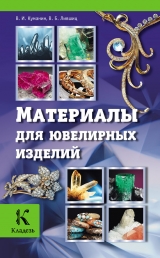
Текст книги "Материалы для ювелирных изделий"
Автор книги: Владимир Куманин
Соавторы: Виктор Лившиц
Жанры:
Хобби и ремесла
,сообщить о нарушении
Текущая страница: 3 (всего у книги 14 страниц) [доступный отрывок для чтения: 6 страниц]
3.2. Классификация ювелирных материалов
На рис. 3.Зб приведен классификатор материалов, из которых изготовляются ювелирные изделия. Наибольшее их количество выполняется из сплавов на медной основе и благородных металлов. В меньшей степени используются сплавы на алюминиевой основе и сплавы цинка. Однако для бижутерии, пуговиц, зажимов, пряжек, недорогой домашней утвари, накладок на подарочные папки и оружие и т. п. их значение остается доминирующим. Невысокая стоимость и привлекательный внешний вид, особенно после нанесения декоративных покрытий, обуславливают их широкое применение.

Рис. З.Зб. Классификатор ювелирных материалов.
3.3. Диаграммы состояния ювелирных сплавов
В ювелирной технике применяются сплавы на основе благородных металлов: серебра, золота и платины. Это основные металлы. Для имитации золотых и серебряных сплавов используют некоторые сплавы на основе меди и алюминия. Они применяются только для изготовления дешевых изделий – бижутерии.
В зависимости от состава сплав может иметь различную структуру при комнатной температуре. Структурное состояние сплава, превращения при нагреве и охлаждении описываются диаграммами состояния.
Взаимодействие двух компонентов можно изобразить графически. Такое изображение называется диаграммой состояния или диаграммой равновесия. Диаграммы состояния строятся в координатах состав – температура. Они показывают связь между составом, температурой и фазовым состоянием, структурой сплава. Вид диаграммы состояния зависит от характера взаимодействия компонентов в твердом состоянии.
Для построения диаграммы состояния выбирают отрезок на оси абсцисс, который принимается за 100 % компонента (рис. 3.4). Тогда любая точка на этом отрезке соответствует составу сплава, содержащего х%компонента А и 100 % – х%компонента В. Таким образом, если сплав содержит два компонента, то его состав определяется одной точкой на оси абсцисс. По оси ординат откладывается температура.

Рис. 3.4.
Графическое изображение состава двухкомпонентного сплава.
Между некоторыми металлами, применяемыми в ювелирной технике, образуется неограниченная растворимость в твердом состоянии. К таким системам относятся золото – серебро, золото – медь, платина – иридий. Диаграмма состояния для случая неограниченной растворимости в твердом состоянии показана на рис. 3.5. На диаграмме состояния две линии. Верхняя отделяет область, в которой сплавы находятся в жидком состоянии, т. е. в виде расплава. Эта линия называется «линия ликвидуса». Таким образом, при температурах выше линии ликвидуса все сплавы золота и серебра представляют собой расплавленный металл.

Рис. 3.5. Диаграмма состояния Au – Ag.
Нижняя линия на диаграмме называется «линия солидуса». При температурах ниже линии солидуса все сплавы в этой системе находятся в твердом состоянии. Их структура – твердый раствор золота и серебра. Между линиями ликвидуса и солидуса в сплавах в равновесии находятся две фазы – жидкость и кристаллы твердого раствора.
Кристаллизация сплава любого состава начинается при охлаждении его немного ниже линии ликвидуса. Разность между теоретической и реальной температурой начала кристаллизации называется степенью переохлаждения. В жидкой фазе зарождаются и растут кристаллы твердого раствора. Кристаллизация сплава происходит при понижении температуры и заканчивается при достижении температуры линии солидуса или несколько ниже.
Если скорость охлаждения сплава невелика, то в результате кристаллизации структура сплава представляет собой однородный твердый раствор, состав которого точно отвечает составу сплава.
Если скорость охлаждения достаточно высокая, то твердый раствор оказывается неоднородным. Это связано с особенностью кристаллизации твердых растворов при температурах, лежащих в интервале между линиями ликвидуса и солидуса. Например, при температуре 1000 °C (рис. 3.6) состав образовавшихся кристаллов твердого раствора определяется точкой А.

