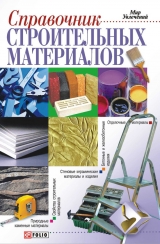
Текст книги "Справочник строительных материалов, а также изделий и оборудования для строительства и ремонта квартиры"
Автор книги: Владимир Онищенко
Жанры:
Хобби и ремесла
,сообщить о нарушении
Текущая страница: 11 (всего у книги 32 страниц) [доступный отрывок для чтения: 12 страниц]
Свойства и применение низкообжиговых гипсовых вяжущих веществ
Основными характеристиками гипсовых вяжущих являются сроки схватывания, тонкость помола, прочность при сжатии и растяжении, водопотребность и др.
Гипсовое вяжущее является быстросхватывающим и быстро-твердеющим вяжущим веществом. По срокам схватывания вяжущие материалы подразделяются на: быстротвердеющие (индекс А) с началом схватывания не ранее 2 мин, концом – не позднее 15 мин; нормальнотвердеющие (индекс Б) с началом схватывания не ранее 6 мин, концом – не позднее 30 мин; медленнотвердеющие (индекс Б) с началом схватывания не ранее 20 мин, конец схватывания не нормируется. В зависимости от степени помола различают вяжущие грубого, среднего и тонкого помола с максимальным остатком на сите с размером ячеек в свету 0,2 мм не более 23, 14 и 2 % (обозначаемые соответственно индексами I, II и III). Марку гипсовых вяжущих характеризуют по прочности при сжатии образцов-балочек 40x40x160 мм в возрасте 2 ч после затворения водой. Четкое индексирование различных сортов гипсовых вяжущих позволяет давать большой объем информации в сокращенной форме. Например, гипсовое вяжущее с прочностью при сжатии
5,2 МПа, началом схватывания 5 мин, концом схватывания 9 мин и остатком на сите 0,2 мм 9 %, т. е. вяжущее марки Г-5 быстро-твердеющее, среднего помола, записывается в виде сокращенного обозначения Г-5АП.
Чтобы получить гипсовое удобное для укладки тесто, необходимо взять 60–80 % воды от массы вяжущего, а на химическую реакцию гидратации требуется лишь 18,6 % воды. Избыток ее остается в порах, затем испаряется, поэтому получившийся в результате твердения полуводного гипса гипсовый камень обладает высокой пористостью, достигающей 40–60 % и более. Чем больше воды затворения, тем выше пористость камня, а прочность его, соответственно, меньше. Прочность гипсовых образцов, высушенных при температуре до 60 °C, в 2–2,5 раза выше прочности влажных образцов после 1,5 ч твердения. Лучшие сорта гипса после сушки имеют прочность при сжатии 18–20 МПа, а прочность при растяжении в 6–8 раз меньше.
При твердении гипс расширяется в объеме до 1 %, благодаря чему гипсовые отливки хорошо заполняют форму и передают ее очертания. При его высыхании трещин не образуется, что позволяет применять гипсовое вяжущее без заполнителей. Гипсовое вяжущее в воде снижает свою прочность вследствие растворения дигидрата и разрушения кристаллического сростка. Водостойкость его может быть повышена введением небольших количеств гидрофобных веществ (олеиновой кислоты и др.), добавкой молотого гранулированного шлака, извести, портландцемента.
Наряду с гипсовыми вяжущими общестроительного назначения выпускаются вяжущие для фарфоро-фаянсовой и керамической промышленности, к которым предъявляется ряд дополнительных требований: объемное расширение – не более 0,15 %; примесей, нерастворимых в НС1, – не более 1 %; водопоглощение – не менее 30 %.
Гипсовые вяжущие применяют при производстве гипсовой штукатурки, перегородочных стеновых плит и панелей, вентиляционных коробов и других деталей в зданиях и сооружениях, работающих при относительной влажности воздуха не выше 65 %. Изделия из них обладают небольшой плотностью, несгораемостью и рядом других ценных свойств, но при увлажнении прочность их снижается.
