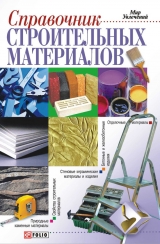
Текст книги "Справочник строительных материалов, а также изделий и оборудования для строительства и ремонта квартиры"
Автор книги: Владимир Онищенко
Жанры:
Хобби и ремесла
,сообщить о нарушении
Текущая страница: 10 (всего у книги 32 страниц) [доступный отрывок для чтения: 12 страниц]
Из сборных железобетонных конструкций и деталей в сельских местностях возводят жилые дома, здания машинно-тракторных станций, животноводческие фермы, силосные сооружения, склады, теплицы и другие постройки сельскохозяйственного назначения. Изделия для сельскохозяйственных сооружений изготовляют из бетона класса не ниже В15; изделия для силосных траншей, ям и башен должны иметь защитный слой от действия органических кислот.
Сборные железобетонные конструкции и детали для сельского строительства принципиально не отличаются от применяемых в гражданском и промышленном строительстве, но некоторые сооружения, например силосные башни и бункера элеваторов, выполняются из деталей несколько другой конструкции. В данном случае применяют сборные железобетонные кольца, диаметр которых равен диаметру будущего сооружения. При возведении башен большого диаметра кольца заменяют криволинейными плитами.
Производство железобетонных изделий
Технологический процесс производства сборных бетонных и железобетонных изделий состоит из ряда самостоятельных операций, объединяемых в отдельные процессы. Операции условно разделяют на основные, вспомогательные и транспортные.
К основным операциям относят: приготовление бетонной смеси, включая подготовку составляющих материалов; изготовление арматурных элементов и каркасов; формироание изделий, куда входит их армирование; тепловую обработку отформованных изделий, освобождение готовых изделий от форм и подготовка форм к очередному циклу; отделку и обработку лицевой поверхности некоторых видов изделий и т. п.
Кроме основных технологических операций на каждом этапе производят вспомогательные операции: получение и подача пара и воды, сжатого воздуха, электроэнергии, складирование сырьевых материалов, полуфабрикатов и готовой продукции, пооперационный контроль и контроль качества готовой продукции и др., необходимые для выполнения основных операций. К транспортным относят операции по перемещению материалов, полуфабрикатов и изделий без изменения их состояния и формы.
Оборудование, используемое для выполнения надлежащих операций, называют соответственно основным (технологическим), вспомогательным и транспортным. Основное и транспортное оборудование, предназначенное для выполнения операций в определенной последовательности, называют технологической линией.
На заводах сборного железобетона используются поточные методы организации технологического процесса, сущность которых состоит в том, что весь процесс расчленяется на отдельные операции, которые выполняются в строгой последовательности на определенных рабочих местах, оснащенных специализированным оборудованием. На каждом рабочем месте в соответствии с принятыми методами обработки, оборудованием и организационным строением выполняется одна или несколько близких между собой технологических операций.
В промышленности сборного железобетона наиболее распространены два основных метода организации производства : в перемещаемых и неперемещаемых формах. Они отличаются условиями перемещения форм, изделий, машин и рабочих. Выполнение комплекса основных технологических операций по изготовлению сборного железобетона осуществляется по трем принципиальным схемам: стендовой, поточно-агрегатной и конвейерной. При изготовлении изделий в неперемещаемых формах все технологические операции, от подготовки форм до распалубки готовых отвердевших изделий, осуществляются на одном месте. К этому способу относится формование изделий на плоских стендах или матрицах, в кассетах.
При изготовлении изделий в перемещаемых формах отдельные технологические операции формования или отдельный комплекс их производятся на специализированных постах. Форма, а затем изделие вместе с формой перемещаются от поста к посту по мере выполнения отдельных операций. В зависимости от степени расчлененности общего технологического процесса формования по отдельным постам различают конвейерный, имеющий наибольшую расчлененность, и поточно-агрегатный способы. Последний отличается тем, что ряд операций – укладка арматуры и бетонной смеси, уплотнение – выполняются на одном посту, т. е. сегрегированы между собой. При конвейерном способе большинство операций выполняется на соответствующих постах, образующих в совокупности технологическую линию.