Рис. 3.6. Определение состава фаз по диаграмме состояния Au – Ag.
И при содержании в сплаве 50 % Au и 50 % Ag, в твердом растворе будет 70 % Ag и 30 % Au. В то же время в жидкой фазе находятся 70 % Au и 30 % Ag (точка В). При изменении температуры состав твердой фазы изменяется по линии солидуса, жидкой – по линии ликвидуса. Таким образом, при охлаждении, т. е. при изменении температуры, состав твердой фазы непрерывно изменяется.
Изменение состава происходит за счет перемещения атомов, т. е. за счет диффузии. В твердых телах подвижность атомов невелика, диффузия происходит значительно медленней, чем в жидкости. Если скорость охлаждения при кристаллизации достаточно велика, то выравнивающая диффузия не успевает произойти и состав твердого раствора оказывается неоднородным. В центральной части зерен, которая образовалась при более высоких температурах, повышенное содержание Ag, в периферийной части – повышенное содержание Au по сравнению с составом сплава. Это явление называется дендритной ликвацией. Чем шире интервал кристаллизации сплава, т. е. чем больше разница между температурами ликвидуса и солидуса, тем больше вероятность такого явления.
Неоднородность зерен сплава по составу – нежелательное явление для ювелирных сплавов. Такие сплавы сильнее корродируют, имеют неоднородные механические свойства и т. д.
Дендритную ликвацию можно устранить, если отжечь сплав при температурах на 50—100 °C ниже линии солидуса.
Диаграмму состояния, характерную для системы золото – серебро, имеют также сплавы системы золото – медь и платина – иридий. Кристаллизация сплавов в этих системах происходит аналогично сплавам золото – серебро.
Если два металла ограниченно растворимы в твердом состоянии, то вид диаграммы состояния изменяется. На рис. 3.7 показана диаграмма состояния медь – серебро. Эти два металла ограниченно растворимы в твердом состоянии. Твердый раствор меди в серебре обозначен а. Растворимость меди в серебре изменяется от 0,2 % при 200 °C до 8,8 % при 779 °C. Это максимальная растворимость. Растворимость серебра в меди (область β-раствора) изменяется от 0 % при 200 °C до 8,0 % при 779 °C.