Для гипсовых строительных изделий всех видов рекомендуются марки от Г-2 до Г-7 всех сроков твердения и степеней помола; для тонкостенных строительных изделий и декоративных деталей может использоваться гипс тех же марок, но только тонкого и среднего помола, быстрого и нормального твердения. При штукатурных работах и заделке швов применяют марки Г-2—Г-25 нормального и медленного твердения. Гипс марок Г-5—Г-25 тонкого помола с нормальными сроками твердения служит для изготовления форм и моделей в керамической, машиностроительной промышленности, а также в медицине.
Ангидритовые вяжущие вещества
Ангидритовое вяжущее получают обжигом природного двуводного гипса при температуре 600–700 °C с последующим его измельчением с добавками – катализаторами твердения (известью, смесью сульфата натрия с медным или железным купоросом, обожженным доломитом, основным доменным гранулированным шлаком и др.). Ангидритовое вяжущее можно получить также путем помола природного ангидрита с указанными выше добавками.
Наиболее распространено ангидритовое вяжущее следующего состава: известь – 2–5 %; смесь бисульфата или сульфата натрия с железным или медным купоросом – по 0,5–1 % каждого; доломит, обожженный при 800–900 °C, – 3–8 %; основной гранулированный доменный шлак – 10–15 %. Железный и медный купоросы уплотняют поверхность затвердевшего ангидритового цемента, вследствие чего катализаторы не выделяются и не образуют выцветы на поверхности изделия. Действие катализаторов объясняется тем, что ангидрит обладает способностью образовывать комплексные соединения с различными солями в виде неустойчивого сложного гидрата, который затем распадается.
Ангидритовый цемент – это медленно схватывающееся вяжущее вещество с началом схватывания не ранее 30 мин, концом – не позднее 24 ч. Марки ангидритового цемента по прочности при сжатии – М50, 100, 150 и 200. Применяют ангидритовые цементы для приготовления кладочных и отделочных растворов, бетонов, производства теплоизоляционных материалов, искусственного мрамора и других декоративных изделий.
Высокообжиговый гипс (эстрих-гипс) является разновидностью ангидритовых цементов. Его получают обжигом природного гипса или ангидрита при температуре 800—1000 °C с последующим тонким измельчением. При этом происходит не только полное обезвоживание, но и частичная диссоциация (разложение) ангидрита с образованием СаО (в количестве 3–5 %). При затворении водой СаО действует как катализатор по схеме твердения ангидритового цемента, рассмотренной выше.
Высокообжиговый гипс медленно схватывается и твердеет, но водостойкость и прочность при сжатии (10–20 МПа) позволяют успешно использовать его при устройстве мозаичных полов, изготовлении искусственного мрамора и др. Изделия из высокообжигового гипса мало тепло– и звукопроводны, они обладают по сравнению с изделиями из гипсового вяжущего более высокой морозостойкостью, повышенной водостойкостью и меньшей склонностью к пластическим деформациям.
Магнезиальные вяжущие вещества
Разновидностями магнезиальных вяжущих веществ являются каустический магнезит и каустический доломит.
Каустический магнезит получают при обжиге горной породы магнезита MgC0 3в шахтных или вращающихся печах при 650–850 °C. В результате MgC0 3разлагается. Оставшееся твердое вещество (окись магния) измельчают в тонкий порошок. Каустический доломит MgO и СаС0 3получают путем обжига природного доломита CaC0 3MgC0 3с последующим измельчением его в тонкий порошок. При обжиге доломита СаС0 3не разлагается и остается инертным как балласт, что снижает вяжущую активность каустического доломита по сравнению с каустическим магнезитом.