Способы уплотнения бетонной смесиКак уже отмечалось ранее в разделе «Особые свойства бетона», одна из важнейших характеристик бетонной смеси – способность пластически растекаться под действием собственной массы или приложенной к ней нагрузки. Это и определяет сравнительную легкость изготовления из бетонной смеси изделий самого разнообразного профиля и возможность уплотнения ее различными способами. При этом способ уплотнения и свойства смеси (ее подвижность или текучесть) находятся в тесной связи. Так, жесткие нетекучие смеси требуют энергичного уплотнения, и при формовании из них изделий следует применять интенсивную вибрацию или вибрацию с дополнительным прессованием (так называемым пригрузом). Возможны также и другие способы уплотнения жестких смесей – трамбование, прессование, прокат.
Подвижные смеси легко и эффективно уплотняются вибрацией. Применение же сжимающих (прессующих) видов уплотнения – прессования, проката, а также и трамбования – для таких смесей непригодно. Под действием значительных прессующих усилий или часто повторяющихся ударов трамбовки смесь будет легко вытекать из-под штампа или разбрызгиваться трамбовкой. Литые смеси способны уплотняться под действием собственной массы. Для повышения эффекта уплотнения их иногда подвергают кратковременной вибрации.
Наиболее эффективным как в техническом, так и в экономическом отношениях способом уплотнения бетонных смесей является вибрирование. Его успешно применяют также в сочетании с другими способами механического уплотнения – трамбованием(вибротрамбование), прессованием(вибропрессование), прокатом(вибропрокат). Разновидностью механических способов уплотнения подвижных бетонных смесей является центрифугирование, используемое при формовании полых изделий трубчатого сечения. Хорошие результаты в отношении получения бетона высокого качества дает вакуумирование смесив процессе ее механического уплотнения (преимущественно вибрированием), однако значительная продолжительность операции вакуумирования существенно снижает ее технико-экономический эффект.
Армирование железобетонных изделийАрмирование железобетонных изделий, как уже говорилось в начале этого раздела нашей книги, подразделяется на два вида: ненапряженное (обыкновенное) и предварительно напряженное. Операции армирования и виды арматуры, применяемые при каждом из этих способов армирования, имеют ряд принципиальных отличий.
Арматурные сетки и каркасы изготовляют в арматурном цехе, оборудованном резательными, гибочными и сварочными аппаратами. Процесс производства строится по принципу единого технологического потока, от подготовки арматурной стали до получения готового изделия. Арматурные сетки и каркасы изготовляют в соответствии с рабочими чертежами, в которых указаны длина и диаметр стержней, их количество, расстояние между ними, места приварки закладных деталей и расположения монтажных петель. При установке и раскреплении каркасов в форме необходима высокая точность, так как от этого зависит величина защитного слоя бетона в изделии. Стержневую арматурную сталь диаметром до 10 мм поставляют на завод в мотках (бухтах), а диаметром от 10 мм и более – в прутках длиной 6—12 м или мерной длины, оговариваемой в заказах.
Арматурную проволоку поставляют в мотках, причем каждый моток состоит из одного отрезка проволоки. Изготовление арматуры складывается из следующих операций: подготовки проволочной и прутковой стали – чистки, правки, резки, стыкования, гнутья; сборки стальных стержней в виде плоских сеток и каркасов; изготовления объемных арматурных каркасов, включая приварку монтажных петель, закладных частей, фиксаторов. Подготовка арматуры, поступающей на завод в мотках и бухтах, заключается в их размотке, выпрямлении (правке), очистке и резке на отдельные стержни заданной длины. Правку и резку арматурной стали осуществляют на правильно-отрезных станках-автоматах.
Прутковую арматурную сталь разрезают на стержни заданной длины, а также стыкуют сваркой в целях уменьшения отходов. Стыкуют стержни посредством контактной стыковкой электросварки и только в отдельных случаях при использовании стержней больших диаметров применяют дуговую сварку. Контактную стыковую сварку осуществляют методом оплавления электрическим током торцов стержней в местах их будущего стыка. При этом стержни сильно сжимают и сваривают между собой.