Рис. 3.7. Диаграмма состояния Ag – Си.
Сплав, содержащий 28 % серебра, называется эвтектическим. Его кристаллизация происходит при постоянной температуре 779 °C. При этом из жидкой фазы кристаллизуются сразу два твердых раствора α и β. Процесс кристаллизации начинается с образования зародышей р-твердого раствора. Состав этих зародышей в равновесных условиях кристаллизации соответствует предельной растворимости серебра в меди, т. е. образующиеся кристаллы содержат всего 8,0 % серебра и 92,0 % меди. Иными словами, из жидкой фазы, которая содержала 28 % меди, образуется твердый объем, содержащий 92 % меди, т. е. медь выходит из жидкой фазы состав которой изменяется в сторону увеличения содержания в ней серебра. Обогащение жидкости серебром стимулирует зарождение кристаллов α-твердого раствора. Они зарождаются на уже имеющихся кристалликах β-фазы, и в дальнейшем оба кристалла α– и β-твердых растворов растут совместно. В результате такой кристаллизации структура сплава состоит из зерен двух видов, двух фаз: α-твердого раствора, содержащего 8,8 % меди и 91,2 % серебра, и β-твердого раствора, содержащего 8,0 % серебра и 92 % меди. Такая механическая смесь двух фаз, образующаяся из жидкости при постоянной температуре и имеющая постоянный состав, называется эвтектикой.
Сплавы, содержащие от 8,8 до 28 % меди, называются доэвтектическими. Их кристаллизация начинается при температурах ниже линии ликвидуса с образования кристаллов α-твердого раствора. Так как эти кристаллы содержат больше серебра, чем жидкость, в жидком расплаве содержание серебра уменьшается, а следовательно, увеличивается содержание меди. Состав жидкой фазы изменяется по линии ликвидуса, и при температуре 779 °C жидкая фаза имеет эвтектический состав, т. е. содержит 28,0 % меди. Таким образом, при температуре 779 °C все доэвтектические сплавы состоят из двух фаз: жидкого расплава, содержащего 28 % меди и 72 % серебра, и кристаллов α-твердого раствора меди в серебре. При этой температуре происходит кристаллизация жидкости с образованием эвтектики. Процесс эвтектической кристаллизации рассмотрен выше. В твердом состоянии все эти сплавы имеют следующую структуру: первичные кристаллы α-твердого раствора и окружающая их смесь кристаллов α– и β-твердых растворов – эвтектика.
Сплавы, содержащие более 28 % меди (от 28 до 92 %), называются заэвтектическими. Их кристаллизация происходит аналогично кристаллизации доэвтектических сплавов. Различие заключается в том, что в этих сплавах ниже температуры ликвидуса из жидкости выделяются кристаллы β-твердого раствора. Структура этих сплавов в твердом состоянии такова: первичные кристаллы β-фазы, окруженные эвтектикой.
При нагревании всех сплавов, содержащих от 8 до 92 % меди, плавление начинается при температуре 779 °C. Первой плавится эвтектика. При дальнейшем повышении температуры происходит плавление кристаллов α-фазы в доэвтектических сплавах или β-фазы в заэвтектических сплавах. Окончательный переход сплава в жидкое состояние соответствует нагреву до температуры линии ликвидуса. Как показывает опыт, при плавлении перегрев сплава выше линии ликвидуса не наблюдается.
4. Механические свойства сплавов
4.1. Основные механические свойства материалов
Изготовление ювелирных изделий – процесс многоступенчатый и начинается всегда с литья, т. е. получения сплава в жидком состоянии, заливки его в форму, кристаллизации. В отдельных случаях сплав используют в виде полуфабриката, например в виде проволоки. Тогда литье было проведено на заводе-изготовителе.
В процессе изготовления ювелирных изделий, например сканных, возникает задача пластической деформации сплава.
Пластическая деформация – это изменение размера и формы под влиянием внешних напряжений, которое сохраняется после снятия внешней нагрузки.
Под влиянием внешних усилий любое изделие может деформироваться. Если величина приложенных напряжений невелика, то после снятия нагрузки размер и форма изделия возвращаются к исходному состоянию. Такая деформация считается упругой. С увеличением нагрузки происходит пластическая деформация. Последняя стадия деформации – разрушение изделия.
Величина напряжений, которые может выдержать данное изделие без деформации и разрушения, зависит от механических свойств материала, из которого оно изготовлено. Стандартный способ определения механических характеристик (ГОСТ 1497-73) – испытание на растяжение цилиндрических образцов. Кривая растяжения, т. е. зависимость удлинения образца от приложенной силы, показана на рис. 4.1. До величины Р упробразец деформируется упруго и после снятия нагрузки возвращается к исходной длине. Величина Р пцназывается пределом пропорциональности, т. е. характеризует максимальную нагрузку, до которой Δ1 пропорционально Р. Различие Р пци Р упрневелико, и им обычно пренебрегают.