Магнезиальные вяжущие затворяют не водой, а водными растворами солей сернокислого или хлористого магния. Магнезиальные вяжущие, затворенные на растворе хлористого магния, дают большую прочность, чем на растворе сернокислого магния. Магнезиальные вяжущие, являясь воздушными, слабо сопротивляются действию воды. Их можно использовать только при затвердении на воздухе с относительной влажностью не более 60 %. Каустический магнезит легко поглощает влагу и углекислоту из воздуха, в результате чего образуются гидрат оксида магния и углекислый магний. В связи с этим каустический магнезит хранят в плотной герметической таре. На основе магнезиальных вяжущих в прошлом времени изготовляли ксилолит (смесь вяжущего с опилками), используемый для устройства полов, а также фибролит и другие теплоизоляционные материалы. В настоящее время применение магнезиальных вяжущих резко сократилось.
Строительная известь
Строительную известь получают из кальциево-магниевых горных пород – мела, известняка, доломитизированных и мергелистых известняков, доломитов – путем обжига (до удаления углекислоты).
Для производства тонкодисперсной строительной извести гасят водой или размалывают негашеную известь, вводя при этом минеральные добавки в виде гранулированных доменных шлаков, активные минеральные добавки или кварцевые пески. Строительную известь применяют для приготовления растворов и бетонов, вяжущих материалов и в производстве искусственных камней, блоков и строительных деталей.
В зависимости от условий твердения различают строительную известь воздушную, обеспечивающую твердение строительных растворов и бетонов и сохранение ими прочности в воздушно-сухих условиях, и гидравлическую, обеспечивающую твердение растворов и бетонов и сохранение ими прочности как на воздухе, так и в воде. Воздушная известь по виду содержащегося в ней основного оксида бывает кальциевая, магнезиальная и доломитовая. Воздушную известь подразделяют на негашеную и гидратную (гашеную), получаемую гашением кальциевой, магнезиальной и доломитовой извести. Гидравлическую известь делят на слабогидравлическую и сильногидравлическую. Также различают гидравлическую известь комовую и порошкообразную. В свою очередь порошкообразная известь бывает двух видов: молотая и гидратная (гашеная вода). Комовую известь выпускают без добавок и с добавками.
Строительную негашеную известь по времени гашения делят на быстрогасящуюся – не более 8 мин, среднегасящуюся – не более 25 мин, медленногасящуюся – более 25 мин. Воздушную известь получают из кальциево-магниевых карбонатных пород. Технологический процесс получения извести состоит из добычи известняка в карьерах, его подготовки (дробления и сортировки) и обжига. После обжига производят помол комовой извести, получая молотую негашеную известь, или гашение комовой извести водой, с образованием гашеной извести.
Основным процессом при производстве извести является обжиг, при котором известняк декарбонизуется и превращается в известь. Диссоциация карбонатных пород сопровождается поглощением теплоты. Реакция разложения углекислого кальция обратима и зависит от температуры и парциального давления углекислого газа. Диссоциация углекислого кальция достигает заметной величины при температуре свыше 600 °C. Теоретически нормальной температурой диссоциации считают 900 °C.
Гидравлическая известьГидравлическая известь – продукт умеренного обжига при температуре 900—1100 °C мергелистых известняков, содержащих 6—20 % глинистых примесей. При обжиге известняков этого типа после разложения углекислого кальция часть образующегося СаО соединяется в твердом состоянии с оксидами Si0 2, А1 20 3, Fe 20 3, содержащимися в минералах глины, образуя силикаты 2CaOSiC) 2, алюминаты СаОА1 2С) 3и ферриты кальция 2Ca0-Fe 20 3, обладающие способностью твердеть не только на воздухе, но и в воде. Так как в гидравлической извести содержится в значительном количестве свободный оксид кальция СаО, то она, так же как и воздушная известь, гасится при действии воды, причем чем больше содержание свободного СаО, тем меньше способность извести к гидравлическому твердению.
Строительную гидравлическую известь выпускают в виде тонкоизмельченного порошка, при просеивании которого остаток частиц на сите № 008 не должен превышать 15 %. Кроме глинистых и песчаных примесей мергелистые известняки обычно содержат до 2–5 % углекислого магния и другие примеси.
Для производства гидравлической извести необходимо применять известняки с возможно более равномерным распределением глинистых и других включений, так как от этого в значительной степени зависит качество получаемого продукта.