При изготовлении монтажных петель, хомутов и других фигурных элементов арматуры прутковую и проволочную арматурную сталь после резки подвергают гнутью. Сборку сеток и каркасов из стальных арматурных стержней производят посредством точечной контактной электросварки. Сущность ее заключается в следующем. При прохождении электрического тока через два пересекающихся стержня в местах их контакта электрическое сопротивление оказывается наибольшим, стержни в этом месте разогреваются и, достигнув пластического состояния металла, свариваются между собой. Прочной сварке способствует также сильное сжатие стержней между собой. Процесс точечной сварки может длиться доли секунды при применении тока в несколько десятков тысяч ампер. Точечную сварку осуществляют с помощью специальных сварочных аппаратов. Они отличаются мощностью трансформатора, количеством одновременно свариваемых точек (одно– и многоточечные), характером используемых устройств для сжатия свариваемых стержней. Сварочные машины позволяют создавать в комплексе с другими машинами и установками поточные автоматические линии изготовления плоских сеток как готового арматурного элемента, так и полуфабрикатов для изготовления пространственных каркасов.
Для обеспечения обжатия бетона применяемая арматурная сталь должна находиться в пределах упругих деформаций и не превышать 85–90 % от предела текучести стали, а для углеродистых сталей, не имеющих четко выраженного предела текучести, – 65–70 % от предела прочности на разрыв. В качестве основной напрягаемой арматуры применяют проволочную и прутковую арматурные стали, а в качестве вспомогательной ненапрягаемой арматуры, если она имеет место в напряженных изделиях, – сварные сетки и каркасы. При изготовлении предварительно напряженных изделий пользуются одноосным обжатием бетона отдельными стержнями или пучками проволок, располагаемых в изделии вдоль его продольной оси, и объемным обжатием путем навивки напряженной проволоки в двух или нескольких направлениях. Можно навивать проволоку и на готовое изделие с последующей защитой арматуры слоем бетона.
Арматурные элементы, применяемые в конструкциях, состоят из собственно арматуры, устройств для закрепления арматуры при натяжении и приспособлений для обеспечения проектного расположения отдельных стержней и проволок, из которых комплектуется арматурный элемент. Конструкция устройств для закрепления арматуры связана с технологией изготовления арматурного элемента, типом натяжения машин и приспособлений. Применяют два вида этих устройств: зажимы и анкеры. В свою очередь, зажимы и анкеры подразделяют по способу закрепления арматуры на клиновые, плоские, конические, волновые, петлевые, резьбовые, шпоночные и глухие анкеры, в которых концы арматурных пучков опрессовываются в обойме из мягкой стали. Все приведенные устройства, за исключением резьбовых, применяют для закрепления как круглых стержней, так и стержней периодического профиля.
Формование железобетонных изделийЗадача технологического комплекса формования изделий состоит в получении плотных изделий заданных формы и размеров, что обеспечивается применением соответствующих форм, а их высокая плотность достигается уплотнением бетонной смеси.
Комплекс технологических операций процесса формования может быть условно разделен на две группы: первая включает операции по изготовлению и подготовке форм (очистке, смазке, сборке), вторая – уплотнение бетона изделий и получение их заданной формы. Не менее важны при этом и транспортные операции. Наиболее характерным в данном случае является изготовление крупноразмерных особо тяжелых изделий – балок, ферм, пролетных строений мостов, когда по причине значительных затрат на их перемещение изготовление таких изделий организуют на одном месте, т. е. применяют стендовую схему организации процесса.
В общем технологическом комплексе изготовления железобетонных изделий операции формования и ускоренного твердения бетона занимают определяющее место. Все другие операции – приготовление бетонной смеси, изготовление арматуры – являются в какой-то степени подготовительными.
Формы и смазочные материалы для них . Для изготовления железобетонных изделий применяют формы деревянные, стальныеи железобетонные, а иногда металложелезобетонные.Следует отметить, что выбор материала форм весьма принципиален как в техническом, так и в экономическом отношениях.