Рис. 4.1. Диаграмма растяжения металла.
Р – растягивающая сила (нагрузка),
ΔI – удлинение образца (деформация).
Нагрузка больше Р упрвызывает необратимое изменение длины – происходит пластическая деформация. Величина σ 0,2называется пределом текучести. Предел текучести – это условная характеристика. Это такое напряжение, которое вызывает в образце пластическую деформацию в 0,2 %. При достижении предела текучести пластическая деформация развивается без увеличения нагрузки. Однако для создания последующей пластической деформации необходим рост внешней нагрузки. После достижения Р мaxнагрузка на образец уменьшается, так как уменьшается площадь поперечного сечения образца. Образуется «шейка». В то же время напряжение (отношение силы, приложенной к образцу, к площади поперечного сечения) продолжает расти. Таким образом, можно отметить несколько стадий деформации материала под действием внешнего напряжения: упругая деформация (участок 0–2), текучесть (участок 2–3), упрочнение (участок 3–4) и разрушение (точка 5, соответствующая нагрузке Р k).
Основные характеристики прочности материала – предел текучести σ 0,2, предел упругости σ упр, предел прочности σ в.
Предел упругости – максимальное напряжение, при снятии которого величина остаточной деформации не превышает тысячных долей процента. Предел прочности – временное сопротивление разрыву – максимальное напряжение, выдерживаемое образцом.
При выборе материала для изготовления ювелирных изделий эти характеристики играют немаловажную роль.
Высокий предел упругости и текучести обеспечивает неизменность формы и размера изделия при воздействии на него различных нагрузок. Высокий предел прочности препятствует разрушению изделия.
Одним из важных механических свойств материала является его твердость. Твердость – это способность материала сопротивляться пластической деформации при внедрении в него более твердого тела. Чем выше твердость материала, тем он лучше полируется до зеркально гладкой поверхности, меньше царапается в процессе эксплуатации, сохраняя внешний вид неизменным. Высокая твердость обеспечивает обычно и высокую износостойкость.
4.2. Механизм пластической деформации
Пластическая деформация осуществляется посредством сдвига внутри кристалла по определенным кристаллографическим плоскостям, которые называются плоскостями скольжения. Сдвиг в кристалле начинается при достижении внешним напряжением величины предела текучести. Так как зерна в образце ориентированы различно относительно внешнего напряжения, то пластическая деформация развивается в металле неоднородно. В первую очередь деформируются те зерна, которые ориентированы таким образом, что напряжение в их плоскости скольжения достигает величины напряжения сдвига. Форма зерна в результате многочисленных сдвигов изменяется. При этом, так как зерна взаимно связаны, происходит поворот соседних зерен, их ориентация относительно внешнего напряжения изменяется, и пластическая деформация распространяется на другие зерна. Постепенно все зерна металла деформируются, их форма изменяется, зерна вытягиваются в направлении приложенного напряжения. В кристаллической структуре металла возникают дефекты.
В результате пластической деформации изменяются механические свойства металла: прочность увеличивается, пластичность уменьшается. Это явление называется «наклеп».
Упрочнение металла при пластической деформации и уменьшение его пластичности ограничивает возможность дальнейшей деформации. Так, при волочении проволоки с уменьшением сечения при следующих проходах через фильеру возникают обрывы.
На рис. 4.2 показана зависимость прочности и пластичности латуни Л68 от степени пластической деформации. В качестве характеристики пластичности выбрано относительное удлинение, δ%, т. е. отношение прироста длины разрушенного образца к его первоначальной длине. Степень пластической деформации оценивается по отношению:
с. п.д. = (d 2 0– d 2 д/ d 2 0,
где с.п.д. – степень пластической деформации,
d Q– диаметр проволоки до волочения,
d д– диаметр проволоки после волочения.

Рис. 4.2. Влияние степени холодной пластической деформации на твердость (НВ), прочность (σ в) и пластичность (δ,%) латуни А68.
Упрочнение, вызванное предварительной пластической деформацией, можно снять нагревом деформированного металла. В процессе пластической деформации металл запасает энергию, и поэтому состояние его является неустойчивым. Однако при низких температурах диффузия в металле не происходит, так как подвижность атомов в твердом теле мала. При нагреве металла подвижность атомов увеличивается и, начиная с определенной температуры, возникают самопроизвольное зарождение новых, недеформированных зерен и их рост.
Этот процесс называется рекристаллизацей обработки или первичной рекристаллизацей. Температуру, при которой начинается этот процесс, называют температурой начала рекристаллизации Т нр. С повышением температуры выше температуры начала рекристаллизации образование и рост новых зерен продолжается вплоть до того, как будет достигнута температуры конца рекристаллизации Т кр. Температура начала рекристаллизации зависит от множества факторов. В первую очередь она связана с природой самого металла, для чистого металла ее можно приближенно оценить по температуре его плавления:
Т нр= 0,ЗТ пл(К),
где Т пл– температура плавления металла,
Т нр– температура начала рекристаллизации.
Коэффициент 0,3 приближенный и зависит от чистоты металла. Для особо чистых металлов он уменьшается до 0,25—0,15, для сплавов увеличивается до 0,6.
Температура начала рекристаллизации зависит также от степени пластической деформации и уменьшается с увеличением степени пластической деформации.
Образование новых недеформированных зерен и снижение внутренней энергии металла за счет уменьшения концентрации дефектов приводит к изменению механических свойств.
На рис. 4.3 показана зависимость прочности и пластичности холоднодеформированного железа от температуры отжига. Пластичность и вязкость металлов и сплавов существенно зависят от размера зерна. В свою очередь, размер зерна зависит от температуры рекристализационного отжига и степени предварительной пластической деформации. В процессе рекристаллизации обработки размер зерна обычно уменьшается по сравнению с исходным, так как происходит влияние температуры отжига на прочность и пластичность холоднодеформированного металла.