Для характеристики химического состава сырья, содержащего известняк и глину, а также готового вяжущего вещества обычно пользуются так называемым гидравлическим, или основным модулем. Слабогидравлическая известь с модулем 4,5–9, а сильно-гидравлическая – с модулем 1,7–4,5.
Гидравлическая известь, затворенная водой, после предварительного твердения на воздухе продолжает твердеть и в воде, при этом физико-химические процессы воздушного твердения сочетаются с гидравлическими. Гидрат оксида кальция при испарении влаги постепенно кристаллизуется, а под действием углекислого газа подвергается карбонизации. Гидравлическое твердение извести происходит в результате гидратации силикатов, алюминатов и ферритов кальция так же, как в портландцементе. Предел прочности образцов через 28 суток твердения должен быть не менее: для слабогидравлической и сильногидравлической соответственно при изгибе – 0,4 и 1,0 МПа и при сжатии – 1,7 и 0,5 МПа.
Гидравлическая известь по химическому составу должна соответствовать стандартам, в частности, она должна выдерживать испытание на равномерность изменения объема. Гидравлическую известь применяют в тонкоизмельченном виде для приготовления строительных растворов, предназначенных для сухой или влажной среды, бетонов низких марок и т. д. Такая известь дает менее пластичные, чем воздушная, растворы, быстрее и равномернее твердеющие по всей толще стены и обладающие большей прочностью.
Цементы
Кислотоупорные цементыКислотоупорные цементы состоят из смеси водного раствора силиката натрия (растворимого стекла), кислотоупорного наполнителя и добавки – ускорителя твердения. В качестве микронаполнителя используют кварц, кварциты, андезит, диабаз и другие кислотоупорные материалы; ускорителем твердения служит кремнефтористый натрий. Вяжущим материалом в кислотоупорном цементе является растворимое стекло – водный раствор силиката натрия или силиката калия. Отношение числа молекул кремнезема к числу молекул щелочного оксида называется модулем стекла и колеблется для разных видов цемента от 2,5 до 3,5.
Добавка кремнефтористого натрия также повышает водостойкость и кислотоупорность цемента. Отечественная промышленность выпускает кислотоупорный кварцевый кремнефтористый цемент, состоящий из смеси тонкомолотого чистого кварцевого песка 15–30 % и кремнефтористого натрия – 4–6 % от массы наполнителя.
Кислотоупорные цементы применяют для футеровки химической аппаратуры, возведения башен, резервуаров и других сооружений химической промышленности, а также для приготовления кислотоупорных замазок, растворов и бетонов. Как указывалось ранее, для приготовления кислотоупорного цемента применяют растворимое стекло. Его получают при сплавлении в течение 7– 10 ч в стекловарочных печах при 1300–1400 °C кварцевого песка, измельченного и тщательно смешанного с кальцинированной содой, сульфатом натрия или с поташом.
Твердеет растворимое стекло (довольно медленно) только на воздухе, вследствие выделения и высыхания аморфного кремнезема под действием углекислоты воздуха. Однако глубина проникания углекислоты сравнительно невелика и положительное ее действие наблюдается только на поверхности.
Ускоряет твердение растворимого стекла добавка катализатора – кремнефтористого натрия Na 2SiF 6. Последний вступает во взаимодействие с растворимым стеклом, в результате чего быстро образует гель кремнекислоты – клеящее вещество, что приводит к быстрому твердению системы.
ПортландцементПортландцемент – гидравлическое вяжущее вещество, твердеющее в воде и на воздухе. Его получают тонким измельчением обожженной до спекания сырьевой смеси известняка и глины, обеспечивающей преобладание в клинкере силикатов кальция. Клинкером называется спекшаяся сырьевая смесь в виде зерен размером до 40 мм; от его качества зависят важнейшие свойства цемента: прочность и скорость ее нарастания, долговечность, стойкость в различных эксплуатационных условиях. Для регулирования сроков схватывания в обычных цементах марок 300–500 при помоле к клинкеру добавляют гипс в количестве не менее 1,0 % и не более 3,5 % от массы цемента в пересчете на ангидрид серной кислоты S0 3, а в цементах высокомарочных и быстротвердеющих – не менее 1,5 % и не более 4,0 %. Портландцемент выпускают без добавок или с активными минеральными добавками.