Независимо от материала к формам предъявляются следующие общие требования: обеспечение необходимых форм и размеров изделий и сохранность их в процессе всех технологических операций; минимальная масса по отношению к единице массы изделия, что достигается рациональной конструкцией форм; простота и минимальная трудоемкость сборки и разборки форм; высокая жесткость и способность сохранить свою форму и размеры при динамических нагрузках, неизбежно возникающих при транспортировании, распалубке изделий и сборке форм.
Особую значимость для качества изделий и сохранности форм имеет правильный выбор смазочных материалов, препятствующих сцеплению бетона с материалом формы. Смазка должна хорошо удерживаться на поверхности формы в процессе всех технологических операций, обеспечивать возможность ее механизированного нанесения (распылением), полностью исключать сцепление бетона изделия с формой и не должна портить внешнего вида изделия. Этим требованиям в значительной степени удовлетворяют смазочные материалы следующих составов: масляные эмульсии с добавкой кальцинированной соды, масляные смазки – смесь солярового (75 %) и веретенного (25 %) масел или машинного масла (50 %) и керосина (50 %) и др.
Твердение железобетонных изделийТвердение отформованных изделий – заключительная операция технологии изготовления железобетона, в процессе которой изделия приобретают требуемую прочность. Отпускная прочность может быть равна классу бетона или меньше его. Так, прочность бетона изделий при отгрузке потребителю должна быть не менее 70 % проектной (28-суточной) прочности для изделий из бетона на портландцементе или его разновидностях и 100 % – для изделий из силикатного (известково-песчаного) или ячеистого бетона. Однако для железнодорожных шпал отпускная прочность должна превышать 70 % и для пролетных строений мостов – 80 % от класса. Допускаемое снижение отпускной прочности изделий определяется исключительно экономическими соображениями, так как в этом случае сокращается продолжительность производственного цикла и, соответственно, ускоряется оборачиваемость оборотных средств.
При этом имеется в виду, что недостающую до проектной прочность изделия наберут в процессе их транспортирования и монтажа и к моменту загружения эксплуатационной нагрузкой прочность их будет не ниже проектной.
В зависимости от температуры среды различают следующие три принципиально отличающихся режима твердения изделий: нормальный при температуре 15–20 °C; тепловлажностная обработка при температуре до 100 °C и нормальном давлении; автоклавная обработка – пропаривание при повышенном давлении (0,8–1,5 МПа) и температуре 174–200 °C. Независимо от режима твердения относительная влажность среды должна быть близкой к 100 %, иначе будет происходить высушивание изделий, что приведет к замедлению или прекращению роста их прочности, так как твердение бетона – это в первую очередь гидратация цемента, т. е. взаимодействие цемента с водой.
Нормальные условия твердения достигаются в естественных условиях без затрат тепла. Это важнейшее технико-экономическое преимущество указанного способа твердения, отличающегося простотой в организации и минимальными капитальными затратами. В то же время экономически оправдан он может быть только в исключительных случаях.
В естественных условиях изделия достигают отпускной 70 %-ной прочности в течение 7—10 суток, тогда как при искусственном твердении – пропаривании или автоклавной обработке – эта прочность достигается за 10–16 ч. Соответственно, при этом снижается потребность в производственных площадях, объеме парка форм, сокращается продолжительность оборачиваемости средств. Это достигается применением высокопрочных быстротвердеющих цементов, жестких бетонных смесей, интенсивного уплотнения вибрацией с дополнительным пригрузом, применением добавок – суперпластификаторов, ускорителей твердения, виброактивизации бетонной смеси перед формованием, применением горячих бетонных смесей.
Отделка поверхности железобетонных изделийВыбор метода отделки поверхностей железобетонных изделий производят с учетом целого ряда требований. Отделка должна быть долговечной и защищать бетон от атмосферных и агрессивных воздействий, а также отвечать архитектурно-декоративным требованиям.
В настоящее время отделку поверхностей выполняют путем использования окрасочных составов, облицовочных материалов и цветных бетонов.