Рис. 4.3. Зарождение новых мелких зерен, которые не успевают вырасти к моменту окончания процесса.
С увеличением температуры выше температуры конца рекристаллизации зерно продолжает расти. Особенно интенсивно это происходит в чистых металлах. На размер зерна оказывает влияние также степень предварительной холодной пластической деформации. Чем выше степень деформации, тем меньше размер рекристаллизованного зерна.
Температура рекристаллизации обработки является физической границей между холодной и горячей пластической деформацией.
Пластическая деформация ниже этой температуры является холодной. При этом возникает упрочнение металла – наклеп. Пластическая деформация при температурах выше температуры рекристаллизации называется горячей. При горячей пластической деформации наклеп непрерывно снимается процессом рекристаллизации. После горячей пластической деформации упрочнения металла не наблюдается.
Выбор температуры рекристаллизационного отжига определяется составом сплава и степенью холодной пластической деформации. Обычно она устанавливается на 50—100 °C выше температуры конца рекристаллизации.
5. Технологические свойства сплавов
Под технологическими свойствами металлов и сплавов понимают способность металла подвергаться различным видам обработки. К технологическим свойствам металлов и сплавов относятся: литейные, ковкость, или деформируемость, в горячем и холодном состоянии, свариваемость, прокаливаемость и обрабатываемость резанием.
5.1. Литейные свойства
Литейные свойства двух– и трехкомпонентных сплавов можно оценить по положению их на диаграмме состояния. Закономерности изменения литейных свойств определяются при построении кривых состав – литейное свойство в совокупности с диаграммой состояния. К литейным свойствам сплавов можно отнести жидкотекучесть, линейную и объемную усадки, трегциностойкость, поверхностное натяжение, вязкость и др.
Жидкотекучесть– свойство, характеризующее способность расплавов заполнять литейные формы.
Влияние различных факторов на жидкотекучесть.Величина жидкотекучести непосредственно не связана с вязкостью и поверхностным натяжением жидкого металла, а определяется интервалом кристаллизации и совокупностью теплофизических свойств металлов: теплотой кристаллизации, теплоемкостью и теплопроводностью, вязкостью, окисляемостью. При этом теплота кристаллизации является основным фактором: чем больше теплота кристаллизации, тем выше жидкотекучесть. Минимумы и максимумы жидкотекучести (X)сплавов в зависимости от состава отвечают определенным участкам и критическим точкам на диаграммах состояния (рис. 5.1). Сплавы с широким интервалом кристаллизации, как правило, обладают минимальной жидкотекучестью, а максимумы на диаграммах состав – жидкотекучесть соответствуют эвтектическим сплавам и химическим соединениям.

Рис. 5.1. Жидкотекучесть сплавов системы А-Б в зависимости от их состава.
Необходимо также учитывать размеры, форму кристаллов, образующихся в начальной стадии затвердевания сплавов, и теплоту их образования. Прослеживается следующая зависимость. Если первичные кристаллы растут в виде разветвленных дендритов, граница нулевой жидкотекучести, соответствующей температуре, при которой поток перестает течь, находится вблизи линии ликвидуса,
Если первичные кристаллы растут компактно и имеют небольшие размеры, то граница нулевой жидкотекучести тяготеет к линии солидуса, т. е. при выделении значительной части твердой фазы металл продолжает течь, что объясняется несвязанностью между собой выделившихся первичных кристаллов. Таким образом, увеличение размеров первичных кристаллов и образование ими разветвленной структуры снижает жидкотекучесть. Оценивая величину жидкотекучести, для получения более точных результатов необходимо также учитывать формы кристаллов, образующихся в начальной стадии затвердевания сплавов, и теплоту их образования.
На жидкотекучесть влияют также условия плавки и заливки, перегрев металла, насыщение металла посторонними включениями, условия подвода металла к форме.
Пробы для измерения жидкотекучести.Количественные значения жидкотекучести определяют по длине заполнения канала литейной формы с определенной площадью поперечного сечения.
Технологические пробы для определения жидкотекучести можно разделить на три вида:
– пробы, основанные на прекращении течения в сужающемся канале;
– пробы, основанные на прекращении течения вследствие кристаллизации металла в узком выходном канале;
– пробы, основанные на прекращении течения в длинном канале постоянного сечения вследствие охлаждения и кристаллизации.
К пробам первого вида (сужающийся канал) относятся клиновые пробы (рис. 5.2).