Качество клинкера зависит от его химического и минералогического составов. Для производства портландцементного клинкера применяют известняк и глину. Известняк в основном состоит из двух оксидов: СаО и С0 2, а глина – из различных минералов. В процессе обжига сырьевой смеси удаляется С0 2, а оставшиеся четыре оксида образуют клинкерные минералы. Содержание оксидов в цементе примерно следующее: 64–67 % СаО, 21–24 % Si0 2, 4–8 % А1 20 3, 2–4 % Fe 20 3. Кроме указанных основных оксидов в портландцементном клинкере могут присутствовать MgO и щелочные оксиды, которые снижают качество цемента. Оксид магния, обожженный при температуре около 1500 °C, при взаимодействии с водой очень медленно гасится и вызывает появление трещин в уже затвердевшем растворе или бетоне, поэтому его содержание в портландцементе не должно быть более 5 %. Наличие в цементе щелочных оксидов свыше 1 % может вызвать разрушение отвердевшего бетона.
Указанные выше основные оксиды находятся в клинкере не в свободном виде, а образуют при обжиге четыре основных минерала, относительное содержание которых в портландцементе следующее (%): трехкальциевый силикат (алит) – 45–60; двухкальциевый силикат (белит) —20–35; трехкальциевый алюминат – 4—12; четырехкальциевый алюмоферрит – 10–18.
Алит — основной минерал клинкера, быстро твердеет и практически определяет скорость твердения и нарастания прочности портландцемента. Он представляет собой твердый раствор трехкальциевого силиката и небольшого количества (2–4 %) других примесей, которые могут существенно влиять на структуру и свойства портландцемента. Белит – второй по важности и содержанию силикатный минерал клинкера, медленно твердеет и достигает высокой прочности при длительном твердении. Белит в клинкере представляет собой твердый раствор двухкальциевого силиката и небольшого количества (1–3 %) др. примесей. В связи с тем, что белит при медленном охлаждении клинкера теряет вяжущие свойства, это явление предотвращается быстрым охлаждением клинкера.
Содержание минералов-силикатов в клинкере в сумме составляет около 75 %, поэтому гидратация алита и белита в основном определяет свойства портландцемента. Трехкальциевый алюминат при благоприятных условиях обжига образуется в виде кубических кристаллов. Он очень быстро гидратирует и твердеет. Продукты гидратации имеют пористую структуру и низкую прочность. Кроме того, он является причиной сульфатной коррозии цемента, поэтому его содержание в сульфатостойком цементе ограничено 5 %. Четырехкальциевый алюмоферрит – алюмоферритная фаза промежуточного вещества клинкера – представляет собой твердый раствор алюмоферритов кальция разного состава. По скорости гидратации этот минерал условно занимает промежуточное положение между алитом и белитом и не оказывает определяющего значения на скорость твердения и тепловыделение портландцемента.
На структуру бетона оказывает значительное влияние пористость цементного камня, связанная с начальным содержанием воды в бетонной смеси. Для получения удобной для укладки бетонной смеси в нее вводят в 2–3 раза больше воды, чем требуется на реакцию с цементом. Таким образом, большая часть воды затворения оказывается в свободном состоянии и образует в затвердевшем камне множество мелких пор. Поэтому для получения плотной структуры цементного камня необходимо применять бетонные смеси с минимальным содержанием воды. В результате повышаются прочность и морозостойкость бетона.