Окрасочные составы должны быть щелоче– и водостойкими, долговечными и устойчивыми против выцветания. В качестве окрасочных составов используют силикатные, цементные и полимерные краски. Силикатные краскиприготовляют из жидкого стекла, минеральных красящих веществ (пигментов) и наполнителей. Цементные краскиготовят из белого цемента с минеральными красящими веществами, а перхлорвиниловые (полимерные) краски– из минеральных красящих веществ, разбавленных перхлорвиниловым лаком. Нанесение красок на поверхность железобетонных изделий производят с помощью пистолета-распылителя за два или три приема в зависимости от цвета используемого красящего вещества и консистенции раствора. Покраску поверхностей ведут при положительных температурах.
К облицовочным материаламнаряду с архитектурно-декоративными требованиями предъявляются требования высокой прочности и долговечности в условиях переменных атмосферных воздействий. В настоящее время в качестве облицовочных материалов используют плитки из природных каменных материалов, керамические, асбестоцементные, стеклянные плитки, плитки и блоки из цветного бетона, гофрированные листы из алюминия.
Плитки из природных каменных материалов– наиболее долговечный, обеспечивающий разнообразную гамму цветов материал, получаемый в результате распиловки мраморов, гранитов, лабрадоритов, кварцитов, известняков и других окрашенных горных пород.
Бетонные плиткиизготовляют на специальных гидравлических прессах из цветного бетона.
Керамические облицовочные плиткиобладают высокими и декоративными свойствами, хорошо сцепляются с бетоном. Плитки выпускают крупноразмерные (10x10, 10x20 см) и мелкоразмерные (48x48 мм). При производстве крупноразмерных железобетонных панелей облицовка из мелкоразмерной ковровой плитки оказывается менее трудоемкой и более производительной по сравнению с облицовкой крупноразмерной плиткой, которая укладывается поштучно вручную.
Стеклянные плиткивыпускают различных цветов – от белого до черного.
В качестве облицовочных материалов для отделки железобетонных стеновых панелей используют также цветные цементные плиткии алюминиевые листы.Последние обладают высокой атмо-сферостойкостью, прочностью и хорошими архитектурно-декоративными свойствами.
Минеральные вяжущие материалы
Минеральными вяжущими материалами называют тонкоизмельченные порошки, образующие при смешивании с водой пластичное тесто, под влиянием физико-химических процессов переходящее в камневидное состояние. Это свойство вяжущих веществ используют для приготовления на их основе растворов, бетонов, безобжиговых искусственных каменных материалов и изделий. Различают минеральные вяжущие вещества воздушные и гидравлические.
Воздушные вяжущие веществатвердеют, долго сохраняют и повышают свою прочность только на воздухе. К воздушным вяжущим веществам относятся гипсовые и магнезиальные вяжущие, воздушная известь и кислотоупорный цемент. Гидравлические вяжущие веществаспособны твердеть и длительно сохранять свою прочность не только на воздухе, но и в воде. В группу гидравлических вяжущих входят портландцемент и его разновидности, пуццолановые и шлаковые вяжущие, глиноземистый и расширяющиеся цементы, гидравлическая известь. Их используют в надземных, в подземных и подводных конструкциях.
Наряду с этим различают вяжущие вещества, эффективно твердеющие только при автоклавной обработке – давлении насыщенного пара 0,8–1,2 МПа и температуре 170–200 °C. В группу вяжущих веществ автоклавного твердениявходят известково-кремнеземистые и известково-нефелиновые вяжущие.
Гипсовые вяжущие веществаделят на две группы: низкообжиговые и высокообжиговые. Низкообжиговые гипсовые вяжущие веществаполучают при нагревании двуводного гипса CaS0 42H 20 до температуры 150–160 °C с частичной дегидратацией двуводного гипса и переводом его в полуводный гипс CaS0 40,5H 20.
Высокообжиговые (ангидритовые) вяжущиеполучают обжигом двуводного гипса при более высокой температуре до 700—1000 °C с полной потерей химически связанной воды и образованием безводного сульфата кальция – ангидрита CaS0 4. К низкообжиговым относится строительный, формовочный и высокопрочный гипс, а к высокообжиговым – ангидритовый цемент и эстрихгипс.