Рис. 5.2. Клиновая проба для определения жидкотекучести.
Показателем жидкотекучести в клиновой пробе является расстояние Iмежду вершиной клина и закругленной вершиной затвердевшего металла.
Пробы второго вида – шариковые – можно использовать для определения жидкотекучести по весу вытекшего металла.
Мерой жидкотекучести в шариковой пробе, предложенной А. Г. Спасским (рис. 5.3), является диаметр отверстия, образующегося в отливке, залитой в металлическую форму 1с вертикальным разъемом. Металл заливается через воронку 4,поступает в полость формы через литниковый канал 5, заполняет полость формы и подтекает в пространство между планкой (клином) 3и шариком 2диаметром 20 мм, но не заполняет все пространство, оставляя отверстие.

Рис. 5.3. Шариковая проба для определения жидкотекучести (по А. Г. Спасскому):
1 – полуформа; 2 – шарик; 3 – клин; 4 – воронка; 5 – литниковый канал.
Клиновые и шариковые пробы можно использовать для оценки заполнения тонких рельефов.
К пробам третьего вида относятся прямые, спиральные, U-образные, лабиринтные и винтовые.
Пробы этого вида дают более точные результаты с меньшим разбросом параметров. Показателем жидкотекучести является длина пути потока металла до остановки. Пробы третьего вида заливают гравитационным или вакуумным методом. К этому же виду можно отнести пробы с несколькими каналами разной толщины, заполняемыми из общего центрального стояка.
Наибольшее распространение получили спиральные (рис. 5.4.) и U-образные (рис. 5.5) пробы с гравитационным заполнением. Испытание материала на жидкотекучесть заключается в заполнении спиральной или U-образной формы расплавленным металлом и определении длины полученной спиральной или U-образной пробы. На модели спирали и соответственно в форме имеются отметки через каждые 50 мм. Длина спирали (в спиральной пробе) или длина заполнившейся части вертикального канала диаметром б мм (в U-образной пробе), выраженные в миллиметрах, являются характеристикой жидкотекучести сплава в данных условиях.

Рис. 5.4. Спиральная проба для определения жидкотекучести по Самарину-Нехендзи:
1 – чаша нарощалка; 2 – сетка, 3 – стояк, 4 – зумпф, 5 – бобышка спираль, 6 – выступы

Рис. 5.5.
U-образная проба для определения жидкотекучести литейных сплавов.
Причем спиральная проба проводится для материалов с высокой жидкотекучестью (для чугунов, силуминов и т. д.), U-образная проба – для материалов, обладающих относительно низкой жидкотекучестью (для высоколегированных сталей, жаропрочных и тугоплавких металлов и сплавов).
При этом основным является определение условий остановки движущегося потока: выделение 20 % твердой фазы, образование на конце потока прочной твердой корочки, рост в канале литейной формы дендритов, препятствующих движению потока, накопление твердых кристаллов на конце потока.
Для обеспечения идентичных условий заполнения проб при сравнении жидкотекучести предложено различать два вида жидкотекучести: практическую и условную.
Практическая жидкотекучесть определяется в условиях постоянной температуры заливки (и, следовательно, неодинакового перегрева для всех сплавов данной группы). При этом можно оценивать влияние на жидкотекучесть изменений химического состава сплава в цеховых условиях, при поддержании постоянной температуры в плавильном агрегате. Условная жидкотекучесть определяется в условиях одинакового перегрева над температурой ликвидуса. Данный вид пробы получил наибольшее распространение.