изготовил опытно-промышленную серию подобных печей с использованием магнетронов непрерывного действия мощностями 600 и 1600 Вт.
В начале 60-х годов проводились опытные работы по промышленному применению нагрева на сверхвысоких частотах, в частности для разрушения горных пород (США, Япония) и получения плазменного факела (США, ФРГ). У нас в стране работы по измельчению твердых горных пород проводил в 60-х годах Институт горного дела имени А.А. Скачинского, но из-за экономических показателей этот способ оказался неконкурентоспособным.
В конце 80-х годов фирма «Линн» (Австрия) разработала высокотемпературную СВЧ-установку для спекания оксидов (температура до 2000 °С), в которой использованы футеровка и водоохлаждение резонатора.
В последние годы в нашей стране выпускается ряд промышленных СВЧ-установок для диэлектрического нагрева мощностью 0,5–60 кВт.