Сырьем для производства гипсовых вяжущих служат природный гипсовый камень и природный ангидрит CaS0 4, а также отходы химической промышленности, содержащие двуводный или безводный сернокислый кальций, например фосфогипс. Возможно применение гипсосодержащего природного сырья в виде сажи и глиногипса.
Гипсовым вяжущим называют воздушное вяжущее вещество, состоящее преимущественно из полуводного гипса и получаемое путем тепловой обработки гипсового камня при температуре 150–160 °C. При этом двуводный гипс CaS0 4*2H 20, содержащийся в гипсовом камне, дегидратирует.
В этих условиях образуются мелкие кристаллы полуводного сернокислого кальция-модификации; такой гипс обладает повышенной водопотребностью (60–65 % воды). Избыточная вода, т. е. сверх необходимого на гидратацию гипса (15 %), испаряется, образуя поры, вследствие чего затвердевший гипс имеет высокую пористость (до 40 %) и, соответственно, небольшую прочность. Производство гипса складывается из дробления, помола и тепловой обработки (дегидратации) гипсового камня. Имеется несколько технологических схем производства гипсового вяжущего: в одних помол предшествует обжигу, в других помол производится после обжига, а в третьих помол и обжиг совмещаются в одном аппарате. Последний способ получил название «обжига гипса во взвешенном состоянии». Тепловую обработку гипсового камня производят в варочных котлах, сушильных барабанах, шахтных или других мельницах.
Наиболее распространена схема производства гипсового вяжущего с применением варочных котлов. Гипсовый камень, поступающий на завод в крупных кусках, сначала дробят, затем измельчают в мельнице, одновременно подсушивая его. В порошкообразном виде камень направляют в варочный котел периодического или в установку непрерывного действия. При варке в котле гипс не соприкасается с топочными газами, что позволяет получать чистую продукцию, не загрязненную золой топлива.
Гипсовое вяжущее в сушильных барабанах получают путем обжига гипсового камня в виде щебня размером до 20 мм. В результате вращения наклонного барабана перемещается в сторону наклона. Из топки в барабан поступают раскаленные дымовые газы, которые при движении вдоль барабана обжигают гипсовый камень, а с противоположной стороны удаляются вентилятором. Далее гипсовый камень измельчают в мельницах.
Быстрое схватывание гипса затрудняет в ряде случаев его использование и вызывает необходимость применения замедлителей схватывания (кератинового, известково-кератинового клея, сульфитно-дрожжевой бражки в количестве 0,1–0,3 % от массы гипса). Замедлители схватывания уменьшают скорость растворения полу-водного гипса и замедляют диффузионные процессы. При необходимости ускорить схватывание гипса к нему добавляют двуводный гипс, поваренную соль, серную кислоту. Одни из них повышают растворимость полуводного гипса, другие (двуводный гипс) образуют центры кристаллизации, вокруг которых быстро закристаллизовывается вся масса.
Применяется гипсовое вяжущее для производства гипсовых и гипсобетонных строительных изделий для внутренних частей зданий (перегородочных плит, панелей, сухой штукатурки, приготовления гипсовых и смешанных растворов, производства декоративных и отделочных материалов, например искусственного мрамора), а также для производства гипсоцементно-пуццолановых вяжущих.
Высокопрочный гипс является разновидностью полуводного гипса. Этот полуводный гипс a-модификации, который имеет более крупные кристаллы, обусловливающие меньшую водопотребность гипса (40–45 % воды), позволяет получать гипсовый камень с большей плотностью и прочностью. Получают его путем нагревания природного гипса паром под давлением 0,2–0,3 МПа с последующей сушкой при температуре 160–180 °C. Прочность его за
7 суток достигает 15–40 МПа.
Формовочный гипс состоит в основном из кристаллов р-модификации и незначительного количества примесей. Он обладает повышенной водопотребностью, а будучи затвердевшим, имеет высокую пористость. Это свойство формовочного гипса успешно используется в керамической и фарфорофаянсовой промышленности для изготовления форм.