Структура цементного камня, а именно наличие в нем пор и гелеобразного вещества, обусловливает склонность его к влажностным деформациям. При увлажнении он разбухает, а при высушивании дает усадку. Знакопеременные сжимающие и растягивающие напряжения, вызываемые изменением влажности окружающей среды, расшатывают структуру цементного камня и понижают прочность бетона. Степень влажностных деформаций зависит от соотношения гелеобразных и кристаллических фаз в цементном камне. С увеличением последней стойкость камня в таких условиях, называемая воздухостойкостью, повышается. В отличие от рассмотренных далее пуццолановых портландцементов, обыкновенный портландцемент отличается высокой воздухостойкостью. Расширение и растрескивание цементного камня могут вызвать также свободные СаО и MgO, присутствующие в цементе при низком качестве обжига. Гашение их сопровождается значительным увеличением в объеме, и продукты этого гашения разрывают цементный камень.
Прочность портландцемента характеризуют пределами прочности при сжатии и изгибе. Марку цемента устанавливают по пределу прочности при изгибе образцов балочек 40x40x160 мм и при сжатии их половинок, изготовленных из раствора состава 1:3 (по массе) с нормальным песком при водоцементном отношении 0,4 и испытанных через 28 суток; образцы в течение этого времени хранят во влажных условиях при температуре 20±2 °C. Предел прочности при сжатии в возрасте 28 суток называется активностью цемента.
Влияние влажности и температуры среды. Большое влияние на рост прочности цементного камня оказывают влажность и температура среды. Скорость химических реакций между клинкерными минералами и водой увеличивается с повышением температуры, а также значительно возрастает скорость уплотнения продуктов гидратации цемента. Твердение цементного камня на практике может происходить в широком диапазоне температур: нормальное твердение – при температуре 15–20 °C, пропаривание – 80–90 °C, автоклавная обработка – до 170–200 °C, давление пара – до 0,8–1,2 МПа и твердение – при отрицательной температуре.
Продолжительность хранения . Длительное хранение цемента даже в самых благоприятных условиях влечет за собой некоторую потерю его активности. После трех месяцев хранения потеря активности цемента может достигать 20 %, а через год – доходить до 40 %. Цементы более тонкого помола теряют больший процент активности, так как влага воздуха, соприкасаясь с цементом, вызывает преждевременную его гидратацию. Восстанавливать активность лежалого цемента можно вторичным помолом. Наиболее эффективен вибродомол цемента, в процессе которого повышается тонкость помола цемента, а также происходит обдирка гидратных и инертных оболочек с цементных зерен. Наиболее целесообразным методом предотвращения потери активности цемента является гидрофобизация.
Стойкость цементного камня . Бетон в инженерных сооружениях в процессе эксплуатации может быть подвержен агрессивному воздействию внешней среды: пресных и минерализованных вод, совместному действию воды и мороза, попеременному увлажнению и высушиванию. Среди компонентов бетона цементный камень наиболее подвержен развитию коррозионных процессов. Для того чтобы бетон стойко сопротивлялся агрессивному воздействию внешней среды, цементный камень должен быть коррозие-, морозо– и атмосферостойким.
Морозостойкость . При отрицательных температурах вода, находящаяся в порах цементного камня, превращается в лед, который увеличивается в объеме примерно на 9 % по сравнению с объемом воды. Лед давит на стенки пор и разрушает их. Морозостойкость цементного камня зависит от минералогического состава клинкера, тонкости помола цемента и водоцементного отношения. До определенной тонкости помола (5000–6000 см 2/г) морозостойкость цемента увеличивается, но при дальнейшем возрастании тонкости помола она падает. Это объясняется пористой структурой новообразований цемента сверхтонкого измельчения.
Присутствие в цементе в значительном количестве активных минеральных добавок отрицательно влияет на морозостойкость цементного камня вследствие их высокой пористости и низкой морозостойкости продуктов взаимодействия добавок с компонентами цементного камня.
Увеличение водоцементного отношения понижает морозостойкость цементного камня вследствие повышения его пористости. Надо иметь в виду, что замораживание цементного камня в начальный период твердения является наиболее опасным, так как он еще не обладает достаточной прочностью и не может энергично сопротивляться действию льда.